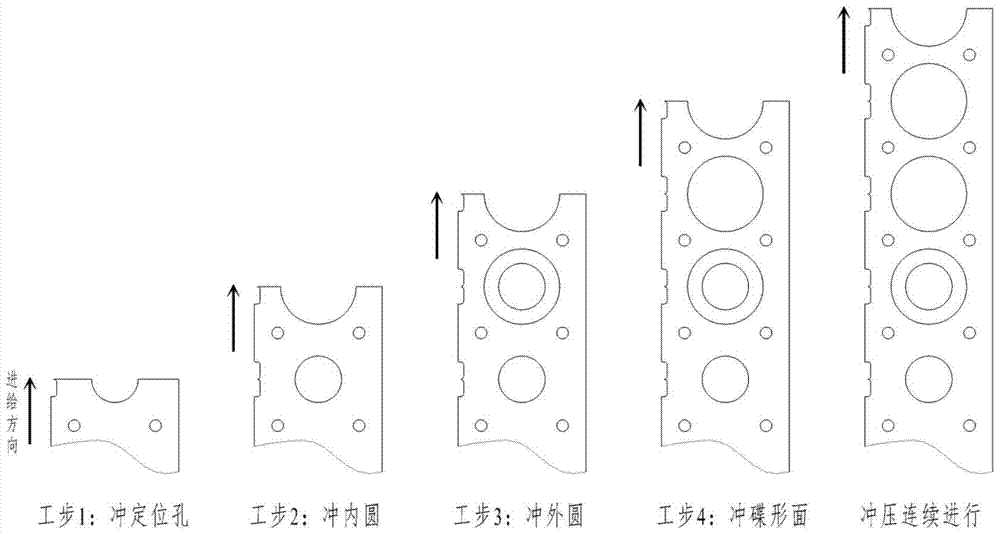
本发明属于制造工艺,具体涉及一种弹簧垫圈制造工艺。
背景技术:
:弹簧垫圈是应用最广泛的减震、缓冲、防脱落的零部件之一。根据应用领域不同,弹簧垫圈的材料也不同。大部分的应用情况不需要弹簧垫圈具备特殊性能,因此大多选用50crva、60si2mna或者其他合金,其制造工艺已经比较成熟。但是在核反应堆上使用的弹簧垫圈情况比较特殊,具体体现在:1.核反应堆对安全的要求很高,因此弹簧垫圈不能只起到减震、缓冲等作用,还需要其具备补充材料间的热胀差的功能。2.核反应堆需要考虑极端情况下抗冲击的能力,要求弹簧垫圈承受较大交变载荷长久工作。3.假设核反应堆出现事故,弹簧垫圈还需要能够长时间承受高温。经过相关领域科研人员的研发和协调,最终确定使用镍基高温合金gh4169作为核级弹簧垫圈的原始材料。但是由于该材料硬度大,变形不易,且需要根据核级需要进行热处理,因此现有的弹簧垫圈制造方法无法针对镍基高温合金gh4169使用。技术实现要素:本发明针对现有技术缺陷,提供一种弹簧垫圈制造工艺。本发明的技术方案是:一种弹簧垫圈制造工艺,包括下述步骤:步骤一:冲压冲压包括:定位孔冲压、内圆冲压、外圆冲压和碟形面冲压,步骤二:时效热处理对冲压得到的弹簧垫圈进行时效热处理,采用高温真空热处理炉进行时效热处理,真空度优于1.33×10-2pa,首先将弹簧垫圈加热,加热速度为150℃/h~180℃/h,当温度达到710℃~730℃时停止升温;然后在710℃~730℃的温度范围内保温8~9h;第三步,以35℃/h~75℃/h的速度降温,直到温度降低到610℃~630℃;第四步,在610℃~630℃的温度范围内保温8~9h;第五步,以35℃/h~75℃/h的速度降温,降温到380℃~420℃;第六步,冲入氩气,氩气压力为0.08~0.09mpa,并冷却;第七步,当温度小于等于120℃时,将弹簧垫圈放置在室温环境自然冷却,步骤三:常温强压处理进行5次常温强压处理,每次都对弹簧垫圈施加2100n的负荷力,保持30~60秒,步骤四:热强压处理1)将弹簧垫圈装在螺杆上,弹簧垫圈内径与螺杆直径的配合间隙控制在0.2~0.3mm,装载数量5~15片,装载时,弹簧垫圈正、反相对顺序放置,2)对弹簧垫圈施加压力,保证施加压力后每个弹簧垫片的高度为0.93~0.95mm,3)将装好的弹簧垫圈放入热处理炉中,进行热处理,热处理工艺为:第一次升温至300℃,保温6h;降温至室温后进行第二次升温;第二次升温至250℃,保温6h。如上所述的一种弹簧垫圈制造工艺,其中,所述的步骤一中,定位孔冲压:在带材两端冲压定位孔,定位孔以两个为一组,同组定位孔位于带材两端,相邻组别的定位孔之间的距离相同,该定位孔用于后续工艺的定位,内圆冲压:使用内孔冲头进行内圆冲压,将多余的圆形部分冲压掉,形成一个圆孔,该圆孔是弹簧垫圈的圆孔,外圆冲压:使用外圆冲头进行外圆冲压,按照弹簧垫圈外圆的尺寸进行冲压,冲压掉的圆环就是弹簧垫圈的雏形,冲压完成后将冲压出来的圆环再放置回原位置,碟形面冲压:用碟形面凸模进行碟形面冲压,将圆环形的弹簧雏形冲压成弹簧垫圈的形状,所述的碟形面凸模的形状与要生产的弹簧垫圈的形状相匹配。如上所述的一种弹簧垫圈制造工艺,其中,所诉的外圆冲压按照下述过程进行:在带材上方设置外圆冲头,在带材下方外圆冲头对应的位置设置顶料块,在顶料块下方设置弹簧,冲压时,用外圆冲头向下冲压,冲压出圆环形的弹簧雏形,该圆环形的弹簧雏形被压到顶料块上,当外圆冲头回位时,顶料弹簧将顶料块定回原位,因而被冲压掉的圆环形的弹簧雏形也就被顶回原位。。本发明的显著效果是:1.自动化,效率高。操作人员只需将gh419带材通过送料器送进模具,模具一次完成全部冲压成型工艺。2.成本低,特别适合小批量生产。只需一套结构简单的冲压模具即可完成弹簧垫圈的冲压工艺,操作简单,成本低廉。3.灵活多变,适用性强。只需要更换一套冲头和凹模,即可适用于不同规格的弹簧垫圈的加工,特别适用于多种类小批量弹簧垫圈的生产以及科研任务。4.产品尺寸精度高。该模具采取精冲模设计结构,产品成形精度较高,成形后弹簧内、外直径以及同轴度、平行度等重要尺寸精度能达到0.02mm。5.可改造性强。在该级进模基础上,并排增加冲头数量,可实现批量弹簧垫圈的规模化生产,且单个凸、凹模独立运行,方便维修和更换。附图说明图1是本申请弹簧垫圈制造工艺的工作过程示意图;图2是被加工条带在不同步骤加工情况的示意图;图3是时效热处理时间温度曲线图;图4是强压处理的曲线图。图中:1.起始端、2.带材、3.定位冲孔、4.内孔冲头、5.外圆冲头、6.碟形面凸模、7.弹簧垫圈、8.碟形面凹模、9.顶料弹簧、10.顶料块。具体实施方式一种弹簧垫圈制造工艺,包括下述步骤:步骤一:冲压冲压包括:定位孔冲压、内圆冲压、外圆冲压和碟形面冲压。定位孔冲压:在带材两端冲压定位孔,定位孔以两个为一组,同组定位孔位于带材两端,相邻组别的定位孔之间的距离相同。该定位孔用于后续工艺的定位。内圆冲压:使用内孔冲头进行内圆冲压,将多余的圆形部分冲压掉,形成一个圆孔,该圆孔是弹簧垫圈的圆孔。外圆冲压:使用外圆冲头进行外圆冲压,按照弹簧垫圈外圆的尺寸进行冲压,冲压掉的圆环就是弹簧垫圈的雏形,冲压完成后将冲压出来的圆环再放置回原位置。外圆冲压按照下述过程进行:在带材上方设置外圆冲头,在带材下方外圆冲头对应的位置设置顶料块,在顶料块下方设置弹簧。冲压时,用外圆冲头向下冲压,冲压出圆环形的弹簧雏形,该圆环形的弹簧雏形被压到顶料块上,当外圆冲头回位时,顶料弹簧将顶料块定回原位,因而被冲压掉的圆环形的弹簧雏形也就被顶回原位。碟形面冲压:用碟形面凸模进行碟形面冲压,将圆环形的弹簧雏形冲压成弹簧垫圈的形状。所述的碟形面凸模的形状与要生产的弹簧垫圈的形状相匹配。步骤二:时效热处理对冲压得到的弹簧垫圈进行时效热处理。采用高温真空热处理炉进行时效热处理,真空度要求优于1.33×10-2pa。首先将弹簧垫圈加热,加热速度为150℃/h~180℃/h,当温度达到710℃~730℃时停止升温;然后在710℃~730℃的温度范围内保温8~9h;第三步,以35℃/h~75℃/h的速度降温,直到温度降低到610℃~630℃;第四步,在610℃~630℃的温度范围内保温8~9h;第五步,以35℃/h~75℃/h的速度降温,降温到380℃~420℃;第六步,冲入氩气,氩气压力为0.08~0.09mpa,并自然冷却;第七步,当温度小于等于120℃时,将弹簧垫圈放置在室温环境自然冷却。步骤三:常温强压处理进行5次常温强压处理,每次都对弹簧垫圈施加2100n的负荷力,保持30~60秒。步骤四:热强压处理1)将弹簧垫圈装在螺杆上,弹簧垫圈内径与螺杆直径的配合间隙控制在0.2~0.3mm,装载数量5~15片。装载时,弹簧垫圈正、反相对顺序放置,不得有连续2片同为正向或反向。2)对弹簧垫圈施加压力,保证施加压力后每个弹簧垫片的高度为0.93~0.95mm。3)将装好的弹簧垫圈放入热处理炉中,进行热处理,热处理工艺为:第一次升温至300℃,保温6h;降温至室温后进行第二次升温;第二次升温至250℃,保温6h。下面给出一个具体的例子:需要加工的gh4169合金性,性能如表1所示:表1gh4169合金性能参数表需要加工的弹簧垫圈的尺寸为外径φ13mm,内径φ8mm,厚度0.8mm,自由高度1.05mm~1.1mm,内外圆同轴度φ0.05mm,两平面平行度0.06mm。首先将上述合金加工成宽度22mm的带材,使用80t冲床按步骤冲压,按照冲定位孔、冲内孔、冲外圆、冲碟形面的顺序自动完成整个成形过程。冲压形成的弹簧垫圈的相关参数如表2所示。表2改进后碟形弹簧检测数据编号自由高度/mm同轴度/mm平行度/mmb-11.070.00680.0125b-21.070.00390.0089b-31.070.00830.0157b-41.070.00440.0182时效热处理采用高温真空热处理炉进行,真空度要求优于1.33×10-2pa,具体热处理工艺如下:以150℃/h的速率升温至720±10℃,保温8~9小时,再以55℃/h速率降至620±10℃,保温8~9小时,炉冷至400℃后冲氩快冷,120℃以下出炉。强压处理后弹簧垫圈的参数如表3所示。表3强压处理弹簧高度实测值对弹簧垫片进行压力测试得到的结果如附图4所示。强压处理过程中,发现第一次强压时,弹簧垫圈有一个很明显的屈服过程,屈服状态下,弹簧产生较大的塑性变形,弹簧力值呈现下降趋势。之后若干次压缩,弹簧的屈服极限大幅度提升,不再出现屈服情况,当弹簧经过4-5次压缩后,其高度趋于稳定,弹簧受力后也不再产生塑性变形。热强压处理完成后,弹簧垫片的性能满足设计要求。图1对应定位孔冲压、内圆冲压、外圆冲压和碟形面冲压。图2中,带材随工作流程也会产生的四个不同形状。当前第1页12