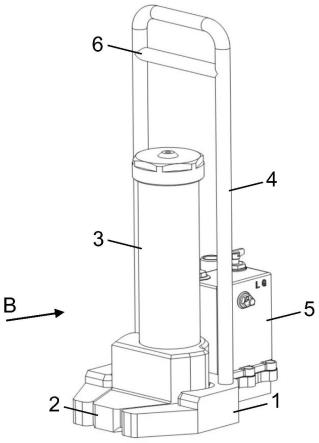
1.本发明涉及一种工务维修装置上的零部件,更具体地说,涉及一种道岔基板更换装置的液压道岔起道器。
背景技术:2.自2003年起中国铁路快速发展,截至2020年高铁里程已达3.9万公里,普铁里程也已突破十万公里,中国铁路在数量上在全球遥遥领先,为了确保在质量上也首屈一指,对工务部门的工作也提出了更高、更全面的要求。道岔作为铁路线路病害的三个重点部位之一,在工务检修中占有重要位置,不仅直接影响着线路平顺等指标,更对线路控制等影响线路安全运行有着举足轻重的影响。
3.高速铁路无砟线路道岔地段的检修和精调作业是工务部门工作的重要内容,目前国内外俊缺少专用的装置,还停留在使用传统工具勉强施工的水平,作业质量取决于操作者的责任心和技术水平,作业效率更是无法保证,一些传统工具(如齿条式千斤顶)不仅作业效果差,还存在安全隐患。
4.目前以液压为动力的各种工具使用效果好、质量稳定、安全性有保障,但普遍存在起始高度偏高、升程偏少、起升力偏小的问题,无法适应现有线路条件。
5.在道岔的岔心整体起升方面,更是缺少配套的工具,各部门虽根据各自管辖的线路特点,自行制作了少量专用夹具,但普遍存在通用性差、笨重、效率低、作业效果不好的缺点。
技术实现要素:6.针对现有技术中存在的上述缺陷,本发明的目的是提供一种道岔基板更换装置的液压道岔起道器,以解决现有技术中液压为动力工具存在的起始高度偏高、升程偏少、起升力偏小的问题。
7.为实现上述目的,本发明采用如下技术方案:
8.一种道岔基板更换装置的液压道岔起道器,包括底座、起道板、液压油缸、提把和液压动力单元;
9.所述液压油缸的活塞端、所述液压动力单元均设于所述底座上且所述液压动力单元向所述液压油缸输入压力油;
10.所述起道板设于所述液压油缸上;
11.所述提把也设于所述底座上。
12.较佳的,所述液压油缸的活塞端设于所述底座的中间位置,所述液压动力单元设于所述底座的后端位置。
13.较佳的,所述底座的前端位置至中间位置设置为中凹结构。
14.较佳的,所述起道板的上端设于所述液压油缸上,下端设置为中空结构;
15.所述起道板的下端形状与所述底座上所述中凹结构相适配。
16.较佳的,所述提把设置为u形状,倒插于所述底座上且位于所述液压油缸的外侧;
17.所述提把上还设有限位标志杆。
18.较佳的,所述液压油缸的油缸端上设有顶帽,所述顶帽与所述限位标志杆相配合。
19.较佳的,所述液压动力单元包括油箱,以及设于其内的柱塞总成和泵座总成;
20.所述油箱设于所述底座的后端位置;
21.所述柱塞总成和所述泵座总成相配合。
22.较佳的,所述底座内开设有连通所述泵座总成与所述液压油缸的油管通道。
23.较佳的,所述液压动力单元还包括设于所述油箱内的回油阀总成和限压阀总成。
24.较佳的,所述回油阀总成包括回油阀套、回油阀罩帽和回油阀组件;
25.所述回油阀套设于所述油箱内,所述回油阀组件设于所述回油阀套内,所述回油阀罩帽插入所述回油阀套的顶部以固定所述回油阀组件。
26.本发明所提供的一种道岔基板更换装置的液压道岔起道器,确保了作业质量和作业效率,实现了多快好省的作用。具有保证起升过程中不破坏道岔现有几何尺寸的能力,解决高铁线路道岔地段的基板更换的难题;该装置还通过结构上的合理布置,解决了轨底间距40mm工况下,道岔平顺的精调难题。采用液压作为动力源,具有操作便捷、效率高的特点,作业质量及作业安全性方面较现有施工方式也有较大提高。
附图说明
27.图1是本发明液压道岔起道器的立体示意图;
28.图2是本发明液压道岔起道器的俯视示意图;
29.图3是图2中a-a向的剖视示意图;
30.图4是图1中b向的示意图;
31.图5是图2中c向的示意图;
32.图6是图2中d-d向的剖视示意图;
33.图7是本发明液压道岔起道器与夹具配合使用的示意图;
34.图8是本发明液压道岔起道器单独使用的示意图。
具体实施方式
35.为了能更好地理解本发明的上述技术方案,下面结合附图和实施例进一步说明本发明的技术方案。
36.结合图1至图6所示,本发明所提供的一种道岔基板更换装置的液压道岔起道器,包括底座1、起道板2、液压油缸3、提把4和液压动力单元5。
37.液压油缸3的活塞端301、液压动力单元5均设于底座1上且液压动力单元5向液压油缸3输入压力油。
38.起道板2设于液压油缸3上,当液压动力单元5向液压油缸3输入压力油时,起道板2、液压油缸3与底座1之间发生相对运动,向道岔输出起升力。
39.提把4也设于底座1上,提把4上还设有限位标志杆6。
40.液压油缸3的活塞端301设于底座1的中间位置,液压动力单元5设于底座1的后端位置。
41.底座1的前端位置至中间位置设置为中凹结构,可容纳起道板2,从而达到降低起道板2起始高度的目的。
42.起道板2的上端设于液压油缸3上,下端设置为中空结构,可避免与底座1固定的活塞端301之间发生干涉。
43.起道板2的下端形状与底座1上中凹结构相适配,当起道板2处于起始状态时,其底面与底座1的底面齐平。
44.提把4设置为u形状,倒插于底座1上且位于液压油缸3的外侧,并再通过插销401加以固定。
45.液压油缸3的油缸端上设有顶帽7,顶帽7与限位标志杆6相配合,可防止起道板2在起升过程中超过额定升程,造成危险。
46.液压油缸3与底座1之间的接缝位置、液压油缸3与顶帽7的接缝位置以及液压油缸3内部的接缝位置设置多条o型圈8,以防止液压油的外泄。其中在液压油缸3内部的最上方o型圈8位置上配有碗形垫9。
47.顶帽7通过螺钉10固定在液压油缸3的油缸端上,螺钉10又再通过钢球11以旋拧限位。
48.液压动力单元5包括油箱501,以及设于其内的柱塞总成502和泵座总成503。
49.油箱501设于底座1的后端位置,通过螺钉504固定在底座1上,螺钉504又再通过钢球505以旋拧限位。
50.油箱501与底座1之间的接缝位置上设有油箱垫507,以防止液压油外泄。
51.柱塞总成502的上端通过连接板506相连,柱塞总成502的下端与和泵座总成503相配合。
52.底座1内开设有用以连通泵座总成503与液压油缸3的油管通道508,油管通道508与泵座总成503之间的接缝位置上设有o型圈509,以防止液压油外泄。
53.液压动力单元5还包括设于油箱501内的回油阀总成和限压阀总成510。
54.回油阀总成包括回油阀套511、回油阀罩帽512和回油阀组件513。
55.回油阀套511设于油箱501内,回油阀组件513设于回油阀套511内,回油阀罩帽512插入回油阀套511的顶部用以固定回油阀组件153。
56.回油阀罩帽512与油箱501之间的接缝位置上设有o型圈514、尼龙垫片515,以防止液压油外泄。
57.回油阀组件513与油箱501之间的接缝位置上设有o型圈516、钢垫517、钢球518,以防止液压油外泄。
58.限压阀总成510与油箱501之间的接缝位置上设有铜垫圈519,以防止液压油外泄。
59.油箱501上还设有放气加油螺塞520,其上配有尼龙垫片521,以防止液压油外泄。
60.结合图7所示,本发明液压道岔起道器100在进行作业时与更换夹具200配合使用,具体如下:
61.s1、现场可布置多套更换夹具200,将更换夹具200中的主夹具体从道岔300的下部穿过;
62.s2、将更换夹具200中的活动夹具体通过销轴与主夹具体连接安装;
63.s3、将更换夹具200上的其余部分(如压杆、夹具体螺杆和限位结构等)连接安装完
毕;
64.s4、在每套更换夹具200的端部的下部布置本发明液压道岔起道器100,即可开始道岔举升作业,将道岔下的旧基板抽出,新基板换入。
65.结合图8所示,本发明液压道岔起道器100不但可与更换夹具200配合进行道岔举升作业,还可独立进行道岔300的举升作业,完成线路的精调作业。
66.液压道岔起道器100进行起重作业时,起道板2的前端面必须与钢轨轨底侧面紧贴,或必须与更换夹具200的两端面紧贴,这样起道板2不会发生旋转,可顺利回落到底座1的中凹结构中。
67.本技术领域中的普通技术人员应当认识到,以上的实施例仅是用来说明本发明,而并非用作为对本发明的限定,只要在本发明的实质精神范围内,对以上所述实施例的变化、变型都将落在本发明的权利要求书范围内。