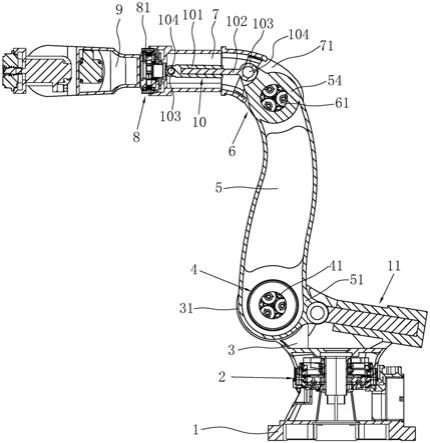
1.本实用新型涉及工业机器人技术领域,尤其涉及一种内置力矩平衡装置的工业机器人。
背景技术:2.工业机器人,特别是大负载工业机器人的垂直关节,一般都需要安装力矩平衡装置,不仅可以减小关节的驱动力矩和驱动功率,从而减小伺服电机和减速机的配置、重量和尺寸,而且可以减小不平衡力矩的波动,有利于控制和改善机器人的动力学特性,提高运行精度和稳定性。在工业机器人的应用中,力矩平衡系统主要分为附加配重式、弹簧式、气缸式以及液压
‑
气动式等。现有的平衡装置大多安装应用于机器人的二关节处,国内外主流大负载机器人第三关节大多采用配重式力矩平衡,不仅增加了机器人的关节负载和体积,增大了平衡缸受损的风险,而且影响了机器人的整体美观。
技术实现要素:3.本实用新型的目的是提供一种内置力矩平衡装置的工业机器人,通过在第三关节处设置氮气平衡缸,有效减少第三关节的驱动力矩,减小伺服电机和减速机的配置、重量和尺寸,并且可以大幅提升机器人特别是大型负载机器人的运行平稳性;同时氮气平衡缸内置,提高了对氮气平衡缸的保护性,降低了故障率,提升了机器人整体的安全和美观。
4.本实用新型的上述技术目的是通过以下技术方案得以实现的:
5.一种内置力矩平衡装置的工业机器人,包括底座、第一关节、第一轴臂、第二关节、第二轴臂、第三关节、第三轴臂、第四关节、第四轴臂;
6.所述第一轴臂一端通过第一关节与底座转动连接,且所述第一关节的转动轴线竖直设置;
7.所述第二轴臂一端通过第二关节与第一轴臂远离底座的一端转动连接,另一端通过第三关节与第三轴臂转动连接,所述第二关节、第三关节的转动轴线相互平行且与第一关节的转动轴线垂直;
8.所述第四轴臂一端通过第四关节与第三轴臂远离第二轴臂的一端转动连接,所述第四关节的转动轴线水平设置且与第三关节的转动轴线垂直;
9.所述第三关节包括两个位于其转动轴线两端且对称设置的第三减速机,其中一个所述第三减速机一侧设置有驱动两个第三减速机同步转动的第三伺服电机;
10.所述第三关节处设有位于两个第三减速机对称平面上的氮气平衡缸,所述氮气平衡缸一端与第二轴臂连接,另一端与第三轴臂连接。
11.通过采用上述技术方案,第一关节、第二关节、第三关节以及第四关节的设置实现机器人在三维立体空间内的转动,第三关节一个第三伺服电机驱动两个第三减速机同步转动,单电机双减速机的结构不仅可以传递双倍扭矩,而且在输出扭矩相同的情况下,有效减小第三减速机的体积。当第三轴臂及第四轴臂位于竖直姿态时,氮气平衡缸处于自由状态,
力矩为最小值;当第三轴臂绕其转动轴线摆动时,氮气平衡缸被拉伸或压缩,给第三轴臂提供运动方向相反的作用力,起到平衡力矩的作用。这样在第三关节处设置氮气平衡缸,相较于现有技术在第二关节处设置平衡装置,有效减少第三关节的驱动力矩,减小伺服电机和减速机的配置、重量和尺寸,并且可以大幅提升机器人特别是大型负载机器人的运行平稳性。其中,氮气平衡缸设置在两个第三减速机的对称平面上,避免重心偏移,保证氮气平衡缸的平衡效果。采用氮气平衡缸作为力矩平衡装置,取代传统的弹簧平衡缸,其结构简单、体积较小、方便安装,可以实现机器人在不同负载、不同位置情况下的完全力矩平衡,有利于改善机器人的动力学特性。
12.进一步地,所述氮气平衡缸一端转动连接在第二轴臂靠近第三轴臂的一端,另一端转动连接在第三轴臂靠近第四关节的一端,其转动轴线平行于第三关节的转动轴线;此时,所述第三关节的两个第三减速机安装在第三轴臂上。
13.通过采用上述技术方案,提供一种氮气平衡缸连接在第二轴臂和第三轴臂上的安装方式,此时第三关节的两个第三减速机安装在第三轴臂上,经过三维模拟和加工判断,两个第三减速机安装在第三轴臂上使得机器人的结构更合理,稳定性更好。
14.进一步地,所述第三轴臂内为腔体结构,所述氮气平衡缸内置在第三轴臂的腔体内。
15.通过采用上述技术方案,氮气平衡缸内置在第三轴臂的腔体内,不仅提高了对氮气平衡缸的保护性,降低氮气平衡缸的故障率,提高机器人整体的安全和美观;而且由于要在第三轴臂内给氮气平衡缸留出安装空间,则需要将第四关节前置,这样由于氮气平衡缸的力矩平衡作用以及第四关节前置带来的中心前移,可以将将第四关节中第四减速机、第四伺服电机的功率配置、重量、体积等缩小30%以上。
16.进一步地,所述第三轴臂靠近第二轴臂的一端设有两个用于安装第三减速机的侧耳,两个所述侧耳之间形成与第三轴臂的腔体连通的让位口;所述第二轴臂靠近第三轴臂的一端设有安装在让位口内的凸耳,所述第三伺服电机的驱动轴穿过两个第三减速机和凸耳;所述氮气平衡缸靠近第二轴臂的一端与凸耳转动连接,远离第二轴臂的一端转动连接在第三轴臂腔体内。
17.通过采用上述技术方案,两个侧耳和之间的让位口使得第三轴臂靠近第二轴臂的一端形成分叉结构,第二轴臂上的凸耳安装在让位口内,两个第三减速机安装在侧耳上,第三伺服电机的驱动轴穿过两个第三减速机和凸耳,实现第二轴臂和第三轴臂之间的转动连接。氮气平衡缸一端转动连接在凸耳上,实现氮气平衡缸与第二轴臂的转动连接;氮气平衡缸另一端转动连接在第三轴臂腔体内,实现氮气平衡缸与第三轴臂的转动连接。
18.进一步地,所述氮气平衡缸一端转动连接在第三轴臂靠近第二轴臂的一端,另一端转动连接在第二轴臂靠近第一轴臂的一端,其转动轴线平行于第三关节的转动轴线;此时,所述第三关节的两个第三减速机安装在第二轴臂上。
19.通过采用上述技术方案,提供另一种氮气平衡缸连接在第二轴臂和第三轴臂上的安装方式,此时第三关节的两个第三减速机安装在第二轴臂上,这样第四关节、第四轴臂的结构无需改变,降低设计成本。
20.进一步地,所述第二轴臂内为腔体结构,所述氮气平衡缸内置在第二轴臂的腔体内。
21.通过采用上述技术方案,氮气平衡缸内置在第二轴臂的腔体内,提高对氮气平衡缸的保护性,降低氮气平衡缸的故障率,提高机器人整体的安全和美观。
22.进一步地,所述第二轴臂靠近第三轴臂的一端设有两个用于安装第三减速机的耳座,两个所述耳座之间形成与第二轴臂的腔体连通的耳口;所述第三轴臂靠近第二轴臂的一端设有安装在耳口内的延伸耳,所述第三伺服电机的驱动轴穿过两个第三减速机和延伸耳;所述氮气平衡缸靠近第三轴臂的一端与延伸耳转动连接,远离第三轴臂的一端转动连接在第二轴臂腔体内。
23.通过采用上述技术方案,两个耳座和之间的耳口使得第二轴臂靠近第三轴臂的一端形成分叉结构,第三轴臂上的延伸耳安装在耳口内,两个第三减速机安装在耳座上,第三伺服电机的驱动轴穿过两个第三减速机和耳座,实现第二轴臂和第三轴臂之间的转动连接。氮气平衡缸一端转动连接在耳座上,实现氮气平衡缸与第三轴臂的转动连接;氮气平衡缸另一端转动连接在第二轴臂腔体内,实现氮气平衡缸与第二轴臂的转动连接。
24.进一步地,所述氮气平衡缸包括缸体和滑动安装在缸体的活塞杆,且所述活塞杆伸出缸体的一端靠近第三关节,所述缸体远离活塞杆的一端远离第三关节。
25.通过采用上述技术方案,氮气平衡缸的活塞杆靠近第三关节,缸体远离第三关节,这样保证在第三轴臂绕其转动轴线摆动时,氮气平衡缸被拉伸或压缩,给第三轴臂提供运动方向相反的作用力,起到平衡力矩的作用,保证氮气平衡缸的使用效果。
26.进一步地,所述第二关节处设有外置平衡缸,所述外置平衡缸一端转动连接在第一轴臂上,另一端转动连接在第二轴臂靠近第一轴臂的一端,且其转动轴线与第二关节的转动轴线平行。
27.通过采用上述技术方案,在第二关节设置外置平衡缸,可以有效减小第二关节的驱动力矩,从而减小第二关节处伺服电机和减速机的配置、重量和尺寸,并且可以大幅度提升机器人特别是大型负载机器人的运行平稳性。
28.综上所述,本实用新型具有以下有益效果:
29.1、在机器人第二关节处设置外置平衡缸、在第三关节处设置氮气平衡缸,可以有效减少第二关节、第三关节的驱动力矩,从而减小伺服电机和减速机的配置、重量和尺寸,并且可以大幅提升机器人特别是大型重负载机器人的运行平稳性;
30.2、第三关节处设置两个第三减速机并利用一个第三伺服电机同步驱动,单电机双减速机的结构不仅可以传递双倍扭矩,而且在输出扭矩相同的情况下,有效减小第三减速机的体积;
31.3、利用氮气平衡缸取代传统的弹簧平衡缸、配重式平衡装置等,结构简单,便于安装,可以实现机器人在不同载荷、不同位置情况下的完全力矩平衡,有利于改善机器人的动力学特性;
32.4、将氮气平衡缸内置在第二轴臂或第三轴臂内,提高对氮气平衡缸的保护性,降低故障率,提升机器人整体的安全性和美观度;
33.5、将氮气平衡缸内置在第三轴臂内时,需要将第四关节的第四减速机和第四伺服电机前置,进而减小了第四关节所承受的弯矩,从而可以将第四关节减速机与伺服电机的功率配置、重量、体积缩小30%以上。
附图说明
34.图1是一种内置力矩平衡装置的工业机器人的氮气平衡缸内置在第三轴臂内的整体示意图;
35.图2是一种内置力矩平衡装置的工业机器人的氮气平衡缸内置在第三轴臂内的剖视图;
36.图3是一种内置力矩平衡装置的工业机器人的氮气平衡缸内置在第二轴臂内的整体示意图;
37.图4是一种内置力矩平衡装置的工业机器人的氮气平衡缸内置在第二轴臂内的剖视图。
38.图中,1、底座;2、第一关节;3、第一轴臂;31、安装耳;32、安装口;4、第二关节;41、第二减速机;42、第二伺服电机;5、第二轴臂;51、连接耳;52、耳座;53、耳口;54、凸耳;6、第三关节;61、第三减速机;62、第三伺服电机;7、第三轴臂;71、侧耳;72、让位口;73、延伸耳;8、第四关节;81、第四减速机;82、第四伺服电机;9、第四轴臂;10、氮气平衡缸;101、缸体;102、活塞杆;103、连接环;104、连接轴;11、外置平衡缸。
具体实施方式
39.以下结合附图和实施例,对本实用新型进行进一步详细说明。应当理解,此处所描述的具体实施例仅用以解释本实用新型,并不用于限定本实用新型。
40.一种内置力矩平衡装置的工业机器人,如图1或图3所示,包括底座1、第一关节2、第一轴臂3、第二关节4、第二轴臂5、第三关节6、第三轴臂7、第四关节8、第四轴臂9、第五关节、第五轴臂和第六关节,六个关节均由减速机和伺服电机构成,用于相邻关节之间的转动连接。
41.如图1或图3所示,具体为,第一轴臂3下端通过第一关节2与底座1转动连接,且第一关节2的转动轴线竖直设置,带动其他轴臂沿竖直轴线转动。第一轴臂3左上端通过第二关节4与第二轴臂5下端转动连接,第二轴臂5上端通过第三关节6与第三轴臂7右端转动连接,且第二关节4和第三关节6的转动轴线水平垂直于第一关节2的转动轴线,带动二、三、四、五轴臂前后摆动。第三轴臂7左端通过第四关节8与第四轴臂9右端转动连接,且第四关节8的转动轴线垂直于第一关节2、第二关节4的转动轴线,带动第五轴臂沿水平轴线转动。第四轴臂9左端通过第五关节与第五轴臂转动连接,且第五关节的转动轴线平行与第三关节6的转动轴线。第五轴臂另一端设有第六关节,可以连接第六轴臂,且第六关节的转动轴线垂直于第五关节的转动轴线。
42.如图1和图2所示,第二关节4包括两个对称设置在其转动轴线两端的第二减速机41,其中一个第二减速机41的一侧连接驱动两个第二减速机41同步转动的第二伺服电机42,而两个第二减速机41安装在第一轴臂3上。具体为,在第一轴臂3左上端设有与其一体成型的用于安装两个第二减速机41的安装耳31,两个安装耳31之间形成位于两个第二减速机41对称平面上的安装口32;第二轴臂5下端设有凸出的连接耳51,连接耳51安装在安装口32内,且第二伺服电机42的驱动轴穿过两个第二减速机41和连接耳51,实现第一轴臂3和第二轴臂5之间的转动连接。
43.如图1和图2所示,在第二关节4处设有外置平衡缸11,外置平衡缸11一端转动连接
在第二轴臂5的连接耳51上,另一端转动连接在第一轴臂3的右上端,且外置平衡缸11两端的转动轴线平行于第二关节4的转动轴线。当第二轴臂5位于竖直姿态时,外置平衡缸11处于自由状态,力矩为最小值;当第二轴臂5带动其他轴臂摆动时,外置平衡缸11被拉伸或压缩,给第二轴臂5提供运动方向相反的作用力,起到平衡力矩的作用。在本实施例中,外置平衡缸11为氮气平衡缸,结构简单,方便安装,平衡稳定。外置平衡缸11包括与第一轴臂3转动连接的缸筒和与第二轴臂5上连接耳51转动连接的缸杆,缸杆滑动安装在缸筒内。
44.如图1和图2所示,第三关节6也包括两个位于其转动轴线两端且对称设置的第三减速机61,其中一个第三减速机61一侧设置有驱动两个第三减速机61同步转动的第三伺服电机62。第三关节6处设有位于两个第三减速机61对称平面上的氮气平衡缸10,且氮气平衡缸10一端与第二轴臂5连接,另一端与第三轴臂7连接。当第三轴臂7及第四轴臂9位于竖直姿态时,氮气平衡缸10处于自由状态,力矩为最小值;当第三轴臂7绕其转动轴线摆动时,氮气平衡缸10被拉伸或压缩,给第三轴臂7提供运动方向相反的作用力,起到平衡力矩的作用。
45.第二关节4和第三关节6均为单电机双减速机结构,不仅可以传递双倍扭矩,而且在输出扭矩相同的情况下,有效减小第二减速机41、第三减速机61的体积。在第二关节4处设置外置平衡缸11、在第三关节6处设置氮气平衡缸10,可以有效减少第二关节4、第三关节6的驱动力矩,从而减小伺服电机和减速机的配置、重量和尺寸,并且可以大幅提升机器人特别是大型重负载机器人的运行平稳性。利用氮气平衡缸10取代传统的弹簧平衡缸、配重式平衡装置等,结构简单、体积较小、便于安装,可以实现机器人在不同载荷、不同位置情况下的完全力矩平衡,有利于改善机器人的动力学特性。
46.如图2或图4所示,氮气平衡缸10包括缸体101和滑动安装在缸体101的活塞杆102,且活塞杆102伸出缸体101的一端靠近第三关节6,缸体101远离活塞杆102的一端远离第三关节6。其中,为了提高对氮气平衡缸10的保护性,降低故障率,提升机器人整体的安全性和美观度,氮气平衡缸10内置在第二轴臂5或第三轴臂7内。
47.氮气平衡缸10内置在第三轴臂7内时,第三关节6的两个第三减速机61安装在第三轴臂7右端;氮气平衡缸10内置在第二轴臂5内时,第三关节6的两个第三减速机61安装在第二轴臂5上端。这样就对应两种不同的第二轴臂5、第三轴臂7结构,下面具体阐述。
48.如图1和图2所示,氮气平衡缸10内置在第三轴臂7内时,第三轴臂7内为腔体结构,氮气平衡缸10内置在第三轴臂7的腔体内,且氮气平衡缸10的活塞杆102端与第二轴臂5上端转动连接,缸体101端与第三轴臂7的左内端壁转动连接。具体为,在第三轴臂7靠近第二轴臂5的右端设有两个用于安装第三减速机61的侧耳71,两个侧耳71之间形成与第三轴臂7的腔体连通的让位口72,两个侧耳71和让位口72形成分叉结构。在第二轴臂5靠近第三轴臂7的上端设有安装在让位口72内的凸耳54,第三伺服电机62的驱动轴穿过两个第三减速机61和凸耳54,且氮气平衡缸10的活塞杆102与凸耳54转动连接。
49.如图2所示,在本实施例中,在氮气平衡缸10的缸体101和活塞杆102相互远离的一端分别设有连接环103,且连接环103的轴线沿第三关节6的转动轴线设置;在凸耳54和第三轴臂7的左内端壁上分别设有与连接环103配合的连接轴104,氮气平衡缸10通过连接环103和连接轴104的配合实现与第二轴臂5、第三轴臂7的转动连接。其中,在连接环103和连接轴104之间可以设置轴承,保证转动的稳定性。
50.如图2和图4所示,将氮气平衡缸10内置在第三轴臂7内时,需要在第三轴臂7预留安装氮气平衡缸10的位置,而为保证整个机器人轴臂长度一定,就需要将第四关节8的第四减速机81和第四伺服电机82前置,进而减小了第四关节8所承受的弯矩,从而可以将第四关节8中第四减速机81与第四伺服电机82的功率配置、重量、体积缩小30%以上。
51.如图3和图4所示,氮气平衡缸10内置在第二轴臂5内时,第二轴臂5为腔体结构,氮气平衡缸10安装在第二轴臂5的腔体内,且氮气平衡缸10的活塞杆102端与第三轴臂7靠近第二轴臂5的右端连接,氮气平衡缸10的缸体101端与第二轴臂5远离第三轴臂7的下内端壁转动连接。具体为,在第二轴臂5靠近第三轴臂7的一端设有两个用于安装第三减速机61的耳座52,两个耳座52之间形成与第二轴臂5的腔体连通的耳口53,两个耳座52和耳口53形成分叉结构。在第三轴臂7靠近第二轴臂5的一端设有安装在耳口53内的延伸耳73,第三伺服电机62的驱动轴穿过两个第三减速机61和延伸耳73,且氮气平衡缸10的活塞杆102端与延伸耳73转动连接。
52.如图2和图4所示,与氮气平衡缸10内置在第三轴臂7内时不同的是,此时是延伸耳73和第二轴臂5的下内端壁设有与氮气平衡缸10两端连接环103配合的连接轴104,实现氮气平衡缸10和第二轴臂5、第三轴臂7的转动连接。氮气平衡缸10内置在第二轴臂5内时,第三轴臂7前端的第四关节8就无需改变,降低设计成本。
53.本实用新型的工作原理和使用方法:
54.第二关节4和第三关节6均为单电机双减速机结构,不仅可以传递双倍扭矩,而且在输出扭矩相同的情况下,有效减小第二减速机41、第三减速机61的体积。在第二关节4处设置外置平衡缸11、在第三关节6处设置氮气平衡缸10,可以有效减少第二关节4、第三关节6的驱动力矩,从而减小伺服电机和减速机的配置、重量和尺寸,并且可以大幅提升机器人特别是大型重负载机器人的运行平稳性。
55.当第二轴臂5位于竖直姿态时,外置平衡缸11处于自由状态,力矩为最小值;当第二轴臂5带动其他轴臂摆动时,外置平衡缸11被拉伸或压缩,给第二轴臂5提供运动方向相反的作用力,起到平衡力矩的作用。当第三轴臂7及第四轴臂9位于竖直姿态时,氮气平衡缸10处于自由状态,力矩为最小值;当第三轴臂7绕其转动轴线摆动时,氮气平衡缸10被拉伸或压缩,给第三轴臂7提供运动方向相反的作用力,起到平衡力矩的作用。
56.将氮气平衡缸10内置在第二轴臂5或第三轴臂7内,提高对氮气平衡缸10的保护性,降低故障率,提升机器人整体的安全性和美观度;同时,将氮气平衡缸10内置在第三轴臂7内时,需要将第四关节8的第四减速机81和第四伺服电机82前置,进而减小了第四关节8所承受的弯矩,从而可以将第四关节8中第四减速机81与第四伺服电机82的功率配置、重量、体积缩小30%以上。
57.上述说明示出并描述了本实用新型的优选实施例,如前所述,应当理解本实用新型并非局限于本文所披露的形式,不应看作是对其他实施例的排除,而可用于各种其他组合、修改和环境,并能够在本文所述实用新型构想范围内,通过上述教导或相关领域的技术或知识进行改动。而本领域人员所进行的改动和变化不脱离本实用新型的精神和范围,则都应在本实用新型所附权利要求的保护范围内。