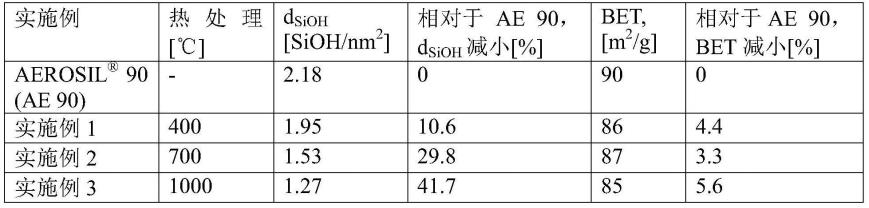
1.本发明涉及一种摩擦静电荷(tribo-electrostatic charge)减少的经表面改性的气相硅石(fumed silica)、其制备方法及其在调色剂(toner)中的用途。
背景技术:2.调色剂可以用于图像形成装置,例如打印机、复印机和传真机,以在介质片材上形成图像。图像形成设备可以利用在调色剂颗粒与显影剂体系中的各种组分之间产生的差分电荷,经由显影剂体系将调色剂从储槽转移到介质。调色剂摩擦电荷和流动特性的控制可以通过干燥调色剂表面改性以及在调色剂颗粒表面上附着细颗粒来实现。调色剂颗粒的摩擦电荷可以通过正确选择外部添加剂而在很大程度上得到控制。由于其高纯度和非常低的含水量,气相硅石是极好的绝缘体,即具有非常高的电阻。因此,气相硅石在与其他颗粒碰撞时能够积聚并携带高静电荷。术语“摩擦充电(tribo-charging)”通常用于调色剂技术,因为它指的是通过表面之间的摩擦产生静电荷。这种特性使得气相硅石在以明确方式控制和调节调色剂电荷特性方面非常有效。本质上,调色剂表面具有气相硅石表面的特性并相应地充电。
3.现有技术说明
4.各种经表面改性的气相硅石颗粒可以用作调色剂配制物中的添加剂。适当硅石添加剂的选择取决于特定调色剂应用的要求。决定硅石在调色剂中的可用性的最重要参数之一是其摩擦静电电荷(也简称为摩擦电荷)。根据气相硅石的物理化学性质,包括表面改性化学、颗粒表面积等,可以实现宽范围的摩擦电荷。因此,由evonik industries生产、bet表面积为215-265m2/g的经表面改性的气相硅石r 976 s提供-680μc/g的摩擦电荷,而同一生产商的另一种经表面改性的硅石na 200 y(bet=100-150m2/g)提供+260μc/g的摩擦电荷。这些和其他适用于调色剂中的典型气相硅石在产品手册“fumed silica andoxides for toner technical information ti 1222”中进行了说明,该手册可在www.aerosil.com上在线获取。
5.具有高负电荷的经表面处理的气相硅石通常是高度疏水的,而带正电荷的颗粒或具有减少的负电荷的颗粒通常用极性氨基硅烷或季三烷基铵部分进行表面改性,从而使这些颗粒的疏水性降低甚至呈亲水性。因此,ep0992857a2中的实施例1中公开了使用(3-缩水甘油氧基丙基)三甲氧基硅烷作为表面处理剂来制备摩擦电荷为-300μc/g的高疏水性硅石粉末。同一专利申请的对比例1中示出用(3-缩水甘油氧基丙基)三甲氧基硅烷和1,3-二氨基丙烷进行表面处理来制备摩擦电荷为-150μc/g的高亲水性硅石。
6.含有对水具有高亲和力的亲水性硅石的调色剂组合物的带电性质可能取决于环境变化,例如湿度变化。
7.高疏水性和亲水性的经表面处理的气相硅石通常都以较高碳含量为特征。因此,需要相对大量且通常成本高昂的表面处理剂。
8.具有减少的电荷的调色剂组合物需要具有减少的摩擦电荷的经表面改性的气相
硅石颗粒。这些硅石颗粒的特征通常是摩擦电荷相对于bet表面积的比相对较高。因此,经表面改性的气相硅石rx 50(生产商:evonik industries)的摩擦电荷为-200μc/g、bet表面积为25-45m2/g(摩擦电荷/平均bet=-5.7μc/m2)、碳含量为0.5-1.0重量%。
9.在其他情况下,具有减少的摩擦电荷例如从-200μc/g至+200μc/g的气相硅石呈现出与表面积相关的相对较高的碳含量。因此,摩擦电荷为-110μc/g的经表面改性的气相硅石ry 50(生产商:evonik industries)的bet表面积为15-45m2/g、碳含量为3.0-5.0重量%(碳含量/平均bet》0.100重量%
×
g/m2)。ep 0992857 a2的实施例2中公开的气相硅石粉末呈现出+200μc/g的摩擦电荷、130m2/g的bet表面积和5.5重量%的碳含量(碳含量/bet=0.042重量%
×
g/m2)。
10.问题和解决方案
11.本发明解决的技术问题是提供特别适合用作具有相对较低表面电荷的调色剂组合物中的添加剂的气相硅石。
12.这些调色剂组合物的带电性质不应依赖于环境变化,例如湿度。
13.应最大限度减少制备这些气相硅石粉末所需的表面处理剂的量。
14.本发明提供经表面处理的气相硅石,其特征在于:
15.摩擦静电电荷为-500μc/g至+500μc/g;
16.摩擦静电电荷与bet表面积的比为-3.5μc/m2至+3.5μc/m2;
17.甲醇润湿度为甲醇/水混合物中至少20体积%的甲醇;
18.碳含量与bet表面积的比至多为0.020重量%
×
g/m2。
19.这种气相硅石特别适合用作具有相对较低的表面电荷的调色剂组合物中的添加剂。所得调色剂组合物的带电性质不依赖于诸如湿度等环境变化。制备这种气相硅石所需的表面处理剂的量相对较低,降低了这种硅石的制备成本。
20.硅石
21.本发明的硅石优选以颗粒(particles)形式存在,例如粉末或细粒(granules)。最优选地,本发明的硅石是硅石粉末。
22.在本发明中,术语“细粒”被理解为是指粒状、易于倾倒、自由流动的颗粒状固体材料。细粒可以是球形或任何其他形状例如小球、环等的粒状颗粒的形式,或者是粉碎颗粒材料的不规则形成的碎片,例如具有统计粒径分布的形式。
23.本发明上下文中的术语“粉末”包括细颗粒(fine particles)。
24.在本发明的上下文中使用的术语“摩擦电荷”等同于术语“摩擦静电电荷”。该参数常规用于评估不同调色剂添加剂的静电性质。摩擦电荷的值可以使用吹出式静力静电计(blow-off static electrometer)来确定,例如,如ep2676930a1中的第[0118]段所述。
[0025]
以下程序可用于测量摩擦电荷:
[0026]
将50g无涂层铁氧体载体和0.1g气相硅石颗粒(可以根据需要在测量前对粗硅石颗粒进行磨碎和研压)放入75ml玻璃容器中,盖上盖子,并且使用混合器以90rpm的转速混合5分钟。随后,取出0.1g如此制备的混合物并进行氮气吹扫1分钟,再通过使用吹出式静力静电计(tb-200型,生产商:toshiba chemical)测量摩擦电荷。在25℃的温度和55%的相对湿度下进行测量。
[0027]
本发明的气相硅石的摩擦静电电荷为-500μc/g至+500μc/g,优选为-400μc/g至+
of span)(d
90-d
10
)/d
50
小于3.0,优选为0.4-3.0,更优选为0.5-2.0,更优选为0.6-1.8,更优选为0.7-1.7,更优选为0.8-1.6。
[0038]
上述粒径d
10
、d
50
和d
90
是指聚集和团聚的气相硅石颗粒的粒径。这些值是通过在25℃下对5重量%的硅石在甲醇中的分散体进行超声处理120秒后进行静态光散射测定。d
10
、d
50
和d
90
值分别反映了所有颗粒的10%、50%或95%不超过的颗粒尺寸。
[0039]
各种粉状或粗粒颗粒材料的夯实密度(tamped densities)(也称为“拍实密度(tapped density)”)可以根据din iso 787-11:1995“general methods of test for pigments and extenders
‑‑
part 11:determination of tamped volume and apparent density after tamping”来测定。这涉及在搅拌和夯实后测量床的表观密度。优选地,本发明的硅石的夯实密度为不大于600g/l、更优选地不大于500g/l、更优选地不大于400g/l、更优选地不大于300g/l,更优选地不大于250g/l,更优选地为20g/l到200g/l,更优选地为30g/l到180g/l,更优选地为40g/l到150g/l,更优选地为50g/l到120g/l。
[0040]
硅石的干燥失重(lod)优选地小于2.0重量%,更优选地小于1.5重量%,更优选地小于1.0重量%,更优选地小于0.5重量%,更优选地小于0.4重量%,更优选地小于0.35重量%,更优选地小于0.3重量%,更优选地小于0.25重量%,更优选地小于0.2重量%,更优选地小于0.15重量%,更优选地小于0.1重量%。干燥失重可以根据astm d280-01(方法a)测定。因此,本发明的气相硅石通常含有较低量的水,使其特别适用于需要低含水量的应用。
[0041]
本发明的硅石是气相(也称为“热解”)硅石。气相(热解)硅石通过火焰水解或火焰氧化来制备。这涉及通常在氢/氧火焰中氧化或水解可水解或可氧化的起始物料。用于热解法的起始物料包括有机物质和无机物质。四氯化硅特别合适。如此得到的亲水性硅石是无定形的。气相硅石通常以聚集形式存在。“聚集”被理解为是指最初形成的所谓初级颗粒,随后在反应中彼此牢固地结合以形成三维网络。初级颗粒基本上没有孔并且在其表面上具有游离羟基。这种亲水性硅石可以根据需要疏水化,例如通过用反应性硅烷处理。
[0042]
本发明的硅石的平均初级粒径d
50
可以为5nm到50nm,优选地5nm到40nm。平均初级粒径d
50
可以通过透射电子显微镜(tem)分析来测定。应分析至少100个颗粒以计算代表性平均值d
50
。
[0043]
本发明的硅石可以包含单独的化合物(二氧化硅(silicon dioxide))、基于硅石的混合氧化物、基于硅石的掺杂氧化物或其混合物。
[0044]
气相硅石的一个实例是基于硅石的混合氧化物。已知通过在h2/o2火焰中同时使至少两种以挥发性金属化合物例如氯化物形式存在的不同金属源反应来生产这些混合氧化物。这些氧化物的一个实例是sio2/al2o3混合氧化物,它由evonik以mox 170的商品名制备。在制备mox 170时,sicl4和alcl3的混合物在火焰中直接水解。如de-a 952 891、de-a 25 33 925和de-a 27 02 896中所述,相应的硅烷例如甲基三氯硅烷、三氯硅烷等也可用作代替氯化物或除氯化物之外的原料。
[0045]
如此制备的混合氧化物的所有组分,例如上述情况下的硅石和氧化铝,通常均匀分布在整个混合氧化物材料中,这与其他种类的材料例如几种金属氧化物、掺杂的金属氧化物等的机械混合物不同。在后一种情况下,例如对于几种金属氧化物的混合物,可能存在相应纯氧化物的分离域,这决定了这种混合物的性质。
[0046]
本发明的硅石包含二氧化硅作为主要组分。优选地,按重量计,硅石包含至少50%,更优选地至少60%,更优选地至少70%,更优选地70%-99.9%,更优选地80%-99.5%,更优选地90%-99.0%,更优选地92%-98.5%,更优选地95%-98.0%的二氧化硅。最优选地,本发明的硅石大体上不含除二氧化硅之外的氧化物。
[0047]
表面处理剂
[0048]
在本发明中,术语“经表面处理的”是指硅石与相应表面处理剂发生化学反应,其通过对硅石的游离硅烷醇基团进行全部或部分改性来改变硅石的表面性质。
[0049]
这种表面处理可以赋予本发明的硅石的表面亲水或疏水性质。本发明上下文中的术语“疏水化”或“疏水性”涉及对极性介质例如水具有低亲和力的经表面处理的颗粒。相反,亲水颗粒对极性介质例如水具有高亲和力。疏水材料的疏水性通常可以通过将适当的非极性基团施加到硅石表面来实现。硅石的疏水性程度可以通过包括其甲醇润湿度的参数来确定,例如在例如wo2011/076518a1第5-6页中详细描述。在纯水中,疏水性硅石完全从水中分离并且漂浮在其表面上而不被溶剂润湿。相反,在纯甲醇中,疏水性硅石分布在整个溶剂体积中;发生完全润湿。为测定甲醇润湿度,在每种情况下称取0.2g(
±
0.005g)疏水性或疏水化颗粒放入透明离心管中。将8.0ml份甲醇/水混合物与10体积%、20体积%、30体积%、40体积%、50体积%、60体积%、70体积%或80体积%的甲醇添加到每个样品中。将试管摇动30秒,然后以2500min-1
离心5分钟。确定沉积物体积。甲醇润湿度确定为沉降物体积为100%(被测试硅石样品的最大可能值)时,甲醇的体积百分比。数值越高,疏水性越高。
[0050]
本发明的硅石的甲醇润湿度为甲醇/水混合物中至少20%、更优选地20体积%至80体积%、更优选地25体积%到75体积%、更优选地30体积%至70体积%、更优选地35体积%至65体积%、最优选地40体积%至60体积%的甲醇。
[0051]
本发明的硅石优选地使用选自有机硅烷、硅氮烷、无环聚硅氧烷、环状聚硅氧烷及其混合物的表面处理剂得到。
[0052]
一种优选的有机硅烷是以下通式的烷基有机硅烷
[0053]
r'
x
(ro)ysi(c
nh2n+1
)(ia),和
[0054]
r'
x
(ro)ysi(c
nh2n-1
)(ib)
[0055]
其中
[0056]
r=烷基,例如甲基-、乙基-、正丙基-、异丙基-、丁基-[0057]
r'=烷基或环烷基,例如甲基、乙基、正丙基、异丙基、丁基、环己基、辛基、十六烷基。
[0058]
n=1-20
[0059]
x+y=3
[0060]
x=0-2,并且
[0061]
y=1-3。
[0062]
在式(ia)和(ib)的烷基有机硅烷中,特别优选的是辛基三甲氧基硅烷、辛基三乙氧基硅烷、十六烷基三甲氧基硅烷、十六烷基三乙氧基硅烷。
[0063]
用于表面处理的有机硅烷可以含有卤素,例如cl或br。特别优选的是以下类型的卤代有机硅烷:
[0064]-以下通式的有机硅烷
[0065]
x3si(c
nh2n+1
)(iia),和
[0066]
x3si(c
nh2n-1
)(iib),
[0067]
其中x=cl、br,n=1-20;
[0068]-以下通式的有机硅烷
[0069]
x2(r')si(c
nh2n+1
)(iiia),和
[0070]
x2(r')si(c
nh2n-1
)(iiib),
[0071]
其中x=cl、br
[0072]
r'=烷基,例如甲基、乙基、正丙基、异丙基、丁基、环烷基例如环己基
[0073]
n=1
–
20;
[0074]-以下通式的有机硅烷
[0075]
x(r')2si(c
nh2n+1
)(iva),和
[0076]
x(r')2si(c
nh2n-1
)(ivb),
[0077]
其中x=cl、br
[0078]
r'=烷基,例如甲基、乙基、正丙基、异丙基、丁基、环烷基例如环己基
[0079]
n=1
–
20。
[0080]
在式(ii)-(iv)的卤代有机硅烷中,特别优选的是二甲基二氯硅烷和氯三甲基硅烷。
[0081]
所用的有机硅烷还可以含有除烷基或卤素以外的取代基,例如氟取代基或某些官能团。优选使用以下通式的官能化的有机硅烷
[0082]
(r")
x
(ro)ysi(ch2)mr'(v),
[0083]
其中
[0084]
r”=烷基,例如甲基、乙基、丙基,或卤素例如cl或br,
[0085]
r=烷基,例如甲基、乙基、丙基,
[0086]
x+y=3
[0087]
x=0-2,
[0088]
y=1-3,
[0089]
m=1-20,
[0090]
r'=甲基-、芳基(例如,苯基或取代的苯基残基)、杂芳基
[0091]-c4f9、ocf
2-chf-cf3、-c6f
13
、-o-cf
2-chf2、-nh2、-n3、-scn、-ch=ch2、-nh-ch
2-ch
2-nh2、-n-(ch
2-ch
2-nh2)2、-ooc(ch3)c=ch2、-och
2-ch(o)ch2、-nh-co-n-co-(ch2)5、-nh-coo-ch3、-nh-coo-ch
2-ch3、-nh-(ch2)3si(or)3、-s
x-(ch2)3si(or)3、-sh、-nr1r2r3(r1=烷基、芳基;r2=h、烷基、芳基;r3=h、烷基、芳基、苄基、c2h4nr4r5,其中r4=h、烷基并且r5=h、烷基)。
[0092]
在式(v)的官能化的有机硅烷中,特别优选的是3-甲基丙烯酰氧基丙基三甲氧基硅烷、3-甲基丙烯酰氧基丙基三乙氧基硅烷、缩水甘油氧基丙基三甲氧基硅烷、缩水甘油氧基丙基三乙氧基硅烷、氨基丙基三乙氧基硅烷。
[0093]
通式r'r2si-nh-sir2r'(vi)的硅氮烷,其中r=烷基,例如甲基、乙基、丙基;r'=烷基、乙烯基,也适合作为表面处理剂。最优选的式(vi)的硅氮烷是六甲基二硅氮烷(hmds)。
[0094]
还适合作为表面处理剂的是环状聚硅氧烷,例如八甲基环四硅氧烷(d4)、十甲基环五硅氧烷(d5)、十二甲基环六硅氧烷(d6)、六甲基环三硅氧烷(d6)。在环状聚硅氧烷中,
最优选使用d4。
[0095]
另一种可用类型的表面处理剂是通式(vii)的聚硅氧烷或硅油:
[0096][0097]
其中
[0098]
y=h、ch3、c
nh2n+1
,其中n=1-20,si(ch3)axb,
[0099]
其中a=2-3,b=0或1,a+b=3,
[0100]
x=h、oh、och3、c
mh2m+1
,其中m=1-20。
[0101]
r,r'=烷基,例如c
oh2o+1
,其中o=1到20,芳基例如苯基和取代的苯基残基、杂芳基、(ch2)
k-nh2,其中k=1-10,h,
[0102]
u=2-1000,优选地u=3-100。
[0103]
在式(vii)的聚硅氧烷和硅油中,最优选使用聚二甲基硅氧烷作为表面处理剂。这种聚二甲基硅氧烷通常具有162g/mol到7500g/mol的摩尔质量、0.76g/ml到1.07g/ml的密度,和0.6mpa*s到1 000 000mpa*s的粘度。
[0104]
制备硅石的方法
[0105]
本发明还提供了一种制备本发明的经表面处理的气相硅石的方法,其包括以下步骤:
[0106]
a)在300℃至1400℃的温度下对具有bet表面积s1和硅烷醇密度d
1sioh
的表面未处理的亲水性气相硅石进行热处理,直到所得到的经热处理的硅石的硅烷醇基团密度d
2sioh
减小d
1sioh
值的至少5%,并且所得到的经热处理的硅石的bet比表面积s2减小s1值的至多30%;
[0107]
b)用选自有机硅烷、硅氮烷、无环聚硅氧烷、环状聚硅氧烷及其混合物的至少一种表面处理剂对步骤a)中得到的经热处理的硅石进行表面处理;
[0108]
c)任选地粉碎在步骤a)和/或步骤b)中得到的硅石。
[0109]
在本发明方法的步骤a)中使用的上述表面未处理的亲水性气相法硅石未经表面处理,即未用任何表面处理剂改性,因此本质上是亲水性的。
[0110]
本发明方法的步骤a)和b)中提及的术语“表面未处理的亲水性硅石”和“经热处理的硅石”不限于硅石粉末,而是包括硅石粉末,以及具有球形或任何其他形状例如小球、环等的其他颗粒或物质,或粉碎颗粒材料例如具有统计粒径分布的不规则形成的碎片。
[0111]
因此,在进行本发明方法的步骤a)之前,可以将表面未处理的亲水硅石致密化以得到亲水性硅石,例如以细粒的形式。
[0112]
这种致密化可以例如通过脱气或压实来实现,以使得硅石的夯实密度为至少80g/l、优选地80g/l-2000g/l、更优选地90g/l-1500g/l、更优选地90g/l-800g/l,更优选地100g/l-700g/l,更优选地110g/l-600g/l,更优选地120g/l-500g/l。
[0113]
在本发明方法的步骤a)中使用的表面未处理的亲水性硅石也可以是未经致密化的粉末。
[0114]
在根据本发明的方法的步骤a)中,亲水性硅石的热处理在300℃至1400℃,优选地350℃至1300℃,更优选地400℃至1200℃,更优选地400℃至1100℃,更优选地400℃至1050℃,更优选地400℃至1000℃的温度下进行。步骤a)的持续时间取决于所施加的温度并且通常可以为1秒到20小时,优选地1分钟至10小时,更优选地2分钟至8小时,更优选地5分钟至5小时,更优选地10分钟至3小时,更优选地15分钟至2小时。
[0115]
本发明方法的步骤a)中的热处理显然通过游离硅烷醇基团的缩合和形成o-si-o桥而减少游离硅烷醇基团的数量。该方法还可以减小bet表面积。亲水性硅石的初始硅烷醇基含量及其bet表面积的减小程度可以根据所施加的温度以及该热处理的持续时间进行调整。
[0116]
进行本发明方法的步骤a)直到所得到的经热处理的硅石的硅烷醇密度d
2sioh
减小该方法的步骤a)中所使用的硅石的硅烷醇密度d
1sioh
的至少5%,优选地至少7%,更优选地至少10%,更优选地10%-50%,更优选地10%-45%;并且所得到的经热处理的硅石的bet表面积s2减小该方法的步骤a)中所使用的硅石的bet表面积s1的至多30%,优选地至多25%,更优选地至多20%,更优选地至多15%,更优选地1%-10%。
[0117]
硅烷醇密度d
sioh
是相对于bet表面积的硅烷醇基团数,以sioh基团/nm2表示。该参数可以通过包括硅石与氢化铝锂反应的方法来确定,例如ep 0725037a1第8页第17到第9页第12行中所详细描述。该方法在journal of colloid and interface science第125卷第1期(1988)第61-68页中也有详细描述。
118.干燥的硅石样品的硅烷醇(sioh)基团与氢化铝锂(lialh4)反应,确定该反应期间形成的气态氢的量,从而确定样品中的硅烷醇基团的量n
oh
(以mmol sioh/g为单位)。使用测试材料的相应bet表面积(以m2/g为单位),以mmol oh/g为单位的硅烷醇基团含量可以很容易地转换为相对于bet表面积的硅烷醇基团的数d
sioh
:
[0119]doh
[sioh/nm2]=(n
oh
[mmol sioh/g]
×
na)/(bet[m2/g]
×
10
21
),
[0120]
其中na是阿伏伽德罗数(约6.022*10
23
)
[0121]
本发明方法中使用的表面未处理的气相硅石相对于bet表面积的硅烷醇基团数d
1sioh
通常为至少1.40sioh/nm2,优选地1.40sioh/nm
2-3.00sioh/nm2,更优选地1.50sioh/nm
2-2.80sioh/nm2。
[0122]
本发明方法中所采用的表面未处理的气相硅石的bet表面积可以是大于20m2/g,优选地30m2/g至500m2/g,更优选地50m2/g至400m2/g,更优选地70m2/g至350m2/g,最优选地80m2/g至300m2/g。可以根据din9277:2014,通过依据brunauer-emmett-teller方法的氮吸附来测定比表面积,也简称为bet表面积。
[0123]
在本发明方法的步骤a)中的热处理期间,所使用的硅石通常被致密化。在本发明方法的步骤a)中热处理的硅石的夯实密度优选地比该步骤中所使用的硅石的夯实密度高至少5%、更优选地高至少10%、更优选地高至少20%。
[0124]
本发明方法的步骤a)优选地在硅石运动期间进行,优选地在该方法期间以恒定运动,即在热处理期间硅石移动。该“动态”方法与“静态”热处理方法相反,在“静态”热处理方法中硅石颗粒不移动,例如在马弗炉中热处理期间以层的形式存在。
[0125]
已经令人惊讶地发现,在步骤a)中使用表面未处理的亲水性硅石粉末的这种动态热处理方法、结合热处理的适当温度和持续时间,能够产生特别适用于调色剂组合物的窄
粒径分布的小颗粒。相反,在热处理步骤中没有任何移动的“静态”热处理,得到具有更大的粒径和更宽的粒径分布的烧结聚集体。
[0126]
本发明方法的步骤a)可以在任何适当设备中进行,使得能够优选地在移动硅石的同时,将硅石粉末在上述指定温度下保持指定的时间段。一些适当的设备是流化床反应器和回转窑。在本发明方法的步骤a)中优选使用回转窑,特别是直径为1cm到2m,优选地5cm到1m,更优选地10cm到50cm的回转窑。
[0127]
硅石优选地以至少1cm/min、更优选地至少10cm/min、更优选地至少25cm/min、更优选地至少50cm/min的运动速率移动。优选地,硅石在热处理步骤a)的整个持续时间内以该运动速率移动。回转窑中的运动速率对应于这种反应器类型的周向速度。流化床反应器中的运动速率对应于载气流速(流化速度(fluidization velocity))。
[0128]
进一步优选地,在进行本发明方法的步骤a)之前、期间或之后基本上不添加水。以这种方式,避免了吸收的水的额外蒸发,并且可以得到具有较低水含量的经热处理的硅石。
[0129]
热处理步骤a)可以在气体例如空气或氮气流下进行,该气体优选地基本上不含水或预干燥。
[0130]“基本不含水”是指对于气体的湿度不超过在采用所述气体的温度和压力等条件下的湿度的气体,即在使用前不向气体中添加蒸汽或水蒸气。本发明方法的步骤a)中使用的气体的含水量优选地小于5体积%,更优选地小于3体积%,更优选地小于1体积%,更优选地小于0.5体积%。
[0131]
本发明方法的步骤b)可以在10℃至250℃的温度下进行1分钟至24小时。步骤b)的时间和持续时间可以根据方法和/或目标硅石性质的具体要求来选择。因此,较低的处理温度通常需要较长的疏水化时间。在本发明的一个优选实施方案中,表面未处理的亲水性硅石的疏水化在10℃至80℃下进行3到24小时,优选地5到24小时。在本发明的另一个优选实施方案中,该方法的步骤b)在90℃至200℃、优选地100℃至180℃、最优选地120℃至160℃下进行0.5到10小时,优选地1到8小时。根据本发明的方法的步骤b)可以在0.1-10bar、优选地0.5-8bar、更优选地1-7bar、最优选地1.1-5bar的压力下进行。最优选地,步骤b)在反应温度下,在使用的表面处理剂的自然蒸气压下在封闭系统中进行。
[0132]
本发明方法的步骤b)可以在水的存在下进行。
[0133]
本发明方法的步骤b)中水与表面处理剂的摩尔比优选地为0.1-100,更优选地0.5-50,更优选地1.0-10,更优选地1.2-9,更优选地1.5-8,更优选地2-7。
[0134]
但是,如果应得到具有特别低含水量的经表面处理的硅石,则优选地在进行本发明方法的步骤b)之前、期间或之后基本上不添加水。
[0135]
在本发明方法中,表面处理剂和/或水优选地以液体形式使用。
[0136]
在本发明方法的步骤b)中,在步骤a)中经过热处理的硅石优选地在环境温度(约25℃)下以任何顺序喷雾液体表面处理剂和任选地水,并且该混合物随后在50℃至400℃的温度下热处理1至6小时。
[0137]
步骤b)中表面处理的替代方法可以通过以下方式执行:首先用水然后用表面处理剂对在步骤a)中进行热处理的硅石进行处理,或首先用表面处理剂然后用水对其进行处理,或者使用水与表面处理剂的混合物进行处理,其中水和/或表面处理剂呈蒸气形式,随后在50℃至800℃的温度下对混合物进行热处理0.5至6小时。
[0138]
另一种可能的表面处理方法包括将适当的表面处理剂添加到分散体中,所述分散体例如含水分散体,其包含经热处理的硅石。该混合物可以在搅拌的同时加热,然后可以通过过滤分离经表面处理的产物。
[0139]
步骤b)中表面处理之后的热处理可以在保护气体例如氮气下进行。表面处理可以在可加热的混合器和带有喷雾装置的干燥器中连续或间歇进行。适当的装置可以是例如犁铧混合器或板式、旋风分离器或流化床干燥器。
[0140]
所使用的表面处理剂的量取决于颗粒的类型和所使用的表面处理剂的类型。但是,相对于在步骤a)中进行热处理的硅石的量,通常使用1重量%至25重量%,优选2重量%至20重量%,更优选地5重量%至18重量%的表面处理剂。
[0141]
任选使用的水的量还取决于颗粒的类型和所使用的表面处理剂的类型。但是,相对于在步骤a)中进行热处理的硅石的量,通常使用0.5重量%至15重量%,优选地1重量%至12重量%,更优选地2重量%至10重量%的水。
[0142]
所需的表面处理剂和任选的水的量可以取决于所使用的表面未处理的亲水性硅石的bet表面积。因此,相对于每m2在步骤a)中进行热处理的表面未处理的亲水性硅石的bet比表面积,使用的表面处理剂中的硅原子优选地为0.1μmol-100μmol、更优选地1μmol-50μmol、更优选地3.0μmol-20μmol,并使用0.1μmol-500μmol、更优选地1μmol-100μmol、更优选地10μmol-50μmol的水。
[0143]
在本发明方法的任选步骤c)中,将在步骤a)中进行热处理的硅石和/或在步骤b)中得到的经表面处理的硅石粉碎。因此,特别是如果在步骤a)和/或b)中使用或得到致密体或粗颗粒,则可以在一个或两个后续步骤c)中将其粉碎以得到硅石粉末。
[0144]
本发明方法的任选步骤c)中的粉碎可以通过任何适用于此用途的机器例如磨机来实现。
[0145]
如果在步骤a)和b)中都使用和得到硅石粉末,则不需要粉碎。尽管如此,在这种情况下得到的硅石可以进一步粉碎,例如研磨以得到更小的硅石颗粒。
[0146]
包含硅石的组合物
[0147]
本发明的另一个主题是包含本发明的硅石的组合物,尤其是调色剂组合物。
[0148]
根据本发明的组合物可以包含至少一种粘合剂,其将组合物的各个部分彼此接合并且任选地接合一种或多种填料和/或其他添加剂,从而可以改善组合物的机械性能。这种粘合剂可以含有有机物质或无机物质。粘合剂任选地含有反应性有机物质。例如,有机粘合剂可以选自(甲基)丙烯酸酯、醇酸树脂、环氧树脂、阿拉伯树胶、酪蛋白、植物油、聚氨酯、硅树脂、蜡、纤维素胶及其混合物。这些有机物质可以导致所用组合物的固化,例如通过蒸发溶剂、聚合、交联反应或其他类型的物理或化学转化。例如,这种固化可以通过热或在uv辐射或其他辐射的作用下进行。单(一)组分(1-c)和多组分体系,特别是双组分体系(2-c)均可以用作粘合剂。本发明特别优选的是水基或与水混溶的(甲基)丙烯酸酯基粘合剂和环氧树脂(优选地作为双组分体系)。
[0149]
除了有机粘合剂或作为其替代物,本发明的组合物可以含有无机可固化物质。这种无机粘合剂(也称为矿物粘合剂)具有与有机粘合剂基本相同的任务,即将添加剂物质相互接合。此外,无机粘合剂分为非水硬性粘合剂和水硬性粘合剂。非水硬性粘合剂是仅在空气中固化的水溶性粘合剂,例如钙石灰、白云石石灰、石膏和硬石膏。水硬性粘合剂是在空
气中和在水存在下固化并且在固化后不溶于水的粘合剂。这些粘合剂包括水硬石灰、水泥和砌筑水泥。不同无机粘合剂的混合物也可用于本发明的组合物中。
[0150]
除了硅石和粘合剂之外,根据本发明的组合物还可以含有至少一种溶剂和/或填料和/或其他添加剂。
[0151]
本发明的组合物中使用的溶剂可以选自水、醇、脂族烃和芳族烃、醚、酯、醛、酮及其混合物。例如,使用的溶剂可以是水、甲醇、乙醇、丙醇、丁醇、戊烷、己烷、苯、甲苯、二甲苯、二乙醚、甲基叔丁基醚、乙酸乙酯和丙酮。特别优选地,溶剂的沸点低于300℃,特别优选地低于200℃。在根据本发明的组合物的固化过程中,这种相对易挥发的溶剂可以容易地蒸发或汽化。
[0152]
硅石的用途
[0153]
本发明的硅石可用作油漆或涂料、硅酮(silicones)、药物或化妆品制备物、粘合剂或密封剂、调色剂组合物的成分,以及用于改变液体体系的流变性能、用作抗沉降剂、用于改进粉末的流动性,和用于改进硅酮组合物的机械或光学性能。
[0154]
本发明的硅石特别适用于调色剂组合物中。
[0155]
本发明还提供包含本发明的硅石的调色剂组合物。
[0156]
这些调色剂组合物通常包含平均尺寸在1μm-25μm范围内的调色剂颗粒。本发明的气相硅石可以以调色剂组合物的0.01重量%至2.0重量%的范围存在。
实施例
[0157]
分析方法
[0158]
摩擦电荷[μc/g]
[0159]
将50g未涂覆的铁氧体载体和0.1g气相硅石放入75ml玻璃容器中,盖上盖子,并使用混合器摇动5分钟。随后,取出0.1g如此制备的混合物并进行氮气吹扫1分钟,再通过使用吹出式静力静电计(来自toshiba chemical的tb-200型)测量摩擦电荷。在25℃的温度和55%的相对湿度下进行测量。
[0160]
甲醇润湿度[以甲醇/水混合物中甲醇的体积%计],根据wo2011/076518a1第5-6页中详细描述的方法测定。
[0161]
碳含量[重量%],根据en iso3262-20:2000(第8章)通过元素分析来确定。将被分析的样品称重到陶瓷坩埚中,提供燃烧添加剂,并在感应炉中在氧气流下加热。所存在的碳被氧化成co2。使用红外检测器对co2气体的量进行量化。
[0162]
相对于bet表面积的硅烷醇基团数d
sioh
[硅烷醇密度,sioh/nm2],如ep 0725037a1第8页第17行到第9页第2行中详细描述,通过使硅石的预干燥样品与氢化铝锂溶液反应测定。
[0163]
干燥失重(lod,重量%),根据astm d280-01(方法a)测定。
[0164]
比bet表面积[m2/g],根据din 9277:2014,依据brunauer-emmett-teller方法通过氮气吸附测定。
[0165]
硅石的制备
[0166]
实施例1-3
[0167]
热处理
[0168]
在碾压机中以2kn/cm的压力压缩气相硅石粉末90(bet=90m2/g,生产商:evonik resource efficiency gmbh)。将由此得到的压缩棒在筛网造粒机中粉碎,将得到的夯实密度约为320g/l的粉碎碎片在回转窑中在400℃(实施例1)、700℃(实施例2)或1000℃(实例3)下进行热处理。硅石在回转窑中的平均停留时间为30-60分钟。
[0169]
将得到的粗颗粒研磨以得到粉末,将其用于随后的疏水化。
[0170]
表面处理
[0171]
将热处理步骤后的亲水性硅石粉末(100g)放入反应器中。在25℃下连续搅拌下加入水(1.0g),然后将六甲基二硅氮烷(hmds)(10g)喷雾在硅石上。在氮气气氛下在200℃继续搅拌120分钟。此后,将硅石粉末放入干燥盘中,在120℃的氮气气氛中,在烘箱中干燥至多1cm厚的薄层3小时以蒸发所有挥发物。
[0172]
热处理后亲水性硅石的物理化学性质如表1所示。表2总结了相应的经表面处理的硅石粉末的物理化学性质,并与市售产品nx 90g和nx 90s进行了比较,这两者均使用亲水性90作为前体制备并用hmds进行表面处理(数据基于产品手册“fumed silica andoxides for toner technical information ti 1222”,可访问www.aerosil.com在线获取)。
[0173]
从表1中可以看出,与未经热处理的起始材料(90)相比,bet表面积为90m2/g的硅石在400℃-1000℃下热处理30-60分钟致使硅烷醇基含量d
sioh
减小了约11%-42%,而bet表面积仅减小了约4%-6%。
[0174]
从表2中可以看出,经过热处理且用hmds进行疏水化的样品(实施例1-3)使材料的摩擦电荷在-20
…‑
70uc/g范围内,相比之下,相应未热处理和疏水化的样品(nx 90g和nx 90s)的摩擦电荷约为-300uc/g。因此,所得到的硅石材料的摩擦电荷与bet表面积的比为0.25-0.96,远低于从现有技术已知的类似材料例如nx 90g和nx90s所报告的值,见表2。
[0175]
表1:热处理后亲水性硅石的物理化学性质
[0176][0177]
表2:经表面处理的硅石粉末的物理化学性质
[0178]