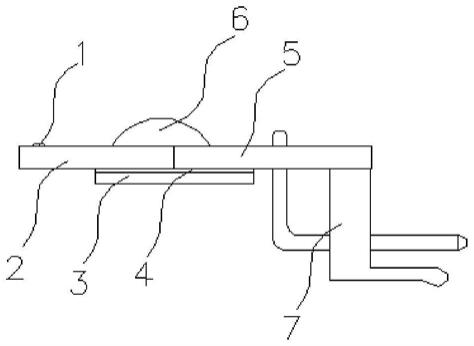
:
1.本发明涉及热敏打印头制造技术领域,具体的说是一种能够避免相邻的打印单元相互挤压,进而提高产品质量的拼接式热敏打印单元及热敏打印头和其装配方法。
背景技术:2.热敏打印头一般由发热陶瓷基板、pcb线路板及散热板构成的,陶瓷基板与pcb线路板固定在散热板上。散热板的材质为铝型材,铝制的散热板热膨胀系数约24.9x10-6
/℃,陶瓷基板的热膨胀系数约8.8x10-6
/℃,两者膨胀系数不同,温度降低,铝制散热板形变量大于陶瓷基板。
3.目前热敏打印头在宽幅打印领域越来越多,打印宽度超过600mm,因生产工艺及成本限制,单台热敏打印头的打印宽度可以做到300mm。要满足条幅打印,需要采用两组以上打印单元拼接实现。
4.然而由于不同组件膨胀系数不同,导致当环境温度变化时,相邻的打印单体发生挤压,不仅影响产品打印质量,甚至会造成陶瓷基板受力后被破坏,产品的寿命降低。
技术实现要素:5.本发明针对现有技术中存在的缺点和不足,提出了一种能够避免相邻的打印单元相互挤压,进而提高产品质量的拼接式热敏打印单元及热敏打印头和其装配方法。
6.本发明通过以下措施达到:
7.一种拼接式热敏打印单元,包括陶瓷基板、pcb板以及底板,陶瓷基板和pcb板分别固定在底板上,陶瓷基板的上表面设有发热体电阻安装区,发热体电阻安装区内设置发热体电阻;其特征在于,陶瓷基板的非发热电阻安装区与底板固定连接,陶瓷基板对应发热体电阻安装区的下侧悬空。
8.本发明所述底板采用金属基台,陶瓷基板背面对应非发热电阻安装区的位置与金属基台胶黏固定,pcb板与金属基台胶黏固定,pcb板和金属基台开设相对应的螺钉孔,螺钉孔呈条形,其中优选宽度4mm,长度6mm。
9.本发明为了提高pcb板、金属基台以及其他组件的固定稳定性,可以在pcb板、金属基台上沿直线设置两个以上的条形螺钉孔。
10.一种拼接式热敏打印头,设有散热板,散热板上设有两个以上的拼接式热敏打印单元,其特征在于,散热板上开设螺钉孔,两个以上的拼接式打印单元分别经螺钉固定在散热板上,其中拼接式打印单元的陶瓷基板对应发热体电阻安装区的下表面与散热板之间设有导热硅脂填充层。
11.本发明中与发热体电阻安装区位置对应的导热硅脂填充层高度范围为0.1-0.3mm,宽度范围为4.0-6.0mm。
12.本发明为了保证导热硅脂填充层稳定的位于陶瓷基板与散热板之间,在散热板的上表面开设两条彼此平行的导热硅脂导流槽,两条导热硅脂导流槽之间为导热硅脂填充层
设置区,进一步,导热硅脂填充层设置区的高度略高于散热板其他区域高度,以便于安装时快速对齐两个以上拼接式热敏打印单元的对应位置。
13.本发明为了保证对两个以上拼接式热敏打印单元的快速对齐和固定,所述散热板上表面一侧设有对齐台阶,优选在散热板靠近导热硅脂填充层设置区的侧边设有对齐台阶,用于保证在装配过程中,两个以上拼接式热敏打印单元快速找正位置。
14.本发明两个以上的拼接式热敏打印单元分别经螺钉固定在散热板上,且相邻的拼接式热敏打印单元保留间隙y,y的宽度小于0.2mm,进一步优选y的宽度为0.15mm。
15.本发明为了提高拼接式热敏打印单元与散热板之间的固定效果,设有压板,压板上开设条形螺钉孔,安装时,螺钉依次穿过压板上的螺钉孔、两个以上拼接式打印单元上的螺钉孔后,与散热板上螺钉孔锁紧,螺钉采用m3盘头式螺丝,螺钉与条形螺钉孔为间隙配合,且螺丝与条形螺丝孔的间隙余量为1mm-3mm,当外界环境温度发生变化,各组件热胀冷缩彼此挤压时存在一定活动余量。
16.本发明还提出了一种如上所述拼接式热敏打印头的装配方法,其特征在于包括以下步骤:
17.步骤1:装配拼接式热敏打印单元,将陶瓷基板与pcb板分别胶黏固定在金属基台上侧,其中陶瓷基板对应发热电阻安装区的下表面区域外悬于金属基台外;
18.步骤2:在散热板上表面设置导热硅脂填充层,在散热板上表面的导热硅脂填充层设置区刷涂高度为0.1-0.3mm,宽度为4-6mm的导热硅脂填充层;
19.步骤3:将两个以上拼接式热敏打印单元放置在散热板上,使每个拼接式热敏打印单元的陶瓷基板悬空处均经导热硅胶填充层与散热板紧密贴合,相邻的拼接式热敏打印单元之间保留间隙y;
20.步骤4:利用压板和锁紧螺钉将两个以上拼接式热敏打印单元固定在散热板上。
21.本发明提出了一种拼接式热敏打印单元以及拼接式热敏打印头,通过设置陶瓷基板部分悬空式结构,在陶瓷基板悬空部分与散热板之间设置导热性良好且不固化的导热硅脂填充层,保证陶瓷基板上的发热体电阻的散热效果,同时保证了陶瓷基板与散热板之间存在相对位移量,当产品处于由高温固化降至室温或低温保存等过程中,组件热胀冷缩对陶瓷基板产生挤压时,陶瓷基板相适应位移,避免陶瓷基板及其上的组件被损伤,具有结构合理、装配简便、打印质量高等显著的优点。
附图说明:
22.附图1是本发明实施例1中拼接式热敏打印单元的一种结构示意图。
23.附图2是本发明实施例1中pcb板与金属基台开孔示意图。
24.附图3是本发明中拼接式热敏打印头的一种结构示意图。
25.附图4是本发明实施例2中压板的一种结构示意图。
26.附图5是本发明实施例2中散热板的一种结构示意图。
27.附图6是本发明实施例2中拼接式热敏打印头的结构示意图。
28.附图7是本发明实施例2中条形螺钉孔的结构示意图。
29.附图8是本发明实施例2中相邻两个拼接式热敏打印单元设置示意图。
30.附图标记:发热体电阻1、陶瓷基板2、金属基台3、双面胶带4、pcb板5、封装胶6、连
接器7、导热硅脂8、散热板9、压板10、压紧螺丝11。
具体实施方式:
31.下面结合附图和实施例,对本发明作进一步的说明。
32.如附图3所示,本发明提出了一种拼接式热敏打印单元及热敏打印头,其中所述拼接式热敏打印单元包括陶瓷基板2、pcb板5以及底板,陶瓷基板2和pcb板5分别固定在底板上,陶瓷基板2的上表面设有发热体电阻安装区,发热体电阻安装区内设置发热体电阻1;陶瓷基板2的非发热电阻安装区与底板固定连接,陶瓷基板2对应发热体电阻安装区的下侧悬空;所述底板采用金属基台3,陶瓷基板3背面对应非发热电阻安装区的位置与金属基台3胶黏固定,pcb板5与金属基台3胶黏固定,pcb板5和金属基台3开设相对应的螺钉孔,螺钉孔呈条形,其中优选宽度4mm,长度6mm;
33.所述拼接式热敏打印头,设有散热板9,散热板9上设有两个以上的拼接式热敏打印单元,散热板9上开设螺钉孔,两个以上的拼接式打印单元分别经螺钉固定在散热板9上,其中拼接式打印单元的陶瓷基板2对应发热体电阻安装区的下表面与散热板9之间设有导热硅脂8填充层;导热硅脂8填充层高度范围为0.1-0.3mm,宽度范围为4.0-6.0mm;
34.本发明为了保证导热硅脂填充层稳定的位于陶瓷基板与散热板之间,在散热板的上表面开设两条彼此平行的导热硅脂导流槽,两条导热硅脂导流槽之间为导热硅脂填充层设置区,进一步,导热硅脂填充层设置区的高度略高于散热板其他区域高度,以便于安装时快速对齐两个以上拼接式热敏打印单元的对应位置。
35.本发明为了保证对两个以上拼接式热敏打印单元的快速对齐和固定,所述散热板上表面一侧设有对齐台阶,优选在散热板靠近导热硅脂填充层设置区的侧边设有对齐台阶,用于保证在装配过程中,两个以上拼接式热敏打印单元快速找正位置。
36.本发明两个以上的拼接式热敏打印单元分别经螺钉固定在散热板上,且相邻的拼接式热敏打印单元保留间隙y,y的宽度范围小于0.2mm,进一步优选y的宽度为0.15mm。
37.本发明为了提高拼接式热敏打印单元与散热板之间的固定效果,设有压板,压板上开设条形螺钉孔,安装时,螺钉依次穿过压板上的螺钉孔、两个以上拼接式打印单元上的螺钉孔后,与散热板上螺钉孔锁紧,螺钉采用m3盘头式螺丝,螺钉与条形螺钉孔为间隙配合,且螺丝与条形螺丝孔的间隙余量为1mm-3mm,当外界环境温度发生变化,各组件热胀冷缩彼此挤压时存在一定活动余量。
38.本发明还提出了一种如上所述拼接式热敏打印头的装配方法,其包括:装配拼接式热敏打印单元,将陶瓷基板与pcb板分别胶黏固定在金属基台上侧,其中陶瓷基板对应发热电阻安装区的下表面区域外悬于金属基台外;在散热板上表面设置导热硅脂填充层,在散热板上表面的导热硅脂填充层设置区刷涂高度为0.1-0.3mm,宽度为4-6mm的导热硅脂填充层;将两个以上拼接式热敏打印单元放置在散热板上,使每个拼接式热敏打印单元的陶瓷基板悬空处均经导热硅胶填充层与散热板紧密贴合,相邻的拼接式热敏打印单元之间保留间隙y;利用压板和锁紧螺钉将两个以上拼接式热敏打印单元固定在散热板上。
39.实施例1:
40.如附图1及附图2所示,本例提供了一种拼接式热敏打印单元,包括陶瓷基板2、pcb板5以及底板,陶瓷基板2和pcb板5分别固定在底板上,陶瓷基板2的上表面设有发热体电阻
安装区,发热体电阻安装区内设置发热体电阻1;陶瓷基板2的非发热电阻安装区与底板固定连接,陶瓷基板2对应发热体电阻安装区的下侧悬空;
41.所述底板采用金属基台3,陶瓷基板2背面对应非发热电阻安装区的位置与金属基台3经双面胶带4胶黏固定,pcb板5与金属基台3也经双面胶带4胶黏固定,pcb板5和金属基台3开设相对应的螺钉孔,螺钉孔呈条形,宽度4mm,长度6mm;为了提高pcb板、金属基台以及其他组件的固定稳定性,可以在pcb板、金属基台上沿直线设置两个以上的条形螺钉孔。
42.实施例2:
43.本例提供了一种拼装式热敏打印头及其制造方法,如附图4至附图8所示,包括绝缘材料构成的绝缘基板(即陶瓷基板3),pcb板5,金属基台3以及两个以上的单体热敏打印单元,其中采用金属基台3为底板,将陶瓷基板2与pcb板5用双面胶带4固定在金属基台3上,制作成单体热敏打印单元,该热敏打印单元的主打印方向的发热体电阻1背部无金属基台3,发热体电阻1的热量通过导热硅脂快速传导于散热板9,同时pcb板5与金属基台3各开两个长圆孔(条形螺钉孔):孔直径φ4mm,孔长6mm,紧螺丝为m3盘头螺丝,其外径为φ3mm,当两热敏打印单元因环境温度变化,热胀冷缩,发生挤压时,可以移动;
44.产品在制造组装时,将导热硅脂8涂敷在金属散热板9上,涂覆高度0.1~0.3mm,涂敷的宽度为4~6mm,导热硅脂要求的宽度与厚度是保证散热效果;
45.将两台及两台以上的单体热敏打印单元依次组合在散热板9上,调整两热敏打印单元上发热体电阻1的对应位置后,安放压板10,将压紧螺丝11通过压板10、热敏打印单元拧进散热板9上;压紧螺丝11的扭力为3~4kgf/cm;
46.其中附图4中为本例的压板10开孔图,条形螺钉孔的孔直径d2=4mm,孔宽度l2=6mm;附图5为本例中散热板9涂敷导热硅脂8的断面图,导热硅脂涂敷规格:厚度t=0.1~0.3mm,宽度w=4~6mm;附图6为本例中组立后的效果断面图,组立过程中需保证发热体电阻1下部的导热硅脂8无空腔;附图7为本例中压紧螺丝通过压板及与热敏打印头过孔配合尺寸示意;附图8为本例中热敏打印头的组立后的效果断面图,其中固定螺丝11与热敏打印单元1-1及热敏打印单元1-2之间存在间隙x,x=1.5mm,1-1与1-2之间的间隙y,y=0.15mm;当温度降低,热敏打印单元1-1与热敏打印单元1-2挤压,y=0,热敏打印单元与底部散热板9形成位移,x值减小,避免陶瓷基板碰伤;
47.本例采用的导热硅脂是硅油+填料等组成,目前可知的硅油基本上是甲基硅油、甲基苯基硅油、氯烃基改性硅油、氟氯烃改性硅油、长链烷基硅油等,填料为zno/al2o3/氮化硼/碳化硅/铝粉等,由于硅油对温度不敏感,且不挥发,低温不变稠,高温不会变稀,硅油保证了一定的流动性,而填料填充散热板与热敏打印头之间的微小缝隙,保证了导热性;具体地说,导热硅脂具有以下特性:
①
良好的热传导性能,导热系数从1.0w/m.k~4.5w/m.k;
②
较强的电绝缘性能,可耐压1万伏以上;
③
耐高低温性能好,可在-50℃~+230℃度(摄氏)的温度范围内使用;
④
防水,可渗透、不固化,化学性能稳定;
48.不选择使用导热硅胶,是因为导热硅胶是通过空气中的水份发生缩合反应放出低分子引起交联固化,而硫化成高性能弹性体;而导热硅脂不固化,能保证陶瓷基板与散热板之间保持相对位移。
49.本发明采用导热硅脂散热,用螺丝通过压板将热敏打印头压着在散热板上,利用导热硅脂具有的良好的导热性和不固化性,在温度降低时,相邻的两个热敏打印单元相互
挤压形成位移,避免引起的基板伤的现象,提高产品寿命。