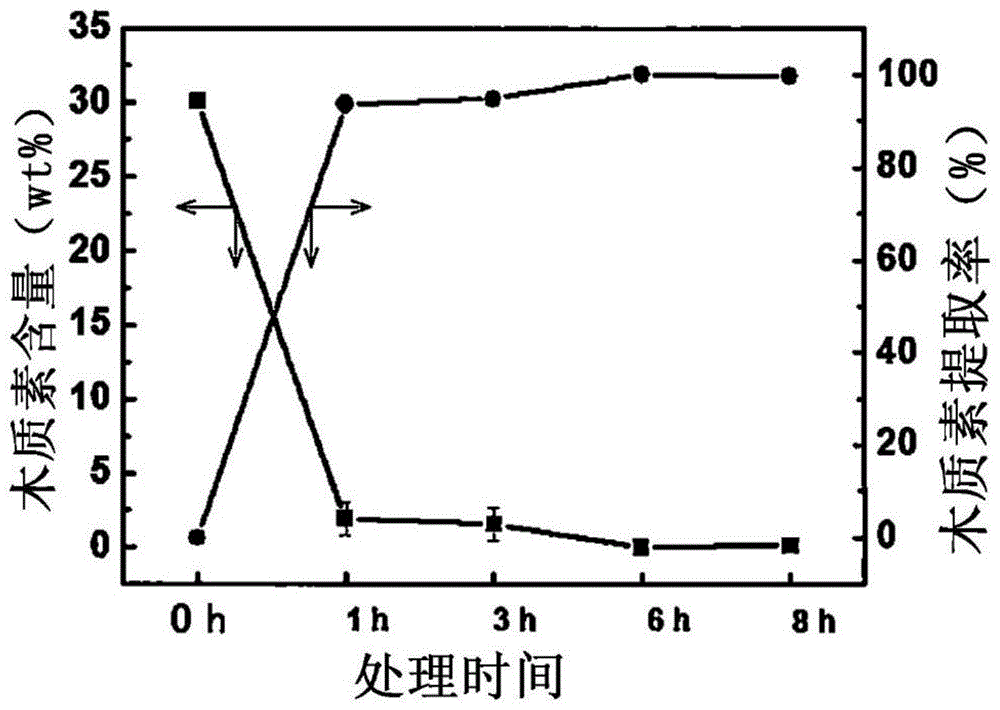
本发明涉及纤维素纳米纤维,更具体来说,涉及以竹为原料获得的纤维素纳米纤维、由其形成的片状材料以及它们的制造方法。本发明还涉及通过该制造方法得到的包含少量木质素的也作为“木质纤维素纳米纤维”已知的纳米纤维。
背景技术:
:近年来,以植物为原料的纤维素纳米纤维在塑料的加强材料、太阳能电池、医疗等广泛的领域中受到关注,特别是对于以其为原料而制造的片状材料的关注也增加。一直以来,作为纤维素纳米纤维的原料,主要使用针叶树纸浆。近年来,除针叶树以外,还以竹为原料进行纤维素纳米纤维的制造。例如,专利文献1中解释了由来源于竹的纤维素纳米纤维得到的拉伸强度和拉伸弹性模量高、导电性良好的复合材料及其制造方法。专利文献2中记载了直径为50nm左右的纤维素纳米纤维及其制造方法,作为纤维素原料,与各种植物原料一起,例举了竹。专利文献3中记载了微细纤维状纤维素的制造方法,作为纤维素原料,与各种植物原料一起,还是例举了竹。纤维素纳米纤维的制造方法有机械解纤方法和化学解纤方法。如以针叶树或竹为原料通过机械解纤方法制造纤维素纳米纤维,则结晶度容易偏低。以竹为原料的工艺制品由例如中越纸浆工业株式会社提供,其制造通过机械解纤方法进行。目前已知的纤维素纳米纤维的纯度最大为87%左右,纤维素结晶度最大为66%左右,纵横比最大为100左右。为了获得更高性能的片状材料,需要提高纤维素纳米纤维的特性。现有技术文献专利文献专利文献1:日本专利特开2017-115069号公报专利文献2:日本专利特许第5910504号公报专利文献3:日本专利特开2012-012713号公报技术实现要素:发明所要解决的技术问题本发明鉴于上述的现状,以能够提供更高性能的片状材料的纤维素纳米纤维及其制造方法、由该纤维素纳米纤维得到的片状材料的提供为目的。此外,本发明的目的还在于通过所述制造方法得到的包含少量木质素的也作为“木质纤维素纳米纤维”已知的纳米纤维。解决技术问题所采用的技术方案发明人在对以竹材代替针叶树纸浆为原料的纤维素纳米纤维进行研究的过程中,探明通过同时实施较温和的机械解纤方法(使用混合机)和多步的化学解纤方法,可获得纤维素纯度为90%以上、纤维直径为10~20nm左右且结晶度为70%以上的纤维素纳米纤维,从而完成了本发明。具体来说,基于本发明的来源于竹的纤维素纳米纤维的特征在于,纤维素纯度为90%以上,纤维直径为10~20nm,且结晶度为70%以上。基于本发明的来源于竹的纤维素纳米纤维可通过以包括下述的工序(1)~(5)为特征的制造方法获得:(1)对竹材实施碱处理和机械处理而制成竹纤维的工序;(2)对所得的竹纤维进行脱木质素处理的工序;(3)对经脱木质素处理的竹纤维以机械方式进行解纤的工序;(4)从经解纤的竹纤维中除去半纤维素的工序;(5)从除去半纤维素后的竹纤维中除去金属成分的工序。由基于本发明的来源于竹的纤维素纳米纤维形成的片状材料的特征在于,相对于基重10~210g/cm2,显示7~200n的拉伸强度。其特征还在于,相对于密度0.3~1.1g/cm3,显示7~200n的拉伸强度。由基于本发明的来源于竹的纤维素纳米纤维形成的片状材料可通过对基于本发明的来源于竹的纤维素纳米纤维进行片状化的制造方法获得。片状化可通过从纤维素纳米纤维的悬浮液中除去分散介质的方法进行。作为分散介质的除去方法的例子,可例举自然干燥、热压处理或冷冻干燥。作为分散介质,可使用水、有机溶剂,作为有机溶剂的例子,可例举醇。热压处理的情况下,可优选通过(a)制备使来源于竹的纤维素纳米纤维分散于水中而得的悬浮液,(b)从悬浮液中除去水并回收残留物,(c)对回收的残留物实施热压处理而获得片状材料,从而对纤维素纳米纤维进行片状化。可从所述(a)悬浮液回收纤维素纳米纤维,对使回收的纤维素纳米纤维分散于醇中而得的另一悬浮液实施热压处理而获得片状材料。冷冻干燥的情况下,可优选通过(a)制备使纤维素纳米纤维分散于醇中而得的悬浮液,(b)将悬浮液展开于基材上而形成膜状,(c)对膜状的悬浮液实施冷冻干燥处理而获得片状材料,从而对纤维素纳米纤维进行片状化。此外,基于本发明的来源于竹的木质纤维素纳米纤维的木质素含量为1~2wt%左右,通过在得到规定的木质素含量时停止上述的来源于竹的纤维素纳米纤维的制造方法的工序(2)的脱木质素处理来获得。发明的效果如果采用本发明,则可提高来源于竹的纤维素纳米纤维的性能,能够利用以其为原料的高强度的片状材料。由此,可期待它们在新用途中的应用。此外,基于本发明的来源于竹的木质纤维素纳米纤维可期待用作与利用通过与树脂混合而进一步减少了木质素含量的高纯度的纤维素纳米纤维的复合材料相比更有用的复合材料(例如汽车用或家电用的复合材料)。附图说明图1是表示相对于用过乙酸的处理时间的竹纤维的木质素含量和提取率的图表。图2是相对于处理时间表示过乙酸处理后的竹纤维的半纤维素含量和提取率的图表。图3是表示koh水溶液浓度与竹纤维的半纤维素含量和提取率的关系的图表。图4是表示koh水溶液量与竹纤维的半纤维素含量和提取率的关系的图表。图5是表示半纤维素除去的处理温度与半纤维素含量和提取率的关系的图表。图6是表示脱木质素处理前的竹纤维的fe-sem观察结果的图,(a)为fe-sem图像,(b)为表示纤维分布的图表。图7是表示脱木质素处理1小时后的竹纤维的fe-sem观察结果的图,(a)为fe-sem图像,(b)为表示纤维分布的图表。图8是表示脱木质素处理3小时后的竹纤维的fe-sem观察结果的图,(a)为fe-sem图像,(b)为表示纤维分布的图表。图9是表示脱木质素处理6小时后的竹纤维的fe-sem观察结果的图,(a)为fe-sem图像,(b)为表示纤维分布的图表。图10是表示脱木质素处理8小时后的竹纤维的fe-sem观察结果的图,(a)为fe-sem图像,(b)为表示纤维分布的图表。图11是表示半纤维素除去后的竹纤维的fe-sem观察结果的图,(a)为fe-sem图像,(b)为表示纤维分布的图表。图12是基于本发明的纤维素纳米纤维片的ft-ir图谱。图13是表示以水为分散介质通过热压制成的纤维素纳米纤维片的电子显微镜观察结果的图,(a)为tem图像,(b)将fe-sem图像与片的外观照片一并示出。图14是表示以乙醇为分散介质通过热压制成的纤维素纳米纤维片的电子显微镜观察结果的图,(a)为tem图像,(b)将fe-sem图像与片的外观照片一并示出。图15是表示通过冷冻干燥制成的纤维素纳米纤维片的电子显微镜观察结果的图,(a)为tem图像,(b)将fe-sem图像与片的外观照片一并示出。图16是基于本发明的纤维素纳米纤维片的样品的xrd图案。图17是基于本发明的纤维素纳米纤维片的另一样品的xrd图案。图18是基于本发明的纤维素纳米纤维片的又另一样品的xrd图案。图19是基于本发明的纤维素纳米纤维片的气体吸附等温线。图20是表示以水为分散介质通过热压制成的基于本发明的纤维素纳米纤维片的细孔径分布的图表。图21是表示以乙醇为分散介质通过热压制成的基于本发明的纤维素纳米纤维片的细孔径分布的图表。图22是表示通过冷冻干燥制成的基于本发明的纤维素纳米纤维片的细孔径分布的图表。图23是将以水为分散介质通过热压制成的基于本发明的纤维素纳米纤维片的相对于质量的拉伸强度与比较片的相应值一并示出的图表。图24是将以水为分散介质通过热压制成的基于本发明的纤维素纳米纤维片的相对于厚度的拉伸强度与比较片的相应值一并示出的图表。图25是将以水为分散介质通过热压制成的基于本发明的纤维素纳米纤维片的相对于密度的拉伸强度与比较片的相应值一并示出的图表。图26是将以水为分散介质通过热压制成的基于本发明的纤维素纳米纤维片的相对于基重的拉伸强度与比较片的相应值一并示出的图表。图27是对基于本发明的纤维素纳米纤维片中的纤维进行说明的图,(a)为fe-sem图像,(b)为表示纤维分布的图表。图28是对通过celish(商标)制成的片中的纤维进行说明的图,(a)为fe-sem图像,(b)为表示纤维分布的图表。具体实施方式为了获得由来源于竹的纤维素纳米纤维形成的片状材料,需要制造作为其原料的来源于竹的纤维素纳米纤维。根据本发明,通过利用较温和的机械解纤方法(使用混合机)与多步的化学解纤方法的组合,可制造显示出与以往相比更好的特性的纤维素纳米纤维。具体来说,基于本发明的来源于竹的纤维素纳米纤维的制造方法包括下述的工序(1)~(5):(1)对竹材实施碱处理和机械处理而制成竹纤维的工序;(2)对所得的竹纤维进行脱木质素处理的工序;(3)对经脱木质素处理的竹纤维以机械方式进行解纤的工序;(4)从经解纤的竹纤维中除去半纤维素的工序;(5)从除去半纤维素后的竹纤维中除去金属成分的工序。竹纤维制备工序(1)中,利用碱处理和机械处理,由竹材制备竹纤维。作为本发明中使用的竹材,无特别限定,可使用例如孟宗竹、桂竹、紫竹、日本矢竹等所谓的包含竹纤维的植物。为了使碱处理的效果和所得的纤维的纯度提高,竹材较好是预先除去其内外皮。为了使所制造的纤维的直径均一,更好是以仅留下使用的竹材的纤维束均一的部分的方式进行内外皮除去。竹材还较好是在其后的采用碱水溶液的处理之前,例如预先通过带有周速差的夹送辊进行加压辊压(压榨处理)而将其疏解。由此,可加大碱水溶液的渗透速度,且使渗透均匀,提高其后的基于碱处理的木质素和半纤维素的分离除去效率。为了实现该目的,除此之外,还可应用例如采用油压机的处理或采用辊轧机的处理。另外,使用碱水溶液的处理时,如果竹材干燥,则处理效果差,因此较好是到处理开始为止,竹材在液体中保存而使其不会干燥,或者冷冻或冷藏保存。更好是为了抑制杂菌的繁殖,浸渍于对其有效的液体、例如过氧化氢、高氯酸、硫酸等的水溶液,冷藏保存。从安全性和废弃物的角度来看,最好是使用过氧化氢。实施碱处理的竹材根据处理容器的容量适当截断使用。为了提高处理效率,本发明中,较好是使用截断为例如长度1~10cm左右而片材化的竹材。碱处理可将竹片浸于例如氢氧化钠、碳酸氢钠、氢氧化钾等碱水溶液来进行。使用氢氧化钠水溶液的情况下,从效率的观点来看,水溶液的浓度较好是0.01~1.00m,更好是0.10~1.00m,进一步更好是0.10~0.50m。处理温度较好是30~200℃,更好是50~150℃,进一步更好是100~150℃。处理压力较好是101~500kpa,更好是101~200kpa。处理时间较好是1~3小时,更好是3小时。将经碱处理的竹片从碱水溶液中取出并水洗。水洗持续至清洗后的水达到中性为止。接着,为了获得竹纤维,以机械方式对竹片进行处理。该处理可使用通常的混合机,将竹片与室温的水一起搅拌来进行。只要可将竹片分解而形成纤维状,使用的混合机的种类无特别限定。此外,处理条件按照可获得规定的处理效果的条件适当设定即可。处理后,干燥而获得竹纤维。脱木质素处理工序(2)可使工序(1)中得到的竹纤维与脱木质素处理液接触来进行。作为脱木质素处理液,可使用过乙酸、亚氯酸、亚硫酸钠、硫酸、臭氧、酶、微生物(细菌)等的溶液。使竹纤维分散于脱木质素处理液中并静置后,从处理液分离,再清洗干燥,从而可获得经脱木质素处理的竹纤维。脱木质素处理液可在例如室温~220℃左右、较好是60~100℃左右的温度下进行。静置时间较好是1~8小时,更好是1~6小时,进一步更好是3~6小时。随着处理时间的加长,木质素提取率增大。例如,使用过乙酸(乙酸:过氧化氢体积比=1:1),将静置温度设为80℃的情况下,通过6小时的处理,提取率达到100%,获得白色的纤维。该情况下,半纤维素几乎未被提取。处理时间越长,则竹纤维的直径越细,通过6小时的处理,获得平均直径约16nm的纤维。木质素含量为1~2wt%左右的本发明的来源于竹的木质纤维素纳米纤维可通过在得到规定的木质素含量时停止该脱木质素处理工序(2)的脱木质素处理液中的竹纤维静置来获得。此处的静置在如上所述用过乙酸于80℃静置的情况下可为例如0.5~2小时左右或者0.5~1.5小时左右。除了工序(2)中的静置时间这点之外,本发明的来源于竹的木质纤维素纳米纤维可通过与本发明的来源于竹的纤维素纳米纤维的制造同样的方法制造。例如使用过乙酸作为处理液的情况下,如下所示发生木质素的芳香环的断开,可认为木质素被从竹纤维除去(参照畠山兵卫,纸浆技术协会志,第20卷,第11号,第15页(1966))。[化1]经脱木质素处理的竹纤维的机械解纤工序(3)可通过将竹纤维与水一起用混合机搅拌来进行。只要采用搅拌的解纤不被妨碍,混合机的种类无特别限定。从处理效率的观点来看,水的量较好是竹纤维的质量的10~1000倍左右,更好是100~500倍左右,进一步更好是100~150倍左右。此外,搅拌处理较好是在5~60℃左右的温度下进行,更好的温度是5~40℃左右。混合机的运行条件按照可获得规定的解纤效果的条件适当设定即可。从经解纤的竹纤维中除去半纤维素的工序(4)可通过对经解纤的竹纤维进行碱处理来进行。碱处理可通过使经解纤的竹纤维浸渍于碱水溶液中来进行。作为碱水溶液,可使用氢氧化钾的水溶液,除此之外,还可使用氢氧化钠水溶液等。使用氢氧化钾水溶液的情况下,从处理效率的观点来看,相对于5g纤维,可使用50~500ml左右、较好是200~500ml左右的0.5~5.0m左右、较好是1.0~2.0m左右的koh水溶液。浸渍可在20~100℃左右进行。浸渍时间较好是1~24小时,更好是1~12小时,进一步更好是1~8小时。从除去半纤维素后的竹纤维中除去金属成分的工序(5)可对除去了半纤维素的竹纤维实施酸处理来进行。酸处理可通过使竹纤维接触酸溶液并振荡规定时间来进行。作为酸溶液,可使用盐酸、高氯酸、硫酸、硝酸等的水溶液。例如使用盐酸水溶液的情况下,溶液的浓度较好是0.001~1.0m左右,更好是0.01~1.0m,进一步更好是0.01~0.1m。接触时间较好是1~24小时,更好是3~24小时,进一步更好是1~12小时。该处理可在室温(20~30℃左右)进行。竹纤维的木质素量可通过例如硫酸法(日本木材学会,木质科学实验手册,第96-97页,文英堂出版(2010))进行测定(参照后述的实施例)。竹纤维的半纤维素量可基于除去半纤维素前后的竹纤维的质量来进行测定(参照后述的实施例)。通过本发明的方法制造的来源于竹的纤维素纳米纤维的特征是显示90%以上的纤维素纯度,纤维直径为10~20nm,且结晶度为70%以上。本发明的纤维素纳米纤维的纤维素纯度和结晶度与以往的纤维素纳米纤维的纤维素纯度(最大87%左右)和结晶度(最大66%左右)相比高出许多。通过对基于本发明的来源于竹的纤维素纳米纤维进行片状化,可获得基于本发明的片状材料。片状化例如可采用热压或冷冻干燥来进行。还可采用自然干燥。采用热压的片状化可优选使用对向水中加入除去金属成分后的纤维素纳米纤维的被处理液进行搅拌而得的悬浮液来进行。将从悬浮液中除去作为分散介质的水而回收的残留物不经干燥通过热压机进行处理而片状化,可获得由基于本发明的纤维素纳米纤维形成的片状材料。可使用使从悬浮液除去了水的残留物再次分散于乙醇等醇的分散介质而得的悬浮液。分散介质为水的情况下,所得的片状材料中可见纤维的凝集,而分散介质为醇的情况下,醇使纤维素分子间形成溶剂合物,从而可见纤维的离解。采用冷冻干燥的片状化可优选使用以有机溶剂(例如醇)为分散介质的悬浮液进行。将悬浮液展开于规定的基材上而形成膜状后,冷冻,实施冷冻干燥处理,可获得由基于本发明的纤维素纳米纤维形成的片状材料。分散介质为醇的情况下,可使用乙醇或丁醇等。作为除醇以外的有机溶剂,可使用酮类(例如丙酮)、芳香族化合物(例如甲苯)、羧酸(例如乙酸)、胺类(例如n,n-二甲基甲酰胺)、乙腈等。分散介质(醇等)通过冷冻干燥而升华,从而纤维的凝集得到抑制。分散介质可仅使用1种(例如乙醇),也可使用多种的混合物,或者还可以依次使用多种(例如从乙醇的悬浮液一度回收纤维素后,从使其再次分散于丁醇而得的悬浮液制作片状材料)。后者的情况下,在抑制纤维素纳米纤维的凝集方面有利。不论是何种片状化手段,用于获得悬浮液的搅拌均可利用通常的混合机或超声波来进行。悬浮液中的纤维素纳米纤维的含量通常可为0.1~10wt%,较好是0.1~2.0wt%,更好是0.1~1.0wt%。只要可获得纤维素纳米纤维充分分散的悬浮液,搅拌条件无特别限定。分散介质的水或醇的除去可采用过滤等任意的处理。采用自然干燥的情况下,将分散来源于竹的纤维素纳米纤维并展开于基材上形成膜状的悬浮液静置,除去分散介质来进行。分散介质可以是水或者有机溶剂、例如醇等。根据情况,也可通过通风等促进分散介质的除去。从基于本发明的来源于竹的纤维素纳米纤维制作的片状材料与以往的从纤维素纳米纤维制作的片状材料相比,在相同的条件下测定时显示更高的强度。例如,比较相对于200g/m2基重(每1m2片状材料的质量)的拉伸强度的情况下,基于本发明的片状材料的拉伸强度为约200n,而从由大赛璐精细化工株式会社获得的纤维素纤维fd100g制作的片状材料和由蒙迪集团获得的市售纸(iso9707认证纸)的拉伸强度分别为约100n和145n。这样显示高拉伸强度的由基于本发明的来源于竹的纤维素纳米纤维形成的片状材料可期待增强、音响、医疗、食品、包装材料、运输等领域中的应用。[实施例]以下,通过实施例对本发明进行进一步说明。当然,本发明并不仅限于以下的实施例。1.纳米尺寸竹纤维的制作除去内皮和外皮并进行压榨处理,将120g片材化至长约10cm的竹片加入电压力锅(松下株式会社,sr-p37-n),浸于2l的0.10m的氢氧化钠水溶液,以120℃、200kpa的条件处理3小时。将经处理的竹片放冷后,移至金属制的篓筐,用超纯水清洗至清洗后的水达到中性为止,获得竹纤维。将60g得到的纤维放入混合机(vitamix(商标)abs-bu),加入1l超纯水,以37000rpm搅拌1分钟。然后,弃去超纯水并干燥,获得竹纤维。2.脱木质素处理向300ml的玻璃制三角烧瓶中,加入17.5m乙酸溶液,用分液漏斗向其中慢慢滴加11.6m过氧化氢水溶液,制成100ml过乙酸溶液。其中,乙酸与过氧化氢的体积比为1:1。用玻棒搅拌的同时将10g由上述1得到的竹纤维向放有100ml过乙酸溶液的容器中分别加入约1g后,将水浴(东京理化器械株式会社,sb-350)的温度设定为80℃,将容器设置于低温恒温水槽(东京理化器械株式会社,ncb-1200),回流下静置1、3、6或8小时。然后,放冷,用塑料制的过滤器(艾凡特公司(advantec),kp-47h和kp-47s)进行抽滤。将残留物用超纯水清洗至中性为止,用保持于60℃的干燥机干燥12小时,得到经脱木质素处理的竹纤维。通过过乙酸中的1小时的处理,纤维从褐色变为黄色,处理3小时后变为黄白色。进而通过处理6小时而获得白色的竹纤维。这被认为缘于随着过乙酸处理时间的推移,作为着色成分的木质素被逐步除去。6小时以上的处理下未见变化。3.解纤相对于超纯水将经脱木质素处理的竹纤维以其浓度达到0.7wt%的条件加入,用混合机(vitamix(商标)abs-bu)以37000rpm搅拌5分钟。然后,放冷,间歇地搅拌合计60分钟,获得经解纤的竹纤维的悬浮液。4.木质素的定量向100ml的玻璃制烧杯中,加入15ml的13.4m硫酸和1g由上述2得到的生成物(经脱木质素处理的竹纤维),用玻棒搅拌至硫酸均匀地浸含于纤维为止。静置4小时后,回流下煮沸4小时并放冷。然后,通过使用玻璃过滤器(柴田科学株式会社,1gp16)的抽滤回收残渣,将其用500ml的热水清洗后,用保持于105℃的干燥机干燥12小时。干燥后,称量收量至小数点后第4位,用下述的式(1)求出木质素的含量(参照日本木材学会,木质科学实验手册,第97页,文英堂出版(2010))。木质素含量(wt%)=(实验后质量/实验前质量)×100(1)相对于用过乙酸的处理时间的木质素含量和提取率示于表1,其图表示于图1。过乙酸处理的时间越长,提取率越高,木质素经6小时被全部提取。[表1]表1要获得作为所谓的“木质纤维素纳米纤维”已知的含少量的残留木质素的纳米纤维的情况下,对于处理约1小时后得到的竹纤维(含1wt%左右的残留木质素),可按照以下说明的步骤继续进行处理。5.半纤维素的定量根据参考文献,β-纤维素和γ-纤维素以及半纤维素被分类为半纤维素,除此以外被分类为α-纤维素(参照日本木材学会,木质科学实验手册,第95页,文英堂出版(2010))。本发明中,首先按照该分类,使用α-纤维素的定量方法,对半纤维素进行了测定(参照日本木材学会,木质科学实验手册,第96-97页,文英堂出版(2010))。因此,此处的半纤维素也包括β-纤维素和γ-纤维素。向200ml的塑料制烧杯中,加入25ml的5.80m氢氧化钠水溶液和1g由上述2得到的生成物(经脱木质素处理的竹纤维)。将纤维均匀地浸含于液中后,静置4分钟,然后用塑料制的搅棒搅拌5分钟后,静置30分钟。向烧杯中再加入超纯水,搅拌1分钟,静置5分钟。然后,使用玻璃过滤器(柴田科学株式会社,1gp250)进行抽滤,回收滤液并再过滤后,用超纯水清洗残留物至滤液达到中性为止。将残留物和40ml的1.75m乙酸水溶液加入100ml的玻璃制烧杯中并静置5分钟后,通过抽滤回收残留物,用1l的超纯水清洗。然后,将残留物用保持于105℃的干燥机干燥12小时,称量收量至小数点后第4位,用下述的式(2)求出半纤维素含量(参照日本木材学会,木质科学实验手册,第96页,文英堂出版(2010))。半纤维素定量(wt%)=((实验前质量-(α-纤维素质量))/实验前质量)×100(2)过乙酸处理后的竹纤维的半纤维素的含量和提取率示于表2,其图表示于图2。过乙酸处理中,半纤维素含量未大幅减少。此外,也未见基于处理时间的较大差异。[表2]表26.半纤维素的除去和定量将5g实施了采用过乙酸的6小时的脱木质素处理和解纤处理的竹纤维加入200ml的玻璃制三角烧瓶,加入200ml的0.71或1.18m的氢氧化钾水溶液,使纤维均匀地浸含于液中。加塞在室温下静置12小时后,用塑料制的过滤器(艾凡特公司,kp-47h和kp-47s)进行抽滤,用超纯水清洗残留物至清洗液达到中性为止。然后,将残留物用保持于60℃的干燥机干燥12小时,使用与上述5同样的步骤和算式测定半纤维素的含量。结果示于表3,同时处理液浓度与半纤维素的含量和提取率的关系示于图3。可知1.18m的情况下,包含7%左右的半纤维素。另外,α-纤维素含量为93%左右。[表3]表3于是,为了探明氢氧化钾处理时的体积与提取率的关系,将koh水溶液的浓度固定为1.18m,将溶液的量改变为100或200ml的情况下的定量结果示于表4,同时溶液量与半纤维素的含量和提取率的关系示于图4。由这些结果可知,该例子中,相对于5g竹纤维使用200ml的1.18m的koh水溶液时提取到最多的半纤维素。[表4]表4接着,考察处理温度与半纤维素的含量和提取率的关系,其定量结果示于表5和图5。将koh水溶液浓度设为1.18m、相对于5g的竹纤维的溶液量设为200ml的情况下,与100℃相比,室温下处理时提取到更多的半纤维素。其中,处理温度100℃的情况下,向特氟龙(注册商标)容器中加入竹纤维和koh水溶液,再将该容器加入耐热不锈钢容器并密封。干燥机的温度设定为100℃,静置12小时。放冷后,如上所述进行了抽滤、水洗、干燥。[表5]表57.β-纤维素的定量以最适条件实施了处理的生成物中的α-纤维素含量为93%左右。为了探明该生成物中的准确的β-纤维素量,将生成物加入10ml的30%乙酸水溶液中,加入200ml上述5中得到的清洗液,加热至80℃,保温放置9小时。将所得的沉淀物用预先称重的滤纸回收,将干燥后的质量增加部分作为β-纤维素含量(参照日本木材学会,木质科学实验手册,第96页,文英堂出版(2010))。[表6]表6由表6的从上往下数第3行和第4行中记载的结果可知,通过上述5中记载的方法测定的半纤维素的97%为β-纤维素。与α-纤维素含量合计,确认纤维素含有率为99.8%。8.基于场发射型扫描电子显微镜的形态观察向1滴上述1中得到的竹纤维(脱木质素前的竹纤维)的悬浮液中加入1ml乙醇,超声波分散。向玻璃碳上滴加10μl超声波分散后的悬浮液,用保持于60℃的干燥机干燥。然后,用蒸镀装置(日本电子株式会社,jfc-1600)在经干燥的竹纤维上蒸镀铂,通过场发射型扫描电子显微镜(fe-sem(日本电子株式会社,jsm-6701f))观察了竹纤维的形态。蒸镀条件示于表7,测定条件示于表8。此外,对于实施了1、3、6、8小时的上述2中说明的脱木质素处理的竹纤维,进行了同样的观察。各观察结果分别示于图6(a)~10(a)(fe-sem图像)和图6(b)~10(b)(纤维分布图)。[表7]表7溅射电流20ma蒸镀时间15s蒸镀次数2[表8]表8加速电压3kv运作距离3mm照射电流7μa发射电流10μa用fe-sem以高倍数观察后,发现脱木质素处理前的竹纤维的光学显微镜观察中确认的直径16μm左右的短纤维(未图示)为具有宽范围的直径的纤维纠缠成束(图6(a)和(b))。存在随着脱木质素处理时间的加长,纤维直径微量减小的倾向。其中,fe-sem图像中所见的粒状物质为蒸镀的铂。此外,纤维直径在8小时后平均为15.9nm。一般来说,木材等所含的纤维素纳米纤维的直径被认为是数nm,所以与之相比直径稍稍变粗。作为其理由,可例举采用fe-sem的观察中需要使观察材料绝对干燥,由于该干燥时纤维素分子间的氢键而缔合的可能性。接着,对于除去木质素的同时还除去了半纤维素的竹纤维(上述6中用1.18m氢氧化钾水溶液处理的竹纤维),进行采用fe-sem的同样的观察。结果示于图11(a)(fe-sem图像)和图11(b)(纤维分布图)。试着除去了半纤维素的纤维也残存部分束,但平均纤维直径变小,这被认为与半纤维素的提取和所制造的纤维素纳米纤维的直径有关。9.采用傅立叶变换红外分光法的定性分析1、3、6、8小时的过乙酸处理(脱木质素处理)后的竹纤维和8小时的过乙酸处理后进一步进行了半纤维素除去的纤维放入混合机(vitamix(商标)abs-bu),加入超纯水,搅拌60分钟。然后,用塑料制的过滤器(艾凡特公司,kp-47h和kp-47s)进行抽滤,用保持于60℃的干燥机干燥,对于所得的竹纤维片,通过具备漫反射单元的傅立叶变换红外分光装置(ft-ir(赛默飞世尔科技公司,artid5)),在4000~550cm-1的范围内测定了ft-ir光谱。结果示于图12。未确认到过乙酸处理(脱木质素处理)前的原料竹纤维的ft-ir光谱(未图示)中确认的对应于木质素的1760cm-1的co伸缩、1500cm-1的芳香环的c=c伸缩、1250cm-1的甲氧基的co反对称伸缩、840cm-1的芳香环的ch伸缩的峰,确认到了对应于纤维素和半纤维素的3600~3000cm-1的oh伸缩、2920cm-1的ch伸缩的峰。10.金属成分的除去和采用icp发光分光分析的金属的定性及定量分析使由上述2得到的竹纤维(除去了木质素的竹纤维)与盐酸水溶液接触,进行了金属成分的除去。向塑料制的样品管中,加入1g竹纤维和50ml的0.01m的盐酸水溶液。残留竹纤维,从样品管中迅速取出溶液而获得“处理前”的溶液。向样品管中新加入50ml盐酸水溶液并继续振荡24小时后,残留竹纤维,迅速取出溶液而获得“处理后”的溶液。将各溶液加入玻璃制的10ml螺口试验管并用离心分离机(亚速旺株式会社,c-12b)处理而使固体成分沉淀,取出上清溶液。将该上清液用电感耦合等离子体发光分光分析装置(icp-oes(安捷伦科技公司,710icp-oes))进行分析,进行了竹纤维所含的金属的定性和定量。结果示于表9。[表9]表9已知竹中作为无机物主要含有大量氧化硅、钙、钾、镁以及钠。在此分析的基于本发明的竹纤维确认含有钾和锌,但除这些以外接近于0,非常微量。另外,发现通过本发明,可将金属类通过浸渍于盐酸24小时来除去,其含有率相对于所得的纤维素纳米纤维的质量可减少至0.06%左右。11.采用热压的纤维素纳米纤维片的制作将3.5g按照上述2中说明的步骤与过乙酸溶液反应了6小时的竹纤维按照纤维含量达到0.7wt%的条件加入500ml超纯水中,用混合机(vitamix(商标)abs-bu)以37000rpm搅拌5分钟,放冷,间歇地搅拌合计60分钟,获得悬浮液。将所得的悬浮液用玻璃制的过滤器(艾凡特公司,kg-47)进行抽滤后,不经干燥,用小型热压机(亚速旺株式会社,ah-2003)于120℃压制而制成片材。此外,将如上所述得到的悬浮液过滤后,将残留物加入100ml乙醇中,超声波分散后,抽滤。重复该操作2次后,用小型热压机以同样的方法制成片材。12.采用冷冻干燥的纤维素纳米纤维片的制作将上述11中得到的悬浮液过滤后,加入50ml乙醇中,超声波分散后,抽滤。重复该操作2次后,将残留物加入50ml叔丁醇中,超声波分散。该操作也重复2次,过滤后将残留物移至培养皿,用冷冻库(松下株式会社,nr-b175w)冷冻,用冷冻真空干燥装置(日立株式会社,es-2030)干燥,制成片材。干燥条件示于表10。此外,为了比较形态,将水的悬浮液直接用冷冻库冷冻,也制成冷冻干燥的片材。[表10]表10设定温度-10℃干燥结束时的真空度低于0.1torr(13.3pa)13.基于场发射型扫描电子显微镜和透射型电子显微镜的片材的形态观察通过场发射型扫描电子显微镜(fe-sem)观察所得的纤维素纳米纤维片的形态。测定条件示于表11。其中,观察前用蒸镀装置(日本电子株式会社,jfc-1600)将铂蒸镀于片材。蒸镀条件示于表12。[表11]表11加速电压3kv运作距离3mm照射电流7发射电流10μa[表12]表12此外,使制成的片材超声波分散于1-丁醇,滴加于tem用栅极(应研商事株式会社,stem150cu栅极)并在100℃的干燥器内干燥后,用透射型电子显微镜(tem(日本电子株式会社,jem-2100))观察片材的形态。以水为分散介质通过热压制成的纤维素纳米纤维片的tem图像示于图13(a),外观照片和fe-sem图像示于图13(b),以乙醇为分散介质通过热压制成的片材的这些示于图14(a)和14(b)。以水为分散介质的情况下,确认到纤维凝集的状况,这被认为是由于纤维素分子间较强的氢键。若将分散介质改为乙醇,确认到纤维稍微分散的状况,这被认为是由于乙醇进入纤维素分子间,形成溶剂合物而离解。通过冷冻干燥制成的纤维素纳米纤维片的tem图像示于图15(a),外观照片和fe-sem图像示于图15(b)。通过进行冷冻干燥,与通过热压制成的片材(图13(a)、(b)和图14(a)、(b))相比,确认到纤维素未凝集而离解的状况。这被认为是由于通过冷冻干燥,使作为分散介质的叔丁醇从固体状态不经液体而直接升华为气体,从而纤维的凝集得到抑制。14.基于xrd的片材的结晶性的评价用x射线衍射装置(xrd(理学电机株式会社,rint-ultimaiii))对所得的纤维素纳米纤维片的结晶性进行了评价。测定条件示于表13。[表13]表13此外,纤维素的结晶度根据2θ=15°的纤维素的10-1衍射线的自以2θ=10°~80°所作的基线的强度(ia)和自以2θ=10°~20°所作的基线的强度(ib)用式(3)算出。结晶度=(ia/ib)×100(3)由3个样品得到的3个纤维素纳米纤维片的样品的xrd图案示于图16~18。所有的样品中,均在2θ=15°和22.5°确认到纤维素的10-1和002衍射线。此外,根据这些峰强度算出的纤维素的结晶度示于表14。不论是何种分散介质,结晶度均为71~77%。[表14]表14片材制作方法结晶度(%)热压、水分散介质75.0热压、乙醇分散介质71.4冷冻干燥、丁醇分散介质77.515.基于气体吸附测定的表面积的测定用氮气吸附装置(汤浅离子株式会社(yuasaionicsco.,ltd.),autosorb-3)对所得的纤维素纳米纤维片的bet表面积进行了测定。使氮气(纯度99.9%)于77k吸附于样品池内的片材,测定其吸附量和样品池内的压力,从而得到吸附等温线。通过bet法分析所得的吸附等温线,从而算出bet表面积。其中,测定前将试样在200℃抽真空24小时来脱气。所测得的气体吸附等温线示于图19,其bet表面积示于表15。[表15]表15片材制作方法bet表面积(m2/g)热压(hp)、水分散介质3.18热压(hp)、乙醇分散介质22.6冷冻干燥、叔丁醇分散介质36.0以乙醇为分散介质通过热压制成的片材的情况下,纤维发生离解,因此表面积与以水为分散介质的情况相比增大。通过冷冻干燥制成的片材与通过热压制成的片材相比,纤维的凝集得到防止,因此得到了更大的表面积。此外,片材的细孔径分布示于图20(以水为分散介质通过热压制成的片材)、图21(以乙醇为分散介质通过热压制成的片材)和图21(通过冷冻干燥制成的片材)。16.基于拉伸试验的强度测定对以水为分散介质采用热压制成的纤维素纳米纤维片的拉伸强度进行了测定。将制成的片材切成宽1.5cm、长2.5cm的长条状,上下夹住约5mm左右,以1mm/min的拉伸速度用桌面型精密拉伸试验机(株式会社岛津制作所,ags-j)进行了测定。其中,作为比较,对于由大赛璐精细化工株式会社制的食品用纤维素纳米纤维(celish(商标))用热压成形而得的片材和蒙迪集团制的市售纸(iso9707认证纸,低木质素残留量),进行了同样的测定。各样品的相对于质量的最大强度示于图23,相对于厚度的最大强度示于图24,相对于密度的最大强度示于图25,相对于基重(每1m2的质量)的最大强度示于图26。所有的样品均确认随着质量、厚度、密度和基重的增大,强度也增大。此外,进行了试验的3种片材中,基于本发明的来源于竹的纤维素纳米纤维片显示了最大的强度。这被认为是由于基于本发明的来源于竹的纤维素纳米纤维与其他纤维相比,纤维更细,所以单位质量的纤维量多,纤维间的氢键结合的点增加,因而强度增加。例如,如果对由基于本发明的来源于竹的纤维素纳米纤维的片材和以同样作为纤维素纳米纤维的celish(商标)制成的片材得到的fe-sem图像和纤维直径分布(分别为图27(a)和(b)以及图28(a)和(b))进行比较,则可确认前者的纤维更细。当前第1页12