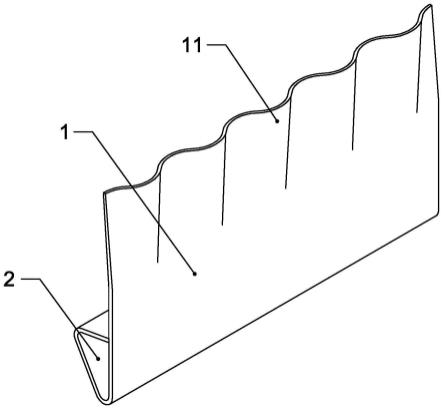
1.本技术涉及加劲板领域,尤其是一种加劲肋以及一种加劲板。
背景技术:2.加劲肋作为条状加强件,通常设置在单层的钢顶板或面板一侧,形成加劲板,以增加单板的虚拟厚度,提高单板的抗弯、抗扭等性能。因其质量轻、力学性能佳,得到广泛应用。比如桥梁中的桥面板是典型的加劲板的应用。桥面板是桥梁结构中的重要构件,除了参与桥梁结构的整体受力外,更主要的是直接承受桥面车辆荷载作用,把桥梁上的车辆荷载传递到其他结构构件中。
3.从加劲肋的形式上来看,主要分为开口肋与闭口肋。常见的开口肋形式主要有:t形肋、正球头肋,偏球头肋,不等边角钢肋、板肋等。但由于开口肋均存在的抗扭和抗弯刚度偏小,且需要热轧或焊接的缺点,比如球扁肋需通过钢厂热轧定制,规格死板;板肋惯性矩小;l形加劲肋在受弯时远端翼缘存在翻起降效现象;t形加劲肋与l形加劲肋相似,且需热轧或焊接等,因而开口肋桥面板具有较小的横向荷载分布能力,结构的屈曲强度较低,且每条开口肋与面板连接需要两条贴角焊,单位面积所需焊缝数量多;因此,开口肋比闭口肋桥面板效率低。
4.常见闭口肋形式主要有:梯形肋、u形肋、v形肋、y字形肋等,同样,闭口肋虽然截面性能好,抗弯、抗扭转的性能均优于开口肋,但闭口肋由于是闭口截面,焊接只能从外部进行,内侧焊接难度大,焊缝难以检测以及后续的维修,常常引起疲劳开裂问题,成为行业头痛不已的典型顽症。
技术实现要素:5.本技术的目的是为了解决现有加劲板开口肋抗扭和抗弯刚度差,闭口肋焊接难度大,抗疲劳性能差等问题,提供一种半闭口半开口的加劲肋,上部仍采用开口截面,保留了开口肋的连接优势,下部钢板折弯形成管状的翼缘部,不仅增大加劲肋下缘的截面积,同时通过下部截面微小变形吸能,大幅提高加劲肋抗扭、抗弯性能,同时本技术提供了一种包含上述加劲肋的加劲板。
6.为了实现上述申请目的,本技术采用了以下技术方案:
7.本技术一方面提供了一种半闭口半开口的加劲肋,包括腹板和翼缘部,所述加劲肋由一张钢板成型而成,所述腹板和翼缘部一体相连;
8.所述翼缘部为管状,由腹板下部的钢板成型所围成,所述翼缘部具有与腹板靠拢的尾端,尾端与腹板的距离为0~15mm。
9.作为优选,所述尾端与腹板之间不焊接或局部焊接连接。与传统构造的通过焊接强化的方式不同,本技术尾端与腹板之间不焊接,或只需在交叉加劲肋等复杂的构造部位少量采用焊接,大量的结合部不焊接,不仅减少焊接工作量,降低成本,不焊接还能从根本上减少焊接疲劳发生的基础条件,即从根本上杜绝了焊接疲劳发生的概率,且不焊接能够
释放一侧约束,允许翼缘部截面存在部分变形,以变形吸能。
10.作为优选,所述翼缘部的断面为三角形,翼缘部包括第一边、第二边和第三边,所述第一边与腹板一体连接,所述第二边连接第一边和第三边,所述第三边与腹板靠拢。三角形的稳定性相对其他形状更好,加劲肋受压或受弯时,通过三角形第一边的下挠或弯曲,引起第二边产生向上的力,由于第二边偏离腹板中心线,继而第二边又产生一个向内的闭合力,由于翼缘部的尾端与腹板结合处设在腹板的其中一侧,从而产生的向内的偏心力,使得原第三边与腹板自然闭合的少量缝隙减少和顶紧,在此过程中截面变形消耗了荷载能量,有效地减少了对加劲肋与面板连接部的应力分配,也因滞后延迟效应,降低了加劲肋与面板连接部的应力变化的速率或斜率。
11.作为优选,所述第一边和第二边的夹角为α,α<60
°
。用小角度减少翼缘部的宽度,既减少剪力滞的负面效应,又将第一边的变形直接传递给第二边,角度越小,传递越快越直接,对第三边与腹板的闭合效果也越好,通过上述传递路径,以不焊接或极少焊接的代价,形成了一种有耗能作用的、良好综合性能的半闭口加劲肋。
12.作为优选,所述第一边和第三边的夹角为β,β大于60
°
。第三边与第一边以较大角度闭合,是直接顶紧形成闭合截面的有效手段。
13.作为优选,所述腹板远离翼缘部的一侧设置波形部,所述波形部的波形方向沿加劲肋长度方向延伸,且越往腹板外侧波高越高。通过在加劲肋腹板上端轧制波形,增加了加劲肋腹板的虚拟厚度,提高了抗剪和抗屈曲性能,同时,由于腹板端部具有波形,加劲肋与面板焊接的焊缝由传统的单一方向的直线焊缝变为曲线焊缝,增加了焊缝的长度,同时焊缝沿多个方向延伸,受力时,总有一个有利方向承担载荷,焊缝强度增加。同时,波形焊道增大了面板承力的区域,使得加劲肋的抗摇头弯矩性能几何级增加,也有利于减少加劲肋对面板的局部应力,对防止肋板给面板造成瘦马现象也有显著好处。
14.作为优选,波形部为正弦波、梯形波或折线波。正弦波形板与面板的焊道顺畅平滑,梯形波抗屈曲刚度高,折线波兼顾上述两者性能,且制作也比较简单。
15.作为优选,所述加劲肋还包括与腹板相连的连接板,连接板与腹板具有夹角φ,85
°
≤φ≤95
°
。连接板用于与被加劲的面板进行连接,连接时连接板与面板贴合,既可以通过焊接固定,也可以通过螺栓连接等装配化的方式进行连接。
16.作为优选,所述连接板上具有连接孔。连接孔内可设置螺栓等连接件,尤其适用于组合结构桥面,下部螺杆利用腹板防松,上部螺母利用面板上部混凝土固结,形成永不松动构造,本连接构造稳定可控,与传统采用焊接连接的开口肋相比,减少了每延米两侧2米的焊缝。
17.作为优选,所述翼缘部断面为多边形。多边形截面相对于底部为尖角的三角形截面,多边形底部通常为板状,可以作为与其他部件形成支撑、承托的连接部。
18.本技术另一方面提供了一种加劲板,包括上述的半闭口半开口的加劲肋,还包括面板,所述加劲肋与面板固定连接,所述翼缘部位于加劲肋远离面板的一端。
19.与现有技术相比,上述技术方案具有如下有益效果:
20.1、解决了传统开口肋惯性矩小,需要通过加焊或热轧方式形成较大下翼缘断面来增加抗弯、抗扭惯性矩的问题,另辟蹊径地采用母材折弯围成较大截面的方式,增大肋下缘截面,提高了抗扭、抗弯惯性矩,因而其抗弯扭的性能大幅提升。同时,本技术的加劲肋上部
仍采用开口截面,保留传统开口肋两侧可视、作业方便的连接优势。
21.2、加劲肋上部为腹板,下部折弯成管状,且翼缘部的尾端与腹板留有少量间隙或自然贴合的零间隙,加劲肋受力时,因翼缘部的尾端与腹板结合部在腹板的其中一侧,加劲肋下挠,翼缘部受弯产生偏向腹板中心的压合力,从而将翼缘部的尾部与腹板的结合部顶紧,并进一步截面产生微小变形,通过截面微小变形吸能,将荷载转换为闭合截面的微变,增加结构的柔韧性和应变性。同时,受力时形成半开口半闭口的截面结构,相对于传统开口肋,增加了闭口截面,其抗弯抗扭的性能大幅提升。
22.3、由于本技术翼缘部的尾端与腹板留有少量间隙或自然贴合的零间隙,不焊接或少量焊接的前提下而在荷载向前移动或撤除时,该间隙又基本恢复,不但规避了焊接疲劳因子,还形成了一个实用的耗能的动态构造,利用既有缝隙状态
‑‑
闭合顶紧
‑‑
恢复的延时效应,延长了力的作用时间,通过变形耗能还分担或减少了加劲肋与顶板连接点的原有的动载冲击能量,对加劲肋与顶板连接点的抗疲劳性能有显著的提升,且加劲肋由等厚的整块钢板经加工成型制成,用成型代替常用开口肋的焊接,不仅具有低成本,同时减少焊缝,进一步提升了抗疲劳性。
附图说明
23.图1为本技术实施例1加劲肋的立体结构示意图;
24.图2为本技术实施例1加劲肋的平面结构示意图;
25.图3为本技术实施例1加劲肋翼缘部微变形的示意图;
26.图4为图3的局部放大图;
27.图5为本技术实施例2的加劲肋的立体结构示意图;
28.图6为本技术实施例2的加劲肋的平面结构示意图;
29.图7为本技术实施例3的加劲肋的立体结构示意图;
30.图8为本技术实施例3的加劲肋的平面结构示意图;
31.图9为本技术实施例4的加劲肋的结构示意图;
32.图10为本技术实施例5的加劲板的结构示意图。
33.附图标记:1、腹板;11、波形部;2、翼缘部;20、尾端;21、第一边;22、第二边;23、第三边;3、连接板;31、连接孔;4、面板。
具体实施方式
34.下面结合附图对本技术做进一步描述。需要说明的是,在本技术的描述中,术语“横向”,“纵向”、“上”、“下”、“前”、“后”、“左”、“右”、“竖直”、“水平”、“顶”、“底”、“内”、“外”等指示的方位或位置关系为基于附图所示的方位或位置关系,仅是为了便于描述本技术和简化描述,并不是指示或暗示所指的装置或元件必须具有特定的方位,以特定的方位构造和操作,因此不能理解为对本技术的限制。
35.实施例1:
36.如图1所示,实施例1提供了一种用于加劲板的半闭口半开口的加劲肋,加劲肋为长条形,加劲肋由一张钢板成型而成,包括腹板1和翼缘部2,腹板1和翼缘部2一体相连;翼缘部2为管状,由腹板1下部的钢板成型围成管状构件,翼缘部2具有与腹板1靠拢的尾端20。
如图4的局部放大图所示,尾端20与腹板1留有少量间隙或自然贴合,尾端20与腹板1的距离为0~15mm。尾端20与腹板1之间不焊接,也可局部焊接连接。
37.加劲肋上部为腹板1,下部围成管状,形成半开口半闭口的结构。相对于传统开口肋,如球扁肋需通过钢厂热轧定制,规格死板;板肋惯性矩小;l形加劲肋在受弯时远端翼缘存在翻起降效现象;t形加劲肋与l形加劲肋相似,且需热轧或焊接等,上述加劲肋均存在抗扭刚度低,且需要热轧或焊接。本技术实施例的加劲肋上部仍采用开口截面,既保留了开口肋的连接优势,不管是焊接连接或螺栓连接,由于两侧可视,作业方便,质量可控。同时通过下部折弯形成管状,增大肋下翼的缘截面,增加了远离中性轴处的用钢量,提高抗扭、抗弯惯性矩,因而其抗弯扭的性能大幅提高。
38.如图3所示,当本实施例中加劲肋受力时,面板下挠带动加劲肋下弯,通过翼缘部2的受弯,,因翼缘部2的尾端20与腹板1结合部在腹板1的其中一侧,翼缘部2受弯产生偏向腹板中心的压合力,由于在管状翼缘部2成型时,翼缘部2的尾端20与腹板1留有少量间隙或自然贴合,压合力先将翼缘部2的尾端与腹板1的结合部顶紧使截面闭合,进一步闭合截面产生微小变形,通过截面微小变形吸能,将荷载转换为截面的微变,增加结构的柔韧性和应变性。且由于翼缘部2为钢板折弯成型,自然状态下往往在合拢部位很难完全贴合,留有小缝隙,既吸收了成型误差,也给后续翼缘部2的受弯时变形留有空间,当加劲肋受载时,尾端20与腹板1能够完全顶紧,形成半开口半闭口截面,提高加劲肋的抗弯、抗扭转性能。
39.同时,加劲肋由等厚的钢板经加工成型制成,用成型减少焊接,不仅具有低成本,同时由于焊缝少,其抗疲劳性能更好。
40.由于三角形的稳定性相对其他形状更好,且加工制作简便,翼缘部2优选采用三角形截面,如图2所示,开口肋下部为一块钢板通过成型围成的三角形截面,三角形截面包括第一边21、第二边22和第三边23,第一边21与腹板1一体连接,第二边22连接第一边21和第三边23,第三边23与腹板1靠拢。第一边21和第二边22的夹角为α,α<60
°
。第一边21和第三边23的夹角为β,β大于60
°
。
41.如图3、4,当三角形截面受压或受弯时,通过三角形第一边21的下挠或弯曲,引起第二边22产生向上的力,由于第二边22偏离腹板1中心线,继而第二边22又产生一个向内的闭合力,使得原第三边23与腹板1自然闭合的少量缝隙减少和顶紧,在此过程中截面变形消耗了荷载能量,由于加劲肋往往是纵向较长的,荷载发生或移动,变形也随之发生或移动,荷载消失,变形也随之消失,在时间上具有滞后延迟效应,从而形成吸能效应,有效地减少了对加劲肋与面板连接部的应力分配,也因滞后延迟效应,降低了加劲肋与面板连接部的应力变化的速率或斜率。
42.第一边21和第二边22采用小角度的夹角α减少翼缘部2的宽度,既减少剪力滞的负面效应,又将第一边21的变形直接传递给第二边22,角度越小,传递越快越直接,对第三边23与腹板1的闭合效果也越好,这样通过上述传递路径,以不焊接或极少焊接的代价,形成了一种有耗能作用的、良好综合性能的半闭口加劲肋。第三边23与第一边1以较大角度β闭合,是直接形成闭合截面的有效手段。
43.实施例2:
44.如图5和图6所示,实施例2与实施例1的区别在于:实施例2中腹板1远离翼缘部2的一端具有波形部11,波形部11的波形方向沿加劲肋长度方向延伸,且越往腹板端部波高越
高。
45.受加劲肋板厚同肋高的高厚比限制,采用较高的梁高或肋高往往需要增加肋的板厚,这不仅增加了材料成本,更重要的是桥面系的自重过大削弱了其在大跨径桥梁中的适用性。通过在加劲肋腹板1轧制波形,增加了加劲肋腹板1的虚拟厚度,提高了加劲肋其抗剪和抗屈曲性能,同时,由于端部具有波形,加劲肋与面板焊接连接形成的焊缝由传统的单一方向的直线焊缝变为曲线焊缝,增加了焊缝的长度,同时焊缝沿多个方向延伸,受力时,总有一个有利方向承担载荷,焊缝强度增加。波形的设置显著减少了高厚比的限制条件,使得用较薄的板厚就能形成了更高性能的加劲肋。同时,波形焊缝增大了面板承力的区域,使得加劲肋的抗摇头弯矩性能几何级增加,也有利于减少加劲肋对面板的局部应力,对防止肋板给面板造成瘦马现象也有显著好处。
46.波形部11波形可以为正弦波、梯形波或折线波。正弦波形板与面板的焊道顺畅平滑,梯形波抗屈曲刚度高,折线波兼顾上述两者性能,且制作也比较简单。
47.实施例3:
48.如图7、8所示,实施例3与实施例1的区别在于:加劲肋还包括与腹板1的另一端相连的连接板3,连接板3与腹板1具有夹角φ,85
°
≤φ≤95
°
。连接板3上具有连接孔31。连接板11用于与被加劲的面板进行连接,连接时连接板11与面板贴合,既可以通过焊接固定,也可以通过螺栓连接等装配化的方式进行连接。
49.实施例4
50.如图9所示,实施例4与实施例3的区别在于:翼缘部2断面为多边形。多边形截面相对于底部为尖角的三角形截面,多边形底部通常为板状,可以作为与其他部件形成支撑、承托的连接部。
51.实施例5:
52.如图10所示,实施例5提供了一种加劲板,包括加劲肋和面板4,加劲肋与面板固定连接,翼缘部2位于加劲肋远离面板一端。实施例5中,加劲肋与面板4通过螺栓组件连接。螺栓连接与面板4上的组合结构结合,形成下部螺杆利用腹板1防松,上部螺母利用混凝土固结的永不松动构造,本连接构造稳定可控,与传统开口肋相比,减少了每延米两侧2米的焊缝。
53.以上是本技术的优选实施方式,对于本领域的普通技术人员来说不脱离本技术原理的前提下,还可以做出若干变型和改进,这些也应视为本技术的保护范围。