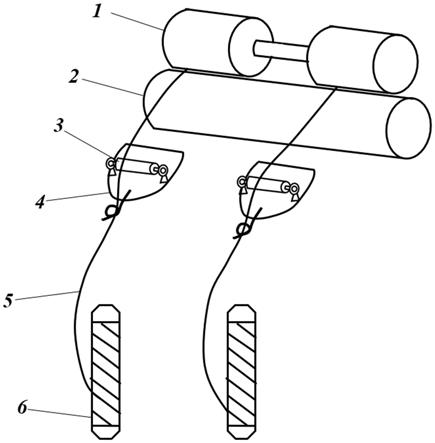
1.本发明涉及纺纱设备,具体涉及一种用于减少毛羽量的纺纱设备。
背景技术:2.纱线毛羽的多少不仅影响纱线本身性能和质量,而且影响后道工序生产,同时毛羽的多少与织物外观的光洁、纹理清晰、手感滑爽密切相关,并且最终影响到产品的内在质量和外观。棉、毛或其他原料的短纤维可以稳定地捻成连续的纱线,最终通过捻度传递变得更细、更紧。目前,环锭纺纱以其原料适应性强、品种全、成纱质量高等特点,在纺纱工业中占据主导地位。但也存在纱线毛羽过多、分布不规律和生产效率低等缺点。
3.随着人们对低能耗、高品质、高效率纺纱的要求越来越高,普通环锭纺纱已难以满足这一要求。根据环锭纺纱的原理,在加捻点开始成纱后,在钳口啮合线的出口处出现纤维束形成的加捻三角形,然后从底部传递而来的捻度使短纤维束逐渐变得更紧密、更细。然而,由于在环锭纺成纱过程中对加捻三角区区域过大的应力控制不足,造成加捻三角区边缘纤维易发生断裂;同时因为在加捻过程中纤维末端不受控制,一些纤维毛羽完全脱离纱体,所以导致环锭纺纱线会出现毛羽多、强力不足、柔软性差的问题。因此为了解决高品质纱线的生产问题,采用了各种新型的短纤维纺纱方法来满足企业的迫切要求,如紧密纺、赛络纺、复合纺等。
4.紧密纺纱近年来发展迅速,其关键机制是尽可能减小甚至消除纺纱三角区,通过集聚从主牵伸区输出的短纤维束来增强对纤维的控制。由于纤维控制性能优异,紧密纺纱纱线品质高,外观光滑均匀,强力高。相比之下,赛络纺纱通过将单股短纤维束分为双股来增强纤维控制,因而赛络纺纱线以其低毛羽、高强力和优异的耐磨性而著称。此外,复合纺纱技术则结合了长丝连续性、高强度、光滑性的优点和天然纤维的风格、手感和吸湿性的特点,通过长丝与短纤维的协同作用,使成纱具有较高的品质以及独特的结构。目前的环锭复合纺纱技术已被广泛使用,包括包芯纺、赛络菲尔纺等,都是通过调整长丝和短纤维束喂入前钳口时的间距来控制长丝和短纤维束之间的会聚。在包芯纺纱方法下,在一根短纤维束的中心喂入长丝使得短纤维在捻回过程中包裹在中心长丝上从而产生长丝为芯和短纤维为鞘结构的纱线,因此包芯纺纱线结合了环锭纺的外观和高强度的优点。但是由于长丝与短纤维之间缺乏结合力,易发生相对滑移,导致局部长丝暴露在纱线表面,而且这种现象会恶化纱线外观和力学性能。赛络菲尔纺纱是通过将一根短纤维和长丝在纺纱三角区汇合而成,长丝以均匀的螺旋结构缠绕在纱条表面。不幸的是,赛络菲尔纺纱线的短纤维没法完全被长丝包缠,在拉伸过程中容易造成结构损伤。综上所述,尽管上述新型短纤维纺纱方法可以有效地改善成纱质量,但环锭纺纱的在成纱三角区生产毛羽问题尚未从根本上得到解决。
5.基于此,牵伸过程结束后,纱条从前罗拉输送出,再由成纱区自下而上的捻度传递使纤维在内部和外部发生转移;捻度传递使纱条变得更细、更紧,最终成为纱线。关键在于,在成纱过程中,纱线质量问题主要发生在加捻三角区,较短的纤维具有更高的刚性,这使得
边缘纤维难以在成纱区得到控制,因而造成加捻过程中边缘纤维不能有效捻入纱线主体而产生毛羽。同时由于加捻三角区中的应力分布不均匀,一些边缘纤维甚至无法被捕获,最终导致纤维损失。此外,机械紧密纺纱设备旨在对三角区纤维进行低能耗集聚,但集聚通道容易堵塞和操作复杂的问题阻碍了其在纺织厂的应用。因此,在加捻三角区广泛采用附加装置的额外应力来控制纤维的运动,从而生产出少毛羽、高强度的优质纱线。然而现有的机械去羽技术往往只是将纤维毛羽聚拢贴附于纱表、经络筒后再次暴露,且集中于对三角区的处理。烧毛等后处理方法可以显著去羽,但工艺复杂成本高难以得到广泛应用。
技术实现要素:6.本发明所要解决的技术问题在于一种环锭纺纱线强制去羽装置,能够剥离纱表外的纤维,降低纱线表面的毛羽量。
7.为解决上述技术问题,本发明的环锭纺纱线强制去羽装置包括由前皮辊与前罗拉配合形成的钳口区,所述钳口区下方通过两块叶子板分别设置有导纱钩,其特征在于:所述两块叶子板上都设置有去羽组件,所述去羽组件包括通过支架连接的可自转的摩擦辊。所述前皮辊、前罗拉、摩擦辊互相平行设置。
8.所述叶子板上设置有下支架,所述下支架上通过定位器连接有上支架,所述上支架上设置有通孔,所述摩擦辊中心固定设置有连接轴杆,所述连接轴杆两端分别通过滚动轴承与所述上支架连接。
9.所述上支架、定位器、下支架组合形成角度可调的支架,从而使得摩擦辊运行角度可调、摩擦辊与纱线之间形成包围角。
10.所述连接在上支架和下支架之间的定位器上设有量角器。可根据量角器读数来判断上支架和下支架调节所形成的角度。
11.所述摩擦辊表面设置有橡胶层、聚氨酯层之一;所述摩擦辊直径设置为10
‑
25mm;所述摩擦辊的宽度设置为20
‑
30mm;所述摩擦辊表面摩擦系数设置为0.5
‑
0.8。
12.本发明还提供了所述环锭纺纱线强制去羽装置的使用方法,包括:a、将纱线经导纱钩牵引在钳口区至锭子之间;b、通过定位器调节上支架,使纱线与摩擦辊之间形成包围角;c、所述纱线行走,所述纱线在接触摩擦辊时由摩擦力带动摩擦辊旋转,同时纱线沿轴向捻回旋转时与摩擦辊表面产生相对运动,从而达到促使伸出于纱表外的纤维在摩擦作用下断裂并剥离,降低纱线表面的毛羽量,形成表层平整光洁、内部充分转移的纱线结构的目的。
13.本发明的环锭纺纱线强制去羽装置,通过在导纱钩叶子板上设置有绕中心轴线自由转动的强制去羽装置,且在与纱线呈包围角接触时由纱线运动带动其同步旋转,消除纱线运动方向上摩擦导致的意外牵伸、纤维堆积现象,减少纱线条干性能的恶化;同时纱线在沿轴向加捻运动时与摩擦辊表面产生相对运动,促使伸出于纱表外的纤维在摩擦作用下随纱线转动全部断裂并强制剥离于纱表,以降低纱线表面的毛羽量,形成表层平整光洁、内部充分转移的纱线结构,突破了调控三角区降低毛羽的理论瓶颈,解决了传统去羽方法所纺纱线表层纤维包缠、贴附于纱体而经络筒后毛羽再次产生的技术问题,且保持了环锭纺内部转移充分、纱体柔软的结构特征,克服了传统紧密纺纱线内外层结构紧密、手感差、耐络筒性差的局限性,装置操作简单、成本低廉、可使用范围广。
附图说明
14.图1是本发明的环锭纺纱线强制去羽装置的结构示意图;图2是图1的侧视图;图3是本发明中去羽组件、叶子板与导纱钩的配合示意图;图4是本发明中去羽组件的正视图;图5是本发明工作状态示意图;图6是成纱外观比较图。
具体实施方式
15.以下结合附图对本发明的具体实施方式作进一步说明。
16.如图1、图2、图3、图4、图5可见,本发明的环锭纺纱线强制去羽装置,包括由前皮辊1与前罗拉2配合形成的钳口区,所述钳口区下方通过两块叶子板4分别设置有导纱钩41,所述两块叶子板4上都设置有去羽组件3,所述去羽组件3包括通过支架连接的可自转的摩擦辊31。所述前皮辊1、前罗拉2、摩擦辊31互相平行设置。
17.如图2、图3、图4可见,所述叶子板4上设置有下支架36,所述下支架36上通过定位器35连接有上支架33,所述上支架33上设置有通孔,所述摩擦辊31中心固定设置有连接轴杆37,所述连接轴杆37两端分别通过滚动轴承32与所述上支架33连接。
18.如图3可见,所述上支架33、定位器35、下支架36组合形成角度可调的支架,从而使得摩擦辊31运行角度可调、摩擦辊31与纱线之间形成包围角。
19.所述连接在上支架33和下支架36之间的定位器35上设有量角器34。可根据量角器读数来判断上支架33和下支架36调节所形成的角度。
20.所述摩擦辊31表面设置有橡胶层、聚氨酯层之一;所述摩擦辊直径设置为10
‑
25mm;所述摩擦辊的宽度设置为20
‑
30mm;所述摩擦辊31表面摩擦系数设置为0.5
‑
0.8。
21.所述环锭纺纱线强制去羽装置的使用方法,包括:a、将纱线5经导纱钩41牵引在钳口区至锭子6之间;b、通过定位器35调节上支架33,使纱线5与摩擦辊31之间形成包围角;c、所述纱线5行走,所述纱线5在接触摩擦辊31时由摩擦力带动摩擦辊31旋转,同时纱线5沿轴向捻回旋转时与摩擦辊31表面产生相对运动,促使伸出于纱表外的纤维在摩擦作用下断裂并剥离,以降低纱线表面的毛羽量,形成表层平整光洁、内部充分转移的纱线结构。
22.应用实验为了验证本发明效果,分别采用11.8tex、29.2tex与19.4tex三个纱支品种进行应用实验,每组实验设置一个对比例,对比例中采用传统设备和方法进行纺纱,每组实验设一个实施例,实施例中纺纱设备加装了本发明的环锭纺纱线强制去羽装置进行纺纱,其余条件相同。
23.生产完成后,分别对三组6个产品进行取样分析。
24.第一组实验对比例采用传统设备进行纺纱;实施例中,环锭纺纱线强制去羽装置参数如下:摩擦辊直径设置为25mm,摩擦辊的宽度设置为20mm,摩擦辊31表面为橡胶层,摩擦辊31表面摩擦系数设置为0.8,强制去羽装
置与纱线间形成30
°
包围角,上支架33和下支架36调节所形成的角度为45
°
。
25.本组实验对象均为11.8tex纱支。
26.第二组实验对比例采用传统设备进行纺纱;实施例中,环锭纺纱线强制去羽装置参数如下:摩擦辊直径设置为25mm,摩擦辊的宽度设置为20mm,摩擦辊31表面为橡胶层,摩擦辊31表面摩擦系数设置为0.8,强制去羽装置与纱线间形成30
°
包围角,上支架33和下支架36调节所形成的角度为45
°
。
27.本组实验对象均为29.2tex纱支。
28.第三组实验对比例采用传统设备进行纺纱;实施例中,环锭纺纱线强制去羽装置参数如下:摩擦辊直径设置为25mm,摩擦辊的宽度设置为20mm,摩擦辊31表面为橡胶层,摩擦辊31表面摩擦系数设置为0.8,强制去羽装置与纱线间形成30
°
包围角,上支架33和下支架36调节所形成的角度为45
°
。
29.本组实验对象均为19.4tex纱支。
30.实验结果三组实验结果如表1,实验证明,使用本发明方法和装置,有害毛羽数量能明显降低,具体数据如下:a、对于第一组(11.8tex),与对比例相比,实施例中2mm毛羽根数下降57.3%,3mm毛羽根数下降65.8%;b、对于第二组(29.2tex),与对比例相比,实施例中2mm毛羽根数下降81.1%,3mm毛羽根数下降80.2%;c、对于第三组(19.4tex),与对比例相比,实施例中2mm毛羽根数下降72.2%,3mm毛羽根数下降82.9%。
31.以上三组覆盖了典型的纱支品种,均产生了较好的成纱性能,证明本发明具备较好的推广应用价值。
32.表1 本发明装置对不同纱线成纱性能影响对比一览表
原因分析:纱线在沿轴向加捻及转移运动时与摩擦辊表面产生相对运动,促使伸出于纱表外的纤维在摩擦作用下随纱线转动全部断裂并强制剥离于纱表,以降低纱线表面的毛羽量,形成表层平整光洁、内部充分转移的纱线结构,突破了调控三角区降低毛羽的理论瓶颈,解决了传统去羽方法所纺纱线表层纤维包缠、贴附于纱体而经络筒后毛羽再次产生的技术问题,且保持了环锭纺内部转移充分、纱体柔软的结构特征,克服了传统紧密纺纱线内外层结构紧密、手感差、耐络筒性差的局限性,装置操作简单、成本低廉、可使用范围广。
33.外观对比图6示出了若干种成纱的外观。图6中,纱线a是常规环锭纺纱线、纱线b是紧密纺纱线、纱线c是常规环锭纺纱线,纱线d是使用本发明装置所得纱线。
34.如图6可见,纱线a、纱线c表面毛羽数量较多,纱线b中,毛羽捻入纱体且一部分包缠于表面,说明紧密纺所的纱线其表面毛羽数量少于常规的环锭纺纱线。在四组纱线中,纱线d表面毛羽最少,其原因是使用本发明装置后,纱线d的表面毛羽被强制剥离、外露毛羽断裂。
35.本发明的具体实施方式包括但不局限于上述实施例,在不背离本发明精神及其实质的情况下,熟悉本领域的技术人员可根据本发明作出各种相应的改变和变形,但仍然落入本发明的保护范围。