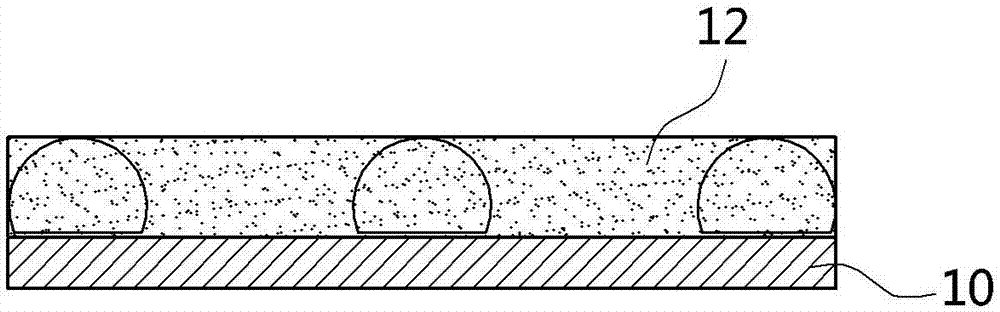
本申请要求于2014年11月27日提交的韩国专利申请no.10-2014-0167056和于2015年11月27日提交的韩国专利申请no.10-2015-0167488的优先权,在相应的韩国专利申请的文献中公开的全部内容作为本说明书的一部分被包含。本发明涉及一种基板接合方法和由该基板接合方法制备的显示基板。
背景技术:
:近来,为了实现各种功能,已经将用于显示设备的基板在向其粘附功能薄膜的同时来使用。由于电子设备具有尺寸减小以及性能改善的趋势,因此,需要更轻、更薄、更短和更紧凑的电子产品作为技术问题。同时,在接合基板玻璃与薄膜的常规方法中,使用厚度为约100μm的透明粘合剂片来粘接它们。然而,存在不足以满足目前客户对显示材料的较高的功能性、较小的尺寸和较薄的厚度的要求的问题。因此,已经使用诸如棒涂布或狭缝式模具涂布的印刷技术来接合基板玻璃和具有10μm以下的较小的均匀厚度的薄膜。然而,所述方法也具有局限性,即基板和功能薄膜不能以均匀的厚度彼此接合,并且不能达到足够小的厚度。技术实现要素:技术问题在常规的基板接合方法中,使用诸如棒涂布或狭缝式模具涂布的印刷技术。然而,所述方法在实现具有均匀的厚度和较小的厚度的接合层方面具有局限性。因此,本发明的一个目的是提供一种使用印刷工艺的基板接合方法。特别地,本发明的一个目的是通过使用印刷工艺形成间隔体(spacer)以均匀的厚度接合下基板和上基板。另外,本发明的一个目的是提供一种不仅以均匀的厚度,而且以较小的厚度接合下基板和上基板的方法。此外,本发明的一个目的是提供一种能够通过使用本发明的接合方法而用于各种显示器的基板。技术方案为了实现所述目的,本发明提供一种基板接合方法,该基板接合方法包括以下步骤:(1)通过在下基板上喷墨印刷光固化粘合剂油墨形成图案;(2)通过使所述图案光固化在下基板上形成间隔体;(3)通过在其上形成有间隔体的下基板的表面上喷墨印刷所述光固化粘合剂油墨形成粘合层;以及(4)通过进行光固化使下基板的粘合层和上基板层合。根据本发明的一个优选实施方案,下基板和上基板可以是玻璃或薄膜。另外,步骤(1)中的图案可以是选自点图案和线图案中的任意一种或多种,并且所述图案可以额外包括在基板的外围(outeredge)上的隔离墙(partitionwallpattern)图案。根据本发明的一个优选实施方案,隔离墙图案可以是部分开放的形状,并且隔离墙图案可以具有圆边部分。根据本发明的一个优选实施方案,光固化粘合剂油墨可以通过uv固化或电子束固化而固化,并且可以包含环氧化合物、光聚合引发剂、表面活性剂、光稳定剂和溶剂。根据本发明的一个优选实施方案,步骤(2)中的光固化可以通过使用强度为50至500mw/cm2的uv照射进行5至500秒,或者可以通过使用电子束进行5至500秒。根据本发明的一个优选实施方案,间隔体的高度可以是1.0至10μm。根据本发明的一个优选实施方案,间隔体之间的点间距可以是300μm以上,优选是300至2,500μm。根据本发明的一个优选实施方案,当在步骤(3)中形成粘合层时,喷墨印刷的点间距可以是100至150μm。本发明的另一方面提供一种通过本发明的基板接合方法制备的显示基板。有益效果本发明可以提供一种使用喷墨工艺的基板接合方法。另外,本发明可以通过使用喷墨工艺在较短的时间内以非接触的方式形成所需的图案。此外,本发明可以以均匀的间距接合上基板和下基板。另外,基板通过使用具有较小的厚度的粘合层来接合,因此可以用于各种显示设备。附图说明图1a至图1c是根据本发明的一个优选实施方案的基板接合方法的示意图;图2a至图2c是根据本发明的一个优选实施方案的基板接合方法的示意图;图3a和图3b是根据本发明的一个优选实施方案的在基板上形成的图案的示意图;图4a至图4c是根据本发明的另一优选实施方案的在基板上形成的图案的示意图;图5是根据本发明的试验实施例1的间隔体的横截面形状的图;图6是示出根据本发明的试验实施例2的实施例和比较例的粘合强度试验结果的图;图7是示出在本发明的试验实施例2中的根据比较例制备的基板的照片。具体实施方式下文中,将详细描述本发明。下面的具体说明描述了本发明的示例性实施方案,因此,即使存在限定的表达,也不意在限制权利要求书所限定的权利范围。在现有技术中的基板接合方法中,使用诸如棒涂布或狭缝式模具涂布的印刷技术。然而,所述方法在实现以均匀的厚度和较小的厚度接合方面具有局限性。因此,作为为了解决上述问题而进行的深入研究的结果,本发明人发现,当通过使用喷墨工艺来接合基板时,厚度可以调节。也就是说,本发明提供一种基板接合方法,该基板接合方法包括以下步骤:(1)通过在下基板上喷墨印刷光固化粘合剂油墨形成图案;(2)通过使所述图案光固化在下基板上形成间隔体;(3)通过在其上形成有间隔体的下基板的表面上喷墨印刷所述光固化粘合剂油墨形成粘合层;以及(4)通过进行光固化来使下基板的粘合层和上基板层合。本发明的点是指在喷墨工艺中通过喷墨加热由光固化粘合剂的排出物在基材上形成的液滴。图1a至图1c和图2a至图2c是根据本发明的一个优选实施方案的基板接合方法的示意图。当具体描述所述方法时,在图1a和图2a中,使通过喷墨工艺形成的光固化粘合剂图案固化,结果,在下基板10上形成间隔体11。此外,在图1b和图2b中,将光固化粘合剂油墨喷射到其上形成有间隔体的下基板的整个表面上,结果,形成粘合层。在图1c和图2c中,通过进行光固化使粘合层和上基板层合,从而将下基板接合至上基板。下文中,将描述本发明的基板接合方法。首先,将描述步骤(1)。在该步骤中,通过在下基板上喷墨印刷光固化粘合剂油墨形成图案。具体地,可以使用光固化粘合剂油墨并通过喷墨印刷机的喷墨头将其喷射在下基板上,从而形成作为点的图案。根据本发明的一个优选实施方案,下基板可以是玻璃或薄膜。此外,可以使用任何薄膜,只要该薄膜是通常使用的即可,并且基板可以根据预期用途适当地来选择和使用。如果使用热固化粘合剂油墨,由于伴随有高温调节,因此难以使用薄膜作为基板。然而,在本发明中,通过使用光固化粘合剂油墨,在使用基板中,可以没有任何限制地使用薄膜。可以使用任何油墨,只要光固化粘合剂油墨可以通常使用即可,所述光固化粘合剂油墨可以优选地包含环氧化合物、光聚合引发剂、表面活性剂、光稳定剂和溶剂。此外,除了上述成分之外,光固化粘合剂油墨还可以包含防腐剂以及ph调节剂中的一种或多种。根据本发明的一个优选实施方案,光固化粘合剂油墨可以用于uv固化或电子束固化,并且可以优选地用于uv固化。根据本发明的一个优选实施方案,步骤(1)中的图案可以包括选自点图案和线图案中的任意一种或多种。当参考图3a和图3b描述步骤(1)中的图案时,在图3a中,通过使用点在基板上形成点图案,在图3b中,点彼此连接以形成线图案。在本发明中,在基本上保持图案的形状的同时形成间隔体。也就是说,由于本发明提出的光固化粘合剂油墨被固化,然后几乎不收缩,因此可以保持它本来的形状。然而,当液滴被排出然后没有立即固化时,形状会随着粘度或表面张力而改变,但是液滴会稍微铺展。然而,也可以看出,当液滴被排出然后立即固化时,几乎没有异样。同时,当形成图案时,必须调整图案的排布和形状,使得在层压上基板的步骤(4)中,空气容易排出。在该步骤中,可以通过调整喷射过程中的点直径、点高度和点间距形成图案。此外,如上所述的点直径、点高度和点间距可以通过光固化粘合剂油墨的喷射条件或/和组成来调节。根据本发明的一个优选实施方案,步骤(1)中的点间距可以是300至2,500μm,优选是500至1,800μm。如果点间距小于300μm,当在步骤(3)中通过将油墨涂布在下基板的整个表面上形成粘合层时,由于毛细管效应,油墨不会在整个基板上均匀地铺展。此外,会存在作为点的间隔体之间产生气孔的问题,结果,基板不整齐地接合,并且容易分离。此外,当点间距大于2,500μm时,由于基板的下垂等,会难以均匀地接合基板。根据本发明的一个优选实施方案,图案可以额外包括在基板的外围上的隔离墙图案。隔离墙图案用于防止在步骤(3)中当喷墨印刷光固化粘合剂油墨时粘合剂油墨溢出到接合表面的外部。此外,隔离墙图案可以是部分开放的形状。当隔离墙图案是部分开放的形状时,当进行步骤(3)时,多余的粘合剂会通过开口部分溢出到外部,从而有助于在随后的工艺中除去多余的粘合剂。此外,隔离墙图案可以具有圆边部分。在形成隔离墙时,为了防止气泡在边缘部分处聚集,可以通过将边缘形成为圆形来解决边缘部分处气泡的聚集。当参考图4a至图4c描述本发明的图案时,在图4a中,在基板的外围上形成隔离墙图案并且在隔离墙图案内部形成点图案。在图4b中,在基板的外围上形成部分开放的形状的隔离墙图案,并且在隔离墙图案内部形成点图案。在图4c中,在基板的外围上形成具有圆边部分的隔离墙图案,并且在隔离墙图案内部形成线图案。此外,线图案是可以移除当在步骤(4)中将光固化粘合剂油墨涂布至下基板的整个表面上时形成的气泡的图案。接下来,将描述步骤(2)。该步骤是通过使步骤(1)中的光固化粘合剂油墨图案固化形成间隔体的步骤。光固化可以根据步骤(1)中使用的光固化粘合剂油墨的种类来进行。根据本发明的一个优选实施方案,光固化可以是紫外线(uv)固化或电子束(e-beam)固化,并且可以优选是紫外线(uv)固化。此外,可以使用任何方法,只要可以通常使用紫外线(uv)固化即可,但是,优选地,紫外线(uv)固化可以在50至500mw/cm2的强度下进行5至500秒。此外,电子束固化可以进行5至500秒。本发明的间隔体用作支撑体,用来以均匀的间距接合下基板和上基板,并且可以具有与在步骤(1)中形成的粘合剂油墨的图案相同的形状和尺寸。也就是说,间隔体的高度可以是1.0至10μm。如果间隔体的高度小于1.0μm,会难以形成间隔体,如果所述高度大于10μm,难以形成较薄的粘合层。接下来,将描述步骤(3)。在该步骤中,根据在步骤(2)中通过喷墨工艺形成的间隔体的高度,通过将光固化粘合剂油墨喷射在其上形成有间隔体的下基板的整个表面上形成粘合层。也就是说,根据本发明的一个优选实施方案,粘合层的厚度可以是1.0至10μm,相当于间隔体的高度。此外,在该步骤中的光固化粘合剂可以与步骤(1)中的粘合剂相同。作为现有技术中的基板接合方法,通过使用粘合剂片作为粘合层来接合基板。或者,作为现有技术中的另一方法,通过棒涂布或狭缝式涂布形成粘合层。然而,通过现有技术中的方法,难以以均匀的间距形成粘合层,并且难以形成厚度较小的粘合层。因此,本发明可以具有均匀的间距,并且可以通过喷墨工艺形成间隔体形成与间隔体的高度一致的粘合层,从而形成具有较小的厚度的粘合层。因此,可以均匀地实现下基板和上基板之间的对齐,从而接合厚度为10μm以下(是与间隔体的高度相同的高度)的粘合层。根据本发明的一个优选实施方案,步骤(3)中的点间距可以为50至200μm,优选地为100至150μm。如果点间距小于50μm,会存在如下问题:当形成步骤(3)中的粘合层时,涂布至整个表面的油墨的量太多,以至于油墨溢出并且难以仅接合所需的区域。此外,如果点间距大于200μm,会存在如下问题:当形成步骤(3)中的粘合层时,涂布至整个表面的油墨的量太少,以至于不能很好地粘附上基板。也就是说,由于步骤(1)中的点间距是用于形成图案的间距,并且步骤(3)中的点间距是用于形成粘合层的间距,因此它们的范围彼此不同。接下来,将描述步骤(4)。该步骤是通过将上基板粘附至步骤(3)中形成的粘合层,通过进行光固化来将上基板层压至步骤(3)中形成的粘合层的步骤。该步骤的光固化可以根据粘合层的种类进行,光固化粘合剂可以与步骤(1)中的粘合剂相同。此外,根据本发明的一个优选实施方案,上基板可以是玻璃或薄膜。总之,在本发明中,通过使用喷墨工艺并形成间隔体,下基板和上基板可以以均匀且较小的厚度彼此接合。本发明的另一方面提供一种通过本发明的基板接合方法制备的显示基板。下文中,将基于实施例更详细地描述本发明,但是下面将要公开的本发明的示例性实施方案仅是说明性的,本发明的范围不局限于这些示例性实施方案。本发明的范围由权利要求书限定,并且意在包括在与权利要求书等同的含义和范围内的任何改变。此外,在下面的实施例和比较例中,除非另外特别提及,否则表示含量的“%”和“份”是重量标准。实施例1通过使用一次排出的uv粘合剂油墨的量为80pl的nova头将初级油墨喷射在作为下基板的玻璃基板上。将在油墨的喷射过程中制备的点形成为直径平均为200μm且高度平均为3.5μm。此外,nova头的喷嘴间距为279μm,并且形成间距为558μm的点图案。通过波长为395nm的uv灯将形成的点图案固化约5秒,从而形成间隔体。然后,将与在初级油墨喷射中相同的uv粘合剂涂布至其上形成有间隔体的基板的整个表面,从而形成厚度为3.5μm的粘合层。对于在整个表面上的涂布,通过使喷墨头倾斜以将点间距确定为150μm来涂布uv粘合剂。当整个表面的涂布完成时,将作为上基板的玻璃粘附至下基板,然后以与使用uv灯形成间隔体时相同的方式进行固化5秒来将上基板完全接合至下基板。实施例2至6和比较例1至10除了采用下面的表1中的间隔体间距和点间距之外,以与实施例1相同的方式进行试验。[表1]间隔体间距在涂布整个表面的过程中的点间距实施例1558μm150μm实施例2558μm100μm实施例31116μm150μm实施例41116μm100μm实施例52232μm150μm实施例62232μm100μm比较例1279μm50μm比较例2279μm100μm比较例3279μm150μm比较例4279μm200μm比较例5558μm50μm比较例6558μm200μm比较例71116μm50μm比较例81116μm200μm比较例92232μm50μm比较例102232μm200μm比较例11通过使用一次排出的uv粘合剂油墨的量为80pl的nova头将油墨喷射在作为下基板的玻璃基板上。将在油墨的喷射过程中制备的点形成为直径平均为200μm且高度平均为3.5μm。此外,nova头的喷嘴间距为279μm,并且形成间距为558μm的点图案。然后,通过将作为上基板的玻璃粘附至下基板来将上基板接合至下基板。试验实施例1通过使用α台阶(α-台阶)测量仪器,由实施例1测量间隔体的横截面形状,结果示于图5中。最后,通过图5能够证实,点直径为200μm,高度为3.5μm。试验实施例2通过对实施例1至6和比较例1至11中的接合后的玻璃基板施加约1,000gf/cm2的握力强度来测定接合强度。○:由于优异的接合强度而不分离×:由于较差的接合强度而分离从图6中可以看出,通过将粘合剂涂布于整个表面以形成粘合层,同时,当形成作为点图案的间隔体时将点间距充分地确定为300μm以上,在粘合层的形成过程中,当点间距为150μm以下且为100μm以上时,实施例1至6具有优异的接合强度。相反,可以看出,比较例1至10不能满足间隔体的点间距以及粘合层的形成过程中的点间距,结果,接合强度劣化。另外,从图7可以看出,在比较例11中,形成的点被压碎,并且难以形成均匀的间距。[附图标记说明]10:下基板11:间隔体12:粘合层13:上基板当前第1页12