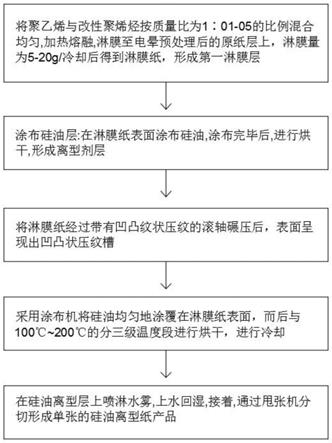
1.本发明涉及离型纸生产技术领域,具体为一种无溶剂硅油双面离型纸及其制备工艺。
背景技术:2.离型纸主要贴覆在胶带的上胶表面用于保护胶带表面的胶粘剂层。离型纸是由底纸、隔离层和防粘层组成制备工艺是在底纸的整个表面淋膜一层隔离剂(采用的隔离剂主要有聚乙烯)然后再在淋膜层的表面涂布一层防粘剂(采用的防粘剂主要为硅油)得到离型纸,离型硅油按组成成分可分为:溶剂型离型硅油,无溶剂型硅油和乳液型离型硅油。溶剂型离型硅油由于本身含有溶剂,使用过程中还需要添加大量的溶剂,对环境和人员有较大的危害,将逐渐被淘汰;而乳液型离型硅油目前适用范围较小,对纸张尤其是格拉辛纸基材适应性差;无溶剂型离型硅油适应性广,尤其对各种纸张基材拥有良好的适应性,并且产品本身无毒无污染,使用过程中也不需要使用溶剂,对环境无污染,对人员无毒害作用,成为离型硅油市场应用的最主要方向,无溶剂离型硅油根据其剥离力可分为以下几类:超轻剥离力(1-3克),轻剥离力(8-13克),中重型剥离力(15-30克),重剥离力(35-60克),超重型剥离力(>70克)。目前离型纸产品越来越多样化,对不同剥离力的离型纸均有需求,整个产业逐渐进入细分化,因此对离型硅油的要求越来越细致,进一步,现有的无溶剂硅油离型纸在加工过程中,须在原纸上涂上化工原料底涂,而原纸克重高、平滑度低,需要进行至少一次超压以后,才能在其上涂上无溶剂硅油层,由于多出超压此道工序,加工过程较为复杂、生产效率低。
3.目前离型纸普遍使用的是含有溶剂型的有机硅离型剂,溶剂的含量高达70%,而且在涂布使用时必须要添加5到7倍的溶剂稀释至较低的粘度,这种离型剂使用的溶剂量极大,对环境造成严重污染,而且该溶剂离型剂的性能一般,离型力偏高,不能适用于轻离型力及超轻离型力的要求产品,在现有离型纸的生产工艺中,由于在底纸的整个表面都涂布一层具有防粘作用的硅油,而硅油的原料价格昂贵增加生产成本,而且硅油大多采用有机溶剂稀释,这些有机溶剂易挥发、难以完全回收利用,生产过程不仅有毒性,还不利于环境保护。
技术实现要素:4.本发明的目的在于提供一种无溶剂硅油双面离型纸及其制备工艺,具备使用时无需添加任何溶剂,可直接涂布使用,而且适合于轻离型力及超轻离型力的产品和的硅油用量小、保护环境的优点,解决了在涂布使用时必须要添加5到7倍的溶剂稀释至较低的粘度,这种离型剂使用的溶剂量极大,对环境造成严重污染,而且该溶剂离型剂的性能一般,离型力偏高,不能适用于轻离型力及超轻离型力的要求产品,在现有离型纸的生产工艺中,由于在底纸的整个表面都涂布一层具有防粘作用的硅油,而硅油的原料价格昂贵增加生产成本,而且硅油大多采用有机溶剂稀释,这些有机溶剂易挥发、难以完全回收利用,生产过程
不仅有毒性,还不利于环境保护的问题。
5.为实现上述目的,本发明提供如下技术方案:一种无溶剂硅油双面离型纸,包括以下重量组成份:
6.无溶剂硅油0.3-1.5g/m2,针叶木浆25-35g/m2,33-40阔叶木浆g/m2,发泡剂0.6-0.9g/m2,活性剂11-14g/m2,高分子聚合物11-15g/m2,聚环氧乙烷7-11g/m2,润滑剂12-15g/m2。
7.优选的,所述高分子聚合物由如下重量份的组分组成:4-6份的聚氨酯、7-9份的聚乳酸、11-15份的聚乙烯醇2-5份的聚苯乙烯,针叶木浆采用马尾松纤维木浆、落叶松纤维木浆、红松纤维木浆、云杉纤维木浆中的一种或两种以上混合物,发泡剂由如下重量份的原料制成:1-2份的碳酸镁、3-5份的石油醚、2-4份的偶氮二甲酰胺;活性剂采用硬脂酸;润滑剂采用氯化石蜡。
8.一种无溶剂硅油双面离型纸制备工艺,包括以下步骤:
9.步骤1:将聚乙烯与改性聚烯烃按质量比为1∶01-05的比例混合均匀,加热熔融,淋膜至电晕预处理后的原纸层上,淋膜量为5-20g/冷却后得到淋膜纸,形成第一淋膜层;
10.步骤2:涂布硅油层:在淋膜纸表面涂布硅油,涂布完毕后,进行烘干,形成离型剂层;
11.步骤3:将淋膜纸经过带有凹凸纹状压纹的滚轴碾压后,表面呈现出凹凸状压纹槽;
12.步骤4:采用涂布机将硅油均匀地涂覆在淋膜纸表面,而后与100℃~200℃的分三级温度段进行烘干,进行冷却;
13.步骤5:在硅油离型层上喷淋水雾,上水回湿,接着,通过甩张机分切形成单张的硅油离型纸产品。
14.优选的,所述在步骤1中,原纸层制作选择格拉辛纸,在原纸层上下两面电晕处理,然后双面淋膜。优选pe塑料粒子,具有良好的熔融指数,与原纸有较好的粘结力,快速淋膜并控制涂布量,淋膜后的离型纸防潮效果更佳,淋膜层为pe塑料粒子,采用的电晕处理机对原纸层表面以370-525w的公里进行处理180s。
15.优选的,所述在步骤2中,离型剂层为无溶剂硅油,涂布定量:0.3-1.5g/m2,离型层均选用无溶剂硅油,使用时无需添加任何溶剂,可直接涂布使用,而且适合于轻离型力及超轻离型力的产品。
16.优选的,所述在步骤4中,三级温度段,其头端温度段的温度区间为100~150℃,中间温度段的温度区间为150~200℃,尾端温度段的温度区间为150~100℃。
17.优选的,所述聚乙烯与改性聚烯烃混合物,先经过温度为150~250℃加热架桥,然后再将温度提高至280~400℃熔融后再施加10mpa~20mpa的压力将其挤出,淋膜时保持温度在300~400℃之间。
18.优选的,所述淋膜纸经凹凸状压纹的滚轴压碾时传送带走纸速度,为50~100m/min。
19.优选的,所述硅油是以0.5~10g/
㎡
的干硅涂量均匀地涂在淋膜纸凸状面上。
20.优选的,所述涂了硅油的淋膜纸烘干时,采用传送带方式将淋膜纸送入烘干箱,传送带走纸速度为50~100m/min。
21.与现有技术相比,本发明的有益效果是:本发明通过设置离型剂层、淋膜层和原纸层,解决了在涂布使用时必须要添加5到7倍的溶剂稀释至较低的粘度,这种离型剂使用的溶剂量极大,对环境造成严重污染,而且该溶剂离型剂的性能一般,离型力偏高,不能适用于轻离型力及超轻离型力的要求产品,在现有离型纸的生产工艺中,由于在底纸的整个表面都涂布一层具有防粘作用的硅油,而硅油的原料价格昂贵增加生产成本,而且硅油大多采用有机溶剂稀释,这些有机溶剂易挥发、难以完全回收利用,生产过程不仅有毒性,还不利于环境保护的问题,该一种无溶剂硅油双面离型纸及其制备工艺,具备使用时无需添加任何溶剂,可直接涂布使用,而且适合于轻离型力及超轻离型力的产品和的硅油用量小、保护环境的优点。
附图说明
22.图1为本发明工艺流程示意图。
具体实施方式
23.下面将通过实施例的方式对本发明作更详细的描述,这些实施例仅是举例说明性的而没有任何对本发明范围的限制。
24.本发明提供一种技术方案:一种无溶剂硅油双面离型纸,包括以下重量组成份:
25.无溶剂硅油0.3-1.5g/m2,针叶木浆25-35g/m2,33-40阔叶木浆g/m2,发泡剂0.6-0.9g/m2,活性剂11-14g/m2,高分子聚合物11-15g/m2,聚环氧乙烷7-11g/m2,润滑剂12-15g/m2。
26.一种无溶剂硅油双面离型纸制备工艺,包括以下步骤:
27.步骤1:将聚乙烯与改性聚烯烃按质量比为1∶01-05的比例混合均匀,加热熔融,淋膜至电晕预处理后的原纸层上,淋膜量为5-20g/冷却后得到淋膜纸,形成第一淋膜层;
28.步骤2:涂布硅油层:在淋膜纸表面涂布硅油,涂布完毕后,进行烘干,形成离型剂层;
29.步骤3:将淋膜纸经过带有凹凸纹状压纹的滚轴碾压后,表面呈现出凹凸状压纹槽;
30.步骤4:采用涂布机将硅油均匀地涂覆在淋膜纸表面,而后与100℃~200℃的分三级温度段进行烘干,进行冷却;
31.步骤5:在硅油离型层上喷淋水雾,上水回湿,接着,通过甩张机分切形成单张的硅油离型纸产品。
32.实施例一:
33.将聚乙烯与改性聚烯烃按质量比为1∶01-05的比例混合均匀,加热熔融,淋膜至电晕预处理后的原纸层上,淋膜量为5-20g/冷却后得到淋膜纸,形成第一淋膜层;涂布硅油层:在淋膜纸表面涂布硅油,涂布完毕后,进行烘干,形成离型剂层;将淋膜纸经过带有凹凸纹状压纹的滚轴碾压后,表面呈现出凹凸状压纹槽;采用涂布机将硅油均匀地涂覆在淋膜纸表面,而后与100℃~200℃的分三级温度段进行烘干,进行冷却;在硅油离型层上喷淋水雾,上水回湿,接着,通过甩张机分切形成单张的硅油离型纸产品。
34.实施例二:
35.将聚乙烯与改性聚烯烃按质量比为1∶01-05的比例混合均匀,加热熔融,淋膜至电晕预处理后的原纸层上,淋膜量为5-20g/冷却后得到淋膜纸,形成第一淋膜层;高分子聚合物由如下重量份的组分组成:4-6份的聚氨酯、7-9份的聚乳酸、11-15份的聚乙烯醇2-5份的聚苯乙烯,针叶木浆采用马尾松纤维木浆、落叶松纤维木浆、红松纤维木浆、云杉纤维木浆中的一种或两种以上混合物,发泡剂由如下重量份的原料制成:1-2份的碳酸镁、3-5份的石油醚、2-4份的偶氮二甲酰胺;活性剂采用硬脂酸;润滑剂采用氯化石蜡,在步骤1中,原纸层制作选择格拉辛纸,在原纸层上下两面电晕处理,然后双面淋膜。优选pe塑料粒子,具有良好的熔融指数,与原纸有较好的粘结力,快速淋膜并控制涂布量,淋膜后的离型纸防潮效果更佳,淋膜层为pe塑料粒子,采用的电晕处理机对原纸层表面以370-525w的公里进行处理180s,涂布硅油层:在淋膜纸表面涂布硅油,涂布完毕后,进行烘干,形成离型剂层;在步骤2中,离型剂层为无溶剂硅油,涂布定量:0.3-1.5g/m2,离型层均选用无溶剂硅油,使用时无需添加任何溶剂,可直接涂布使用,而且适合于轻离型力及超轻离型力的产品,将淋膜纸经过带有凹凸纹状压纹的滚轴碾压后,表面呈现出凹凸状压纹槽;采用涂布机将硅油均匀地涂覆在淋膜纸表面,而后与100℃~200℃的分三级温度段进行烘干,进行冷却;在硅油离型层上喷淋水雾,上水回湿,接着,通过甩张机分切形成单张的硅油离型纸产品。
36.实施例三:
37.将聚乙烯与改性聚烯烃按质量比为1∶01-05的比例混合均匀,加热熔融,淋膜至电晕预处理后的原纸层上,淋膜量为5-20g/冷却后得到淋膜纸,形成第一淋膜层;高分子聚合物由如下重量份的组分组成:4-6份的聚氨酯、7-9份的聚乳酸、11-15份的聚乙烯醇2-5份的聚苯乙烯,针叶木浆采用马尾松纤维木浆、落叶松纤维木浆、红松纤维木浆、云杉纤维木浆中的一种或两种以上混合物,发泡剂由如下重量份的原料制成:1-2份的碳酸镁、3-5份的石油醚、2-4份的偶氮二甲酰胺;活性剂采用硬脂酸;润滑剂采用氯化石蜡,在步骤1中,原纸层制作选择格拉辛纸,在原纸层上下两面电晕处理,然后双面淋膜。优选pe塑料粒子,具有良好的熔融指数,与原纸有较好的粘结力,快速淋膜并控制涂布量,淋膜后的离型纸防潮效果更佳,淋膜层为pe塑料粒子,采用的电晕处理机对原纸层表面以370-525w的公里进行处理180s,涂布硅油层:在淋膜纸表面涂布硅油,涂布完毕后,进行烘干,形成离型剂层;在步骤2中,离型剂层为无溶剂硅油,涂布定量:0.3-1.5g/m2,离型层均选用无溶剂硅油,使用时无需添加任何溶剂,可直接涂布使用,而且适合于轻离型力及超轻离型力的产品,将淋膜纸经过带有凹凸纹状压纹的滚轴碾压后,表面呈现出凹凸状压纹槽;在步骤4中,三级温度段,其头端温度段的温度区间为100~150℃,中间温度段的温度区间为150~200℃,尾端温度段的温度区间为150~100℃,聚乙烯与改性聚烯烃混合物,先经过温度为150~250℃加热架桥,然后再将温度提高至280~400℃熔融后再施加10mpa~20mpa的压力将其挤出,淋膜时保持温度在300~400℃之间,淋膜纸经凹凸状压纹的滚轴压碾时传送带走纸速度,为50~100m/min,采用涂布机将硅油均匀地涂覆在淋膜纸表面,而后与100℃~200℃的分三级温度段进行烘干,进行冷却;在硅油离型层上喷淋水雾,上水回湿,接着,通过甩张机分切形成单张的硅油离型纸产品。
38.实施例四:
39.将聚乙烯与改性聚烯烃按质量比为1∶01-05的比例混合均匀,加热熔融,淋膜至电晕预处理后的原纸层上,淋膜量为5-20g/冷却后得到淋膜纸,形成第一淋膜层;高分子聚合
物由如下重量份的组分组成:4-6份的聚氨酯、7-9份的聚乳酸、11-15份的聚乙烯醇2-5份的聚苯乙烯,针叶木浆采用马尾松纤维木浆、落叶松纤维木浆、红松纤维木浆、云杉纤维木浆中的一种或两种以上混合物,发泡剂由如下重量份的原料制成:1-2份的碳酸镁、3-5份的石油醚、2-4份的偶氮二甲酰胺;活性剂采用硬脂酸;润滑剂采用氯化石蜡,在步骤1中,原纸层制作选择格拉辛纸,在原纸层上下两面电晕处理,然后双面淋膜。优选pe塑料粒子,具有良好的熔融指数,与原纸有较好的粘结力,快速淋膜并控制涂布量,淋膜后的离型纸防潮效果更佳,淋膜层为pe塑料粒子,采用的电晕处理机对原纸层表面以370-525w的公里进行处理180s,涂布硅油层:在淋膜纸表面涂布硅油,涂布完毕后,进行烘干,形成离型剂层;在步骤2中,离型剂层为无溶剂硅油,涂布定量:0.3-1.5g/m2,离型层均选用无溶剂硅油,使用时无需添加任何溶剂,可直接涂布使用,而且适合于轻离型力及超轻离型力的产品,将淋膜纸经过带有凹凸纹状压纹的滚轴碾压后,表面呈现出凹凸状压纹槽;在步骤4中,三级温度段,其头端温度段的温度区间为100~150℃,中间温度段的温度区间为150~200℃,尾端温度段的温度区间为150~100℃,聚乙烯与改性聚烯烃混合物,先经过温度为150~250℃加热架桥,然后再将温度提高至280~400℃熔融后再施加10mpa~20mpa的压力将其挤出,淋膜时保持温度在300~400℃之间,淋膜纸经凹凸状压纹的滚轴压碾时传送带走纸速度,为50~100m/min,硅油是以0.5~10g/
㎡
的干硅涂量均匀地涂在淋膜纸凸状面上,涂了硅油的淋膜纸烘干时,采用传送带方式将淋膜纸送入烘干箱,传送带走纸速度为50~100m/min,采用涂布机将硅油均匀地涂覆在淋膜纸表面,而后与100℃~200℃的分三级温度段进行烘干,进行冷却;在硅油离型层上喷淋水雾,上水回湿,接着,通过甩张机分切形成单张的硅油离型纸产品。
40.尽管已经示出和描述了本发明的实施例,对于本领域的普通技术人员而言,可以理解在不脱离本发明的原理和精神的情况下可以对这些实施例进行多种变化、修改、替换和变型,本发明的范围由所附权利要求及其等同物限定。