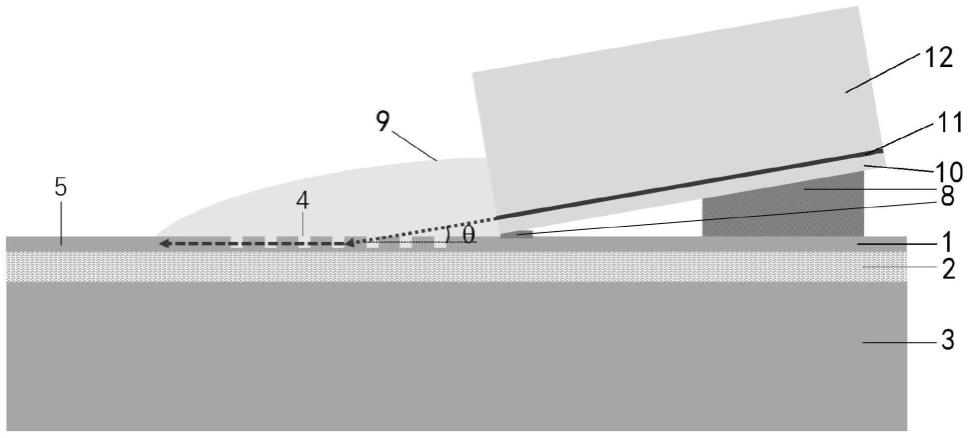
1.本发明涉及光子集成技术领域,特别是涉及一种边发射激光芯片与硅光芯片中光波导的耦合结构及方法。
背景技术:2.基于硅cmos工艺的硅光芯片在数据传输、光通信、激光雷达、健康医疗等诸多领域有重要的和潜在的应用价值。硅光芯片的信息载体是光。采用芯片外光源,可以避免硅光芯片与激光芯片制作工艺的交叉和芯片热管理等重大难题,但是,实现外光源与硅光芯片输入光波导间的高效光耦合具有非常大的挑战性。
3.目前,外光源与硅光芯片光波导间的耦合主要采用端面耦合、隐逝波耦合和光栅耦合方案。在端面和隐逝波耦合方案中,光束从光源侧端出射并沿此方向传播、耦合入波导。这两种方案虽然具有耦合高效、高带宽和偏振不敏感的优点,但外光源与硅光芯片光波导间的对准要求苛刻、工艺特殊且自动化水平低,对测试和封装精度有高要求,在大规模生产中会带来额外的制造成本。
4.光栅耦合方案利用光栅结构改变外光源出射的光束在波导方向上的动量大小,实现光束耦合入波导。光栅耦合方案又分两种,垂直入射-光栅耦合和水平入射-光栅耦合。采用垂直光栅耦合封装具有对准容差大的优点,但目前所用的光源仅限于面发射光源(vcsel)。采用水平入射-光栅耦合,在边发射激光芯片与硅波导光栅之间需要加入全内反射转接结构,或者把边发射激光芯片输出波段端面磨成合适的斜角,前者多引入的反射面增加了损耗、降低了耦合效率,后者的工艺复杂费时。
技术实现要素:5.为解决上述问题,本发明提出一种边发射激光芯片与硅光芯片中光波导的耦合结构及方法,以简化耦合封装工艺流程、降低加工封装成本并提高耦合效率。
6.为实现上述目的,本发明提供了如下方案:
7.一种边发射激光芯片与硅光芯片中光波导的耦合结构,包括:边发射激光芯片、硅光芯片以及金属焊料;所述硅光芯片包括层叠设置的顶层硅、氧化硅层以及硅衬底;所述顶层硅的一端刻蚀有矩形的无源硅光波导区和楔形的硅光波导入射光栅,所述顶层硅的另一端为激光芯片装焊预留区;所述硅光波导入射光栅的窄端连接所述无源硅光波导区,所述硅光波导入射光栅的宽端连接所述激光芯片装焊预留区;所述硅光波导入射光栅的刻蚀深度小于所述顶层硅的厚度;
8.所述激光芯片装焊预留区中间设置有对准标记;所述对准标记的连线与所述无源硅光波导区的中心线重合;所述激光芯片装焊预留区内设置有金属焊料;所述激光芯片装焊预留区内靠近所述硅光波导入射光栅一端设置的金属焊料高度低于所述激光芯片装焊预留区内远离所述硅光波导入射光栅一端设置的金属焊料高度;所述边发射激光芯片通过所述金属焊料倾斜倒装焊到所述硅光芯片上;所述边发射激光芯片的中心线与所述对准标
记的连线对准;所述边发射激光芯片的出光口延长线与所述无源硅光波导区的中心线对准。
9.可选地,所述边发射激光芯片的倾斜角度为8
°
至14
°
。
10.可选地,所述硅光波导入射光栅的光栅周期长度范围为540纳米至560纳米,占空比为0.2,光栅刻蚀深度为200纳米。
11.可选地,所述无源硅光波导区的宽度范围为400纳米至5000纳米,厚度范围为220纳米至3000纳米。
12.可选地,所述金属焊料为焊珠或焊条;所述金属焊料的高度范围为10微米至100微米。
13.可选地,所述边发射激光芯片与所述硅光波导入射光栅之间还填充有介质填充物;所述介质填充物与所述边发射激光芯片接触的一端覆盖所述边发射激光芯片的出光口;所述介质填充物底端覆盖所述硅光波导入射光栅。
14.可选地,所述介质填充物包括su-8光刻胶、聚二甲基硅氧烷、玻璃胶、聚甲基丙烯酸甲酯。
15.一种边发射激光芯片与硅光芯片中光波导的耦合方法,包括:
16.在硅光芯片的顶层硅上利用光刻和等离子体刻蚀,制备出矩形的无源硅光波导区和楔形的硅光波导入射光栅;矩形的无源硅光波导区和楔形的硅光波导入射光栅位于所述顶层硅的一端,所述顶层硅的另一端为激光芯片装焊预留区;所述硅光波导入射光栅的窄端连接所述无源硅光波导区,所述硅光波导入射光栅的宽端连接所述激光芯片装焊预留区;所述硅光波导入射光栅的刻蚀深度小于所述顶层硅的厚度;
17.在所述激光芯片装焊预留区中间设置对准标记,令所述对准标记的连线与所述无源硅光波导区的中心线重合;
18.在所述激光芯片装焊预留区内预置金属焊料;所述激光芯片装焊预留区内靠近所述硅光波导入射光栅一端预置的金属焊料高度低于所述激光芯片装焊预留区内远离所述硅光波导入射光栅一端预置的金属焊料高度;
19.将所述边发射激光芯片通过所述金属焊料倾斜倒装焊到所述硅光芯片上,令所述边发射激光芯片的中心线与所述对准标记的连线对准,令所述边发射激光芯片的出光口延长线与所述无源硅光波导区的中心线对准。
20.可选地,所述硅光波导入射光栅包括均匀光栅、啁啾光栅、聚焦光栅和变折射率光栅。
21.可选地,所述耦合方法还包括:
22.在所述边发射激光芯片与所述硅光波导入射光栅之间填充介质填充物,令所述介质填充物与所述边发射激光芯片接触的一端覆盖所述边发射激光芯片的出光口,令所述介质填充物底端覆盖所述硅光波导入射光栅。
23.根据本发明提供的具体实施例,本发明公开了以下技术效果:
24.本发明提供了一种边发射激光芯片与硅光芯片中光波导的耦合结构及方法,通过将边发射激光芯片倾斜装焊在硅光芯片之上,把倾斜输出的光直接投射到硅光波导入射光栅上。相比于端面和隐逝波耦合方案,本发明对激光芯片和硅光芯片的结构和加工工艺无特殊要求,对于波导和光源的对准精度要求低、加工容差大,有利于增加回路设计灵活性、
降低加工封装成本。相比于垂直入射-光栅耦合,本发明中入射至硅光波导入射光栅的光线与垂直方向之间存在倾角,可以有效抑制光耦合过程中的背向反射,提高耦合效率。相比于水平入射-光栅耦合,本发明无需引入额外的全内反射转接结构或将激光芯片输出波段端面进行额外加工,降低了反射损耗、简化了工艺流程。本发明还可以完全在现有微电子或光电子的封装线上完成,不引入额外加工步骤,因此可批量放大自动化生产,具有广泛的应用前景。
25.此外,本发明将聚合物、玻璃透明介质等介质填充物填充在边发射激光芯片与硅光波导入射光栅之间,避免了光路径中可能的微尘对光的散射,也起到折射率匹配的作用,减小了光场损耗,进一步提高了耦合效率。
附图说明
26.为了更清楚地说明本发明实施例或现有技术中的技术方案,下面将对实施例中所需要使用的附图作简单地介绍,显而易见地,下面描述中的附图仅仅是本发明的一些实施例,对于本领域普通技术人员来讲,在不付出创造性劳动的前提下,还可以根据这些附图获得其他的附图。
27.图1为本发明边发射激光芯片与硅光芯片中光波导的耦合结构的主视方向示意图;
28.图2为本发明边发射激光芯片与硅光芯片中光波导的耦合结构的俯视方向剖视图;
29.其中附图标记为:顶层硅1、氧化硅层2、硅衬底3、硅光波导入射光栅4、无源硅光波导区5、激光芯片装焊预留区6、对准标记7、金属焊料8、介质填充物9、上包覆层10、多量子阱有源层11、下包覆层12。
具体实施方式
30.下面将结合本发明实施例中的附图,对本发明实施例中的技术方案进行清楚、完整地描述,显然,所描述的实施例仅仅是本发明一部分实施例,而不是全部的实施例。基于本发明中的实施例,本领域普通技术人员在没有做出创造性劳动前提下所获得的所有其他实施例,都属于本发明保护的范围。
31.本发明的目的是提供一种边发射激光芯片与硅光芯片中光波导的耦合结构及方法,以简化耦合封装工艺流程、降低加工封装成本并提高耦合效率。
32.为使本发明的上述目的、特征和优点能够更加明显易懂,下面结合附图和具体实施方式对本发明作进一步详细的说明。
33.图1为本发明边发射激光芯片与硅光芯片中光波导的耦合结构的主视方向示意图;图2为本发明边发射激光芯片与硅光芯片中光波导的耦合结构的俯视方向剖视图。
34.实施例1
35.参见图1和图2,在本发明边发射激光芯片与硅光芯片中光波导的耦合结构的实施例1中,所述边发射激光芯片与硅光芯片中光波导的耦合结构包括:边发射激光芯片(简称激光芯片)、硅光芯片以及金属焊料。
36.如图1所示,所述硅光芯片包括层叠设置的顶层硅1、氧化硅层2以及硅衬底3;所述
顶层硅1的一端刻蚀有矩形的无源硅光波导区5和楔形的硅光波导入射光栅4,所述顶层硅的另一端为激光芯片装焊预留区6;所述硅光波导入射光栅4的窄端连接所述无源硅光波导区5,所述硅光波导入射光栅4的宽端连接所述激光芯片装焊预留区6;所述硅光波导入射光栅4的刻蚀深度小于所述顶层硅1的厚度。
37.未进行刻蚀加工之前,硅光芯片为标准soi(silicon-on-insulator)结构,从上到下包括顶层硅1、氧化硅层2和硅衬底衬底3。本发明在硅光芯片上利用光刻和等离子体刻蚀顶层硅1,制备出无源硅光波导区5和楔形的硅光波导入射光栅4,其中楔形硅光波导入射光栅4的窄端与无源硅光波导区5相连。因此硅光芯片包括硅衬底3、氧化硅层2、顶层硅1上的硅光波导入射光栅4、与之相连的矩形无源硅光波导区5以及激光芯片装焊预留区6。
38.如图1所示,普通边发射激光芯片,也称为边发射激光器,其包含磷砷化镓铟(ingaasp)多量子阱有源层11及两侧的磷化铟(inp)材料上下包覆层,即上包覆层10和下包覆层12。
39.参见图2,所述激光芯片装焊预留区6中间设置有对准标记7;所述对准标记7的连线与所述无源硅光波导区5的中心线重合。所述激光芯片装焊预留区6内还设置有金属焊料8;所述激光芯片装焊预留区6内靠近所述硅光波导入射光栅4一端设置的金属焊料8高度低于所述激光芯片装焊预留区6内远离所述硅光波导入射光栅4一端设置的金属焊料8高度。所述边发射激光芯片通过所述金属焊料8倾斜倒装焊到所述硅光芯片上。所述边发射激光芯片的中心线与所述对准标记7的连线对准;所述边发射激光芯片的出光口延长线与所述无源硅光波导区5的中心线对准。
40.如图1所示,本发明将激光芯片倾斜倒装焊在硅光芯片之上,其倾斜角度的稳定控制是本发明的关键,考虑边发射激光芯片出射光的垂直发散角,作为优选,所述边发射激光芯片的倾斜角度θ为8
°
至14
°
。
41.本发明硅光芯片的顶层硅1上设有硅光波导入射光栅4及无源硅光波导区5,可以通过调节耦合光栅(即硅光波导入射光栅4)的刻蚀深度、光栅周期和占空比f(定义为刻蚀宽度占周期宽度的比例)等参数实现波矢匹配、优化耦合强度。根据光栅方程,作为优选,所述硅光波导入射光栅4的光栅周期长度范围为540纳米至560纳米,占空比f为0.2,光栅刻蚀深度为200纳米。所述无源硅光波导区5的宽度(即波导宽度d)范围为400纳米至5000纳米,对应厚度范围为220纳米至3000纳米。所述金属焊料8可以为焊珠或焊条;所述金属焊料8的高度范围为10微米至100微米。
42.本发明边发射激光芯片与硅光芯片中光波导的耦合结构实施例1的制备方法包括:
43.s101、在硅光芯片的顶层硅1上利用光刻和等离子体刻蚀,制备出矩形的无源硅光波导区5和楔形的硅光波导入射光栅4,作为外光源向硅光芯片的光耦合器;其中,矩形的无源硅光波导区5和楔形的硅光波导入射光栅4位于所述顶层硅1的一端,所述顶层硅1的另一端为激光芯片装焊预留区6;所述硅光波导入射光栅4的窄端连接所述无源硅光波导区2,所述硅光波导入射光栅4的宽端连接所述激光芯片装焊预留区6;所述硅光波导入射光栅4的刻蚀深度小于所述顶层硅1的厚度;因此,介质填充物9接触到的光栅底部依然为顶层硅1,介质填充物9与氧化硅层2不接触。本发明刻蚀的硅光波导入射光栅4可以是均匀光栅、啁啾光栅、聚焦光栅或变折射率光栅。
44.s102、在所述激光芯片装焊预留区6中间设置对准标记7,令所述对准标记7的连线与所述无源硅光波导区5的中心线重合。
45.s103、在所述激光芯片装焊预留区6内预置金属焊料8;所述激光芯片装焊预留区6内靠近所述硅光波导入射光栅4一端预置的金属焊料8高度低于所述激光芯片装焊预留区6内远离所述硅光波导入射光栅4一端预置的金属焊料8高度。
46.鉴于边发射激光芯片的长度一般为100微米至1000微米,根据激光芯片的倾角θ,金属焊料8(焊珠或焊条)的高度大约为10微米至100微米。
47.s104、将所述边发射激光芯片通过所述金属焊料8倾斜倒装焊到所述硅光芯片上,令所述边发射激光芯片的中心线与所述对准标记7的连线对准,令所述边发射激光芯片的出光口延长线与所述无源硅光波导区5的中心线对准。
48.即,激光芯片在硅光芯片上的装焊位置需要满足出射光能斜入射在硅光波导入射光栅4之上。在硅光芯片需要连接激光芯片的位置处(即激光芯片装焊预留区6内)预置焊料8以及对准标记7后,让激光芯片的中心线与对准标记7重合,能够使入射光进入硅光波导入射光栅4后的传播方向与无源硅光波导区5的传输方向之间无角度差,同时让激光芯片出光口的延长线对准硅光波导入射光栅4,在此前提下将激光芯片倒装焊到硅光芯片上。正置的激光芯片1从上到下包括上包覆层10、多量子阱有源层11和下包覆层12,在激光芯片下包覆层12的下方通常还设有衬底等,因此本发明“倒装焊”指的是激光芯片进行装焊时,将上包覆层10一侧朝下,其令上包覆层10与金属焊料8进行焊接。倒装焊(flip-chipbonding)是一种比较标准的微电子封装技术。
49.本发明耦合方法制备的该耦合结构实施例1可工作于o-,c-,l-等波段。作为优选,工作波段为c-波段,更优选的,波长为1550纳米。
50.实施例2
51.本发明边发射激光芯片与硅光芯片中光波导的耦合结构实施例2与实施例1的区别在于,所述边发射激光芯片与所述硅光波导入射光栅4之间还填充有介质填充物9;所述介质填充物9与所述边发射激光芯片接触的一端覆盖所述边发射激光芯片的出光口;所述介质填充物9底端覆盖所述硅光波导入射光栅4。所述介质填充物9包括su-8光刻胶、聚二甲基硅氧烷、玻璃胶、聚甲基丙烯酸甲酯。
52.本发明耦合结构实施例2与实施例1的结构类似,但用聚合物、玻璃透明介质等介质填充物9填充在边发射激光芯片与硅光波导入射光栅4之间,避免了光路径中可能的微尘对光的散射,同时起到折射率匹配的作用。
53.与实施例1类似,本发明边发射激光芯片与硅光芯片中光波导的耦合结构实施例2中,边发射激光芯片也包含磷砷化镓铟(ingaasp)多量子阱有源层11和磷化铟(inp)材料的上、下包覆层10、12。激光芯片倾斜倒装焊在硅光芯片之上,其倾斜角度θ的稳定控制是本发明的关键,考虑边发射激光器在垂直方向的发散角,作为优选,激光器倾斜角度θ为8
°
至14
°
。
54.硅光芯片,其上设有入射耦合光栅(即硅光波导入射光栅4)及波导(即无源硅光波导区5),其中可以通过调节耦合光栅的刻蚀深度、光栅周期和占空比f(定义为刻蚀宽度占周期宽度的比例)等参数实现波矢匹配、优化耦合强度。根据光栅方程,光栅周期长度在560纳米至600纳米范围内,占空比f为0.2,光栅刻蚀深度为200纳米。波导宽度d在400纳米至
5000纳米范围内、对应厚度范围为220纳米至3000纳米。
55.介质填充物9,通常为聚合物或玻璃透明介质,其填充于边发射激光芯片与硅光栅(即硅光波导入射光栅4)之间,与边发射激光芯片和硅光栅相连接,覆盖出射光的传播路径(图1中虚线箭头所示)。作为优选,介质填充物9的材料为su-8光刻胶,其折射率为1.56(对应c-波段,波长为1550纳米时)。
56.上述边发射激光芯片与硅光芯片中光波导的耦合结构实施例2的制备方法包括:
57.s101、在硅光芯片的顶层硅1上利用光刻和等离子体刻蚀,制备出矩形的无源硅光波导区5和楔形的硅光波导入射光栅4,作为外光源向硅光芯片的光耦合器;其中,矩形的无源硅光波导区5和楔形的硅光波导入射光栅4位于所述顶层硅1的一端,所述顶层硅1的另一端为激光芯片装焊预留区6;所述硅光波导入射光栅4的窄端连接所述无源硅光波导区2,所述硅光波导入射光栅4的宽端连接所述激光芯片装焊预留区6;所述硅光波导入射光栅4的刻蚀深度小于所述顶层硅1的厚度;因此,介质填充物9接触到的光栅底部依然为顶层硅1,介质填充物9与氧化硅层2不接触。本发明刻蚀的硅光波导入射光栅4可以是均匀光栅、啁啾光栅、聚焦光栅或变折射率光栅。
58.s102、在所述激光芯片装焊预留区6中间设置对准标记7,令所述对准标记7的连线与所述无源硅光波导区5的中心线重合。
59.s103、在所述激光芯片装焊预留区6内预置金属焊料8;所述激光芯片装焊预留区6内靠近所述硅光波导入射光栅4一端预置的金属焊料8高度低于所述激光芯片装焊预留区6内远离所述硅光波导入射光栅4一端预置的金属焊料8高度。
60.鉴于边发射激光芯片的长度一般为100微米至1000微米,根据激光芯片的倾角θ,金属焊料8(焊珠或焊条)的高度大约为10微米至100微米。
61.s104、将所述边发射激光芯片通过所述金属焊料8倾斜倒装焊到所述硅光芯片上,令所述边发射激光芯片的中心线与所述对准标记7的连线对准,令所述边发射激光芯片的出光口延长线与所述无源硅光波导区5的中心线对准。
62.即,激光芯片在硅光芯片上的装焊位置需要满足出射光能斜入射在硅光波导入射光栅4之上。在硅光芯片需要连接激光芯片的位置处(即激光芯片装焊预留区6内)预置焊料8以及对准标记7后,让激光芯片的中心线与对准标记7重合,能够使入射光进入硅光波导入射光栅4后的传播方向与无源硅光波导区5的传输方向之间无角度差,同时让激光芯片出光口的延长线对准硅光波导入射光栅4,在此前提下将激光芯片倒装焊到硅光芯片上。正置的激光芯片1从上到下包括上包覆层10、多量子阱有源层11和下包覆层12,在激光芯片下包覆层12的下方通常还设有衬底等,因此本发明“倒装焊”指的是激光芯片进行装焊时,将上包覆层10一侧朝下,其令上包覆层10与金属焊料8进行焊接。倒装焊(flip-chip bonding)是一种比较标准的微电子封装技术。
63.s105、在所述边发射激光芯片与所述硅光波导入射光栅4之间填充介质填充物9,令所述介质填充物9与所述边发射激光芯片接触的一端覆盖所述边发射激光芯片的出光口,令所述介质填充物9底端覆盖所述硅光波导入射光栅4。
64.介质填充物9的材料可以为su-8光刻胶、pdms(聚二甲基硅氧烷)、玻璃胶、pmma(聚甲基丙烯酸甲酯)等。该介质填充物9填满入射光栅4以及光栅4与边发射激光器之间的空隙,如图1所示,其顶端形状通常为胶滴落后的自然形状。介质填充物9的右端与激光芯片相
连且覆盖激光芯片出光部分,其底端覆盖整个硅光波导入射光栅4并延伸至光栅4与无源硅光波导区5的连接处。由于光栅4刻蚀深度小于硅光芯片上层硅1的厚度,因此介质填充物9与氧化硅层2无直接接触。
65.与实施例1类似,本发明耦合方法制备的该耦合结构实施例2可工作于o-,c-,l-等波段。作为优选,工作波段为c-波段,更优选的,波长为1550纳米。
66.本发明提供的边发射激光芯片与硅光芯片中光波导的耦合结构实施例中,边发射激光器(其包含边发射激光芯片)倾斜装焊在硅光芯片之上;硅光芯片,其上设有耦合光栅4及波导5;聚合物、玻璃透明介质等构成的介质填充物9,其填充于边发射激光芯片与硅光栅4之间,与激光芯片和硅光栅4相连接,覆盖出射光的传播路径。本发明采用边发射激光芯片与硅光芯片中的输入光栅4进行倾斜耦合封装,把倾斜输出的光直接投射到硅光栅4上,通过合理设计倾斜角度和光栅周期,使得入射波矢、光栅矢量与硅波导中波矢三者满足光栅方程,从而完成光到硅波导中的耦合。
67.本发明提供的边发射激光芯片与硅光芯片中光波导的耦合方法实施例中,在硅光芯片上利用光刻和等离子体刻蚀,制备出矩形的硅波导5和楔形的光栅结构4,作为外光源向硅光芯片的光耦合器;此光栅可以是均匀光栅、啁啾光栅、聚焦光栅或变折射率光栅;在硅光芯片需要连接激光芯片位置处预置一组特定高度的焊料8(焊珠或焊条)以及对准标记7;把边发射的激光芯片对准倾斜倒装焊到硅光芯片之上;再利用聚合物或玻璃透明介质的介质填充物9填充激光芯片与硅光栅之间光的路径,如图1中两根虚箭头所示。本发明将边发射激光芯片与硅光芯片中的输入光栅4进行倾斜耦合封装的方法,可完全在现有微电子和光电子的封装线上完成,可批量放大自动化生产,封装成本低。
68.基于上述耦合结构及耦合方法实施例可知,本发明全反射转接的边发射激光芯片与硅光芯片中光波导的倾角-光栅耦合结构及方法相对于现有技术至少具有以下优势:
69.(1)本发明通过将边发射激光芯片倾斜装焊在硅光芯片之上,把倾斜输出的光直接投射到硅光栅上,这种方案相比于端面和隐逝波耦合方案,对激光芯片和硅光芯片的结构和加工工艺无特殊要求,对于波导和光源的对准精度要求低,加工容差大,有利于增加回路设计灵活性、降低加工封装成本。
70.(2)相比于垂直入射-光栅耦合,本发明中入射输入光栅的光线与垂直方向之间存在倾角,可以有效抑制光耦合过程中的背向反射,提高耦合效率。
71.(3)相比于水平入射-光栅耦合,本发明无需引入额外的全内反射转接结构或将激光芯片输出波段端面进行额外加工,降低了反射损耗、简化了工艺流程。
72.(4)本发明用聚合物、玻璃透明介质等介质填充物9填充在激光芯片与硅光栅之间,避免了光路径中可能的微尘对光的散射,也起到折射率匹配的作用,减小了光场损耗,进一步提高耦合效率。
73.(5)本发明可完全在现有微电子或光电子的封装线上完成,不引入额外加工步骤,因此可批量放大自动化生产,具有广泛的应用前景。
74.本文中应用了具体个例对本发明的原理及实施方式进行了阐述,以上实施例的说明只是用于帮助理解本发明的控制方法及其核心思想;同时,对于本领域的一般技术人员,依据本发明的思想,在具体实施方式及应用范围上均会有改变之处。综上所述,本说明书内容不应理解为对本发明的限制。