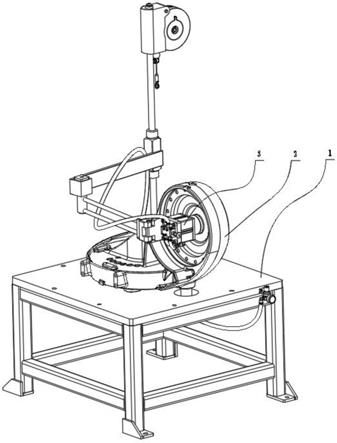
1.本实用新型涉及油封装配工装技术领域,尤其涉及一种适用于超大本体的油封装配工装。
背景技术:2.在工业应用领域,对超大本体的油封装配,通常借用定心轴,将油封套在定心轴上,油封装配要求要有良好的定心度,压装深度又有准确的位置要求。目前一种方式是采用人工敲击方式进行装配作业,该装配方式,对操作工人的技能要求高,且劳动强度大,尤其是大直径油封,定心轴的重量也较大,采用人工敲击的办法可能导致敲击力偏斜,导致油封不正或骨架变形,影响密封性能或损坏油封,且会导致漏油、摩擦力矩增大进而导致油封失效,此外,油封压装偏斜后,不便于返修处理,只有破坏油封取出,导致成本高,作业保证力不足。
3.对超大本体的油封装配另一方法,是采用超大定位工装平台,利用工装进行超大本体定心,再进行工装油封压装,该设施,存在工装大,结构复杂,场地占用大,造价高的特点。同时,还需满足超大本体的吊装可行性实施,将超大本体放置在定位工装台上,以实施油封的压装,装配效率低。
技术实现要素:4.本实用新型提供了一种适用于超大本体的油封装配工装,以解决现有技术中通过人工装配导致劳动强度大,且易导致骨架变形和密封性受损,通过超大定位工装平台导致造价高,占用场地大,装配效率低的问题。
5.本实用新型采用的技术方案是:提供一种适用于超大本体的油封装配工装,包括油封定位轴、压装模块执行机构、气压控制机构;所述压装模块执行机构包括执行气缸、安装在所述执行气缸上的压装模块、安装在所述执行气缸伸缩轴上的拉杆,所述压装模块中部设置有压装深度限位台阶孔,所述拉杆端部设置有压装台阶;所述油封定位轴包括安装板、固定安装在所述安装板一侧的芯轴、通过铰制孔螺栓安装在所述安装板另一侧的转向压板;所述超大本体和油封依次套设在所述芯轴上并被所述安装板限位,所述芯轴和所述安装板的中部具有供所述拉杆穿过的过穿孔,所述转向压板用于卡合所述拉杆,所述拉杆端部的压装台阶对所述转向压板进行限位,所述压装深度限位台阶孔对油封的压装深度进行限位,所述气压控制机构安装在所述执行气缸上并对执行气缸提供动力。
6.优选地,所述转向压板上设置有与所述铰制孔螺栓相配合的铰制固定孔,所述转向压板呈吊钩状,其中部形成压装弧形槽,所述转向压板的压装弧形槽用于卡入所述拉杆。
7.优选地,所述气压控制机构包括通过气管相连的气源控制阀和气压调节阀,所述气源控制阀通过螺栓及后固定板安装在所述执行气缸上。
8.优选地,还包括助力机构,所述助力机构包括助力臂、铰链板、固定铰板,所述铰链板铰接在所述助力臂的一端,所述铰链板通过销与所述固定铰板连接,所述固定铰板通过
螺栓固定在所述后固定板上。
9.优选地,还包括安装所述助力机构的工作台。
10.本实用新型的有益效果是:(1)本实用新型提供一款可移动式,可转向角度的轻便油封压装工装,以保证作业效率高,精确控制压装位置,从而达到降低制造成本的目的。
11.(2)本实用新型提供一种适用于超大本体的油封装配工装操作简单,省力,对工人熟练程度无要求,可靠性有保障,位置深度可精确控制,大大提高工业领域超大本体油封装配实施的作业效率。
附图说明
12.图1为本实用新型实施例1公开的一种适用于超大本体的油封装配工装的结构示意图。
13.图2为本实用新型公开的压装模块执行机构的结构示意图。
14.图3为本实用新型公开的油封定位轴的结构示意图。
15.图4为本实用新型公开的气压控制机构的结构示意图。
16.图5为本实用新型公开的助力机构的结构示意图。
17.图6为本实用新型实施例2公开的一种适用于超大本体的油封装配工装的结构示意图。
18.图7为本实用新型实施例3公开的一种适用于超大本体的油封装配工装的结构示意图。
19.图8为本实用新型实施例3公开的一种适用于超大本体的油封装配工装的局部破视图。
20.附图标记:1、工作台;2、超大本体;3、油封装配工装;31、油封定位轴;311、安装板;312、芯轴;3121、安装盘;3122、过穿孔;313、转向压板;3131、铰制固定孔;3132、压装弧形槽;314、铰制孔螺栓;32、助力机构;321、助力臂;322、铰链板;3221、槽;3222、螺钉孔;323、固定铰板;324、销;325、挡圈;33、压装模块执行机构;331、执行气缸;332、压装模块;3321、压装深度限位台阶孔;333、拉杆;3331、压装台阶;334、后固定板;34、气压控制机构;341、气源控制阀;342、气管;343、气压调节阀;4、油封。
具体实施方式
21.为了使本实用新型的目的、技术方案和优点更加清楚,下面将结合附图对本实用新型作进一步详细描述,但本实用新型的实施方式不限于此。
22.实施例1:
23.参见图1,本实施例公开一种适用于超大本体的油封装配工装,包括油封定位轴31、压装模块执行机构33、气压控制机构34。
24.参见图2,压装模块执行机构33包括执行气缸331、压装模块332、拉杆333以及后固定板334。其中压装模块332中部设置有压装深度限位台阶孔3321,将压装深度限位台阶孔3321穿过执行气缸331的伸缩轴进而将压装模块332安装在执行气缸331的端面上。拉杆333安装在执行气缸331的伸缩轴上的,拉杆333端部设置有压装台阶3331。后固定板334安装在执行气缸331的后部,用于给气压控制机构34提供安装位。
25.参见图3,油封定位轴31包括安装板311、芯轴312、转向压板313以及铰制孔螺栓314。其中芯轴312端部设置有安装盘3121,安装盘3121通过螺栓安装在安装板311的一侧。转向压板313通过铰制孔螺栓314安装在安装板311的另一侧,具体的,转向压板313上设置有与铰制孔螺栓314相配合的铰制固定孔3131,使得转向压板313能够相对于铰制孔螺栓314转动。转向压板313呈吊钩状,其中部形成压装弧形槽3132。芯轴312和安装板311的中部具有供拉杆333穿过的过穿孔3122。
26.参见图4,气压控制机构34包括通过气管342相连的气源控制阀341和气压调节阀343,气源控制阀341通过螺栓安装在后固定板334上,气压控制机构34用于给执行气缸331提供动力。
27.在使用的过程中,将超大本体2和油封4依次套设在芯轴312上,使安装板311或安装盘3121对超大本体2进行限位。然后由工作人员抱起执行气缸331,使拉杆333穿过芯轴312和安装板311中部的过穿孔3122,然后转动转向压板313,使转向压板313的压装弧形槽3132卡入拉杆333,在执行气缸331的伸缩轴带动拉杆333收缩的过程中,拉杆333端部的压装台阶3331对转向压板313进行限位,并且压装模块332上设置的压装深度限位台阶孔3321可以对油封4的压装深度进行限位,从而保证油封4能准确的压入超大本体2内。
28.实施例2
29.本实施例与实施例1的区别在于,本实施例除了包括实施例1的所有部件外,还包括助力机构32。
30.参见图5、图6,助力机构32包括助力臂321、铰链板322、固定铰板323,助力臂321有3个自由旋转副铰链:j1、j2、j3,以及弹簧吊,能在图中h方向上下移动。助力臂321为现有技术,本实施例不对其结构做具体分析。铰链板322上设置有与助力臂321一端相连接的槽3221和螺钉孔3222。铰链板322通过销324和挡圈325与固定铰板323铰接,固定铰板323通过螺钉固定在后固定板334上。由于助力臂321的能轻易的将压装模块执行机构33旋转至需要的方向及高度,从而极大的方便工作人员进行操作,大大节省了劳动强度。
31.实施例3
32.本实施例与实施例2的区别在于,本实施例除了包括实施例2的所有部件外,还包括工作台1。
33.参见图7,为了更便利的安装超大本体2,还可以将助力机构32安装在工作台1上,从而为超大本体2提供了一个更稳定的安装环境。
34.参见图8,在使用的过程中,将超大本体2放置在工作台1上,不用固定,位置无要求。让芯轴312依次穿过超大本体2中部的轴孔和油封4,使安装板311或安装盘3121对超大本体2进行限位。转动助力臂321,使执行气缸331上的使拉杆333穿过芯轴312和安装板311中部的过穿孔3122,然后转动转向压板313,使转向压板313的压装弧形槽3132卡入拉杆333,在执行气缸331的伸缩轴带动拉杆333收缩的过程中,拉杆333端部的压装台阶3331对转向压板313进行限位,并且压装模块332上设置的压装深度限位台阶孔3321可以对油封4的压装深度进行限位,从而保证油封4能准确的压入超大本体2内。
35.以上实施例仅用以说明本实用新型的技术方案,而非对其限制;尽管参照前述实施例对实用新型进行了详细的说明,本领域的普通技术人员应当理解:其依然可以对前述各实施例所记载的技术方案进行修改,或者对其中部分技术特征进行等同替换;而这些修
改或者替换,并不使相应技术方案的本质脱离本实用新型各实施例技术方案的精神和范围。