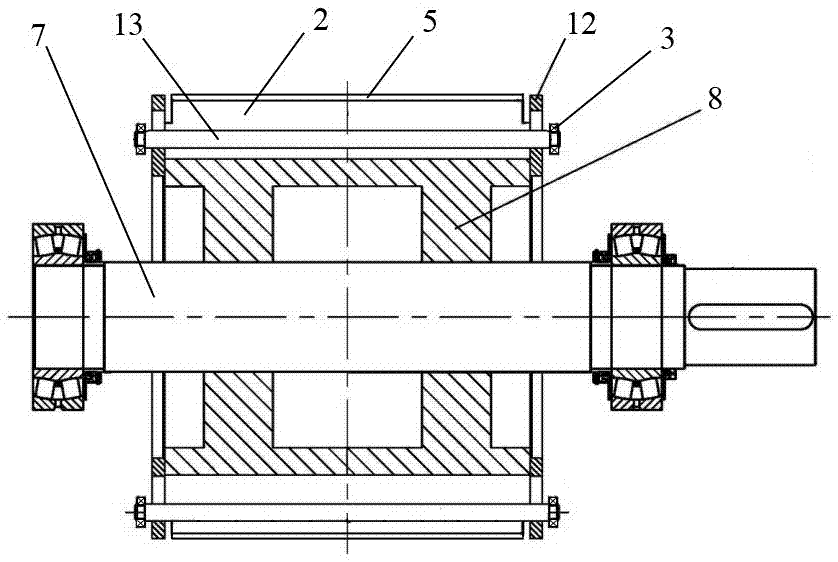
本发明涉及一种型煤生产设备,具体地说是一种型煤对辊挤压成型机构、型煤生产装置及型煤生产方法。
背景技术:
发电、焦炭和化肥等行业是用煤大户,而所供应的无烟煤又多数都是粉煤,而粉煤需要制成型煤才能满足需要。现有由无烟粉煤制成的型煤存在的问题是强度低,气化工艺技术指标不理想。为提高型煤强度,就要增大型煤生产设备的工作压力和出口阻力,由此既造成巨大的能源浪费,也相应降低了型煤的生产效率。而工作压力的增大,使得型煤的出模困难,并且还加重了轧辊的磨损,造成轧辊的使用寿命降低,使用成本提高。
技术实现要素:
本发明的目的之一就是提供一种型煤对辊挤压成型机构,以解决现有型煤成型机构存在的出模困难和磨损严重的问题。
本发明的目的之二就是提供一种型煤生产装置,以解决现有型煤生产设备耗能大、型煤强度低和生产效率低的问题。
本发明的目的之三就是提供一种型煤生产方法,以实现型煤的高强、快速和高效生产。
本发明的目的之一是这样实现的:一种型煤对辊挤压成型机构,包括轴向并置的第一轧辊和第二轧辊;所述第一轧辊的结构是:在所述第一轧辊的辊面上设置有沿圆周均布的条形凸板,所述条形凸板的侧向中心线指向所述第一轧辊的轴心线,在所述条形凸板的顶面设有压条,所述压条的宽度小于条形凸板的顶面宽度,但大于相邻两个条形凸板的相邻顶沿间的槽口宽度;在相邻两个条形凸板之间的沟槽中设置有横置的顶出杆,在所述顶出杆的两端分别设有伸出沟槽侧端口的伸出轴,在所述伸出轴上套接有挂板和轴承,所述挂板的指向圆心的一端通过拉簧与固定在轧辊中心轴轴头上的圆盘相连接。
所述第二轧辊的结构与所述第一轧辊的结构相同。两个轧辊平行设置并以凸板上沿与沟槽交替相对的方式相对同步旋转运行;即在两个轧辊的压合面处,第一轧辊辊面上的一个沟槽与第二轧辊辊面上的一个条形凸板相对,且第二轧辊的条形凸板上的压条伸入到第一轧辊的沟槽上面的两个相邻的压条之间,但不与第一轧辊上的该两个压条相接触,也不与第一轧辊上设置该两个压条的条形凸板相接触;第一轧辊上的条形凸板与第二轧辊上的沟槽的配合运行方式与上述的配合运行方式相同。
本发明型煤对辊挤压成型机构通过在轧辊的条形凸板上设置凸起的压条,使由两个相邻条形凸板构成的沟槽的上口形成一种非平齐的凹凸槽口,这样,在两轧辊交替相对的排布形式下,一个轧辊上的压条就恰好形成封堵另一轧辊的沟槽上口的伸入式封压件,而且两轧辊压条在相互封堵对方沟槽的过程中,还不与对方轧辊上的压条相接触,由此形成一种非接触式的轧辊封合挤压结构。而这种非接触式的封合挤压结构,既满足了高压压合型煤的工作需要,相应提高了型煤的强度,而且还有效避免了对辊成型机构中两轧辊间的相互磨损,使得轧辊的使用寿命得以大幅提高。
另外,在两个轧辊的沟槽中设置顶出杆,通过轴头的轴承与推料导轨的配合,强迫顶出杆在随轧辊的旋转过程中,将沟槽中轧制的型煤顶出沟槽,由此实现了型煤的顺利脱出,解决了现有辊轧成型机构存在的型煤脱出不便的技术难题,有利于提高型煤生产的工作效率。
本发明的目的之二是这样实现的:一种型煤生产装置,包括机架、喂料机构、挤压输送机构和对辊挤压成型机构;所述对辊挤压成型机构,包括轴向并置的第一轧辊和第二轧辊;所述第一轧辊的结构是:在所述第一轧辊的辊面上设置有沿圆周均布的条形凸板,所述条形凸板的侧向中心线指向所述第一轧辊的轴心线,在所述条形凸板的顶面设有压条,所述压条的宽度小于条形凸板的顶面宽度,但大于相邻两个条形凸板的相邻顶沿间的槽口宽度;在相邻两个条形凸板之间的沟槽中设置有横置的顶出杆,在所述顶出杆的两端分别设有伸出沟槽侧端口的伸出轴,在所述伸出轴上套接有挂板和轴承,所述挂板的指向圆心的一端通过拉簧与固定在轧辊中心轴轴头上的圆盘相连接。
所述第二轧辊的结构与所述第一轧辊的结构相同;两个轧辊平行设置并以凸板上沿与沟槽交替相对的方式相对同步旋转运行;即在两个轧辊的压合面处,第一轧辊辊面上的一个沟槽与第二轧辊辊面上的一个条形凸板相对,且第二轧辊的条形凸板上的压条伸入到第一轧辊的沟槽上面的两个相邻的压条之间,但不与第一轧辊上的该两个压条相接触,也不与第一轧辊上设置该两个压条的条形凸板相接触;第一轧辊上的条形凸板与第二轧辊上的沟槽的配合运行方式与上述的配合运行方式相同。
在两个轧辊的端部分别设置有遮挡沟槽侧端口的圆环形侧护板,所述侧护板固定在所述机架上。
在两个轧辊的中心轴的同侧端部分别设置有齿轮,两个轧辊上的齿轮相啮合,所述第一轧辊的中心轴外接减速驱动机构。
在所述机架上的相对轧辊端部且在轧辊压合面以后的旋转位置处,对称设置有推料导轨,使经过其上的轴承带动顶出杆向沟槽的槽口方向移动。
本发明型煤生产装置利用挤压输送机构对煤粉进行挤压式输送,使煤粉带压进入轧辊的沟槽中,利用对辊的强力压合和压条对沟槽的伸入式的压缩作用,可使型煤的制作强度明显提高,而设备的自动挤出脱料工作方式,使得型煤脱出的能源消耗趋近于零,由此克服了现有型煤生产设备的弊端,使能源消耗大幅降低,而生产效率却能够大幅提高,相应提高了企业的经济效益。
本发明的目的之三是这样实现的:一种型煤生产方法,包括以下步骤:
a、设置如前所述的型煤生产装置;
b、加水湿润后的煤粉连续进入与机架相接的喂料机构,并由喂料机构向设置在机架中的挤压输送机构进行连续输送;
c、挤压输送机构将送入的煤粉强力压向位于其下部的对辊挤压成型机构中的第一轧辊和第二轧辊开口向上的沟槽中;
d、对辊挤压成型机构中的第一轧辊和第二轧辊在减速驱动机构的带动下,以一个轧辊上的凸板上沿与另一轧辊上的沟槽在压合面交替相对的方式,相对同步旋转运行;在此运行过程中,由挤压输送机构强力压入轧辊沟槽中的煤粉被逐步压实,并被带向两轧辊间最接近处的压合面;在两个轧辊的压合面处进行轧辊间的非接触式挤压,即第二轧辊的条形凸板上的压条伸入到第一轧辊的沟槽上面的两个相邻的压条之间,但不与第一轧辊上的该两个压条相接触,也不与第一轧辊上设置该两个压条的条形凸板相接触,从而将第一轧辊沟槽中承载的煤粉全部压入该沟槽中;同理,第一轧辊上的条形凸板与第二轧辊上的沟槽采用轧辊间的非接触式挤压方式,将第二轧辊沟槽中承载的煤粉全部压入该沟槽中,完成该沟槽的压型操作;
e、当完成压型操作的沟槽转出轧辊压合面后,在该沟槽中的顶出杆两端伸出轴上套接的轴承转动到推料导轨上,并带动顶出杆逐步向该沟槽的槽口方向移动,将嵌入沟槽中的型煤逐步顶出沟槽,并在该沟槽转到槽口冲下的位置时,型煤从沟槽中自行脱出,并自动掉落到设置在对辊挤压成型机构下方的型煤传送带上;
f、当顶出杆两端的轴承运行脱离开推料导轨后,在拉簧作用下,顶出杆回位到沟槽的底部,随着轧辊的旋转,开始下一轮工作循环。
本发明型煤生产方法以非接触式的轧辊封合挤压对型煤进行压入式的压缩,而轧辊沟槽中的型煤的脱出是依靠顶出杆轴头的轴承与推料导轨的配合来自动实现,由此实现了型煤的高强、快速和高效的生产,满足了生产实际的使用需要,也满足了发电、焦炭和化肥等用煤大户的对型煤的使用需求。
附图说明
图1是本发明型煤对辊挤压成型机构的结构示意图。
图2是图1所示型煤对辊挤压成型机构在压合面处的局部放大图。
图3是第一轧辊的剖面图。
图4是本发明型煤生产装置的结构示意图。
图5是图4所示型煤生产装置的俯视图。
图中:1、挂板,2、条形凸板,3、轴承,4、拉簧,5、压条,6、圆盘,7、中心轴,8、轧辊本体,9、推料导轨,10、第一轧辊,11、第二轧辊,12、侧护板,13、顶出杆,20、机架,21、输送电机,22、进料口,23、挤压输送机构,24、对辊挤压成型机构,25、从动齿轮,26、变速箱,27、成型电机,28、主动齿轮。
具体实施方式
实施例1
如图1所示,本发明型煤对辊挤压成型机构包括第一轧辊10和第二轧辊11,两个轧辊的轴心线相互平行,且两个轧辊的结构相同。
如图1、图2、图3所示,所述第一轧辊10是在轧辊本体8的辊面上设置有沿圆周均布的若干条形凸板2,条形凸板2沿轴向分布,其侧向的中心线均指向第一轧辊10的轴心线。在条形凸板2的顶面设有压条5。由图2可见,压条5的宽度小于条形凸板2的顶面宽度,但大于相邻两个条形凸板2的相邻顶沿间的槽口宽度。压条5与条形凸板2可以是一体制作成型;也可以是分体制作,然后再通过机加工方式固定连接在一起。
在相邻两个条形凸板2之间的沟槽中设置有横置的顶出杆13(图3),顶出杆13的截面外形与沟槽的底部形状相同,顶出杆13的顶面为平面。在顶出杆13的两端分别设有伸出沟槽侧端口的伸出轴(图3),在伸出轴上套接有挂板1和轴承3(图1),挂板1的指向圆心的一端接有两个拉簧4,两个拉簧4的另一端连接在圆盘6的连接孔上。圆盘6固定在轧辊的中心轴7的轴头上。常态下,顶出杆13的两端通过两个挂板和四根拉簧拉向沟槽的底部。
第二轧辊11与第一轧辊10平行设置,并且是以一个轧辊上的凸板上沿与另一个轧辊上的沟槽交替相对的方式,相对同步旋转运行(图2)。意即,在两个轧辊的压合面处(即位置最近处),第一轧辊10辊面上的一个沟槽与第二轧辊11辊面上的一个条形凸板2相对,且第二轧辊11的条形凸板2上的压条5伸入到第一轧辊10的沟槽上面的两个相邻的压条5之间,但不与第一轧辊10上的该两个压条5相接触,也不与第一轧辊10上设置该两个压条5的条形凸板2相接触。第一轧辊10上的条形凸板2与第二轧辊11上的沟槽的配合运行方式与上述的配合运行方式相同。这样,在两轧辊交替相对的排布运行形式下,一个轧辊上的压条就恰好形成封堵另一轧辊的沟槽上口的伸入式封压件,而且两轧辊压条在相互封堵对方沟槽的过程中,还不与对方轧辊上的压条相接触,由此形成一种非接触式的轧辊封合挤压结构。
如图3所示,在第一轧辊10和第二轧辊11这两个轧辊的端部分别设置有遮挡沟槽侧端口的圆环形侧护板12,侧护板12是固定在型煤生产装置的机架上,不随轧辊转动。
图1中,在型煤生产装置的机架上还固定连接有推料导轨9。在每个轧辊的两端分别设置一个推料导轨9,推料导轨9相对于轧辊的端部且在轧辊压合面以后的旋转位置处。每个轧辊两端的推料导轨9为对称设置结构。在两个轧辊的同一侧面上的两个推料导轨9也是呈对称形式。推料导轨9与顶出杆13轴端上的轴承3在一个旋转平面上,当轧辊转动时,轴承3经过推料导轨9的外边沿,被推离圆周运行轨道,从而带动对应的顶出杆13向所在沟槽的槽口方向外移,以实现对沟槽中轧制的型煤的顶出操作,使型煤脱离沟槽而掉落在型煤生产装置的机架下部的输送带上。
实施例2
如图4、图5 所示,本发明型煤生产装置包括机架20、喂料机构(未图示)、挤压输送机构23和对辊挤压成型机构24等部分。在机架20上设有进料口22,用以连接喂料机构,以将加水湿润后的煤粉连续送入挤压输送机构23中。挤压输送机构23采用立式绞龙结构,通过设置在机架20顶部的输送电机21驱动旋转,将通过进料口22送入的煤粉加压输送到机架20下部的对辊挤压成型机构24中。
对辊挤压成型机构24采用实施例1的结构形式,以两个轧辊上的条形凸板与沟槽的交替配合挤压的运行方式,将煤粉挤压成条棒式的型煤。图5中,在两个轧辊的中心轴7的同侧端分别设置有齿轮,一个是第一轧辊10上连接的是主动齿轮28,第二轧辊11上连接的是从动齿轮25,两个齿轮相互啮合,实现两个轧辊的相向同步旋转。图5中,第一轧辊的中心轴连接减速驱动机构。减速驱动机构包括变速箱26、皮带传动机构和成型电机27等。由成型电机27通过皮带传动机构带动变速箱26输出低速大扭矩的旋转动力,驱动对辊挤压成型机构24工作。
与对辊挤压成型机构24配合的侧护板12(图3)和推料导轨9(图1)等部件均固定在机架20上的对应位置处。因前已述及,此处不再赘述。
实施例3
本发明型煤生产方法是利用本发明型煤生产装置的一种专用型煤制作方法,具体包括以下步骤:
一、加水湿润后的煤粉连续进入与机架20相接的喂料机构,并由喂料机构向设置在机架20中的挤压输送机构23进行连续输送。
二、挤压输送机构23将送入的煤粉强力压向位于其下部的对辊挤压成型机构24中的第一轧辊和第二轧辊中的开口向上的沟槽中。
三、对辊挤压成型机构24中的第一轧辊10和第二轧辊11在减速驱动机构的带动下,以一个轧辊上的凸板上沿与另一轧辊上的沟槽在压合面交替相对的方式,相对同步旋转运行(图1)。在此运行过程中,由挤压输送机构23强力压入轧辊沟槽中的煤粉被逐步压实,并被带向两轧辊间最接近处的压合面(图2)。在两个轧辊的压合面处进行轧辊间的非接触式挤压(图2),即第二轧辊11的条形凸板2上的压条5伸入到第一轧辊10的沟槽上面的两个相邻的压条5之间,但不与第一轧辊10上的该两个压条5相接触,也不与第一轧辊10上设置该两个压条5的条形凸板2相接触,从而将第一轧辊10沟槽中承载的煤粉全部压入该沟槽中。同理,第一轧辊10上的条形凸板2与第二轧辊11上的沟槽采用轧辊间的非接触式挤压方式,将第二轧辊11沟槽中承载的煤粉全部压入该沟槽中,完成该沟槽的压型操作。
四、当完成压型操作的沟槽转出轧辊压合面后,在该沟槽中的顶出杆13两端伸出轴上套接的轴承3转动到推料导轨9上(图1),并带动顶出杆13逐步向该沟槽的槽口方向移动(图2),将嵌入沟槽中的型煤逐步顶出沟槽,并在该沟槽转到槽口冲下的位置时,型煤从沟槽中自行脱出,并自动掉落到设置在对辊挤压成型机构24下方的型煤传送带上。
五、当顶出杆13两端的轴承3运行脱离开推料导轨9后,在拉簧4的作用下,顶出杆13回位到轧辊上的沟槽的底部,随着轧辊的连续旋转,开始下一轮的工作循环。