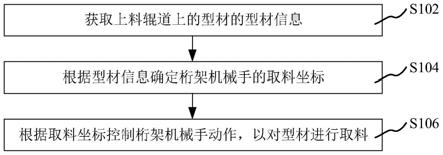
1.本发明涉及智能机械领域,具体地,涉及一种用于桁架机械手的控制方法、处理器、控制装置及生产线。
背景技术:2.桁架机械手是智能搬运机械设备的一种,可以用来进行型材的搬运。现有的桁架机械手在进行型材的抓取时,需要人工对抓取位置的坐标进行校对,以确定该抓取位置是否准确。校对完成以后,才能进行该规格型材的抓取。对于多规格型材交叉搬运的工况,即产线来料规格多、堆垛上料的情况,每次抓取过程都进行人工校核存在人力成本较大的问题。
技术实现要素:3.本发明实施例的目的是提供一种用于桁架机械手的控制方法、处理器、用于桁架机械手的控制装置、桁架机械手、用于输送的生产线以及存储介质,以解决现有技术存在人力成本较大的问题。
4.为了实现上述目的,本发明第一方面提供一种用于桁架机械手的控制方法,控制方法包括:
5.获取上料辊道上的型材的型材信息;
6.根据型材信息确定桁架机械手的取料坐标;以及
7.根据取料坐标控制桁架机械手动作,以对型材进行取料。
8.在本发明实施例中,型材信息包括型材长度和型材位置;取料坐标包括x轴方向的x轴取料坐标;根据型材信息确定桁架机械手的取料坐标包括:根据型材长度和型材位置确定桁架机械手在x轴方向上的x轴取料坐标;根据取料坐标控制桁架机械手动作包括:控制桁架机械手的x轴执行器按照x轴取料坐标动作。
9.在本发明实施例中,型材信息包括型材宽度和型材码放列数;取料坐标包括y轴方向的y轴取料坐标;根据型材信息确定桁架机械手的取料坐标包括:根据型材宽度和型材码放列数确定桁架机械手在y轴方向上的y轴取料坐标;根据取料坐标控制桁架机械手动作包括:控制桁架机械手的y轴执行器按照y轴取料坐标动作。
10.在本发明实施例中,型材信息包括型材高度和型材码放层数;取料坐标包括z轴方向的z轴取料坐标;根据型材信息确定桁架机械手的取料坐标包括:根据型材高度和型材码放层数确定桁架机械手在z轴方向上的z轴取料坐标;根据取料坐标控制桁架机械手动作包括:控制桁架机械手的z轴执行器按照z轴取料坐标动作。
11.在本发明实施例中,控制方法还包括:根据预存储的放料辊道的辊道信息和型材信息确定放料辊道的最大允许放料数量,其中放料辊道与上料辊道平行;获取放料辊道的当前放料数量;在当前放料数量小于最大允许放料数量的情况下,根据型材信息确定桁架机械手的放料坐标;根据放料坐标控制桁架机械手动作,以对型材进行放料。
12.在本发明实施例中,辊道信息包括辊道宽度;型材信息包括型材宽度;根据预存储的放料辊道的辊道信息和型材信息确定放料辊道的最大允许放料数量,包括:根据辊道宽度、预设型材间隔宽度以及型材宽度,确定放料辊道的最大允许放料数量。
13.在本发明实施例中,辊道信息还包括辊道位置;型材信息还包括型材位置;放料坐标包括y轴方向的y轴放料坐标;根据型材信息确定桁架机械手的放料坐标包括:确定型材位置与辊道位置之间的距离;根据距离、当前放料数量、型材宽度以及预设型材间隔宽度,确定桁架机械手在y轴方向上的y轴放料坐标;根据放料坐标控制桁架机械手动作包括:控制桁架机械手的y轴执行器按照y轴放料坐标动作。
14.在本发明实施例中,型材信息还包括型材高度;放料坐标包括z轴方向的z轴放料坐标;根据型材信息确定桁架机械手的放料坐标包括:根据辊道位置和型材高度确定桁架机械手在z轴方向上的z轴放料坐标;根据放料坐标控制桁架机械手动作包括:控制桁架机械手的z轴执行器按照z轴放料坐标动作。
15.在本发明实施例中,控制方法还包括:在对每一个型材进行取料之后,对型材信息进行更新,以得到更新后的型材信息;在对每一个型材进行放料之后,对放料辊道的放料数量进行更新,以得到更新后的放料数量。
16.在本发明实施例中,更新后的型材信息包括更新后的型材数量;控制方法还包括:在更新后的型材数量为零的情况下,确定取料完成和/或放料完成;在更新后的放料数量达到最大允许放料数量的情况下,确定放料完成。
17.在本发明实施例中,获取上料辊道上的型材的型材信息之后还包括:将型材的型材信息与待取料型材的型材信息进行比对;在确定型材不是待取料型材的情况下,禁止桁架机械手动作。
18.在本发明实施例中,控制方法还包括:确定上料辊道上的型材的最大高度;在最大高度小于或等于桁架机械手的最大允许高度的情况下,发出允许取料信号。
19.在本发明实施例中,控制方法还包括:在最大高度大于最大允许高度的情况下,禁止桁架机械手动作。
20.本发明第二方面提供一种处理器,被配置成执行根据上述的用于桁架机械手的控制方法。
21.本发明第三方面提供一种用于桁架机械手的控制装置,包括:信息输入终端,用于接收上料辊道上的型材的型材信息;以及根据上述的处理器。
22.在本发明实施例中,信息输入终端包括远程输入终端和本地输入终端,本地输入终端还用于显示桁架机械手的运行信息和/或接收操作指令。
23.本发明第四方面提供一种桁架机械手,包括:x轴执行器;y轴执行器;z轴执行器;以及根据上述的用于桁架机械手的控制装置。
24.在本发明实施例中,桁架机械手还包括夹具,夹具包括电磁吸盘。
25.本发明第五方面提供一种用于输送的生产线,包括根据上述的桁架机械手。
26.在本发明实施例中,桁架机械手包括第一桁架机械手,被配置成:对上料辊道上的型材进行取料,并将型材放料至放料辊道上;在放料完成后存储型材信息,型材信息至少包括型材的位置信息;以及第二桁架机械手,与第一桁架机械手进行通信,被配置成:在取料之前向第一桁架机械手发送数据请求;接收第一桁架机械手响应于数据请求发送的型材信
息;根据型材的位置信息和预存储的第一桁架机械手与第二桁架机械手的相对距离确定第二桁架机械手的取料坐标;以及根据取料坐标对放料辊道上的型材进行取料。
27.在本发明实施例中,型材的位置信息与第一桁架机械手放料时的位置相关联。
28.在本发明实施例中,型材信息还包括型材类型、型材规格以及型材数量中的至少一者。
29.在本发明实施例中,生产线还包括:抛丸机,分别与第一桁架机械手、第二桁架机械手进行通信;第一桁架机械手还被配置成:在放料完成后发送放料完成信号至抛丸机;抛丸机被配置成:接收第一桁架机械手发送的放料完成信号;对放料辊道上的型材进行抛丸处理,以得到抛丸处理后的型材;在抛丸处理后发送允许取料信号至第二桁架机械手;第二桁架机械手还被配置成:接收抛丸机发送的允许取料信号;对抛丸处理后的型材进行取料。
30.在本发明实施例中,第二桁架机械手还被配置成:在取料后发送取料完成信号至第一桁架机械手;第一桁架机械手还被配置成:接收第二桁架机械手发送的取料完成信号;根据先进先出的原则对存储的型材信息进行刷新。
31.本发明第六方面提供一种机器可读存储介质,该机器可读存储介质上存储有指令,该指令在被处理器执行时使得处理器执行根据上述的用于桁架机械手的控制方法。
32.上述用于桁架机械手的控制方法,通过获取上料辊道上的型材的型材信息,并根据型材信息确定桁架机械手的取料坐标,从而根据取料坐标控制桁架机械手动作,以对型材进行取料。上述技术方案,可以根据上料辊道上的型材的型材信息自动计算桁架机械手的取料坐标,无需人工对桁架机械手的位置坐标进行手动校核,减少了人力成本,可以适用多规格型材交叉搬运的工况,且计算结果的准确性较高,提高了桁架机械手的取料效率,加快了机械作业的进程,给型材搬运过程带来了极大的便利性。
33.本发明实施例的其它特征和优点将在随后的具体实施方式部分予以详细说明。
附图说明
34.附图是用来提供对本发明实施例的进一步理解,并且构成说明书的一部分,与下面的具体实施方式一起用于解释本发明实施例,但并不构成对本发明实施例的限制。在附图中:
35.图1示意性示出了本发明一实施例中用于桁架机械手的控制方法的流程示意图;
36.图2a示意性示出了本发明另一实施例中用于桁架机械手的控制方法的部分的流程示意图;
37.图2b示意性示出了本发明另一实施例中用于桁架机械手的控制方法的其余部分的流程示意图;
38.图3示意性示出了本发明一实施例中用于桁架机械手的控制装置的结构框图示意图;
39.图4示意性示出了本发明一实施例中用于桁架机械手的控制系统的结构框图示意图;
40.图5示意性示出了本发明一实施例中带电电磁吸盘的桁架机械手的结构示意图;
41.图6示意性示出了本发明一实施例中带电电磁吸盘的桁架机械手的主视示意图;
42.图7示意性示出了本发明一实施例中带电电磁吸盘的桁架机械手的俯视示意图;
43.图8示意性示出了本发明一实施例中带电电磁吸盘的桁架机械手的控制柜的外部示意图;
44.图9示意性示出了本发明一实施例中带电电磁吸盘的桁架机械手的控制柜内平面示意图。
45.附图标记说明
[0046]1ꢀꢀꢀ
立柱
ꢀꢀꢀꢀꢀꢀꢀꢀꢀꢀꢀꢀꢀꢀꢀꢀꢀꢀꢀꢀꢀꢀꢀ2ꢀꢀ
x轴从动滑移小车机构
[0047]3ꢀꢀꢀ
x轴双输出驱动(蜗轮蜗杆减速机机构)
ꢀꢀꢀ4ꢀꢀꢀ
x轴横梁
[0049]5ꢀꢀꢀ
x轴主动滑移小车a
ꢀꢀꢀꢀꢀꢀꢀꢀꢀꢀꢀ6ꢀꢀꢀ
x轴横梁
[0050]7ꢀꢀꢀ
x轴移动横梁
ꢀꢀꢀꢀꢀꢀꢀꢀꢀꢀꢀꢀꢀꢀꢀꢀ8ꢀꢀꢀ
x轴主动滑移小车b
[0051]9ꢀꢀꢀ
框架连接支撑
ꢀꢀꢀꢀꢀꢀꢀꢀꢀꢀꢀꢀꢀꢀꢀ
10
ꢀꢀ
y轴移动轴横梁
[0052]
11
ꢀꢀ
y轴双输出驱动(蜗轮蜗杆减速机机构)
ꢀꢀꢀ
12
ꢀꢀ
y轴滑移小车(z轴载板)
[0054]
13
ꢀꢀ
z轴双输出驱动(蜗轮蜗杆减速机机构)
ꢀꢀꢀ
16
ꢀꢀ
连接法兰
[0056]
17
ꢀꢀ
夹具主体
ꢀꢀꢀꢀꢀꢀꢀꢀꢀꢀꢀꢀꢀꢀꢀꢀꢀꢀꢀ
18
ꢀꢀ
电磁铁
[0057]
19
ꢀꢀ
z轴主体a
ꢀꢀꢀꢀꢀꢀꢀꢀꢀꢀꢀꢀꢀꢀꢀꢀꢀꢀꢀ
20
ꢀꢀ
本地hmi触摸屏
[0058]
21
ꢀꢀ
x轴伺服驱动器
ꢀꢀꢀꢀꢀꢀꢀꢀꢀꢀꢀꢀꢀꢀ
22
ꢀꢀ
di/do低压端子
[0059]
23
ꢀꢀ
交流互感器
ꢀꢀꢀꢀꢀꢀꢀꢀꢀꢀꢀꢀꢀꢀꢀꢀꢀ
24
ꢀꢀ
交流端子
[0060]
25
ꢀꢀ
y轴伺服驱动器
ꢀꢀꢀꢀꢀꢀꢀꢀꢀꢀꢀꢀꢀꢀ
26
ꢀꢀ
z轴伺服驱动器
[0061]
27
ꢀꢀ
plc及模块
ꢀꢀꢀꢀꢀꢀꢀꢀꢀꢀꢀꢀꢀꢀꢀꢀꢀꢀ
28
ꢀꢀ
交换机
具体实施方式
[0062]
以下结合附图对本发明实施例的具体实施方式进行详细说明。应当理解的是,此处所描述的具体实施方式仅用于说明和解释本发明实施例,并不用于限制本发明实施例。
[0063]
需要说明,若本发明实施例中有涉及方向性指示(诸如上、下、左、右、前、后
……
),则该方向性指示仅用于解释在某一特定姿态(如附图所示)下各部件之间的相对位置关系、运动情况等,如果该特定姿态发生改变时,则该方向性指示也相应地随之改变。
[0064]
另外,若本发明实施例中有涉及“第一”、“第二”等的描述,则该“第一”、“第二”等的描述仅用于描述目的,而不能理解为指示或暗示其相对重要性或者隐含指明所指示的技术特征的数量。由此,限定有“第一”、“第二”的特征可以明示或者隐含地包括至少一个该特征。另外,各个实施例之间的技术方案可以相互结合,但是必须是以本领域普通技术人员能够实现为基础,当技术方案的结合出现相互矛盾或无法实现时应当认为这种技术方案的结合不存在,也不在本发明要求的保护范围之内。
[0065]
图1示意性示出了本发明一实施例中用于桁架机械手的控制方法的流程示意图。如图1所示,在本发明实施例中,提供了一种用于桁架机械手的控制方法,以该方法应用于处理器为例进行说明,该控制方法可以包括以下步骤:
[0066]
步骤s102,获取上料辊道上的型材的型材信息。
[0067]
可以理解,上料辊道即来料辊道,也就是型材来料时放置的初始位置。型材信息的示例可以包括但不限于,例如型材规格、型材类型等。型材可以为需要桁架机械手进行搬运的物体,例如角钢、圆钢等。
[0068]
具体地,处理器可以获取上料辊道上的型材的型材信息。例如,处理器可以获取用
户通过信息输入终端输入的上料辊道上的型材的型材信息,和/或可以获取图像采集设备采集到的图像,通过图像识别得到料辊道上的型材的型材信息。
[0069]
步骤s104,根据型材信息确定桁架机械手的取料坐标。
[0070]
可以理解,桁架机械手包括x轴执行器、y轴执行器以及z轴执行器,取料坐标为桁架机械手的x轴执行器和/或y轴执行器和/或z轴执行器需要执行取料动作的具体坐标值,也就是可以包括x轴方向和/或y轴方向和/或z轴方向上的坐标值。
[0071]
具体地,处理器可以根据型材信息确定桁架机械手的取料坐标。
[0072]
在一个实施例中,型材信息包括型材长度和型材位置;取料坐标包括x轴方向的x轴取料坐标;根据型材信息确定桁架机械手的取料坐标包括:根据型材长度和型材位置确定桁架机械手在x轴方向上的x轴取料坐标;根据取料坐标控制桁架机械手动作包括:控制桁架机械手的x轴执行器按照x轴取料坐标动作。
[0073]
可以理解,型材位置为型材的位置信息,具体可以通过相应的检测设备或仪器检测得到型材的端点的位置从而得到型材的位置信息。型材长度即型材的长度信息,可以通过用户输入的信息得到,也可以是通过预先存储的型材信息得到。x轴取料坐标为桁架机械手在x轴方向上的取料坐标,也就是x轴执行器的目标坐标值。
[0074]
具体地,处理器可以将上料辊道的某一侧的某一个端点作为桁架机械手的原点坐标,从而可以基于上述原点坐标,根据型材长度和型材位置确定桁架机械手在x轴方向上的x轴取料坐标,从而控制桁架机械手的x轴执行器按照x轴取料坐标动作。进一步地,型材长度和型材位置一确定,处理器则可以确定型材的长度的一半所在的位置(或是其他某一位置),从而将该位置确定为桁架机械手在x轴方向上的x轴取料坐标,从而控制桁架机械手的x轴执行器按照该x轴取料坐标执行取料动作。再进一步地,型材位置可以包括型材两个端点中至少一个端点的位置,处理器可以根据两个端点中任意一个端点的位置和型材长度确定型材在x轴方向上的中点位置(或是其他某一位置),也就是x轴取料坐标。
[0075]
在一个实施例中,型材信息包括型材宽度和型材码放列数;取料坐标包括y轴方向的y轴取料坐标;根据型材信息确定桁架机械手的取料坐标包括:根据型材宽度和型材码放列数确定桁架机械手在y轴方向上的y轴取料坐标;根据取料坐标控制桁架机械手动作包括:控制桁架机械手的y轴执行器按照y轴取料坐标动作。
[0076]
可以理解,通常型材采用逐件逐层向上重叠而成堆垛的形式,即重叠式堆垛,型材码放列数为型材堆码的列数,型材码放列数可以通过用户输入的信息得到,也可以是通过预先存储的型材信息得到。型材宽度为型材的宽度信息,可以通过用户输入的信息得到,也可以是通过预先存储的型材信息得到。y轴取料坐标为桁架机械手在y轴方向上的取料坐标,也就是y轴执行器的目标坐标值。
[0077]
具体地,处理器可以将上料辊道的某一侧的某一个端点作为桁架机械手的原点坐标,从而可以基于上述原点坐标,根据型材宽度和型材码放列数确定桁架机械手在y轴方向上的y轴取料坐标,从而控制桁架机械手的y轴执行器按照y轴取料坐标动作。例如,若型材宽度为20厘米,型材码放列数为3列,处理器可以基于上述原点坐标,确定y轴取料坐标为y轴方向上10厘米或30厘米或50厘米所在的位置,即型材宽度的一半也就是型材在y轴方向上的中点位置,即y轴取料坐标。
[0078]
在一个实施例中,型材信息包括型材高度和型材码放层数;取料坐标包括z轴方向
的z轴取料坐标;根据型材信息确定桁架机械手的取料坐标包括:根据型材高度和型材码放层数确定桁架机械手在z轴方向上的z轴取料坐标;根据取料坐标控制桁架机械手动作包括:控制桁架机械手的z轴执行器按照z轴取料坐标动作。
[0079]
可以理解,通常型材采用逐件逐层向上重叠而成堆垛的形式,即重叠式堆垛,型材码放层数为型材的堆码层数,型材码放层数可以通过用户输入的信息得到,也可以是通过预先存储的型材信息得到。型材高度为型材的高度信息,可以通过用户输入的信息得到,也可以是通过预先存储的型材信息得到。z轴取料坐标为桁架机械手在z轴方向上的取料坐标,也就是z轴执行器的目标坐标值。
[0080]
具体地,处理器可以将上料辊道的某一侧的某一个端点作为桁架机械手的原点坐标,从而可以基于上述原点坐标,根据型材高度和型材码放层数确定桁架机械手在z轴方向上的z轴取料坐标,从而控制桁架机械手的z轴执行器按照z轴取料坐标动作。例如,以圆钢为例进行说明,若圆钢的高度即型材高度为10厘米,型材码放层数为5,那么处理器可以基于上述原点坐标,确定z轴取料坐标为五根圆钢的高度之和,也就是说,型材的总高度即为z轴取料坐标。若以角钢为例进行说明,角钢包括尖角,z轴取料坐标即型材的总高度可以为:型材的单根高度+(型材数量-1)
×
角钢尖角高度。
[0081]
步骤s106,根据取料坐标控制桁架机械手动作,以对型材进行取料。
[0082]
具体地,处理器在确定了桁架机械手的取料坐标之后,可以根据取料坐标控制桁架机械手动作,例如控制桁架机械手的y轴执行器按照y轴取料坐标动作,以对上料辊道上的型材进行取料。
[0083]
上述用于桁架机械手的控制方法,通过获取上料辊道上的型材的型材信息,并根据型材信息确定桁架机械手的取料坐标,从而根据取料坐标控制桁架机械手动作,以对型材进行取料。上述技术方案,可以根据上料辊道上的型材的型材信息自动计算桁架机械手的取料坐标,无需人工对桁架机械手的位置坐标进行手动校核,减少了人力成本,可以适用多规格型材交叉搬运的工况,且计算结果的准确性较高,提高了桁架机械手的取料效率,加快了机械作业的进程,给型材搬运过程带来了极大的便利性。
[0084]
在一个实施例中,控制方法还可以包括放料过程,放料过程可以包括以下步骤:根据预存储的放料辊道的辊道信息和型材信息确定放料辊道的最大允许放料数量,其中放料辊道与上料辊道平行;获取放料辊道的当前放料数量;在当前放料数量小于最大允许放料数量的情况下,根据型材信息确定桁架机械手的放料坐标;根据放料坐标控制桁架机械手动作,以对型材进行放料。
[0085]
可以理解,放料辊道通常与上料辊道平行,以便于桁架机械手实现型材的搬运过程,由于放料辊道上的型材需要进行其他处理(例如,抛丸处理),故放料辊道上的型材通常不进行堆垛放置,而是进行铺设放置,由于放料辊道的宽度有限,故放料辊道上可以放置的型材的数量也有限,放料辊道上最多可以放置的型材数量即为放料辊道的最大允许放料数量。放料辊道的当前放料数量为放料辊道上当前已放置的型材的数量,具体可以根据桁架机械手执行取料动作的次数确定,也可以根据图像采集设备采集到的图像进行图像识别得到。放料坐标为桁架机械手的x轴执行器和/或y轴执行器和/或z轴执行器需要执行放料动作的具体坐标值,也就是可以包括x轴方向和/或y轴方向和/或z轴方向上的放料坐标。
[0086]
具体地,处理器可以根据预存储的放料辊道的辊道信息和型材信息确定放料辊道
的最大允许放料数量,进而获取放料辊道的当前放料数量,在当前放料数量小于最大允许放料数量的情况下,根据型材信息确定桁架机械手的放料坐标,也就是说,若放料辊道的当前放料数量还未达到放料辊道的最大允许放料数量,则可以根据型材信息确定放料坐标以将型材放置在该放料辊道上,进而根据放料坐标控制桁架机械手动作,以对型材进行放料。
[0087]
在一个实施例中,辊道信息包括辊道宽度;型材信息包括型材宽度;根据预存储的放料辊道的辊道信息和型材信息确定放料辊道的最大允许放料数量,包括:根据辊道宽度、预设型材间隔宽度以及型材宽度,确定放料辊道的最大允许放料数量。
[0088]
可以理解,放料辊道的辊道宽度通常是固定的,通常型材的两端预留一定的宽度作为空闲区域,故可以设定两根型材之间的排布宽度,也就是预设型材间隔宽度,即预先设置的放料辊道上的型材的间隔宽度。
[0089]
具体地,处理器可以根据辊道宽度、预设型材间隔宽度以及型材宽度,确定放料辊道的最大允许放料数量。
[0090]
在一个实施例中,辊道信息还包括辊道位置;型材信息还包括型材位置;放料坐标包括y轴方向的y轴放料坐标;根据型材信息确定桁架机械手的放料坐标包括:确定型材位置与辊道位置之间的距离;根据距离、当前放料数量、型材宽度以及预设型材间隔宽度,确定桁架机械手在y轴方向上的y轴放料坐标;根据放料坐标控制桁架机械手动作包括:控制桁架机械手的y轴执行器按照y轴放料坐标动作。
[0091]
可以理解,y轴放料坐标为桁架机械手在y轴方向上的放料坐标,也就是y轴执行器的目标坐标值。
[0092]
具体地,处理器可以先确定型材位置与放料辊道的辊道位置之间的距离,进而根据该距离、当前放料数量、型材宽度以及预设型材间隔宽度,确定桁架机械手在y轴方向上的y轴放料坐标,从而控制桁架机械手的y轴执行器按照y轴放料坐标动作。例如,处理器可以确定型材位置与放料辊道靠近上料辊道的一侧的距离为a,当前放料数量为b,型材宽度为c,预设间隔宽度为d,则处理器可以以型材位置为原点坐标,确定桁架机械手在y轴方向上的y轴放料坐标为:a+b
×
(c+d)。
[0093]
在一个实施例中,型材信息还包括型材高度;放料坐标包括z轴方向的z轴放料坐标;根据型材信息确定桁架机械手的放料坐标包括:根据辊道位置和型材高度确定桁架机械手在z轴方向上的z轴放料坐标;根据放料坐标控制桁架机械手动作包括:控制桁架机械手的z轴执行器按照z轴放料坐标动作。
[0094]
可以理解,z轴放料坐标为桁架机械手在z轴方向上的放料坐标,也就是z轴执行器的目标坐标值。
[0095]
具体地,处理器可以根据辊道位置和型材高度确定桁架机械手在z轴方向上的z轴放料坐标,也就是说处理器可以在辊道位置的z轴坐标上增加型材高度对应的数值,从而可以得到z轴放料坐标。
[0096]
在一个实施例中,放料坐标还包括x轴方向的x轴放料坐标,由于放料辊道与上料辊道平行,故x轴放料坐标可以保持不变,即保持x轴取料坐标不变。
[0097]
在一个实施例中,上述控制方法还可以包括:在对每一个型材进行取料之后,对型材信息进行更新,以得到更新后的型材信息;在对每一个型材进行放料之后,对放料辊道的放料数量进行更新,以得到更新后的放料数量。
[0098]
具体地,处理器可以在每次取料动作之后,更新上料辊道上的型材的型材信息,从而得到更新后的型材信息。同样地,处理器可以在每次放料动作之后,对放料辊道的放料数量进行更新,以得到更新后的放料数量。
[0099]
在本发明实施例中,通过对上料辊道上的型材的型材信息和放料辊道的放料数量进行更新,可以方便用户了解型材的实时数量,也便于桁架机械手的自动化运行。
[0100]
在一个实施例中,更新后的型材信息包括更新后的型材数量;控制方法还包括:在更新后的型材数量为零的情况下,确定取料完成和/或放料完成;在更新后的放料数量达到最大允许放料数量的情况下,确定放料完成。
[0101]
具体地,若更新后的上料辊道上的型材数量为零,处理器可以确定此时取料完成和/或放料完成。进一步地,处理器可以发出取料完成信号和/或放料完成信号。若更新后的放料辊道的放料数量达到放料辊道的最大允许放料数量,处理器可以确定此时放料完成。进一步地,处理器可以发出放料完成信号。
[0102]
在一个实施例中,获取上料辊道上的型材的型材信息之后还包括:将型材的型材信息与待取料型材的型材信息进行比对;在确定型材不是待取料型材的情况下,禁止桁架机械手动作。
[0103]
可以理解,待取料型材为需要进行取料的型材。
[0104]
具体地,处理器可以将上料辊道上的型材的型材信息与待取料型材的型材信息进行比对,在确定该型材不是待取料型材的时候,处理器禁止桁架机械手动作,以防止取料错误。
[0105]
进一步地,在一些实施例中,型材信息可以包括型材类型,也就是说,处理器可以将上料辊道上的型材的型材类型与待取料型材的型材类型进行比对,在确定型材类型不是待取料型材对应的型材类型的情况下,禁止桁架机械手动作。
[0106]
在另一些实施例中,型材信息可以包括型材类型和型材规格,也就是说,处理器可以将上料辊道上的型材的型材类型和型材规格与待取料型材的型材类型和型材规格进行比对,在确定型材类型和型材规格中的任意一者不是待取料型材对应的型材类型或型材规格的情况下,禁止桁架机械手动作。
[0107]
在一个实施例中,控制方法还包括:确定上料辊道上的型材的最大高度;在最大高度小于或等于桁架机械手的最大允许高度的情况下,发出允许取料信号。
[0108]
可以理解,在型材具备多个堆垛时,型材的码放层数可以相同,也可以不同,最大高度为型材堆放的最大高度。桁架机械手的最大允许高度为桁架机械手在z轴方向上可以达到的最大高度。允许取料信号为允许桁架机械手进行取料动作的信号或指令。
[0109]
具体地,处理器可以根据型材高度和型材码放层数确定上料辊道上的型材的最大高度,进而将该最大高度与桁架机械手的最大允许高度进行比较,在该最大高度小于或等于桁架机械手的最大允许高度的情况下,处理器可以发出允许取料信号。
[0110]
在本发明实施例中,通过将上料辊道上的型材的最大高度与桁架机械手的最大允许高度进行比较,可以确定是否发出允许取料信号,保证桁架机械手的安全运行。
[0111]
在一个实施例中,上述控制方法还包括:在最大高度大于最大允许高度的情况下,禁止桁架机械手动作。
[0112]
具体地,当上料辊道上的型材的最大高度大于桁架机械手的最大允许高度的时
候,处理器可以禁止桁架机械手动作,以保证桁架机械手的安全运行。
[0113]
目前的桁架机械手适用的工况较为单一,即为只能执行相对较为固定的动作流程,或许在有人操作的模型下进行不同物体的搬运。此外,桁架机械手在进行型材抓取或释放时,第一步需要对抓取和释放位置坐标进行校对,校对完成以后,方能进行该规格型材抓取或释放。对于多规格型材交叉搬运的工况,每次校核显然带来了工作上的不便,尤其不能满足自动运行的条件。
[0114]
在一个具体的实施例中,提供了一种用于桁架机械手的控制方法,该控制方法包括抓取/释放三维坐标实时动态计算技术,中控(即控制器或处理器)将来料信息发送给桁架机械手,来料信息可以包含上料识别号、上料批号、型材规格、型材长度、型材数量、本次上料数量、已上料数量、上料辊道拉线编码器数值,该控制方法具体可以包括以下步骤:
[0115]
第一步,控制系统将来料型材规格和数据库中的型材信息进行比对,如果比对失败,则返回型材信息查询失败,桁架机械手不执行任何动作,提示桁架机械手维护人员,需要对型材数据库进行升级维护,若比对成功,则返回型材的相关信息,以角钢为例,返回的数据可以包含角钢的宽度,角钢厚度,角钢的尖角高度,角钢的斜边宽度,角钢的总高度,转入下一步。
[0116]
第二步,控制系统对来料数量进行校验,根据解析出的型材信息,结合中控给出的来料数量信息,计算出型材的总高度,若总高度大于桁架机械手允许的最大高度,则返回来料超高信息,并且桁架机械手不执行任何动作,若总高度小于桁架机械手的允许最大高度,则转入下一步。
[0117]
第三步,根据初始来料数量,及型材解析出的相关信息,以角钢为例,型材的总高度的计算公式可以为:型材的单根高度+(型材数量-1)
×
角钢尖角高度,计算出初始抓取时桁架机械手的下降高度,即为抓取的z轴坐标,转入下一步。
[0118]
第四步,来料经过一个油缸推齐机构,将型材往一个固定的方向推齐,推出触发一个行程限位开关后,推齐油缸停止工作,同时推齐机构将推出行程通过拉线编码器反应到控制系统中,以角钢为例,斜边宽度的一半加上拉线编码器值即为桁架机械手y轴方向抓取坐标,通常在一堆来料系统中,抓取的y轴坐标保持不变,转入下一步。
[0119]
第五步,根据中控发送的型材信息,型材的长度一定,型材的停料位置通过一个辊道传感器检测完型材料头以后停止,因此,无论型材长短如何变化,料头的位置均是固定的,根据桁架机械手的位置换算,可以计算出桁架机械手抓取型材正中间的位置,该位置即为x轴坐标信息,通常在一堆来料系统中,抓取的x轴坐标保持不变,转入下一步。
[0120]
第六步,桁架机械手接收到允许取料信号及允许放料信号以后,根据取料坐标信息,进行第一根型材抓取,转入下一步。
[0121]
第七步,桁架机械手放料的辊道宽度是固定的,通常型材的两端预留一定的宽度作为空闲区域,同时约定两根型材之间的排布宽度,结合解析出的型材斜边宽度,即可自动计算出放料辊道允许放料的数量,转入下一步。
[0122]
第八步,在不超过辊道允许放料的数量的前提下,桁架机械手完成型材的放料动作,同时进料辊道上余料数量减一,放料辊道上数量加一,转入下一步。
[0123]
第九步,进料辊道上由于型材被抓走,导致余料在实时变化,桁架机械手抓取的z轴坐标也将实时变化,保证每次z轴的抓取坐标和辊道上余料的数量实时对应,转入下一
步。
[0124]
第十步,放料辊道上每多放一根料,放料的y轴坐标将自动加上型材的斜边宽度和两根型材之间允许的放料宽度,转入下一步。
[0125]
第十一步,在上料辊道来料未取完或放料辊道未排布满的情况下,桁架机械手重复上述的抓料/放料动作,直至上料辊道来料被取完,返回取料完成信息,即给中控发信息,从而中控允许进下一批次料,放料辊道排布满以后,返回放料完成信号,以告诉中控可以自行下一步动作,桁架机械手待机等待下一个工作周期。具体的抓取/释放流程可以参照图2a和图2b所示的用于桁架机械手的控制方法的流程示意图。其中,图2a中的a、b、c、d、e、f、g分别对应于图2b中的a’、b’、c’、d’、e’、f’、g’,即a、b、c、d、e、f、g分别连接a’、b’、c’、d’、e’、f’、g’,也就是说图2a和图2b可以合并成一个完整的流程图。
[0126]
综上,本发明实施例提供的技术方案存在以下优点:能够针对不同规格型材自动抓取,比如l型角钢、圆钢、方管、方钢、工字钢、槽钢等。本本发明实施例的技术方案中的桁架机械手作为智能化产线的关键组成部分,首先,桁架机械手不需要人工干预及监控即可自动运行。其次,针对产线来料规格多、堆垛上料的情况,本方案中的桁架机械手能够根据上位机系统下发的型材基本信息自动计算出抓取或释放位置坐标,无需进行位置坐标手动校核,直接根据计算结果精确定位,进一步完成物料的搬运及抓取。
[0127]
本发明实施例提供了一种处理器,该处理器被配置成执行根据上述实施方式中的用于桁架机械手的控制方法。
[0128]
图3示意性示出了本发明一实施例中用于桁架机械手的控制装置的结构框图示意图。如图3所示,在本发明实施例中,提供了一种用于桁架机械手的控制装置300,该用于桁架机械手的控制装置包括信息输入终端310和处理器320,其中:
[0129]
信息输入终端310,用于接收上料辊道上的型材的型材信息。
[0130]
处理器320,被配置成:获取上料辊道上的型材的型材信息;根据型材信息确定桁架机械手的取料坐标;以及根据取料坐标控制桁架机械手动作,以对型材进行取料。
[0131]
上述用于桁架机械手的控制装置300,处理器320通过信息输入终端310获取上料辊道上的型材的型材信息,并根据型材信息确定桁架机械手的取料坐标,从而根据取料坐标控制桁架机械手动作,以对型材进行取料。上述技术方案,可以根据上料辊道上的型材的型材信息自动计算桁架机械手的取料坐标,无需人工对桁架机械手的位置坐标进行手动校核,减少了人力成本,可以适用多规格型材交叉搬运的工况,且计算结果的准确性较高,提高了桁架机械手的取料效率,加快了机械作业的进程,给型材搬运过程带来了极大的便利性。
[0132]
在一个实施例中,型材信息包括型材长度和型材位置;取料坐标包括x轴方向的x轴取料坐标;处理器320进一步被配置成:根据型材长度和型材位置确定桁架机械手在x轴方向上的x轴取料坐标;以及控制桁架机械手的x轴执行器按照x轴取料坐标动作。
[0133]
在一个实施例中,型材信息包括型材宽度和型材码放列数;取料坐标包括y轴方向的y轴取料坐标;处理器320进一步被配置成:根据型材宽度和型材码放列数确定桁架机械手在y轴方向上的y轴取料坐标;以及控制桁架机械手的y轴执行器按照y轴取料坐标动作。
[0134]
在一个实施例中,型材信息包括型材高度和型材码放层数;取料坐标包括z轴方向的z轴取料坐标;处理器320进一步被配置成:根据型材高度和型材码放层数确定桁架机械
手在z轴方向上的z轴取料坐标;以及控制桁架机械手的z轴执行器按照z轴取料坐标动作。
[0135]
在一个实施例中,处理器320进一步被配置成:根据预存储的放料辊道的辊道信息和型材信息确定放料辊道的最大允许放料数量,其中放料辊道与上料辊道平行;获取放料辊道的当前放料数量;在当前放料数量小于最大允许放料数量的情况下,根据型材信息确定桁架机械手的放料坐标;根据放料坐标控制桁架机械手动作,以对型材进行放料。
[0136]
在一个实施例中,辊道信息包括辊道宽度;型材信息包括型材宽度;处理器320进一步被配置成:根据辊道宽度、预设型材间隔宽度以及型材宽度,确定放料辊道的最大允许放料数量。
[0137]
在一个实施例中,辊道信息还包括辊道位置;型材信息还包括型材位置;放料坐标包括y轴方向的y轴放料坐标;处理器320进一步被配置成:确定型材位置与辊道位置之间的距离;根据距离、当前放料数量、型材宽度以及预设型材间隔宽度,确定桁架机械手在y轴方向上的y轴放料坐标;以及控制桁架机械手的y轴执行器按照y轴放料坐标动作。
[0138]
在一个实施例中,型材信息还包括型材高度;放料坐标包括z轴方向的z轴放料坐标;处理器320进一步被配置成:根据辊道位置和型材高度确定桁架机械手在z轴方向上的z轴放料坐标;以及控制桁架机械手的z轴执行器按照z轴放料坐标动作。
[0139]
在一个实施例中,处理器320进一步被配置成:在对每一个型材进行取料之后,对型材信息进行更新,以得到更新后的型材信息;在对每一个型材进行放料之后,对放料辊道的放料数量进行更新,以得到更新后的放料数量。
[0140]
在一个实施例中,更新后的型材信息包括更新后的型材数量;处理器320进一步被配置成:在更新后的型材数量为零的情况下,确定取料完成和/或放料完成;在更新后的放料数量达到最大允许放料数量的情况下,确定放料完成。
[0141]
在一个实施例中,处理器320进一步被配置成:将型材的型材信息与待取料型材的型材信息进行比对;在确定型材不是待取料型材的情况下,禁止桁架机械手动作。
[0142]
在一个实施例中,处理器320进一步被配置成:确定上料辊道上的型材的最大高度;在最大高度小于或等于桁架机械手的最大允许高度的情况下,发出允许取料信号。
[0143]
在一个实施例中,处理器320进一步被配置成:在最大高度大于最大允许高度的情况下,禁止桁架机械手动作。
[0144]
在一个实施例中,信息输入终端310包括远程输入终端和本地输入终端,本地输入终端还用于显示桁架机械手的运行信息和/或接收操作指令。
[0145]
可以理解,远程输入终端可以包括但不限于远程触摸屏等,可以方便用户远程输入型材信息。本地输入终端可以包括但不限于本地触摸屏等,除了方便用户输入型材信息之外,还可以进行桁架机械手的运行信息本地显示,运行信息比如运行的实时坐标、速度、故障记录等显示信息,此外还可以接收用户通过操作本地触摸屏上的组态的按钮输入的桁架机械手的操作指令,即可以操作桁架机械手单步运行。
[0146]
进一步地,在一些实施例中,本地输入终端还可以进行参数设置,比如桁架机械手x、y、z方向的速度值设定、桁架机械手的坐标基准点标定以及载荷传感器保护值设定。
[0147]
本发明实施例提供了一种桁架机械手,包括:x轴执行器;y轴执行器;z轴执行器;以及根据上述实施方式中的用于桁架机械手的控制装置。
[0148]
在一个实施例中,桁架机械手还包括夹具,夹具包括电磁吸盘。
[0149]
可以理解,电磁吸盘为特殊材料制作的永磁体,其作用是利用处理器(或控制器)给其发送的充磁脉冲信号将型材抓取,处理器(或控制器)发送退磁信号将型材释放,从而实现型材的搬运。
[0150]
本发明实施例提供了一种用于输送的生产线,包括根据上述实施方式中的桁架机械手。
[0151]
在一个实施例中,桁架机械手包括第一桁架机械手,被配置成:对上料辊道上的型材进行取料,并将型材放料至放料辊道上;在放料完成后存储型材信息,型材信息至少包括型材的位置信息;以及第二桁架机械手,与第一桁架机械手进行通信,被配置成:在取料之前向第一桁架机械手发送数据请求;接收第一桁架机械手响应于数据请求发送的型材信息;根据型材的位置信息和预存储的第一桁架机械手与第二桁架机械手的相对距离确定第二桁架机械手的取料坐标;以及根据取料坐标对放料辊道上的型材进行取料。
[0152]
可以理解,数据请求为关于型材信息的数据请求。
[0153]
具体地,第一桁架机械手用于对上料辊道上的型材进行取料,并将型材放料至放料辊道上,放料动作完成后可以存储型材信息,第二桁架机械手可以与第一桁架机械手进行通信以获取数据信息,第二桁架机械手可以在取料之前向第一桁架机械手发送数据请求,并接收第一桁架机械手响应于该数据请求发送的型材信息,进而根据型材的位置信息和预存储的第一桁架机械手与第二桁架机械手的相对距离确定第二桁架机械手的取料坐标,从而根据取料坐标对放料辊道上的型材进行取料。进一步地,第一桁架机械手与第二桁架机械手的相对距离为预先固定的数值,第二桁架机械手可以根据第一桁架机械手发送的型材的位置信息和预存储的第一桁架机械手与第二桁架机械手的相对距离进行坐标转换,从而确定第二桁架机械手的取料坐标,并根据该取料坐标对放料辊道上的型材进行取料。
[0154]
在一个实施例中,型材的位置信息与第一桁架机械手放料时的位置相关联。
[0155]
可以理解,第一桁架机械手在释放型材时的位置坐标即放料时的位置,与放料辊道上的型材的位置,两者存在关联关系,即可以根据该关联关系将第一桁架机械手放料时的位置进行转换,从而得到型材的位置信息。
[0156]
在一个实施例中,型材信息还包括型材类型、型材规格以及型材数量中的至少一者。
[0157]
在一个实施例中,生产线还包括:抛丸机,分别与第一桁架机械手、第二桁架机械手进行通信;第一桁架机械手还被配置成:在放料完成后发送放料完成信号至抛丸机;抛丸机被配置成:接收第一桁架机械手发送的放料完成信号;对放料辊道上的型材进行抛丸处理,以得到抛丸处理后的型材;在抛丸处理后发送允许取料信号至第二桁架机械手;第二桁架机械手还被配置成:接收抛丸机发送的允许取料信号;对抛丸处理后的型材进行取料。
[0158]
可以理解,抛丸机用于对放料辊道上的型材进行抛丸处理,例如除锈处理。
[0159]
具体地,第一桁架机械手在放料完成后,可以发送放料完成信号至抛丸机,抛丸机接收第一桁架机械手发送的放料完成信号,并对放料辊道上的型材进行抛丸处理,以得到抛丸处理后的型材,抛丸机在抛丸处理后发送允许取料信号至第二桁架机械手,第二桁架机械手在接收到抛丸机发送的允许取料信号后对抛丸处理后的型材进行取料,即开始进行取料。
[0160]
在一个实施例中,第二桁架机械手还被配置成:在取料后发送取料完成信号至第
一桁架机械手;第一桁架机械手还被配置成:接收第二桁架机械手发送的取料完成信号;根据先进先出的原则对存储的型材信息进行刷新。
[0161]
具体地,处理器在完成单个型材的取料动作或批次型材的取料动作后,发送取料完成信号至第一桁架机械手,第一桁架机械手接收该取料完成信号,并根据先进先出的原则对已经存储的型材信息进行刷新,以实现桁架机械手抓取的滚动自动化运行。
[0162]
目前的桁架机械手基本上均是作为单一的设备进行运行,只需完成载荷的搬运即可。而本发明实施例中的桁架机械手作为智能化产线的一部分,本发明实施例中创新性地提出产线上两台桁架机械手进行协同工作。具体地,第一桁架机械手和第二桁架机械手之间可以进行信息共享,以进行协同工作。第一桁架机械手将型材抓取并释放完成以后,其将型材的排布坐标信息及数量发送至第二桁架机械手。鉴于第一桁架机械手与第二桁架机械手之间有一段较长的辊道,该辊道例如可以排布三组型材,因此第一桁架机械手创建了一个全局数据块,该数据块能存储三组数据信息(型材类型、规格、数量、每根型材的位置坐标),当第一桁架机械手每批次放料完成后均会把数据存储在数组里。第二桁架机械手在型材抓取之前,向第一桁架机械手发送数据请求信息,第一桁架机械手将最先存储的数组信息发送给第二桁架机械手,由于第一桁架机械手和第二桁架机械手之间的空间相对坐标是恒定的,存在一个固定的函数关系,因此第一桁架机械手所排布的型材坐标经过换算以后可以直接成为第二桁架机械手的抓取坐标,即第一桁架机械手的释放坐标(即第一桁架机械手放料时的位置)可以换算成第二桁架机械手的抓取坐标。具体地,第一桁架机械手在完成型材释放以后,会自动发送批次放料完成信号给抛丸机,抛丸机接收该信号后开始输送型材并进行抛丸,抛丸结束后,抛丸机发送允许取料信号给第二桁架机械手,第二桁架机械手根据第一桁架机械手共享的信息对型材进行逐一抓取,直至该批次型材抓取/堆垛完成。在完成每一批次型材抓取以后,第二桁架机械手发送取料完成信号给第一桁架机械手,然后第一桁架机械手根据先进先出的原则将型材数组数据进行刷新,实现了桁架机械手抓取的滚动自动化运行。
[0163]
值得注意的是,本发明实施例中的第一桁架机械手和第二桁架机械手进行通信以实现信息共享的技术方案与上述实施例中提供的用于桁架机械手的控制方法的技术方案可以单独实施,也可以进行结合。
[0164]
智能搬运机械手可以包括传感器单元、智能控制系统(控制器)、执行单元、显示单元这几个部分,其可以组成一个全闭环控制机构。可通过传感器单元采集载荷重量、高度、位置等相关数据,智能控制系统进行算法调整,控制执行单元完成无人化载荷安全搬运,通过数据交互传输给上位机对当前数据进行实时显示。
[0165]
图4示意性示出了本发明一实施例中用于桁架机械手的控制系统的结构框图示意图。如图4所示,在一个实施例中,提供了一种用于桁架机械手的控制系统,硬件部分主要可以包括远程hmi触摸屏、上位机(工程师站)、本地hmi触摸屏、控制器、伺服驱动器、永磁铁、x轴向执行器、y轴向执行器、z轴向执行器以及传感器,其中:
[0166]
远程hmi触摸屏401,其作用为型材信息的录入确认,确认后的信息可以通过frofinet发送给上位机工程师站402。
[0167]
上位机(工程师站)402,其作用为采集来自于本地hmi触摸屏401发送的信息,并将数据下发给桁架机械手的控制器404,并采集桁架的相关信息。
[0168]
本地hmi触摸屏403,其作用是桁架机械手的运行信息本地显示,比如运行的实时坐标、速度、故障记录等信息显示;型材信息录入;参数设置,比如桁架机械手x、y、z方向速度值设定,桁架机械手的坐标基准点标定,载荷传感器保护值设定;桁架操作权限下,用户登录信息采集;桁架机械手在非自动运行状态下,兼作辅助操作设备,即通过本地触摸屏401上组态的按钮可以操作桁架机械手单步运行。
[0169]
控制器404,桁架机械手的核心控制单元,其负责数据采集,比如di数字开关量、超载传感器ai模拟量、编码器数据等,并进行逻辑运算输出控制do、或许通过frofinet控制伺服驱动器405。
[0170]
伺服驱动器405,其作用是根据控制器404所下发的命令,控制三维坐标执行器动作。
[0171]
x轴向执行器406、y轴向执行器407以及z轴向执行器408,为三维坐标执行器,负责执行伺服驱动器405的控制命令,完成桁架的精准定位。
[0172]
永磁铁409,为特殊材料制作,其作用是利用控制器404给其发送充磁脉冲信号将型材抓取,控制器404发送退磁信号将型材释放,从而实现型材的搬运。
[0173]
传感器410,其作用是提供桁架的实时信息给控制器404。
[0174]
为了更好呈现本发明实施例中的用于桁架机械手的控制系统构成,通过附图5至附图9作说明。具体地,图5示意性示出了本发明一实施例中带电电磁吸盘的桁架机械手的结构示意图;图6示意性示出了本发明一实施例中带电电磁吸盘的桁架机械手的主视示意图;图7示意性示出了本发明一实施例中带电电磁吸盘的桁架机械手的俯视示意图;图8示意性示出了本发明一实施例中带电电磁吸盘的桁架机械手的控制柜的外部示意图;图9示意性示出了本发明一实施例中带电电磁吸盘的桁架机械手的控制柜内平面示意图。
[0175]
机械结构说明如下:
[0176]
x轴驱动机构采用中间驱动两边输出的机构,保证两侧运行小车沿x轴方向运动保持同步,减速机采用低背隙蜗轮蜗杆减速机。
[0177]
y轴驱动机构采用中间驱动两边输出的结构,保证两侧输送提升轴沿y轴方向运动保持同步,减速机采用低背隙蜗轮蜗杆减速机。
[0178]
z轴驱动机构采用中间驱动两边输出的结构,保证两根提升轴上升保持同步,减速机采用低背隙蜗轮蜗杆减速机。
[0179]
x、y轴驱动机构采用中间驱动两边输出的结构,保证两侧运行小车沿x、y轴方向运动保持同步,减速机采用低背隙蜗轮蜗杆减速机。从而确保抓取较长型材的稳定性和安全性,杜绝型材抖动和晃动的情况。
[0180]
z轴驱动机构采用中间驱动两边输出的结构,保证两根提升轴上升保持同步,减速机采用低背隙蜗轮蜗杆减速机。从而确保型材两端不会因为偏重而翘起。
[0181]
桁架机械手的机构形式可以是框架式龙门双竖轴,z轴末端法兰负债可以是双z轴同时承受负载,驱动方式可以是齿轮齿条。
[0182]
桁架机械手的动作流程可以如下:
[0183]
1)首先,人工通过吊具按排程软件给出的型材将型材放置于上料输送线,同时确认型材详细信息(长度、种类、码放层数、码放列数等)。型材随输送线运行至桁架ⅰ(即第一桁架机械手)上料区域,输送线防呆装置确认型材信息后通知第一桁架机械手型材上料到
位,机械手执行上料动作。
[0184]
2)桁架ⅰ(第一桁架机械手)将码放好的型材依次取出,排列于喷砂机上料输送辊道,排放完成后通知总控系统(即控制器),型材通过喷砂机上料输送线输送进入喷砂机喷砂。
[0185]
3)喷砂完成后型材运行至喷砂机下料输送位置,桁架ⅱ(第二桁架机械手)根据输入的型材详细信息和相关的动作要求,将排列好的型材搬运码放至锯床输送线并根据需要堆垛(具体堆垛方式可以由排程系统提供)。其中若因为返工喷砂工艺,需要人工干预,则后续动作可以切换至人工手动操作。
[0186]
本发明实施例中的用于桁架机械手的控制系统的控制流程为:本地hmi触摸屏(20)或远程工程师站发送控制指令(包括伺服驱动器启/停命令、坐标信息以及来料信息等)至包括电磁铁的桁架机械手的plc控制器(27)。具体执行如下步骤往复运行:
[0187]
步骤(1),人工通过本地触摸屏系统按照排程软件给出的上料需求上料,完成后确认型材详细信息(长度、种类、码放层数、码放列数等),启动产线辊道将型材输送至桁架机械手抓取区域的上料输送线辊道,并发送通知信息给桁架机械手告知物料到达抓取位置,允许桁架机械手进行抓取,同时把型材信息同步发送至桁架机械手,桁架机械手执行取料动作。
[0188]
步骤(2),桁架机械手的动作执行流程为:桁架机械手的plc控制器(27)在接受到控制指令以后,将型材信息与plc中所存储的型材信息库数据进行比对(型材信息库通过本档案的型材信息录入技术建立),然后通过本发明实施例中的型材信息解析技术解提取型材数据。
[0189]
步骤(3),基于解析出的型材数据,利用本方案中的抓取三维坐标实时动态计算技术,将型材数据转换为动态三维抓取坐标。
[0190]
步骤(4),桁架机械手的plc控制器(27)将三维坐标发送至x轴伺服驱动器(21),x轴伺服驱动器(21)通过伺服电机驱动x轴双输出驱动(蜗轮蜗杆减速机机构)(3),从而驱动x轴主动滑移小车a和x轴主动滑移小车b而实现桁架机械手的x向小车移动,以实现x轴方向定位。
[0191]
步骤(5),桁架机械手plc控制器(27)将三维坐标发送至y轴伺服驱动器(25),y轴伺服驱动器(25)通过伺服电机驱动y轴双输出驱动(蜗轮蜗杆减速机机构)(11),从而驱动y轴滑移小车(z轴载板),以实现y轴方向定位。
[0192]
步骤(6),桁架机械手plc控制器(27)将三维坐标发送至z轴伺服驱动器(26),z轴伺服驱动器(26)通过伺服电机驱动z轴双输出驱动(蜗轮蜗杆减速机机构)(13),从而驱动z轴夹具主体上下移动,以实现z轴方向定位。
[0193]
步骤(7),三维坐标定位完成以后,电磁铁(18)充磁2s,充磁成功以后开始进行物料抓取。
[0194]
步骤(8),通过本方案中的释放三维坐标及释放数量实时动态计算技术,动态计算出三维型材释放坐标。
[0195]
步骤(9),根据三维坐标重复步骤(5)至步骤(7)进行型材在放料辊道上退磁2s释放,从而完成一次取料/放料循环。
[0196]
步骤(10),通过本方案中的释放三维坐标及释放数量实时动态计算技术,实时计
算出上料辊道上余料数量和放料辊道上已放料数量,若没有超过放料辊道上允许放料的最大数量,则重复步骤(5)至步骤(9),直至放料辊道上已放料数量达到最大允许放料数量,桁架机械手给上位机(工程师站)发送放料完成信号,放料结束。
[0197]
本发明实施例中的用于桁架机械手的控制系统适用于型材搬运生产线的零件的抓取和转运,在满足精度及速度的前提下,具有高强度、高抗震性结构,运行平稳可靠等特点。通过与总控设备实施联动控制,达到自动抓取和转运、堆垛。将伺服和电磁铁结合在一起,并且辅助控制程序,实现桁架的高精度运行,定位精度可以小于1mm,自动运行,在自动化产线上有广泛的使用需求,给社会带来极大的经济效益。
[0198]
本发明实施例提供的技术方案通过型材信息录入技术对型材信息录入的唯一性、准确性进行自动校验判别,并提供型材信息修正删除等功能,并且该功能模块具有独立性,在其他项目可以直接移植使用。以角钢为例,录入的信息包括型材规格、角钢尖角高度,型材斜边宽度、型材高度等信息,在手动从触摸屏上输入以上信息后,点击确认按钮即可完成型材信息的录入。
[0199]
在本发明实施例中,通过型材信息解析技术,相应的功能模块作为独立运行的单元,可以在其他项目独立运行,将排程系统输入的型材信息和本地数据库中的已存储数据自动进行比对,如果比对不成功,则弹出窗口提示型材查询失败,需要录入该种型材信息。当型材信息配对成功,则输出型材的相关信息。
[0200]
在本发明实施例中,通过三维坐标计算技术,根据型材的信息,结合现场辊道实际情况,自动计算辊道上允许放置型材的数量,并且将每一根型材所放置的坐标自动计算出来。一方面为第一台桁架提供型材放置坐标,另一方面,放置的坐标信息将通过两台桁架间的信息共享技术,传递给第二台桁架机械手,以作为第二台桁架机械手的抓取坐标。该模块作为独立的模块,接口独立,可以在其他项目直接移植使用。
[0201]
在本发明实施例中,通过桁架机械手间信息技术共享技术,第一桁架机械手需要将至少三组数据存储在本地数据块中,并且该数据需要在一定的条件下进行先后传递,比如第一桁架机械手已经抓取3组不同的型材,每次型材放置的数量、规格可能均不一样,并且3组型材均通过辊道输送至抛丸机辊道上,此时第二桁架机械手可能才开始抓取第一组型材,所以第一桁架机械手中存取的数组需要遵循先进先出的原则,信息存储时需要插入在数据块的尾部,当第二桁架机械手取完一组数据时,需要对数据进行移位。
[0202]
在一些实施例中,本发明的技术方案还可以运用于桁架搬运机械人中。
[0203]
本发明实施例提供了一种机器可读存储介质,该机器可读存储介质上存储有指令,该指令在被处理器执行时使得处理器执行根据上述实施方式中的用于桁架机械手的控制方法。
[0204]
以上结合附图详细描述了本发明的优选实施方式,但是,本发明并不限于上述实施方式中的具体细节,在本发明的技术构思范围内,可以对本发明的技术方案进行多种简单变型,这些简单变型均属于本发明的保护范围。
[0205]
另外需要说明的是,在上述具体实施方式中所描述的各个具体技术特征,在不矛盾的情况下,可以通过任何合适的方式进行组合。为了避免不必要的重复,本发明对各种可能的组合方式不再另行说明。
[0206]
此外,本发明的各种不同的实施方式之间也可以进行任意组合,只要其不违背本
发明的思想,其同样应当视为本发明所公开的内容。