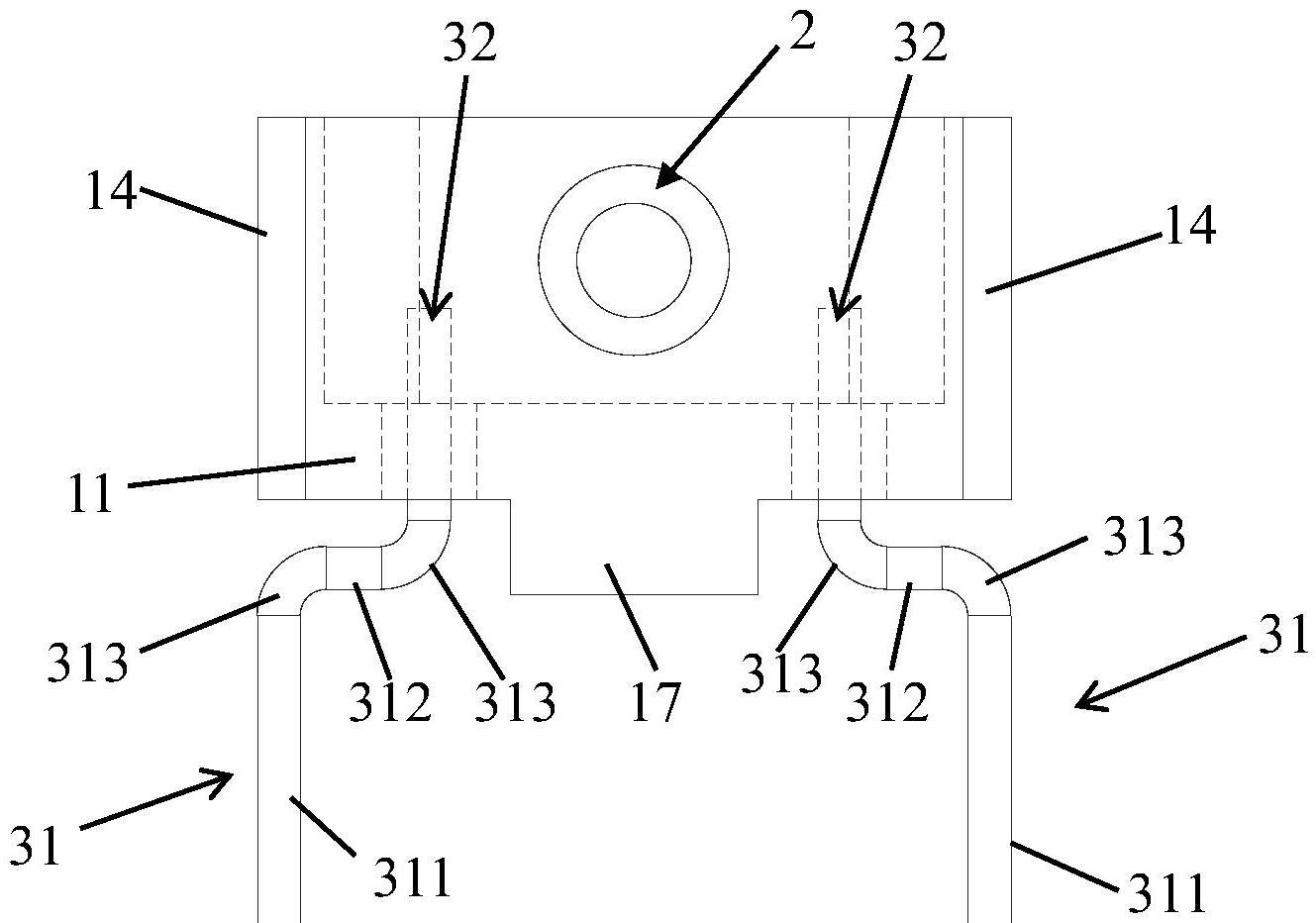
1.本实用新型涉及光电相关技术领域,尤其涉及一种光接收组件的管壳封装结构。
背景技术:2.光接收组件是将光信号转换为电信号的电器元件。公告号为cn217689524u的中国实用新型专利公开了一种光接收组件管壳封装结构。如图1-3所示,光接收组件管壳封装结构包括具有电路板容置腔12
′
的金属壳体1
′
、多个金属管脚2
′
以及与所述金属壳体1
′
连接的光纤管3
′
,光纤管3
′
与电路板容置腔12
′
连通,金属壳体1
′
的壳体侧板11
′
设有多个壳体通孔,金属管脚2
′
一端从壳体通孔插入金属壳体1
′
的电路板容置腔12
′
中,金属管脚2
′
的主体部分处于壳体侧板11
′
的外侧并向下延伸。金属管脚2
′
的主体部分与壳体侧板11
′
需要预留出一定的空间,以避免金属管脚2
′
的主体部分与壳体侧板11
′
接触干涉。
3.光接收组件管壳封装结构最后要通过夹具组装到盒体中,在盒体底板上开设有底板通孔,金属管脚2
′
从底板通孔中向下穿出。
4.因为,金属管脚2
′
的主体部分处于金属壳体1
′
的外侧,在将光接收组件管壳封装结构组装到盒体中时,还需要在盒体侧板与金属管脚2
′
之间留出一定的间隙,以避免挤压金属管脚2
′
,产品的宽度尺寸大。
5.另外,由于两排金属管脚2
′
的主体部分处于金属壳体1
′
的两侧,在夹取光接收组件管壳封装结构进行组装时,夹具需要避开两侧的金属管脚2
′
,只能夹持在前后两根金属管脚2
′
之间,定位要求高。
技术实现要素:6.本实用新型的目的在于克服现有技术的不足,提供一种新型的光接收组件的管壳封装结构,其金属管脚的管脚主体段处于金属壳体的底板的下方,不再占用宽度方向的空间,夹具可夹持金属壳体的侧板的任意位置,便于夹持操作和组装。
7.本实用新型技术方案提供一种光接收组件的管壳封装结构,包括具有安装腔的金属壳体、连接在所述金属壳体的前部的光纤管和连接在所述金属壳体底部的两排金属管脚,两排所述金属管脚处于所述光纤管的轴线的相对两侧;
8.所述金属壳体的底板上处于所述光纤管的轴线的相对两侧分别设置有一排管脚安装孔,每根所述金属管脚与一个所述管脚安装孔对应连接;
9.所述金属管脚包括管脚主体段和连接在所述管脚主体段的上端的管脚连接段;
10.所述管脚主体段处于所述底板的下方,所述管脚连接段穿过所述管脚安装孔并伸入所述安装腔中,所述管脚连接段与所述管脚安装孔的孔壁连接固定。
11.在其中一项可选技术方案中,每排述金属管脚中,其中一根所述金属管脚的所述管脚连接段与所述管脚安装孔的孔壁焊接,另外的所述金属管脚的所述管脚连接段与所述管脚安装孔的孔壁之间填充有玻璃焊料层。
12.在其中一项可选技术方案中,每排管脚安装孔包括一个第一通孔和至少两个第二
通孔,其中,所述第二通孔的半径大于所述第一通孔的半径;
13.所述第二通孔中填充有所述玻璃焊料层。
14.在其中一项可选技术方案中,所述底板的底面向下延伸有支撑凸台,所述支撑凸台处于两排所述金属管脚的所述管脚主体段之间。
15.在其中一项可选技术方案中,所述管脚主体段包括有竖直延伸段和连接在所述竖直延伸段的上端的水平延伸段,所述管脚连接段的下端与所述水平延伸段连接;
16.所述竖直延伸段与所述支撑凸台之间的距离大于所述管脚连接段与所述支撑凸台之间的距离;
17.所述水平延伸段的底面与所述支撑凸台的底面平齐,或者,所述水平延伸段的底面处于所述支撑凸台的底面的上方。
18.在其中一项可选技术方案中,所述水平延伸段与所述竖直延伸段的上端之间及所述水平延伸段与所述管脚连接段的下端之间分别通过圆弧过渡段连接。
19.在其中一项可选技术方案中,所述支撑凸台与所述金属壳体一体成型。
20.在其中一项可选技术方案中,所述支撑凸台以所述光纤管的轴线对称布置。
21.在其中一项可选技术方案中,所述管脚主体段与所述底板的侧边之间的最小距离为d,其中,d≥0。
22.在其中一项可选技术方案中,每排金属管脚分别包括四根所述金属管脚。
23.采用上述技术方案,具有如下有益效果:
24.本实用新型提供的光接收组件的管壳封装结构,包括金属壳体、两排金属管脚和光纤管。金属壳体中具有安装腔,用于安装电路板,光纤管连接在金属壳体的前端并与安装腔连通。金属壳体的底板上设置有两排管脚安装孔,每根所述金属管脚与一个管脚安装孔对应连接。连接时,金属管脚的管脚主体段处于底板的下方,金属管脚的管脚连接段穿过底板的管脚安装孔并伸入到安装腔中,管脚连接段与管脚安装孔的孔壁连接固定。
25.本实用新型提供的光接收组件的管壳封装结构,两排金属管脚的管脚主体段都处于金属壳体的底板的下方,不再占用宽度方向的空间,减小了管壳封装结构的宽度方向的尺寸。在将管壳封装结构安装到盒体中时,无需再在盒体侧板与金属壳体之间留出避让金属管脚的空间,减小了组装产品在宽度方向的结构尺寸。在将管壳封装结构通过夹具安装到盒体中时,夹具可夹持金属壳体的侧板的任意位置,便于夹持操作和组装。
附图说明
26.参见附图,本实用新型的公开内容将变得更易理解。应当理解:这些附图仅仅用于说明的目的,而并非意在对本实用新型的保护范围构成限制。图中:
27.图1为现有技术中的光接收组件管壳封装结构的主视图;
28.图2为图1所示的光接收组件管壳封装结构的俯视图;
29.图3为图1所示的光接收组件管壳封装结构的侧视图;
30.图4为本实用新型一实施例提供的管壳封装结构的俯视图;
31.图5为图4所示的管壳封装结构的主视图;
32.图6为图4所示的管壳封装结构的侧视图;
33.图7为图4沿着a-a向的剖视图;
34.图8为图4沿着b-b向的剖视图;
35.图9为图5沿着c-c向的剖视图;
36.图10为图5沿着d-d向的剖视图;
37.图11为组装在一起的金属壳体与光纤管的俯视图。
具体实施方式
38.下面结合附图来进一步说明本实用新型的具体实施方式。其中相同的零部件用相同的附图标记表示。需要说明的是,下面描述中使用的词语“前”、“后”、“左”、“右”、“上”和“下”指的是附图中的方向,词语“内”和“外”分别指的是朝向或远离特定部件几何中心的方向。
39.如图4-8和图11所示,本实用新型一实施例提供的光接收组件的管壳封装结构,包括具有安装腔15的金属壳体1、连接在金属壳体1的前部的光纤管2和连接在金属壳体1底部的两排金属管脚3,两排金属管脚3处于光纤管2的轴线的相对两侧。
40.金属壳体1的底板11上处于光纤管2的轴线的相对两侧分别设置有一排管脚安装孔16,每根金属管脚3与一个管脚安装孔16对应连接。
41.金属管脚3包括管脚主体段31和连接在管脚主体段31的上端的管脚连接段32。
42.管脚主体段31处于底板11的下方,管脚连接段32穿过管脚安装孔16并伸入安装腔15中,管脚连接段32与管脚安装孔16的孔壁连接固定。
43.本实用新型提供的光接收组件的管壳封装结构,包括金属壳体1、两排金属管脚3和光纤管2。金属壳体1的散热效果好,其可以采用可伐合金镀金壳体。金属壳体1包括矩形的底板11、前端板12、后端板13和两块侧板14。前端板12连接在底板11的前端,后端板13连接在底板11的后端,侧板14连接在前端板12、后端板13及底板11的侧边之间。底板11、前端板12、后端板13和侧板14可一体成型。在底板11、前端板12、后端板13及两块侧板14之间围成有安装腔15,安装腔15用于安装电路板。
44.光纤管2连接在金属壳体1的前端板12上,光纤管2与安装腔15连通,使得光纤能够从光纤管2伸入安装腔15中,以与电路板耦合。光纤管2为金属管,其与金属壳体1可用金属焊料焊接。
45.底板11上设置有两排管脚安装孔16,两排管脚安装孔16以光纤管2的中心轴对称布置。每排管脚安装孔16包括多个间隔布置的管脚安装孔16。
46.在底板11的底部相应地连接有两排金属管脚3,每排金属管脚3包括多根间隔布置的金属管脚3。每根金属管脚3与一个管脚安装孔16对应连接。金属管脚3包括管脚主体段31和管脚连接段32,管脚连接段32连接在管脚主体段31的上端。管脚连接段32与管脚主体段31一体成型。管脚连接段32与管脚主体段31连接可呈直线形或呈折弯形。
47.在将金属管脚3与金属壳体1连接时,每根金属管脚3的管脚主体段31都处于底板11的下方,每根金属管脚3的管脚连接段32都穿过底板11的一个管脚安装孔16并伸入到安装腔15中,管脚连接段32与管脚安装孔16的孔壁连接固定。管脚连接段32伸入安装腔15中以与电路板连接。
48.由此,本实用新型提供的光接收组件的管壳封装结构,两排金属管脚3的管脚主体段31都处于金属壳体1的底板11的下方,不再占用宽度方向的空间,减小了管壳封装结构在
宽度方向的尺寸。
49.在将管壳封装结构安装到盒体中时,无需再在盒体侧板与金属壳体1之间留出避让金属管脚3的空间,减小了组装产品在宽度方向的结构尺寸。在将管壳封装结构通过夹具安装到盒体中时,夹具可夹持金属壳体1的侧板14的任意位置,便于夹持操作和组装。
50.在其中一个实施例中,如图7-10所示,每排述金属管脚3中,其中一根金属管脚3的管脚连接段32与管脚安装孔16的孔壁焊接,另外的金属管脚3的管脚连接段32与管脚安装孔16的孔壁之间填充有玻璃焊料层4。
51.本实施例中,每排述金属管脚3中,其中一根金属管脚3为短路管脚,使得电源地与信号地是同一个地,减少电磁干扰。另外的金属管脚3与管脚安装孔16的孔壁之间采用玻璃焊料层4绝缘并焊接连接。在焊接时,将作为短路管脚的金属管脚3的管脚连接段32直接与管脚安装孔16的孔壁采用金属焊料焊接,在另外的金属管脚3的管脚连接段32与管脚安装孔16的孔壁之间填充玻璃焊料,将管脚连接段32与孔壁通过玻璃焊料焊接,玻璃焊料最终形成绝缘的玻璃焊料层4。
52.在其中一个实施例中,如图7-11所示,每排管脚安装孔16包括一个第一通孔161和至少两个第二通孔162,其中,第二通孔162的半径大于第一通孔161的半径。第二通孔162中填充有玻璃焊料层4。
53.本实施例中,为了便于实现不同的管脚连接段32的焊接连接,将管脚安装孔16分为一个第一通孔161和两个以上的第二通孔162。
54.第一通孔161半径略大于管脚连接段32的半径,以便将管脚连接段32穿过第一通孔161,并与第一通孔161的孔壁通过金属焊料焊接。
55.第二通孔162的半径远大于管脚连接段32的半径,以便在第二通孔162中填充玻璃焊料,以将管脚连接段32与第二通孔162的孔壁通过玻璃焊料焊接。
56.第一通孔161的半径可设置为在0.5mm左右,第二通孔162的半径可设置为在1mm左右。相邻的管脚安装孔16的中心之间的距离在2.54mm左右。
57.在其中一个实施例中,如图6和8所示,底板11的底面向下延伸有支撑凸台17,支撑凸台17处于两排金属管脚3的管脚主体段31之间。
58.本实施例中,在底板11的底部设置有支撑凸台17,支撑凸台17处于底板11的中部并沿着底板11的长度方向延伸,以将两排金属管脚3的管脚主体段31间隔在支撑凸台17的两侧,避免两侧的金属管脚3的管脚主体段31受压接触。
59.在将管壳封装结构安装到盒体中时,支撑凸台17处于盒体的底板上,起到支撑作用。
60.在其中一个实施例中,如图6和8所示,管脚主体段31包括有竖直延伸段311和连接在竖直延伸段311的上端的水平延伸段312,管脚连接段32的下端与水平延伸段312连接。
61.竖直延伸段311与支撑凸台17之间的距离大于管脚连接段32与支撑凸台17之间的距离。
62.水平延伸段312的底面与支撑凸台17的底面平齐,或者,水平延伸段312的底面处于支撑凸台17的底面的上方。
63.本实施例中,金属管脚3呈折弯状。管脚主体段31包括有竖直延伸段311和水平延伸段312,水平延伸段312连接在竖直延伸段311的上端,并朝向支撑凸台17侧延伸,管脚连
接段32的下端与水平延伸段312连接。竖直延伸段311处于管脚连接段32的外侧,以增加处于支撑凸台17两侧的竖直延伸段311之间的距离,减少相互影响。
64.水平延伸段312的底面与支撑凸台17的底面平齐或处于支撑凸台17的底面的上方。在将管壳封装结构安装到盒体中时,支撑凸台17处于盒体的底板上,水平延伸段312的底面不与盒体的底板接触,从而避免水平延伸段312受压。
65.在其中一个实施例中,如图6和8所示,水平延伸段312与竖直延伸段311的上端之间及水平延伸段312与管脚连接段32的下端之间分别通过圆弧过渡段313连接,实现圆滑过渡。
66.竖直延伸段311、圆弧过渡段313、水平延伸段312及管脚连接段32一体成型为金属管脚3。
67.在其中一个实施例中,支撑凸台17与金属壳体1一体成型,方便加工成型,结构强度高。
68.在其中一个实施例中,如图6和8所示,支撑凸台17以光纤管2的轴线对称布置,以便更好地隔开以光纤管2的轴线对称布置的两排管脚主体段31。
69.在其中一个实施例中,如图6和8所示,管脚主体段31与底板11的侧边之间的最小距离为d,其中,d≥0。
70.本实施例中,管脚主体段31与底板11的侧边或侧板14之间的距离大于0,也即是说,管脚主体段31处于底板11的边界范围内,不会凸出金属壳体1的外侧,不会增加结构沿着宽度方向的尺寸。
71.在其中一个实施例中,如图4-5和图7所示,每排金属管脚3分别包括四根金属管脚3,为8pin管壳封装结构。
72.在其中一个实施例中,金属壳体1的宽度在7-8mm之间,长度在11-12mm之间。安装腔15的宽度在6-7mm之间,长度在9-10mm之间。
73.在其中一个实施例中,光纤管2的长度在2-2.5mm之间,外径在2mm左右,内径在1.2mm左右。
74.根据需要,可以将上述各技术方案进行结合,以达到最佳技术效果。
75.以上的仅是本实用新型的原理和较佳的实施例。应当指出,对于本领域的普通技术人员来说,在本实用新型原理的基础上,还可以做出若干其它变型,也应视为本实用新型的保护范围。