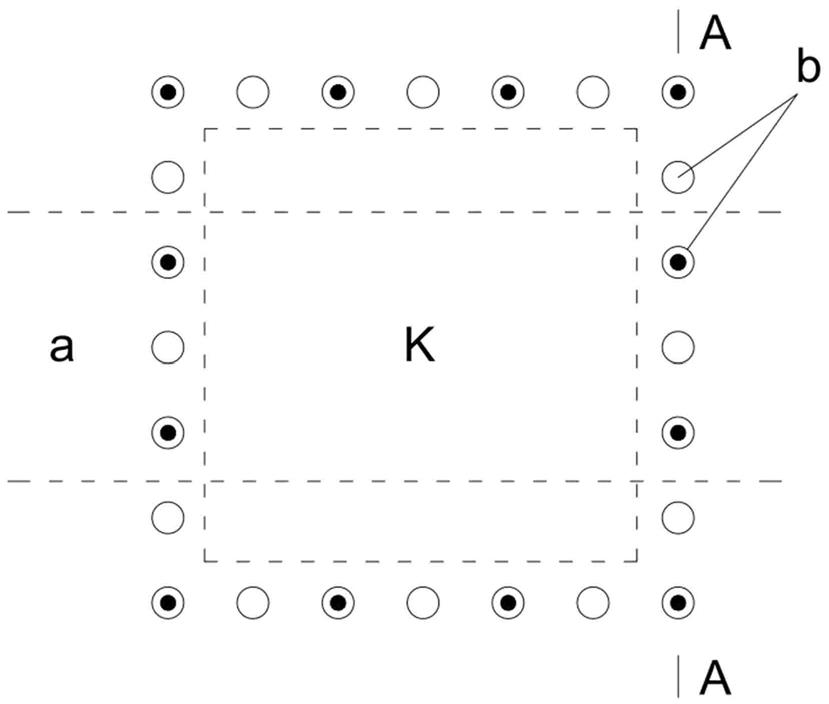
1.本发明涉及施工监控测量技术领域,尤其是涉及一种用于深基坑悬臂围护桩桩体变形的监测方法。
背景技术:2.目前,地铁车站的围护施工主要包括钻孔桩围护结构、地连墙围护结构、以及直接放坡开挖等。对于钻孔桩围护结构,通常采用先施工钻孔灌注桩+内支撑结构、再修建车站、最后施作隧道区间的工序。为了保证整体施工安全,需要在施作围护桩时提前预埋桩体测斜管,在施工车站时对桩体的位移情况进行监测。然而,在某些情况下,会改变施工顺序,例如,先施工围护桩、然后施作隧道区间、最后施作车站。这种施工方式,会将处于隧道a开挖区的围护桩b截断(见图1、2),导致之前预埋好的桩体测斜管被破坏,无法采用常规方式对基坑内桩体的深层水平位移情况进行监测。此外,被截断的围护桩被隧道分为上下两段、中部悬空,更加容易出现移位现象,当不能及时准确地了解悬臂桩的位移状况时,就不能准确反应基坑的稳定性,不能提前对基坑的安全做出提前预警,导致车站基坑存在巨大的安全隐患。
技术实现要素:3.为了解决上述问题,本发明提供一种简单易行、准确可靠的用于深基坑悬臂围护桩桩体变形的监测方法,具体可采取如下技术方案:本发明所述的用于深基坑悬臂围护桩桩体变形的监测方法,适用于开挖隧道后的车站施工,包括如下步骤:第一步,按照设计方案,进行第一段车站基坑的开挖;第二步,对暴露出的围护桩进行测量放样,确定其中被隧道截断的钢筋混凝土桩,并进行标识;第三步,在每一钢筋混凝土桩上分别安装多个沿竖向设置的定位装置,并采用全站仪定时测量各定位装置的坐标;第四步,将步骤三得到的各定位装置的坐标传输至计算机系统,通过坐标值的变化量判断钢筋混凝土桩的位移情况;第五步,继续向下分段开挖车站基坑,在每一阶段均按照步骤二至步骤四的方法监测钢筋混凝土桩的位移情况,直至车站施工结束。
4.所述定位装置包括支架,具有位于钢筋混凝土桩内的埋设段和延伸至钢筋混凝土桩外侧的连接段,所述埋设段设置有防脱环;安装板,设置在所述连接段上,具有与钢筋混凝土桩半径垂直的安装面,且所述安装面背向钢筋混凝土桩;反射片,设置在所述安装板的安装面上,用于与所述全站仪相配合。
5.所述第三步中,首先在钢筋混凝土桩上钻孔,孔内清渣后,采用植筋方式将定位装置的支架安装在孔内,完成定位装置的安装。
6.所述定位设备在每一钢筋混凝土桩上均按照0.5m/个的间距竖向布置为一列,且每一定位设备与所在钢筋混凝土桩的桩顶至少相距1m。
7.所述第三步中,测量每一定位装置的坐标均按照如下步骤:s1,设定坐标系,选取点a和点b,其中,点a的坐标为(xa,ya),直线ab的方位角为α
a-b
;s2,将全站仪放置在点b,测量其与定位装置所在点p的距离d,以及直线ab和直线ap的夹角β;s3,按照公式 x
p
=xa+d*cos(α
a-b
+β)计算定位装置所在点p的坐标(x
p
,y
p
)。
8.y
p
=xa+d*sin(α
a-b
+β)所述第四步中,通过比较同一个定位装置的坐标在不同时刻的变化量判断钢筋混凝土桩的位移情况。
9.本发明提供的用于深基坑悬臂围护桩桩体变形的监测方法,操作简单、经济可靠,选择在含有预埋钢筋的悬臂桩上安装定位装置,其与现场全站仪相配合,能够快速、准确地测定悬臂桩的坐标,进而得到悬臂桩的位移数据,及时发现基坑围护桩是否发生险情,从而对基坑的安全稳定性做出判断,以便采取合理措施进行补救,防止出现基坑坍塌或周围路面隆起等问题,保证施工安全。
附图说明
10.图1是基坑、隧道和围护桩的位置关系图。
11.图2是图1的a-a截面图。
12.图3是本发明中定位装置的安装位置示意图。
13.图4是本发明中对定位装置进行坐标测量的结构示意图。
14.图5是实施例中进行坐标测量的坐标系设定的示意图。
具体实施方式
15.下面结合附图对本发明的实施例作详细说明,本实施例在以本发明技术方案为前提下进行实施,给出了详细的实施方式和具体的施工过程,但本发明的保护范围不限于下述实施例。
16.如图3、4所示,本发明所述的用于深基坑悬臂围护桩桩体变形的监测方法,适用于开挖隧道后的车站施工,包括如下步骤:第一步,按照设计方案,进行第一段车站基坑的开挖;第二步,对暴露出的围护桩进行测量放样,确定其中被隧道截断的钢筋混凝土桩1(即内设钢筋的围护桩),并进行标识;第三步,在每一钢筋混凝土桩1上分别安装多个沿竖向设置的定位装置2,并采用全站仪3定时测量各定位装置2的坐标;上述定位装置2由支架21、安装板22和反射片23组成,其中,支架21是由φ14的钢筋制作的l形结构,其具有位于钢筋混凝土桩1内的埋设段和延伸至钢筋混凝土桩1外侧的
连接段,埋设段上设置有防脱环24;安装板22为6
×
6cm的镀锌钢板,其焊接在支架21的连接段上,具有与钢筋混凝土桩1半径垂直的安装面,且安装面背向钢筋混凝土桩1;该安装面上安装有与全站仪3配合使用的反射片25。
17.定位装置2安装时,首先采用φ14的钻头在钢筋混凝土桩1上钻孔,达到设计孔深后,用吹风机对孔内清渣,然后采用植筋方式将带有反射片25的支架21安装在孔内。上述支架21安装孔在每一钢筋混凝土桩1上均按照0.5m/个的间距竖向布置为一列,且最顶部的安装孔与所在钢筋混凝土桩1的桩顶至少相距1m。
18.上述定位装置结构简单、易于制作,其与全站仪3相配合能够方便地测得每一定位装置2的坐标,具体如下:s1,设定坐标系,选取点a和点b,其中,点a的坐标为(xa,ya),直线ab的方位角为α
a-b
;s2,将全站仪放置在点b,测量其与定位装置所在点p的距离d,以及直线ab和直线ap的夹角β;s3,按照公式 x
p
=xa+d*cos(α
a-b
+β)计算定位装置所在点p的坐标(x
p
,y
p
)。
19.y
p
=xa+d*sin(α
a-b
+β)为了保证测量准确性,需要按照上述方法对每一定位装置2的坐标进行2-4次测量,取β和d的平均值,再根据s3所述公式计算点p的坐标。
20.每一定位装置2的坐标通常间隔24小时均进行一次测量计算。
21.第四步,将步骤三得到的各定位装置2的坐标传输至计算机系统,通过坐标值的变化量比较来判断钢筋混凝土桩1的位移情况。通常情况下,多采用对同一个定位装置2的坐标在不同时刻的变化量为依据,对钢筋混凝土桩1的位移情况进行判断。
22.如图5所示,以矩形基坑k和隧道a交叠区的中心为坐标系原点o,以隧道a的中轴线(东西方向)为x轴,中轴线的垂线(南北方向)为y轴,第一天测得的点p坐标为(x1,y1),第二天测得的点p坐标为(x2,y2),当(x
2-x1)的差值为正值时,该钢筋混凝土桩1有东移趋势,反之,为负值时,有西移趋势;同理,当(y
2-y1)的差值为正值时,该钢筋混凝土桩1有北移趋势,反之,为负值时,有南移趋势。此外,还可以通过计算位移量。
23.第五步,继续向下分段开挖车站基坑,在每一阶段均按照步骤二至步骤四的方法监测钢筋混凝土桩的位移情况,直至车站施工结束。
24.需要说明的是,在本发明的描述中,诸如“前”、“后”、“左”、“右”、“垂直”、“水平”、“内”、“外”等指示的方位或位置关系的术语是基于附图所示的方位或位置关系,仅是为了便于描述本发明和简化描述,而不是指示或暗示所指的装置或元件必须具有特定的方位、以特定的方位构造和操作,因此不能理解为对本发明的限制。