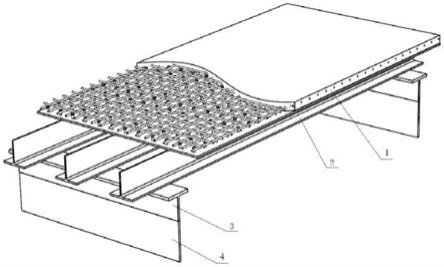
1.本发明涉及桥梁工程领域,具体涉及一种桥梁的组合桥面结构和桥梁结构及其施工方法。
背景技术:2.正交异性钢桥面具有自重轻、施工速度快、不受主梁形式限制等优点,在钢桥(尤其是大跨径钢桥)中得到了广泛应用。传统的正交异性钢桥面由钢顶板,纵向加劲肋和横隔板组成,钢桥面中的纵肋、横隔板相互交叉焊接,且均与钢面板焊接。常规正交异性钢桥面构造复杂,焊缝数量众多。焊接引入初始缺陷,并在钢板中产生残余应力。同时,焊接钢板因构造要求的局部开孔,易产生应力集中。当焊接钢结构承受重载车的反复作用时,焊缝处的钢板极易萌生疲劳裂纹,随着裂纹扩展,逐渐演化为宏观裂缝,甚至引发断裂。
3.钢桥面疲劳开裂是钢桥领域公认的世界性难题,一直是钢桥发展的重大技术瓶颈,我国重载交通量远高于发达国家,导致钢桥的上述病害尤为严重。长期以来,钢桥的运营维护负担过重,不仅给国民经济带来巨大损失,还对社会造成难以消除的负面影响。
技术实现要素:4.本发明提供了一种桥梁的组合桥面结构和桥梁结构及其施工方法,用以解决目前正交异性钢桥面存在的钢板焊缝过多、易产生疲劳裂纹的技术问题。
5.为解决上述技术问题,本发明采用以下技术方案:
6.一种桥梁的组合桥面结构,包括顶板和固定在顶板下表面的纵向肋,还包括拼接在桥梁主梁结构的横隔板上方的横向肋,纵向肋与横向肋固接,并通过横向肋连接至横隔板,横向肋上不设有用于容置纵向肋的开口。
7.上述技术方案的设计思路在于,现有技术中常规正交异性钢桥面的纵向肋需穿过横隔板并焊接,因此横隔板上需在施工时开设用于容置、焊接纵向肋的开口,但是纵向肋和横隔板相交处的焊缝和横隔板开口处疲劳应力较大,造成桥面结构中钢材的疲劳现象;本发明则通过设置一拼接在横隔板上方的横向肋直接与纵向肋进行连接,且通过不需要在横向肋上开口的连接方式将纵向肋与横隔板进行固定,避免了开口造成的应力过大的问题,减轻了桥面结构的钢材疲劳现象,提升了桥面结构的使用寿命和安全性能。
8.作为上述技术方案的进一步改进:
9.纵向肋和横向肋为市售常见型钢。本优选方案选择市售常见型钢作为纵向肋和横向肋有以下两个技术效果:首先,现有纵向肋一般采用现场拼接、切割钢板的方式制得,因此焊缝、加工处较多,应力较为集中,而采用型钢自身不需要焊接,减少了焊缝数量,型钢母材本身抗疲劳能力大大高于焊缝,在桥面板的高应力区设置型钢,可显著减少焊接、加工造成的疲劳开裂风险源。其次,型钢为工程常用材料,在生产纵向肋和横向肋时,只需要根据主梁构造要求截取不同长度的型钢,自身不需要额外轧制弯曲、开孔和焊接,减少了加工工序,降低了施工成本,制造便利性大大增强,同时型钢来源广泛、成本低廉,还可显著降低材
料成本。
10.纵向肋包括纵向腹板和位于纵向腹板的一端的纵向翼缘板;横向肋包含横向腹板和位于横向腹板的一端的横向翼缘板;纵向肋和横向肋之间通过纵向翼缘板和横向翼缘板相接触的面进行固接。本优选方案对纵向肋和横向肋的具体结构进行了限定,采用至少包含一个翼缘板的型钢作为纵向肋和横向肋的材料,并通过两翼缘板之间的连接将纵向肋和横向肋固接,可增加固接点位或者固接面积,使得固接更为稳定。
11.纵向肋位于横向肋的上方。桥面车辆荷载通过上部超高性能混凝土和纵向肋的进行应力扩散,纵向肋和横向肋连接通过面积较大的翼缘板接触承压,翼缘板之间连接构造处于翼缘板边缘低应力区,该种连接方式还可显著降低连接处的应力。
12.纵向肋和横向肋为h型钢、角钢、工字钢和t型钢中的一种。上述三种型钢较为常见、易于获得,且满足上述技术方案对翼缘板的相关要求,使用上述型钢可显著降低材料成本、施工难度和施工成本。
13.横向腹板的中轴线与桥梁主梁结构中横隔板腹板中轴线上下平齐。
14.纵向翼缘板和横向翼缘板的宽度均大于等于100mm。对翼缘板宽度的限定可保证纵肋和横肋的接触受力面积,并保证纵横肋之间焊缝的焊接连接强度(此处焊缝的焊接长度=翼缘板宽度)。
15.纵向腹板的厚度大于等于6mm,横向腹板的厚度大于等于8mm。腹板厚度根据现有桥梁工程中的经验厚度来取值,发明人根据多次研究和反复试验确定的最小厚度可保证桥梁结构满足受力要求。
16.纵向肋的高度小于等于800mm,横向肋的高度小于等于400mm。
17.纵向肋间隔布置在顶板下表面,且相邻纵向肋之间的间距为300~800mm。
18.顶板为的组合板,组合板包括钢面板和浇筑在钢面板表面的超高性能混凝土板;钢面板上设置有栓钉,栓钉的直径为10~30mm,高度为25~65mm。栓钉的直径和高度规定,是用以满足钢顶板和浇注其上的超高性能混凝土的连接,并满足构造要求。取值范围为发明人根据现有研究结果而限定合理取值区间。
19.超高性能混凝土板内布置单层纵横交错的加强钢筋网,横向钢筋位于纵向钢筋之上。横向钢筋和纵向钢筋的直径为8~20mm,相邻的纵向钢筋以及相邻的横向钢筋之间的间距均为15~300mm。
20.超高性能混凝土板是由超高性能混凝土浇筑而成,超高性能混凝土是指组分中含钢纤维、抗压强度不低于100mpa、轴拉强度不低于7mpa的混凝土。
21.钢面板为平板,厚度为6~20mm;超高性能混凝土板为等厚板,其厚度为30~100mm。
22.纵向肋与顶板的钢面板采用焊接的方式连接;纵向肋的纵向翼缘板与横向肋的横向翼缘板采用焊接或栓接的方式连接;横向肋和横隔板采用焊接的方式连接。
23.一种包括上述技术方案中的组合桥面结构的桥梁结构,包括所述组合桥面结构和主梁结构,所述主梁结构为钢箱梁、钢桁梁和钢板梁。所述主梁结构包括横隔板,所述组合桥面结构固定在主梁上方,且所述横向肋拼接在所述主梁结构的横隔板上方。
24.作为上述技术方案的进一步改进:
25.横隔板在主梁结构中间隔布置,且相邻横隔板之间的距离为2.5~8m。为满足桥梁
整体的受力,该距离为发明人根据一般桥梁工程经验取值范围确定。
26.一种上述技术方案的桥梁结构的施工方法,包括以下步骤:
27.s1、在工厂预制车间,将钢面板置于底层,在钢面板上焊接纵向肋;同时完成桥面以下包含横隔板的钢梁节段预制;
28.s2、在纵向肋上固结横向肋,形成桥面正交组合单元;
29.s3、将桥面正交组合单元翻转后,将桥面单元横向肋和钢梁节段的横隔板对应焊接,形成整体桥梁钢主梁节段;
30.s4、将钢主梁节段运输至桥梁施工现场后逐段拼接成全长主梁后,在钢面板上焊接栓钉,布置加强钢筋网,现场浇注超高性能混凝土,最终形成完整桥梁结构。
31.上述技术方案的设计思路在于,通过本发明的桥面结构的独特设计,减少了现有技术中对纵向肋以及横隔板的现场加工工艺步骤,可减少桥梁桥面焊接操作,且原材料常见易得,成本较低,可显著降低施工成本。
32.与现有技术相比,本发明的优点在于:
33.(1)本发明通过横向肋将纵向肋和横隔板进行连接,避免了现有技术中需在横隔板上开口的操作,减少了开口产生的应力,且采用热轧一体成形的型钢代替焊接钢板作为桥面纵向肋和横向肋,减少了焊缝,通过将型钢置于高应力区,焊缝置于低应力区,提高了桥面结构的抗疲劳能力;
34.(2)本发明的桥梁结构具有良好的经济性、安全性以及更长的使用寿命,施工方式比现有技术更简便、易于操作,原材料常见易得,成本较低,可显著降低施工成本。
附图说明
35.图1为实施例1桥梁的组合桥面结构的三维结构示意图;
36.图2为实施例1焊接有栓钉的钢面板示意图;
37.图3为实施例1纵向肋和横向肋连接关系示意图;
38.图4为实施例1桥面结构沿横桥向的截面示意图(也即图5中a
‑
a截面剖视图);
39.图5为实施例1桥面结构沿纵桥向的截面示意图(也即图4中b
‑
b截面剖视图);
40.图6为实施例1的桥梁结构沿横桥向的截面示意图。
41.图例说明:
42.1、顶板;2、纵向肋;3、横向肋;4、横隔板;11、超高性能混凝土板;12、钢面板;13、栓钉;14、纵向钢筋;15、横向钢筋;21、纵向腹板;22、纵向翼缘板;23、第一类焊缝;24、第二类焊缝;31、横向翼缘板;32、横向腹板;33、第三类焊缝;5、主梁结构;6、组合桥面结构。
具体实施方式
43.以下结合附图和具体实施例对本发明作进一步详细说明。
44.实施例1:
45.如图1
‑
图5所示,本实施例的桥梁的组合桥面结构,包括顶板1和固定在顶板1下表面的纵向肋2,还包括拼接在桥梁主梁结构5的横隔板4上方的横向肋3,纵向肋2与横向肋3固接,并通过横向肋3连接至横隔板4,横向肋3和横隔板4上均不设有用于容置、焊接纵向肋2的开口。
46.本实施例中,纵向肋2和横向肋3为市售常见型钢。
47.本实施例中,纵向肋2位于横向肋3上方。
48.本实施例中,纵向肋2包括纵向腹板21和位于纵向腹板21的一端的纵向翼缘板22;横向肋3包含横向腹板32和位于横向腹板32的一端的横向翼缘板31;纵向肋2和横向肋3之间通过纵向翼缘板22和横向翼缘板31相接触的面进行固接。
49.本实施例中,纵向肋2为倒t型钢,横向肋3为t型钢。
50.本实施例中,横向肋3与桥梁主梁结构5中横隔板4纵向布置位置和间距一致,且横向腹板32的中轴线与桥梁主梁结构5中横隔板4腹板中轴线上下平齐。
51.本实施例中,各项尺寸参数均根据桥梁施工现场情况确定。
52.本实施例中,纵向翼缘板22和横向翼缘板31的宽度均大于等于100mm。
53.本实施例中,纵向腹板21的厚度大于等于6mm,横向腹板32的厚度大于等于8mm。
54.本实施例中,纵向肋2的高度小于等于800mm,横向肋3的高度小于等于400mm。
55.本实施例中,纵向肋2间隔布置在顶板1下表面,且相邻纵向肋2之间的间距为300~800mm。
56.本实施例中,顶板1为的组合板,组合板包括钢面板12和浇筑在钢面板12表面的超高性能混凝土板11;钢面板12为平板,厚度为6~20mm,超高性能混凝土板11内布置单层纵横交错的加强钢筋网,横向钢筋15位于纵向钢筋14之上。横向钢筋15和纵向钢筋14的直径为8~20mm,相邻的纵向钢筋14以及相邻的横向钢筋15之间的间距为30~300mm,超高性能混凝土板11是由超高性能混凝土浇筑而成,超高性能混凝土是指组分中含钢纤维、抗压强度不低于100mpa、轴拉强度不低于7mpa的混凝土。超高性能混凝土板11为等厚板,厚度为30~100mm;钢面板12上设置有栓钉13,栓钉13的直径为10~30mm,高度为25~65mm。
57.本实施例中,纵向肋2与钢面板12通过第一类焊缝23连接。
58.本实施例中,纵向翼缘板22与横向翼缘板31通过第二类焊缝24连接。
59.本实施例中,横向肋3底部和横隔板4顶部通过第三类焊缝33连接。
60.对上述结构进行分析,可知第一类焊缝23为钢面板12与纵向肋2的焊缝,其疲劳细节分为钢面板12处疲劳细节a和纵向肋2处的疲劳细节b;第二类焊缝24为纵向翼缘板22与横向翼缘板31的焊缝,其疲劳细节分为纵向肋2处的疲劳细节c和横向肋3处的疲劳细节d;纵向肋2型钢本身的疲劳细节分为纵向腹板21的疲劳细节e和纵向翼缘板22处的疲劳细节f;横向肋3型钢本身的疲劳细节分为横向翼缘板31出的疲劳细节g和横向腹板32处的疲劳细节h,对上述疲劳细节应力与《公路钢结构设计桥梁规范》jtg d64
‑
2015规定的疲劳等级和常幅疲劳极限进行比对分析,结果如表1所示:
61.表1.本实施例各位置疲劳应力分析结果
[0062][0063]
表1中,疲劳细节应力是根据本实施例构造建立有限元模型,在模型中加载疲劳荷载得到最不利工况下的疲劳应力,疲劳荷载采用《公路钢结构设计桥梁规范》jtg d64
‑
2015规定的单车模型,总重480kn,单轴重120kn。
[0064]
由此可见,本发明的桥面结构其各处的疲劳细节应力均处在常幅疲劳极限以下,有效地解决了材料的疲劳应力过大产生的疲劳开裂。且横向肋3和纵向肋2如果采用焊接钢材,则焊缝的疲劳应力大于常幅疲劳极限,不满足规范要求,因此纵向肋2和横向肋3均采用一体轧制型钢,而非焊接钢材。
[0065]
如图6所示,本实施例的桥梁结构包括组合桥面结构6和主梁结构5,主梁结构5为钢箱梁。主梁结构包括横隔板4,组合桥面结构6固定在主梁结构5上方,且横向肋3拼接在主梁结构5的横隔板4上方。
[0066]
本实施例中,横隔板4在主梁结构5中间隔布置,且相邻横隔板4之间的距离为2.5~8m。
[0067]
本实施例的桥梁结构的施工方法,包括以下步骤:
[0068]
s1、在工厂预制车间,将钢面板12置于底层,在钢面板12上焊接纵向肋2;在工厂同时完成桥面以下包含横隔板4的钢梁节段预制;
[0069]
s2、在纵向肋2上固结横向肋3,形成桥面正交组合单元;
[0070]
s3、将桥面正交组合单元翻转后,将桥面单元横向肋3和钢梁节段的横隔板4对应焊接,形成整体桥梁钢主梁节段;
[0071]
s4、将钢主梁节段运输至桥梁施工现场后逐段拼接成全长主梁后,在钢面板12上焊接栓钉13,布置加强钢筋网,现场浇注超高性能混凝土,最终形成完整桥梁结构。
[0072]
以上所述仅是本发明的优选实施方式,本发明的保护范围并不仅局限于上述实施例。对于本技术领域的技术人员来说,在不脱离本发明技术构思前提下所得到的改进和变换也应视为本发明的保护范围。