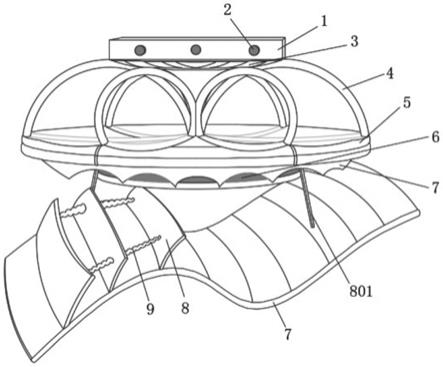
1.本发明涉及机器人焊接技术领域,具体为一种适合机器人焊接的节点模型构建方法及装置。
背景技术:2.机器人焊接在各行各业得到了一些广泛的应用,甚至部分实现自动焊接,但是它所应用的面和点都很窄,只适合在特定工作环境下对特定的构件实现机器人专机焊接,但是对于企业焊接场景中的实际需求来说是远远不够的,更别说推广。
3.实现机器人焊接的痛点主要集中在以下几个方面:一,成熟的焊接工作站一般都是国外品牌,企业引进成本过高,可选择余地小;二,目前国内外的焊接工作站只能解决一些成批标准的构件焊接,专机专用,产品适应性差,不易推广;三,机器人焊接技术不够智能,限定条件多、工效不能满足工厂需求;四,机器人焊前辅助工作过多,增加了离线建模、离线仿真、联机再定位再计算的工作;五,机器人焊接工艺参数、焊枪姿态控制的自动匹配复杂;六,对于非标构件和小批量工件焊接适应性差,甚至难以实现机器人焊接。
4.焊接效率低,工人干预工作量大,很难将机器人应用到非标构件的焊接场景。工件变化后,机器人适应能力差。不能自动进行焊缝位置纠偏,不能完全自动编程,不能自动适应焊接工艺变化。
5.焊接的过程中,需要根据装置的笔头来对底部的模板进行标记记号,通常无法自动导出记号笔芯,或者在导入一半的过程中导致卡壳,若是在这个过程中手动标记记号,容易跟不上焊接的速度,就会容易出现偏差,导致误差变大。
技术实现要素:6.为解决上述的问题,本发明提供如下技术方案:一种适合机器人焊接的节点模型构建方法,包括以下步骤:
7.s1、采用参数化方式创建节点模型,建模内容包括:节点位置尺寸、边界约束几何尺寸、焊接部位及形式、焊接工艺参数。
8.s2、通过节点建模将一个零件或者一个构件所涉及的所有相关参数集中到一个模型结构中,供后续计算使用,节点数据以文件形式保存。
9.s3、创建节点扫描点表,用线激光获取关键点的实际坐标值,结合节点模板中约定的几何拓扑关系计算出实际的焊缝位置边界点坐标。
10.s4、创建实际焊接路径,将焊接工艺包中的参数和机器人位姿要求消化到实际焊接路径中。
11.s5、创建焊接程序,将包含工艺信息的路径点表翻译成机器人可识别的执行程序。
12.其中,节点模板的技术步骤设计方法如下:
13.a.节点建模:创建节点模型是该方法的基础,是后续工作的参数值来源;主要包含节点类型、定位尺寸、结构尺寸、焊缝位置、焊缝范围、焊接工艺等。
14.b.扫描点表:扫描点按约定的顺序使用线激光器逐个扫描后获得机器人的三维坐标值,扫描点的位姿需事先根据节点建模信息中构件尺寸设计计算出来,扫描点的设置是根据最后需要计算的几何约束边界点来布置的,数量尽可能的少,并适当考虑线激光器在扫描运动过程中的姿态避免触碰周边结构为宜。
15.c.焊接点表:焊缝顶点坐标计算成功后,按选择焊缝范围进行焊缝的设计,根据焊缝的不同位置分别设置不同的焊接工艺包选择,平角焊缝和立焊缝分别采用不同的焊接枪姿态和焊接电流、电压、速度等参数。
16.d.焊接程序:各类机器人最后执行的对应代码程序,不同的机器人有不同的格式和语句要求。在生成焊接程序时需增加一些辅助的过渡点和回枪动作,使机器人运行起来动作流畅,减少奇异点的产生和触碰结构的风险。
17.一种适合机器人焊接的节点模型构建装置,包括支撑台,所述支撑台的侧壁处设置有控制钮,支撑台的底侧壁处贯穿连接有锁撑机构,锁撑机构的内部包括支撑盘,支撑盘的侧壁处设置有滑套,支撑盘的内侧壁轴心处贯穿连接有叠盘,叠盘的侧壁处底侧壁处贯穿连接有变形架,所述支撑盘的内侧壁处设置有软棉层,所述锁撑机构的底侧壁处贯穿连接有弹力管,弹力管的底端贯穿连接有支撑架,支撑架的底侧壁处贯穿连接有支撑垫,支撑垫的底部贯穿连接有组合机构,支撑垫的侧壁处贯穿连接有卡针,卡针的底端环连接有底座,底座的顶侧壁处摆动连接有压板,压板的侧壁处贯穿连接有拉索。
18.优选的,所述组合机构的内部包括滑板,滑板的侧壁中部贯穿连接有移位套,移位套的内侧壁处贯穿连接有弹力带,弹力带的外侧壁处贯穿连接有活动套,活动套的内侧壁处贯穿连接有激光器。
19.优选的,所述变形架的侧壁处滑动连接于软棉层的侧壁处,叠盘的侧壁处向外撑开后,叠盘的侧端可推动软棉层的侧壁使其撑起。
20.优选的,所述变形架的外端滑动贯穿连接于滑套的内侧壁处,变形架的侧壁变直后,可推动滑套的侧壁。
21.优选的,所述滑套的内侧壁处滑动连接于组合机构的外侧,滑套的侧壁受推力后可将组合机构向外推出。
22.优选的,所述压板的侧壁处滑动连接于卡针的侧壁处,压板的侧壁沿着y轴活动时,可带动卡针的侧壁一同沿着y轴移动。
23.与现有技术相比,本发明提供了一种适合机器人焊接的节点模型构建方法及装置,具备以下有益效果:
24.1、该适合机器人焊接的节点模型构建方法,本发明专门用于解决批量小、非标准构件的机器人焊接。运用节点模板技术,可将机器焊接应用到各行各业金属构件的焊接场景中,可以快速实现对构件的实施平角焊和对接焊,摆脱手工示教方式编写焊接程序,完全采用自动扫描、自动生成焊接程序的方式提高作业效率。
25.2、该适合机器人焊接的节点模型构建装置,通过压板的侧壁向中部推动,压板的侧壁可向内推动,卡针的侧壁底端,卡针的顶端支撑在支撑架的底侧壁处,支撑架的侧壁随着卡针的活动而拉开,支撑架的侧壁夹层向外张开,支撑架的顶端侧壁缩小范围,支撑架的右侧壁处向外呈斜坡状,使得弹力管的侧壁顺着支撑架的侧壁处向下滑动,刚好位于支撑垫侧壁处的弧线处,与后面伸出的激光器的侧壁处进行贴合,顺着激光器的侧壁处进行对
着xyz轴进行定点焊接。
26.3、该适合机器人焊接的节点模型构建装置,通过移位套的侧壁向外挤出后,移位套的侧壁滑出滑套的外部时会向外变得蓬松出现沟状,移位套的侧壁向底部折断下垂,带动活动套的侧壁向下移动,结合图中的所示,可顺着卡针的侧壁向下,卡针的侧壁可向下底座的位置展开xyz的三轴,卡针的侧壁处附着传感器,感应到激光器的侧壁,在开始定位的卡针的侧壁处,就可对z轴进行定位,当数据发生变化时,改变节点的位置,移动卡针的位置。
附图说明
27.图1为本发明节点建模的方法示意图;
28.图2为本发明扫描点表的方法示意图;
29.图3为本发明焊接点表的方法示意图;
30.图4为本发明整体结构连接示意图;
31.图5为本发明锁撑机构内部相关结构连接顶面示意图;
32.图6为本发明组合机构内部相关结构和滑套之间的结构连接正面和右侧展示图。
33.图中:1、支撑台;2、控制钮;3、锁撑机构;311、支撑盘;312、滑套;313、叠盘;314、软棉层;315、变形架;4、弹力管;5、支撑架;6、组合机构;601、滑板;602、移位套;603、弹力带;604、活动套;605、激光器;7、支撑垫;8、压板;801、卡针;9、拉索;10、底座。
具体实施方式
34.下面将结合本发明实施例中的附图,对本发明实施例中的技术方案进行清楚、完整地描述,显然,所描述的实施例仅仅是本发明一部分实施例,而不是全部的实施例。基于本发明中的实施例,本领域普通技术人员在没有做出创造性劳动前提下所获得的所有其他实施例,都属于本发明保护的范围。
35.实施例一:
36.一种适合机器人焊接的节点模型构建方法,包括以下步骤:
37.s1、采用参数化方式创建节点模型,建模内容包括:节点位置尺寸、边界约束几何尺寸、焊接部位及形式、焊接工艺参数。
38.s2、通过节点建模将一个零件或者一个构件所涉及的所有相关参数集中到一个模型结构中,供后续计算使用,节点数据以文件形式保存。
39.a.节点建模的方法如下(如图1所示):
40.创建节点模型是该方法的基础,是后续工作的参数值来源;主要包含节点类型、定位尺寸、结构尺寸、焊缝位置、焊缝范围、焊接工艺等。
41.虽然金属结构的类型千差万别,每个行业的焊接工艺要求不一样,但是仔细研究构件上零件之间的连接方式和关系,是可以根据共性特征抽象分离出不同的可重复、可共用的节点模板。这些节点模板可应用在不同行业不同类型构件的焊接上。比如图示为一块异形加劲板与h型主构件的连接形式,加劲板底部h型钢腹板、两侧与h型构件翼板连接,共有两道平角焊缝和四道垂直立缝。
42.s3、创建节点扫描点表,用线激光获取关键点的实际坐标值,结合节点模板中约定
的几何拓扑关系计算出实际的焊缝位置边界点坐标。
43.b.扫描点表的方法如下(如图2所示):
44.图中标注的扫描点按约定的顺序使用线激光器逐个扫描后获得机器人的三维坐标值。
45.扫描点的位姿需事先根据节点建模信息中构件尺寸设计计算出来的,扫描点的设置是根据最后需要计算的几何约束边界点来布置的,数量尽可能的少,并适当考虑线激光器在扫描运动过程中的姿态避免触碰周边结构为宜。
46.s4、创建实际焊接路径,将焊接工艺包中的参数和机器人位姿要求消化到实际焊接路径中。
47.c.焊接点表的方法如下(如图3所示):
48.图中标记点边界顶点坐标是根据扫描的系列点通过几何拓扑关系计算出来的,这些顶点一般都是焊缝的首末点,顶点的实际精度取决于扫描取点的精度,一般偏差控制在1mm左右都是可用的。
49.焊缝顶点坐标计算成功后,按选择焊缝范围进行焊缝的设计,根据焊缝的不同位置分别设置不同的焊接工艺包选择,平角焊缝和立焊缝分别采用不同的焊接枪姿态和焊接电流、电压、速度等参数。
50.s5、创建焊接程序,将包含工艺信息的路径点表翻译成机器人可识别的执行程序。
51.d.焊接程序的方法如下:
52.焊接程序是各类机器人最后执行的对应代码程序,不同的机器人有不同的格式和语句要求,在生成焊接程序时需增加一些辅助的过渡点和回枪动作,使机器人运行起来动作流畅,减少奇异点的产生和触碰结构的风险;同时在焊接程序时需要消化焊接工艺包对所使用的焊接参数的影响,把不同类型的焊缝和工艺偏移量增加进最后的焊接路径表中,确保焊接质量符合预期工艺要求。
53.实施例二:
54.请参阅图4
‑
6,一种适合机器人焊接的节点模型构建装置,包括支撑台1,支撑台1的侧壁处设置有控制钮2,支撑台1的底侧壁处贯穿连接有锁撑机构3,锁撑机构3的内部包括支撑盘311,支撑盘311的侧壁处设置有滑套312,支撑盘311的内侧壁轴心处贯穿连接有叠盘313,叠盘313的侧壁处底侧壁处贯穿连接有变形架315,支撑盘311的内侧壁处设置有软棉层314,锁撑机构3的底侧壁处贯穿连接有弹力管4,弹力管4的底端贯穿连接有支撑架5,支撑架5的底侧壁处贯穿连接有支撑垫7,支撑垫7的底部贯穿连接有组合机构6,支撑垫7的侧壁处贯穿连接有卡针801,卡针801的底端环连接有底座10,底座10的顶侧壁处摆动连接有压板8,压板8的侧壁处贯穿连接有拉索9。
55.其中,组合机构6的内部包括滑板601,滑板601的侧壁中部贯穿连接有移位套602,移位套602的内侧壁处贯穿连接有弹力带603,弹力带603的外侧壁处贯穿连接有活动套604,活动套604的内侧壁处贯穿连接有激光器605。
56.其中,变形架315的侧壁处滑动连接于软棉层314的侧壁处,叠盘313的侧壁处向外撑开后,叠盘313的侧端可推动软棉层314的侧壁使其撑起。
57.其中,变形架315的外端滑动贯穿连接于滑套312的内侧壁处,变形架315的侧壁变直后,可推动滑套312的侧壁。
58.其中,滑套312的内侧壁处滑动连接于组合机构6的外侧,滑套312的侧壁受推力后可将组合机构6向外推出。
59.其中,压板8的侧壁处滑动连接于卡针801的侧壁处,压板8的侧壁沿着y轴活动时,可带动卡针801的侧壁一同沿着y轴移动。
60.工作原理:在使用时,如图4所示,将底座10的侧壁处平躺铺平,使定位的纸板放置在底座10的顶侧壁处能够保持平整并贴合于底座10的顶侧壁处,将底座10顶侧壁处的压板8向下扣住,使压板8的侧壁能够贴合于底座10的顶侧壁处,压板8的侧壁顺时针旋转扣动时可拽动侧壁处连接的拉索9,使得压板8的侧壁被扯动呈叠加的状态,压板8的侧壁向中部推动,压板8的侧壁可向内推动,卡针801的侧壁底端,卡针801的顶端支撑在支撑架5的底侧壁处,支撑架5的侧壁随着卡针801的活动而拉开,支撑架5的侧壁夹层向外张开,支撑架5的顶端侧壁缩小范围,支撑架5的右侧壁处向外呈斜坡状,使得弹力管4的侧壁顺着支撑架5的侧壁处向下滑动,刚好位于支撑垫7侧壁处的弧线处,与后面伸出的激光器605的侧壁处进行贴合,顺着激光器605的侧壁处进行对着xyz轴进行定点焊接;
61.如图4和图6所示,激光器605的侧壁被开启光源后,锁撑机构3的内部受到控制,叠盘313的侧壁向外撑开,向底部撑起变形架315的侧壁,变形架315的侧壁可受力撑至向外推动滑套312,滑套312的侧壁受到压力,滑套312的侧壁将移位套602的侧壁向外挤出,移位套602的侧壁向外挤出后,移位套602的侧壁滑出滑套312的外部时会向外变得蓬松出现沟状,移位套602的侧壁向底部折断下垂,带动活动套604的侧壁向下移动,结合图1中的所示,可顺着卡针801的侧壁向下,卡针801的侧壁可向下底座10的位置展开xyz的三轴,卡针801的侧壁处附着传感器,感应到激光器605的侧壁,在开始定位的卡针801的侧壁处,就可对z轴进行定位,当数据发生变化时,改变节点的位置,移动卡针801的位置。
62.尽管已经示出和描述了本发明的实施例,对于本领域的普通技术人员而言,可以理解在不脱离本发明的原理和精神的情况下可以对这些实施例进行多种变化、修改、替换和变型,本发明的范围由所附权利要求及其等同物限定。