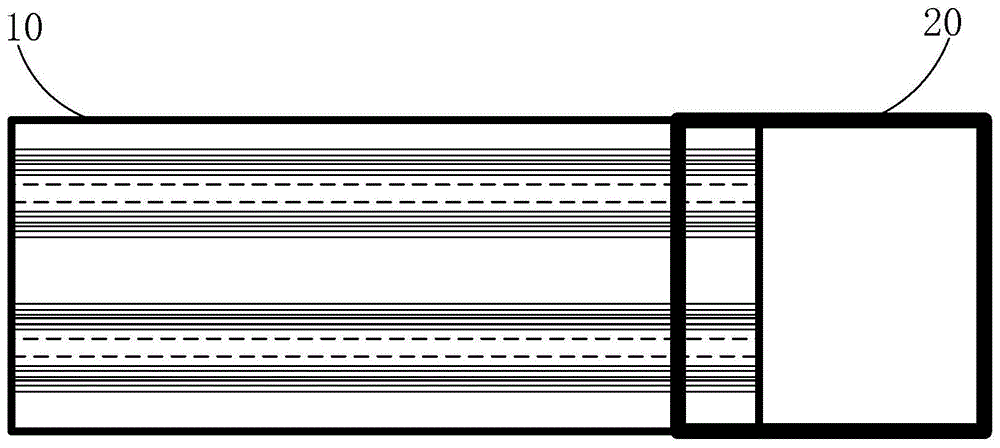
【
技术领域:
】本发明涉及光纤
技术领域:
,更具体地,涉及一种光纤耦合器和光纤耦合的方法。
背景技术:
:由于多芯光纤可提供空间这种新的复用维度,可以极大增加通信系统容量,为满足今后通信系统需求,多芯光纤在通信系统中的使用愈发受到重视。多芯光纤通信系统需要与现有单模光纤通信系统相兼容,就需要多芯光纤和单模光纤实现低损耗连接。为了连接单模光纤和多芯光纤,通常使用光纤耦合器作为桥梁。因此光纤耦合器和光纤耦合器中的桥接光纤成为推广多芯光纤实际应用与降低多芯光纤使用成本的关键技术之一。目前,多芯光纤耦合器制备通常使用多包层光纤的熔融拉锥法来制备,如申请号为:201811089100.0和201811393656.9的专利提供的技术方案,但其所使用的桥接光纤都是单芯多包层光纤。单芯多包层光纤作为桥接光纤时,会使用熔融拉锥法将多根标准单模光纤与多根多单芯包层光纤进行熔接,并穿入套管内进行拉锥,再经过切割后与多芯光纤熔接。由于对多根单芯多包层光纤组成的光纤束拉锥与切割精度难以控制,这种方法的插入损耗比较大。综上所述,目前各类多芯光纤耦合器制备过程中都受到所使用的桥接光纤类型的影响,使得加工精度、加工难度、成本以及损耗等方面都存在问题。技术实现要素:针对现有技术的缺陷,本发明的目的在于解决现有光纤耦合器加工精度、加工难度、成本以及损耗等方面都存在不足的技术问题。为实现上述目的,第一方面,本发明提供了一种光纤耦合器,包括多芯多包层光纤10和套管20;多芯多包层光纤10的第一端与套管20耦合;多芯多包层光纤10包含至少两根纤芯11,每根纤芯11的外部的包层自内向外依次包括:内包层12、下陷内包层13、环形包层14、外包层15、下陷外包层16和机械包层17;多芯多包层光纤10的外表面半径大于预设最小半径,任两个纤芯11的芯间距大于预设最小芯间距。优选的,下陷内包层13的折射率小于纤芯11的折射率,下陷内包层13的折射率小于内包层12的折射率,下陷外包层16的折射率小于外包层15的折射率。优选的,多芯多包层光纤10的每个纤芯11外的包层成阶跃型折射率剖面。优选的,每个包层的半径位于该包层的预设半径范围之内,每个包层的相对折射率差位于该包层的预设相对折射率差范围之内。优选的,多芯多包层光纤10的每个纤芯11的性能相同。第二方面,本发明还提供了一种光纤耦合的方法,其步骤包括:获取一个第一方面中提供的光纤耦合器1;对光纤耦合器1的多芯多包层光纤10的第二端进行拉锥处理,使多芯多包层光纤10第二端的芯间距达到预设芯间距阈值,并将多芯多包层光纤10的第二端与多芯光纤2固定;将单模光纤3穿入光纤耦合器1的套管20内,每根单模光纤3与多芯多包层光纤10的一个纤芯11对准并固定。优选的,对光纤耦合器1的多芯多包层光纤10的第二端进行拉锥处理,具体包括:多芯多包层光纤(10)的第二端拉锥前的纤芯11、内包层12、下陷内包层13和环形包层14构成被拉锥后的纤芯,多芯多包层光纤10的第二端拉锥前的外包层15、下陷外包层16和机械包层17构成拉锥后的包层。优选的,将多芯多包层光纤10的第二端与多芯光纤2固定,具体包括:将多芯多包层光纤10的第二端进行切割,切割后的端面与多芯光纤2进行熔接。优选的,每根单模光纤3与多芯多包层光纤10的一个纤芯11对准并固定之前,还包括:剥去每一根单模光纤3的涂覆层,并对单模光纤3进行切割。优选的,每根单模光纤3与多芯多包层光纤10的一个纤芯11对准并固定,具体包括:将一根单模光纤3穿入套管20;将单模光纤3与多芯多包层光纤10的一个纤芯11对准,对准后进行固定;依次完成所有单模光纤3与多芯多包层光纤10的每个纤芯11的对准和固定。总体而言,通过本发明所构思的以上技术方案与现有技术相比,具有以下有益效果:本发明提供的光纤耦合器的桥接光纤包括多个多包层的纤芯,其多芯多包层光纤包括:纤芯、内包层、下陷内包层、环形包层、外包层、下陷外包层以及机械包层,其制备过程简单,不需要腐蚀等处理,可扩展性好,成品率高。本发明提供的光纤耦合器,在一根光纤中包括多个多包层的纤芯,其下陷内包层作为沟道,其折射率小于纤芯和内包层,在光纤发生弯曲时可以限制场的覆盖范围,避免场向环形包层泄露,因此多芯多包层光纤具有小的宏弯损耗。本发明提供的多芯光纤耦合器将多芯多包层光纤经过拉锥之后,纤芯、内包层、下陷内包层、环形包层形成新的纤芯,外包层、下陷外包层、机械包层构成新的包层,因此在和多芯光纤熔接时具有较低的熔接损耗。通过多芯多包层光纤和标准单模光纤模场的匹配,使得多芯多包层光纤和标准单模光纤熔接时具有低的熔接损耗。本发明提供的光纤耦合器,由于多芯多包层光纤的下陷外包层的折射率小于外包层,可以限制场的覆盖范围,避免场向外泄露,因此和多芯光纤熔接后具有小的芯间串扰。本发明提供的光纤耦合器的制备方法以及本发明提供的光纤耦合方法,工艺流程的步骤较少,同时避免了光纤束切割难度较高的问题,重复性高,易于实现。【附图说明】为了更清楚地说明本发明实施例的技术方案,下面将对本发明实施例中所需要使用的附图作简单地介绍。显而易见地,下面所描述的附图仅仅是本发明的一些实施例,对于本领域普通技术人员来讲,在不付出创造性劳动的前提下,还可以根据这些附图获得其他的附图。图1为本发明提供的一种光纤耦合器的结构示意图;图2为现有的光纤耦合器结构及耦合方式示意图;图3为本发明提供的一种光纤耦合器的耦合方式示意图;图4本发明提供的一种光纤耦合器中每个纤芯外部的包层结构示意图;图5为本发明提供的一种光纤耦合器中每个纤芯外部的包层折射率示意图;图6为本发明提供的一种光纤耦合方法流程图;图7为使用本发明提供的光纤耦合方法进行耦合后的连接结构示意图;图8为本发明提供的一种光纤耦合方法流程图;图9为使用本发明提供的光纤耦合方法进行耦合后的连接结构示意图;其中,附图标记如下:10:多芯多包层光纤,11:纤芯,12:内包层,13:下陷内包层,14:环形包层,15:外包层,16:下陷外包层,17:机械包层,20:套管,1:光纤耦合器,2:多芯光纤,3:单模光纤,4:多芯多包层光纤10与多芯光纤2熔接截面,5:单模光纤3与多芯多包层光纤10熔接截面。【具体实施方】为了使本发明的目的、技术方案及优点更加清楚明白,以下结合附图及实施例,对本发明进行进一步详细说明。应当理解,此处所描述的具体实施例仅用以解释本发明,并不用于限定本发明。此外,下面所描述的本发明各个实施方式中所涉及到的技术特征只要彼此之间未构成冲突就可以相互组合。首先,对本发明中涉及的一些术语的定义做如下说明:(1)相对折射率差δi:其中δi为纤芯各包层的相对折射率差,ni为第i层光纤材料的折射率,n0为最外层机械包层的折射率。各包层的折射率分布为该包层在各径向点处的折射率值,除非另做说明,本发明中δi均为各纤芯包层中的绝对值最大的相对折射率差。(2)半径:ri表示各包层的半径,下标i取值为i={1,2,3,4,5,6,7},依次表示由内到外的各包层,ri为从光纤的中心线到该包层离中心线最远的点的距离。实施例1:为了解决现有的单芯多包层光纤作为光纤耦合器的桥接光纤时插入损耗大的问题,可以使用多芯多包层光纤作为桥接光纤,但是,普通的多芯多包层光纤的最外层直径与单模光纤最外层直径接近,无法直接与多根单模光纤进行耦合。本发明实施例提供了一种光纤耦合器,使用多芯多包层光纤作为桥接光纤,每个包层具备特定的光学性能参数,并且包层半径满足一定的规格,不仅可以简单方便的和标准单模光纤实现低损耗熔接,而且通过微拉锥方法制备后,可以和多芯光纤之间实现低损耗熔接。如图1所示的纵向剖面图,本实施例提供的光纤耦合器包含多芯多包层光纤10和套管20。本实施例使用的各结构示意图中,虚线表示纤芯,细实线表示纤芯外部的包层,粗实线表示光纤和套管的外表面。为了简化图示线条,图1中多芯多包层光纤10在剖面中显示的纤芯11数量为2个,实际使用中,可以根据需要耦合的多芯光纤的纤芯数量选择合适的纤芯11数量。在现有光纤耦合技术方案中,如图2所示的纵向剖面图,一般使用多根单芯多包层光纤作为桥接光纤,每根桥接光纤的第二端分别与一根单模光纤连接,再将多根桥接光纤的第一端穿入套管内后,将多根桥接光纤与套管一起进行拉锥和切割,并将拉锥和切割后的第一端与多芯光纤熔接。该方案中,需要对多根桥接光纤组成的光纤束进行拉锥与切割,切割过程有很大误差,会导致光纤束端面不平整,使耦合后的插入损耗较大。在本实施例提供的技术方案中,如图3所示的纵向剖面图,使用多芯多包层光纤10作为桥接光纤,多芯多包层光纤10包含至少两根纤芯11,使用多芯多包层光纤10作为桥接光纤时,将单模光纤穿入与多芯多包层光纤10的第一端耦合的套管20中,每根单模光纤分别对准一根纤芯11并固定连接,多芯多包层光纤10的第二端被拉锥和切割后与多芯光纤连接。本实施例提供的光纤耦合器,第一端通过套管辅助,每个纤芯11分别与一个单模光纤连接固定,加工较为简便;另一方面,第二端与多芯光纤连接时,直接对一根多芯多包层光纤10进行拉锥和切割,而不需要对多根光纤组成的光纤束进行拉锥和切割,工艺难度较小,造成的误差也较小,能够降低耦合后的插入损耗。光纤耦合器的作用是将多芯光纤中每一根纤芯中的光信号导入至一根对应单模光纤中去,因此需要与多根单模光纤连接。由于普通的多芯光纤最外层直径与普通单模光纤直径较为接近,因此无法直接使用一根多芯光纤作为桥接光纤与多根单模光纤连接。例如,最常用7芯光纤的外部直径一般为150μm,芯间距42μm,而g.652标准单模光纤包层直径一般为125μm,纤芯直径8.8μm。由上述数据可见,普通7芯光纤的外部直径与标准单模光纤接近,无法直接作为耦合器同时与多根单模光纤连接。本实施例中提供的光纤耦合器中,多芯多包层光纤10的外表面半径需要达到预设最小半径,任两个纤芯11之间的芯间距也需要达到最小预设芯间距,以提供充足的空间固定多根单模光纤,满足与多根单模光纤连接的需求。在本发明实施例的具体使用中,预设最小半径和预设最小芯间距根据实际连接的单模光纤的半径、纤芯直径和数量确定。本实施例中为了与多根单模光纤连接,使用了半径较大的多芯多包层光纤10作为桥接光纤,多芯多包层光纤10的第二端半径会大于普通多芯光纤,因此,在使用本实施例提供的光纤耦合器与多芯光纤连接时,需要将第二端进行拉锥以匹配普通多芯光纤的直径以及纤芯距。进一步的,为了降低耦合连接后的插损,多芯多包层光纤10中的每一个纤芯11的模场都需要与其连接的光纤的模场相匹配。为了保证不需要拉锥的第一端与每一根单芯单模光纤的模场匹配,同时还要保证需要拉锥的第二端与多芯光纤的每一个纤芯的模场匹配,因此每个纤芯11外部需要包裹多个特定光学参数和结构的包层。如图4所示,为图1中每个纤芯11及其外部包层的截面图放大后的示意图,每根纤芯11外部的包层自内向外依次包括:内包层12、下陷内包层13、环形包层14、外包层15、下陷外包层16和机械包层17。对多芯多包层光纤10的第二端进行拉锥后,纤芯11、内包层12、下陷内包层13和环形包层14构成拉锥后的纤芯,外包层15、下陷外包层16和机械包层17构成拉锥后的包层,多芯多包层光纤10的第二端拉锥后与多芯光纤熔接。为了保证拉锥前后各包层的光学性能,多芯多包层光纤10的每个纤芯11外的包层成阶跃型折射率剖面结构,纤芯11以及各个包层内部的折射率均匀分布,且在纤芯11和内包层12,以及各个包层与其相邻的包层的分界面处折射率发生突变。各包层的折射率分布如图5所示,可见每个包层内部的折射率保持均匀一致,但是在各个层交界面处折射率发生突变。图5中,横坐标表示图4中各结构的半径区间,纵坐标仅为相对值大小的参考,不包含具体数值含义。进一步的,如图5所示,下陷内包层13的折射率小于纤芯11的折射率,且小于内包层12的折射率。因此,下陷内包层13可以作为沟道,在光纤发生弯曲时限制场的覆盖范围,避免场向环形包层14泄露,使多芯多包层光纤10具有小的宏弯损耗。下陷外包层16的折射率小于外包层15的折射率,可以限制场的覆盖范围,避免场向外包层15泄露,因此多芯多包层光纤10和多芯光纤熔接后会具有小的芯间串扰。为了使光纤耦合器具有最佳的光学性能,每根纤芯11的每个包层的半径位于该包层的预设半径范围之内,每根纤芯11每个包层的相对折射率差位于该包层的预设相对折射率差范围之内。在发明本实施例的实际使用中,预设半径范围和预设相对折射率差范围参考各包层材料不同、多芯多包层光学的预设最小半径和预设最小芯间距不同、以及加工精度的不同等因素,根据实际光学测试结果确定,以耦合后能获得最佳光学性能为标准。以下提供一组可供使用的预设半径范围和预设相对折射率差范围。该范围值仅为某一具体场景中的实施实例,在不同的实施场景中,任何可获得耦合后最佳光学性能的材质、预设半径范围和预设相对折射率范围组合都包含在本发明实施例的保护范围之内,而不限于本实施例提供的具体数据。本发明实施例虽未做具体举例,但本领域技术人员可以理解的是,上述参数范围均可使得制备的多芯光纤耦合器相比现有技术具有改进。纤芯11为掺锗的石英玻璃层,其半径r1为4.7μm~4.9μm,相对折射率差δ1为0.54%~0.81%。内包层12主要掺有锗,其半径r2为10.2μm~10.6μm,相对折射率差δ2为0.21%~0.48%。下陷内包层13的半径r3为14.8μm~16.8μm,相对折射率差δ3为-0.14%~0.14%。环形包层14主要掺有锗,其半径r4为19.7μm~21.7μm,相对折射率差δ4为0.23%~0.50%。外包层15的半径r5为30.0μm~35μm,相对折射率差δ5为0.0%。下陷外包层16主要掺有氟,其半径r6为40.0μm~44.6μm,相对折射率差δ6为-0.62%~-0.34%。机械包层17的半径r7为60.0μm~65.0μm,相对折射率差δ7为0.0%。在该具体实施场景中,经实验测定的最佳预设半径范围和预设相对折射率差范围如表1所示。半径(μm)相对折射率差(%)纤芯114.80.68内包层1210.40.34下陷内包层1315.80环形包层1420.70.37外包层1532.50下陷外包层1642.3-0.48机械包层1762.10表1进一步的,为了保证耦合后的光学性能,避免因纤芯导光性能不同而导致的光信号不稳定,多芯多包层光纤在制备过程中,需要保证每个纤芯的同一性,使每个纤芯的导光性能一致。另一方面,套管20仅起到辅助固定作用,而不涉及耦合后的光学特性,并且套管20可能与需要拉锥的部分重合,因此只需选用可拉锥的材质即可。为了便于耦合时查看穿入套管20内部的单模光纤的位置和形体、便于加工、降低成本,本方案优选使用玻璃材质的套管。本实施例提供的光纤耦合器,使用多芯多包层光纤作为桥接光纤,避免了现有光纤耦合器光纤束切割难度较高的问题,光纤耦合器的耦合过程可重复性高,易于实现。多芯多包层光纤的下陷外包层的折射率小于外包层,可以限制场的覆盖范围,避免场向外泄露,和多芯光纤熔接后具有小的芯间串扰。通过多芯多包层光纤和标准单模光纤模场的匹配,使得多芯多包层光纤和标准单模光纤熔接时具有低的熔接损耗。实施例2:在实施例1提供的光纤耦合器的基础上,本实施例还提供了一种光纤耦合的方法,使用实施例1提供的光纤耦合器对单模光纤和多芯光纤进行耦合。如图6所示,本实施例提供的光纤耦合的方法的具体步骤如下。完成下述步骤101-步骤103后,光纤耦合器1、多芯光纤2和多根单模光纤3的连接结构如图7所示,其中,虚线框内部为光纤耦合器1的整体结构。步骤101:获取一个实施例1中提供的光纤耦合器1。本实施例提供的光纤耦合方法,使用实施例1中提供的光纤耦合器1对单根多芯光纤2和多根单模光纤3进行耦合。光纤耦合器1中使用的多芯多包层光纤10的长度根据实际的连接需要确定,综合考虑耦合时的加工难度和耦合后的信号质量后,经实验测得的最优长度为15cm-20cm。步骤102:对光纤耦合器1的多芯多包层光纤10的第二端进行拉锥处理,使多芯多包层光纤10第二端的芯间距达到预设芯间距阈值,并将多芯多包层光纤10第二端与多芯光纤2固定。为了匹配多根单模光纤3的直径,光纤耦合器1中的多芯多包层光纤10的直径和芯间距大于多芯光纤2的直径。因此,将光纤耦合器1与多芯光纤2进行耦合时,需要将多芯多包层光纤10的一端进行拉锥处理,在拉锥过程中,通过控制拉锥参数,使得多芯多包层光纤10的直径和芯间距与多芯光纤2相匹配,多芯多包层光纤10的纤芯模场、各纤芯11位置与多芯光纤2的各纤芯模场、纤芯位置也相互匹配。在实际使用中,由于涉及到多芯多包层光纤的拉锥,可以使用商业的大包层直径光纤拉锥机。进一步的,为了在耦合后获得最好的光学性能,拉锥长度不宜过长,过长的拉锥长度会影响后续多芯耦合器的保护封装,增大多芯耦合器的体积;同时,拉锥长度也不宜过短,过短的拉锥长度会导致多芯多包层光纤10的包层机械性能发生改变,无法对光纤内传导的光进行有效的束缚,导致器件的损耗增大。在具体实施中,可以根据实际测试值选择光学性能最好的拉锥长度。例如,在某个具体实施场景中,对七芯光纤进行耦合,七芯光纤有七个纤芯,其中中心有一个纤芯,周围六个纤芯占据正六边形的六个角,七芯光纤的纤芯间距为42μm;光纤耦合器1使用的多芯多包层光纤10的纤芯布与七芯光纤一致,纤芯间距为125μm。在该场景下,参考拉锥比为3倍,拉锥长度为5~10cm。进一步的,为了使多芯光纤2中每个纤芯的光信号都能导入至一根单模光纤3中,并且保证多芯光纤2的纤芯与多芯多包层光纤10的纤芯11分布一致,在本实施例的优选方案中,多芯多包层光纤10中纤芯11的数量与需要耦合的多芯光纤2的纤芯数量一致,避免纤芯无法全部对准。在某些特殊场景中,多芯多包层光纤10中纤芯11的数量与需要耦合的多芯光纤2的纤芯数量也可以不一致,只要在多芯多包层光纤10的第二端拉锥后能够使需要进行信号传导的纤芯能够对准即可。为了确保多芯多包层光纤10在拉锥后和多芯光纤2的模场匹配,对多芯多包层光纤10拉锥时,需要调整拉锥时的工艺参数,以达到以下工艺标准:多芯多包层光纤10的第二端拉锥前的纤芯11、内包层12、下陷内包层13和环形包层14构成被拉锥后的纤芯,多芯多包层光纤10的第二端拉锥前的外包层15、下陷外包层16和机械包层17构成拉锥后的包层。根据图5所示的各包层相对折射率示意图,以及实施例1中提供的预设半径范围和预设相对折射率差范围,下陷内包层13的折射率小于纤芯11、内包层12和环形包层14。因此,下陷内包层13可以作为沟道,在光纤发生弯曲时可以限制场的覆盖范围,避免场向环形包层泄露,使得耦合后的光纤具有小的宏弯损耗。对多芯多包层光纤10拉锥后,多芯多包层光纤10被拉锥的第二端直径和芯间距与多芯光纤2的直径和芯间距一致,此时,将多芯多包层光纤10被拉锥的第二端上的所有纤芯11和多芯光纤2中的所有需要进行光信号传导的纤芯一一对准,即可完成光纤耦合器1与多芯光纤2的耦合。光纤耦合器1与多芯光纤2的纤芯对准后,还需要进行固定连接。具体实施中,可以根据实际需要选择合适的连接方式,如使用各种机械、化学、放电等方法进行固定连接。优选方案中,为了降低固定连接后的信号衰减,也为了增加固定连接处的强度,使用熔接的方式进行固定连接,将多芯多包层光纤10的被拉纤的第二端进行切割,切割后的端面与多芯光纤2进行熔接。步骤103:将单模光纤3穿入光纤耦合器1的套管20内,每根单模光纤3与多芯多包层光纤10的一个纤芯11对准并固定。将光纤耦合器1与单模光纤3进行耦合时,使用的单模光纤3的数量通常与多芯多包层光纤10的纤芯11数量一致,或与需要耦合的多芯光纤2的数量一致,以确保将多芯光纤2中每一个纤芯中的光信号导入到一根对应的单模光纤3中。但是,在某些特殊场景中,也可以根据需要使用少于多芯多包层光纤10的纤芯11数量的单模光纤3,仅将多芯光纤2中部分纤芯的光信号导入单模光纤3中。由于耦合时需要使用多根单模光纤3,为了便于进行固定和对准,可以使用套管20进行辅助固定。将每根单模光纤3依次穿入套管20中,与一个多芯多包层光纤10的纤芯11对准并固定。在具体实施过程中,如图8所示,可以使用以下步骤将每根单模光纤3与多芯多包层光纤10的一个纤芯11对准并固定。步骤201:将一根单模光纤3穿入与多芯多包层光纤10耦合固定的套管20。由于套管20套在多芯多包层光纤10的外部,且与多芯多包层光纤10耦合固定,可以借助套管20进行单模光纤3的辅助定位和初步固定。将单模光纤3穿入套管20内完成初步定位,再通过精确定位将单模光纤3的纤芯对准任一个纤芯11,即可完成单模光纤3与多芯多包层光纤10的一个纤芯11的耦合。具体的,为了便于进行单模光纤3和纤芯11对准时的微调,可以使用六维调整架或其它位置微调装置对每根单模光纤3进行初步固定和定位。步骤202:将单模光纤3与多芯多包层光纤10的一个纤芯11对准,对准后进行固定。完成每根单模光纤3的对准后,还需要对单模光纤3进行固定,具体的固定方法可以根据工艺需求以及耦合后的性能要求进行选择。由于单模光纤3已穿入套管20中,并且周围还存在其它单模光纤3,为了简化工艺、降低对周围其它单模光纤3的影响,因此优选使用点胶的方法进行固定。经过步骤201-步骤202,可以完成一根单模光纤3的对准和固定,实现单模光纤3与一根纤芯11的耦合。依次对每根需要进行耦合的单模光纤3完成步骤201和步骤202,即可完成所有单模光纤3与多芯多包层光纤10的每个纤芯11的对准和固定。所有单模光纤3依次堆叠穿入并固定在套管内之后,每一根单模光纤3的纤芯模场、各纤芯位置与多芯多包层光纤10的各纤芯模场、纤芯位置相匹配。进一步的,为了提高对准效率,可以采用光纤熔接机自带的对准程序同时对多根单模光纤3进行对准,将多芯多包层光纤10和单模光纤3的各对应纤芯对准,使各纤芯对准损耗均最小。由于某些多芯光纤2或单模光纤3的外部包裹有涂覆层,为了便于切割,并便于使多芯光纤2或单模光纤3的直径与多芯多包层光纤10的芯间距相匹配,多芯光纤2和单模光纤3与多芯多包层光纤10的每一个纤芯11对准并固定之前,还需要剥去多芯光纤2和每一根单模光纤3的涂覆层并完成光纤清洁。在具体实施中,为了尽可能避免剥离、清洁过程给光纤表面带来的损坏而削弱光纤强度,影响后续步骤,可以使用商用的光纤剥离设备对涂覆层进行剥离。另一方面,为了减少耦合后的信号衰减,提高耦合精度,在某些场景中,还需要对多芯多包层光纤10、多芯光纤2或单模光纤3进行适当的切割,以获得平整端面。在具体实施中,可能存在大尺寸的光纤切割,可以使用商用的大包层直径的光纤切割刀或光纤切割机对光纤端面进行切割。经过步骤101-步骤103,通过使用实施例1中提供的光纤耦合器,简便的完成了和单模光纤实现低损耗熔接,而且通过微拉锥方法完成了和多芯光纤之间的低损耗熔接。耦合完成后,光纤耦合器1、多芯光纤2和单模光纤3的具体连接结构如图9所示。使用本实施例提供的光纤耦合方法,可以使光纤耦合中切割、对准和固定等步骤的工艺难度低、光纤耦合器的损耗较小、耦合后的信号衰减降低。进一步的,为了检验连接精度,保证耦合后的信号质量,在步骤102和步骤103将多芯光纤2的纤芯或每一根单模光纤3的纤芯与多芯多包层光纤10的纤芯11对准后,还可以进行信号衰减测试的工序,或使用其它方式进行对准精度测试,根据测试结果对多芯光纤2或单模光纤3进行更精确的位置调整,找到最优的对准位置后再进行固定,以确保耦合后的光纤性能达到最优。步骤102和步骤103中,具体的熔接方式可以为电极放电熔接,也可以为石墨加热熔接,也可以为其它满足工艺和材质要求的熔接方式。在具体实施过程中,可以通过测试不同熔接参数下熔接损耗的变化情况,找到最低熔接损耗时光纤熔接机的参数,以该参数进行光纤的熔接耦合。本领域的技术人员容易理解,以上所述仅为本发明的较佳实施例而已,并不用以限制本发明,凡在本发明的精神和原则之内所作的任何修改、等同替换和改进等,均应包含在本发明的保护范围之内。当前第1页12