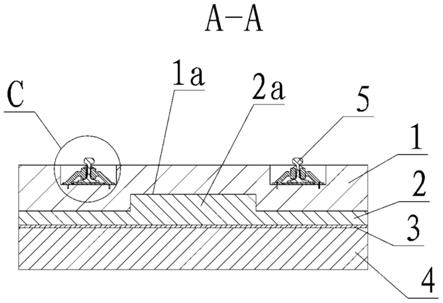
[0001]
本发明涉及一种高速铁路用轨道结构。
背景技术:[0002]
高速铁路已经成为我国铁路系统发展的必然趋势和现实需要。为了满足客运专线列车运行的安全性和乘车的舒适性,要求铁路轨道必须具备高平顺性和高稳定性。嵌入式无砟轨道结构具有良好的结构恒定性、稳定性、耐久性、少维修性、经济性等技术特点,因而在国内外高速铁路得到了广泛的应用。
[0003]
嵌入式无砟轨道结构是由离散(相隔一定间距)的扣件将钢轨压紧在现浇的单元板组的钢轨槽中构成。而扣件又主要由轨侧的锚固螺栓、压紧弹条和轨底的多块垫板构成。其钢轨和钢轨槽之间存在大量空隙,存在以下问题:1、列车经过时的冲击载荷由垫板和离散的压紧弹条缓冲,属于离散的点式缓冲,其缓冲能力有限,环境振动和噪声较大。2、轨道以扣件连接支撑,也是由离散、点式结构;加之,各连接点位的弹条的弹力取决于锚固螺栓的预紧扭矩,而轨道上各点锚固螺栓的预紧力很难保持一致,这导致钢轨各处的支撑刚度变化大,平顺性差,容易导致钢轨产生纵向方向的波磨(钢轨沿纵向表面出现不规则的波浪形状的磨损)损耗,进一步引发强烈的振动和噪声,增大了钢轨的养护成本。3、轨道上锚固螺栓与弹条形成动态的平衡预紧状态,在使用过程中,预紧力容易发生偏离,导致其需要经常更换和养护,增加了线路的养护成本。
技术实现要素:[0004]
本发明的目的是提供一种高速铁路嵌入式轨道结构,该结构能够大幅降低环境噪声,减少钢轨的波磨和锚固螺栓的维护,轨道养护方便,养护成本较低;还能实现轨道的批量化、机械化生产和自动化铺设,缩短铁路建设工期,使高速铁路线路铺设方便、快捷。
[0005]
本发明实现其发明目的所采用的技术方案为:一种高速铁路嵌入式轨道结构,包括基座和基座上方的轨道板,其特征在于:
[0006]
所述的轨道板为钢筋混凝土预制而成,轨道板上纵向对称分布有两条承轨槽,所述的承轨槽横截面呈瓶形,承轨槽内从下至上依次铺设有调高垫板、弹性垫板和钢轨,调高垫板和弹性垫板的宽度与承轨槽的宽度相等,钢轨的宽度小于承轨槽的宽度,钢轨的轨顶高过承轨槽;
[0007]
所述的承轨槽在纵向上等间距设置有宽度大于承轨槽的调轨槽,所述的调轨槽横截面呈矩形,且调轨槽的纵向轴线与承轨槽的纵向轴线重合;所述的调轨槽内钢轨两侧设有锤形的调轨件,调轨件的前锤面面向钢轨,调轨件的斜把的底座通过锚固螺栓固定在调轨槽两侧的底部;且调轨件的前锤与钢轨的轨腰间紧密嵌合有阻尼块;所述的调轨槽以外的承轨槽区域与钢轨间的空隙,用聚氨酯填充体填充;
[0008]
所述的轨道板底部纵向均匀设有两个凹槽,轨道板的底面与现浇的自密实砂浆层连接,自密实砂浆层顶面的两个凸起与轨道板底面的两个凹槽配合;所述的自密实砂浆层
的底面通过隔离层与基座紧密贴合;所述的基座由钢筋混凝土预制而成或者由金属制成。
[0009]
本发明的嵌入式轨道结构的铺设方法是:
[0010]
先铺设基座和基座顶面的隔离层,再在隔离层顶面的四周架设现浇自密实砂浆层的模板,然后将轨道板对准置于模板上部,通过轨道板上的注浆孔,向模板内注入自密实砂浆,然后拆掉模板,即在隔离层与轨道板之间形成底面带凸起的自密实砂浆层;随后,在轨道板的承轨槽中依次铺设调高垫板、弹性垫板和钢轨,再在调轨槽中用锚固螺栓固定调轨件,即完成嵌入式轨道结构的铺设。
[0011]
与现有技术相比,本发明的有益效果是:
[0012]
一、调轨件的一级支撑是用锚固螺栓的锚固固定方式实现,较之现有的扣件依靠锚固螺栓的预紧力和弹条的反向弹力形成的动态平衡实现支撑,其支撑作用更牢固、稳定,能更好的保证列车运行的安全。各调轨件牢固、稳定的锚固力不易变化,使得各调轨件间的锚固力容易保持一致;加上聚氨酯填充体填满承轨槽中的各处空隙,形成二级支撑。两级支撑配合构成连续的整体式支撑结构,使得钢轨各处的刚度变化小,平顺性好,大幅减轻了钢轨的波磨损耗,明显降低了列车运行时的振动和噪声,提高了乘车的舒适性,也降低了钢轨的养护成本。
[0013]
二、当列车通过时,车轮与钢轨接触产生的垂向冲击载荷由钢轨底部的弹性垫板,再加上自密实砂浆层和隔离层组成的一级减振结构衰减吸收。横向冲击载荷在调轨槽内被钢轨轨腰与调轨件之间的阻尼块衰减吸收,在调轨槽外的承轨槽区域,钢轨的横向冲击载荷则被周围全包围式的聚氨酯填充体进一步衰减吸收;总之,阻尼块和聚氨酯填充体巧妙配合组成的二级减振结构,对横向冲击载荷实现连续的全面吸收、衰减。这种多级减振消噪轨道结构,大幅减少了列车通过时的振动和噪声,使列车运行更加平稳,乘坐更舒适。
[0014]
三、通过轨道板的注浆孔现浇的自密实砂浆层,底面能与隔离层紧密连接,顶面能与轨道板凝固连接,同时自密实砂浆层在轨道板的凹槽中形成的两个凸起,使得自密实砂浆层与轨道板的连接更牢固。除自密实砂浆层为现浇外,其余构件均为工厂预制件;最大程度的实现了轨道构件的批量化、机械化生产和自动化铺设,缩短了铁路建设的工期,使高速铁路线路铺设方便、快捷。
[0015]
进一步,弹性垫板的顶面为与钢轨轨底坡适配的斜坡。
[0016]
这样,方便钢轨安装时形成规定的轨底坡,以满足列车运行的需要。
[0017]
进一步,承轨槽顶部两侧与聚氨酯填充体间留有条状通孔,形成疏水带。
[0018]
这样,疏水带能有效的将水排出,防止水渗入承轨槽内、产生积水,降低了隔离层、弹性垫板、调高垫板的老化及钢轨的腐蚀。
[0019]
更进一步,调轨件的斜把的底座通过锚固螺栓固定在调轨槽两侧的底部的具体方式是:锚固螺栓穿过调轨件的底座上的横向条形通孔,与调轨槽底部预埋的套筒螺纹连接。
[0020]
这样,通过调轨件底座上的横向条形通孔,可根据钢轨的实际需要调整调轨件的横向位置,既保证了钢轨的稳固固定,又方便了钢轨的横向精确定位。
[0021]
下面结合附图和具体实施方式对本发明作进一步的详细说明。
附图说明
[0022]
图1是本发明实施例的俯视结构示意图。
[0023]
图2是图1的端面结构示意图。
[0024]
图3是图1的局部b的放大示意图。
[0025]
图4是图1的a-a剖面示意图。
[0026]
图5是图4的局部c放大示意图。
具体实施方式
[0027]
实施例
[0028]
图1-图5示出,本发明的一种具体实施方式为:一种高速铁路嵌入式轨道结构,包括基座4和基座4上方的轨道板1,其特征在于:
[0029]
所述的轨道板1为钢筋混凝土预制而成,轨道板1上纵向对称分布有两条承轨槽7,所述的承轨槽7横截面呈瓶形,承轨槽7内从下至上依次铺设有调高垫板12、弹性垫板11和钢轨5,调高垫板12和弹性垫板11的宽度与承轨槽7的宽度相等,钢轨5的宽度小于承轨槽7的宽度,钢轨5的轨顶高过承轨槽7;
[0030]
图5及图1-4示出,所述的承轨槽7在纵向上等间距设置有宽度大于承轨槽7的调轨槽6,所述的调轨槽6横截面呈矩形,且调轨槽6的纵向轴线与承轨槽7的纵向轴线重合;所述的调轨槽6内钢轨5两侧设有锤形的调轨件,调轨件的前锤10c面面向钢轨5,调轨件的斜把10b的底座10a通过锚固螺栓15固定在调轨槽6两侧的底部;且调轨件的前锤10c与钢轨5的轨腰间紧密嵌合有阻尼块14;所述的调轨槽6以外的承轨槽7区域与钢轨5间的空隙,用聚氨酯填充体13填充;
[0031]
图1、图4示出,所述的轨道板1底部纵向均匀设有两个凹槽1a,轨道板1的底面与现浇的自密实砂浆层2连接,自密实砂浆层2顶面的两个凸起2a与轨道板1底面的两个凹槽1a配合;所述的自密实砂浆层2的底面通过隔离层3与基座4紧密贴合;所述的基座4由钢筋混凝土预制而成或者由金属制成。
[0032]
图5示出,本例的弹性垫板11的顶面为与钢轨5轨底坡适配的斜坡。
[0033]
图2示出,本例的承轨槽7顶部两侧与聚氨酯填充体13间留有条状通孔,形成疏水带17。
[0034]
图3、图5示出,本例的调轨件的斜把10b的底座10a通过锚固螺栓15固定在调轨槽6两侧的底部的具体方式是:锚固螺栓15穿过调轨件的底座10a上的横向条形通孔,与调轨槽6底部预埋的套筒18螺纹连接。