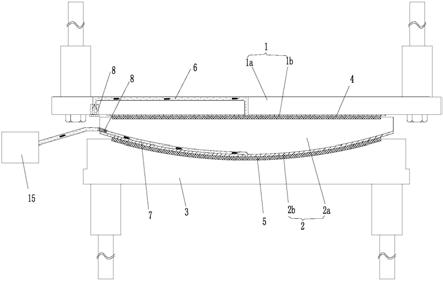
1.本实用新型属于建筑及桥梁支座技术领域,具体涉及一种持久润滑球型支座。
背景技术:2.球型支座是在盆式橡胶支座的基础上发展起来的一种支座。它取消了原有盆式支座中的承压橡胶板,通过在支座钢部件间设置滑动摩擦副及转动摩擦副实现结构的位移和转动,从而释放建筑结构及桥梁结构因温度、环境、载荷作用在局部节点产生过大的应力。球型支座各向转动性能一致,适用于弯桥、坡桥、斜桥、宽桥及大跨径桥梁以及大跨空间结构。球型支座的优点在于:传力可靠,各方向转动性能一致,不仅具备盆式橡胶支座承载能力强、水平位移大的特点,而且能使用大转角的需要,不存在橡胶低温脆性等影响,支座的温域使用范围广。
3.球型支座由下座板、球冠衬板、上座板、滑板(平面和球面各一块)及防尘罩等部件组成。球冠衬板是球型支座的核心,它的平面部分分开有镶嵌滑板的凹槽,用以固定平面滑板。下座板由钢板或铸钢制成,主要起固定球面滑板的作用,并将支座反力分散传递到桥墩、桥台及建筑结构上。平面滑板和球面滑板是支座的主要滑动部件,在滑板表面用专用模具压制成硅脂贮油坑,并涂以硅脂,以减小滑动摩擦系数,减少滑板的损耗。平面滑板与上座板的不锈钢板之间的滑动能满足支座的位移需要,其工作原理与盆式橡胶支座完全一致。
4.硅脂在球型支座中的润滑作用至关重要,是球型支座工作中控制摩擦系数和滑板材料线磨耗率的关键所在。球型支座在实际使用过程中硅脂易发生离析流失,导致支座的摩擦系数增大,线磨耗率增加,严重影响球型支座的长期使用寿命。有研究报告表明:每年有近3.5%的球型支座的病害是因为内部硅脂的缺失引起的。
5.目前也有专利公开了补充硅脂方法,如中国专利cn212742177u公开一种可补充硅脂的耐久型球型支座,包括下支座板、球面滑板、球冠钢衬板、平面滑板和上支座板,在下支座板上端设置有挡沿,在上支座板上设置有上输送通道,在挡沿外侧设置有挡环,所述挡环上边高出所述挡沿上边,在所述挡环与所述球冠钢衬板之间形成硅脂存储腔。通过上支座板上的上输送通道向上支座板与平面滑板之间注入硅脂,硅脂存储腔内的硅脂将球冠钢衬板与下支座板之间的硅脂封闭,在球冠钢衬板在下支座板中转动或摆动时,硅脂存储槽中的硅脂可以随时补充至球冠钢衬板和下支座板之间。然而该硅脂补偿方式是从结构外沿处补充,硅脂不易进入平面滑板和上支座板之间及球面滑板和球冠钢衬板之间,并且硅脂还存在沿缝隙进入支座其他部件内部,进而影响支座使用的稳定性问题。
技术实现要素:6.本实用新型所要解决的技术问题是克服现有技术的不足提供一种硅脂补充效果好且支座使用稳定性好的持久润滑球型支座。
7.为解决以上技术问题,本实用新型采用如下技术方案:
8.一种球型支座,包括由上至下依次设置的上座板、上表面与所述上座板的下表面滑动配合的平面滑板、用于装配所述平面滑板的且下表面为曲面的球冠衬板、上表面为曲面且与所述球冠衬板下表面转动配合的球面滑板及用于装配所述球面滑板的下座板,所述球型支座还包括用于补充硅脂的硅脂补充机构,所述硅脂补充机构包括设置在所述上座板内的用于输送硅脂的第一输送单元及设置在所述球冠衬板内的用于输送硅脂的第二输送单元,在所述上座板的下表面的对应所述平面滑板的位置开设第一出口,所述第一输送单元通过所述第一出口将硅脂输送至所述平面滑板的上表面,在所述球冠衬板的下表面的对应所述球面滑板的位置开设第二出口,所述第二输送单元通过所述第二出口将硅脂输送至所述球面滑板的上表面。
9.在一些优选且具体实施方式中,所述第一出口开设在所述上座板的下表面的中部;和/或,所述第二出口开设在所述球冠衬板的下表面的中部。
10.在一些优选且具体实施方式中,所述平面滑板的上表面设置多个第一储油槽,相邻二个所述第一储油槽之间设置用于将二个所述第一储油槽连通的第一连通槽;和/或,所述球面滑板的上表面设置多个第二储油槽,相邻二个所述第二储油槽之间设置用于将二个所述第二储油槽连通的第二连通槽。
11.在一些具体实施方式中,所述第一连通槽的槽深小于等于所述第一储油槽的槽深;和/或,所述第二连通槽的槽深小于等于所述第二储油槽的槽深。优选地,所述第一连通槽的槽深小于所述第一储油槽的槽深;和/或,所述第二连通槽的槽深小于所述第二储油槽的槽深。便于硅脂能够快速填满所述平面滑板或球面滑板上的全部储油槽。
12.在一些实施方式中,所述第一输送单元的进口端设置单向阀,所述单向阀可以控制流体由所述单向阀向支座内部流动,支座内部及第一输送单元中的流体无法通过所述单向阀向外流动,避免支座内部的硅脂通过第一输送单元外溢,所述单向阀的外端口设置用于防止灰尘杂物堵塞硅脂输送的保护套;和/或,所述第二输送单元的进口端设置单向阀,所述单向阀可以控制流体由所述单向阀向支座内部流动,支座内部及第二输送单元中的流体无法通过所述单向阀向外流动,避免支座内部的硅脂通过所述第二输送单元外溢,所述单向阀的外端口设置用于防止灰尘杂物堵塞硅脂输送的保护套。
13.在一些实施方式中,所述平面滑板为聚四氟乙烯板或超高分子量聚乙烯板;和/或,所述球面滑板为聚四氟乙烯板或超高分子量聚乙烯板。
14.在一些实施方式中,所述第一输送单元包括开设在所述上座板上且一端与所述第一出口连通的第一通道及设置在所述第一通道内的用于输送硅脂的第一管道,所述第一管道的出口端对应设置在所述第一出口位置;所述第二输送单元包括开设在所述上座板上且一端与所述第二出口连通的第二通道及设置在所述第二通道内的用于输送硅脂的第二管道,所述第二管道的出口端对应设置在所述第二出口位置。
15.进一步地,所述第一出口的内径小于等于所述第一管道的管内径;和/或,所述第二出口的内径小于等于所述第二管道的管内径。
16.进一步地,所述上座板包括上座板本体及设置在所述上座板本体下表面的平面不锈钢板,所述第一出口设置在所述平面不锈钢板上,所述第一通道设置在所述上座板本体上,所述第一管道的出口端与所述平面不锈钢板满焊连接;和/或,所述球冠衬板包括上表面设置所述平面滑板的球冠衬板本体及设置在所述球冠衬板本体下表面的球面不锈钢板,
所述第二出口设置在所述球面不锈钢板上,所述第二通道设置在所述球冠衬板本体上,所述第二管道的出口端与所述球面不锈钢板满焊连接。
17.在一些具体实施方式中,所述第一通道的另一端的端口设置在所述上座板本体的下表面的靠近外侧位置,所述第一通道包括竖直设置在所述上座板本体内的通道一段、由所述通道一段的上端部向靠近所述上座板本体的中部方向延伸且开设在所述上座板本体的上表面上的通道二段及由所述通道二段的端部向靠近所述第一出口方向延伸且竖直设置在所述上座板本体内的通道三段,所述通道一段靠近所述上座板本体的外侧设置;和/或,所述第二通道的另一端的端口设置在所述球冠衬板本体的侧面,所述第二通道由所述球冠衬板本体的侧面向靠近所述球冠衬板本体的中部方向延伸且开设在所述球冠衬板本体的下表面。
18.由于上述技术方案运用,本实用新型与现有技术相比具有下列优点:
19.本实用新型通过将第一输送单元设置在上座板上及第二输送单元设置在球冠衬板上,且使得第一开口对准平面滑板,第二开口对准球面滑板,硅脂分别通过第一开口、第二开口直接输送至平面滑板和球面滑板上,硅脂补充效果好,使滑动摩擦副和转动摩擦副长久保持良好的润滑状态,保证摩擦系数稳定可靠、减小滑板材料的线磨耗率,保障球型支座滑动、转动灵活性,进而延长支座的使用寿命,减少支座维护次数及成本,还能避免硅脂从缝隙进入支座内部的其他部件,支座使用稳定性好。
附图说明
20.图1为传统的球型支座结构示意图,其中,图1a为固定球型支座、图1b为单向滑动球型支座、图1c为双向滑动球型支座;
21.图1中:1、上座板;2、球冠衬板;3、下座板;4、平面滑板;5、球面滑板。
22.图2为本实用新型实施例1的球型支座的结构示意图;
23.图3为本实用新型实施例1的球型支座的球冠衬板的结构示意图;
24.图4为本实用新型实施例1的球型支座的平面滑板的俯视结构示意图(显示部分第一储油槽和第一连通槽);
25.图5为本实用新型实施例1的球型支座的平面滑板的剖视结构示意图;
26.图6为本实用新型实施例1的球型支座的球面滑板的俯视结构示意图(显示部分第二储油槽和第二连通槽);
27.图7为本实用新型实施例1的球型支座的球面滑板的剖视结构示意图;
28.图8为本实用新型实施例1的球型支座的上座板的剖视结构示意图;
29.图9为本实用新型实施例1的球型支座的上座板的俯视结构示意图;
30.图10为本实用新型实施例2的球型支座的上座板的剖视结构示意图;
31.图11为本实用新型实施例2的球型支座的上座板的俯视结构示意图;
32.图12为本实用新型实施例3的球型支座的上座板的剖视结构示意图;
33.图13为本实用新型实施例3的球型支座的上座板的俯视结构示意图;
34.图中:1、上座板;1a、上座板本体;1b、平面不锈钢板;2、球冠衬板;2a、球冠衬板本体;2b、球面不锈钢板;3、下座板;4、平面滑板;5、球面滑板;6、第一管道;7、第二管道;8、单向阀;9、第一储油槽;10、第一连通槽;11、第二储油槽;12、第二连通槽;13、第一出口;14、第
二出口;15、增压加注设备;16、挡块。
具体实施方式
35.传统的球型支座结构形式主要可分为3类,如图1所示:固定球型支座、单向滑动球型支座、双向滑动球型支座。基本组件包括:上座板1、滑动摩擦副(由上座板1的平面不锈钢板和平面滑板4构成)、球冠衬板2、转动摩擦副(由球冠衬板2的球面不锈钢板和球面滑板5构成)、下座板3以及连接锚固系统,摩擦副包含镜面不锈钢、含有贮油槽的滑板、硅脂三部分。镜面不锈钢通过焊接工艺与球型支座钢制部件连接,滑板材料通过镶嵌工艺、螺栓锚固与球型支座钢制部件连接。固定球型支座上座板与球冠衬板间的允许滑动位移较小、单向滑动球型支座允许一个水平方向上有较大的滑动位移、双向滑动球型支座允许在两个方向上较大的滑动位移。滑板材料可以是聚四氟乙烯板、超高分子量聚乙烯板、其他固体润滑材料(如全氟聚醚涂层、纳米氧化铝、石墨等)。常规的聚四氟乙烯板、超高分子量聚乙烯板上设置储油槽,储油槽贮存有硅脂,起到润滑、较小摩擦系数、降低材料磨耗的作用。但储油槽内贮存的硅脂会随着支座使用年限的增加而含量降低,润滑效果逐渐下降,滑板的磨耗会增大。而现有的补充硅脂方法存在硅脂补充效果不好及支座使用稳定性差的问题。本技术通过结构优化设计将硅脂直接补充到平面滑板上表面和球面滑板上表面,硅脂补充效果好,同时避免硅脂通过缝隙进入到支座其他部件内。进一步地,通过平面滑板和球面滑板上凹槽的改进设计,进一步提升硅脂的补充效果。
36.以下结合说明书附图及具体实施例对本实用新型做进一步描述:
37.实施例1
38.本实施例提供的球型支座,其为双向滑动球型支座,包括由上至下依次设置的上座板1、上表面与上座板1的下表面滑动配合的平面滑板4、用于装配平面滑板4的且下表面为曲面的球冠衬板2、上表面为曲面且与球冠衬板2下表面转动配合的球面滑板5及用于装配球面滑板5的下座板3。
39.该球型支座还包括用于补充硅脂的硅脂补充机构,硅脂补充机构包括设置在上座板1内的用于输送硅脂的第一输送单元及设置在球冠衬板2内的用于输送硅脂的第二输送单元,在上座板1的下表面的对应平面滑板4的位置开设第一出口13,第一输送单元通过第一出口13将硅脂输送至平面滑板4的上表面,在球冠衬板2的下表面的对应球面滑板5的位置开设第二出口14,第二输送单元通过第二出口14将硅脂输送至球面滑板5的上表面。
40.第一出口13开设在上座板1的下表面的中心位置,第二开口14开设在球冠衬板2的下表面的中心位置。参见图4~7,在平面滑板4的上表面设置多个第一储油槽9,球面滑板5的上表面设置多个第二储油槽11,为了进一步提升硅脂补充效果,在相邻二个第一储油槽9之间设置用于将二个第一储油槽9连通的第一连通槽10,在相邻二个第二储油槽11之间设置用于将二个第二储油槽11连通的第二连通槽12,第一连通槽10的槽深小于第一储油槽9的槽深,第二连通槽12的槽深小于第二储油槽11的槽深。储油槽和连通槽均通过模压作用形成。第一开口13位于一个或多个第一储油槽11的上方,第二开口14位于一个或多个第二储油槽12的上方。
41.本例中,平面滑板4、球面滑板5分别为聚四氟乙烯板或超高分子量聚乙烯板,平面滑板4、球面滑板5分别锚接在球冠衬板2的上表面和下座板3的上表面,具体地,在球冠衬板
2的上表面内凹设置有安装槽,下座板3的上表面内凹设置有安装槽,平面滑板4、球面滑板5分别锚接在对应的安装槽内。
42.本例中,上座板1包括上座板本体1a及设置在上座板本体1a下表面的镜面的平面不锈钢板1b,上座板本体1a与平面不锈钢板1b之间通过焊接固定,第一输送单元包括开设在上座板本体1a上的第一通道及固定在第一通道内的用于输送硅脂的第一管道6,第一出口13开设在平面不锈钢板1b上,第一管道6的进口端设置单向阀8,第一管道6的出口端对应设置在第一出口13位置,第一出口13的内径小于第一管道6的内径,且第一管道6的出口端与平面不锈钢板1b之间满焊连接,形成封闭的传输通道,防止硅脂在传输过程中从缝隙进入支座内部的其他部件(如平面滑板4和球冠衬板2之间、平面不锈钢板1b和上座板本体1a之间),满焊后硅脂只会沿着平面滑板4的表面由中心向四周扩散,满焊焊缝处应打磨光滑,不影响滑动摩擦副的摩擦效果。
43.球冠衬板2包括上表面设置平面滑板4的球冠衬板本体2a及设置在球冠衬板本体2a下表面的镜面的球面不锈钢板2b,球冠衬板本体2a与球面不锈钢板2b之间通过焊接固定,第二输送单元包括开设在球冠衬板本体2a上的第二通道及固定在第二通道内的用于输送硅脂的第二管道7,第二出口14开设在球面不锈钢板2b上,第二管道7的进口端设置单向阀8,第二管道7的出口端对应设置在第二出口14位置,第二出口14的内径小于第二管道7的内径,且第二管道7的出口端与球面不锈钢板2b满焊连接,形成封闭的传输通道,防止硅脂在传输过程中从缝隙进入支座内部的其他部件(如球面滑板5和下座板3之间、球面不锈钢板2b和球冠衬板本体2a之间),满焊后硅脂只会沿着球面滑板5的表面由中心向四周扩散,满焊焊缝处应打磨光滑,不影响滑动摩擦副的摩擦效果。
44.第一管道6、第二管道7上的单向阀8,加压流体可以通过单向阀向管道内流动,而管道内的流体无法通过单向阀向外流动,防止支座在工作过程中硅脂通过管道外溢。支座组装时,管道内需充满硅脂,防止平面滑板4或球面滑板5上的硅脂在支座运营过程中进入管道,影响摩擦副的润滑效果。单向阀8的输入端口设置有卡扣接口或螺纹接口,可以安装卡扣或螺帽,防止灰尘或其他物体堵塞硅脂输入端口。
45.出于耐久性考虑,第一管道6、第二管道7可以使用金属铜管、铝管、不锈钢管等,第一管道6、第二管道7的中部通过多个固定卡口分别固定在第一通道和第二通道内,固定卡口采用机械锚固或点焊,保证第一管道6和第二管道7的连接可靠性。
46.为了不降低支座的强度,尽量避免在支座内部钻孔,第一通道、第二通道的设置分别如下:第一通道的一端与第一出口13连通、另一端的端口设置在下座板本体1a的下表面的靠近外侧位置,具体地,第一通道包括竖直设置开设在上座板本体1a内的通道一段、由通道一段的上端部向靠近上座板本体1a的中部方向延伸且开设在上座板本体1a的上表面上的通道二段及由通道二段的端部向靠近第一出口13方向延伸且竖直设置在上座板本体1a内的通道三段,通道一段靠近上座板本体1a的外侧设置;第二通道的一端与第二出口14连通、另一端的端口设置在球冠衬板本体2a的侧面,第二通道由球冠衬板本体2a的侧面向靠近球冠衬板本体2a的中部方向延伸且开设在球冠衬板本体2a的下表面。制作时,在下座板本体1a的上表面铣槽形成通道二段,在球冠衬板本体2a的下表面铣槽形成第二通道,加工便利,且不影响构件承载,不会对滑板部件产生不利影响,并且补充硅脂时,因为滑板部件上没有开孔,硅脂只会沿着滑板表面流动,不会沿缝隙进入支座其他部件内部。
47.该球形支座补充硅脂时,在第一管道6或第二管道7上连接硅脂增压加注设备15。
48.当球型支座正常工作时,平面滑板4或球面滑板5表面的硅脂填充了滑动或转动摩擦副间的空间形成密闭空间;当需要补充硅脂时,增压加注设备15连接到第一管道6或第二管道7,向第一管道6或第二管道7加注硅脂,然后从第一出口13或第二出口14进入平面滑板4或球面滑板5表面,而平面滑板4上的第一储油槽9之间通过第一连通槽10贯通相连,当第一储油槽9内的硅脂受到压力作用时,硅脂会由中心向四周流动直至平面滑板4上的第一储油槽9全部被填满;同理,当球面滑板5上的第二储油槽11内的硅脂受到压力作用时,硅脂由中心向四周流动直至球面滑板5上的第二储油槽11全部被填满。
49.通过上述设置,该球型支座,无需在支座内部钻孔,特别是球冠衬板内部无需钻孔,构件承载性能不受影响,补充硅脂时,硅脂直接补充到平面滑板4和球面滑板5中部,且通过第一连通槽10和第二连通槽12的作用,平面滑板4和球面滑板5上的第一储油槽9和第二储油槽11能够快速被填满,硅脂补充效果好,快速便捷,并且平面滑板4和球面滑板5上没有钻孔,硅脂不会沿缝隙进入支座的其他部件内,支座使用稳定性好。
50.实施例2
51.本实施例提供的球型支座,参见图10~11,其为固定球型支座,结构基本同实施例1,不同之处在于:在下座板本体1a的下表面沿球冠衬板2的周向设有挡块16。
52.实施例3
53.本实施例提供的球型支座,参见图12~13,其为单向滑动球型支座,结构基本同实施例1,不同之处在于:在下座板本体1a的下表面且位于球冠衬板2的相对二侧设有挡块16。
54.上述实施例只为说明本实用新型的技术构思及特点,其目的在于让熟悉此项技术的人士能够了解本实用新型的内容并据以实施,并不能以此限制本实用新型的保护范围,凡根据本实用新型精神实质所作的等效变化或修饰,都应涵盖在本实用新型的保护范围之内。