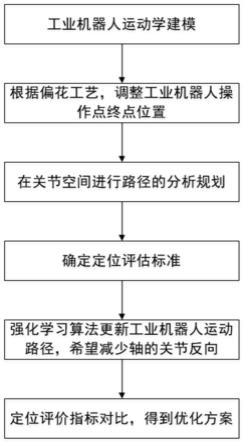
1.本发明涉及工业机器人领域,尤其涉及一种减少工业机器人关节反向的板料定位方法。
背景技术:2.当前门类制造过程中的板料压纹环节,存在不同的偏花工艺,而所谓偏花工艺的效果,是由压纹前放置板料时的位置偏移量所实现的,因此涉及到板料的定位精度问题,需要严格控制好定位的误差。
3.目前在工业领域,板料上料定位环节主要有两种方式,一种是人工手动放置定位,除此之外,还会使用工业机器人,通过末端操作点吸盘吸附的方式搬运板料,再根据预设的程序执行,移动到对应位置进行板料的放置定位。
4.纯人工进行上料及定位出现的误差由人工操作决定,对人员技术水平要求极高,效率极低,会造成人力物力资源的大量浪费。
5.而使用工业机器人时,其在运动过程中会产生绝对定位误差,此类误差来源之一就是关节反向,即关节正反转交替时会出现减速器回差,从而影响绝对定位精度。如果关节反向次数过多,会造成较大的绝对定位误差。这种情况就会导致在改变偏花工艺时,板料放置定位时的实际位置与期望位置偏差过大,造成无法进行下一步的压纹操作或压纹后压纹板不符合精度要求报废等情况。
6.因此,目前工业上板料定位环节还是需要人工干预,即改变偏花工艺后,在板料放置完毕时,仍需专业工作人员进行人工测量校准,如误差过大则要再进行多次微调,纯人工上料时需手动微调板料位置,而使用工业机器人上料时需手动微调工业机器人相关设置参数再通过多次实际放置进行验证,进而会增加人力物力,降低生产效率。
技术实现要素:7.本发明目的在于针对现有技术的不足,提出一种减少工业机器人关节反向的板料定位方法,本发明方法能在板料压纹需改变偏花工艺时,通过工业机器人末端操作点运动路径的分析,有效减少关节反向出现的情况,即减少关节正反转的次数,降低板料放置到压纹台时的定位误差,避免后续多次人工干预的同时也提高定位的准确性,推动下一步的压纹以及后续生产环节的顺利进行,提高生产效率。
8.本发明的目的是通过以下技术方案来实现的:一种减少工业机器人关节反向的板料定位方法,包括以下步骤:
9.步骤1:建立工业机器人的d-h模型;
10.步骤2:改变偏花工艺时,根据新的偏移距离,在工业机器人工作空间内调整其末端操作点终点,记为o
x
,其余点可沿用改变偏花工艺前的点,记起点为o1,和若干中间点中第i个点为oi,其中i∈(1,x),共x个点;
11.步骤3:利用强化学习算法,以工业机器人运送板料过程中减少各轴的关节反向次
数,即各轴运动所需的最少关节反向次数到达目标点为优化目标,强化学习过程中状态为工业机器人末端操作点位姿,动作为各轴的关节正转和关节反转的转动角度,以单次轴关节转动的奖励减去轴出现关节反向情况或当轴的转动角度超过限制时的惩罚作为瞬时回报进行强化学习得到满足优化目标的规划路径。
12.进一步地,步骤1包括以下子步骤:
13.(1.1)根据d-h建模过程的连杆坐标系约定,建立工业机器人各个轴的连杆坐标系;
14.(1.2)用关节角、杆件长度、扭转角和横距这4个参数来描述工业机器人杆件运动,创建d-h参数表,用于后续的路径分析规划;
15.(1.3)由d-h参数表计算得到末端操作点坐标系到机器人基坐标系下的齐次变换矩阵,得到工业机器人的d-h模型。
16.进一步地,步骤3包括以下子步骤:
17.(3.1)强化学习算法采用sarsa算法,sarsa算法采取q表作为动作策略的选取参照,因此需初始化q表,该表以状态为行,以动作为列,q表中的q值表示特定状态下的动作价值;
18.(3.2)在某时刻t,初始化状态s
t
,s
t
为工业机器人末端操作点的起点位姿,再根据ε-贪婪策略从当前状态s
t
的所有可能的关节正转ω和关节反转-ω动作中选择一个动作a
t
,ω为当前工业机器人各轴可实现的最小转动角度;
19.(3.3)通过ε-贪婪策略选择的动作a
t
,a
t
为当前时刻某一轴的关节正转ω或反转-ω,在当前状态s
t
下执行动作a
t
,得到状态s
t+1
,s
t+1
为工业机器人末端操作点的下一个位姿,同时还有瞬时回报r
t
,r
t
由两部分组成,r
t
=r
t-p
t
,r
t
为单次轴关节转动的奖励,而p
t
为轴出现关节反向情况或当轴的转动角度超过限制时的惩罚;
20.(3.4)在当前状态s
t+1
的各轴关节所有可能的关节正转ω和关节反转-ω动作中按ε-贪婪策略选择一个动作a
t+1
;
21.(3.5)根据新的q值q(s
t+1
,a
t+1
),更新价值函数以及状态和动作,学习并寻找得到最大回报的各轴关节正转和反转的策略。如当前状态非最终状态,则重复执行(3.3)至(3.5)这三步,期望板料运送定位过程中获得最大的累计回报t为总运料时长;
22.(3.6)直到s为最终状态,最终状态为工业机器人末端操作点的终点位姿,此时q(s,a)收敛,迭代执行完毕,当q(s,a)收敛时,ε-贪婪策略同时也收敛,得到最优策略,分析得到规划后的运动路径。
23.进一步地,步骤(3.2)中,ε-贪婪策略具体如下:
[0024][0025]
其中q(s,a)为价值函数;ε为0.1,表示探索率,有1-ε的概率从各轴的关节正转和反转中选择有最大价值的动作行动,有ε的概率随机行动;a为各轴的关节正转和关节反转的动作集;m为各轴关节正转和反转的所有可选动作数;表示以ε的概率在各轴正转和反
转行为中选中动作a的概率;a
*
为当前有最大价值的动作,即某一轴的关节正转或反转,其有两种情况下可能被选中,一为1-ε的概率下选择当前认为有最大价值的行为时选中,二为随机选择时也恰好选中。
[0026]
进一步地,步骤(3.5)中,更新价值函数、状态和动作,具体如下:
[0027]
q(s,a)=q(s
t
,a
t
)+α[r+γq(s
t+1
,a
t+1
)-q(s
t
,a
t
)]
[0028]
s=s
t+1
,a=a
t+1
[0029]
其中r=r
t
,γ是衰减因子,α是迭代步长,α要随着迭代的进行逐渐变小,保证价值函数可以收敛。
[0030]
进一步地,得到满足优化目标的规划路径后,根据强化学习q表中的各轴动作变化情况,统计分析得到各轴的关节反向次数,将各轴的关节反向次数求和后得到规划后路径的定位评价指标。
[0031]
本发明的有益效果:本发明通过减少工业机器人运料路径中关节反向情况的出现,即减少关节正反转次数,从而有效降低因此产生的减速器回差所造成的绝对定位误差,在不需改变相关硬件结构和精度的情况下,提高板料放置定位环节的绝对定位精度,减少人力物力的浪费,提高压纹板生产效率。
附图说明
[0032]
为了更清楚地说明本发明实施例或现有技术中的技术方案,下面将对实施例或现有技术描述中所需要使用的附图做简单地介绍,显而易见地,下面描述中的附图仅仅是本发明的一些实施例,对于本领域普通技术人员来讲,在不付出创造性劳动前提下,还可以根据这些附图获得其他附图。
[0033]
图1为本发明提供的一种减少工业机器人关节反向的板料定位方法流程图。
具体实施方式
[0034]
以下结合附图对本发明具体实施方式作进一步详细说明。
[0035]
如图1所示,本发明应用领域为门板压纹产线,对在改变偏花工艺时,在不需人工手动操作的情况下提高工业机器人在放置板料时的绝对定位精度。本发明提供的一种减少工业机器人关节反向的板料定位方法,包括以下步骤:
[0036]
步骤1:建立工业机器人的d-h模型。
[0037]
(1.1)根据d-h建模过程的连杆坐标系约定,建立工业机器人各个轴的连杆坐标系;
[0038]
(1.2)用关节角、杆件长度、扭转角和横距这4个参数来描述工业机器人杆件运动,创建d-h参数表,用于后续的路径分析规划;
[0039]
(1.3)由d-h参数表计算得到末端操作点坐标系到机器人基坐标系下的齐次变换矩阵,得到工业机器人的d-h模型。
[0040]
步骤2:改变偏花工艺时,根据新的偏移距离,在工业机器人工作空间内调整其末端操作点终点,记为o
x
,其余点可沿用改变偏花工艺前的点,记起点为o1,和若干中间点中第i个点为oi,其中i∈(1,x),共x个点。
[0041]
步骤3:使用选取的点在关节空间内进行路径的分析规划,得到当前的运动路径,
同时需进行验证。
[0042]
(3.1)记关节角为θi,首先基于d-h参数表得到各轴的初始关节转角信息θ
i1
,再利用反向运动学求解θ
i2
,同理如有多个目标点,则会形成一个策略集合,形似[θ
i1
,θ
i2
,θ
i3
,θ
i4
,θ
i5
…
];
[0043]
(3.2)利用对工业机器人各轴的关节角度变化进行曲线拟合,可得到路径中各轴的关节角度变化与时间的关系,即角度变化函数曲线,可作为坐标系的映射。该步骤可能会出现非唯一解的情况,任选一种验证即可,不影响后续路径的更新优化;
[0044]
(3.3)利用正向运动学进行验证,将各轴的关节角状态转换为末端操作点的状态,即可规划出工业机器人末端操作点的路径,验证是否均经过最初所选取的x个点。因为步骤(3.1)和(3.2)中的解是根据末端操作点的轨迹计算得出,若是表示计算均正确,若不是则表示计算有错误,需重新计算再验证。
[0045]
步骤4:因工业机器人运料过程中出现的关节反向情况会引起减速器回差,从而产生绝对定位误差,影响板料的绝对定位精度,所以考虑将各轴的关节反向次数作为定位评价指标,设ni=ai+bi+ci+di+ei+fi,其中ai,bi,ci,di,ei,fi分别表示工业机器人六个轴的关节角度变化出现关节反向的次数,min{ni}代表完成优化的方案。
[0046]
步骤5:利用sarsa强化学习算法,以工业机器人运送板料过程中减少各轴的关节反向次数,即各轴运动所需的最少关节反向次数到达目标点为优化目标,进行新的路径规划。sarsa算法是一种属于value-based类别的强化学习算法,其通过计算并选取最大价值函数对应的动作,更新价值函数获得优化策略。
[0047]
(5.1)sarsa算法采取q表作为动作策略的选取参照,因此需初始化q表,该表以状态为行,以动作为列,其中状态为工业机器人末端操作点位姿,动作为各轴的关节正转和关节反转的转动角度,q表中的q值表示特定状态下的动作价值;
[0048]
(5.2)在某时刻t,初始化状态s
t
,s
t
为工业机器人末端操作点的起点位姿,再根据ε-贪婪策略从当前状态s
t
的所有可能的关节正转ω和关节反转-ω动作中选择一个动作a
t
,ω为当前工业机器人各轴可实现的最小转动角度。
[0049]
ε-贪婪策略:其中q(s,a)为价值函数;ε为较小值,一般设为0.1,表示探索率,有1-ε的概率从各轴的关节正转和反转中选择有最大价值的动作行动,有ε的概率随机行动;a为各轴的关节正转和关节反转的动作集;m为各轴关节正转和反转的所有可选动作数,六轴工业机器人每个轴有两种可能的动作,取m为12;表示以ε的概率在各轴正转和反转行为中选中动作a的概率;a
*
为当前有最大价值的动作,即某一轴的关节正转或反转,其有两种情况下可能被选中,一为1-ε的概率下选择当前认为有最大价值的行为时选中,二为随机选择时也恰好选中;
[0050]
(5.3)通过ε-贪婪策略选择的动作a
t
,a
t
为当前时刻某一轴的关节正转ω或反转-ω,在当前状态s
t
下执行动作a
t
,得到状态s
t+1
,s
t+1
为工业机器人末端操作点的下一个位姿,同时还有瞬时回报r
t
,r
t
由两部分组成,r
t
=r
t-p
t
,r
t
为单次轴关节转动的奖励,而p
t
为轴出现关节反向情况或当轴的转动角度超过限制时的惩罚;
[0051]
(5.4)在当前状态s
t+1
的各轴关节所有可能的关节正转ω和关节反转-ω动作中按
ε-贪婪策略选择一个动作a
t+1
;
[0052]
(5.5)根据新的q值q(s
t+1
,a
t+1
),更新价值函数以及状态和动作,学习并寻找得到最大回报的各轴关节正转和反转的策略。如当前状态非最终状态,则重复执行(5.3)至(5.5)这三步,其本质就是期望板料运送定位过程中获得最大的累计回报t为总运料时长。
[0053]
更新价值函数:q(s,a)=q(s
t
,a
t
)+α[r+γq(s
t+1
,a
t+1
)-q(s
t
,a
t
)],其中r=r
t
,γ是衰减因子,α是迭代步长,α要随着迭代的进行逐渐变小,这样才能保证价值函数可以收敛。
[0054]
更新状态和动作:s=s
t+1
,a=a
t+1
;
[0055]
(5.6)直到s为最终状态,最终状态为工业机器人末端操作点的终点位姿,此时q(s,a)收敛,迭代执行完毕,当q(s,a)收敛时,ε-贪婪策略同时也收敛,得到最优策略,分析得到更新后的运动路径。
[0056]
步骤6:根据得到的更新后的路径,结合步骤4中提出的定位评价指标计算可得更新后的评价指标,并与初始评价指标对比,从而得到优化方案。
[0057]
(6.1)分析步骤3中初始条件下各轴的关节角度随时间变化的函数曲线,当曲线斜率为0时,表示出现关节反向的情况,即切线斜率为0的坐标点数量就是各轴的关节反向次数,带入步骤4中设定的定位评价指标公式计算可得初始路径的定位评价指标n1。
[0058]
n1=a1+b1+c1+d1+e1+f1[0059]
其中,a1,b1,c1,d1,e1,f1,分别为初始路径中各轴的关节反向次数;
[0060]
(6.2)根据步骤5强化学习过程q表中的各轴动作变化情况,统计分析各轴在运料过程中的关节反向次数,带入步骤4中设定的定位评价指标公式计算得到更新后路径的定位评价指标n2;
[0061]
(6.3)对n1和n2进行比较,如n1>n2,则min{n}=n2表示板料定位优化完成;而如n1=n2,则min{n}=n2=n1表示初始路径在该方法下的板料定位已无需优化。
[0062]
n2=a2+b2+c2+d2+e2+f2[0063]
其中,a2,b2,c2,d2,e2,f2,分别为更新后路径中各轴的关节反向次数。
[0064]
传统的板料定位在偏花工艺改变后,无论采取人工还是工业机器人上料的方法,均需多次的人工介入调整,而采用本发明方法可以在不需改变相关硬件结构和精度的情况下,减小减速器回差带来的绝对定位误差,从而提高工业机器人的绝对定位精度,降低板料放置到压纹台时的定位误差,做到避免后续多次人工干预的同时也提高定位的准确性,推动下一步的压纹以及后续生产环节的顺利进行,提高生产效率。
[0065]
上述实施例用来解释说明本发明,而不是对本发明进行限制,在本发明的精神和权利要求的保护范围内,对本发明作出的任何修改和改变,都落入本发明的保护范围。