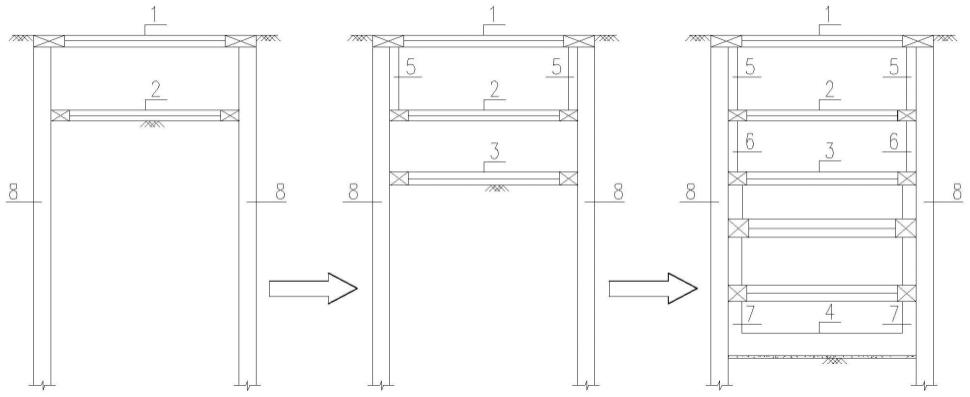
1.本发明属于土建基坑施工技术领域,具体涉及一种明挖逆作基坑主体结构及其施工方法。
背景技术:2.明挖逆作法是在基坑开挖时,采取由上而下浇筑主体结构的施工方法,利用基坑主体结构与基坑围护结构共同作为基坑支护结构,即基坑开挖到达某一设计标高时,就开始施做主体结构,达到设计强度后再继续向下开挖,直至开挖至设计基底标高,施做完成最后一层主体结构。传统的明挖逆作法施工方法,需待上部主体结构施工完成达到设计强度后,方可进行下部基坑土石方开挖,影响施工工期,导致主体结构施工间断,造成人员窝工。
3.例如中国发明专利申请号为cn201710227466.9的专利申请公开了一种大型深基坑主体结构侧墙的快速施工方法,其深基坑围护结构采用地下连续墙,采用在地下连续墙内侧设置沿地下连续墙长度方向延伸的腰梁作为支撑体系,每层腰梁间隔设主体结构侧墙;包括以下步骤:
4.s1、根据拟开挖深基坑开挖深度和周长确定地下连续墙的厚度、槽段总数构筑深基坑周边地下连续墙;槽段两侧设有搅拌桩槽壁加固;地下连续墙插入深度比基坑开挖深度深,嵌入基岩1~2米;绑扎基坑连续墙钢筋时,沿侧墙高度方向间隔均匀布置有若干排钢筋接驳器组,每排钢筋接驳器组由若干个沿侧墙长度方向间隔均匀布置的钢筋接驳器组成;上述的钢筋接驳器预埋在侧墙内;
5.s2、侧墙内侧基坑采用分层、分段开挖,挖至每层侧墙底部;
6.s3、绑扎侧墙钢筋,露出钢筋接驳器端部;
7.s4、侧墙防水和砼垫层施工,在砼垫层上绑扎侧墙钢筋;每个钢筋接驳器均连接有防水对拉螺杆;
8.s5、侧墙模板采用轻型复合材料模板,根据侧墙可拆除支撑空间、主体侧墙高度及侧墙混凝土裂缝控制最佳尺寸来设计轻型复合材料模板的整体长度和高度,将轻型复合材料模板移向钢筋绑扎好的侧墙,将轻型复合材料模板安装在防水对拉螺杆上,实现快速立侧模;
9.s6、浇筑前模板变形测点埋设,观测记录测点位移、高程数据变化,并监测腰梁支撑轴力;
10.s7、利用汽车输送泵多点分层分段浇筑;浇筑过程中模板变形测点观测,观测计算模板变形值,并监测腰梁支撑轴力变化;
11.s8、侧墙砼强度达到80%以上后,开始松动模板进行脱模;
12.s9、脱模后,在模板上涂刷脱模剂;重复上述步骤进行下一层侧墙施工。
13.上述现有技术公开了一种大型深基坑主体结构侧墙的快速施工方法施工工序安排不合理,在实际的施工过程中,即存在窝工的情况,工程质量也得不到保障。
14.基于现有技术存在的上述技术问题,本发明提供一种明挖逆作基坑主体结构及其
施工方法。
技术实现要素:15.为解决现有技术存在的上述技术问题,本发明提供一种明挖逆作基坑主体结构施工方法。
16.本发明采用以下技术方案:
17.本发明提供一种明挖逆作基坑主体结构施工方法,包括:
18.步骤1,根据基坑开挖施工工序,先施做基坑围护结构及地下连续墙,待围护结构完成后,对地下连续墙桩身完整性进行检测,进行抽水试验并进行基坑降水;
19.步骤2,开挖基坑冠梁及第一道混凝土支撑底部以上土方,绑扎冠梁及第一道混凝土支撑的钢筋,安装两侧模板支护并浇筑混凝土;
20.步骤3,待冠梁及第一道混凝土支撑达到设计强度后,开挖基坑第二道环梁及混凝土支撑底部以上土方,绑扎第二道环梁及混凝土支撑的钢筋,安装两侧模板支护并浇筑混凝土;
21.步骤4,待第二道环梁及混凝土支撑达到设计强度后,开挖基坑第三道环梁及混凝土支撑底部以上土方,绑扎第三道环梁及混凝土支撑钢筋,安装两侧模板支护并浇筑混凝土,同时,在第二道环梁边缘搭设1.5m宽作业平台,作业平台采用3根工字钢连接成一个整体固定在第二道环梁及混凝土支撑上部,在作业平台上部搭设临时钢管脚手架绑扎第一层侧墙钢筋、安装模板支护,最后浇筑侧墙混凝土,第三道环梁及混凝土支撑与负一层侧墙上下同步交叉作业,互不干扰,加快工期;
22.步骤5,待第三道环梁及混凝土支撑达到设计强度后,搭设作业平台,同步施工第三道环梁上部负二层侧墙及下部第四道环梁及混凝土支撑,继续开挖基底,进行人工清底,浇筑混凝土垫层混凝土,敷设防水卷材,浇筑防水保护层,绑扎结构底板钢筋,浇筑底板混凝土,完成结构封底。
23.进一步地,步骤1中,施做基坑围护结构地下连续墙包括:
24.步骤1.1,施做地下连续墙的导墙;
25.步骤1.2,地下连续墙成槽施工,将地下连续墙分幅,采用抓斗成槽设备开挖槽段,槽段挖掘完成后采用自动测斜仪和激光尺检查槽段,根据自动测斜仪和激光尺的检测结果挖掘修正槽段,采用压实辊压实槽段底端;
26.步骤1.3,钢筋笼的吊放,根据钢筋笼重量及重心,选择起吊吊点,根据槽段宽度来设置导管仓,钢筋笼在吊点处采用桁架进行加固;
27.步骤1.4,在钢筋笼吊装完毕后12小时内进行浇筑混凝土,地下连续墙一次性浇筑完成;
28.步骤1.5,待浇筑混凝土凝固后,进行养护作业。
29.进一步地,步骤1.4中,混凝土的坍落度控制在150-170mm,每立方米混凝土中水泥用量不小于400kg,骨料最大粒径不大于35mm,砂率控制在35%-45%之间。
30.进一步地,步骤1.4中,采用边浇筑边振捣的浇筑方式,振捣采用插入振动棒振捣结合表面振动器振捣的方式进行。
31.进一步地,步骤1.4中,还包括在地下连续墙上安装钢筋计、应变计和监测管的步
骤。
32.进一步地,步骤1中,基坑围护结构地下连续墙施工完成后,采用经纬仪和水准监测地下连续墙水平位移和沉降量。
33.进一步地,步骤1中,结合地勘报告,施做三口试验井抽水试验,根据试验结果进行基坑降水设计,施做基坑内外降水井,使基坑内水位降低至基底以下1m。
34.进一步地,步骤3中还包括在第二道环梁及混凝土支撑上预埋pvc套管作为侧墙混凝土浇筑口。
35.进一步地,步骤4中,在绑扎第一层侧墙钢筋之前,进行侧墙凿毛并涂刷防水材料。
36.进一步地,步骤4中,采用水准监测第二道环梁及混凝土支撑的沉降量。
37.进一步地,步骤4中,还包括在作业平台外侧安装防护栏杆,满挂密目网。
38.本发明的优越技术效果在于:
39.1、本发明所述明挖逆作基坑主体结构施工方法,通过将环梁及混凝土支撑与侧墙同步施作,使明挖逆作基坑主体结构施工方法提高了基坑开挖的效率,减少了窝工;
40.2、本发明所述明挖逆作基坑主体结构施工方法,通过采用对地下连续墙和环梁及混凝土支撑进行监测,减少了施工过程中的风险。
附图说明
41.图1是本发明实施例中明挖逆作基坑主体结构施工工序的示意图;
42.图2是本发明实施例中作业平台的结构示意图。
43.图中,1-冠梁及第一道混凝土支撑、2-第二道环梁及混凝土支撑、3-第三道环梁及混凝土支撑、4-底板混凝土、5-负一层侧墙、6-负二层侧墙、7-底层结构侧墙、8-围护结构、9-脚手架、10-工字钢、11-作业平台、12-防护栏杆、13-pvc套管、14-侧墙混凝土浇筑口。
具体实施方式
44.为了能够更清楚地理解本发明的上述目的、特征和优点,下面结合附图和具体实施方式对本发明进行进一步的详细描述,需要说明的是,在不冲突的情况下,本技术的实施例及实施例中的特征可以相互组合。
45.实施例
46.所述明挖逆作基坑主体结构施工方法,包括:
47.步骤1,根据基坑设计图纸,先施做基坑围护结构8的地下连续墙,待围护结构8完成后,对地下连续墙桩身完整性进行检测,结合地勘报告,施做三口试验井抽水试验,根据试验结果进行基坑降水设计,施做基坑内外降水井,使基坑内水位降低至基底以下1m;
48.步骤2,开挖基坑冠梁及第一道混凝土支撑1底部以上土方,按照设计图纸绑扎冠梁及第一道混凝土支撑的钢筋,安装两侧模板支护并浇筑混凝土;
49.步骤3,待冠梁及第一道混凝土支撑1达到设计强度后,开挖基坑第二道环梁及混凝土支撑2底部以上土方,按照设计图纸绑扎第二道环梁及混凝土支撑2的钢筋,安装两侧模板支护并浇筑混凝土;
50.步骤4,待第二道环梁及混凝土支撑2达到设计强度后,开挖基坑第三道环梁及混凝土支撑3底部以上土方,按照设计图纸绑扎第三道环梁及混凝土支撑3的钢筋,安装两侧
模板支护并浇筑混凝土,同时,在第二道环梁边缘搭设1.5m宽作业平台,作业平台采用3根工字钢连接成一个整体固定在第二道环梁及混凝土支撑2上部,在作业平台上部搭设临时钢管脚手架绑扎第一层侧墙钢筋、安装模板支护,最后浇筑侧墙混凝土,第三道环梁及混凝土支撑3与负一层侧墙5上下同步交叉作业;
51.步骤5,待第三道环梁及混凝土支撑3达到设计强度后,搭设作业平台,同步施工第三道环梁上部负二层侧墙6及下部第四道环梁及混凝土支撑,根据同步施作上层侧墙和下层环梁及混凝土支撑的方式施作,直至基坑基底,进行人工清底,浇筑混凝土垫层混凝土,敷设防水卷材,浇筑防水保护层,绑扎结构底板钢筋,浇筑底板混凝土4,完成结构封底。
52.在本实施例中,如图1所示,围护结构8完成后,按照降水专项方案进行基坑降水施工,开挖第一层土方施做冠梁及第一道混凝土支撑1,待冠梁及第一道混凝土支撑1达到设计强度后,开挖第二层土方施做第二道环梁及混凝土支撑2,待第二道环梁及混凝土支撑2达到设计强度后,开挖第三层土方施做第三道环梁及混凝土支撑3,依此类推,直至开挖最后一层土方至基底,施做结构底板4,同时,主体结构侧墙与基坑开挖交叉作业,当第二道环梁及混凝土支撑2达到设计强度后,在第二道环梁及混凝土支撑2上部架设工字钢10,搭设作业平台11,平台上部搭建临时脚手架9施做负一层侧墙5防水、钢筋及混凝土,后续类推至底层结构侧墙7;
53.主体结构侧墙与下部基坑土方开挖及环梁施工同步作业,需待该层环梁及混凝土支撑达到设计强度后,如图2所示,在环梁外沿及混凝土支撑上架设两根工字钢10,工字钢两侧采用m12膨胀螺栓固定在支撑梁上,防止工字钢移位或侧翻,工字钢上部满铺钢板作业平台11,并固定牢固,作业平台11上部搭建临时脚手架9进行侧墙凿毛、涂刷防水、钢筋绑扎及模板安装施工,作业平台11外侧安装防护栏杆12,满挂密目网,在每层环梁上部预埋pvc套管13作为侧墙混凝土浇筑口14进行侧墙混凝土浇筑;
54.在施工过程当中,地下连续墙建成,当基坑开挖的应力释放与上部荷载共同作用下,地下连续墙会发生抬升和沉降问题,一旦沉降较大,就会对建筑物结构安全产生影响,一般沉降差不能超过20mm,如果超过警报值,应该停止施工,在部分节点上加强压重,也可放慢挖土或者局部加快挖土等,有些地方也可采取加固与注浆的方法,因此,需要对地下连续墙进行沉降监测;
55.同样的,冠梁及第一道混凝土支撑、第二道环梁及混凝土支撑、第三道环梁及混凝土支撑、底板混凝土均存在变形沉降的情况,因此,也需要对冠梁及第一道混凝土支撑、第二道环梁及混凝土支撑、第三道环梁及混凝土支撑、底板混凝土进行沉降监测。
56.施做基坑围护结构地下连续墙包括:
57.步骤1.1,施做地下连续墙的导墙;
58.步骤1.2,地下连续墙成槽施工,根据设计图纸将地下连续墙分幅,采用抓斗成槽设备开挖槽段,槽段挖掘完成后采用自动测斜仪和激光尺检查槽段,根据自动测斜仪和激光尺的检测结果通过人工挖掘修正槽段,采用压实辊压实槽段底端;
59.步骤1.3,钢筋笼的吊放,根据钢筋笼重量及重心,选择起吊吊点,根据槽段宽度来设置导管仓,钢筋笼在吊点处采用桁架进行加固;
60.步骤1.4,在钢筋笼吊装完毕后12小时内进行浇筑混凝土,地下连续墙一次性浇筑完成;
61.步骤1.5,待浇筑混凝土凝固后,进行养护作业;
62.在本实施例中,导墙的作用在于:作为地下连续墙在地表面的基准物,确定地下连续墙单元槽段在实地的位置,作为地表土体的挡土墙,防止泥浆流失,作为容纳和储蓄泥浆的沟槽,作为挖槽机挖槽起始阶段的导向,作为检测槽段形位偏差的基准,作为钢筋笼入槽吊装时的支承,作为顶拔接头管时的支座;
63.采用压实辊压实槽段底端,用于替代传统的清孔施工,传统技术采用抓斗直接挖除槽底沉渣之后,进行进一步清除抓斗未能挖除的细小土渣,采用压实的方式能够有效的节省施工时间;
64.为了防止钢筋笼在吊装过程中产生不可复原的变形,钢筋笼均设置纵向抗弯桁架,转角形钢筋笼还需增设定位斜拉杆;
65.本实施例采用钢筋笼整体起吊的方案,先用主钩起吊钢筋笼主吊吊点,副钩起吊钢筋笼的副吊吊点,多组葫芦主副钩同时工作,为防止起吊钢筋笼在下端拖引,笼下端系上绳子,人力操作以减少摆动,使钢筋笼缓慢吊离地面,控制钢筋笼垂直度,对准槽段位置缓慢入槽并控制其标高,并用槽钢制作的扁担搁置在导墙上;
66.浇筑混凝土时,应经常观察钢筋笼的情况,当发现有变形、移位时,应立即停止浇筑,并应在已浇筑的混凝土凝结前修整完好。
67.步骤1.4中,混凝土的坍落度控制在150-170mm,每立方米混凝土中水泥用量不小于400kg,骨料最大粒径不大于35mm,砂率控制在35%-45%之间;
68.在本实施例中,为了加强混凝土的性能,在混凝土中加入防冻剂和防水剂。
69.步骤1.4中,采用边浇筑边振捣的浇筑方式,振捣采用插入振动棒振捣结合表面振动器振捣的方式进行;
70.在本实施例中,采用50型混凝土输送泵进行混凝土的浇筑;
71.在将混凝土泵与输送管连通后,应按所用混凝土泵使用说明书的规定进行全面检查,符合要求后方能开机进行空运转,混凝土泵启动后,应先泵送适量的水,以湿润混凝土泵的料斗、活塞及输送管的内壁等直接与混凝土接触的部位,经泵送水检查,确认混凝土泵和输送管中没有异物后,可以采用与将要泵送的混凝土内除粗骨料外的其他成分相同配合比的水泥砂浆进行泵管和输送管的润滑,也可以采用纯水泥浆或1:2水泥浆;润滑用的水泥浆或水泥砂浆应分散布料,不得集中浇筑在同一处。
72.步骤1.4中,还包括在地下连续墙上安装钢筋计、应变计和监测管的步骤。
73.本发明不受上述实施例的限制,上述实施例和说明书中描述的只是说明本发明的原理,在不脱离本发明精神和范围的前提下,本发明还会有各种变化和改进,这些变化和改进都落入要求保护的本发明范围内。本发明要求保护范围由所附的权利要求书界定。