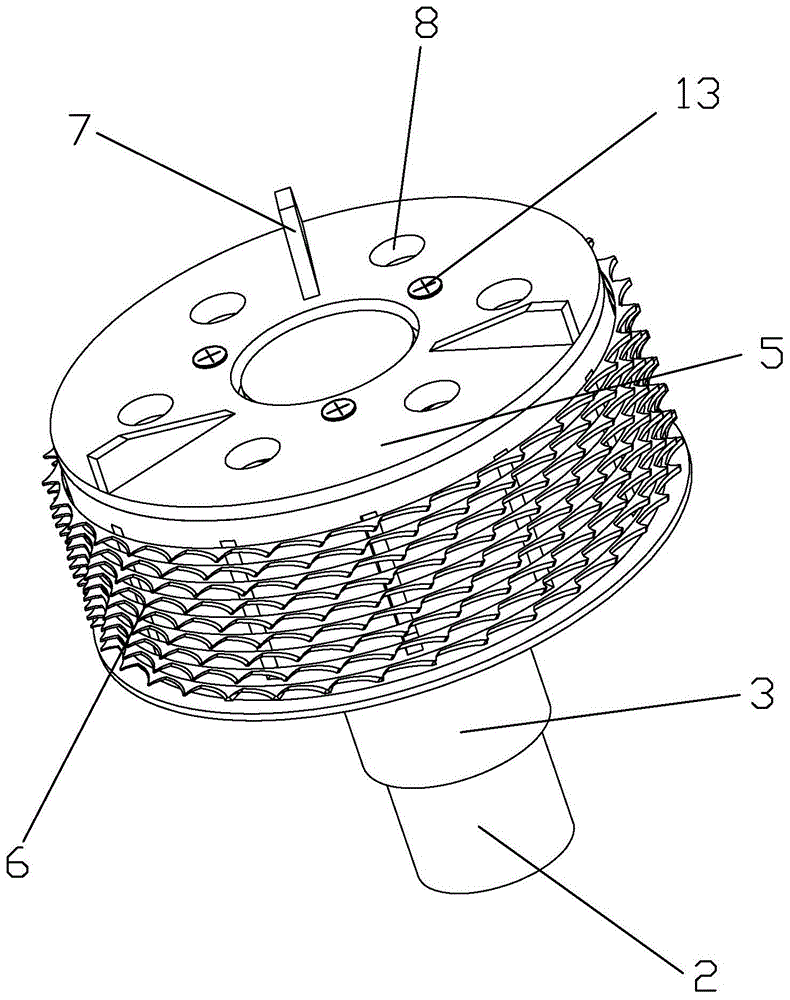
本实用新型涉及纺织领域,特别涉及一种喷毛机分梳辊。
背景技术:
:加捻纱是现今应用最多的纱线,纤维加捻可以提高纱线的强度、延伸性和弹性,提高纱线的可纺性能。但加捻纱往往是短纤维或长丝单独的加捻成纱,为了满足多样化的需求,喷毛纱应运而生,它是短纤维和长丝结合而成的无捻纱,有蓬松轻柔、保暖性好的特点。喷毛纱的结构特点是,用一个网状纱线包住内部松散无序的纤维,使其具有轻而蓬松的效果。喷毛纱有比加捻纱同样支数下体积大,制成的衣服轻的优势,是近几年发展产生的新型纱线。但由于喷毛纱条干不均和掉毛问题,起初未能广泛推广。直到国内推出全新产品,并可以生产毛条和短纤维产品,解决掉毛问题后,喷毛纱才得到了更广泛的应用。喷毛机出毛要稳定和均匀,不然生产出的喷毛纱会有粗细节,影响喷毛纱的质量。现今喷毛机的工作原理是将纤维条梳理成单纤维喷出,梳理用的分梳辊针齿有植针式和齿条式。植针式是将针齿植种在分梳辊辊体表面,梳理时纤维与针齿之间的摩擦系数小,易于纤维从针齿上的脱离,但植针针辊的耐磨性低于齿条辊,由于针齿和分梳辊为一整体,出故障后需要更换整个分梳辊,增加了隐形成本。齿条式分梳辊是将锯齿针布条搭接在分梳辊上,可以循环利用分梳辊辊体,但存在纤维难从分梳辊脱离的现象,不均匀的纤维产出直接造成喷毛纱的粗细节率高,并且长细节也占很大的比例,从而喷毛纱生产切头率高,次品率高,提高了喷毛纱的生产成本,制约了喷毛纱的发展。技术实现要素:针对现有技术的不足,本实用新型提出了一种喷毛机分梳辊,解决纤维难从喷毛机分梳辊脱离的问题,提高喷毛机出毛的均匀程度,减低喷毛纱的粗细节数量,切头率和次品率。为解决上述技术问题,本实用新型的目的是这样实现的:一种喷毛机分梳辊,包括分梳辊辊体、摩擦辊、分梳辊轴承和针布;其特征在于:所述分梳辊辊体包括圆筒状的侧壁和位于侧壁内部的锥台,所述侧壁和所述锥台之间形成空腔;在所述侧壁和所述锥台连接处所在端固定连接所述摩擦辊,所述分梳辊轴承套设固定在所述摩擦辊表面;所述喷毛机分梳辊还包括进气端和出气端。进一步地:所述进气端为包括叶片和进气孔的端盖,在所述端盖的下表面的外沿还设有凸起的密封环;所述出气端为所述分梳辊辊体上的出气槽。分梳辊在高速旋转时,叶片扰动空气使空气对流,空气从进气孔涌入,再从出气槽吹出,将分梳辊针齿梳理的纤维向外推出,降低纤维难从针齿脱离的情况。端盖上凸起的密封环和分梳辊辊体侧壁卡合,起密封作用,保证对流空气能完全从出气槽吹出。进一步地:所述叶片在所述端盖的上表面,数量在2-5个。叶片数量根据实际对流风力需要合理配置。进一步地:所述叶片形状为有厚度的直角梯形,且直腰面位于所述端盖边缘,斜腰面指向所述端盖内侧。直角梯形直腰位于端盖边缘,斜腰面在端盖内侧,这样分梳辊在高速旋转时,空气受到离心力作用从直腰面旋转路径上甩出,流失的空气将从斜腰面和上底面旋转路径上补入,形成强对流,更利于对流空气从进气孔进入分梳辊空腔。进一步地:所述叶片沿所述端盖径向设置。进一步地:所述进气孔部分或完全处于所述叶片下底面在所述端盖的r1和r2的区间。进气孔在此处的位置主要接收高速旋转的斜腰面路径上形成的对流空气,由于斜腰面是倾斜的,对流空气极易从进气孔涌入到分梳辊空腔。进一步地:所述进气孔为圆形。进一步地:所述端盖和所述分梳辊辊体用螺丝固定。分梳辊辊体的圆台上底面有螺纹孔,端盖上对应有螺丝孔,螺丝穿过螺丝孔后拧入螺纹孔,将端盖和分梳辊辊体固定。进一步地:所述出气槽为长条形,数量在6-15条之间,并均匀排布所述分梳辊辊体一周。针布在分梳辊上的排布有一定的宽度,长条形的出气槽能更好适应,使对流空气高效提供针齿上纤维的推力,出气槽数量应根据实际需要合理配置。本实用新型的有益效果是:在分梳辊上加一带叶片和进气孔的端盖,并将分梳辊辊体设空腔,外壁上配置出气槽。分梳辊高速旋转,叶片产生的对流空气从进气孔涌入,经空腔并从出气槽吹出,对分梳辊针齿上的纤维提供一个推力,将纤维推离针齿,使纤维易于从分梳辊上脱离。改进后的分梳辊使喷毛机出毛均匀,喷毛纱粗细节数量、切头率和次品率明显降低,减少了原料的浪费而降低了生产成本。附图说明附图用来提供对本实用新型的进一步理解,并且构成说明书的一部分,与本实用新型的具体实施方式一起用于解释本实用新型,并不构成对本实用新型的限制。图1表示实施例一的分梳辊立体结构图;图2表示实施例一的分梳辊下视立体结构图;图3表示实施例一的分梳辊辊体立体结构图;图4表示实施例一的分梳辊端盖的上表面立体结构图;图5表示实施例一的分梳辊端盖的下表面立体结构图;图6表示实施例一的分梳辊端盖的上视图;图中标号:1-分梳辊辊体;2-摩擦辊;3-分梳辊轴承;4-空腔;5-端盖;6-针布;7-叶片;8-进气孔;9-密封环;10-出气槽;11-螺丝孔;12-螺纹孔;13-螺丝;21-侧壁;22-锥台具体实施方式下面结合本实用新型的具体实施方式中的附图,对本实用新型的具体实施方式的技术方案进行清楚、完整地描述,显然,所描述的具体实施方式仅仅是本实用新型一部分的具体实施方式,而不是全部的具体实施方式,基于本实用新型中的具体实施方式,本领域普通技术人员在没有做出创造性劳动前提下所获得的所有其他具体实施方式,都属于本实用新型保护的范围。实施例一参考附图1-5,一种喷毛机分梳辊,包括分梳辊辊体1、摩擦辊2、分梳辊轴承3和针布6;分梳辊辊体1直径为70mm,包括圆筒状的侧壁11和位于侧壁11内部的锥台12,侧壁11和锥台12之间形成空腔4;在侧壁11和锥台12连接处所在端,有凹陷,在凹陷处固定连接摩擦辊2,分梳辊轴承3套设固定在摩擦辊2表面。分梳辊上有一直径为70mm的端盖5,端盖5包括叶片7和进气孔8,端盖5下表面的外沿还设有凸起的密封环9。叶片7数量为3个,沿所述端盖5径向设置,形状为厚度为2mm的直角梯形,直角梯形上底和高都为5mm,下底长20mm,且直腰面位于所述端盖5边缘,斜腰面指向所述端盖5内侧。进气孔8为直径为6mm的圆形,有6个,其部分或完全处于叶片7下底面在端盖5的r1和r2的区间。分梳辊辊体1侧壁上的出气槽10为长条形,数量为12条,并均匀排布分梳辊辊体1一周。端盖5和分梳辊辊体1用螺丝13固定,端盖5上配置有螺丝孔11,对应于分梳辊辊体1上的螺纹孔12,螺丝13穿过螺丝孔11后拧入螺纹孔12,将端盖5和分梳辊辊体1固定。特别需要说明的是,分梳辊有不同的规格大小,配合的端盖直径、叶片的厚度、进气孔的直径以及相应的尺寸都要进行调整,并不局限于以上所说的尺寸。本实施例的喷毛机分梳辊工作过程如下:分梳辊在高速旋转时,空气受到离心力作用从叶片7的直腰面旋转路径上甩出,流失的空气将从斜腰面和上底面旋转路径上补入,形成空气对流。进气孔8位于叶片7斜腰在端盖5圆面垂直投影后的半径r1和r2之间,由于斜腰面是倾斜的,对流空气极易从进气孔8涌入到分梳辊空腔4,再从出气槽10吹出。出气槽10为长条形,是因为针布6在分梳辊上的排布有一定的宽度,长条形的出气槽10能更好适应,使对流空气高效提供针齿上纤维的推力。整个原理就是叶片7产生的对流空气从进气孔8涌入,经空腔9并从出气槽10吹出,对分梳辊针齿上的纤维提供一个推力,将纤维推离针齿,使纤维易于从分梳辊上脱离。这样,改进后的分梳辊使喷毛机出毛均匀,喷毛纱粗细节数量、切头率和次品率明显降低,减少了原料的浪费而降低了生产成本。为了体现本喷毛机分梳辊带来的有益效果,将本实施例一的喷毛机分梳辊和普通靠离心力分离纤维的喷毛机分梳辊(对比例)进行对比,两种喷毛机分梳辊都生产规格为7支的喷毛纱,外部编织的网纱用细度为50d锦纶弹丝,网重占喷毛纱重量的38.5%。下表1表示实施例一和对比例生产的喷毛纱设定门限。表1实施例一对比例棉结270%230%短粗节幅宽200%180%短粗节长度1.5cm1.0cm长粗节幅宽60%30%长粗节长度20cm20cm长细节幅宽-30%-18%长细节长度30cm30cm需要解释的是,表1所说的幅宽指和正常7支喷毛纱所相差的比例,长度指超出该幅宽的纱疵长度不应高于该长度值,超出设定的门限,纱线会被剪断,再重新接头后继续络筒。表2表示在表1设定的门限下,实施例一和对比例的生产的喷毛纱百万米纱疵对比。表2从表1和表2的数据可以看出,实施例一比对比例的喷毛纱各纱疵数量都减少了很多。所以本实施例一提供的喷毛机分梳辊,采用气流推动纤维脱离针齿的方式,比对比例靠离心力使纤维脱离针齿的方式,非常明显的减少了喷毛纱的纱疵。实施例二本实施例和实施例一基本相同,由于只是相应结构替换,故不再另做附图。本实施例和实施例一的区别在于,本实施例用于短纤维和抗静电纤维的喷毛纱生产。叶片数量为2个,进气孔数量为4个,出气槽数量为6个。短纤维和抗静电纤维易于从分梳辊针齿上脱离,故空气对流强度可以适当低一些,否者会影响梳理效果造成分散成单纤维程度低的不利影响,制成的喷毛纱蓬松程度下降。实施例三本实施例和实施例一基本相同,由于只是相应结构替换,故不再另做附图。本实施例和实施例一的区别在于,本实施例用于中短纤维和易产生静电的纤维的喷毛纱生产。叶片数量为5个,进气孔为长条形,出气槽数量为15个。此处的中短纤维只是比短纤维稍长;易产生静电的纤维,比如腈纶纤维、涤纶纤维,摩擦产生静电力是纤维附着在分梳辊上难以脱离,故空气对流强度应强一些。以上为本实用新型较佳的实施方式,本实用新型所属领域的技术人员还能够对上述实施方式进行变更与修改,因此,本实用新型并不局限于上述的具体实施方式,凡是本领域技术人员在本实用新型的基础上所作的任何显而易见的改进、替换或变型均属于本实用新型的保护范围。当前第1页12