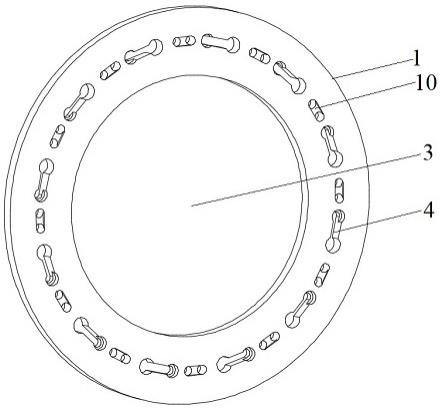
1.本发明涉及预制桩技术领域,具体涉及一种预制桩用预应力钢筋锚固增强装置。
背景技术:2.预制桩作为一种主要的桩基类型,具有工厂化生产的优势,其造价低,工期快,在工程中得到了广泛的应用。为了充分发挥预制桩的材料性能和保证运输过程中桩体不开裂,在预制桩制作时,往往会对其中的受力钢筋施加预应力,施加预应力的操作过程为:1,预应力钢筋在端部镦粗头形成钢筋镦头;2,桩基端板上设置多组连通的一大一小两个穿筋孔;3,制作钢筋笼;4,钢筋镦头穿过端板上的大头开孔,固定在小孔上;5,张拉端板施加预应力。预制桩身混凝土浇筑完成并达到放张要求后,放张预应力,通过端板顶压桩身混凝土,保持钢筋受拉和混凝土受压状态。
3.但是在多组预制桩桩身荷载试验中,整个桩身最先被破坏的是钢筋镦头部位,其表现为钢筋镦头被拉断脱离预应力钢筋,其破坏荷载常常小于桩身的极限荷载,不符合接头极限荷载大于桩身极限荷载这一常规设计要求。为了增强端板与桩身混凝土的粘结力,减少钢筋镦头受到的拉力以确保钢筋镦头破坏迟于桩身破坏,常见的增强方式是在端板上焊接锚固增强钢筋,锚固增强钢筋一端与端板焊接,另一端锚固在桩身混凝土中。但是增强钢筋的焊接施工操作复杂,受限于工人素质和技术水平很容易出现焊接质量差等问题。
技术实现要素:4.本发明针对现有技术的不足,提出了一种结构简单、施工方便、锚固效果更加可靠的预制桩用预应力钢筋锚固增强装置。
5.本发明是通过以下技术方案予以实现的:一种预制桩用预应力钢筋锚固增强装置,包括端板和增强钢筋,所述端板上还设有多组锚固组件,所述锚固组件包括预应力筋锚固孔、连接槽、螺纹孔,所述螺纹孔的孔径大于等于预应力钢筋的钢筋镦头最大直径,所述连接槽宽度大于等于预应力钢筋直径且小于所述螺纹孔的孔径,所述预应力筋锚固孔孔径大于所述连接槽的宽度并且小于所述螺纹孔的孔径,所述预应力筋锚固孔内设有环形凸台,将预应力筋锚固孔沿端板厚度方向分为外部大孔和内部小孔,所述外部大孔孔径大于所述连接槽的宽度并且小于预应力钢筋镦头直径,所述内部小孔孔径等于所述连接槽的宽度,所述连接槽贯穿所述端板并连接所述预应力筋锚固孔和所述螺纹孔;所述增强钢筋呈“u”型,所述端板上设有多组成对设置的增强钢筋锚固孔,所述增强钢筋的两个端头穿过所述增强钢筋锚固孔。
6.作为本发明的进一步改进,所述端板在每对增强钢筋锚固孔之间设有钢筋凹槽,所述增强钢筋的两个端头穿过一对所述增强钢筋锚固孔后其根部嵌入所述钢筋凹槽并与所述端板的表面保持齐平或低于所述端板的表面。
7.作为本发明的进一步改进,所述增强钢筋的端头处设有螺纹并安装有配套的螺栓锚头。
8.作为本发明的进一步改进,所述端板为圆形,多组所述锚固组件绕所述中心定位孔周向排布。为了使端板受力均匀,多组所述锚固组件在所述端板上呈周向排布。
9.作为本发明的进一步改进,所述端板为方形,多组所述锚固组件在所述端板上呈方形排布。为了使端板受力均匀,述锚固组件应当保持绕所述中心定位孔均匀排布。
10.作为本发明的进一步改进,多组成对设置的所述增强钢筋锚固孔在所述端板呈周向排布,为了使增强钢筋受力保持一致,所述增强钢筋锚固孔应当绕所述中心定位孔周向均匀排布,任意一对所述增强钢筋锚固孔位于相邻的所述锚固组件之间。
11.作为本发明的进一步改进,多组成对设置的所述增强钢筋锚固孔在所述端板上呈方形排布,任意一对所述增强钢筋锚固孔位于相邻的所述锚固组件之间。
12.作为本发明的进一步改进,所述端板上设有中心通孔。当预制桩是空心桩时,所述端板上设置有中心通孔,将所述端板的形状限定为预制桩截面形状,当预制桩是实心桩时,则不用在端板设置中心通孔。
13.作为本发明的进一步改进,所述预应力筋锚固孔与所述螺纹孔的中心连线相对所述端板的中心呈放射状,所述预应力筋锚固孔与所述增强钢筋锚固孔位于同一半径的圆周上。
14.与现有技术相比,本发明的有益效果在于:通过“u”型的增强钢筋穿过增强钢筋锚固孔来代替传统的焊接增强钢筋的方式,施工操作效率更高也更简单,并且增强钢筋没有做任何截面的削弱,使端板处的受力更加均匀可靠。
附图说明
15.为了更清楚地说明本发明具体实施方式或现有技术中的技术方案,下面将对具体实施方式或现有技术描述中所需要使用的附图做简单的介绍,显而易见地,下面描述中的附图是本发明一些实施方式,对于本领域普通技术人员来讲,在不付出创造性劳动的前提下,还可以根据这些附图获得其他的附图。
16.图1是本发明预制桩用预应力钢筋锚固增强装置的第一实施例的端板立体图;图2是本发明预制桩用预应力钢筋锚固增强装置的第一实施例的装配示意图;图3是本发明预制桩用预应力钢筋锚固增强装置的第一实施例的装配示意图;图4是本发明预制桩用预应力钢筋锚固增强装置的第一实施例的局部剖视图;图5是本发明预制桩用预应力钢筋锚固增强装置的第一实施例的端板的局部剖视图;图6是本发明预制桩用预应力钢筋锚固增强装置的第一实施例的增强钢筋锚固孔位置处的剖视图;图7是本发明预制桩用预应力钢筋锚固增强装置的第一实施例的端板的局部放大图;图8是本发明预制桩用预应力钢筋锚固增强装置的第一实施例的端板设计草图;图9是本发明预制桩用预应力钢筋锚固增强装置的第二实施例的端板设计草图;图10是本发明预制桩用预应力钢筋锚固增强装置的第三实施例的端板设计草图;图11是本发明预制桩用预应力钢筋锚固增强装置的第四实施例的端板设计草图图12是本发明预制桩用预应力钢筋锚固增强装置的第五实施例的端板设计草图。
具体实施方式
17.以下将结合附图对本发明各实施例的技术方案进行清楚、完整的描述,显然,所描述的实施例仅仅是本发明的一部分实施例,而不是全部的实施例。基于本发明的实施例,本领域普通技术人员在没有做出创造性劳动的前提下所得到的所有其它实施例,都属于本发明所保护的范围。
18.下面通过具体的实施例并结合附图对本发明做进一步的详细描述。
19.第一实施例一种预制桩用预应力钢筋锚固增强装置,包括端板1和增强钢筋2,端板1上设有中心通孔3,端板1上还设有多组锚固组件4,锚固组件包括预应力筋锚固孔5、连接槽6、螺纹孔7(螺纹在附图中未示出),螺纹孔7的孔径与预应力钢筋8在钢筋镦头的直径相等,连接槽6宽度等于预应力钢筋8的直径,预应力筋锚固孔5的孔径应大于连接槽6的宽度并且小于螺纹孔的孔径,预应力筋锚固孔5内设有环形凸台9,将预应力筋锚固孔5沿端板1厚度分为外部大孔13和内部小孔14,如图5所示,外部大孔13孔径大于连接槽6的宽度并且小于预应力钢筋镦头直径,内部小孔14孔径等于连接槽6的宽度,连接槽6贯穿端板1并连接预应力筋锚固孔5和螺纹孔7。
20.端板1在每对增强钢筋锚固孔10之间设有钢筋凹槽11,增强钢筋2的两个端头穿过一组增强钢筋锚固孔10后其根部嵌入钢筋凹槽11并与端板1的表面保持齐平,这样就保证了增强钢筋2的根部不会凸出于端板1表面并且在浇筑过程中钢筋凹槽11对增强钢筋2起到固定其位置的作用。在钢筋凹槽11与增强钢筋锚固孔10之间有加工圆角,这样保证了增强钢筋2插入后与端板1完全贴合起来,如图6所示。
21.每根增强钢筋2的端头处设有螺纹并准备有配套的螺栓锚头12。
22.本实施例在使用时有如下步骤,第一步:将增强钢筋2的两个端头插入一对增强钢筋锚固孔10内并将螺栓锚头12旋拧固定在增强钢筋2的端头上;第二步:将端板1安装在制作好的含有预应力钢筋8的钢筋笼的两端,预应力钢筋8的钢筋镦头经螺纹孔7穿过端板1,再通过连接槽6滑入预应力筋锚固孔5内,预应力筋锚固孔5通过环形凸台9将钢筋镦头卡主,安装端板1时要使增强钢筋2的端头朝向钢筋笼内部;第三步:端板1安装完成后在螺纹孔7安装螺栓并连接张拉设备,在拉张设备施加预应力的过程中,预应力钢筋8通过环形凸台9将拉力传递至端板1;第四步:向钢筋笼浇筑混凝土,增强钢筋2及螺栓锚头12被混凝土包裹,待混凝土凝结后由于增强钢筋2的存在使端板1的抗拔力得到了提高。
23.在本实施例中预制桩结构为中空圆柱,因此端板1结构为圆形,中心通孔3为圆孔,锚固组件4和增强钢筋锚固孔10绕中心通孔3周向均匀排布,相邻的锚固组件4之间设有一对增强钢筋锚固孔10,如图8所示,为了提高增强钢筋2的受力均匀性,锚固组件4和增强钢筋锚固孔10被设置在相同的圆周上,在浇筑前利用钢丝将增强钢筋2和预应力钢筋8进行绑扎。
24.第二实施例本实施例与第一实施例的区别在于端板1上只有六组成对设置的增强钢筋锚固孔10,锚固组件4和增强钢筋锚固孔10绕中心通孔3周向均匀排布,相邻的两组增强钢筋锚固孔10之间有两组锚固组件4,如9图所示。
25.第三实施例
本实施例与第一实施例的区别在于锚固组件4上螺纹孔7与预应力筋锚固孔5的中心连线相对中心通孔3呈放射状排布,如图10所示,该实施例中锚固组件4的设置方式适用于预应力钢筋8数量较多按照第一实施例的排布方式导致预应力钢筋8之间的距离较小导致增强钢筋锚固孔10无法设置的情况,将锚固组件4扭转方向后增大了相邻锚固组件4之间的加工空间从而满足在端板1上加工增强钢筋锚固孔10,同时在加工增强钢筋锚固孔10时,将其与预应力筋锚固孔5加工在同一直径的圆上,不仅能改善端板1受力均匀性,还可以让预制桩桩身钢筋笼与增强钢筋进行焊接。
26.第四实施例本实施例与第一实施例的区别在于本实施例中预制桩结构为实心方桩,因此端板1结构为方形且没有中心通孔3,锚固组件4和增强钢筋锚固孔10在端板1上呈方形均匀排布,相邻的锚固组件4之间设有一对增强钢筋锚固孔10,如图11所示。
27.第五实施例本实施例与第四实施例的区别在于预制桩结构为中空方形柱,端板1为方形板,中心通孔3为圆孔,锚固组件4和增强钢筋锚固孔10绕中心通孔3呈方形排布,相邻的锚固组件4之间设有一对增强钢筋锚固孔10,如图12所示。
28.最后应说明的是:以上实施例仅用以说明本发明的技术方案,而非对其限制;尽管参照前述实施例对本发明进行了详细的说明,本领域的普通技术人员应当理解:其依然可以对前述实施例所记载的技术方案进行修改,或者对其中部分或者全部技术特征进行等同替换;而这些修改或者替换,并不使相应技术方案的本质脱离本发明实施例技术方案。