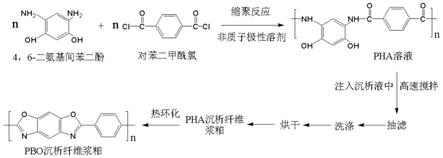
一种用于制备浆粕的pbo沉析纤维的制备方法
技术领域
1.本发明属于高性能纸基材料制造领域,具体提供了一种用于制备浆粕的pbo沉析纤维的制备方法。
背景技术:2.聚对苯撑苯并双噁唑(pbo)纤维是是目前综合性能最好的高性能有机纤维,具有高强度、高模量、耐高温和高阻燃的特点。与芳纶纤维相比,其强度、介电性能和耐热性都更为出色,且吸湿率要低得多。目前航空、航天、兵器和船舶等领域多采用芳纶纸基材料。如采用pbo纸基材料进行替代,可发挥pbo的优良性能,适应更为严苛的环境要求。
3.造纸用高性能合成纤维有两种,一种是短切纤维,一种是沉析纤维浆粕。沉析纤维浆粕表面呈毛绒状,毛羽丰富,比表面积较大,在特种纸的制备中起到至关重要的作用。短切纤维表面光滑,纤维间物理结合力较弱,仅使用短切纤维抄造出来的纸张强度很差,当配抄一定量的沉析纤维浆粕时,浆粕的毛羽间可形成物理交织,增强结合力,纸张的强度可大大增加。
4.pbo浆粕可采用沉析法制备,即将pbo浆液加入到高速剪切流动的沉析液中沉析,pbo聚合物析出得到微纤状的沉析纤维浆粕。目前pbo浆粕制备技术存在的问题是:pbo聚合物具有高度对称的化学结构,惰性极强,在沉析液中分散性能差,制备的沉析纤维浆粕毛羽不够丰富,比表面积太低,后续应用效果较差。
5.因此如何克服现有pbo沉析纤维浆粕制备过程中的上述缺陷,成为亟待解决的问题之一。
技术实现要素:6.本发明针对上述技术存在的问题,提供了一种用于制备浆粕的pbo沉析纤维的制备方法,其主要步骤如下:(1)在非质子极性溶剂中合成聚羟基酰胺(pha)前驱体聚合物;(2)将上述pha溶液过滤、脱泡后通过注入到高速搅拌的沉析浴中,得到pha微细纤维悬浮液;(3)将上述pha悬浮液抽滤、洗涤、绝对干燥,得到pha沉析纤维浆粕;(4)将pha沉析纤维浆粕进行高温热处理,得到pbo沉析纤维浆粕;上述方法以前驱体pha进行打浆,可采用非质子极性溶剂,避免了常规方法采用酸性溶剂对设备的腐蚀,本发明的pha打浆溶液的浓度更高,大幅减少溶剂使用量,节能环保,并且pha中含大量极性基团,在沉析液中分散效果更好,最终制备的pbo沉析纤维浆粕表面呈毛羽状,微纤丛生,具有更大的比表面积,性能更佳。
7.本发明在本领域中首次利用pha溶液进行打浆,pha含大量的极性基团,在沉析液中分散性良好,经高速剪切后,可形成毛羽丰富的pha浆粕,经热环化后生成pbo纤维浆粕,同样保持了原来毛羽丰富的特点,表面微纤丛生,比表面积较高,经抄造后的pbo纸性能更好。另外因pha溶解能力和分散能力更强,打浆用的pha溶液浓度远高于常规pbo溶液,使用的溶剂更少,更加节能环保。并且所用溶剂为非质子极性溶剂,不同于常规方法使用强酸作
为溶剂,对设备腐蚀小,设备维护成本低,且操作更安全。
8.其中所述的pha溶液以4,6
‑
二氨基间苯二酚盐酸盐和对苯二甲酰氯为聚合单体,在非质子极性溶剂中缩聚制得;本发明的具体技术方案如下:一种用于制备浆粕的pbo沉析纤维的制备方法,具体步骤如下:(1)合成前驱体pha聚合物在聚合釜中,加入一定量非质子极性溶剂,通氮气,加入4,6
‑
二氨基间苯二酚盐酸盐,同时加入抗氧化剂氯化亚锡,搅拌20~40min,加入与4,6
‑
二氨基间苯二酚盐酸盐等摩尔的对苯二甲酰氯,搅拌20~40min,加入催化剂异喹啉,0~50℃搅拌反应16~24小时,即制得前驱体pha聚合物溶液;更进一步的,所述的聚合釜容积优选316l;(2)制备pha沉析纤维浆粕将步骤(1)中的pha聚合物溶液经过滤除杂、利用步骤(1)中同种非质子极性溶剂稀释后,注入到高速搅拌的沉析液中,得到pha微细纤维悬浮液,维持搅拌20~30min,将悬浮液抽滤、洗涤、绝对干燥,得到pha沉析纤维浆粕;(3)热环化制备pbo沉析纤维浆粕 将步骤(2)中pha沉析纤维浆粕经300~500℃高温热环化,pha发生闭环生成pbo沉析纤维浆粕。
9.通过上述方法制备获得的pbo沉析纤维浆粕平均长度为1.2~2.5mm,比表面积为30~40m3/g。
10.而采用现有技术制备的pbo沉析纤维浆粕平均长度为0.2~1.0mm,比表面积为15~30m3/g,通过比对可知,现有技术制备的pbo沉析纤维浆粕平均长度和比表面积都低于本发明制备的pbo沉析纤维浆粕,成纸性能较差;上述制备方法中,步骤(1)中非质子极性溶剂选自n,n
‑
二甲基乙酰胺、n
‑
甲级吡咯烷酮或二甲基甲酰胺中的一种或几种;所述步骤(1)中4,6
‑
二氨基间苯二酚盐酸盐和对苯二甲酰氯的质量为溶液总质量的10
‑
15%,抗氧化剂氯化亚锡用量为4,6
‑
二氨基间苯二酚盐酸盐质量的0.1%~0.8%,催化剂异喹啉用量为4,6
‑
二氨基间苯二酚盐酸盐质量的1%~5%;所述步骤(2)中pha溶液稀释后pha质量分数为6%
‑
10%,稀释用溶剂为n,n
‑
二甲基乙酰胺、n
‑
甲级吡咯烷酮或二甲基甲酰胺中的一种或几种;所述步骤(2)中沉析液成分为有机溶剂和水,有机溶剂为n,n
‑
二甲基乙酰胺、n
‑
甲级吡咯烷酮或二甲基甲酰胺中的一种或几种,沉析液中有机溶剂体积分数为5%~20%,打浆时沉析液搅拌速度为800~2000r/min,温度为10~30℃;所述步骤(3)中,pha沉析纤维浆粕经高温热处理后,发生热环化生成pbo沉析纤维浆粕,热环化温度为300~500℃,真空度为
‑
0.06mpa~
‑
0.09mpa,时间为20~40min。
11.与现有技术相比,上述技术方案采用pha前驱体进行打浆,可采用非质子极性溶剂,不需采用强酸溶剂,节能环保;并且pha前驱体为柔性链高分子,含有大量的极性基团,在沉析液中分散效果良好,不需添加分散剂,制备的pha沉析纤维浆粕表面具有丰富的微细纤维,呈毛羽状,微纤丛生,具有更大的比表面积,性能更佳,有利于制备高性能pbo纸基材
料。
附图说明
12.图1为本发明的pbo沉析纤维浆粕制备流程图,本发明提供的pbo沉析纤维浆粕的制备流程如附图1所示,将两单体4,6
‑
二氨基间苯二酚盐酸盐和对苯二甲酰氯在非质子极性溶剂中进行缩聚反应,得到pha溶液,然后将其注入到高速搅拌的沉析液中进行沉淀,然后抽滤、洗涤、烘干得到pha沉析纤维浆粕,再经热环化得到pbo沉析纤维浆粕。
具体实施方式
13.以下通过实施例形式的具体实施方式,对本发明的上述内容做进一步的详细说明,但不应将此理解为本发明上述主题的范围仅限于以下的实例。凡基于本发明上述内容所实现的技术均属于本发明的范围,除特殊说明外,下述实施例中均采用常规现有技术完成。
14.实施例1一种用于制备浆粕的pbo沉析纤维的制备方法,包括如下步骤:(1)合成前驱体pha聚合物在316l不锈钢聚合釜中,加入n,n
‑
二甲基乙酰胺100g,通氮气,加入4,6
‑
二氨基间苯二酚盐酸盐5.69g,加入抗氧化剂氯化亚锡0.006g,搅拌20min,加入对苯二甲酰氯5.42g,搅拌20min,加入催化剂异喹啉0.05g,0℃搅拌反应24小时,即制得前驱体pha聚合物溶液。
15.(2)制备pha沉析纤维浆粕将步骤(1)中的pha聚合物溶液过滤后,稀释为质量分数为6%的pha溶液(稀释用溶剂为n,n
‑
二甲基乙酰胺),然后注入到高速搅拌的沉析液中,得到pha微细纤维悬浮液;该过程使用的沉析液为水和n,n
‑
二甲基乙酰胺混合液,其中n,n
‑
二甲基乙酰胺与水的体积比为5:95,打浆时沉析液搅拌速度为800r/min,温度为10℃,时间为20min。再将pha微细纤维悬浮液抽滤、洗涤、绝对干燥,得到pha沉析纤维浆粕。
16.(3)热环化制备pbo沉析纤维浆粕 将步骤(2)中pha沉析纤维浆粕经高温热环化,pha发生闭环生成pbo沉析纤维浆粕,热环化温度为300℃,真空度为
‑
0.06 mpa,时间为20min。
17.经检测,本实施例方案制备的pbo沉析纤维浆粕平均长度为1.2mm,比表面积为30m3/g。
18.实施例2:一种用于制备浆粕的pbo沉析纤维的制备方法,包括如下步骤:(1)合成前驱体pha聚合物在316l不锈钢聚合釜中,加入n
‑
甲级吡咯烷酮100g,通氮气,加入4,6
‑
二氨基间苯二酚盐酸盐9.03g,加入抗氧化剂氯化亚锡0.072g,搅拌40min,加入对苯二甲酰氯8.61g,搅拌40min,加入催化剂异喹啉0.45g,50℃搅拌反应16小时,即制得前驱体pha聚合物溶液。
19.(2)制备pha沉析纤维浆粕将步骤(1)中的pha聚合物溶液过滤后,稀释为质量分数为10%的pha溶液(稀释用
溶剂为n
‑
甲级吡咯烷酮),然后注入到高速搅拌的沉析液中,得到pha微细纤维悬浮液。该过程使用的沉析液为水和n
‑
甲级吡咯烷酮混合液,其中n
‑
甲级吡咯烷酮与水的体积比为20:80,打浆时沉析液搅拌速度为2000r/min,温度为30℃,时间为40min。再将pha微细纤维悬浮液抽滤、洗涤、绝对干燥,得到pha沉析纤维浆粕。
20.(3)热环化制备pbo沉析纤维浆粕 将步骤(2)中pha沉析纤维浆粕经高温热环化,pha发生闭环生成pbo沉析纤维浆粕,热环化温度为500℃,真空度为
‑
0.09 mpa,时间为40min。
21.经检测,本实施例方案制备的pbo沉析纤维浆粕平均长度为2.5mm,比表面积为40m3/g。
22.实施例3:一种用于制备浆粕的pbo沉析纤维的制备方法,包括如下步骤:(1)合成前驱体pha聚合物在316l不锈钢聚合釜中,加入二甲基甲酰胺100g,通氮气,加入4,6
‑
二氨基间苯二酚盐酸盐7.70g,加入抗氧化剂氯化亚锡0.046g,搅拌35min,加入对苯二甲酰氯7.34g,搅拌30min,加入催化剂异喹啉0.154g,30℃搅拌反应20小时,即制得前驱体pha聚合物溶液。
23.(2)制备pha沉析纤维浆粕将步骤(1)中的pha聚合物溶液过滤后,稀释为质量分数为8%的pha溶液(稀释用溶剂为二甲基甲酰胺),然后注入到高速搅拌的沉析液中,得到pha微细纤维悬浮液。该过程使用的沉析液为水和二甲基甲酰胺混合液,其中二甲基甲酰胺与水的体积比为10:90,打浆时沉析液搅拌速度为1500r/min,温度为20℃,时间为20min。再将pha微细纤维悬浮液抽滤、洗涤、绝对干燥,得到pha沉析纤维浆粕。
24.(3)热环化制备pbo沉析纤维浆粕 将步骤(2)中pha沉析纤维浆粕经高温热环化,pha发生闭环生成pbo沉析纤维浆粕,热环化温度为450℃,真空度为
‑
0.07 mpa,时间为30min。
25.经检测,本实施例方案制备的pbo沉析纤维浆粕平均长度为2.1mm,比表面积为36m3/g。
26.比较例1将2g市售pbo纤维溶解于98g浓硫酸中,制备成质量分数为2%的pbo溶液,然后将其注入到浓硫酸和水体积比为10:90的沉析液中(沉析液中加入质量分数为0.2%的十二烷基硫酸钠),高速搅拌30min,得到pbo浆粕,然后将其沉淀、过滤、洗涤、烘干得到pbo沉析纤维浆粕。
27.经检测,比较例制备的pbo沉析纤维浆粕平均长度为0.9mm,比表面积为20m3/g。该比较例的技术问题在于采用市售pbo纤维,成本极高,溶解时采用强酸溶剂,设备维护费用大。且该技术采用pbo溶液打浆,因pbo分散能力弱,在沉析液中易团聚,制备的pbo沉析纤维浆粕平均长度和比表面积都低于本发明。
28.比较例2在316l不锈钢聚合釜中,加入甲烷磺酸100g,通氮气,加入4,6
‑
二氨基间苯二酚盐酸盐7.70g,加入抗氧化剂氯化亚锡0.046g,搅拌35min,加入对苯二甲酰氯7.34g,搅拌30min,80℃搅拌反应3小时,100℃搅拌反应5小时,120℃搅拌反应5小时,140℃搅拌反应6
小时,180℃搅拌反应10小时,即制得pbo聚合物溶液。
29.将上述pbo聚合物溶液过滤后,稀释为质量分数为2%的pbo溶液(稀释用溶剂为甲烷磺酸),然后注入到高速搅拌的沉析液中(沉析液中加入质量分数为0.2%的十二烷基硫酸钠),得到pbo微细纤维悬浮液。该过程使用的沉析液为水和甲烷磺酸混合液,其中甲烷磺酸与水体积比为10:90,打浆时沉析液搅拌速度为2000r/min,温度为30℃,时间为60min。再将pbo微细纤维悬浮液抽滤、洗涤、绝对干燥,得到pbo沉析纤维浆粕。
30.经检测,上述方法制备的pbo沉析纤维浆粕平均长度为1.0mm,比表面积为23m3/g。该比较例的技术问题在于直接采用pbo溶液进行打浆,因pbo溶解能力差,必须采用强酸溶解,对设备腐蚀严重且具有较大的安全隐患;其次pbo在沉析液中分散能力差,在沉析液中易团聚,因此打浆用的pbo稀释溶液浓度很低,需浪费大量的酸性溶剂,并且因分散不好,导致最终制备的pbo沉析纤维浆粕平均长度和比表面积都较低。
31.通过上述比较例和实施例的比对可知,本技术的技术方案采用pha前驱体进行打浆,可采用非质子极性溶剂,不需采用强酸溶剂,节能环保;并且pha前驱体为柔性链高分子,含有大量的极性基团,在沉析液中分散效果良好,不需添加分散剂,制备的pha沉析纤维浆粕表面具有丰富的微细纤维,呈毛羽状,微纤丛生,具有更大的比表面积,性能更佳,有利于制备高性能pbo纸基材料。