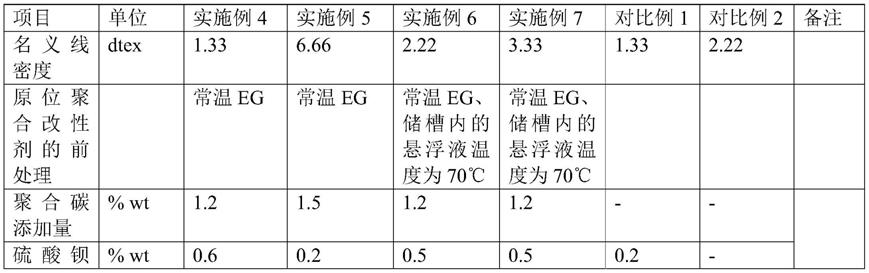
1.本发明属于纺丝技术领域,具体涉及一种超低热收缩率聚酯短纤维及其制备方法。
背景技术:2.聚对苯二甲酸乙二醇酯(pet)纤维已经成为全球纺织用纤维的最重要来源,数量占纺织用纤维的50%以上。90%的聚酯长丝和短纤维用于传统织造及非织造纺织品,10%用于产业用纺织品。采用对苯二甲酸、乙二醇直接酯化-连续缩聚合成pet工艺是1995年以来普遍采用的工业化手段,民用长丝及短纤维采用直接纺丝也成为环保、节能、低成本生产的主要工艺路线。良好性能以及相对低的制造成本,使得应用领域不断开拓。
3.涤纶短纤维与长丝的明显区别在于制造过程中的纤维集束总纤度大大超过涤纶长丝,无论是在纺丝成形及后续的拉伸、卷曲、热定型工序,其加工过程的总纤度是长丝的4百~2万倍,拉伸速度则为长丝的10~20%。因此,提高短纤维物理机械性能均匀性的技术难度相对很高。
4.涤纶短纤维初期主要用于和棉花混纺,随着工艺生产技术的进步,包括共聚、共混、表面改性等技术已经逐步在生产实际中应用,应用领域已经拓展到超仿棉、仿毛、仿黏胶纤维、非织造布、以及缝纫线、产业用超短纤维等多领域。从产品品种开发的角度,采用改性的聚酯切片熔融纺丝相对简易,但制造能耗、物料消耗高、管理成本高,产品质量不均匀。因此,连续聚合直接纺丝的共聚、共混改性短纤维并不常见。
5.新应用领域的拓展,提出涤纶短纤维更高的技术要求,包括更低的热收缩率、更高的均匀性等等。满足这些技术要求的手段主要涉及两个方面,一是现有直接纺丝涤纶短纤维生产装置通过纺丝、后拉伸及热处理等工艺调整实施;二是通过合成聚酯过程的共聚、共混改性或熔体共混实施。
6.第一种手段实施相对简单,但现阶段在很大程度上受到特性黏度在0.64~0.67dl/g的聚对苯二甲酸乙二醇酯聚酯材料特性的限制,与材料微观结构密切关联的大部分工艺调整难以实现突破。例如与纤维内大分子取向、结晶、非晶区取向以及应力松弛有关的宏观热收缩率。
7.热收缩率的大小,在很大程度上与纤维在应用加工过程及最终产品的使用要求关联,热收缩率达到50%以上的短纤维作为非织造布用于原料高密度人造革的基布;而热收缩率小于5%已经成为民用缝纫线用短纤维的基本要求;对于非织造布等复合材料技术加工要求,希望在加工温度180℃时的纤维收缩率小于1%,以满足复合材料的最终技术要求。
8.第二种手段主要涉及了在大容量连续化生产装置的技术经济可行性,尤其是涉及到直接纺丝,随着新型单体的产业化,共聚改性具有比较宽泛的单体选择以及产业化的先例,例如酸改性低熔点聚酯的直接纺丝、酸改性阳离子染料可染聚酯的直接纺丝等;但相对共混改性依然成本较高、品种切换过渡期长等缺陷,依然需要继续技术进步。
9.共混改性的优势在于相对灵活的手段,所选择的共混物不参与聚酯发生化学反
应,可在聚酯合成反应过程参与共混,也可在纺丝以前参与共混。实现在聚酯的基本特性没有变动的前提下可实现纤维性能的大幅度改变。
10.通常,有机物的共混可选择熔融过程,例如染料等;而无机物的共混在熔体状态的混合难度较高,主要涉及两大原因,一是聚酯熔体的动力黏度高,采用机械搅拌将额外能耗,并使得熔体升温,可能引起聚合物的降解;二是超细粉末的无机物自身存在团聚效应,不实施分散手段,将造成改性剂在熔体分布极度不匀,甚至造成纺丝、后拉伸过程的不稳定,是最终产品质量不均匀的主要原因。
11.因此,共混改性的技术难题是筛选不改变聚合反应过程,不影响催化剂的催化效果以及在过程体现中可实现良好分散效果,同时具有原料可得、成本可接受的要求。
12.采用在pta/eg浆料调配过程、预缩聚熔融体过程添加这些改性剂的好处是充分利用了原设计就有的机械和化学热动能分散搅拌手段。
13.近年来,超细颗粒及其分散性研究已经取得了长足的进步,工业化基本成熟,随着贯彻可持续发展理念的进程,选用这些添加剂以及分散剂制造的聚酯以及纤维除了成本,更必须考虑在加工、使用和再生过程对环境的影响以及生产、使用过程的安全性。
14.国内外针对降低聚酯长丝、聚酯膜塑料、薄膜收缩率以及降低收缩率的添加剂和相关的技术尝试和产业化也取得进展。
15.中国专利cn 108130743 b“超低收缩型遮阳布及其制备方法”采用对苯二甲酸、乙二醇和带支链的二元醇共聚,经过固相缩聚增粘、熔融、计量、挤出、冷却、上油、拉伸、热定型和卷绕制得超低收缩型聚酯工业丝,其190℃、15min和0.01cn/dtex条件下的干热收缩率为2.2
±
0.35%。
16.中国专利cn 109750363 b“超低收缩型聚酯工业丝的制备方法”,采用fdy工艺,在紧张热定型工序与卷绕工序之间增设松弛热处理工序,松弛热处理是指将聚酯丝束在适当的松弛状态经过一定温度的空间,适当的松弛状态,超喂率为3.0~5.0%,200~240℃,一对平行排列且非共面的热板之间的空间。在190℃,15分钟,4.0cn/dtex负荷测试条件下的干热收缩率1.8
±
0.25%。
17.中国专利cn 105839207 a“超低收缩有光fdy的生产方法”,双辊加热双辊定型、主网络及后加热板组成,热板加热的温度300~350℃,获得沸水收缩率在3%以下。
18.中国专利cn 107663665 b“一种高强低收缩特亮绣花线聚酯牵伸丝的制备方法”公开了一种高强低收缩特亮绣花线聚酯牵伸丝的制备方法,选取黏度为0.70~0.80dl/g的聚酯切片为原料,其中包含添加石墨烯作为改性聚酯的添加剂,经过熔融纺丝、拉伸定型等工序,其最低的沸水收缩率为2%。
19.中国专利cn 111875941 a“超支化聚酯作为聚酯模塑料低收缩添加剂及增韧剂的用途”公开了超支化聚酯作为聚酯模塑料低收缩添加剂及增韧剂的用途。
20.中国专利cn 113480761 a“一种高韧性低收缩聚酯薄膜及其制备方法”公开了一种高韧性低收缩聚酯薄膜,由pet60-90份、pen10-40份、功能增韧组分5-20份、扩链剂2-6份、复合抗收缩剂1-5份以及热稳定剂0.1-1份组成。复合抗收缩剂由单硬脂酸甘油酯与亚磷酸三月桂酯、气相白炭黑、钛酸酯偶联剂按质量比为10:3-5:1-2:0.2-0.5混合而成。实施后的最低热收缩率150℃,30分钟条件下为0.4%。
21.以上这些公开的专利主要涉及了采用高黏度聚酯熔融纺丝,采用高温热定型得到
长丝的最低干热收缩率为1.8
±
0.25%,尽管收缩率数值已经很接近聚酯短纤维非织造布复合材料加工的要求,但是现阶段高黏度熔融体的输送在聚酯短纤维直接纺丝工艺中难以实现,其高温处理装备也不适合短纤维形式;添加石墨烯对降低长丝的热收缩率并不明显,添加超支化聚酯和单硬脂酸甘油酯与亚磷酸三月桂酯、气相白炭黑、钛酸酯偶联剂按质量比为10:3-5:1-2:0.2-0.5混合而成的复合抗收缩剂,对降低聚酯模塑材料成型及薄膜的收缩率有效,但同样也不适合在聚酯合成过程添加,超支化聚酯的羟基和羧基将参与对苯二甲酸与乙二醇的反应,将妨碍纺丝及后拉伸过程的顺利进行。
22.因此,需要提供一种具有超低热收缩率的聚酯短纤维,同时,原位聚合改性剂在聚酯合成过程中添加,且原位聚合改性剂不参与酯化与缩聚的高分子合成反应,也不影响聚对苯二甲酸乙二醇酯酯化、缩聚钛系、锑系催化剂的催化效果。
技术实现要素:23.本发明所要解决的技术问题是针对现有技术的不足提供一种超低热收缩率聚酯短纤维及其制备方法,本超低热收缩率聚酯短纤维及其制备方法将经过原位聚合改性后的聚对苯二甲酸乙二醇酯熔体经过纺丝、平衡、集束、拉伸、卷曲、热定型后增设对丝片的远红外辐射加热,使切断后的短纤维热收缩率小于采用现有降低纤维热收缩率方法制备纤维的热收缩率。
24.为实现上述技术目的,本发明采取的技术方案为:
25.一种超低热收缩率聚酯短纤维,由原位聚合改性后的聚对苯二甲酸乙二醇酯的熔体纺丝而成,其中原位聚合改性后的聚对苯二甲酸乙二醇酯内包含原位聚合改性剂,所述原位聚合改性剂包括聚合碳和硫酸钡。
26.为实现上述技术目的,本发明采取的另一个技术方案为:
27.一种超低热收缩率聚酯短纤维的制备方法,包括:
28.将经过原位聚合改性后的聚对苯二甲酸乙二醇酯的熔体输送至纺丝箱体,计量并挤出,骤冷成丝条,丝条再经过1000~1350m/min速度的纺丝,在相对湿度为60
±
5rh%、温度为20~28℃的环境条件下平衡24小时以上,集束后再对丝条进行拉伸、卷曲并在190~240℃高温、20~60分钟长时间条件下,采用金属热辊或热空气并增设远红外热量辐射装置对丝条进行处理,之后,切断成为短纤维,该短纤维为超低热收缩率聚酯短纤维;
29.其中原位聚合改性后的聚对苯二甲酸乙二醇酯内包含原位聚合改性剂,所述原位聚合改性剂包括聚合碳和硫酸钡。
30.作为本发明进一步改进的技术方案,原位聚合改性后的聚对苯二甲酸乙二醇酯的制备方法为:
31.步骤1:将聚合碳及硫酸钡在分散剂的存在下,与乙二醇调配成悬浮液,悬浮液的浓度为30~40%wt,悬浮液储存于有搅拌的、夹套保温的储槽内,储槽内的悬浮液温度为70
±
5℃;
32.步骤2:在含有对苯二甲酸与乙二醇的混合浆料中计量注入悬浮液,之后送入酯化釜进行酯化反应,酯化产物通过齐聚物管线送入缩聚釜进行缩聚反应;或者,将含有对苯二甲酸与乙二醇的混合浆料送入酯化釜进行酯化反应,酯化产物通过齐聚物管线送入缩聚釜进行缩聚反应,同时,悬浮液计量注入齐聚物管线;
33.步骤3:缩聚后得到的熔体即为原位聚合改性后的聚对苯二甲酸乙二醇酯的熔体。
34.作为本发明进一步改进的技术方案,所述聚合碳为超细粉末纳米颗粒,其平均粒径为400~1200nm,添加量为聚对苯二甲酸乙二醇酯的0.3~3.5%wt。
35.作为本发明进一步改进的技术方案,所述硫酸钡为超细粉末纳米颗粒,其平均粒径为500~1500nm,添加量为聚对苯二甲酸乙二醇酯的0.2~3.0%wt。
36.作为本发明进一步改进的技术方案,所述分散剂为磷酸盐,添加量为聚合碳和硫酸钡总量的1~3%wt。
37.作为本发明进一步改进的技术方案,所述磷酸盐采用三聚磷酸钾。
38.本发明的有益效果为:
39.本发明原位聚合改性剂不参与酯化与缩聚的高分子合成反应,也不影响聚对苯二甲酸乙二醇酯酯化、缩聚钛系、锑系催化剂的催化效果,这些原位聚合改性剂能够稳定地、均匀地分布于高聚物熔融体内。
40.经过改性后的熔融体其流动性能并没有改变,也不影响熔体过滤器的使用工况,不需要特意调整熔体输送工艺条件。
41.经过纺丝和高速拉伸后的聚酯初生纤维已经具有了各向异性的特点,延纤维轴方向的大分子出现部分取向,这些现象出现会造成集束后再拉伸过程的不稳定并造成最终纤维收缩率的不均匀,因此需要在基本稳定的环境,相对湿度60
±
10rh%、温度24~28℃条件下平衡至少24小时,使得纤维的大分子取向度从20%,下降到小于5%。
42.已经含有原位聚合改性剂的初生纤维与普通的聚酯初生纤维相比,具有更好的导热性和易结晶性特点,可适合3~4倍的机械拉伸,使纤维的拉伸取向程度大幅度提高,并使大分子在后续的热定型过程中更容易砌入晶格形成结晶,这个特点无论对是否添加传统的二氧化钛消光剂都有相同的结果。
43.当经过拉伸纤维内的大分子具有高度取向,并诱导形成部分结晶,通过进一步施以热量以消除晶区外由于高度取向形成的大分子内应力,是降低最终纤维轴方向的热收缩率的重要步骤。由于聚对苯二甲酸乙二醇酯的热传导能力低,金属热辊或热风的热量传递速度受到丝片层的阻碍,造成纤维在不同丝片中得到的热量以及时间不同而造成不均匀,因此传统的后处理工艺,无论是丝束在有张力条件下或无张力条件下的高温差以提高传导速度的热定型难以满足纤维收缩率小于2%的结果。本发明纤维内的原位聚合改性剂都具备了良好的热传导性能,大大改善了纤维之间的热传导效率,因此可以在现有传统的聚酯纤维后处理装置上减少纤维热收缩率的差异。间接地,也可从纤维的拉伸强度的均匀性得到证实。
44.采用远红外加热丝束是弥补现有热定型装备条件下进一步提升加热温度的手段,石英红外灯最大光发射出现在大约1100-1200nm波段范围,但聚对苯二甲酸乙二醇酯在500-2000nm区域吸收能量较差,因此,本发明的原位聚合改性剂,尤其是聚合碳的存在,大大提高了对石英远红外灯发射能量的接受范围。因此,在现有的生产线上,可以在采用热辊式进张热定型工艺的丝束卷曲以后用对丝束进一步红外线辐射加热;也可以在采用松弛热定型工艺的热风定型设备之后增设远红外辐射加热,以进一步对丝片加热。
45.本发明适用聚对苯二甲酸乙二醇酯单纤维线密度为0.88~9.99detx,在180
±
1℃、0.075
±
0.0075cn/dtex、30分钟测得干热收缩率可控制在0.1~1.0%范围内,小于采用
现有降低纤维热收缩率方法制备纤维的热收缩率。其余卷曲性能和物理机械性能均符合涤纶短纤维各品种相应的国家(gb/t 14464涤纶短纤维)、团体(行业)标准(fz/t 52005缝纫线用涤纶短纤维)等的优级品技术要求。
具体实施方式
46.下面对本发明的具体实施方式作出进一步说明:
47.实施例1:
48.本超低热收缩率聚酯短纤维的制备方法,包括:
49.将经过原位聚合改性后的聚对苯二甲酸乙二醇酯的熔体输送至纺丝箱体,计量并挤出,骤冷成丝条,丝条再经过1000m/min速度的纺丝,在相对湿度为55rh%、温度为20℃的环境条件下平衡24小时以上,集束后再对丝条进行拉伸、卷曲并在190℃高温、60分钟长时间条件下,采用金属热辊并增设远红外热量辐射装置对丝条进行处理,之后,切断成为短纤维,该短纤维为超低热收缩率聚酯短纤维。
50.其中原位聚合改性后的聚对苯二甲酸乙二醇酯内包含原位聚合改性剂,所述原位聚合改性剂包括两种,其一为纳米级的聚合碳,一种非结晶碳结构材料,由呋喃树脂高温热解炭化制得。也称玻璃碳,其结构不同于石墨,虽然含有微晶层型结构,但不排成行,整体是无定形碳,但形成聚合物的有节结构。本实施例所采用的是超细粉末微颗粒,其平均粒径为400nm,添加量为聚对苯二甲酸乙二醇酯的3.5%wt。其二为超细粉末硫酸钡,其平均粒径为500nm,添加量为对苯二甲酸乙二醇酯的3.0%wt。
51.原位聚合改性后的聚对苯二甲酸乙二醇酯的制备方法为:
52.步骤1:对上述原位聚合改性剂进行原位聚合的前处理,将聚合碳及硫酸钡在分散剂三聚磷酸钾的存在下,与乙二醇调配成悬浮液,悬浮液的浓度为30%wt,悬浮液储存于有搅拌的、夹套保温的储槽内,储槽内的悬浮液温度为65℃。
53.步骤2:可根据pet合成及直接纺丝的主要工业化工艺路线,可选择在含有对苯二甲酸与乙二醇的混合浆料中计量注入悬浮液,之后送入酯化釜进行酯化反应,酯化产物通过齐聚物管线送入缩聚釜进行缩聚反应;酯化和缩聚的工艺与改性前基本一致,即适合现有生产装置的不同流程和规模。
54.步骤3:缩聚后得到的熔体即为原位聚合改性后的聚对苯二甲酸乙二醇酯的熔体。
55.本实施例的分散剂为磷酸盐,具体为三聚磷酸钾,添加量为聚合碳和硫酸钡总量的1%wt。在步骤2的混合浆料中对苯二甲酸与乙二醇的质量比例为1:1.12,混合浆料还含有催化剂和0.4%wt的消光剂,催化剂为0.18%wt的锑系催化剂或0.0005%wt的钛系催化剂。
56.实施例2:
57.本超低热收缩率聚酯短纤维的制备方法,包括:
58.将经过原位聚合改性后的聚对苯二甲酸乙二醇酯的熔体输送至纺丝箱体,计量并挤出,骤冷成丝条,丝条再经过1350m/min速度的纺丝,在相对湿度为60rh%、温度为28℃的环境条件下平衡24小时以上,集束后再对丝条进行拉伸、卷曲并在240℃高温、20分钟长时间条件下,采用热空气并增设远红外热量辐射装置对丝条进行处理,之后,切断成为短纤维,该短纤维为超低热收缩率聚酯短纤维。
59.其中原位聚合改性后的聚对苯二甲酸乙二醇酯内包含原位聚合改性剂,所述原位聚合改性剂包括两种,其一为纳米级的聚合碳,一种非结晶碳结构材料,由呋喃树脂高温热解炭化制得。也称玻璃碳,其结构不同于石墨,虽然含有微晶层型结构,但不排成行,整体是无定形碳,但形成聚合物的有节结构。本实施例所采用的是超细粉末微颗粒,其平均粒径为1200nm,添加量为聚对苯二甲酸乙二醇酯的0.3%wt。其二为超细粉末硫酸钡,其平均粒径为1500nm,添加量为对苯二甲酸乙二醇酯的0.2%wt。
60.原位聚合改性后的聚对苯二甲酸乙二醇酯的制备方法为:
61.步骤1:对上述原位聚合改性剂进行原位聚合的前处理,将聚合碳及硫酸钡在分散剂三聚磷酸钾的存在下,与乙二醇调配成悬浮液,悬浮液的浓度为40%wt,悬浮液储存于有搅拌的、夹套保温的储槽内,储槽内的悬浮液温度为75℃。
62.步骤2:可根据pet合成及直接纺丝的主要工业化工艺路线,可选择在含有对苯二甲酸与乙二醇的混合浆料中计量注入悬浮液,之后送入酯化釜进行酯化反应,酯化产物通过齐聚物管线送入缩聚釜进行缩聚反应;酯化和缩聚的工艺与改性前基本一致,即适合现有生产装置的不同流程和规模。
63.步骤3:缩聚后得到的熔体即为原位聚合改性后的聚对苯二甲酸乙二醇酯的熔体。
64.本实施例的分散剂为磷酸盐,具体为三聚磷酸钾,添加量为聚合碳和硫酸钡总量的3%wt。在步骤2的混合浆料中对苯二甲酸与乙二醇的质量比例为1:1.17,混合浆料还含有催化剂,催化剂为0.28%wt的锑系催化剂或0.001%wt的钛系催化剂。
65.实施例3:
66.本超低热收缩率聚酯短纤维的制备方法,包括:
67.将经过原位聚合改性后的聚对苯二甲酸乙二醇酯的熔体输送至纺丝箱体,计量并挤出,骤冷成丝条,丝条再经过1200m/min速度的纺丝,在相对湿度为65rh%、温度为24℃的环境条件下平衡24小时以上,集束后再对丝条进行拉伸、卷曲并在215℃高温、40分钟长时间条件下,采用金属热辊并增设远红外热量辐射装置对丝条进行处理,之后,切断成为短纤维,该短纤维为超低热收缩率聚酯短纤维。
68.其中原位聚合改性后的聚对苯二甲酸乙二醇酯内包含原位聚合改性剂,所述原位聚合改性剂包括两种,其一为纳米级的聚合碳,一种非结晶碳结构材料,由呋喃树脂高温热解炭化制得。也称玻璃碳,其结构不同于石墨,虽然含有微晶层型结构,但不排成行,整体是无定形碳,但形成聚合物的有节结构。本实施例所采用的是超细粉末微颗粒,其平均粒径为800nm,添加量为聚对苯二甲酸乙二醇酯的2%wt。其二为超细粉末硫酸钡,其平均粒径为1000nm,添加量为对苯二甲酸乙二醇酯的1.6%wt。
69.原位聚合改性后的聚对苯二甲酸乙二醇酯的制备方法为:
70.步骤1:对上述原位聚合改性剂进行原位聚合的前处理,将聚合碳及硫酸钡在分散剂三聚磷酸钾的存在下,与乙二醇调配成悬浮液,悬浮液的浓度为35%wt,悬浮液储存于有搅拌的、夹套保温的储槽内,储槽内的悬浮液温度为70℃。
71.步骤2:将含有对苯二甲酸与乙二醇的混合浆料送入酯化釜进行酯化反应,酯化产物通过齐聚物管线送入缩聚釜进行缩聚反应,同时,悬浮液计量注入齐聚物管线;酯化和缩聚的工艺与改性前基本一致,即适合现有生产装置的不同流程和规模。
72.步骤3:缩聚后得到的熔体即为原位聚合改性后的聚对苯二甲酸乙二醇酯的熔体。
73.本实施例的分散剂为磷酸盐,具体为三聚磷酸钾,添加量为聚合碳和硫酸钡总量的2%wt。在步骤2的混合浆料中对苯二甲酸与乙二醇的质量比例为1:1.15,混合浆料还含有催化剂和0.4%wt的消光剂,催化剂为0.23%wt的锑系催化剂或0.0008%wt的钛系催化剂。
74.以上实施例均具有以下特点:
75.上述原位聚合改性剂不参与酯化与缩聚的高分子合成反应,也不影响聚对苯二甲酸乙二醇酯酯化、缩聚钛系、锑系催化剂的催化效果,这些原位聚合改性剂能够稳定地、均匀地分布于高聚物熔融体内。
76.经过改性后的熔融体其流动性能并没有改变,也不影响熔体过滤器的使用工况,不需要特意调整熔体输送工艺条件。
77.经过纺丝和高速拉伸后的聚酯初生纤维已经具有了各向异性的特点,延纤维轴方向的大分子出现部分取向,这些现象出现会造成集束后再拉伸过程的不稳定并造成最终纤维收缩率的不均匀,因此需要在基本稳定的环境,相对湿度60
±
10rh%、温度24~28℃条件下平衡至少24小时,使得纤维的大分子取向度从20%,下降到小于5%。
78.已经含有原位聚合改性剂的初生纤维与普通的聚酯初生纤维相比,具有更好的导热性和易结晶性特点,可适合3~4倍的机械拉伸,使纤维的拉伸取向程度大幅度提高,并使大分子在后续的热定型过程中更容易砌入晶格形成结晶,这个特点无论对是否添加传统的二氧化钛消光剂都有相同的结果。
79.当经过拉伸纤维内的大分子具有高度取向,并诱导形成部分结晶,通过进一步施以热量以消除晶区外由于高度取向形成的大分子内应力,是降低最终纤维轴方向的热收缩率的重要步骤。由于聚对苯二甲酸乙二醇酯的热传导能力低,金属热辊或热风的热量传递速度受到丝片层的阻碍,造成纤维在不同丝片中得到的热量以及时间不同而造成不均匀,因此传统的后处理工艺,无论是丝束在有张力条件下或无张力条件下的高温差以提高传导速度的热定型难以满足纤维收缩率小于2%的结果。本发明纤维内的原位聚合改性剂都具备了良好的热传导性能,大大改善了纤维之间的热传导效率,因此可以在现有传统的聚酯纤维后处理装置上减少纤维热收缩率的差异。间接地,也可从纤维的拉伸强度的均匀性得到证实。
80.采用远红外加热丝束是弥补现有热定型装备条件下进一步提升加热温度的手段,石英红外灯最大光发射出现在大约1100-1200nm波段范围,但聚对苯二甲酸乙二醇酯在500-2000nm区域吸收能量较差,因此,本实施例所述的原位聚合改性剂,尤其是聚合碳的存在,大大提高了对石英远红外灯发射能量的接受范围。因此,在现有的生产线上,可以在采用热辊式进张热定型工艺的丝束卷曲以后用对丝束进一步红外线辐射加热;也可以在采用松弛热定型工艺的热风定型设备之后增设远红外辐射加热,以进一步对丝片加热。丝片表面温度达到190~240℃,并根据丝片表面温度,加热时间为30~20分钟。
81.表1为实施例4-7、对比例1-2的主要工艺。表2为实施例4-7、对比例1-2分别制备的纤维质量结果。实施例4-7与实施例1-3的超低热收缩率聚酯短纤维的制备方法相同,仅仅是主要的工艺参数不同,不同的工艺参数均在表1中列出。
82.对比例1的纤维主要制备过程为:在含有对苯二甲酸、乙二醇、催化剂的混合浆料中计量注入硫酸钡和分散剂,之后送入酯化釜进行酯化反应,酯化产物通过齐聚物管线送
入缩聚釜进行缩聚反应;缩聚后得到的聚对苯二甲酸乙二醇酯的熔体经过纺丝、平衡、拉伸、热定型等形成。其中硫酸钡的添加量为聚对苯二甲酸乙二醇酯的0.2%wt,分散剂的添加量为聚对苯二甲酸乙二醇酯的2%wt,混合浆料中,催化剂为锑系催化剂,占0.025%wt。其余主要工艺参数参见表1。
83.对比例2的纤维主要制备过程为:将含有对苯二甲酸、乙二醇、催化剂、消光剂的混合浆料送入酯化釜进行酯化反应,酯化产物通过齐聚物管线送入缩聚釜进行缩聚反应;缩聚后得到的聚对苯二甲酸乙二醇酯的熔体经过纺丝、平衡、拉伸、热定型等形成。混合浆料中,消光剂占0.4%wt,催化剂为钛系催化剂,占0.001%wt。其余主要工艺参数参见表1。
84.表1为实施例4-7、对比例1-2的主要工艺:
85.[0086][0087]
表2为实施例4-7、对比例1-2制备的纤维质量结果:
[0088][0089][0090]
由以上表格内容可知,本发明适用聚对苯二甲酸乙二醇酯单纤维线密度为0.88~
9.99detx,在180
±
1℃、0.075
±
0.0075cn/dtex、30分钟测得干热收缩率可控制在0.1~1.0%范围内。其余卷曲性能和物理机械性能均符合涤纶短纤维各品种相应的国家(gb/t 14464涤纶短纤维)、团体(行业)标准(fz/t 52005缝纫线用涤纶短纤维)等的优级品技术要求。
[0091]
本发明的保护范围包括但不限于以上实施方式,本发明的保护范围以权利要求书为准,任何对本技术做出的本领域的技术人员容易想到的替换、变形、改进均落入本发明的保护范围。