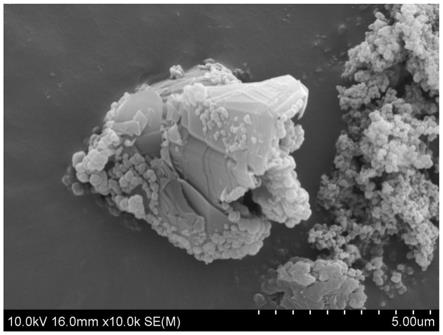
1.本发明属于新材料技术领域,涉及掺杂石墨的聚丙烯腈基纳米复合材料及其制备方法与应用。
背景技术:2.公开该背景技术部分的信息仅仅旨在增加对本发明的总体背景的理解,而不必然被视为承认或以任何形式暗示该信息构成已经成为本领域一般技术人员所公知的现有技术。
3.据发明人研究了解,为了优化碳纤维的结构,通常需要添加碳质材料添加剂,这些添加剂本身有着较为优异的机械性能,可以作为刚性的填料阻碍纤维中裂缝的扩展,且其与纤维基质之间的相互作用有利于基质与填料之间的应力传递,对纤维的强度有增强作用。此外,碳质材料有较为完善的石墨晶格结构,可以在碳纤维制备过程中起到成核剂的作用,诱导纤维内部石墨化晶格结构的形成和完善,不断向上述碳纤维的理想结构靠近。然而,发明人发现,现有碳质材料添加剂一般为石墨烯、碳纳米管等,这些碳质材料添加剂生产工艺复杂、价格过高,难以进行工业化的推广。
技术实现要素:4.为了解决现有技术的不足,本发明在前期研究过程中,采用石墨代替石墨烯、碳纳米管等作为碳质材料添加剂,优化碳纤维的结构,以降低成本,实现工业化的推广。
5.然而,在前期研究中本发明发现,若仅将石墨代替石墨烯、碳纳米管等作为碳质材料添加剂直接引入纺丝体系制备碳纤维或碳纳米纤维,产物的力学性能不仅不会升高,还会下降,这是因为相较之下石墨的尺寸更大,极易在纺丝过程产生团聚,而这种大尺寸添加剂的团聚会降低石墨在纤维基质中的分散性,削弱石墨添加剂与纤维基质之间的相互作用,且容易发展成为最终碳纤维或碳纳米纤维中孔洞、裂纹等缺陷结构,极大地损害纤维的力学性能。
6.为了解决这种问题,本发明的目的是提供掺杂石墨的聚丙烯腈基纳米复合材料及其制备方法与应用,在聚合物制备阶段便将石墨添加剂掺入聚丙烯腈分子间实现均匀分散,将得到的聚丙烯腈/石墨纳米复合材料作为前驱体进行纺丝,以尽可能避免石墨在纤维内的团聚现象。
7.一方面,一种掺杂石墨的聚丙烯腈基纳米复合材料的制备方法,将丙烯腈单体、碳质材料添加剂、引发剂及分子量调节剂混合后加热以引发自由基聚合,即得;所述碳质材料添加剂为石墨,聚合过程中进行机械搅拌及超声处理,所述石墨为鳞片石墨或鳞片石墨的衍生物。
8.本发明在自由基聚合过程中进行机械搅拌及超声处理,通过机械搅拌及超声处理的协同作用,实现石墨在丙烯腈单体间的均匀分散,避免石墨颗粒产生团聚现象,从而在聚合完成后直接实现石墨在聚丙烯腈基质中良好的分散。
9.另一方面,一种掺杂石墨的聚丙烯腈基纳米复合材料,由上述制备方法获得。
10.第三方面,一种上述掺杂石墨的聚丙烯腈基纳米复合材料在制备碳纤维或碳纳米纤维中的应用,通过将上述纳米复合材料溶解后进行凝胶纺丝或静电纺丝,可直接制备均匀分散有石墨的碳纤维或碳纳米纤维。
11.本发明的有益效果为:
12.1.鉴于石墨的尺寸更大,比表面积更小,轻微的团聚便会在最终的碳纤维或碳纳米纤维中发展成为缺陷结构,为了实现石墨添加剂的均匀分散,本发明在制备掺杂石墨的聚丙烯腈基纳米复合材料的过程中采用超声和搅拌相结合的方式,基本实现了石墨的均匀分散,最终得到的复合材料为核壳结构,内核为单一未团聚的石墨或石墨衍生物颗粒,外壳为聚丙烯腈,聚合物外壳隔绝了石墨之间的相互作用,减少其积聚的倾向,有利于实现高浓度石墨的添加。
13.2.本发明中所采用的鳞片石墨来源广泛,价格十分低廉,制备工艺简单,可以根据所需纤维的直径来配合使用相应尺寸的石墨原料,此外,相较于石墨烯和碳纳米管,鳞片石墨有一定的结构刚性,纺丝过程中其在牵伸力的作用下沿纤维轴取向的同时可以保持平面结构,在此基础上诱导纤维基质沿其平面生长出更大的石墨晶格结构,而石墨烯和碳纳米管则容易在纤维基质中扭曲、缠绕,这可能造成纤维中的缺陷结构,需要额外工艺对石墨烯及碳纳米管在纤维基质中的形貌进行控制。因而本发明提供的掺杂石墨的聚丙烯腈基纳米复合材料具有更低的成本及更简易的可操作性。
14.3.本发明所制备的掺杂石墨的聚丙烯腈基纳米复合材料,制备工艺简单,生产效率高,直接实现了聚丙烯腈与石墨的均匀混合,有效避免了二者直接混合情况下因聚丙烯腈分子链缠结造成的石墨分散困难且分散不均匀的情况。
15.4.本发明所制备的掺杂石墨的聚丙烯腈基纳米复合材料可以作为碳纤维的前驱体进行纺丝,将复合材料溶解后直接得到聚丙烯腈与石墨颗粒均匀混合的纺丝溶液,可以通过静电纺丝或溶液纺丝的方法得到均匀掺杂有石墨颗粒的聚丙烯腈基碳纳米纤维或碳纤维,石墨颗粒可以在纤维基质中限制裂缝的扩展,同时石墨颗粒有着与理想碳纤维相同的石墨晶格机构,在预氧化及碳化过程中其可以作为模板诱导纤维基质逐渐转化为与其相同的晶格结构,从而有利于碳纤维综合性能的提升。
附图说明
16.构成本发明的一部分的说明书附图用来提供对本发明的进一步理解,本发明的示意性实施例及其说明用于解释本发明,并不构成对本发明的不当限定。
17.图1为本发明实施例3中水相沉淀聚合所得的聚丙烯腈未完全包覆鳞片石墨的复合颗粒扫描电子显微镜照片。
18.图2为本发明实施例1中水相沉淀聚合所得的聚丙烯腈完全包覆鳞片石墨的复合颗粒扫描电子显微镜照片。
19.图3为本发明实施例4中由实施例2中所得的复合材料制备的鳞片石墨掺杂碳纳米纤维的扫描电子显微镜照片。
20.图4为本发明实施例4中由实施例1、2、3中所得的复合材料制备的鳞片石墨掺杂碳纳米纤维的拉伸应力对比图。
具体实施方式
21.应该指出,以下详细说明都是示例性的,旨在对本发明提供进一步的说明。除非另有指明,本文使用的所有技术和科学术语具有与本发明所属技术领域的普通技术人员通常理解的相同含义。
22.需要注意的是,这里所使用的术语仅是为了描述具体实施方式,而非意图限制根据本发明的示例性实施方式。如在这里所使用的,除非上下文另外明确指出,否则单数形式也意图包括复数形式,此外,还应当理解的是,当在本说明书中使用术语“包含”和/或“包括”时,其指明存在特征、步骤、操作、器件、组件和/或它们的组合。
23.鉴于石墨烯、碳纳米管等作为碳质材料添加剂存在成本较高等问题,本发明提出了提供掺杂石墨的聚丙烯腈基纳米复合材料及其制备方法与应用。
24.本发明的一种典型实施方式,提供了一种掺杂石墨的聚丙烯腈基纳米复合材料的制备方法,将丙烯腈单体、碳质材料添加剂、引发剂及分子量调节剂混合后加热以引发自由基聚合,即得;所述碳质材料添加剂为石墨,聚合过程中进行机械搅拌及超声处理,所述石墨为鳞片石墨或鳞片石墨的衍生物。
25.本发明在加热聚合过程中进行机械搅拌及超声处理,通过机械搅拌及超声处理的协同作用,实现石墨在丙烯腈单体间的均匀分散,避免产生轻微的团聚,团聚的消除可以避免后续制备的石墨掺杂碳纤维或碳纳米纤维中缺陷结构的产生,从而使石墨代替石墨烯、碳纳米管等作为碳质材料添加剂优化碳纤维的结构。
26.本发明所述的鳞片石墨的衍生物是以鳞片石墨为基体的各种衍生物如氧化石墨、可膨胀石墨、氟化石墨等。
27.在一些实施例中,石墨的粒径为0.1~100μm。
28.在一些实施例中,石墨添加量为丙烯腈质量的0.1~5wt%。
29.在一些实施例中,引发剂的添加量为丙烯腈质量的0.01~10wt%。
30.在一些实施例中,采用水相沉淀聚合工艺制备。制备方法更为简单,进一步提高生产效率。
31.在一些实施例中,所述引发剂为过硫酸铵或过硫酸铵-亚硫酸铵复合引发体系。
32.在一些实施例中,聚合温度为40~80℃。聚合时间为60~180min。
33.在一些实施例中,制备步骤包括:
34.将丙烯腈与石墨或石墨的衍生物及分子量调节剂加入到去离子水中,在超声及搅拌的辅助下混合均匀;
35.控制混合均匀的聚合体系温度为40~80℃,滴加引发剂的水溶液引发聚合反应,滴加时间为30~60min,滴加过程中保持超声及搅拌处理;
36.引发剂滴加完之后保温30~120min至反应结束,聚合过程中保持超声及搅拌处理;
37.过滤产物并用去离子水洗涤干净,并于80~100℃下烘干,得到聚丙烯腈/石墨复合材料。
38.本发明的另一种实施方式,提供了一种掺杂石墨的聚丙烯腈基纳米复合材料,由上述制备方法获得。
39.在一些实施例中,产物中聚丙烯腈的分子量为10000~1000000。
40.本发明的第三种实施方式,提供了一种上述掺杂石墨的聚丙烯腈基纳米复合材料在制备碳纤维或碳纳米纤维中的应用。
41.为了使得本领域技术人员能够更加清楚地了解本发明的技术方案,以下将结合具体的实施例详细说明本发明的技术方案。
42.实施例1
43.控制聚合体系温度为50℃,将20ml丙烯腈(占溶液总质量10wt%)、0.02g鳞片石墨(鳞片石墨占总单体含量的0.1wt%)、0.15ml十二硫醇混合均匀,在60min内滴加完10ml含0.75g亚硫酸铵和0.75g过硫酸铵组成的混合引发剂水溶液,滴加完成后保温60min,聚合全部过程均处在机械搅拌和超声振动的共同处理下,将得到的产物水洗并与95℃下烘干,得到最终的复合材料,如图2所示。
44.实施例2
45.控制聚合体系温度为60℃,将20ml丙烯腈(占溶液总质量10wt%)、0.08g鳞片石墨(鳞片石墨烯占总单体含量的0.5wt%)、0.15ml十二硫醇混合均匀,在30min内滴加完10ml含0.5g亚硫酸铵和0.5g过硫酸铵组成的混合引发剂水溶液,滴加完成后保温90min,聚合全部过程均处在机械搅拌和超声振动的共同处理下,将得到的产物水洗并与95℃下烘干,得到最终的复合材料。
46.实施例3
47.控制聚合体系温度为70℃,将20ml丙烯腈(占溶液总质量10wt%)、0.8g鳞片石墨(鳞片石墨占总单体含量的5wt%)、0.15ml十二硫醇混合均匀,在60min内滴加完10ml含1g亚硫酸铵和1g过硫酸铵组成的混合引发剂水溶液,滴加完成后保温60min,聚合全部过程均处在机械搅拌和超声振动的共同处理下,将得到的产物水洗并与95℃下烘干,得到最终的复合材料,如图1所述。
48.实施例4
49.实施例1~3中得到的聚丙烯腈/鳞片石墨复合材料经过常用的静电纺丝及热处理过程可以制备得到鳞片石墨掺杂的复合碳纳米纤维,示例工艺如下:
50.将2g上述聚丙烯腈/石墨复合材料粉末加入至10ml二甲基亚砜,加热至60℃,搅拌均匀,获得纺丝原液,将纺丝原液倒入容积为20ml的针管中,针管装配有内径为0.5mm的静电纺丝针头,进行静电纺丝,静电纺丝的工艺参数为:温度为40℃,供液速度为3ml/h,电场强度为100kv/m,滑台的移动速度为10mm/s,收丝辊的转速为500rpm,待溶液消耗完毕即静电纺丝完毕后获得纳米纤维毡(即原丝)。
51.将上述纳米纤维毡按照收丝辊获得的取向切成长5cm、宽2cm的长条,在135℃的条件下,将长条拉伸至15cm(长条一端用夹子固定,另一端通过砝码施加牵伸),获得纳米纤维条带。
52.将热牵伸后的纳米纤维条带在280℃下预氧化1h,1400℃下碳化5min并在2800℃下石墨化50s,得到最终的碳纳米纤维。
53.以实施例2制备的碳纳米纤维如图3所示。
54.对制备的三种碳纳米纤维进行拉伸应力的检测。具体地,将最终得到的碳纳米纤维条带剪成30mm长、1mm宽的测试样条,然后将测试样条通过东华大学制造的xq-1c牵伸仪测试拉伸应力,结果如图4所示,结果表明随着石墨添加量的增多,碳纳米纤维的抗拉强度
不断提升。
55.以上所述仅为本发明的优选实施例而已,并不用于限制本发明,对于本领域的技术人员来说,本发明可以有各种更改和变化。凡在本发明的精神和原则之内,所作的任何修改、等同替换、改进等,均应包含在本发明的保护范围之内。