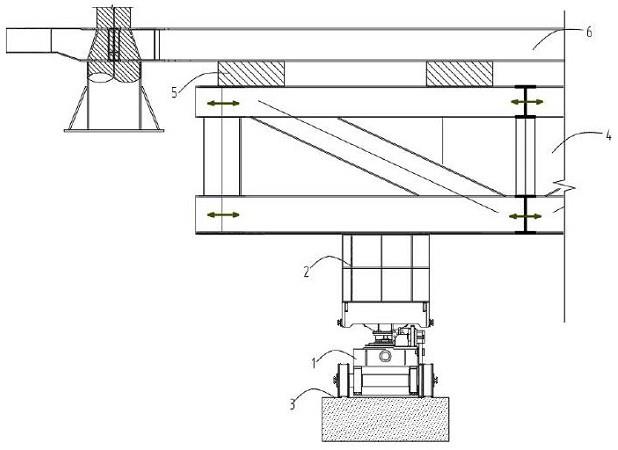
1.本发明属于风力发电技术领域,具体涉及海洋升压站平移接载系统及其平移接载方法。
背景技术:2.风力发电是可再生能源领域中最成熟、最具规模开发条件和商业化发展前景的发电方式之一,且可利用的风能在全球范围内分布广泛、储量巨大;同时,随着风电相关技术不断成熟、设备不断升级,全球风力发电行业高速发展,国内风电更是火爆,升压站是风力发电核心部件,单个重量2800~4000吨不等,如何把这些“巨无霸”转移到船上是整个运输链中至关重要的一个环节。目前采用常规的浮吊进行吊装不仅存在着费用高的问题,例如5000吨浮吊单次吊装费用早已超过1000万。而且由于风电行业的火爆,大型浮吊的主要工作用于升压站的海上安装,导致难以保证码头吊装发运档期,同时如果采用吊装发运就要求需要邻近码头建造升压站,这样导致很难进行多个升压站同时建造的工作因此,目前通过吊装发运的方式不能满足现有的升压站平移接载的需求,需要研发一种新的海洋升压站平移接载系统及其平移接载方法来解决现有的问题。
技术实现要素:3.本发明的目的在于提供一种海洋升压站平移接载系统及其平移接载方法,以解决吊装发运方式成本高的问题。
4.为实现上述目的,本发明提供如下技术方案:一种海洋升压站平移接载系统,包括:托架,所述托架用于支承升压站;轨道式液压小车,所述轨道式液压小车用于平移托架;所述轨道式液压小车包括:主动小车,所述主动小车用于承载托架并驱动其移动;从动小车,所述从动小车用于承载托架;轨道,所述轨道与所述轨道式液压小车匹配,用于承载并控制轨道式液压小车的移动方向;所述轨道包括:前沿轨道、接载轨道以及轨道连接梁;所述轨道连接梁用于在前沿轨道与接载轨道之间连接过载;控制系统,所述控制系统与轨道式液压小车电气连接,用于对采集的数据进行分析处理后,将控制指令发送给轨道式液压小车。
5.优选的,所述托架包括:顶连接梁,所述顶连接梁用于支撑升压站;支柱,所述支柱一端与顶连接梁固定连接;底连接梁,所述底连接梁与支柱另一端相连接;
筋板,所述筋板固定于所述顶连接梁和/或所述底连接梁。
6.优选的,所述顶连接梁与所述底连接梁相互连接后构成框架结构,在框架结构内部设若干个支柱,所述支柱包括竖向支柱和斜拉支柱,所述竖向支柱与顶连接梁节点处以及竖向支柱与所述底连接梁节点处固定设置斜拉支柱,两个所述斜拉支柱与竖向支柱的连接后形成“个”字型;且两个所述斜拉支柱之间的顶连接梁下端均设置有长方形的筋板,长方形的筋板的厚度为整个顶连接梁厚度的1/2,在顶连接梁与所述底连接梁之间还设置有l型筋板,所述l型筋板的上端面与顶连接梁的下端面固定,其下端面与所述底连接梁相固定,在两个l型筋板的两侧分别设置有长方形的筋板,其两端分别与顶连接梁与所述底连接梁相固定。
7.优选的,所述主动小车包括:用于装载托架的主动车装载板;装配于主动车装载板下方用于驱动主动车装载板的第一驱动行走单元;装配于主动车装载板下方用于驱动主动车装载板的第二驱动行走单元;所述第一驱动行走单元包括主动车身,装配于主动车身的四个车轮、装配于主动车身用于使主动车装载板上升或者下降的主动车液压装置、与车轮相连接的驱动源、与主动车液压装置以及驱动源相连接的小车控制单元;所述第一驱动行走单元和第二驱动行走单元同一直线装配于主动车装载板下方;前后车轮之间间距为1250mm。
8.其中,所述第一驱动行走单元与第二驱动行走单元结构相同。
9.优选的,所述从动小车包括:用于装载托架的从动车装载板;装配于从动车装载板下方用于平移的第一行走单元和第二行走单元;所述第一行走单元包括从动车车身,装配于从动车车身的四个车轮、装置于车身上用于使从动车装载板上升或者下降的从动车液压装置、与从动车液压装置相连接的小车控制单元;所述第一行走单元和第二行走单元同一直线装配于从动车装载板下方。
10.优选的,所述小车控制单元还与测距传感器、雷达扫描传感器、激光传感器相连接;所述测距传感器设置于主动小车和从动小车的前后的端面上,用于检测前车间距和后车间距,并将间距数据发送给控制系统,所述主动小车的前端安装有雷达扫描传感器,所述雷达扫描传感器和高精度摄像头对轨道及路面进行扫描及图像采集,并将扫描数据发送给控制系统,所述控制系统对扫描数据进行分析,判断轨道的状态,控制系统对数据进行分析,若轨道偏离时,发送停止指令给主动小车,若轨道的结构形变超过设定值时,发送降低车速的指令给主动小车。
11.优选的,所述主动小车的小车控制单元和从动小车的小车控制单元实时采集从动车液压装置和主动车液压装置的压力数据,并发送给控制系统,控制系统对所有的压力数据进行推测,通过对轨道状态对比控制主动小车驱动源的动力输出。
12.本发明另提供一种基于海洋升压站平移接载系统的平移接载方法,包括以下步骤:步骤1、分析计算托架塑性变形结构,计算轨道连接梁结构强度,确定托架、轨道连接梁结构强度、轨道连接梁材料以及受力点;预测施工区域内的规则半日潮流的最大流速,
确定施工工期;步骤2、船舶通过轨道连接梁与码头前平台的前沿轨道对接,接载轨道调压至与前沿轨道对齐;步骤3、控制系统发送控制指令给轨道式液压小车,轨道式液压小车的小车控制单元发送指令给主动车液压装置和从动车液压装置,主动车液压装置和从动车液压装置同时举升顶触托架,所有轨道式液压小车同步顶举,将外板脱离坞墩,使主动车液压装置和从动车液压装置顶举托架至250mm 高,并拆除坞墩,把定航向;步骤4、控制系统发送驱动指令给主动小车,主动小车的小车控制单元发送驱动信号给驱动源,驱动源带动主动小车移动使升压站开始平移,移动过程中测距传感器、雷达扫描传感器、激光传感器不断检测轨道式液压小车状态,直至将升压站平移至船舶指定位置;步骤5、控制系统发送指令给轨道式液压小车,小车控制单元发送同步下降指令给主动车液压装置和从动车液压装置获取坞墩受力数据及船体精度数据,若船体已全部落墩,则主动车液压装置和从动车液压装置继续下降,托架落地,主动车液压装置和从动车液压装置复位,点检坞墩,敲实后轨道式液压小车熄火;步骤6、轨道式液压小车卸载后托架坐落于甲板面,对升压站进行绑扎加固,拖轮将船舶拖航至施工现场。
13.优选的,所述分析计算托架塑性变形结构的方法包括建模分析时,使用双线性随动强化模型,设塑性斜率为弹性模量的 0.01 倍,即e
t
=0.01e,其中,e
t
表示塑性斜率,e表示弹性斜率,并设置1.2 倍的重量放大系数,使重量平均施加19 个传力点,最大mises 等效应力为 215mpa;所述计算轨道连接梁结构强度的方法包括:在有限元模型建立xyz右手坐标系统,x轴沿连接梁长度方向,向前为正;y轴沿连接梁宽度方向,指向左舷为正;z轴则沿连接梁高度方向,向上为正;设置轨道式液压小车间相距300mm,设置轨道式液压小车布置其最小间距6000mm,计算载荷下轨道连接梁结构的单元相当应力,,其中,为单元x方向正应力,单位:n/mm2;为单元y向正应力,单位:n/mm2;为单元剪应力,单位:n/mm2。
14.本发明的技术效果和优点:该海洋升压站平移接载系统及其平移接载方法,实现多个升压站同时建造,且仅需配备一个发运泊位;同时发运节点更加灵活无需受制于大型浮吊档期,减少了码头泊位需求,提升码头发运效率;摆脱发运对大型浮吊档期需求限制;降低单台升压站发运成本;通过轨道液压小车将建好的升压站平移上船,便于多个升压站同时建造,350米的轨道长度可满足5个400mw升压站同时建造,并预留一个待发运区;仅通过一个发运泊位就能有效完成多个升压站的发运工作;单个轨道液压小车的承载力强,7.28 平方米的接触面积可承载450吨;而且装载速度快,最大负载行走速度不低于3米/分钟,若运输船压载能力足够可以控制在25分钟内完成整个装船过程,可灵活调整发运节点,实现多座升压站同时建造;通过分析计算托架塑性变形结构,计算轨道连接梁结构强度,确定托架、轨道连接梁结构强度、轨道连接梁材料以及受力点;预测施工区域内的规则半日潮流的最大流速,确保平移过程中平稳,减少因结构或者强度问题发生的侧翻事故,通过测距传感器、雷达扫描传感器、激光传感器不断的地面和轨道的实时监控,减少平移过程中的实
发状况,保证移动的速度减少升压站的晃动。
附图说明
15.图1为本发明的轨道式液压小车、增高垫、托架以及升压站连接示意图;图2为本发明装载时的正视图;图3为本发明主动小车的正视图;图4为本发明主动小车的左视图;图5为本发明托架俯视图;图6为本发明装载时的左视图;图7为本发明流程图。
16.图中:1、轨道式液压小车;2、增高垫;3、轨道;4、托架;5、垫木;6、升压站;11、主动车身;12、车轮;13、主动车装载板;14、主动车液压装置;41、顶连接梁;42、底连接梁;43、支柱;44、筋板。
具体实施方式
17.下面将结合本发明实施例中的附图,对本发明实施例中的技术方案进行清楚、完整地描述,显然,所描述的实施例仅仅是本发明一部分实施例,而不是全部的实施例。基于本发明中的实施例,本领域普通技术人员在没有做出创造性劳动前提下所获得的所有其他实施例,都属于本发明保护的范围。
18.本发明提供了如图1中所示的一种海洋升压站平移接载系统,本实施例中,220kv 海上升压站结构共有3 部分组成:桩基础、导管架和上部平台,升压站平台桩基础采用直径2200mm、壁厚36~50mm 的钢管桩,整个平台共布置4 根管桩,导管架采用4 腿导管架型式,导管架顶标高约10.5m,底标高-6.3m。主导管采用φ2500钢管,成矩形布置,在标高9.0m,-4.5m 处设水平拉筋φ800/1200 钢管及斜拉筋φ1200钢管,导管架局部节点用钢材dh36-z25 加强。导管架上设靠船构件、登船平台、j型管等附属构件,升压站将风电场8 回集电线路汇集后升压送出,并作为风电场的现场控制中心,同时也作为风电场的应急避难场所;本发明系统包括:托架4,所述托架4用于支承升压站6;所述托架4如图2、图5、图6包括:顶连接梁41,所述顶连接梁41用于支撑升压站6;支柱43,所述支柱43一端与顶连接梁41固定连接;底连接梁42,所述底连接梁42与支柱43另一端相连接;筋板44,所述筋板44固定于所述顶连接梁41和/或所述底连接梁42;所述顶连接梁41与所述底连接梁42相互连接后构成框架结构,在框架结构内部设若干个支柱43,所述支柱43包括竖向支柱和斜拉支柱,所述竖向支柱与顶连接梁41节点处以及竖向支柱与所述底连接梁42节点处固定设置两个斜拉支柱,两个所述斜拉支柱与竖向支柱的连接后形成“个”字型;且两个所述斜拉支柱之间的顶连接梁41下端均设置有长方形的筋板44,长方形的筋板44的厚度为整个顶连接梁41厚度的1/2,在顶连接梁41与所述底连接梁42之间还设置有l型筋板,所述l型筋板的上端面与顶连接梁41的下端面固定,其下端面与所述底连接梁42相固定,在两个l型筋板的两侧分别设置有长方形的筋板44,其两端分别与顶连接梁41与所述
底连接梁42相固定。
19.轨道式液压小车1,所述轨道式液压小车1用于平移托架4;轨道式液压小车1的外形尺寸5600mm*1300mm*1400mm(+500),顶举力450t/台,轮压39t,总举力4500t;本实施例中,根据实际的需要,在轨道式液压小车1与托架4之间设置增高垫2,同时在托架4与升压站6之间设置垫木5;所述轨道式液压小车1如图3、图4包括:主动小车,所述主动小车用于承载托架4并驱动其移动;所述主动小车包括:用于装载托架4的主动车装载板13;装配于主动车装载板13下方用于驱动主动车装载板13的第一驱动行走单元;装配于主动车装载板13下方用于驱动主动车装载板13的第二驱动行走单元;所述第一驱动行走单元包括主动车身11,装配于主动车身11的四个车轮12、装配于主动车身11用于使主动车装载板13上升或者下降的主动车液压装置14、与车轮12相连接的驱动源、与主动车液压装置14以及驱动源相连接的小车控制单元;所述第一驱动行走单元和第二驱动行走单元同一直线装配于主动车装载板13下方;前后车轮12之间间距为1250mm。
20.其中,所述第一驱动行走单元与第二驱动行走单元结构相同。
21.从动小车,所述从动小车用于承载托架4;本实施例中,从动小车与主动小车在结构的区别为,从动小车未安装驱动源,所述从动小车包括:用于装载托架4的从动车装载板;装配于从动车装载板下方用于平移的第一行走单元和第二行走单元;所述第一行走单元包括从动车车身,装配于从动车车身的四个车轮12、装置于车身上用于使从动车装载板上升或者下降的从动车液压装置、与从动车液压装置相连接的小车控制单元;所述第一行走单元和第二行走单元同一直线装配于从动车装载板下方;轨道3,所述轨道3与所述轨道式液压小车1匹配,用于承载并控制轨道式液压小车1的移动方向;所述轨道3包括:前沿轨道、接载轨道以及轨道连接梁;所述轨道连接梁用于在前沿轨道与接载轨道之间链接过载;控制系统,所述控制系统与轨道式液压小车1电气连接,用于对采集的数据进行分析处理后,将控制指令发送给轨道式液压小车1;所述小车控制单元还与测距传感器相连接、雷达扫描传感器、激光传感器相连接;所述测距传感器设置于主动小车和从动小车的前后的端面上,用于检测前车间距和后车间距,并将间距数据发送给控制系统,所述主动小车的前端还安装有雷达扫描传感器,所述雷达扫描传感器和高精度摄像头对轨道3及路面进行扫描及图像采集,并将扫描数据发送给控制系统,所述控制系统对扫描数据进行分析,判断轨道3的状态,控制系统对数据进行分析,若轨道3偏离时,发送停止指令给主动小车,若轨道3的结构形变超过设定值时,发送降低车速的指令给主动小车。
22.所述主动小车的小车控制单元和从动小车的小车控制单元实时采集从动车液压装置和主动车液压装置14的压力数据,并发送给控制系统,控制系统对所有的压力数据进行推测,通过对轨道3状态对比控制主动小车驱动源的动力输出。
23.本发明另提供一种基于海洋升压站平移接载系统的平移接载方法,如图7所示,包括以下步骤:步骤1、分析计算托架4塑性变形结构,计算轨道连接梁结构强度,确定托架4、轨道连接梁结构强度、轨道连接梁材料以及受力点;预测施工区域内的规则半日潮流的最大流速,确定施工工期;所述托架4塑性变形结构的计算方法包括建模分析时,使用双线性随动强化模型,设塑性斜率为弹性模量的 0.01 倍,即e
t
=0.01e,其中,e
t
表示塑性斜率,e表示弹性斜率,并设置1.2 倍的重量放大系数,使重量平均施加19 个传力点,最大mises 等效应力为 215mpa;本实施例中,本计算采用大型通用有限元分析软件ansys建模分析,本计算考虑上部组块总重量2600 吨,并考虑 1.2 倍的重量放大系数,上部组块重量平均施加至的 19 个传力点上,在所示托架4固定点处仅约束各点的三个平动自由度并释放三个弯曲自由度;强度计算中同时考虑了托架4自身的重力;可见最大位移15mm,位移托架4左右两翼的跨中点,整体变形量很小;三个平动自由度并释放三个弯曲自由度;强度计算中同时考虑了托架4自身的重力。
24.所述轨道连接梁结构分析方法包括:在有限元模型建立xyz右手坐标系统,x轴沿连接梁长度方向,向前为正;y轴沿连接梁宽度方向,指向左舷为正;z轴则沿连接梁高度方向,向上为正;设置轨道式液压小车1间相距300mm,设置轨道式液压小车1布置其最小间距6000mm,计算载荷下轨道连接梁结构的单元相当应力,,其中,为单元x方向正应力,单位:n/mm2;为单元y向正应力,单位:n/mm2;为单元剪应力,单位:n/mm2。
25.步骤2、船舶通过轨道连接梁与码头前平台的前沿轨道对接,接载轨道调压至与前沿轨道对齐;船舶为汉拿山总长189.60m,船长172.83m,满载水线长172.83m,船宽47.0m,型深23m,空载吃水1.549m,满载吃水3.9m,满载排水量32159.9t,空载吃水12423.43t。
26.步骤3、控制系统发送控制指令给轨道式液压小车1,轨道式液压小车1的小车控制单元发送指令给主动车液压装置14和从动车液压装置,主动车液压装置(14)和从动车液压装置同时举升顶触托架4,所有轨道式液压小车1同步顶举,将外板脱离坞墩,使主动车液压装置14和从动车液压装置顶举托架4至250mm 高,并拆除线型坞墩,把定航向;步骤4、控制系统发送驱动指令给主动小车,主动小车的小车控制单元发送驱动信号给驱动源,驱动源带动主动小车移动使升压站6开始平移,移动过程中测距传感器、雷达扫描传感器、激光传感器不断检测轨道式液压小车1状态,直至将升压站6平移至船舶指定位置;步骤5、控制系统发送指令给轨道式液压小车1,小车控制单元发送同步下降指令给主动车液压装置14和从动车液压装置,获取坞墩受力数据及船体精度数据,若船体已全部落墩,则主动车液压装置14和从动车液压装置继续下降,托架4落地,主动车液压装置14和从动车液压装置复位,点检坞墩,敲实后轨道式液压小车(1)熄火;步骤6、轨道式液压小车1卸载后托架4坐落于甲板面,对升压站6进行绑扎加固,待上部组块全部加固完成,确保平稳高效运输,根据航道条件、水深情况,充分利用船机资源,
结合拖轮,采取吊拖及绑拖方式将升压站组块安全平稳托运至安装位置;从制造地码头出发,采用吊拖的方式,沿长江而下至出海口,再沿黄海北上,途中航行基本保障在10m及20m航道水深内,直至施工现场附近。
27.该海洋升压站平移接载系统及其平移接载方法,实现多个升压站同时建造,且仅需配备一个发运泊位;同时发运节点更加灵活无需受制于大型浮吊档期,减少了码头泊位需求,提升码头发运效率;摆脱发运对大型浮吊档期需求限制;降低单台升压站发运成本;通过轨道液压小车将建好的升压站平移上船,便于多个升压站同时建造,350m的轨道长度可满足5个400mw升压站同时建造,并预留一个待发运区;仅通过一个发运泊位就能有效完成多个升压站的发运工作;单个轨道液压小车的承载力强,7.28 平方米的接触面积可承载450吨;而且装载速度快,最大负载行走速度不低于3米/分钟,若运输船压载能力足够可以控制在25分钟内完成整个装船过程,可灵活调整发运节点,实现多座升压站同时建造;通过分析计算托架塑性变形结构,计算轨道连接梁结构强度,确定托架、轨道连接梁结构强度、轨道连接梁材料以及受力点;预测施工区域内的规则半日潮流的最大流速,确保平移过程中平稳,减少因结构或者强度问题发生的侧翻事故,通过测距传感器、雷达扫描传感器、激光传感器不断的地面和轨道的实时监控,减少平移过程中的实发状况,保证移动的速度减少升压站的晃动。
28.最后应说明的是:以上所述仅为本发明的优选实施例而已,并不用于限制本发明,尽管参照前述实施例对本发明进行了详细的说明,对于本领域的技术人员来说,其依然可以对前述各实施例所记载的技术方案进行修改,或者对其中部分技术特征进行等同替换,凡在本发明的精神和原则之内,所作的任何修改、等同替换、改进等,均应包含在本发明的保护范围之内。