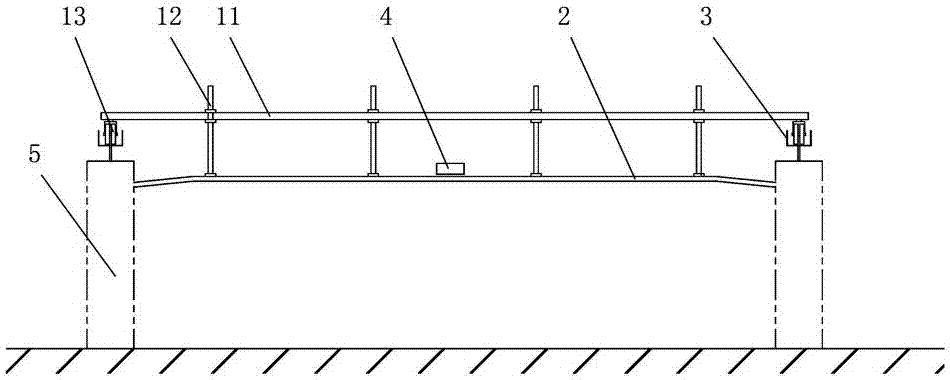
本发明涉及板式无砟轨道施工技术,尤其涉及CRTSⅢ型板式无砟轨道底座板施工方法。
背景技术:CRTSⅢ型板无砟轨道由钢轨、弹性有挡肩扣件、预制轨道板、自密实混凝土填充层、限位凹槽、中间隔离层(土工布)和钢筋混凝土底座板组成,具有性能稳定、耐久性好、使用寿命长等特点。CRTSⅢ型板式无砟轨道底座板作为轨道板与梁面之间的承重层和滑动层,顶面标高、平整度控制要求高,精度难以保证。
技术实现要素:本发明要解决的技术问题是克服现有技术的不足,提供一种适用性强、利用率高、操作方便、可提高作业效率和质量、减少人工作业强度的CRTSⅢ型板式无砟轨道底座板施工方法。为解决上述技术问题,本发明采用以下技术方案:一种CRTSⅢ型板式无砟轨道底座板施工方法,包括以下步骤:S1:施工准备:完成梁面凿毛检查及验收,组织材料、设备进场,测量底座板的四个角点并放样,记录放样点高程,用墨线弹出四个角点之间的角点连线;S2:钢筋安装:钢筋网片分两层铺设,先根据角点连线铺设底层钢筋网片,再在梁面预埋的连接套筒中安装L形连接钢筋,完成后铺设顶层钢筋网片,并通过L形连接钢筋支撑固定,用U形钢筋连接上下层钢筋网片形成钢筋骨架,U型形筋底部与钢筋网片主筋端头对齐绑扎;S3:模板安装:先在梁面弹设好底座板侧模板的安装定位线,从梁面的跨中位置向两端头拼装侧模板,按照安装定位线将侧模板就位并加固,侧模板安装后,安装固定伸缩缝模板;再用定位架安装限位凹槽模板,先将定位架安装在底座板侧模板顶部,再将限位凹槽模板安装在定位架的横梁上,将限位凹槽模板与底座板钢筋网片焊接固定,再撤除定位架,并在模板内侧标示底座板顶面标高线;S4:整平工装安装:沿侧模板顶部安装整平工装的行走轨道,将整平工装的行走机构置入行走轨道,并使连接于行走机构下方的刮尺置于底座板的两侧模板之间,调整刮尺底部标高,使其满足底座板顶面标高要求;S5:混凝土浇筑并整平:先对梁面洒水润湿,再开始浇筑、振捣混凝土,混凝土振捣密实后,两人在底座板两侧同步推进整平工装进行底座板顶面整平提浆,反复整平直至刮尺底部混凝土充实为止;S6:拆模:混凝土初凝前,拆除限位凹槽模板和伸缩缝模板,混凝土终凝前,进行底座板混凝土面压光处理,消除干缩裂纹、砂眼、气泡,混凝土强度达到2.5Mpa以上后,拆除底座板的两侧模板。作为上述技术方案的进一步改进:在执行步骤S2时,梁面预埋的连接套筒如有破损、缺失或位置偏差较大时,进行钻孔植筋处理,植筋深度不少于200mm。曲线地段的U形钢筋加工时,先绘制U形钢筋高度变化斜线,确定每孔梁U形钢筋高度,绑扎时根据每孔梁对应的U形筋高度,测量准确后将U形钢筋绑扎到对应位置。在执行步骤S3时,侧模板采用组合拼装钢模,直线段施工采用单块钢模,曲线段施工时,将两块钢模上下叠加并采用螺栓连接,钢模与梁面之间设置调节螺杆,通过调整调节螺杆,使侧模板顶面标高满足底座板混凝土浇筑要求。单块钢模施工时,在钢模外侧梁面钻孔打入钢筋头,楔入木楔固定模板;两块钢模上下叠加拼装施工时,于钢模机械连接处通过法兰调节螺杆进行模板调整与加固,保证侧模板垂直度及稳定性。在执行步骤S5时,沿梁体纵向从一端向另一端推进浇筑,一次成型;或从限位凹槽处从凹槽中间向周围浇筑,挤出浮浆;或从曲线段的低侧向高侧浇筑;振捣时,振动棒与各模板保持5cm-10cm距离。整平时,专人跟进整平工装并观察刮尺底部混凝土情况,及时铲除多余混凝土并对空洞处补料,刮尺收面后人工收面,完成后用5m靠尺检查平整度,不合格处进行二次修补。在执行步骤S6时,拆除限位凹槽模板和伸缩缝模板后,对限位凹槽进行抹光并检查几何尺寸,不合格的进行修复;检查底座板间错台情况、伸缩缝宽度及平顺情况,如有缺限修复处理。与现有技术相比,本发明的优点在于:本发明的CRTSⅢ型板式无砟轨道底座板施工方法,采用拼装钢模,适用性强、利用率高、装拆灵活方便;采用专用整平工装对底座板上表面整平,有效减少了人工作业量,保证了底座板顶面标高、平整度质量,提高了施工工效,加快了施工进度。附图说明图1是本发明CRTSⅢ型板式无砟轨道底座板施工方法的流程图。图2是用于本发明的整平工装结构示意图。图中各标号表示:1、行走机构;11、上横梁;12、升降螺杆;13、导向轮;2、刮尺;3、行走轨道;4、振平机;5、侧模板。具体实施方式图1示出了本发明的一种CRTSⅢ型板式无砟轨道底座板施工方法实施例的流程,该施工方法包括以下步骤:S1:施工准备:完成梁面凿毛检查及验收,组织材料、设备进场,测量底座板的四个角点并放样,记录放样点高程,用墨线弹出四个角点之间的角点连线;S2:钢筋安装:钢筋网片分两层铺设,先根据角点连线铺设底层钢筋网片,再在梁面预埋的连接套筒中安装L形连接钢筋,完成后铺设顶层钢筋网片,并通过L形连接钢筋支撑固定,用U形钢筋连接上下层钢筋网片形成钢筋骨架,U型形筋底部与钢筋网片主筋端头对齐绑扎;S3:模板安装:先在梁面弹设好底座板侧模板5的安装定位线,从梁面的跨中位置向两端头拼装侧模板5,按照安装定位线将侧模板5就位并加固,侧模板5安装后,安装固定伸缩缝模板;再用定位架安装限位凹槽模板,本实施例中,定位架采用槽钢焊接制作,由定位框、定位横梁、调节螺杆和连接螺栓组成,先将定位架安装在底座板侧模板5顶部,再将限位凹槽模板安装在定位架的横梁上,调节调整螺杆使限位凹槽模板顶面标高满足要求后,用10mm圆钢将限位凹槽模板与底座板钢筋网片焊接固定,再撤除定位架;采用CPIII轨道控制网测量侧模板5高程及平面位置,校准后进行二次微调,微调完成后,再次测量侧模板5顶面高程,并计算侧模板5顶面至底座板设计标高距离,然后在侧模板5内侧标示底座板顶面标高线;S4:整平工装安装:沿侧模板5顶部安装整平工装的行走轨道3,将整平工装的行走机构1置入行走轨道3,并使连接于行走机构1下方的刮尺2置于底座板的两侧模板5之间,调整刮尺2底部标高,使其满足底座板顶面标高要求;S5:混凝土浇筑并整平:先对梁面洒水润湿,再开始浇筑、振捣混凝土,混凝土振捣密实后,两人在底座板两侧同步推进整平工装进行底座板顶面整平提浆,反复整平直至刮尺2底部混凝土充实为止,并确保底座板顶面与侧模板5内侧标示的底座板顶面标高线平齐;S6:拆模:混凝土初凝前,拆除限位凹槽模板和伸缩缝模板,混凝土终凝前,进行底座板混凝土面压光处理,消除干缩裂纹、砂眼、气泡,混凝土强度达到2.5Mpa以上后,拆除底座板的两侧模板5。本发明的CRTSⅢ型板式无砟轨道底座板施工方法,采用拼装钢模,适用性强、利用率高、装拆灵活方便;采用专用整平工装对底座板上表面整平,有效减少了人工作业量,保证了底座板顶面标高、平整度质量,提高了施工工效,加快了施工进度。以郑徐客运专线为例,完成11.59公里底座板施工,较原计划节约了时间18天,节约工程成本52万元。本实施例中,在执行步骤S2时,梁面预埋的连接套筒如有破损、缺失或位置偏差较大时,进行钻孔植筋处理,植筋深度不少于200mm。本实施例中,曲线地段的U形钢筋加工时,先绘制U形钢筋高度变化斜线,确定每孔梁U形钢筋高度,绑扎时根据每孔梁对应的U形筋高度,测量准确后将U形钢筋绑扎到对应位置。本实施例中,在执行步骤S3时,侧模板5采用组合拼装钢模,根据直线段底座板高度及长度设计单块钢模尺寸,本实施例的单块钢模高20cm,长为底座板长度的1/2。直线段施工采用单块钢模,曲线段施工时,将两块钢模上下叠加并采用螺栓连接,钢模与梁面之间设置调节螺杆,通过调整调节螺杆,使侧模板5顶面标高满足底座板混凝土浇筑要求。本实施例中,单块钢模施工时,在钢模外侧梁面钻孔打入钢筋头,楔入木楔固定模板;两块钢模上下叠加拼装施工时,于钢模机械连接处通过法兰调节螺杆进行模板调整与加固,保证侧模板5垂直度及稳定性。本实施例中,在执行步骤S5时,沿梁体纵向从一端向另一端推进浇筑,一次成型;或从限位凹槽处从凹槽中间向周围浇筑,挤出浮浆;或从曲线段的低侧向高侧浇筑;振捣时,振动棒与各模板保持5cm-10cm距离。本实施例中,整平时,专人跟进整平工装并观察刮尺2底部混凝土情况,及时铲除多余混凝土并对空洞处补料,刮尺2收面后人工收面,完成后用5m靠尺检查平整度,不合格处进行二次修补。本实施例中,在执行步骤S6时,拆除限位凹槽模板和伸缩缝模板后,对限位凹槽进行抹光并检查几何尺寸,不合格的进行修复;检查底座板间错台情况、伸缩缝宽度及平顺情况,如有缺限修复处理。图2示出了用于上述CRTSⅢ型板式无砟轨道底座板施工方法的整平工装,该整平工装包括行走机构1、刮尺2以及装设于底座板的侧模板5上的行走轨道3,行走机构1包括上横梁11、升降螺杆12和一对导向轮13,一对导向轮13分设于上横梁11两端,且导向轮13置于行走轨道3内,升降螺杆12可升降调节的装设于上横梁11中部,刮尺2连接于升降螺杆12下端,刮尺2中部装设有振平机4。本发明的用于CRTSⅢ型板式无砟轨道底座板施工方法的整平工装,其结构简单、操作方便,可大大提高整平作业效率和质量,并且有效减少了人工作业量,降低了劳动强度。虽然本发明已以较佳实施例揭露如上,然而并非用以限定本发明。任何熟悉本领域的技术人员,在不脱离本发明技术方案范围的情况下,都可利用上述揭示的技术内容对本发明技术方案做出许多可能的变动和修饰,或修改为等同变化的等效实施例。因此,凡是未脱离本发明技术方案的内容,依据本发明技术实质对以上实施例所做的任何简单修改、等同变化及修饰,均应落在本发明技术方案保护的范围内。