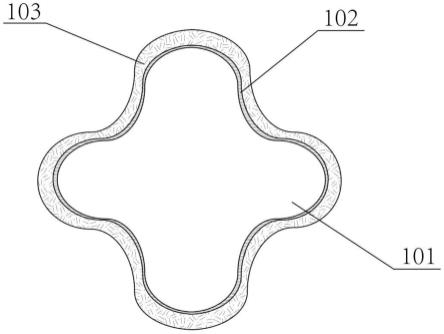
一种光催化co2制备甲醇的导光纤维及其制备方法
技术领域
1.本发明属于光催化导光纤维领域,具体涉及一种光催化co2制备甲醇的导光纤维及其制备方法。
背景技术:2.随着工业化的发展,co2的排放量持续增加,温室效应导致的全球变暖成为制约发展的问题之一,并且随着人们对环境问题的进一步重视和碳中和的提出,co2的捕捉、固定和还原以降低空气中co2的浓度也越来越受重视。co2还原的方法有很多,其中光催化作为一种绿色、可持续发展的方法备受关注。不同的光催化剂可以将co2还原为不同的物质,其中甲醇作为可液化和便于保存运输的燃料是一种理想的产物。由g-c3n4与rgo(还原氧化石墨烯)复合材料组成的光催化剂就是一种定向还原co2为甲醇的光催化剂。内部可传导光线的导光纤维是一种很好的光催化还原co2的反应器。改性pet(聚对苯二甲酸乙二醇酯)作为非常规的光催化反应器的导光材料,在对传导光线要求不高的反应器中占有一定优势。
3.在化学中,光催化是在催化剂的存在下光反应的加速。在催化光解中,光被吸附的底物吸收。在光生催化中,光催化活性(pca)取决于催化剂产生电子-空穴对的能力,该电子-空穴对产生能够进行二级反应的自由基(例如,羟基自由基:
·
oh)。通过二氧化钛(tio)电解水的发现,使其实际应用成为可能)。光催化原理:在宏观上,即光合作用的逆反应,它是一种催化剂,在光的作用下将有机物转化为无机物。1、在微观上,二氧化钛颗粒在吸收了紫外光的能量后,对有机物进行降解,最终生成二氧化碳和水而不损失。光催化是当今世界上最理想的环境净化技术,它具有操作简单、能耗低、无二次污染、效率高等优点。将空气中的氧直接用作氧化剂,可在常温常压下反应。分解有机污染物为无机小分子,如二氧化碳、水等,净化效果彻底。半导体光触媒化学性质稳定,氧化还原性强,成本低,不存在吸附饱和现象,使用寿命长。2、其基本原理是,在光激发下,电子由价带跃进至导带位置,使其在导带上形成光生电子,在价带上形成光生空穴。通过光生电子-空穴对的还原氧化性,可降解环境中的有机污染物,以及制备co2。一个高效率的光催化剂必须满足以下条件:(1)半导体合适的导带和价带位置,在用于净化污染物的应用时,价带电位必须有足够的氧化性能,并且在光解水应用中。(2)有效的电子-空穴分离能力,降低其合成几率。(3)可见光响应特性:不到420nm的紫外光能量大约只占太阳光能的4%,如何利用可见光乃至红外光能量,是决定光催化材料能否得到大规模实际应用的前提。
4.目前已有研究人员对光催化反应器光催化co2还原为甲醇进行相关研究。如专利cn201410446964.9提供了一种具有光源逆向布置的多光纤反应通道反应器,将四根光纤组成一个独立的反应通道,并由多个反应通道组成光纤反应通道反应器,该工艺形成的反应器由于多光纤的布置加强了光子的利用,提高了反应效率以及甲醇产物浓度,但该反应器中用于传导光线的纤维为普通石英光纤,光纤内导光效果虽好但折射出纤维的光强较低,反应效率仍有待提高。专利cn201610144691.1提供了一种光纤式光催化反应器和将co2转化成甲醇的方法,将负载稀土改性的二氧化钛的光纤设置于反应桶内,该反应器光利用率
高、催化剂比表面积大,但该反应器使用的为常规圆形截面光纤,改变为其他截面光纤可以进一步提高比表面积和折射光强。文献“蜂窝光纤反应器中光催化还原二氧化碳的分析与强化”中采用于光纤外壁和反应单元内壁浸涂煅烧光催化剂并由多个反应单元组成反应器的方法进行光催化co2,该反应器虽然负载光催化剂部分增多,但该方法无法适用于不耐高温的导光纤维,无法利用这些纤维的优势。文献“photocatalytic co
2 reduction using an internally illuminated monolith photoreactor”采用只将光催化剂浸涂煅烧于具有多个通道的整个反应器内壁,再将多根pmma(聚甲基丙烯酸甲酯)插入这些通道中组成光催化反应器用于光催化co2还原为甲醇,该方法虽然采用了pmma,但pmma和反应器内壁存在距离,折射出的光线照射到内壁时难免存在一定的损耗,并且该反应器所使用的光催化剂最多吸收460nm的光。
技术实现要素:5.为了克服现有技术的不足,本发明提供了一种光催化co2制备甲醇的导光纤维,为皮芯结构,包括导光层,覆盖于所述导光层上的光催化层和覆盖于所述光催化层上的防护层;
6.所述导光层为十字形,包含具有导光效果的高聚物;所述具有导光效果的高聚物的全光线透过率为88%-90%,折射率为1.45-1.50;
7.所述防护层包含tpu(热塑性聚氨酯弹性体)纳米纤维;
8.所述导光层、光催化层和防护层的等效厚度比为:700-1000:0.3-2:100-500。
9.优选的,所述光催化层中的光催化剂包括g-c3n4和rgo。
10.进一步地,所述g-c3n4和rgo的质量比为92-96:4-8。
11.进一步地,所述具有导光效果的高聚物为改性聚对苯二甲酸乙二酯。
12.优选的,所述防护层的折射率为1.52-1.57。
13.优选的,所述tpu纳米纤维膜的纳米纤维的直径为500-800nm。
14.优选的,所述防护层包含大孔和小孔,所述大孔的直径为90-110nm,所述小孔的直径为15-25nm。
15.优选的,所述导光纤维的等效直径为0.8-1.5mm。
16.本发明还提供一种所述的光催化co2制备甲醇的导光纤维的制备方法,包括如下步骤:
17.s1:将具有导光效果的高聚物热压塑得到所述导光层;
18.所述热压塑的压力为5-10mpa,温度为260-280℃;
19.s2:将浆料煅烧后包覆于所述导光层上,得到预制件;
20.所述浆料是将光催化剂和nahco3溶液加入聚乙二醇水溶液中混合得到;
21.s3:将所述预制件进行热拉伸,得到纤维状长丝;
22.s4:对所述纤维状长丝的外表面进行吹喷纺丝,得到所述光催化co2制备甲醇的导光纤维;所述吹喷纺丝的纺丝液的溶质为tpu,溶剂为dmf,所述tpu的浓度为8-12wt%。
23.优选的,所述步骤s3中,热拉伸的温区温度为80-90℃、260-280℃和90-100℃;
24.优选的,所述步骤s4中,吹喷纺丝的牵伸风压0.08-0.4mpa,挤出速度2-5ml/h,接收距离15-25cm。
25.本发明还提供一种柔性pu(聚氨酯)管,包括上述的光催化co2制备甲醇的导光纤维;
26.所述柔性pu管的弯曲角度为0-60
°
;
27.所述柔性pu管内部设有100-200根所述光催化co2制备甲醇的导光纤维;
28.所述柔性pu管的上表面设有气体入口;
29.所述柔性pu管下表面设有气体出口;所述柔性pu管的一侧设有光源。
30.本发明的技术方案相比现有技术具有以下优点:
31.(1)本发明设计整个导光纤维横截面为十字形,一方面该结构可以使光线在导光层内部传输的同时更便于光线从导光层折射出来以启动光催化反应,另一方面相较于常规的圆形截面,该结构的表面积更大,可以负载的光催化层更多。
32.(2)本发明利用吹喷纺丝制备了tpu纳米纤维膜作为防护层,一方面tpu纳米纤维之间存在着一定的间隙,另一方面tpu纳米纤维上分布着本身自带的以及溶剂挥发导致的诸多大孔和小孔,以上两种结构确保防护层不会对co2气体通过产生影响,同时可以使光线在防护层内部多次反射折射到光催化层以进行多次反应。
33.(3)本发明利用吹喷纺丝制备的tpu纳米纤维作为防护层,可以对内部具有柔性结构的高聚物导光层进行保护,防止其被通入的气体产生的气流干扰出现晃动影响内部光线的传导和光催化反应的进行,并且外部的防护层折射率相较内部的导光层较大,不满足全反射条件,所以光线既可以在导光层内部向前传导,也可以折射出导光层引发光催化反应。
34.(4)本发明设计将光催化层包覆于导光层预制件的外部以共同进行热拉伸,可以利用导光层的高聚物在高温下的粘性充当热熔胶的作用对光催化层进行粘合确保光催化层不会脱落并减少了常规粘合剂的使用,减少污染。
35.(5)本发明设计一步式在线形成导光纤维,在热拉伸的出口处设置吹喷纺丝装置,利用热拉伸后残余的高温对吹喷纺丝的纳米纤维中残余的溶剂进行烘干挥发,以减少后道烘干,节约能源,并且吹喷得到的tpu防护层还具有一定的粘合效果。
36.(6)本发明利用高聚物改性pet作为导光纤维的导光层,改性pet可以很好的将光线折射到外部引发反应,并且将高聚物应用于光催化反应器中,利用高聚物的柔性和韧性,便于生产运输以及反应器内部导光纤维的替换。此外,用于营造封闭环境的pu管为柔性pu管,其可以很好的与具有柔性的导光纤维配合,弯曲一定的角度,从而扩大整个系统的应用范围。
附图说明
37.图1为本发明的整体工艺的侧视示意图;
38.图2为本发明的一种用于光催化co2还原为甲醇的导光纤维的横截面示意图;
39.图3为本发明的光线在导光纤维横截面的传导路径示意图;
40.图4为本发明的防护层内部放大示意图;
41.图5为本发明导光纤维放置于柔性pu管的示意图。
42.附图标记说明:1-导光纤维,2-热拉伸加热器,3-吹喷纺丝注射器,4-空气压缩机,5-吸风机,6-收卷辊,7-柔性pu管,8-气体入口,9-气体出口,101-导光层,102-光催化层,103-防护层,104-光源,105-大孔,106-小孔。
具体实施方式
43.下面结合附图和具体实施例对本发明作进一步说明,以使本领域的技术人员可以更好地理解本发明并能予以实施,但所举实施例不作为对本发明的限定。
44.下述实施例中未作特殊说明,所有原料均来自于商购或通过本领域的常规方法制备而得。
45.tpu购自靖江市晶科贸易商行,牌号为ppc-tpu。
46.pet购自广州市通合塑料制品有限公司,牌号为th0769。
47.g-c3n4购自江苏先丰纳米材料科技有限公司,牌号为xfi10。
48.rgo购自四川垦业科技发展有限公司,牌号为crg2210。
49.实施例1
50.本例提供一种用于光催化co2还原为甲醇的导光纤维及其制备方法,该导光纤维的制备方法包括:
51.结合图1-5,颗粒状的改性pet通过特定的十字形模具利用平板硫化机在一定的温度和压力下形成十字形预制件,该预制件即为导光层101,将粉末状的g-c3n4与rgo复合材料加入nahco3溶液中并超声分散后加入聚乙二醇水溶液并搅拌,待形成均匀浆料后刮涂于玻璃板上,再进行煅烧后取下成形的光催化层102包覆于未进行热拉伸的导光层101外部,随后将导光层101和光催化层102共同通过热拉伸加热器2进行热拉伸,在热拉伸的出口处设置右吹喷纺丝装置,在空气压缩机4产生的气流下带动吹喷纺丝注射器3挤出的纺丝液喷到热拉伸后的导光层101和光催化层102外部得到防护层103,防护层的纳米纤维中存在大孔105和小孔106,并在吹喷纺丝注射器3相对热拉伸加热器2的另一侧设置吸风机5,将吹喷纺丝纺丝液中挥发的溶剂进行回收,防止其污染环境,将最终形成的导光纤维1收集到收卷辊6上。最后将导光纤维1设置于柔性pu管7中,柔性pu管7一端面有光源104发出的光线射入,光源104射入一端的上部存在气体入口8,用于co2的通入,另一端的下部存在气体出口9,用于光催化制备得到的甲醇的排出。
52.在本例中,所述的g-c3n4与rgo复合材料,以重量份计,由92份g-c3n4与8份rgo组成。
53.在本例中,所述的改性pet,其全光线透过率为90%,折射率为1.50。
54.在本例中,所述的预制件成形压力为5mpa,温度为280℃,热拉伸的三温区温度分别为80℃,260℃,90℃。
55.在本例中,所述的吹喷纺丝工艺参数为纺丝液浓度为12%,牵伸风压0.2mpa,挤出速度5ml/h,接收距离25cm。
56.在本例中,所述的tpu纳米纤维直径范围为500-800nm,所述的tpu纳米纤维中存在大孔105和小孔106两类孔,所述大孔105的直径为90-110nm,所述小孔106的直径为15-25nm,防护层折射率为1.55。
57.在本例中,所述的导光层等效厚度为0.9mm;光催化层等效厚度为1μm;防护层等效厚度为400μm。
58.在本例中,所述柔性pu管7内部的导光纤维1的根数为160根,所述柔性pu管7弯曲角度为30
°
。
59.最终得到的导光纤维1的等效直径为1.3mm。
60.实施例2
61.基本同实施例1,其区别仅在于:
62.在本例中,所述的g-c3n4与rgo复合材料,以重量份计,由95份g-c3n4与5份rgo组成。
63.在本例中,所述的改性pet,其全光线透过率为88%,折射率为1.45。
64.在本例中,所述的预制件压力为10mpa,温度为260℃,热拉伸的三温区温度分别为90℃,280℃,100℃。
65.在本例中,所述的吹喷纺丝工艺参数为纺丝液浓度为8%,牵伸风压为0.4mpa,挤出速度为3ml/h,接收距离为15cm。
66.在本例中,其中纳米纤维直径范围为500-800nm,大孔的直径为90-110nm,小孔的直径为15-25nm,防护层的折射率为1.52。
67.在本例中,所述的导光层等效厚度为0.9mm;光催化层等效厚度为2μm;防护层等效厚度为100μm。
68.最终得到的导光纤维等效直径为1.0mm。
69.实施例3
70.基本同实施例1,其区别仅在于:
71.在本例中,所述的g-c3n4与rgo复合材料,以重量份计,由96份g-c3n4与4份rgo组成。
72.在本例中,所述的改性pet,其全光线透过率为89%,折射率为1.47。
73.在本例中,所述的预制件压力为8mpa,温度为270℃,热拉伸的三温区温度分别为85℃,270℃,95℃。
74.最终得到的导光纤维等效直径为1.0mm。
75.对比例1
76.基本同实施例1,其区别仅在于:
77.在本例中,导光层预制件采用圆形截面的模具制备,包覆的光催化层横截面也为圆形,最终导光纤维横截面为圆形截面。
78.在本例中,所述的导光层厚度为0.9mm;光催化层厚度为1μm;防护层厚度为400μm。
79.在本例中,最终得到的导光纤维直径为1.3mm。
80.对比例2
81.基本同实施例1,其区别仅在于:
82.在本例中,导光纤维只有导光层和光催化层,没有吹喷纺丝制备的tpu纳米纤维防护层。
83.在本例中,不存在吹喷纺丝注射器、空气压缩机和吸风机。
84.在本例中,所述的导光层等效厚度为0.9mm;光催化层等效厚度为1μm;无防护层。
85.在本例中,最终得到的导光纤维等效直径为0.9mm。
86.对比例3
87.基本同实施例1,其区别仅在于:
88.在本例中,防护层为将tpu熔融涂覆于导光层和光催化层外部得到,而非吹喷纺丝得到。
89.在本例中,tpu为颗粒状tpu,通过熔融挤出涂覆的方法得到防护层。
90.在本例中,原料在100℃下干燥2h后,通过螺杆挤出机在200℃下熔融挤出。
91.在本例中,所述的导光层等效厚度为0.9mm;光催化层等效厚度为1μm;防护层等效厚度为100μm。
92.在本例中,最终得到的导光纤维等效直径为1.0mm。
93.对比例4
94.基本同实施例1,其区别仅在于:
95.在本例中,所述的导光层材料为石英。
96.在本例中,石英预制棒采用传统ovd工艺制备的圆形横截面预制棒,随后热拉伸温度为2100℃。
97.在本例中,光催化层为将粉末状的g-c3n4与rgo复合材料加入nahco3溶液中并超声分散后加入聚乙二醇水溶液并搅拌,待形成均匀浆料后,将热拉伸后的导光纤维浸于浆料中以负载光催化层,然后在600℃下进行煅烧得到导光层和光催化层。
98.在本例中,吹喷纺丝在已经煅烧完成后纤维的导光层和光催化层外部进行纺丝得到防护层。
99.在本例中,所述的导光层厚度为0.9mm;光催化层厚度为1μm;防护层厚度为400μm。
100.在本例中,最终得到的导光纤维的直径为1.3mm。
101.对比例5
102.基本同实施例1,其区别仅在于:
103.在本例中,所述的导光层材料为pmma,并且其折射率为1.52。
104.在本例中,导光层同样采用预制件-热拉伸法制备,横截面为十字形,导光层外部包覆光催化层共同进行热拉伸,然后在线吹喷一层防护层。
105.在本例中,预制件成形压力为5mpa,温度为230℃,热拉伸三温区温度为80℃,210℃,90℃。
106.在本例中,所述的导光层等效厚度为0.9mm;光催化层等效厚度为1μm;防护层等效厚度为400μm。
107.在本例中,最终得到的导光纤维的直径为1.3mm。
108.性能测试
109.实施例1-2和对比例1-5的相关性能见下表,其中导光纤维的直径或等效直径为圆形截面的直径以及非圆形截面的等效直径;折射光亮度为总入射光射入导光纤维内部导光层后折射出导光层的光线亮度;折射光占比为折射光亮度占总入射光亮度的百分比;甲醇生产速率为反应产物甲醇的生产速率。
[0110][0111]
显然,上述实施例仅仅是为清楚地说明所作的举例,并非对实施方式的限定。对于所属领域的普通技术人员来说,在上述说明的基础上还可以做出其它不同形式变化或变动。这里无需也无法对所有的实施方式予以穷举。而由此所引申出的显而易见的变化或变动仍处于本发明创造的保护范围之中。