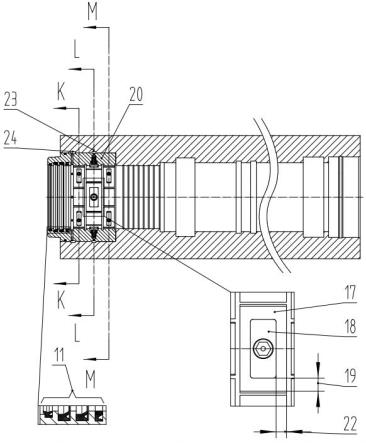
1.本实用新型涉及一种工程机械属具,特别是涉及一种静压悬浮活塞型液压破碎锤。
背景技术:2.液压破碎锤是一种将液压能转换为机械能的冲击机具,其中有两个基本运动元件——活塞和换向阀,两者相互反馈控制,即阀芯的往复运动控制着活塞换向,而活塞在每一个行程的始、终点又通过打开或关闭换向阀的控制油路实现阀芯的换向,如此循环工作。液压破碎锤的基本工作原理为:通过这种活塞和阀芯的反馈控制,实现活塞在液压或液压与气压力驱动下快速往复运动,并打击钎杆对外做功。
3.为了破碎石料、混凝土及其他建筑材料,液压破碎锤可附接到各种机器上,如挖掘机、反向铲或者其他类似机器。液压破碎锤安装到机器的臂上并连接到液压系统。液压系统中的高压流体供给至液压破碎锤以驱动与作业工具接触的活塞往复运动,并打击作业工具,完成破碎任务。
4.现有液压破碎锤锤芯(图1、图2)主要包括:氮气室1、活塞环2、活塞3、缸体4、钎杆座5、内套6、外套7、钎杆8、换向阀9、蓄能器10。回程运动开始(图1),高压油p通过油口a4进入前腔12,同时作用于换向阀9阀芯的下端,使阀芯稳定处于图(1)所示状态。此时前腔12接通高压油p,后腔13通过油口a1通回油t,活塞3在前腔12高压油p的驱动下,加速回程并压缩氮气室1中的氮气储存能量(如果氮气室1中不充气体,则为纯液压式液压锤),蓄能器10储油,当活塞3回程运动至前腔12和控制油口a3连通,高压油p到达阀芯的上端,此时阀芯上、下端都与高压油相通,由于设计中阀芯上端有效面积大于下端有效面积,阀芯在高压油作用下换向至图(2)状态,此时前、后腔都通高压油p,蓄能器10排油补充液压系统,活塞3在氮气压力(纯液压式液压锤除外)及油压的作用下,加速冲程,打击钎杆8,输出冲击能。当活塞3越过打击点,控制口a2和a3导通,并与回油t接通,换向阀9的阀芯上端泄压,下端油压作用下阀芯快速换向至图(1)状态,又恢复初始状态,活塞3开始回程,进入下一个打击循环,如此反复。在钎杆座5中,设有破碎岩石的钎杆8、起导向作用的内套6、外套7,同时内套6、外套7具有保护钎杆座5不被磨损的作用。
5.由于液压破碎锤使用过程中零件之间的磨损、间隙、零件本身的形位精度、工况等原因,使得活塞3和钎杆8的打击面不垂直于活塞3的轴线(影响:产生相对滑动)、打击点不在活塞3的中心(影响:产生偏转趋势),活塞3打击钎杆8后,必然产生径向冲击(侧向冲击),径向冲击力破坏活塞3和缸体4的配合面(拉缸)。由于活塞3和缸体4之间靠间隙密封,配合面破坏后,内泄漏增加,液压破碎锤不能正常工作;活塞3表面破坏后,则同轴安装的油封也将损坏,导致漏油。
6.杨襄璧,罗铭主编的书籍《液压破碎锤设计理论、计算方法与应用》,该书的第6页记载了拉缸问题。拉缸问题是人们一直渴望解决但始终未能获得成功的技术难题。
7.为解决拉缸问题,中国发明专利cn106703105b说明书公开了液压破碎锤活塞静压
支撑及润滑结构。该技术方案为:在缸体和活塞头部配合的区域周向等间隔设置4个油腔用于对活塞头部支承,液压油通过缸体内的油路进入油腔;在活塞最大径处(靠近尾部的一段)周向等间隔设置4个油腔用于对活塞最大径处支承,液压油通过活塞内部的轴向孔和径向孔进入油腔。存在的问题:1.在活塞往复运动的过程中,当活塞靠近头部的一段最大径将最大径处(靠近尾部的一段)的4个油腔的回油堵死(即将缸体内与a2口相通的环形油槽封闭),导致此阶段无支承。2.在活塞往复运动的过程中,当活塞最大径处(靠近尾部的一段)的4个油腔和缸体内与a2或a3口相通的环形油槽相通时,此阶段无支承。3.由于对活塞头部设置4个油腔支承、对活塞最大径设置4个油腔支承,每处4个油腔将对缸体产生4个方向的液压力,导致缸体变形,由于活塞和缸体之间靠间隙密封(配合间隙小),缸体的变形将导致活塞被抱死、损坏,即拉缸。如果想减小变形,必然增加缸体的结构尺寸、重量,则需要大吨位的主机与之相配,在不增加工作效率的情况下,增加主机吨位,将浪费资源。4.活塞上设置轴向油路、径向油路、油腔等,降低了活塞的机械强度,但是活塞往复运动打击钎杆,受到极大的冲击力,容易损坏。5.活塞上设置轴向油路、径向油路均属于细长孔,加工困难、效率低,且不便于清洗维护。
8.为解决拉缸问题,中国发明专利cn110307252b说明书公开了液压破碎锤活塞静压支承及润滑结构。该技术方案为:在缸体和活塞头部配合的区域周向等间隔设置4个油腔用于对活塞头部支承,液压油通过缸体内的油路进入油腔;在缸体的阀控回油环形槽和上腔(别名:后腔)之间周向等间隔设置4个油腔用于对活塞最大径处支承,液压油通过缸体内部的油路进入油腔。存在的问题:1.在活塞往复运动的过程中,当活塞靠近头部的一段最大径(前油槽)将阀控回油环形槽和上腔(别名:后腔)之间的4个油腔的回油堵死(即将缸体内与a2口相通的环形油槽封闭),导致此阶段无支承。2.在活塞往复运动的过程中,当阀控回油环形槽和上腔(别名:后腔)之间的4个油腔和活塞轴向卸荷槽、活塞环形卸荷槽相通时,此阶段无支承。3.由于对活塞头部设置4个油腔支承、对活塞最大径设置4个油腔支承,每处4个油腔将对缸体产生4个方向的液压力,导致缸体变形,由于活塞和缸体之间靠间隙密封(配合间隙小),缸体的变形将导致活塞被抱死、损坏,即拉缸。如果想减小变形,必然增加缸体的结构尺寸、重量,则需要大吨位的主机与之相配,在不增加工作效率的情况下,增加主机吨位,将浪费资源。4.阀控回油环形槽和上腔(别名:后腔)之间的4个油腔需要采用悬臂较长的刀具加工,效率低、精度差。5.对活塞支承的每个油腔均需要细长孔供油,加工困难、效率低,且不便于清洗维护。
技术实现要素:9.针对上述现有技术,本实用新型要解决的技术问题如下。
10.1.由于活塞打击钎杆后,产生的径向冲击(侧向冲击)破坏活塞3和缸体4的配合面(拉缸),受到冲击最严重的必然是靠近打击面的部分,因此需要重点防护,现有技术并未认识到这种导致拉缸的现象。
11.2.活塞往复运动的过程中,油腔不能对活塞全程支承的理论缺陷。
12.3.油腔的液压力导致缸体变形将活塞抱死的技术缺陷,抱死必然拉缸。
13.4.避免活塞因设置油腔、通油孔导致强度下降、加工困难的问题;避免在缸体内设置用于对活塞最大径处支承的油腔,该油腔加工困难、精度不能保证。
14.5.对活塞支承的每个油腔均需要细长孔供油,加工困难、效率低,且不便于清洗维护。
15.为解决上述技术问题,本实用新型提供一种静压悬浮活塞型液压破碎锤。包括:活塞、缸体、钎杆座、内套、外套及钎杆。活塞在缸体内往复运动,打击钎杆;钎杆座中设有破碎岩石的钎杆、起导向作用的内套、外套,同时内套、外套具有保护钎杆座不被磨损的作用。所述缸体和活塞头部相配合的区域(前腔和主密封之间)设置大于或等于两圈、每圈均布大于两个静压悬浮腔,用于对活塞支承。通过静压悬浮支承将活塞浮在缸体中,保证活塞在一定负载、任何速度(包括静止)时,活塞和缸体的配合面均被液压油分隔开,避免接触,避免拉伤。静压悬浮支承的原理:高压油经节流阀进入静压悬浮腔(简称:油腔),当活塞不受载荷时(如:忽略自重),则各油腔的油压相同,保持平衡,活塞在缸体孔的中央。这时各油腔封油面和活塞之间的间隙相同(均为h);如果活塞上施加径向载荷f(如:考虑活塞的自重),活塞将产生偏心量e。这时活塞和缸体在载荷方向(如:重力方向)的间隙减小为h-e,在载荷反方向一侧的间隙增加为h+e,由于油流向间隙小的地方阻力大,流量减小,因而流过节流阀的压降减小,各个静压悬浮腔的供油压力是相同的(一定的),所以该油腔的压力将升高;反之,在载荷反方向一侧由于油流经间隙大的地方阻力小,流量增大,因此流经节流阀的压降增大,所以该油腔的压力将降低。这种压差变化就可以平衡外载荷。如:油腔径向有效承载面积为a,
△
p为两油腔的压力差,则f=
△
p
×
a。随着偏心距e的增大,
△
p将进一步增大,将活塞3悬浮在缸体4中。
16.有益效果:在缸体和活塞头部相配合的区域(前腔和主密封之间)设置大于或等于两圈、每圈均布大于两个静压悬浮腔,用于对活塞支承。既重点保护了受冲击最严重的配合面(缸体和活塞头部的配合面),又解决了现有技术油腔不能对活塞全程支承的理论缺陷。避免了活塞因设置油腔、通油孔导致强度下降、加工困难的问题。避免了在缸体内设置用于对活塞最大径处支承的油腔,该油腔加工困难、精度不能保证。
17.作为本实用新型的进一步改进,相邻两圈静压悬浮腔在垂直于活塞轴线的平面投影交错分布,且相邻投影之间的间隔或重合量相同。
18.有益效果:由于在缸体和活塞头部相配合的区域(前腔和主密封之间)设置大于或等于两圈、每圈均布大于两个静压悬浮腔,且相邻两圈静压悬浮腔在垂直于活塞轴线的平面投影交错分布,且相邻投影之间的间隔或重合量相同。能避免油腔的液压力在缸体内孔周向分布不均,导致缸体严重变形将活塞抱死的技术缺陷。
19.作为本实用新型的进一步改进,相邻两圈静压悬浮腔的周向封油面在垂直于活塞轴线的平面投影重合或部分重合。
20.有益效果:当高压油通过静压悬浮腔的封油面,将出现压力递减的现象,采用本技术方案所述的布局,进一步限定相邻两圈静压悬浮腔在垂直于活塞轴线的平面投影重合的量,使得全部静压悬浮腔所受到的液压力在垂直于活塞轴线的平面内的合力大小基本相同、方向沿缸体内孔径向分布一周,即缸体在垂直于活塞轴线的平面内所受到的液压力大小基本相同,避免了液压力将缸体和活塞配合的内孔压成非圆孔。
21.作为本实用新型的进一步改进,静压悬浮腔设置在衬套内腔中,衬套同轴安装于活塞上,且安装于缸体内。
22.有益效果:避免加工静压悬浮腔的时候,将整个缸体安装在机床上,采用较小的机
床即可对设置在衬套内的静压悬浮腔进行加工,降低了对机床加工范围、刚度的要求,进而降低投资,减少能耗;避免了缸体中为每个油腔通液压油而设置的细长孔,提高了加工效率、便于清洗维护。
23.作为本实用新型的进一步改进,在衬套远离缸体的一端设置主密封槽、径向设置用于安装节流阀的螺纹孔;衬套和缸体之间的配合为过盈配合,过盈量为0.005mm—0.05mm;静压悬浮腔的封油面和活塞之间的间隙大于活塞和缸体之间配合的最小间隙;衬套外圆设置用于静压悬浮腔进油及回油的环形油路。
24.有益效果:将主密封槽和静压悬浮腔同时设置在衬套上,有利于增加衬套的结构尺寸,进而增加刚度;在衬套上安装节流阀,可以缩短节流阀到静压悬浮腔的距离,减少液压油的压缩(液压油一般认为不可压缩,但其中存在空气,在这里认为具有压缩性),增加承载力;静压悬浮腔的封油面和活塞之间的间隙大于活塞和缸体之间配合的最小间隙,这样的设计使液压破碎锤在超负荷工作或液压油脏的情况下,优先保护封油面;衬套和缸体之间的过盈量为0.005mm—0.05mm,避免两者之间的周向转动,同时隔断衬套外圆的高、低压油路。
25.作为本实用新型的进一步改进,在前腔和主密封之间设置两或三圈、每圈均布三或四个静压悬浮腔。有益效果:受液压破碎锤工作原理及结构的限制,采用本方案可以占用小的结构空间,对活塞实现静压悬浮支承。
26.作为本实用新型的进一步改进,活塞和钎杆座接触面所在的平面垂直于活塞的轴线。有益效果:避免活塞接触到钎杆座产生径向力损坏活塞和缸体配合面的现象。
附图说明
27.图1 现有液压破碎锤原理图。
28.图2 现有液压破碎锤原理图。
29.图3 液压破碎锤活塞主视图。
30.图4 本实用新型实施例一的缸体结构图。
31.图5 实施例一的缸体剖视图a-a。
32.图6 实施例一的缸体剖视图b-b。
33.图7 实施例一的衬套主视图及剖视图c-c。
34.图8 本实用新型实施例二的缸体结构图。
35.图9 实施例二的缸体剖视图d-d。
36.图10 实施例二的缸体剖视图e-e。
37.图11 实施例二的衬套主视图及剖视图f-f。
38.图12 本实用新型实施例三的缸体结构图。
39.图13 实施例三的缸体剖视图g-g。
40.图14 实施例三的缸体剖视图h-h。
41.图15 实施例三的缸体剖视图i-i。
42.图16 实施例三的衬套主视图及剖视图j-j。
43.图17 本实用新型实施例四的缸体结构图。
44.图18 实施例四的缸体剖视图k-k。
45.图19 实施例四的缸体剖视图l-l。
46.图20 实施例四的缸体剖视图m-m。
47.图21 实施例四的衬套主视图及剖视图n-n。
48.图22 活塞和钎杆座接触面结构图。
49.附图标记:1氮气室
ꢀꢀ
2活塞环
ꢀꢀ
3活塞
ꢀꢀ
4缸体
ꢀꢀ
5钎杆座
ꢀꢀ
6内套
ꢀꢀ
7外套
ꢀꢀ
8钎杆
ꢀꢀ
9换向阀
ꢀꢀ
10蓄能器
ꢀꢀ
11主密封
ꢀꢀ
12前腔
ꢀꢀ
13后腔
ꢀꢀ
14头部
ꢀꢀ
15最大径
ꢀꢀ
16尾部
ꢀꢀ
17封油面
ꢀꢀ
18静压悬浮腔
ꢀꢀ
19周向封油面
ꢀꢀ
20衬套
ꢀꢀ
21节流阀
ꢀꢀ
22轴向封油面
ꢀꢀ
23进油环形油路
ꢀꢀ
24回油环形油路。
具体实施方式
50.下面结合附图对本实用新型的具体实施方式作进一步详细的说明。
51.实施例一。
52.本实施例主要包括:活塞3和缸体4。活塞3在缸体4内往复运动。在缸体4和活塞3头部14相配合的区域(前腔12和主密封11之间)设置两圈、每圈均布三个静压悬浮腔18,用于对活塞3支承。
53.实施例二。
54.本实施例主要包括:活塞3和缸体4。活塞3在缸体4内往复运动。在缸体4和活塞3头部14相配合的区域(前腔12和主密封11之间)设置两圈、每圈均布四个静压悬浮腔18,用于对活塞3支承。
55.实施例三。
56.本实施例主要包括:活塞3和缸体4。活塞3在缸体4内往复运动。在缸体4和活塞3头部14相配合的区域(前腔12和主密封11之间)设置三圈、每圈均布三个静压悬浮腔18,用于对活塞3支承。
57.实施例四。
58.本实施例主要包括:活塞3和缸体4。活塞3在缸体4内往复运动。在缸体4和活塞3头部14相配合的区域(前腔12和主密封11之间)设置三圈、每圈均布四个静压悬浮腔18,用于对活塞3支承。
59.对于实施例一、实施例二、实施例三、实施例四可以进一步改进,优选的实施方式阐述如下。
60.优选的,相邻两圈静压悬浮腔18在垂直于活塞3轴线的平面投影交错分布,且相邻投影之间的间隔或重合量相同。
61.优选的,相邻两圈静压悬浮腔18的周向封油面19在垂直于活塞3轴线的平面投影重合或部分重合。
62.优选的,静压悬浮腔18设置在衬套20内腔中,衬套20同轴安装于活塞3上,且安装于缸体4内。
63.优选的,在衬套20远离缸体4的一端设置主密封11的安装槽、径向设置用于安装节流阀21的螺纹孔;衬套20和缸体4之间的配合为过盈配合,过盈量为0.005mm—0.05mm;静压悬浮腔18的封油面17(包括:周向封油面19和轴向封油面22)和活塞3之间的间隙大于活塞3和缸体4之间配合的最小间隙;衬套20外圆设置用于静压悬浮腔18进油环形油路23及回油
环形油路24;衬套20上设有轴向孔用于静压悬浮腔18供油。
64.优选的,活塞3和钎杆座5接触面所在的平面垂直于活塞3的轴线。
65.本实用新型并不局限于上述实施方式,基于本实用新型中的实施例,本领域普通技术人员在没有经过创造性劳动而获得的所有其他实施方式,都属于本实用新型的保护范围。