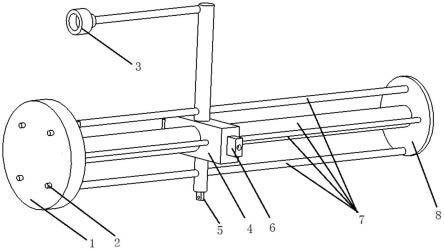
1.本实用新型属于飞机装配技术领域,涉及一种发动机装机模型装置,可高效快速的验证机体机构的准确性,提前发现可能存在的问题,从而保证正式发动机的快速装配,提高工作效率。
背景技术:2.飞机发动机是飞机的重要功能部件,其负责为飞机提供动力,对飞机安全起着关键作用。无论是军用飞机还是民用飞机,发动机尺寸均偏大,这就导致其在安装过程中对于飞机机体结构的装配精度要求高,但鉴于现有零部件生产制造以及装配技术难度大,无法保证高精度,故在原有的发动机安装工作中,由于飞机机体结构问题,需反复拆装发动机进行排故工作。
3.发动机除尺寸大的特点,还有着重量大、表面部件构成复杂以及价格昂贵的特点,反复拆装发动机验证工作存在损坏发动机的可能,对在此过程中操作失误,会导致飞机机构结构受损以及发动机受损的后果,除直接的经济损失外,还会导致飞机交付周期延期等不利后果。
技术实现要素:4.针对以上问题,本实用新型提供了一种发动机装机模型装置,该装置可有效模拟正式装机发动机的关键外形,设计有与机体结构装配的接口关系,可以实现模拟发动机安装。通过此项工作的进行,可避免正式发动机出现损伤的情况,且此发动机装机模型装置较正式装机发动机体积及重量均大幅度降低,在操作过程中较为轻松,安装工作效率高。
5.一种发动机装机模型装置,所述装置包括发动机外形模拟部件1、螺栓2、模拟受油口3、骨架支撑装置4、辅助安装孔5、推力销安装孔6、骨架钢管7、承力骨架8和支撑装置9。
6.所述的发动机外形模拟部件1用于模拟发动机最大理论外形,其根据装机发动机的实际外形尺寸设计,用于模拟检查装机发动机与飞机发动机舱内的机体机构之间的相对位置关系;所述的支撑装置9通过螺栓2连接在发动机外形模拟部件1一侧,支撑装置9一侧用于支撑发动机外形模拟部件1,且发动机外形模拟部件1可拆卸更换,支撑装置9另一侧与多个骨架钢管7焊接在一起做以支撑;所述的骨架钢管7贯穿整个发动机装机模型装置,连接装置各部件;所述的承力骨架8连接在骨架钢管7另一端,用于根据装置长度对骨架钢管7进行位置校正;所述的骨架支撑装置4为方形结构,其焊接连接在骨架钢管7中间段,是骨架钢管7的主要支撑装置,用于骨架钢管7的位置固定;所述的模拟受油口3安装于骨架支撑装置4上方,用于与飞机上管路的模拟安装,依次判断飞机上管路的制造与装配是否存在问题;所述的推力销安装孔6位于骨架支撑装置4两侧,用于在安装至机上时,插入飞机推力销实现模拟安装;所述的辅助安装孔5位于骨架支撑装置4下方,用于在安装至机上时,插入飞机辅助销实现模拟安装。
7.一种发动机装机模型装置的使用方法如下:
8.(1)根据不同飞机型号以及发动机种类,确定需求的装置具体尺寸;
9.(2)根据具体需求尺寸,选择相应的发动机外形模拟部件1并进行安装;
10.(3)将发动机装机模型装置放置在飞机上的正式发动机安装位置;
11.(4)调整发动机装机模型装置,使其辅助安装孔5以及推力销安装孔6与机体的安装孔同心;
12.(5)将推力销插入推力销安装孔6,将辅助销插入辅助安装孔5,实现发动机装机模型装置在机上的模拟安装;
13.(6)检查发动机装机模型装置与飞机机构的相对位置关系;
14.(7)检查结束后拆下推力销以及辅助销;
15.(8)将发动机装机模型装置放置存放位置;
16.(9)若飞机机体结构存在故障,则将故障处理后再次使用发动机装机模型装置放置验装;
17.(10)若不存在飞机机体结构故障或通过再次验装故障解决后,使用正式发动机装机固定。
18.本实用新型的有益效果:
19.(1)本实用新型采用独特的设计思路,其采用预装配的思路,可有效解决因飞机机体结构尺寸不稳定导致的反复拆装正式装机发动机的现状,可在使用此装置验证飞机机体结构无问题后再进行正式发动机的安装工作,从而实现一次装配,避免正式装机发动机出现损伤等情况;
20.(2)本实用新型设计的发动机外形模拟部件与支撑装置采用螺接形式,可根据实际需求,按发动机型号,按照不同的尺寸参数选择不同的发动机外形模拟部件,实现更换,同一装置可实现对不同型号发动机的预安装工作,使用灵活,效率高;
21.(3)本实用新型使用骨架钢管,可在模拟出正式装机发动机关键尺寸参数以及关键装配位置的情况下,最大程度减轻装置的重量,可以在安装过程中减轻人力成本,大幅度提高工作效率。
附图说明
22.图1为一种发动机装机模型装置主视图。
23.图2为一种发动机装机模型装置局部侧视图。
24.图中:1发动机外形模拟部件;2螺栓;3模拟受油口;4骨架支撑装置;5辅助安装孔;6推力销安装孔;7骨架钢管;8承力骨架;9支撑装置。
具体实施方式
25.以下结合附图和技术方案,进一步说明本实用新型的具体实施方式。
26.实施例
27.一种发动机装机模型装置,所述装置包括发动机外形模拟部件1、螺栓2、模拟受油口3、骨架支撑装置4、辅助安装孔5、推力销安装孔6、骨架钢管7、承力骨架8和支撑装置9,如图1所示。
28.所述的发动机外形模拟部件1用于模拟发动机最大理论外形,其根据装机发动机
的实际外形尺寸设计,用于模拟检查装机发动机与飞机发动机舱内的机体机构之间的相对位置关系;所述的支撑装置9通过螺栓2连接在发动机外形模拟部件1一侧,支撑装置9一侧用于支撑发动机外形模拟部件1,且发动机外形模拟部件1可拆卸更换,支撑装置9另一侧与多个骨架钢管7焊接在一起做以支撑,如图2所示;所述的骨架钢管7贯穿整个发动机装机模型装置,连接装置各部件;所述的承力骨架8连接在骨架钢管7另一端,用于根据装置长度对骨架钢管7进行位置校正;所述的骨架支撑装置4为方形结构,其焊接连接在骨架钢管7中间段,是骨架钢管7的主要支撑装置,用于骨架钢管7的位置固定;所述的模拟受油口3安装于骨架支撑装置4上方,用于与飞机上管路的模拟安装,依次判断飞机上管路的制造与装配是否存在问题;所述的推力销安装孔6位于骨架支撑装置4两侧,用于在安装至机上时,插入飞机推力销实现模拟安装;所述的辅助安装孔5位于骨架支撑装置4下方,用于在安装至机上时,插入飞机辅助销实现模拟安装。
29.一种发动机装机模型装置的使用方法如下:
30.(1)根据不同飞机型号以及发动机种类,确定需求的装置1具体尺寸;
31.(2)根据具体需求尺寸,选择相应的发动机外形模拟部件1并进行安装;
32.(3)将发动机装机模型装置放置在飞机上的正式发动机安装位置;
33.(4)调整发动机装机模型装置,使其辅助安装孔5以及推力销安装孔6与机体的安装孔同心;
34.(5)将推力销插入推力销安装孔6,将辅助销插入辅助安装孔5,实现发动机装机模型装置在机上的模拟安装;
35.(6)检查发动机装机模型装置与飞机机构的相对位置关系;
36.(7)检查结束后拆下推力销以及辅助销;
37.(8)将发动机装机模型装置放置存放位置;
38.(9)若飞机机体结构存在故障,则将故障处理后再次使用发动机装机模型装置放置验装;
39.(10)若不存在飞机机体结构故障或通过再次验装故障解决后,使用正式发动机装机固定。
40.以上所述实施例仅表达本实用新型的实施方式,但并不能因此而理解为对本实用新型专利的范围的限制,应当指出,对于本领域的技术人员来说,在不脱离本实用新型构思的前提下,还可以做出若干变形和改进,这些均属于本实用新型的保护范围。