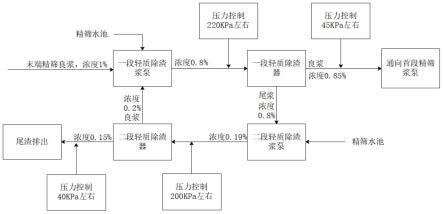
1.本发明属于纸制造纸技术领域,涉及一种减少制浆过程中胶黏物的制浆系统及方法。
背景技术:2.目前制浆造纸企业,在制浆工艺中需要去除浆料中的胶黏物等轻杂质,造纸用纸浆中的轻杂质是一种软性的,较难去除的轻杂质,其密度小于浆料,半成品浆料中总是含有许多胶黏物,这些胶黏物会附着于织物、导辊、烘缸、压光机等部件上,造成断纸、压光斑、湿斑等一系列问题,影响生产稳定和产品质量。目前的生产工艺主要是通过压力筛来筛选系统胶黏物,从而确保制浆半成品浆料质量,以满足纸机抄造的外观质量要求,而系统中胶黏物大量主要集中在长纤维精筛工段的末段精筛阶段,通常只有加大末段精筛的尾渣外排才能保证系统胶黏物减少。
3.但是末段精筛排放的尾渣中通常含有大量可用纤维,为了降低原料单耗,各车间在末端精筛的尾渣大部分重新回到碎浆机,只有一小部分外排,但该回收方式导致系统胶黏物没有有效排出,再反复经过系统机械作用力,较大的胶黏物会分解为较小的胶黏物,部分通过筛鼓进入良浆,会形成一种恶性循环,造成造纸系统中胶黏物无法有效的去除。
4.目前造纸车间中胶黏物的控制手段主要有:浆内添加胶黏物控制剂、增加保洁剂、织物更换防污染型、烘缸保洁剂、干网频繁清洗、部分导辊更换为镀铬辊、人工清理等一系列被动补救手段,但这些被动补救措施需要花费大量人力和财力,并且很难从源头将胶黏物有效分离排出系统。而且制浆系统的胶黏物控制剂一般设置于送浆塔的浆泵口,但药剂反应效果不理想,并不能有效去除造纸系统的胶黏物。
技术实现要素:5.针对上述现有技术中存在的问题,本发明公布了一种减少制浆过程中胶黏物的制浆系统及方法。该制浆系统及工艺主要是在胶黏物集中的末段精筛处,增加一套轻质除渣器系统,放大末段精筛筛缝规格,将包括蜡、聚苯乙烯泡沫、聚乙烯塑料、热熔胶合物和其它轻质、飘浮性物质去除出系统,确保成的质量,同时减少尾渣外排纤维流失,节约原料成本,然后改变制浆胶黏物控制剂添加点位置,使其与浆料接触充分,进一步确保成浆的质量,减少对纸机的影响。
6.为解决上述技术问题,本发明采用的技术方案是:一种减少制浆过程中胶黏物的制浆系统,其包括碎浆机、粗筛系统、分级筛、精筛系统、多盘浓缩系统以及热分散系统,其中碎浆机用于将废纸原料润化碎解成纤维状浆料;粗筛系统用于对碎解后的浆料进行净化筛选,提高浆料洁净度;分级筛用于将粗筛后浆料中长纤维和短纤维进行分离,以便有效利用不同纤维长度的浆料;精筛系统用于去除浆料中细小杂质;多盘浓缩系统则对筛选后的长短纤维进行浓缩处理;热分散系统用于将浓缩后的长纤维浆料中胶黏物杂质分散细化,均匀分布于浆料中,
7.其中所述精筛系统包括多段精筛机构,每段精筛机构包括进浆口、良浆出口以及尾浆出口,所述精筛机构依次串联连接;所述精筛系统中除末段精筛机构外的剩余精筛机构的良浆出口分别连通多盘浓缩系统,尾浆出口连通下一段精筛机构的进浆口;精筛系统中至少末段精筛机构设置有轻质除渣器系统,所述轻质除渣器系统中包括多段轻质除渣器,其中首段轻质除渣器的良浆出口连通首段精筛机构的进浆口,且每段轻质除渣器的尾浆出口连通下一段轻质除渣器的进浆口,下一段轻质除渣器的良浆出口连通上一段轻质除渣器的进浆口,末段轻质除渣器的尾浆出口与外界连通。
8.进一步的,所述精筛系统内末段精筛机构中筛鼓的筛缝为0.35mm,剩余精筛机构中筛鼓的筛缝设置为0.15mm。
9.进一步的,所述精筛系统包括三段精筛机构,所述精筛系统中第一段精筛机构的良浆出口与多盘浓缩系统的进浆口连通,所述第一段精筛机构的尾浆出口与第二段精筛机构的进浆口连通,所述第二段精筛机构的良浆出口与多盘浓缩系统的进浆口连通,所述第二段精筛机构的尾浆出口与第三段精筛机构的进浆口连通,所述第三段精筛机构的良浆出口与轻质除渣器系统连通,所述第三段精筛机构的尾浆出口与碎浆机的进料口连通。
10.进一步的,所述精筛系统中除末段精筛机构外的其他精筛机构均分别设置有轻质除渣器系统,每段精筛机构的良浆出口均连通所对应轻质除渣器系统的首段轻质除渣器的进浆口,首段轻质除渣器的良浆出口连通多盘浓缩系统的进浆口,且轻质除渣器的尾浆出口连通下一段轻质除渣器的进浆口,下一段轻质除渣器的良浆出口连通上一段轻质除渣器的进浆口,末段轻质除渣器的尾浆出口与下一精筛机构的进浆口连通。
11.进一步的,每段所述轻质除渣器均包含有多支除渣器,每支除渣器包括除渣器主体、进浆头、良浆头以及排渣头,其中除渣器主体包括圆筒段和锥筒段,所述圆筒段设置于锥筒段上方,所述进浆头设置于圆筒段上部位置,所述良浆头位于锥筒段下部,所述排渣头位于锥筒段底部,且所述排渣头的一端向锥筒段内部延伸,所述良浆头与排渣头之间设有流动腔体;所述进浆头包括进浆口和锥形导流体,制浆过程中浆料通过浆泵驱动以高流速沿切向方向从进浆头的进浆口流入,且浆料在锥形导流体作用下在除渣器内部进行涡旋流动;浆料中纤维在离心力作用下抛向除渣器主体的内壁,并通过进浆口的浆料压力推动向下螺旋运动,经过圆筒段和锥筒段之后从良浆头的出口流出,而浆料中密度低于水和纤维的各种轻杂质以及空气在浆料涡旋流动过程中聚向涡流中心的低压区,所述排渣头的一端延伸向涡流中心。
12.进一步的,每段轻质除渣器在制浆过程中的进浆浓度《0.8%,进浆压力为170-240kpa,压力降范围为70-100kpa。
13.进一步的,所述轻质除渣器系统中的多支除渣器并排安装固定构成一段轻质除渣器;每段轻质除渣器的进浆口分别连接有一个除渣器浆泵,所述除渣器浆泵均连通精筛系统的白水池。
14.进一步的,所述热分散系统包括稀释管道以及热分散机,所述稀释管道连通热分散机,所述稀释管道上设有胶黏物控制剂添加点,通过胶黏物控制剂添加点向稀释管道中添加胶黏物控制剂,并通入热分散机内。
15.进一步的,本发明还公开了一种减少制浆过程中胶黏物的制浆方法,其包括如下步骤:
16.s1.所述精筛系统中末段精筛机构的良浆经管道通入首段轻质除渣器上游的浆泵内,通过首段轻质除渣器上游的浆泵进行抽送,良浆经过精筛系统的白水池进行补水稀释到《0.8%的浓度,进浆压力控制在220kpa,然后通入首段轻质除渣器内进行除渣处理;
17.s2.经过首段轻质除渣器处理后排出良浆,该良浆浓度0.85%,良浆压力控制在45kpa,首段轻质除渣器排出的良浆经管道直接回流至精筛系统中首段精筛机构;首段轻质除渣器排出的尾浆浓度0.3%,尾浆经管道直接通入下一段轻质除渣器的浆泵。
18.s3.首段轻质除渣器排出的尾浆经过下一段轻质除渣器的浆泵抽送至下一段轻质除渣器内,首段轻质除渣器排出的尾浆经过精筛系统的白水池进行补水稀释到0.19%浓度,进浆压力控制在200kpa,并通入下一段轻质除渣器内进行除渣处理;
19.s4.经过下一段轻质除渣器处理后排出良浆,良浆压力控制在40kpa,下一段轻质除渣器排出的良浆经管道回流至上一段轻质除渣器的进浆口进行再处理;
20.s5.当轻质除渣器排出的尾浆浓度《0.15%时,尾浆排出至废旧筛鼓进行自然过滤浓缩后,直接外排出制浆系统。
21.与现有技术相比,本发明具有以下技术效果:
22.1)本发明的制浆系统中通过在精筛系统尾部增设多段轻质除渣器,可利用轻质除渣器有效去除制浆系统中绝大部分的胶黏物类轻杂质,能实现末段精筛尾渣“0”外排,可以降低原料单耗,节约原料成本,达到成本节降的作用,并且该结构不会过多改变原有制浆系统的结构,仅需要在精筛系统末端增加轻质除渣器,所需要的轻质除渣器数量有限,体积小,能耗低。
23.2)本发明的制浆系统中基于轻质除渣器去除掉绝大多数轻杂质后,流入热分散系统的胶黏物大幅下降,热分散系统所需温度随之降低,进而而可将胶黏物控制剂添加点位置设置于热分散系统的工序前方,使得胶黏物控制剂与浆料接触更充分,反应效果更好,胶黏物物质更易分散细化成肉眼看不到的形态,便于后续工序排出系统,使得困扰纸机的胶黏物控制问题得到缓解,生产运行正常,员工劳动强度降低。
附图说明
24.图1为本实施例中一种制浆系统的工艺流程图:
25.图2为传统精筛系统中浆料的处理工艺;
26.图3为传统制浆工艺中胶黏物控制剂添加点的分布位置图;
27.图4为本实施例中减少制浆过程胶黏物的制浆工艺流程图;
28.图5为本实施例中一种精筛系统与轻质除渣器的分布位置图;
29.图6为本实施例中另一种精筛系统与轻质除渣器的分布位置图;
30.图7为本实施例中胶黏物控制剂添加点的分布位置图;
31.图8为本实施例中除渣器的结构示意图。
具体实施方式
32.为使本发明实施方式的目的、技术方案和优点更加清楚,下面将结合本发明实施方式中的附图,对本发明实施方式中的技术方案进行清楚、完整地描述,显然,所描述的实施方式是本发明一部分实施方式,而不是全部的实施方式。基于本发明中的实施方式,本领
域普通技术人员在没有作出创造性劳动前提下所获得的所有其他实施方式,都属于本发明保护的范围。
33.因此,以下对在附图中提供的本发明的实施方式的详细描述并非旨在限制要求保护的本发明的范围,而是仅仅表示本发明的选定实施方式。基于本发明中的实施方式,本领域普通技术人员在没有作出创造性劳动前提下所获得的所有其他实施方式,都属于本发明保护的范围。
34.实施例1:
35.结合图1所示,本实施例中公开了一种减少制浆过程胶黏物的制浆系统,用于去除制浆系统中的胶黏物,其中制浆系统中的胶黏物多数来源于废纸原料中残余的化学品、油墨载体及残余脱墨添加剂、涂布加工纸中的胶粘剂、自封标签或者信封上的胶粘剂、装订和粘合的书籍及杂志所使用的热熔物以及箱纸板中所浸渍或涂布的蜡质等,这些物质在制浆过程中若不能有效分散和去除便会形成胶黏物沉积在输浆管道、成型网、压榨部毛毯、烘缸表面以及纸张表面,影响纸品的生产效率和生产质量。
36.因此本实施例中为去除胶黏物等杂质,上述系统包括碎浆机、粗筛系统、分级筛、精筛系统、多盘浓缩系统、热分散系统以及轻质除渣器,其中碎浆机用于将废纸原料润化碎解成纤维状浆料;粗筛系统用于对碎解后的浆料进行净化筛选,提高浆料洁净度;分级筛用于将粗筛后浆料中长纤维和短纤维进行分离,以便有效利用不同纤维长度的浆料;精筛系统用于去除浆料中细小杂质;多盘浓缩系统则对筛选后的长短纤维进行浓缩处理;热分散系统用于将浓缩后的长纤维浆料中胶黏物杂质分散细化,均匀分布于浆料中。
37.结合附图1所示,在造纸工艺中,废纸原料通过制浆车间的水力碎浆机润化碎解后,浆料经过高浓除渣器、粗筛器、重质除渣器、分级筛、精筛以及热分散等不同工段流程的处理设备加工,以期望去除浆料内含的各种杂质,保证浆料的洁净度,生产出合格的产品及保障纸机稳定生产运行。
38.但制浆系统,浆料流经分级筛选、精筛后,各种胶黏物以及其他碎小轻杂质会集中在长纤维精筛系统的末段精筛阶段,造纸车间中传统工艺是减小末段精筛系统中的良浆量,增大尾浆的排出量,该方式虽然保证了制浆系统中胶黏物的去除程度,但浪费了尾浆中所含有的大量粗纤维原料,使得造纸成本增高,为降低车间造纸原料的单耗成本,需要控制尾浆中粗纤维原料的排出量,即通过控制尾浆排出量,使尾浆多数回流至碎浆机中重新利用,少部分尾浆排出系统,如图2所示,但该方式又会使得后续浆料纸浆降低,胶黏物经过反复循环的机械作用力下,分解为细小的胶黏物,且部分通过精筛系统中的筛鼓进入良浆中,最终进入制浆系统影响生产运行和产品质量。
39.基于上述问题,本实施例中则在精筛系统中位于末端精筛的下游设置多段轻质除渣器,如图5所示,具体的本实施例中精筛系统中包括三段精筛机构,三段精筛机构依次串联连接,并且第三段精筛机构中筛鼓的筛缝为0.35mm,前两段精筛机构中筛鼓的筛缝设置为0.15mm,结合附图5所示,所述精筛系统中第一段精筛机构的良浆出口与多盘浓缩系统的进浆口连通,所述第一段精筛机构的尾浆出口与第二段精筛机构的进浆口连通,所述第二段精筛机构的良浆出口与多盘浓缩系统的进浆口连通,所述第二段精筛机构的尾浆出口与第三段精筛机构的进浆口连通,所述第三段精筛机构的良浆出口与轻质除渣器的进浆口连通,所述第三段精筛机构的尾浆出口与碎浆机的进料口连通,浆料经过分级筛处理后,分级
筛尾浆主要为含有轻杂质及胶黏物的长纤维浆料,然后通过精筛机构层层筛选。其中第一、二段精筛机构的良浆质量良好,可以直接进入后续工段进行多盘浓缩,而尾浆都是流入下一个精筛机构处理,最终尾浆逐渐集中含有大量轻杂质及胶黏物,且大部分都集中在末段精筛机构中,因此只需要在末段精筛机构增加轻质除渣器即可,且处理总量少,所需除渣器段数及单支数量少。
40.本实施例中所述轻质除渣器设有两段,第一段轻质除渣器的良浆出口与第一段精筛机构的进浆口连通,所述第一段轻质除渣器的尾浆出口与第二段轻质除渣器的进浆口连通,所述第二段轻质除渣器的良浆出口连通至第一段轻质除渣器的进浆口,所述第二段轻质除渣器的尾浆出口排出尾渣。
41.此外需说明的是,制浆系统中精筛机构和轻质除渣器的设置数量不仅限于本实施例的个数,精筛系统中的精筛机构个数可根据制浆原料、杂质含量、杂质类型进行调整,轻质除渣器的个数以及安设位置可根据胶黏物等杂质的类型、含量进行调整,例如当浆料中胶黏物含量过大时,针对精筛系统中进行胶黏物去除的方法有两种:如图5所示,其一是本实施例中精筛系统在位于末端精筛机构位置设置有轻质除渣器系统,该轻质除渣器系统中除渣器数量设置2段或者2段以上,首段轻质除渣器的良浆出口连通首段精筛机构的进浆口,且每段轻质除渣器的尾浆出口连通下一段轻质除渣器的进浆口,下一段轻质除渣器的良浆出口连通上一段轻质除渣器的进浆口,末段轻质除渣器的尾浆出口与外界连通;如图6所示,其二是精筛系统中每段精筛机构均设置有轻质除渣器,除末段精筛机构所对应的轻质除渣器连接结构与方法一相同外,其余每段精筛机构的良浆出口均连通所对应的首段轻质除渣器的进浆口,首段轻质除渣器的良浆出口连通多盘浓缩系统的进浆口,且轻质除渣器的尾浆出口连通下一段轻质除渣器的进浆口,下一段轻质除渣器的良浆出口连通上一段轻质除渣器的进浆口,末段轻质除渣器的尾浆出口与下一精筛机构的进浆口连通。上述方法一中的末段精筛机构设置轻质除渣器系统,通过多级精筛机构串联连接,浆料中的大多数胶黏物将积聚至末段精筛机构,通过末段精筛机构对应的除渣器可将多数胶黏物杂质从浆料中分离;而方法二中则分离效果更优于方法一,但设备成本较高,方法二中通过在每段精筛机构设置轻质除渣器系统,每段精筛机构所筛分出的良浆均会经过多段轻质除渣器筛分出浆料中的胶黏物后再通入多盘浓缩系统,进入下一步工序,从而最大化分离出浆料中胶黏物杂质。
42.本实施例中通过将精筛系统中末段精筛机构0.2mm筛缝的筛鼓更换为0.35mm的筛鼓,在制浆生产过程中,可增大末段精筛的良浆流量,增加胶黏物杂质的通过流量,使尾浆流量降低,减少外排甚至达到“0”外排,并使尾浆连通至碎浆机,采用此种方式进行改善后,制浆过程中末段精筛的压差会随之明显下降,本实施例中末端精筛机构的压差可以从原本的45kpa降低到20kpa,并且精筛系统中筛鼓的筛缝也不会由于缝隙过小而经常堵塞,因此改善了精筛系统中由于压差高而经常易堵筛的情况,进而减轻了筛鼓的清洗频率(原本需一个星期就要拆解清洗一次),该方式不仅保证了制浆生产的稳定性,还降低了劳动成本。
43.需要说明的是,本实施例中每段轻质除渣器均包含有多支除渣器,如图8所示,每支除渣器包括除渣器主体101、进浆头102、良浆头103、排渣头104以及阀门,其中除渣器主体101包括圆筒段和锥筒段,所述圆筒段设置于锥筒段上方,所述进浆头102设置于圆筒段上部位置,所述良浆头103位于锥筒段下部,所述排渣头104位于锥筒段底部,且所述排渣头
104的一端向锥筒段内部延伸,所述良浆头103与排渣头104之间设有流动腔体;所述进浆头包括进浆口和锥形导流体,当除渣器进行除渣处理时,浆料通过浆泵驱动以高流速沿切向方向从除渣器上方的进浆口进入,且浆料在锥形导流体作用下在在除渣器内部进行涡旋流动;浆料中纤维在离心力作用下抛向除渣器主体的内壁,并通过进浆口的浆料压力推动向下螺旋运动,经过圆筒段和锥筒段之后从良浆头的出口流出,而浆料中密度低于水和纤维的各种轻杂质以及空气在浆料涡旋流动过程中聚向涡流中心的低压区,所述排渣头的一端延伸向涡流中心,且各种轻杂质以及空气通过排渣头引出除渣器主体内部。通过上述方式可将浆料中各种轻杂质(包括胶黏物)分离出,保留浆料的水以及纤维。本实施例中通过将多支除渣器并排分布,并利用支架安装固定构成整段轻质除渣器设备。同时在每段轻质除渣器的进口位置分别连接有一个浆泵,各浆泵均连通有精筛系统的白水池,该白水池用于盛装精筛系统所筛除后的废水。
44.本实施例中所采用的轻质除渣器为直流式除渣器,其可从低浓浆料中去除轻质或飘浮性物质,例如蜡状物、聚苯乙烯泡沫、聚乙烯塑料和热熔胶合物等。该除渣器利用直流原理,轻杂质尾渣和良浆均从与进浆头对应的另一端排出,浆料在运行过程中,不会存在逆流现象,除渣器中心的空气柱只与尾浆流相接触,浆料中所带有的多余空气会被排出。该除渣器在保证进浆浓度《0.8%,进浆压力170-240kpa,压力降控制在70-100kpa的条件下,即可有效的去除绝大部分轻杂质。压力降是产生除渣器涡旋运动的推动力,是影响除渣器净化效率的主要因素之一。若压力降过高,系统的良浆产能会增大,尾渣排渣就会相对削减,但这样会影响良浆浆料清洁程度,即除渣效率会变差,部分胶黏物类轻杂质也会进入良浆里面,杂质去除效果反而降低。若压力降过低,系统产能又会降低,而尾渣排渣会上升,良浆浆料清洁度会提升,去除效率变好,但部分有用纤维会随尾渣流送,造成材料浪费。本实施例中则控制压力降控制在70-100kpa的条件下,该范围内良浆产能和尾渣排渣效果最优。
45.本实施例中通过多段除渣器与多段精筛机构共同构成胶黏物循环排出设备,精筛系统中的胶黏物等杂质通过利用多段轻质除渣器设备处理,使胶黏物达到连续集中外排的运行模式,从而确保回流至碎浆机的尾浆中胶黏物含量减少,进而保障后续工段浆料的洁净度,从而改变浆料中物理成分性质,将原本胶黏物被动去除方式变为胶黏物主动去除方式,从源头将制浆系统中浆料的胶黏物杂质在制浆阶段可尽全面的有效去除,避免在进入纸机系统后,需要采用被动方式随纸机系统调整,从而带来的一系列不利影响。
46.更具体的,如图4所示,本实施例中利用上述设备结构减少制浆过程中胶黏物的工艺流程为:
47.精筛系统中提高末段精筛机构中良浆流量,良浆经管道通入第一段轻质除渣器上游的浆泵内,通过第一段轻质除渣器上游的浆泵进行抽送,良浆经过精筛白水池进行补水稀释到《0.8%的浓度,并通入第一段轻质除渣器内进行除渣处理,该阶段第一段轻质除渣器的进浆压力控制在220kpa左右:浆料以较高的流速沿切线方向从除渣器上部进浆口进入,在除渣器顶部锥形导流体作用下,浆料在除渣器内做稳定的涡旋流动,纤维在离心力的作用下抛向筒壁,并在进浆压力推动做向下的螺旋运动,经过圆筒段和锥筒段之后从锥筒底部的良浆口流出,而浆料中密度小于水和纤维的各种轻质杂质以及空气在浆料涡旋流动过程中聚向涡流中心的低压区,由伸向涡流中心的尾浆流管引出。
48.经过第一段轻质除渣器处理后排出良浆,该良浆浓度约0.85%,良浆压力控制在
45kpa左右,第一段轻质除渣器排出的良浆经管道直接回流至精筛系统中第一段精筛机构;第一段轻质除渣器排出的尾浆,浓度约0.3%,尾浆经管道直接通入第二段轻质除渣器的上游浆泵。
49.尾浆经第二段轻质除渣器的上游浆泵抽送,尾浆经过精筛白水池进行补水稀释到0.19%左右浓度,并通入第二段轻质除渣器内进行除渣处理,除渣原理同第一段轻质除渣器,该阶段第二段轻质除渣器的进浆压力控制在200kpa左右。
50.经过第二段轻质除渣器处理后排出良浆,该良浆浓度约0.2%,良浆压力控制在40kpa左右第二段轻质除渣器排出的良浆经管道回流至第一段轻质除渣器的入口进行再处理,第二段轻质除渣器排出的尾浆中含有大量胶黏物物质,该尾浆浓度约0.15%,尾浆通过废旧筛鼓进行自然过滤浓缩后,直接外排出生产系统,从而达到去除制浆系统胶黏物的目的。
51.本实施例中多段轻质除渣器采用气动阀门进行自动调节,可根据不同原料结构及生产状况要求进行自主调节,本实施例中轻质除渣器的压力降一般控制在70-180kpa范围,该轻质除渣器的正常工作温度为49℃左右,其与制浆系统的浆料温度基本一致,且最大操作温度≤70℃,而正常工作状态下,进浆压力控制范围为170-240kpa,最大进浆压力≤400kpa。
52.此外为进一步控制浆料中胶黏物杂质,通常会在制浆过程中添加胶黏物控制剂,如图3所示,传统制浆工艺中在精筛系统连通轻质除渣器前,胶黏物控制剂的添加点会设置于热分散系统的后段工序中,具体将胶黏物控制剂的添加点设置于热分散系统与成浆池之间的浆泵上游位置,其原因是由于经过热分散分散处理过后的浆料,在经过后续一系列浆塔、浆池及纸机流送系统的过程中,随着时间、温度及环境的变化,根据胶黏物特性,原先已经分散细化开的胶黏物物质有可能会再次发生粘合聚集现象,最终会影响纸机生产。而胶黏物控制剂的作用主要为分散钝化胶黏物杂质,减少胶黏物杂质聚集现象,先前胶黏物控制剂添加点位置设置在热分散后成浆池浆泵口,传统制浆工艺中为去除浆料中大量胶黏物多采用热分散系统进行高温加热,控制值95-100℃,促使浆料中胶黏物分散,但为避免过高温度环境使胶黏物控制剂的作用失效,需要在热分散系统的后段工艺中再添加胶黏物控制剂,胶黏物控制剂用量约为110ml/min,但在上述位置设置胶黏物控制剂添加点,胶黏物控制剂的混合效果较差。
53.本实施例中则将胶黏物控制剂的添加点设置于热分散系统的前段工序,如图7所示,具体的该胶黏物控制剂的添加点设置于热分散系统中稀释水管路上,通过将胶黏物控制剂添加在稀释水中后,再通入热分散机中,由于轻质除渣器后,整个制浆系统内胶黏物大部分被去除出生产系统,浆料内含细小胶黏物类杂质成分减少,热分散温度可以下调,在热分散系统前加入胶黏物控制剂,胶黏物控制剂不会再受到过高温度影响而被破坏,并且在热分散系统前的胶黏物添加剂可确保药物反应充分,更有利于帮助被分散在浆料中的细小胶黏物有效钝化分散去除。由于在精筛系统中轻质除渣器已将大部分的胶黏物去除,因此在热分散阶段中无需过高温度进行胶黏物分散,胶黏物控制剂的用量也可减少至约50ml/min。该步骤可进一步减轻胶黏物、粘缸、粘网、粘毛布、断纸及压光斑、湿斑等一系列问题,化辅成本会下降,造纸运行率提升。
54.以上所述仅为本发明的优选实施例而已,并不用于限制本发明,对于本领域的技
术人员来说,本发明可以有各种更改和变化。凡在本发明的精神和原则之内,所作的任何修改、等同替换、改进等,均包含在本发明的保护范围之内。