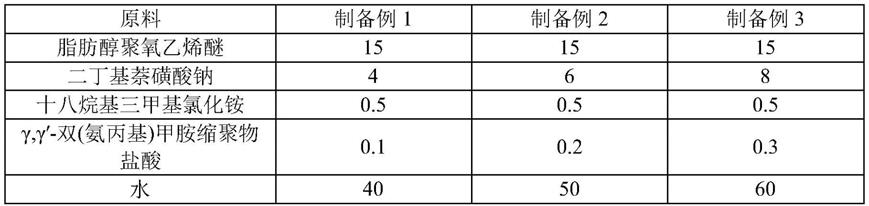
1.本技术涉及再生纤维领域,更具体地说,它涉及一种环保再生原液着色纤维及其制备方法。
背景技术:2.纤维是纺织生产的基础原料,随着纤维消耗量的不断增加,种植生产传统天然纤维的产量已经不足以满足纺织生产的需求,为了满足生产中纤维的使用量,人们发明出再生纤维。再生纤维的资源丰富、吸湿性和透气型优异、手感柔软、悬垂性好,可较大程度代替传统天然纤维,既满足了纺织生产的使用,又具有一定的环保效果。
3.再生纤维主要是以木材、竹、麻、棉短绒、芦苇等纤维素为原料,经过蒸煮、酸处理、漂白、抄浆、脱水等制备方法制备得到,其包括再生纤维素纤维和再生蛋白质纤维。
4.其中,再生纤维素纤维需要经染色后,可得到不同颜色的布料,而原液着色法是再生纤维较为常用的染色法之一。原液着色技术是指在纤维素原液中加入适当的着色剂进行纺丝,直接制成有色纤维的技术。与传统的染色工艺相比,原液着色技术省略了纤维产品的染色环节,有效降低了纤维色丝的生产成本,减少水和能源的消耗,达到环保的效果。但是,由于再生纤维需要在碱性条件进行溶解着色,再生纤维表面会带有一定量的负电荷,而着色剂同样带有一定的负电荷,最终导致再生纤维的上染率较低,色牢度较差。
5.相关技术中,在纺丝溶液加入着色剂的同时,加入阳离子改性剂以提高再生纤维的上染率和色牢度,但阳离子改性剂的渗透性较差,主要在纤维表层,虽提高了上染率,但色牢度依旧较差,依旧导致再生纤维的整体着色性能较弱。
技术实现要素:6.为了提高再生原液着色纤维的着色性能,本技术提供了一种环保再生原液着色纤维及其制备方法。
7.第一方面,本技术提供一种环保再生原液着色纤维,其采用如下技术方案:一种环保再生原液着色纤维,其包括如下重量份的原料:所述再生原液着色纤维包括纤维素原液和色浆,两者的体积比为(100-1000);所述纤维素原液包括如下重量份的原料:纤维素浆粕35-45份、咪唑类离子液体80-90份、没食子酸丙酯5-10份、三水合四丁基氟化铵4-6份、二甲基亚砜8-10份、纤维活化剂11-15份;所述色浆包括如下重量份的原料:活性染料5-15份、磺化琥珀酸二辛酯钠盐0.5-1份、四氢噻吩砜0.1-0.25份、聚羧酸盐类分散剂0.01-0.05份、磷酸氢钠0.01-0.05份、复合固色剂0.5-0.7份、水30-50份。
8.进一步的,纤维素浆粕为木浆粕、棉浆粕、甘蔗渣浆粕、竹浆粕、秸秆浆粕和麻浆粕中的至少一种。
9.进一步的,咪唑类离子液体为1-乙基-3-甲基咪唑磷酸二乙酯,且1-乙基-3-甲基咪唑磷酸二乙酯在25℃下黏度1250mpa
·
s,密度为1.157g/cm3。
10.通过采用上述技术方案,采用咪唑类离子液体溶解纤维素浆粕,具有熔点低、高稳定性、低蒸气压和溶解性能好等优点。咪唑类离子液体是由阴、阳离子构成的液态盐,其高浓度的氯离子与纤维素浆粕的纤维素大分子上的羟键形成氢键,从而破坏了纤维素分子间或分子内的氢键作用,最终达到溶解纤维素浆粕的作用,是溶解纤维素效果较好的一类离子液体。
11.没食子酸丙酯可减少纤维在离子液体中的降解,弥补咪唑类离子液体溶解纤维素浆粕会造成纤维降解的缺陷。三水合四丁基氟化铵的加入,既具有溶解纤维素的作用,又可以改善离子液体高粘度所带来的流动问题。三水合四丁基氟化铵与咪唑离子液体同时加入可达到协同增效的效果,提高纤维素浆粕在咪唑类离子液体中的溶解度。
12.二甲基亚砜作为辅助溶剂加入,与咪唑类离子液体具有较高的相容性,其自身也具有较强的溶解能力,可降低离子液体的粘度,改善活性离子的质量传递,从而提高离子液体的溶解能力,加快纤维素在咪唑类离子液体中的溶解速度。
13.通过加入纤维活化剂,以对纤维素浆粕进行活化改性,增加纤维活性表面积,改善微孔结构,促进其余原料的渗透、扩散和润胀,得到改性的再生纤维素纤维,使再生原液着色纤维表现出较高的匀染性和透染性,且具有较高的色牢度,提升了再生原液着色纤维的着色性能。
14.磺化琥珀酸二辛酯钠盐作为渗透剂加入,其易溶于水,具有优良的渗透性、润湿性和乳化起泡性,可显著降低水的表面张力,有利于色浆的调制;另外,磺化琥珀酸二辛酯钠盐可去除纤维表面的浮色,提高再生原液着色纤维的色牢度。
15.四氢噻吩砜作为助溶剂加入,可提高色浆的浓度,促进活性染料在色浆中的溶解。聚羧酸盐类分散剂的加入,可避免活性染料在染色中的凝聚和沉淀,提高色浆体系的分散稳定性。磷酸氢钠作为稳定剂加入可辅助溶解水性染料,使色浆呈微碱性,可提高色浆的给色量和皂洗牢度,提高再生原液着色纤维的上染率和色牢度。
16.复合固色剂可使再生原液着色纤维和色浆之间形成不溶性的色淀,提高了色浆对纤维染色后的固色作用,提高再生原液着色纤维的色牢度。
17.作为优选:所述纤维活化剂与纤维素浆粕的重量份配比为1:(2.8-3.2);复合固色剂与活性染料的重量份配比为1:(10-20)。
18.通过采用上述技术方案,调节纤维活化剂与纤维素浆粕的重量份配比,更有利于提高纤维素活性表面积,改善微孔结构,更有利于促进其余原料渗透至纤维内部,提高纤维素浆粕的溶解性。
19.调节复合固色剂和活性染料的重量份配比,提高再生原液着色纤维的耐湿色牢度、摩擦色牢度以及日晒色牢度,提高再生原液着色纤维的着色性能。
20.作为优选:所述纤维活化剂包括如下重量份原料:脂肪醇聚氧乙烯醚15-30份、二丁基萘磺酸钠4-8份、十八烷基三甲基氯化铵0.3-0.7份、γ,γ
′‑
双(氨丙基)甲胺缩聚物盐酸0.1-0.3份、水40-60份。
21.通过采用上述技术方案,脂肪醇聚氧乙烯醚为非离子型渗透剂,其润湿渗透性良好,将其自身的醚键引至纤维素分子链上,使纤维素大分子链之间的相互作用力减少,堆砌密度下降,结构更加疏松,从而改善再生原液着色纤维的吸附性,可增强再生原液着色纤维的防静电、抗紫外线性,有效去除再生原液着色纤维表面的蜡质、果胶等杂质,提高氧漂效
果,对色浆具有良好的匀染分散作用。
22.二丁基萘磺酸钠易溶于水,可降低水的表面张力,促使色浆润湿纤维表面,并使色浆渗透再生原液着色纤维内部,具有优良的渗透力和润湿性,具有耐酸、耐碱、耐硬水、乳化和低温流动性好等优点;另外,其与脂肪醇聚氧乙烯醚同时加入具有协同增效的作用,可提高再生原液着色纤维的上染率、匀染性和色牢度。
23.十八烷基三甲基氯化铵是一种阳离子柔软剂,其与脂肪醇聚氧乙烯醚同时使用,可提高纤维活化剂的渗透性,更有利于活化纤维素,提高再生原液着色纤维的着色性能;同时,其可提高再生原液着色纤维的耐拉伸和摩擦能力,改善再生原液着色纤维弹性。
24.γ,γ
′‑
双(氨丙基)甲胺缩聚物盐酸作为交联剂加入,可与纤维中的羟基发生化学键合;同时,γ,γ
′‑
双(氨丙基)甲胺缩聚物盐酸键合后的另一端还可与活性染料的可交联基团羟乙基进行键合,从而使活性染料分子吸附在纤维上,提高活性染料的色牢度;同时,γ,γ
′‑
双(氨丙基)甲胺缩聚物盐酸还可与复合固色剂中的氯乙酸甲酯形成网状结构的坚牢膜层,提高色牢度。
25.作为优选:所述十八烷基三甲基氯化铵与脂肪醇聚氧乙烯醚的重量份配比为1:(30-50)。
26.通过采用上述技术方案,调节十八烷基三甲基氯化铵与脂肪醇聚氧乙烯醚的重量份配比,更有利于提高再生原液着色纤维的着色性能。
27.作为优选:所述复合固色剂包括如下重量份原料:聚二甲基二烯丙基氯化铵3-7份、聚氨酯湿摩擦牢度提升剂0.2-0.3份、阳离子型有机氟硅增深剂1-3份、氰乙酸甲酯2-4份、烷基苯并咪唑磺酸盐1-3份、无水乙醇2-4份、水10-30份。
28.通过采用上述技术方案,聚二甲基二烯丙基氯化铵分子中含有双键和阳离子季铵基团,季铵盐的离子性较强,可与活性染料形成色淀,降低染料的水溶性,提高色牢度。
29.聚氨酯湿摩擦牢度提升剂,可在纤维表面形成一层连续的光滑薄膜,将染料覆盖在膜下,其大分子上的活性基团可在一定条件下与纤维和染料发生共价键结合,从而提高再生原液着色纤维的湿摩擦色牢度,进一步弥补聚二甲基二烯丙基氯化铵湿摩擦色牢度较差的缺陷,从而提高再生原液着色纤维的着色性能。
30.阳离子型有机氟硅增深剂可提高纤维和染料的亲和力,使色浆更易渗透至再生原液着色纤维内部;同时,阳离子型有机氟硅增深剂还可改善活性色浆的溶解性能,从而对活性染料具有增深作用。
31.氰乙酸甲酯作为黏合剂加入,使水性染料与再生原液着色纤维之间粘结,提升再生原液着色纤维耐摩擦和皂洗的色牢度;同时,其还可与纤维活化剂中的γ,γ
′‑
双(氨丙基)甲胺缩聚物盐酸具有协同增效作用,烷基苯并咪唑磺酸盐作为匀染剂加入,在纤维染色中可减缓活性染料上染纤维的速率,并能使染料在纤维上从深色出移至浅色处,提高再生原液着色纤维的匀染性。
32.作为优选:所述复合固色剂通过以下步骤制备得到:将氰乙酸甲酯与无水乙醇混合,充分溶解,备用;将聚二甲基二烯丙基氯化铵、聚氨酯湿摩擦牢度提升剂、阳离子型有机氟硅增深剂和烷基苯并咪唑磺酸盐依次加至水中混合,搅拌均匀,搅拌的同时加入溶解后的氰乙酸甲酯混合,搅拌均匀,即得复合固色剂。
33.通过采用上述技术方案,先将氰乙酸甲酯与无水乙醇混合,使氰乙酸甲酯溶解,避免直接加入氰乙酸甲酯出现沉淀等分散不均匀的现象。最后加入氰乙酸甲酯,利于复合固色剂各原料的分散,提高再生原液着色纤维的色牢度。
34.作为优选:所述聚氨酯湿摩擦牢度提升剂与聚二甲基二烯丙基氯化铵的重量份配比为1:(20-25)。
35.通过采用上述技术方案,调节聚氨酯湿摩擦牢度提升剂与聚二甲基二烯丙基氯化铵的重量份配比,可提高再生原液着色纤维的色牢度。
36.作为优选:所述纤维素浆粕中纤维素的平均聚合度为500-700。
37.通过采用上述技术方案,纤维素浆粕的聚合度要分布均匀,且保持在500-700,聚合度过低,制备得到的再生原液着色纤维质量低劣,降低再生原液着色纤维的拉伸强度和断裂伸长率;聚合度过高,纤维素原液的粘度会增大,影响纤维溶解性,从而影响后期处理过滤和染色。本技术将聚合度控制在500-700,可提高纤维溶解性和再生原液着色纤维的着色性能。
38.第二方面,本技术提供一种环保再生原液着色纤维的制备方法,具体通过以下技术方案得以实现:一种环保再生原液着色纤维的制备方法,其包括以下操作步骤:制备纤维素原液;制备色浆;将色浆与纤维素原液按配比混合,搅拌均匀,静置,过滤,脱泡,得到混合物a;将混合物a进行湿法纺丝,拉伸,塑化定性,得到纤维素长丝;将纤维素长丝水洗,皂洗,烘干,上油,烘干,即得原液着色纤维。
39.进一步的,所述制备纤维素原液的具体操作步骤为:将纤维素浆粕、没食子酸丙酯、三水合四丁基氟化铵、二甲基亚砜和纤维活化剂加入咪唑类离子液体中混合,搅拌均匀后,依次经过浸渍,压榨,粉碎,得到纤维素原液。
40.所述制备色浆的具体操作步骤为:将活性染料、磺化琥珀酸二辛酯钠盐、四氢噻吩砜、聚羧酸盐类分散剂、磷酸氢钠和复合固色剂加入至水中,混合均匀得到色浆。
41.进一步的,所述色浆制备中,将所述活性染料先粉碎至200-300nm粒径,再与色浆其余原料混合均匀,即得色浆。
42.所述脱泡在0.004-0.01mpa、80-90℃条件下进行。
43.所述水洗的水温为20-60℃。
44.所述皂洗是在70-80℃条件下将水洗后的纤维素长丝用酸性皂洗剂皂洗2-5min,所述酸性皂洗剂为脂肪胺聚氧乙烯醚单季铵盐;所述酸性皂洗剂用量为7-9g/l。
45.通过采用上述技术方案,在色浆制备中,将活性染料的粒径粉碎至200-300nm,可提高水性染料的上染率和固色率。
46.原液着色的工艺更易在制备过程中产生气泡,为保证再生原液着色纤维的生产品质,需要进行脱泡处理,以脱出原料中的空气。而且,脱泡质量同样关系着再生原液着色纤维的着色效果。
47.将水洗的水温控制在20-60℃,水温过低水洗不够彻底,水温过高易破坏纤维表面的固色层。
48.通过控制皂洗的条件,有效去除活性染料对再生原液着色纤维染色后纤维中的浮色,减少纤维水洗的次数,同时提高再生原液着色纤维的色牢度。且在皂洗中选用酸性皂洗剂,省去了酸洗的步骤,节约了工艺成本和能耗。选用脂肪胺聚氧乙烯醚单季铵盐作为酸性皂洗剂,改善了皂洗剂的防沾色性能,可进一步提高再生原液着色纤维的色牢度。
49.综上所述,本技术包括以下至少一种有益技术效果:(1)本技术通过控制环保再生原液着色纤维中各原料的种类和掺量,使再生原液着色纤维的干摩擦牢度、湿摩擦牢度、色泽均匀度、耐水洗色牢度、耐汗渍色牢度、耐皂洗色牢度、断裂强度分别为3-4级、3级、3级、3-4级、3级、3-4级和2.42cn/dtex,弹性模量为6.30gpa,表面为较为优异的着色性能和力学性能。
50.(2)本技术通过调控纤维素原液中纤维活化剂与纤维素浆粕的重量份配比,使再生原液着色纤维的湿摩擦牢度和断裂强度分别为3-4级和2.55cn/dtex,弹性模量为6.15gpa,进一步提高了再生原液着色纤维的色泽均匀度和力学性能。
51.(3)本技术通过调控色浆中复合固色剂与活性染料的重量份配比,使再生原液着色纤维的干摩擦牢度、湿摩擦牢度、色泽均匀度、耐水洗色牢度、耐汗渍色牢度、耐皂洗色牢度、断裂强度分别达到4级、4级、3-4级、4级、3-4级、4级和2.60cn/dtex,弹性模量为5.99gpa,提高了再生原液着色纤维的着色性能。
52.(4)本技术通过调控纤维活化剂原料中十八烷基三甲基氯化铵与脂肪醇聚氧乙烯醚的重量份配比为1:40,以及色浆原料中聚氨酯湿摩擦牢度提升剂与聚二甲基二烯丙基氯化铵的重量份配比为1:23,使再生原液着色纤维的耐水洗色牢度、断裂强度分别达到4级和2.65cn/dtex,弹性模量为5.80gpa,进一步提高了再生原液着色纤维的着色性能。
53.(5)本技术通过调控活性染料的粒径、纤维素浆粕的聚合度和皂洗的条件,最终使再生原液着色纤维的干摩擦牢度、湿摩擦牢度、色泽均匀度、耐水洗色牢度、耐汗渍色牢度、耐皂洗色牢度、断裂强度分别达到4-5级、5级、4-5级、4-5级、5级、5级和3.85cn/dtex,弹性模量为5.68gpa,使再生原液着色纤维具有较为优异的着色性能。
具体实施方式
54.以下结合具体实施例对本技术作进一步详细说明。
55.本技术中的如下各原料均为市售产品,均为使本技术的各原料得以公开充分,不应当理解为对原料的来源产生限制作用。具体为:纤维素浆粕的平均聚合度为500-700,甲纤含量≥92.0%,水分≤10%;咪唑类离子液体选自武汉卡米克科技有限公司的1-乙基-3-甲基咪唑磷酸二乙酯,黏度为1250mpa
·
s,密度为1.157g/cm3;活性染料选自邢台振方商贸有限公司,型号为037;聚羧酸盐类分散剂选自山东邦普进出口有限公司,型号为bp-8044;脂肪醇聚氧乙烯醚选自济南硕鼎商贸有限公司;γ,γ
′‑
双(氨丙基)甲胺缩聚物盐酸,型号为交联剂fh;聚二甲基二烯丙基氯化铵选自齐河县聚安环保科技有限公司;聚氨酯湿摩擦牢度提升剂选自上海德缘化工有限公司,型号为dy555;阳离子型有机氟硅增深剂选自上海绿铜物资有限公司,型号为lt-418f;烷基苯并咪唑磺酸盐选自广州恩源化工科技有限公司;脂肪胺聚氧乙烯醚单季铵盐选自常州市骏鑫塑化有限公司,型号为1815。
56.以下为本技术中纤维活化剂的制备例:制备例1
本技术中的纤维活化剂,通过如下方法制备得到:按照表1的掺量,将脂肪醇聚氧乙烯醚、二丁基萘磺酸钠、十八烷基三甲基氯化铵和γ,γ
′‑
双(氨丙基)甲胺缩聚物盐酸加至水中混合,搅拌均匀,即得纤维活化剂。
57.制备例2-3制备例2-3的纤维活化剂与制备例1的制备方法完全相同,区别在于各原料成分不同,具体详见表1所示。
58.表1制备例1-3的纤维活化剂的各原料掺量(单位:kg)制备例4-6制备例4-6的纤维活化剂与制备例2的制备方法完全相同,区别在于各原料成分不同,具体详见表2所示。
59.表2制备例4-6的纤维活化剂的各原料掺量(单位:kg)以下为本技术中复合固色剂的制备例:制备例7本技术中的复合固色剂,通过如下方法制备得到:按照表3的掺量,将聚二甲基二烯丙基氯化铵、聚氨酯湿摩擦牢度提升剂、阳离子型有机氟硅增深剂、氰乙酸甲酯、无水乙醇和烷基苯并咪唑磺酸盐加至水中混合,搅拌均匀,即得复合固色剂。
60.制备例8本技术中的复合固色剂,通过如下方法制备得到:按照表3的掺量,将氰乙酸甲酯与无水乙醇混合,充分溶解,备用;将聚二甲基二烯丙基氯化铵、聚氨酯湿摩擦牢度提升剂、阳离子型有机氟硅增深剂和烷基苯并咪唑磺酸盐依次加至水中混合,搅拌均匀,搅拌的同时加入溶解后的氰乙酸甲酯混合,搅拌均匀,即得复合固色剂。
61.制备例9-10制备例9-10的复合固色剂与制备例8的制备方法完全相同,区别在于各原料成分不同,具体详见表3所示。
62.表3制备例7-10的复合固色剂的各原料掺量(单位:kg)
原料制备例7-8制备例9制备例10聚二甲基二烯丙基氯化钠555聚氨酯湿摩擦牢度提升剂0.30.30.3阳离子型有机氟硅增深剂123氰乙酸甲酯234烷基苯并咪唑磺酸盐123无水乙醇234水102030制备例11-14制备例11-14的复合固色剂与制备例9的制备方法完全相同,区别在于各原料成分不同,具体详见表4所示。
63.表4制备例11-14的复合固色剂的各原料掺量(单位:kg)原料制备例11制备例12制备例13制备例14聚二甲基二烯丙基氯化钠6573聚氨酯湿摩擦牢度提升剂0.30.220.280.2阳离子型有机氟硅增深剂2222氰乙酸甲酯3333烷基苯并咪唑磺酸盐2222无水乙醇3333水20202020实施例1实施例1的环保再生原液着色纤维通过如下操作步骤而得:按照表5的掺量,制备纤维素原液:将纤维素浆粕(平均聚合度为700)、没食子酸丙酯、三水合四丁基氟化铵、二甲基亚砜和制备例1制备的纤维活化剂加入咪唑类离子液体中混合,搅拌均匀后,依次经过浸渍,压榨,粉碎,得到纤维素原液;按照表6的掺量,制备色浆:将活性染料同磺化琥珀酸二辛酯钠盐、四氢噻吩砜、聚羧酸盐类分散剂、磷酸氢钠和制备例7制备的复合固色剂一起加入至水中,混合均匀得到色浆;将色浆与纤维素原液按体积比1:500的比例混合,搅拌均匀,130℃条件静置30min,过滤,在0.004mpa、80℃条件下脱泡,得到混合物a;将混合物a进行湿法纺丝,拉伸,塑化定性,得到纤维素长丝;将纤维素长丝在60℃水洗,在80℃条件下用皂洗剂皂洗2min,用量为8g/l,烘干,上油,烘干,即得原液着色纤维。
64.实施例2-5实施例2-5的环保再生原液着色纤维与实施例1的制备方法及原料种类完全相同,区别在于各原料掺量不同,具体详见表5和表6所示。
65.表5实施例1-5环保再生原液着色纤维中纤维素原液的各原料掺量(单位:kg)
表6实施例1-5环保再生原液着色纤维中色浆的各原料掺量(单位:kg)原料实施例1实施例2实施例3实施例4实施例5活性染料1010101010磺化琥珀酸二辛酯钠盐0.50.70.80.91四氢噻吩砜0.10.140.180.220.25聚羧酸盐类分散剂0.010.020.030.040.05磷酸氢钠0.010.020.030.040.05复合固色剂0.60.60.60.60.6水3035404550实施例6-9实施例6-9的环保再生原液着色纤维与实施例3的制备方法及原料种类完全相同,区别在于纤维素原液中的各原料掺量不同,具体详见表7所示。
66.表7实施例6-9环保再生原液着色纤维中纤维素原液的各原料掺量(单位:kg)原料实施例6实施例7实施例8实施例9纤维素浆粕424535.235咪唑类离子液体86868686没食子酸丙酯8888三水合四丁基氟化铵5555二甲基亚砜9999纤维活化剂15151113.5实施例10-13实施例10-13的环保再生原液着色纤维与实施例7的制备方法及原料种类完全相同,区别在于色浆各原料掺量不同,具体详见表8所示。
67.表8实施例10-13环保再生原液着色纤维中色浆的各原料掺量(单位:kg)原料实施例10实施例11实施例12实施例13活性染料59105.6磺化琥珀酸二辛酯钠盐0.80.80.80.8四氢噻吩砜0.180.180.180.18聚羧酸盐类分散剂0.030.030.030.03磷酸氢钠0.030.030.030.03复合固色剂0.50.60.50.7水40404040
实施例14-18实施例14-19的环保再生原液着色纤维与实施例11的制备方法完全相同,区别在于实施例14-18选用制备2-6制备的纤维活化剂,其余原料种类和掺量与实施例11相同。
68.实施例19-25实施例19-25的环保再生原液着色纤维与实施例17的制备方法完全相同,区别在于实施例19-25选用制备8-14制备的复合固色剂,其余原料种类和掺量与实施例17相同。
69.实施例26实施例26的环保再生原液着色纤维与实施例23的原料种类和掺量完全相同,区别在于:制备方法中活性染料粉碎至250nm,其他制备方法与实施例23相同。
70.实施例27实施例27的环保再生原液着色纤维与实施例23的原料种类和掺量完全相同,区别在于:制备方法中活性染料粉碎至300nm,其他制备方法与实施例23相同。
71.实施例28实施例28的环保再生原液着色纤维与实施例27的原料种类和掺量完全相同,区别在于:制备方法中在80℃下用酸性皂洗剂皂洗3min,酸性皂洗剂选用脂肪胺聚氧乙烯醚单季铵盐,其他制备方法与实施例27相同。
72.实施例29实施例29的环保再生原液着色纤维与实施例27的原料种类和掺量完全相同,区别在于:制备方法中在80℃下用酸性皂洗剂皂洗5min,酸性皂洗剂选用脂肪胺聚氧乙烯醚单季铵盐,其他制备方法与实施例27相同。
73.实施例30实施例30的环保再生原液着色纤维与实施例28的制备方法完全相同,区别在于纤维活化剂选用15kg的壬基酚聚氧乙烯醚,复合固色剂选用0.3kg氨三乙酸三钠和0.3kg磷酸三钠,其他原料种类及掺量与实施例28相同。
74.实施例31实施例31的环保再生原液着色纤维与实施例30的制备方法和原料掺量完全相同,区别在于纤维素浆粕的平均聚合度为800,其他原料种类与实施例30不同。
75.实施例32实施例32的环保再生原液着色纤维与实施例30的制备方法和原料掺量完全相同,区别在于纤维素浆粕的平均聚合度为500,其他原料种类与实施例30不同。
76.对比例1对比例1的环保再生原液着色纤维与实施例1的制备方法完全相同,区别在于:色浆中未添加磺化琥珀酸二辛酯钠盐,其余原料及掺量与实施例1相同。
77.对比例2对比例2的环保再生原液着色纤维与实施例1的制备方法完全相同,区别在于:色浆中未添加四氢噻吩砜,其余原料及掺量与实施例1相同。
78.对比例3对比例3的环保再生原液着色纤维与实施例1的制备方法完全相同,区别在于:色浆中未添加聚羧酸盐类分散剂,其余原料及掺量与实施例1相同。
79.对比例4对比例4的环保再生原液着色纤维与实施例1的制备方法完全相同,区别在于:色浆中未添加磷酸氢钠,其余原料及掺量与实施例1相同。
80.性能检测采用如下检测标准或方法分别对不同的实施例1-32和对比例1-4进行性能检测,检测结果详见表9。
81.干摩擦牢度、湿摩擦牢度:采用gb/t 3920-2008《纺织品.色牢度试验.耐摩擦色牢度》测定环保再生原液着色纤维的干摩擦牢度和湿摩擦牢度。
82.色泽均匀度:采用gb/t 6508-2001《涤纶长丝染色均匀度试验方法》测定环保再生原液着色纤维的色泽均匀度。
83.耐皂洗色牢度:采用gb/t3921 2008《纺织品色牢度试验耐皂洗色牢度》测定环保再生原液着色纤维的皂洗色牢度。
84.耐水洗色牢度:采用aatcc 61:2010《纺织品耐水洗色牢度》的方法测定环保再生纤维素的皂洗色牢度。
85.耐汗渍色牢度:采用gb/t7568.2-2008《纺织品色牢度试验耐汗渍色牢度》测定环保再生原液着色纤维的耐汗渍色牢度。
86.断裂强度:采用gb/t 14344-2008《化学纤维长丝拉伸性能试验方法》测定环保再生原液着色纤维的断裂强度。
87.弹性模量:采用gb/t 3362-2005《碳纤维复丝拉伸性能试验方法》测定环保再生原液着色纤维的抗张弹性模量。
88.表9不同环保再生原液着色纤维的性能检测结果
由表9的检测结果表明,本技术中得到的环保再生原液着色纤维的干摩擦牢度、湿摩擦牢度、耐水洗色牢度、耐汗渍色牢度、耐皂洗色牢度和色泽均匀度分别为3-4~4-5级、3~5级、3~4-5级、3~5级、3~5级和3~4-5级,提高了再生原液着色纤维的色牢度;同时,本技术得到的环保再生原液着色纤维在提高色牢度的同时,再生原液着色纤维的断裂强度和弹性模量最优分别为3.85cn/dtex和5.68gpa,具有较为优异的力学性能,同时具有较高的柔软度。
89.实施例1-5中,实施例3环保再生原液着色纤维的耐水洗色牢度、耐皂洗牢度、断裂强度分别为3-4级、3-4级、3-4级和2.42cn/dtex,均高于实施例1-2和实施例4-5;而且,实施例3环保再生原液着色纤维的弹性模量为6.30gpa,均低于实施例1-2和实施例4-5。表明实施例3纤维素原液的原料中咪唑类离子液体、没食子酸内脂、三水合四丁基氟化铵、二甲基亚砜以及色浆原料中磺化琥珀酸二辛酯钠盐、四氢噻吩砜、聚羧酸盐类分散剂和磷酸氢钠的重量份较为合适,环保再生原液着色纤维具有较高的色牢度和力学性能。
90.实施例6-9中,实施例7环保再生原液着色纤维的湿摩擦牢度、断裂强度分别为3-4级和2.55cn/dtex,均高于实施例6和实施例8-9;而且,实施例7环保再生原液着色纤维的弹性模量为6.15gpa,均低于实施例6和实施例8-9。表明当纤维素原液中纤维活化剂与纤维素浆粕的重量份配比为1:3时较为合适,表现为较高的湿摩擦牢度和力学性能,可能与纤维活化剂对纤维素浆粕中的纤维进行改性有关。
91.实施例10-13中,实施例11环保再生原液着色纤维的干摩擦牢度、湿摩擦牢度、色泽均匀度、耐水洗色牢度、耐汗渍色牢度、耐皂洗色牢度、断裂强度分别为4级、4级、3-4级、4级、3-4级、4级和2.60cn/dtex,均高于实施例10和实施例12-13;而且,实施例11环保再生原液着色纤维的弹性模量为5.99gpa,均低于实施例10和实施例12-13。表明当色浆中复合固色剂与活性染料的重量份配比为1:15时较为合适,表现为较高的湿摩擦牢度和力学性能,可能与复合固色剂提高了色浆在纤维的固色性能有关。
92.结合实施例11和实施例14-15可以发现,实施例14环保再生原液着色纤维的断裂强度为2.62cn/dtex,高于实施例11和实施例15;弹性模量为5.95gpa,低于实施例11和实施
例15;表明纤维活性剂原料中二丁基萘磺酸钠、γ,γ
′‑
双(氨丙基)甲胺缩聚物盐酸的重量份较为合适,再生原液着色纤维的色牢度和力学性能表现较为优异。
93.结合实施例14和实施例16-18中,实施例17环保再生原液着色纤维的耐水洗色牢度和断裂强度分别为4级、2.65cn/dtex,均高于实施例14、实施例16和实施例18;同时,弹性模量为5.80gpa,均低于实施例14、实施例16和实施例18;表明当纤维活化剂原料中十八烷基三甲基氯化铵与脂肪醇聚氧乙烯醚的重量份配比为1:40时,再生原液着色纤维的色牢度和力学性能更为优异;可能与十八烷基三甲基氯化铵和脂肪醇聚氧乙烯醚同时使用,可提高纤维活化剂的渗透性,更有利于活化纤维素,提高再生原液着色纤维的着色性能有关。
94.结合实施例19-21可以看出,实施例20环保再生原液着色纤维的断裂强度为2.69cn/dtex,高于实施例19和实施例21;弹性模量为5.76gpa,低于实施例19和实施例21;表明纤维活性剂原料中阳离子型有机氟硅增深剂、氰乙酸甲酯、烷基苯并咪唑磺酸盐和无水乙醇的重量份较为合适,再生原液着色纤维的色牢度和力学性能表现较为优异。
95.实施例22-25中,实施例23环保再生原液着色纤维干摩擦牢度、湿摩擦牢度、耐皂洗色牢度、断裂强度分别为4-5级、5级、5级和2.76cn/dtex,均高于实施例22和实施例24-25;而且,实施例23环保再生原液着色纤维的弹性模量为5.58gpa,均低于实施例22和实施例24-25。表明当复合固色剂中聚氨酯湿摩擦牢度提升剂与聚二甲基二烯丙基氯化铵的重量份配比为1:23时较为合适,表现为较高的湿摩擦牢度和力学性能,可能与聚氨酯湿摩擦牢度提升剂,可在纤维表面形成一层连续的光滑薄膜,弥补聚二甲基二烯丙基氯化铵湿摩擦色牢度较差的缺陷,从而提高再生原液着色纤维的着色性能有关。
96.实施例26-27中,实施例26环保再生原液着色纤维的色泽均匀度、耐汗渍色牢度、断裂强度分别为4-5级、5级和2.80cn/dtex,均高于实施例27;弹性模量为5.50gpa,低于实施例27,表明色浆原料中将活性染料粉碎至250nm粒径时较为合适,提高了再生原液着色纤维的色牢度和力学性能,可能是由于水性染料颗粒的大小可提高水性染料的上染率和固色率有关。
97.实施例28-29中,实施例28环保再生原液着色纤维的断裂强度分别为3.94cn/dtex,均高于实施例29;弹性模量为5.74gpa,低于实施例29,表明脱泡在0.007mpa、90℃时较为合适,提高了再生原液着色纤维的色牢度和力学性能,可能是表明皂洗3min时较为合适,提高了再生原液着色纤维的色牢度和力学性能,可能是由于选用脂肪胺聚氧乙烯醚单季铵盐作为酸性皂洗剂,改善了皂洗剂的防沾色性能,可进一步提高再生原液着色纤维的色牢度。
98.结合实施例28-29和实施例30可以发现,实施例30的环保再生原液着色纤维的着色性能弱于实施例28-29,表明纤维素原液中加入脂肪醇聚氧乙烯醚、二丁基萘磺酸钠、十八烷基三甲基氯化铵和γ,γ
′‑
双(氨丙基)甲胺缩聚物盐酸作为纤维活化剂和色浆中加入聚二甲基二烯丙基氯化铵、聚氨酯湿摩擦牢度提升剂、阳离子型有机氟硅增深剂、氰乙酸甲酯、烷基苯并咪唑磺酸盐和无水乙醇作为复配固色剂,提升了再生原液着色纤维的着色性能。
99.实施例31-32中,实施例32环保再生原液着色纤维的干摩擦牢度、湿摩擦牢度、色泽均匀度、耐水洗色牢度、耐汗渍色牢度、耐皂洗色牢度、断裂强度分别为4-5级、5级、4-5级、4-5级、5级、5级和3.85cn/dtex,均高于实施例33;弹性模量为5.68gpa,低于实施例33,
结合对比例1-4和实施例1的环保再生原液着色纤维性能检测数据发现,在环保再生原液着色纤维原料中加入磺化琥珀酸二辛酯钠盐、四氢噻吩砜、聚羧酸盐类分散剂和磷酸氢钠,均不同程度的提高了再生原液着色纤维的色牢度和力学性能。
100.本具体实施例仅仅是对本技术的解释,其并不是对本技术的限制,本领域技术人员在阅读完本说明书后可以根据需要对本实施例做出没有创造性贡献的修改,但只要在本技术的权利要求范围内都受到专利法的保护。