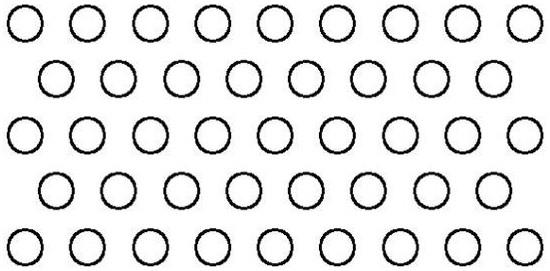
1.本发明属于铁路钢轨强化和修复领域,涉及一种基于层流等离子技术在钢轨表面在线强化处理和修复的方法,具体为一种在线钢轨层流等离子表面强化设备的处理方法。
背景技术:2.随着我国铁路以及城市轨道交通的大规模建设与发展,对铁路钢轨的耐磨性和使用寿命的要求更高,钢轨磨耗以及使用寿命问题一直伴随着铁的发展,线路钢轨中尤其是小半径曲线钢轨磨耗和伤损更为严重。
3.铁路钢轨的损伤大致可以分为磨损和滚动接触疲劳。磨损的主要损伤类型包括钢轨侧磨、钢轨压溃、钢轨剥离、钢轨波磨,占到钢轨磨损损伤量的80%以上。滚动接触疲劳会诱发棘齿裂纹和垂直裂纹,根据接触疲劳裂纹在钢轨踏面处形成的位置和形状,可以将疲劳裂纹分为鱼鳞状剥离裂纹和斜裂纹。几种常见的损伤模式如下:侧磨:磨耗常表现为在钢轨头部发生的沿全长的磨损,以侧面磨耗为主,一般出现在曲线外股钢轨的侧面工作边。列车运行过程中,车轮与钢轨之间的粘着、螺滑及滑动,车轮与钢轨之间由于存在冲击角而造成的对钢轨的冲击,都会导致钢轨侧磨病害。
4.波磨:钢轨投入使用后,轨顶面沿纵向出现有一定规律性的凸凹不平现象被称为波浪型磨损,简称波磨。较大的轮轨载荷导致钢轨塑性变形不均匀是钢轨产生波磨的主要原因。
5.压溃:钢轨连续塑性变形会引起钢轨的压溃,常见于重载线路曲线内股钢轨上,表现为钢轨内轨角处轨头被挤压。造成钢轨压溃的原因为:轨道材料强度不足,硬度不够,曲线超高过高或过低,或者低股钢轨轨底坡不合适,有害夹杂物和元素偏析等。
6.剥离:剥离是指发生在钢轨踏面上一种呈薄片状或块状剥离母体的损伤,常见于线路曲线区段。轮轨接触区过大的接触应力超过钢轨材料的屈服极限,将在轮轨接触处附近发生塑性变形。在循环载荷的作用下,塑性变形会累积增加,进而在钢轨表面和次表面形成微观裂纹。这类微观裂纹如果得不到及时地处理将会逐渐发展呈薄片状剥离或局部发展成剥离掉块。
7.为了提高铁道钢轨的使用寿命,国内外一般采取三种方法:第一,采用全长淬火工艺,获得细片状珠光体组织;第二,采用低合金高碳钢钢轨或者贝氏体钢取代高碳钢,进一步提高钢轨的强度;第三,采用高能束表面处理技术以提高钢轨表面硬度。在过去几年中,钢轨全长淬火技术取得了显著的效果,它使钢轨的耐磨性分别提高了50%(直道)和100%(弯道)。然而,全长淬火技术的主要不足之处在于钢轨的表面不能够出现马氏体甚至贝氏体组织,否则将大幅度降低钢轨的断裂韧性,导致钢轨在服役过程中出现断轨等事故,严重影响到铁道的安全运行。因此,全长淬火后钢轨硬度一般控制在hv320~390之间,其耐磨性潜力的挖掘已经接近极限。低合金高碳钢钢轨或者贝氏体钢虽然大幅提高了钢轨强度和耐磨性能,但强度的提升必然导致钢轨的断裂韧性的降低,在使用过程中加大了钢轨脆断的风险和行车安全隐患,目前也仅应用于少量特殊地段,并未得到进一步推广应用。
8.高能束表面处理技术是近二十年发展十分迅速的金属材料表面强化技术之一,它包括激光相变淬火、熔凝淬火、表面合金化和表面熔覆技术等工艺,其共同特点是加热速度快、热影响区小、工件变形小,因此有望取代感应全长淬火工艺,成为新一代的钢轨表面强化工艺。研究表明,由于激光表面强化技术的高加热速度、高冷却速度、硬化层深度有限和硬化层呈现压应力状态等特点,钢轨表面即使出现马氏体组织,也不会导致钢轨的强韧性显著下降。特别是由于马氏体组织的硬度显著高于细片状珠光体,因此可以突破感应全长淬火工艺时钢轨表面硬度不能高于hv390的上限,使得钢轨的表面耐磨性跃上新台阶。此外,激光表面淬火技术具有硬化层深度方便调控、不需要淬火介质、不需要回火、工件变形小等特点,因此除了可以在生产车间内实现定点加工,考虑到铁路干线繁忙的现状,还可望研发出专用移动设备,将设备搬运到铁路现场,在不拆卸钢轨的前提下,完成轨道的在线淬火。在线处理的移动式激光加工装置应具有高机动性,能够在尽量不影响列车正常运行的前提下,实现钢轨表面强韧化和修复处理。
9.中国发明专利文献“一种用于钢轨表面强韧化处理的在线激光加工设备”(公告号为cn101240367,公开日为2008年08月13日)报道中,提出了一种用于钢轨表面强韧化处理的在线激光加工设备,可以在不拆卸钢轨、不影响列车的正常运行前提下,完成各种钢轨,包括正轨、弯道、护轮轨、道岔等的激光相变淬火、熔凝淬火、合金化和熔覆处理,实现钢轨的在线强化与修复。该发明将激光加工设备分为激光加工车和动力系统集装箱两部分。其中激光加工车包括安装在移动小车上的运动执行机构,激光加工头,导光系统和控制系统;激光加工车采用三轮结构,在两个车轮的一侧安装了一个激光加工头,激光加工头的光路入光口直接采用传输光纤与动力系统集装箱上的光纤激光器连接。在实际加工时,激光加工车在控制系统控制下,沿着轨道方向前进,激光束在导光系统的作用下导向钢轨表面,由运动执行机构带动激光加工头左右摆动,实现对钢轨表面的激光强化及修复处理。激光加工车在加工完一边轨道后,需将激光加工车调头换向,对另一边轨道进行激光强化及修复处理。
10.上述专利文献所提出激光加工车的主要不足之处为加工效率较低,激光加工车一次只能对单边钢轨进行激光强化及修复处理,完成一边之后须将激光加工车调头换向,再对另一边进行加工,且单位处理效率较低,单边小于30米/小时,严重影响了对钢轨实际进行激光处理时的加工效率,不适应现场作业需求。
技术实现要素:11.本发明旨在解决现有技术中激光加工车的主要不足之处为加工效率较低,激光加工车一次只能对单边钢轨进行激光强化及修复处理,完成一边之后须将激光加工车调头换向,再对另一边进行加工,且单位处理效率较低,单边小于30米/小时,严重影响了对钢轨实际进行激光处理时的加工效率,不适应现场作业需求的问题,而提出了一种基于层流等离子技术在线钢轨表面强化设备的处理方法。
12.一种在线钢轨层流等离子表面强化的处理方法,其特征在于包括如下步骤:a.安装有层流等离子发生器组的在线作业小车走行到需要处理的钢轨位置,确定预定的处理范围;b.小车提升层流等离子发生器组到工作位置,开启层流等离子束发生器组,自动升功
至稳定工作状态;c.小车自动定位钢轨并走行,在预定的处理范围内进行两股钢轨表面进行强化处理,处理后在钢轨表面形成多个点状强化带;d.处理完毕之后对钢轨进行检查,检查合格之后回收小车,在新的区段作业,回到步骤a。
13.所述钢轨包括:普通线路钢轨、重载线路钢轨、小半径曲线钢轨或城市轨道交通线路钢轨。
14.所述钢轨表面强化处理的规格为:占空比25~60%,强化层直径φ4.0~6.0mm,深度0.4~2.0mm。
15.所述等离子发生器的生产工艺参数包括:阳极孔径、功率、气体流量、混气比例、强化时间和行走速度。
16.所述阳极孔径为φ3-5.0mm。
17.所述功率为5-15kw。
18.所述气流量为4-8l。
19.所述混气比例为25-65%。
20.所述强化时间为100-350ms。
21.所述行走速度为15-30mm/s。
22.所述步骤d中涉及到的检查包括:检验钢轨外观检查和对钢轨进行探伤。
23.所述步骤c中涉及到的处理范围为:钢轨顶面处理宽度50mm、侧面处理距顶面的长度范围为大于25mm,长度根据钢轨长度确定。
24.本发明的有益效果:1.本发明通过层流等离子体束对钢轨进行快速加热,使钢轨表层温度达到相变临界点以上、熔点以下,并通过钢轨自身的急冷作用和钢轨金属材料良好的导热性,使加热表层区域形成超细、均匀的淬硬组织,并不改变基体内部组织和性能,从而达到强化钢轨表层的目的。
25.2.本发明涉及到的层流等离子体在线强化处理是在不拆卸钢轨的前提下完成,具有高机动性,野外作业适应能力强,设备自动化程度高,生产效率高,将此技术运用于铁路钢轨的表面强化处理中,具有显著的经济及社会效益。
26.3.本发明将钢轨通过层流等离子强化处理后,其硬度和耐磨性大幅提高,使用寿命为未处理前的3倍以上,延长使用时间效果明显。
附图说明
27.图1为经过本发明方法处理后钢轨的结构示意图;图2为经过本发明方法处理后钢轨强化点的分布位置示意图;图3为经过本发明方法处理后钢轨表面硬度分布示意图;图4为经过本发明方法处理后钢轨强化层的金相图。
具体实施方式
28.下面通过对本发明实施例中的技术方案进行清楚、完整地描述,显然,所描述的实
施例仅是本发明的一部分实施例,而不是全部的实施例。基于本发明中的实施例,本领域普通技术人员在没有做出创造性劳动前提下所获得的所有其它实施例,都属于本发明保护的范围。
29.实施例1a.安装有层流等离子发生器组的在线作业小车走行到需要处理的钢轨位置,确定预定的处理范围;b.小车提升层流等离子发生器组到工作位置,开启层流等离子束发生器组,自动升功至稳定工作状态;c.小车自动定位钢轨并走行,在预定的处理范围内进行两股钢轨表面进行强化处理,处理后在钢轨表面形成多个点状强化带;d.处理完毕之后对钢轨进行检查,检查合格之后回收小车,在新的区段作业,回到步骤a。
30.所述钢轨包括:普通线路钢轨。
31.所述钢轨表面强化处理的规格为:占空比25~45%,强化层直径φ4.0~6.0mm,深度0.4~0.6mm。
32.实施例2a.安装有层流等离子发生器组的在线作业小车走行到需要处理的钢轨位置,确定预定的处理范围;b.小车提升层流等离子发生器组到工作位置,开启层流等离子束发生器组,自动升功至稳定工作状态;c.小车自动定位钢轨并走行,在预定的处理范围内进行两股钢轨表面进行强化处理,处理后在钢轨表面形成多个点状强化带;d.处理完毕之后对钢轨进行检查,检查合格之后回收小车,在新的区段作业,回到步骤a。
33.所述钢轨包括:重载线路钢轨。
34.所述钢轨表面强化处理的规格为:占空比45~60%,强化层直径φ5.0~6.0mm,深度0.6~1.0mm。
35.实施例3a.安装有层流等离子发生器组的在线作业小车走行到需要处理的钢轨位置,确定预定的处理范围;b.小车提升层流等离子发生器组到工作位置,开启层流等离子束发生器组,自动升功至稳定工作状态;c.小车自动定位钢轨并走行,在预定的处理范围内进行两股钢轨表面进行强化处理,处理后在钢轨表面形成多个点状强化带;d.处理完毕之后对钢轨进行检查,检查合格之后回收小车,在新的区段作业,回到步骤a。
36.所述钢轨包括:小半径曲线钢轨。
37.所述钢轨表面强化处理的规格为:占空比40~60%,强化层直径φ5.0~6.0mm,深度0.5~1.0mm。
38.实施例4a.安装有层流等离子发生器组的在线作业小车走行到需要处理的钢轨位置,确定预定的处理范围;b.小车提升层流等离子发生器组到工作位置,开启层流等离子束发生器组,自动升功至稳定工作状态;c.小车自动定位钢轨并走行,在预定的处理范围内进行两股钢轨表面进行强化处理,处理后在钢轨表面形成多个点状强化带;d.处理完毕之后对钢轨进行检查,检查合格之后回收小车,在新的区段作业,回到步骤a。
39.所述钢轨包括:城市轨道交通钢轨。
40.所述钢轨表面强化处理的规格为:占空比40~50%,强化层直径φ4.0~6.0mm,深度0.5~0.8mm。
41.实施例5一种在线钢轨层流等离子表面强化的处理方法,其特征在于包括如下步骤:a.安装有层流等离子发生器组的在线作业小车走行到需要处理的钢轨位置,确定预定的处理范围;b.小车提升层流等离子发生器组到工作位置,开启层流等离子束发生器组,自动升功至稳定工作状态;c.小车自动定位钢轨并走行,在预定的处理范围内进行两股钢轨表面进行强化处理,处理后在钢轨表面形成多个点状强化带;d.处理完毕之后对钢轨进行检查,检查合格之后回收小车,在新的区段作业,回到步骤a。
42.所述钢轨包括:普通线路钢轨、重载线路钢轨、小半径曲线钢轨或城市轨道交通线路钢轨。
43.所述钢轨表面强化处理的规格为:占空比25~60%,强化层直径φ4.0~6.0mm,深度0.4~2.0mm。
44.所述等离子发生器的生产工艺参数包括:阳极孔径、功率、气体流量、混气比例、强化时间和行走速度。
45.所述阳极孔径为φ3-5.0mm。
46.所述功率为5-15kw。
47.所述气流量为4-8l。
48.所述混气比例为25-65%。
49.所述强化时间为100-350ms。
50.所述行走速度为15-30mm/s。
51.实施例6一种在线钢轨层流等离子表面强化的处理方法,其特征在于包括如下步骤:a.安装有层流等离子发生器组的在线作业小车走行到需要处理的钢轨位置,确定预定的处理范围;b.小车提升层流等离子发生器组到工作位置,开启层流等离子束发生器组,自动升功
至稳定工作状态;c.小车自动定位钢轨并走行,在预定的处理范围内进行两股钢轨表面进行强化处理,处理后在钢轨表面形成多个点状强化带;d.处理完毕之后对钢轨进行检查,检查合格之后回收小车,在新的区段作业,回到步骤a。
52.所述钢轨包括:普通线路钢轨、重载线路钢轨、小半径曲线钢轨或城市轨道交通线路钢轨。
53.所述钢轨表面强化处理的规格为:占空比25~60%,强化层直径φ4.0~6.0mm,深度0.4~2.0mm。
54.所述等离子发生器的生产工艺参数包括:阳极孔径、功率、气体流量、混气比例、强化时间和行走速度。
55.所述阳极孔径为φ3-5.0mm。
56.所述功率为5-15kw。
57.所述气流量为4-8l。
58.所述混气比例为25-65%。
59.所述强化时间为100-350ms。
60.所述行走速度为15-30mm/s。
61.所述步骤d中涉及到的检查包括:检验钢轨外观检查和对钢轨进行探伤。
62.所述步骤c中涉及到的处理范围为:钢轨顶面处理宽度50mm、侧面处理距顶面的长度范围为大于25mm,长度根据钢轨长度确定。