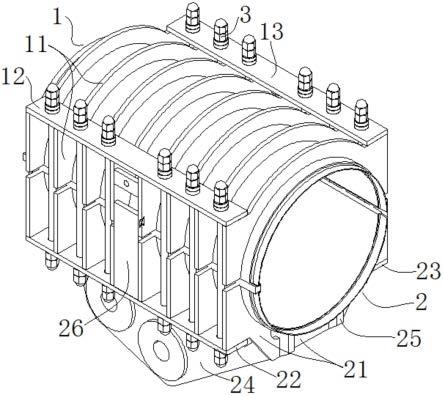
1.本实用新型涉及悬索桥的索夹,具体是一种肋传力方式的索夹结构。
背景技术:2.在悬索桥结构中,桥面的动、静载荷经吊索(吊杆)传递给主缆,而吊索与主缆之间的连接,是通过抱紧在主缆上的索夹实现。因此,索夹的成型质量及与主缆之间抱紧连接的可靠性,直接攸关着悬索桥的使用稳定性和安全性。
3.根据索夹的成型材质不同,可以分为铸造式索夹(例如中国专利文献公开的名称为“一种销接式索夹”、公开号cn 202969271 u、公开日2013年06月05日的技术等),以及焊接式索夹(例如中国专利文献公开的名称为“一种全焊式索夹、公开号cn 107217595 a、公开日2017年09月29日的技术等)。根据索夹与吊索之间连接结构形式的不同,可以分为骑跨式索夹(例如中国专利文献公开的名称为“一种骑跨式索夹”、公开号cn 202969272 u、公开日2013年06月05日的技术等),以及销接式索夹(例如前述公开号cn 202969271 u的技术等)。
4.目前,在悬索桥结构中,无论采用哪种结构形式的索夹,其与主缆之间的抱紧连接通常为壳传力方式实现,即组成索夹的相邻半体的对接承压平台之间所穿装锁合螺栓副的锁紧力,由各半体直接的、基本均匀的作用于主缆上,从而实现索夹在主缆上的抗滑承载抱紧。
5.索夹在主缆上的抗滑承载力,主要取决于主缆与索夹之间的摩擦系数、高强度锁合螺栓副的有效紧固力、以及索夹对主缆的横向压力。壳传力方式的索夹,虽然能够通过各半体将锁合螺栓副的锁紧力直接的、基本均匀的作用于主缆上,但其不利于提高索夹对主缆的横向压力实现,从而在桥面活载变化过程,中随着主缆结构形态及直径的变化,容易影响索夹在主缆上的抗滑承载力。
6.具体而言,在悬索桥的桥面活载大幅度变化过程中,特别是极端变化过程中,由于泊松效应,主缆的轴向拉伸会在一定程度上引起缆体的结构形态变化及缆体直径的减小,这会导致高强度锁合螺栓副的有效紧固力减小,索夹对主缆的横向压力衰减,从而降低了索夹在主缆上的抗滑承载力。
7.中国专利文献公开了一种名称为“一种卡箍式悬索桥索夹”(公开号cn 204282218 u,公开日2015年04月22日)的技术,在该技术中,具体披露了将组成索夹的上半体通过骑跨在外周的多根u形螺栓周向对接组合在下半体上,形成卡箍式周向对接组合。
8.该技术在理论上,通过骑跨于上半体外周的各u形螺栓,在一定程度上可使上半体在主缆上实现肋传力方式的应力相对集中排布。但是,该技术的上半体肋传力实现,需要依赖于u形螺栓在上半体外周的向下拉力,u形螺栓与上半体外周的高精度匹配度,以及上半体的受压屈服高精度的匹配于u形螺栓的锁紧,这在实际应用中很难满足技术要求。即便是满足,对u形螺栓两端的向下下拉,作用于上半体外周的肋传力微乎其微,而且,在u形螺栓作用之下,仅能使组成索夹的上半体在主缆上实现肋传力,下半体在主缆上依然是壳传力。
9.因此,该技术在主缆上很难实现肋传力,即便实现亦是非常有限的,不利于提高索夹对主缆的横向压力,在桥面活载变化过程中随着主缆结构形态及直径的变化,容易影响索夹在主缆上的抗滑承载力。
技术实现要素:10.本实用新型的技术目的在于:针对上述索夹与主缆之间配合关系的特殊性和主缆在悬索桥桥面活载中受力的特殊性,以及现有索夹结构的技术不足,提供一种能够有效提高索夹对主缆横向压力,索夹在主缆上的抗滑承载力可靠的肋传力式索夹。
11.本实用新型实现其技术目的所采用的技术方案是,一种肋传力式索夹,包括索夹上半和索夹下半;
12.所述索夹上半的外周,沿着轴向间距排布有多道顺着圆周凸起成型的上侧肋条;这些上侧肋条对应于所述索夹上半径向侧部的区域,组成能够穿装锁合螺栓副的上侧承压部;
13.所述索夹下半的外周,沿着轴向间距排布有多道顺着圆周凸起成型的下侧肋条;这些下侧肋条对应于所述索夹下半径向侧部的区域,组成能够穿装锁合螺栓副的下侧承压部。
14.上述技术措施,通过索夹上半和索夹下半外周的对应肋条,承载锁合螺栓副的周向对接组合锁紧力,使锁紧力经上侧肋条和下侧肋条作用于对应半体上,再由半体作用于主缆上,一方面能够确保索夹上半和索夹下半的轴向及周向均能全面受力抱紧主缆,二方面能够在对应肋条所在位置的索夹上半和索夹下半的轴向各节点处产生应力集中,从而在索夹的轴向上产生类似于波浪形集中传力的锁紧应力,进而使索夹对所抱紧主缆沿着轴向产生多节点的横向压力。如此,悬索桥桥面在正常活载范围内,上述技术措施的索夹与壳传力式索夹基本一致的牢固抱紧于主缆上,且整个索夹的刚性可靠、结构强度高;当悬索桥桥面的活载变大、甚至产生极端变化时,索夹通过轴向多节点的横向压力,稳固作用于泊松效应之下的主缆上,受力结构稳定,保障了索夹在主缆上的抗滑承载力。
15.上述技术措施相较于公开号cn 204282218 u的技术而言,不仅可靠易行,而且在上、下半体的轴向上均产生类似于波浪形集中传力的锁紧应力,使索夹的整个环周对所抱紧主缆沿着轴向产生多节点的横向压力,进而可靠提高索夹在主缆上的抗滑承载力。
16.作为优选方案之一,所述上侧肋条对应于所述索夹上半径向侧部的顶部区域,具有横折外延成型、用作连接上侧承压板的平台部;
17.所述索夹上半径向同一侧的至少相邻两道上侧肋条的平台部之间,连接有同一块上侧承压板,所述上侧承压板对应于相邻两道上侧肋条之间的区域开设有能够穿装锁合螺栓副的螺栓孔;
18.所述下侧肋条对应于所述索夹下半径向侧部的底部区域,具有横折外延成型、用作连接下侧承压板的平台部;
19.所述索夹下半径向同一侧的至少相邻两道下侧肋条的平台部之间,连接有同一块下侧承压板,所述下侧承压板对应于相邻两道下侧肋条之间的区域开设有能够穿装锁合螺栓副的螺栓孔。
20.上述技术措施,在索夹周向对接组合处所形成的承压平台结构,不仅成型结构简
单、便于成型,而且能够使锁合螺栓副的锁紧力必经对应肋条可靠地传递给索夹上半/索夹下半,清晰、可靠地形成锁合压力经肋条-对应半体-主缆的传递路径,在对应肋条所在位置的索夹上半/索夹下半的轴向各节点处明显、可靠地产生应力集中,从而使索夹对所抱紧主缆沿着轴向可靠地产生多节点的横向压力,通过增大索夹对主缆的横向压力而可靠提高索夹在主缆上的抗滑承载力。
21.进一步的,所述索夹上半上的各道上侧肋条,与所述索夹下半上的各道下侧肋条之间呈一一对应配合关系;
22.所述索夹下半径向同一侧的至少相邻两道下侧肋条之间,具有向上延伸的定位板;
23.在所述索夹上半与所述索夹下半的环周对接组合过程中,所述索夹下半上的定位板嵌入所述索夹上半上的、对应的相邻两道上侧肋条之间。
24.或者,作为定位板排布结构形式的另一种优选方案,所述索夹上半上的各道上侧肋条,与所述索夹下半上的各道下侧肋条之间呈一一对应配合关系;
25.所述索夹上半径向同一侧的至少相邻两道上侧肋条之间,具有向下延伸的定位板;
26.在所述索夹上半与所述索夹下半的环周对接组合过程中,所述索夹上半上的定位板嵌入所述索夹下半上的、对应的相邻两道下侧肋条之间。
27.亦或者,作为定位板排布结构形式的可能替代方案,所述索夹上半上的各道上侧肋条,与所述索夹下半上的各道下侧肋条之间呈一一对应配合关系;
28.所述索夹上半径向同一侧的至少相邻两道上侧肋条之间具有向下延伸的定位板;
29.所述索夹下半径向同一侧的至少相邻两道下侧肋条之间具有向上延伸的定位板,且所述索夹下半上的定位板与所述索夹上半上的定位板错位排布;
30.在所述索夹上半与所述索夹下半的环周对接组合过程中,所述索夹上半上的定位板嵌入所述索夹下半上的、对应的相邻两道下侧肋条之间,所述索夹下半上的定位板嵌入所述索夹上半上的、对应的相邻两道上侧肋条之间。
31.上述技术措施,一方面在索夹上半与索夹下半的周向对接组合过程中,能够通过定位板可靠地实现二者的轴向相对定位,以有利于周向对接组合操作轻松、高效实现;二方面有利于辅助肋条和锁合螺栓副提高整个索夹的结构强度。
32.进一步的,所述定位板排布在所述索夹下半/所述索夹上半的轴向中部区域。该技术措施,更有利于索夹上半与索夹下半在周向对接组合过程中的轴向相对定位操作。
33.作为优选方案之一,所述索夹上半与所述索夹下半在环周对接组合过程中,以直边结构的中分结合面进行对接组合;
34.所述索夹上半的上侧承压板上的螺栓孔,处在所述索夹上半的中分结合面外侧处;
35.所述索夹下半的下侧承压板上的螺栓孔,处在所述索夹下半的中分结合面外侧处。
36.上述技术措施有利于索夹在主缆上的密封作业,对布置在上、下半体中分结合面处的密封结构要求低,而且布置在上、下半体中分结合面处的密封结构能够有效阻却外界对缆孔内部的侵蚀,密封效果好。
37.作为优选方案之一,所述索夹下半的底部,沿着径向间距排布有至少两组顺着轴长凸起成型的耳板;
38.每一组耳板上开设有至少一个用作销接吊索/吊杆的销孔。
39.上述技术措施,通过两组耳板在索夹下半底部的间距排布,使得耳板成型位置避免在索夹下半上对中,在悬索桥结构中对作用于索夹下半上的载荷进行横向分力,可靠防止索夹下半在载荷作用之下于主缆上的脱空现象发生,进一步提高索夹在主缆上的抗滑承载力。
40.进一步的,所述索夹为钢板焊接组合结构;
41.所述索夹下半底部的各组耳板,将所述索夹下半外周排布的下侧肋条沿着径向分为多段,下侧肋条的相邻两段焊接在对应耳板的左右两侧。
42.上述技术措施以钢板作为原材料成型索夹,有效地避免了铸造材料所存在的技术缺陷。其相较于铸造成型式索夹而言,钢板成型式索夹具有成型技术难度小、成型效率高、成型成本低、耐温范围大等特点。
43.再进一步的,所述索夹下半底部的耳板为间距排布的两组,这两组耳板将所述索夹下半外周排布的下侧肋条沿着径向分为下侧边部肋板一、下侧中部肋板和下侧边部肋板二三段,且所述下侧中部肋板的宽度至少是所述下侧边部肋板一/所述下侧边部肋板二宽度的一倍。该技术措施在索夹下半底部所形成的双耳板结构,不仅耳板与索夹下半之间的结构强度高、受力结构稳定,而且在悬索桥结构中对作用于索夹下半上的载荷进行行之有效的横向可靠分力,索夹下半底部的横向两侧受力基本区域均衡、稳定,有效防止了索夹下半在主缆上发生变形脱空而使索夹在主缆上松动的技术问题发生,显著提高了索夹在主缆上的抗滑承载力。
44.本实用新型的有益技术效果是:上述技术措施通过索夹上半和索夹下半外周的对应肋条,承载锁合螺栓副的周向对接组合锁紧力,使锁紧力经上侧肋条和下侧肋条作用于对应半体上,再由半体作用于主缆上,一方面能够确保索夹上半和索夹下半的轴向及周向均能全面受力抱紧主缆,二方面能够在对应肋条所在位置的索夹上半和索夹下半的轴向各节点处产生应力集中,从而在索夹的轴向上产生类似于波浪形集中传力的锁紧应力,进而使索夹对所抱紧主缆沿着轴向产生多节点的横向压力。如此,悬索桥桥面在正常活载范围内,上述技术措施的索夹与壳传力式索夹基本一致的牢固抱紧于主缆上,且整个索夹的刚性可靠、结构强度高;当悬索桥桥面活载变大、甚至产生极端变化时,索夹通过轴向多节点的横向压力,稳固作用于泊松效应之下的主缆上,受力结构稳定,保障了索夹在主缆上的抗滑承载力。
附图说明
45.图1为本实用新型的一种结构示意图。
46.图2为图1的轴端视图。
47.图3为图2中的索夹上半的结构示意图。
48.图4为图2中的索夹下半的结构示意图。
49.图中代号含义:1—索夹上半;11—上侧肋条;12—上侧承压板一;13—上侧承压板二;2—索夹下半;21—下侧肋条;211—下插边部肋板一;212—下侧中部肋板;213—下侧边
部肋板二;22—下侧承压板一;23—下侧承压板二;24—耳板一;25—耳板二;26—定位板;3—锁合螺栓副。
具体实施方式
50.本实用新型涉及悬索桥的索夹,具体是一种肋传力方式的索夹结构,下面以多个实施例对本实用新型的技术内容进行详细说明,其中,实施例1结合说明书附图-即图1、图2、图3和图4对本实用新型的技术方案内容进行清楚、详细的阐释;其它实施例虽未单独绘制附图,但其主体结构仍可参照实施例1的附图。
51.在此需要特别说明的是,本实用新型的附图是示意性的,其为了清楚本实用新型的技术目的已经简化了不必要的细节,以避免模糊了本实用新型贡献于现有技术的技术方案。
52.实施例1
53.参见图1、图2、图3和图4所示,本实用新型包括索夹上半1和索夹下半2。
54.具体的,索夹上半1的本体为钢板卷制或冲压成型的半环状弧型板结构,具有直边结构的中分结合面。
55.索夹上半1的本体内轮廓基本匹配于所要抱紧的悬索桥主缆外轮廓。
56.在索夹上半1的本体外周处,焊接有多道径向外凸成型的上侧肋条11。也就是说,在索夹上半1的外周,沿着其轴向(即索夹上半1的长度方向),间距排布有多道上侧肋条11,每一道上侧肋条11顺着索夹上半1的圆周方向向外凸起成型,每一道上侧肋条11采用钢板裁切而成。通常情况下,相邻上侧肋条11之间的排布间距,约为上侧肋条11厚度的4~10倍(例如5倍、7倍或10倍等),排布间距过小不利于下述锁合螺栓副的连接操作,以及不利于肋传力在轴向上的各应力集中节点形成,排布间距过大则容易影响索夹在主缆上的整体抱紧力;上侧肋条11在索夹上半1外周的径向凸起高度,约为索夹上半1厚度的2~5倍(例如3倍、4倍或5倍等),凸起过小不利于肋传力的应力集中节点形成,凸起过大则容易影响肋条受力的结构刚度。
57.在上述索夹上半1的成型结构中,各道上侧肋条11的两端分别延伸至索夹上半1的中分结合面处,基本与索夹上半1的对应侧中分结合面保持齐平,且各道上侧肋条11的两端亦分别从索夹上半1的径向(即横向)对应侧径向外凸延伸。
58.在上侧肋条11对应于索夹上半1径向侧部的两端上方顶部区域,分别具有横折外延成型、用作连接下述上侧承压板一12和上侧承压板二13的平台部。也就是说,上侧肋条11具有处在索夹上半1横向两侧的上方顶部的平台部,每侧平台部的根部基本处在下方的索夹上半1侧部的内侧附近,这样有利于锁合螺栓副的锁紧力通过上侧肋条11有效地作用于索夹上半1上;每侧平台部的高度基本大于索夹上半1半径的0.7倍,这样有利于锁合螺栓副周向组合对接下的索夹上半1和索夹下半2对主缆抱紧,两侧平台部沿着索夹上半1的横向中心基本对称排布;两侧平台部之间的上侧肋条11顶边为弧形拱边结构,以高于两侧平台部成型,外形美观。
59.沿着上述索夹上半1的长度,在各道上侧肋条11的两端平台部上对应焊接有上侧承压板一12和上侧承压板二13,即上侧承压板一12焊接在各道上侧肋条11的左端平台部上,将各道上侧肋条11的左端平台部串联;上侧承压板二13焊接在各道上侧肋条11的右端
平台部上,将各道上侧肋条11的右端平台部串联。
60.在相邻两道上侧肋条11之间所对应的上侧承压板一12的中心区域处,开设有能够穿装锁合螺栓副3的螺栓孔,上侧承压板一12上的、各相邻两道上侧肋条11之间的螺栓孔基本处在同一直线上,且须处在下方索夹上半1对应侧的外侧,不对下方索夹上半1的中分结合面造成位置干扰。在相邻两道上侧肋条11之间所对应的上侧承压板二13的中心区域处,开设有能够穿装锁合螺栓副3的螺栓孔,上侧承压板二13上的、各相邻两道上侧肋条11之间的螺栓孔基本处在同一直线上,且须处在下方索夹上半1对应侧的外侧,不对下方索夹上半1的中分结合面造成位置干扰。
61.上述索夹上半1本体的钢板厚度、上侧肋条11的钢板厚度、上侧承压板一12的钢板厚度、以及上侧承压板二13的厚度,基本一致。
62.索夹下半2的本体为钢板卷制或冲压成型的半环状弧型板结构,具有直边结构的中分结合面。
63.索夹下半2的本体内轮廓基本匹配于所要抱紧的悬索桥主缆外轮廓,且与上述索夹上半1的弧型宽度及轴向长度基本对应一致。
64.在索夹下半2的本体外周,沿着径向的宽度方向间距焊接有两组耳板,即耳板一24和耳板二25,这两组耳板分处在索夹下半2的横宽中心两侧,且两组耳板至索夹下半2横宽中心的距离,大于两组耳板至索夹下半2对应侧外侧的距离,通常,至横宽中心的距离约为至对应侧外侧距离的1~4倍(例如2倍、3倍或4倍等,优选2~3倍),这样有利于防止受力的索夹下半1在主缆上脱空。
65.耳板一24和耳板二25在索夹下半2的外周底部,顺着索夹下半2的长度方向向下外凸成型,耳板一24和耳板二25上分别开设有至少一个用作销接对应吊索的销孔。
66.在索夹下半2的本体外周处,焊接有多道径向外凸成型的下侧肋条21,要求索夹下半2上的各道下侧肋条21与上述索夹上半1上的各道上侧肋条11呈一一对应配合关系,即当上述索夹上半1与索夹下半2进行周向对接组合时,索夹下半2上的各道下侧肋条21与上述索夹上半1上的各道上侧肋条11在整个索夹的轴向上呈一一对应配合关系。
67.也就是说,在索夹下半2的外周,沿着其轴向,间距排布有多道下侧肋条21,每一道下侧肋条21顺着索夹下半2的圆周方向向外凸起成型,每一道下侧肋条21采用钢板裁切而成。基于上述索夹下半2外周的两组耳板成型,每一道下侧肋条21由两组耳板分隔为下侧边部肋板一211、下侧中部肋板212、下侧边部肋板二213三段,下侧边部肋板一211和下侧边部肋板二213分处在对应耳板的外侧,下侧中部肋板212处在两组耳板之间,下侧中部肋板212的宽度至少是下侧边部肋板一211/下侧边部肋板二213宽度的一倍,优选两至三倍。组成每一道下侧肋条21的各段肋板不仅与索夹下半2外周焊接,而且与所对应耳板的两侧亦分别焊接。各道下侧肋条21在索夹下半2外周的凸起高度,分别小于上述两组耳板在索夹下半2外周的凸起高度。
68.为了便于成型,以及有利于整个索夹的外形美观,各道下侧肋条21的底边基本为平边结构。当然,下侧肋条21在索夹下半2外周的径向凸起高度,亦基本与上述上侧肋条11在索夹上半1外周的径向凸起高度对应,即约为索夹下半2厚度的2~5倍(例如3倍、4倍或5倍等)。
69.在上述索夹下半2的成型结构中,各道下侧肋条21的两端分别延伸至索夹下半2的
中分结合面处,基本与索夹下半2的对应侧中分结合面保持齐平,且各道下侧肋条21的两端亦分别从索夹下半2的径向对应侧径向外凸延伸,向上延伸宽度与上述上侧肋条11从索夹上半1的径向对应侧径向外凸延伸宽度基本对应一致。
70.在下侧肋条21对应于索夹下半2径向侧部的两端下方底部区域,分别具有横折外延成型、用作连接下述下侧承压板一22和下侧承压板二23的平台部,各平台与所在肋板底边以斜边过渡,例如左侧平台与下侧边部肋板一211的底边之间斜边过渡,右侧平台与下侧边部肋板二213的底边之间斜边过渡。也就是说,下侧肋条21具有处在索夹下半2横向两侧的下方底部的平台部,每侧平台部的根部基本处在上方的索夹下半2侧部的内侧附近,这样有利于锁合螺栓副的锁紧力通过下侧肋条21有效地作用于索夹下半2上;每侧平台部的高度基本大于索夹下半2半径的0.7倍,这样有利于锁合螺栓副周向组合对接下的索夹上半1和索夹下半2对主缆抱紧,两侧平台部沿着索夹下半2的横向中心基本对称排布。
71.沿着上述索夹下半2的长度,在各道下侧肋条21的两端平台部上对应焊接有下侧承压板一22和下侧承压板二23,即下侧承压板一22焊接在各道下侧肋条21的左端平台部上,将各道下侧肋条21的左端平台部串联;下侧承压板二23焊接在各道下侧肋条21的右端平台部上,将各道下侧肋条21的右端平台部串联。
72.在相邻两道下侧肋条21之间所对应的下侧承压板一22的中心区域处,开设有能够穿装锁合螺栓副3的螺栓孔,下侧承压板一22上的、各相邻两道下侧肋条21之间的螺栓孔基本处在同一直线上,且须处在上方索夹下半2对应侧的外侧,不对上方索夹下半2的中分结合面造成位置干扰;同时,当上述索夹上半1与索夹下半2进行周向对接组合时,上述上侧承压板一12上的各螺栓孔与下侧承压板一22上的各螺栓孔在上下位呈一一对应配合关系。在相邻两道下侧肋条21之间所对应的下侧承压板二23的中心区域处,开设有能够穿装锁合螺栓副3的螺栓孔,下侧承压板二23上的、各相邻两道下侧肋条21之间的螺栓孔基本处在同一直线上,且须处在上方索夹下半2对应侧的外侧,不对上方索夹下半2的中分结合面造成位置干扰;同时,当上述索夹上半1与索夹下半2进行周向对接组合时,上述上侧承压板二13上的各螺栓孔与下侧承压板二23上的各螺栓孔在上下位呈一一对应配合关系。
73.上述索夹下半2本体的钢板厚度、下侧肋条21的钢板厚度、下侧承压板一22的钢板厚度、以及下侧承压板二23的厚度,基本一致。耳板一24和耳板二25的厚度分别较厚。
74.上述结构的索夹在悬索桥结构的主缆上应用时,索夹上半1排布于主缆的相对上侧,索夹下半2排布于主缆的相对下侧,二者周向对接组合,并由两侧上下位配合的承压板上的各一一对应螺栓孔内所穿装的锁合螺栓副3锁紧,锁合螺栓副3处在索夹上、下两半的直边中分结合面外侧,在直边中分结合面处的密封不受螺栓排布结构的干扰,密封便于成型,亦有利于维持长效。
75.为了提高索夹上半1与索夹下半2之间周向对接组合的便利性,提高对准度及组合结构强度,索夹下半2的径向每一侧,焊接有竖直向上延伸的定位板26,该定位板26竖向排布于索夹下半2的轴向中部处,处在相邻两道下侧肋条21之间。前述每一侧定位板26的向上延伸高度,向上超出各下侧肋条21的顶部,在索夹上半1与索夹下半2的环周对接组合过程中,索夹下半2两侧的定位板26能够嵌入索夹上半1两侧的、对应的相邻两道上侧肋条11之间。为了防止定位板26与锁合螺栓副3位置干涉,可以在定位板26所在区域不开设螺栓孔,即不排布锁合螺栓副,基于此考虑,定位板26在索夹下半2的轴向中部处排布最有利于平衡
受力。
76.为了有利于检修道在索夹上的连接,最好在上述定位板26所对应索夹上半1的相邻两道上侧肋条11之间焊接一块连接板,该连接板处在定位板26的上方,连接板上开设有螺栓孔等连接必要结构。
77.实施例2
78.本实用新型包括索夹上半和索夹下半。
79.具体的,索夹上半的本体为钢板卷制或冲压成型的半环状弧型板结构,具有直边结构的中分结合面。
80.索夹上半的本体内轮廓基本匹配于所要抱紧的悬索桥主缆外轮廓。
81.在索夹上半的本体外周处,焊接有多道径向外凸成型的上侧肋条。也就是说,在索夹上半的外周,沿着其轴向(即索夹上半的长度方向),间距排布有多道上侧肋条,每一道上侧肋条顺着索夹上半的圆周方向向外凸起成型,每一道上侧肋条采用钢板裁切而成。通常情况下,相邻上侧肋条之间的排布间距,约为上侧肋条厚度的4~10倍(例如5倍、7倍或10倍等),排布间距过小不利于下述锁合螺栓副的连接操作,以及不利于肋传力在轴向上的各应力集中节点形成,排布间距过大则容易影响索夹在主缆上的整体抱紧力;上侧肋条在索夹上半外周的径向凸起高度,约为索夹上半厚度的2~5倍(例如3倍、4倍或5倍等),凸起过小不利于肋传力的应力集中节点形成,凸起过大则容易影响肋条受力的结构刚度。
82.在上述索夹上半的成型结构中,各道上侧肋条的两端分别延伸至索夹上半的中分结合面处,基本与索夹上半的对应侧中分结合面保持齐平,且各道上侧肋条的两端亦分别从索夹上半的径向(即横向)对应侧径向外凸延伸。
83.在上侧肋条对应于索夹上半径向侧部的两端上方顶部区域,分别具有横折外延成型、用作连接下述上侧承压板一和上侧承压板二的平台部。也就是说,上侧肋条具有处在索夹上半横向两侧的上方顶部的平台部,每侧平台部的根部基本处在下方的索夹上半侧部的内侧附近,这样有利于锁合螺栓副的锁紧力通过上侧肋条有效地作用于索夹上半上;每侧平台部的高度基本大于索夹上半半径的0.7倍,这样有利于锁合螺栓副周向组合对接下的索夹上半和索夹下半对主缆抱紧,两侧平台部沿着索夹上半的横向中心基本对称排布;两侧平台部之间的上侧肋条顶边为弧形拱边结构,以高于两侧平台部成型,外形美观。
84.沿着上述索夹上半的长度,在各道上侧肋条的两端平台部上对应焊接有上侧承压板一和上侧承压板二,即上侧承压板一焊接在各道上侧肋条的左端平台部上,将各道上侧肋条的左端平台部串联;上侧承压板二焊接在各道上侧肋条的右端平台部上,将各道上侧肋条的右端平台部串联。
85.在相邻两道上侧肋条之间所对应的上侧承压板一的中心区域处,开设有能够穿装锁合螺栓副的螺栓孔,上侧承压板一上的、各相邻两道上侧肋条之间的螺栓孔基本处在同一直线上,且须处在下方索夹上半对应侧的外侧,不对下方索夹上半的中分结合面造成位置干扰。在相邻两道上侧肋条之间所对应的上侧承压板二的中心区域处,开设有能够穿装锁合螺栓副的螺栓孔,上侧承压板二上的、各相邻两道上侧肋条之间的螺栓孔基本处在同一直线上,且须处在下方索夹上半对应侧的外侧,不对下方索夹上半的中分结合面造成位置干扰。
86.上述索夹上半本体的钢板厚度、上侧肋条的钢板厚度、上侧承压板一的钢板厚度、
以及上侧承压板二的厚度,基本一致。
87.索夹下半的本体为钢板卷制或冲压成型的半环状弧型板结构,具有直边结构的中分结合面。
88.索夹下半的本体内轮廓基本匹配于所要抱紧的悬索桥主缆外轮廓,且与上述索夹上半的弧型宽度及轴向长度基本对应一致。
89.在索夹下半的本体外周,焊接有一组耳板,该耳板处在索夹下半的横宽中心处。耳板在索夹下半的外周底部,顺着索夹下半的长度方向向下外凸成型。耳板上开设有至少一个用作销接对应吊索的销孔。
90.在索夹下半的本体外周处,焊接有多道径向外凸成型的下侧肋条,要求索夹下半上的各道下侧肋条与上述索夹上半上的各道上侧肋条呈一一对应配合关系,即当上述索夹上半与索夹下半进行周向对接组合时,索夹下半上的各道下侧肋条与上述索夹上半上的各道上侧肋条在整个索夹的轴向上呈一一对应配合关系。
91.也就是说,在索夹下半的本体外周,沿着其轴向,间距排布有多道下侧肋条,每一道下侧肋条顺着索夹下半的圆周方向向外凸起成型,每一道下侧肋条采用钢板裁切而成。基于上述索夹下半外周的耳板排布结构,每一道下侧肋条由耳板分隔为下侧左部肋板和下侧右部肋板两段,下侧左部肋板和下侧右部肋板分处在耳板的外侧。组成每一道下侧肋条的两段肋板不仅与索夹下半外周焊接,而且与耳板的两侧亦分别焊接。各道下侧肋条在索夹下半外周的凸起高度,分别小于上述耳板在索夹下半外周的凸起高度;当然,下侧肋条在索夹下半外周的径向凸起高度,亦基本与上述上侧肋条在索夹上半外周的径向凸起高度对应,即约为索夹下半厚度的2~5倍(例如3倍、4倍或5倍等)。
92.在上述索夹下半的成型结构中,各道下侧肋条的两端分别延伸至索夹下半的中分结合面处,基本与索夹下半的对应侧中分结合面保持齐平,且各道下侧肋条的两端亦分别从索夹下半的径向对应侧径向外凸延伸,向上延伸宽度与上述上侧肋条从索夹上半的径向对应侧径向外凸延伸宽度基本对应一致。
93.在下侧肋条对应于索夹下半径向侧部的两端下方底部区域,分别具有横折外延成型、用作连接下述下侧承压板一和下侧承压板二的平台部。也就是说,下侧肋条具有处在索夹下半横向两侧的下方底部的平台部,每侧平台部的根部基本处在上方的索夹下半侧部的内侧附近,这样有利于锁合螺栓副的锁紧力通过下侧肋条有效地作用于索夹下半上;每侧平台部的高度基本大于索夹下半半径的0.7倍,这样有利于锁合螺栓副周向组合对接下的索夹上半和索夹下半对主缆抱紧,两侧平台部沿着索夹下半的横向中心基本对称排布;两侧平台部之间的下侧肋条顶边为弧形拱边结构,以低于两侧平台部成型,外形美观。
94.沿着上述索夹下半的长度,在各道下侧肋条的两端平台部上对应焊接有下侧承压板一和下侧承压板二,即下侧承压板一焊接在各道下侧肋条的左端平台部上,将各道下侧肋条的左端平台部串联;下侧承压板二焊接在各道下侧肋条的右端平台部上,将各道下侧肋条的右端平台部串联。
95.在相邻两道下侧肋条之间所对应的下侧承压板一的中心区域处,开设有能够穿装锁合螺栓副的螺栓孔,下侧承压板一上的、各相邻两道下侧肋条之间的螺栓孔基本处在同一直线上,且须处在上方索夹下半对应侧的外侧,不对上方索夹下半的中分结合面造成位置干扰;同时,当上述索夹上半与索夹下半进行周向对接组合时,上述上侧承压板一上的各
螺栓孔与下侧承压板一上的各螺栓孔在上下位呈一一对应配合关系。在相邻两道下侧肋条之间所对应的下侧承压板二的中心区域处,开设有能够穿装锁合螺栓副的螺栓孔,下侧承压板二上的、各相邻两道下侧肋条之间的螺栓孔基本处在同一直线上,且须处在上方索夹下半对应侧的外侧,不对上方索夹下半的中分结合面造成位置干扰;同时,当上述索夹上半与索夹下半进行周向对接组合时,上述上侧承压板二上的各螺栓孔与下侧承压板二上的各螺栓孔在上下位呈一一对应配合关系。
96.上述索夹下半本体的钢板厚度、下侧肋条的钢板厚度、下侧承压板一的钢板厚度、以及下侧承压板二的厚度,基本一致。耳板的厚度较厚。
97.上述结构的索夹在悬索桥结构的主缆上应用时,索夹上半排布于主缆的相对上侧,索夹下半排布于主缆的相对下侧,二者周向对接组合,并由两侧上下位配合的承压板上的各一一对应螺栓孔内所穿装的锁合螺栓副锁紧,锁合螺栓副处在索夹上、下两半的直边中分结合面外侧,在直边中分结合面处的密封不受螺栓排布结构的干扰,密封便于成型,亦有利于维持长效。
98.为了提高索夹上半与索夹下半之间周向对接组合的便利性,提高对准度及组合结构强度,索夹下半的径向每一侧,焊接有竖直向上延伸的定位板,该定位板竖向排布于索夹下半的轴向中部处,处在相邻两道下侧肋条之间。前述每一侧定位板的向上延伸高度,向上超出各下侧肋条的顶部,在索夹上半与索夹下半的环周对接组合过程中,索夹下半两侧的定位板能够嵌入索夹上半两侧的、对应的相邻两道上侧肋条之间。为了防止定位板与锁合螺栓副位置干涉,可以在定位板所在区域不开设螺栓孔,即不排布锁合螺栓副,基于此考虑,定位板在索夹下半的轴向中部处排布最有利于平衡受力。
99.为了有利于检修道在索夹上的连接,最好在上述定位板所对应索夹上半的相邻两道上侧肋条之间焊接一块连接板,该连接板处在定位板的上方,连接板上开设有螺栓孔等连接必要结构。
100.实施例3
101.本实施例的其它内容与实施例1或2相同,不同之处在于:
102.定位板成型在索夹上半的径向两侧,每一侧的定位板超过上侧肋条的底部竖直向下延伸;
103.在索夹上半与索夹下半的环周对接组合过程中,索夹上半上的定位板嵌入索夹下半上的、对应的相邻两道下侧肋条之间。
104.实施例4
105.本实施例的其它内容与实施例1或2相同,不同之处在于:
106.在索夹的径向两侧分别成型有两块定位板,一块定位板成型在索夹上半的轴向中部处,以超过上侧肋条的底部竖直向下延伸;另一块定位板成型在索夹下半的轴向中部处,以超过下侧肋条的顶部竖直向上延伸,且索夹下半上的定位板与索夹上半上的定位板呈轴向错位排布;这两块定位板在索夹同一侧的中部处以间距排布,它们之间至少隔有一组螺栓孔,从而避免它们紧邻排布情况下因没有螺栓锁合而导致的锁合力缺失;
107.在索夹上半与索夹下半的环周对接组合过程中,索夹上半上的定位板嵌入索夹下半上的、对应的相邻两道下侧肋条之间,索夹下半上的定位板嵌入索夹上半上的、对应的相邻两道上侧肋条之间。
108.实施例5
109.本实施例的其它内容与实施例1、2、3或4相同,不同之处在于:
110.索夹上半的本体、索夹上半的各道上侧肋条、以及可能存在的定位板等分别为铸造一体成型结构;各道上侧肋条在索夹上半同一侧所形成的上侧承压平台,焊接有同一块能够将各道上侧肋条串联起来的上侧承压板,上侧承压板为钢板结构;
111.索夹下半的本体、索夹下半的各道下侧肋条、以及可能存在的定位板等分别为铸造一体成型结构;各道下侧肋条在索夹下半同一侧所形成的上侧承压平台,焊接有同一块能够将各道下侧肋条串联起来的下侧承压板,下侧承压板为钢板结构。
112.以上各实施例仅用以说明本实用新型,而非对其限制;
113.尽管参照上述各实施例对本实用新型进行了详细的说明,本领域的普通技术人员应当理解:本实用新型依然可以对上述各实施例中的具体技术方案进行修改,或者对其中部分技术特征进行等同替换,例如上侧肋条同一侧的上侧承压板在长度方向上有多块对接(对接部位处在同一道上侧肋条的端部)等,而这些修改或者替换,并不使相应技术方案的本质脱离本实用新型的精神和范围。