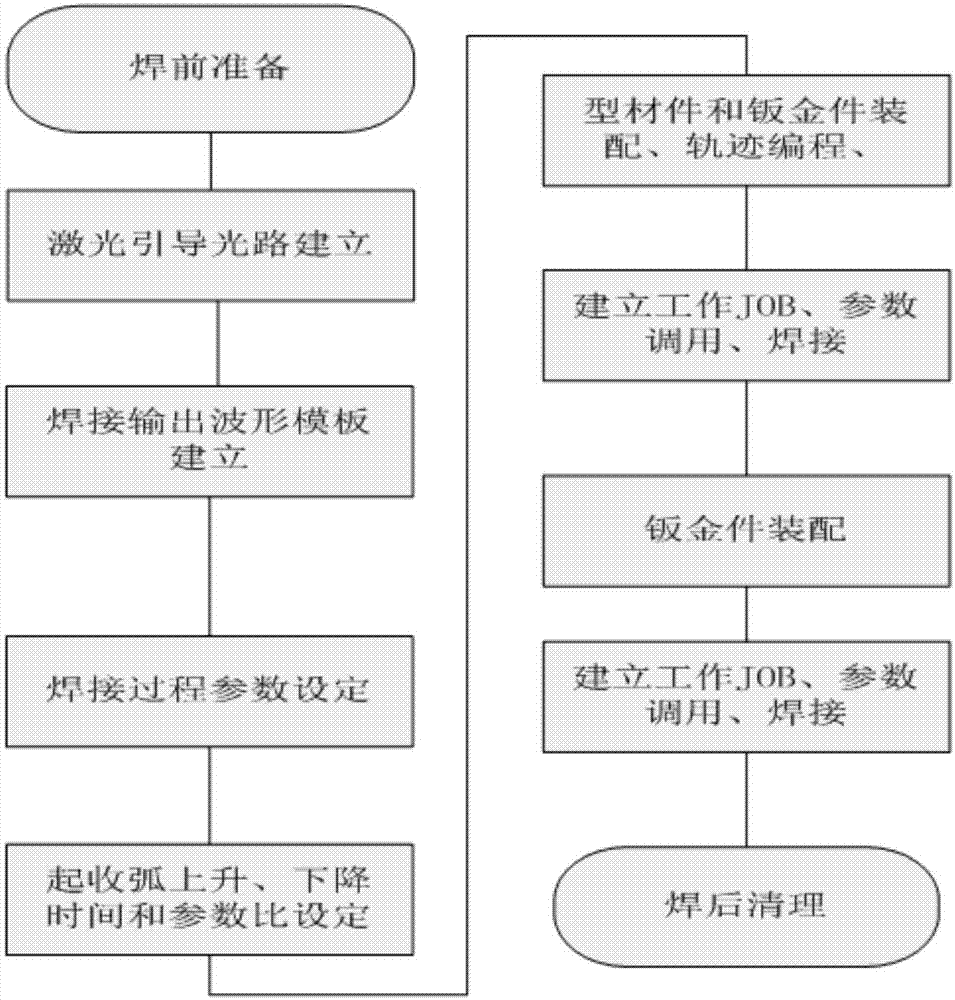
本发明属于轻量化汽车焊接
技术领域:
,涉及一种不加保护气的铝合金激光自熔焊接工艺。
背景技术:
:铝合金密度低,但强度比较高,接近或超过优质钢,塑性好,可加工成各种型材,具有优良的导电性、导热性和抗蚀性,伴随着轻量化汽车的发展,铝合金材质轻,所以铝合金在各行各业的使用比例也越来越大。目前汽车用铝合金主要以5系与6系为主,采用的焊接方法主要有手工mig焊、tig焊等,该焊接过程是焊接人员通过操作焊枪,填丝、外加保护气进行焊接,这些焊接方法在进行焊接时有以下问题点:1、异种系列连接难度大;2、厚板焊接过程中深宽比较小,热影响区较宽,对结构的力学性能降低严重;3、薄铝合金板与厚铝合金板焊接过程中,薄铝合金板易咬边、烧穿,而厚铝合金板不能熔合;4、焊接过程需要加保护气、填焊丝增加了焊接成本。技术实现要素:有鉴于此,本发明为了解决上述不同系列以及不同板厚铝合金板材焊接过程中所存在的问题,提供一种不加保护气的铝合金激光自熔焊接工艺,该激光自熔焊接工艺能够减小铝合金板焊接过程中的焊接变形、减少焊接缺陷的产生;增大焊道深宽比,保证异种型材焊接质量的一致性,降低焊接成本;实现自动化,提高生产效率。为达到上述目的,本发明提供一种不加保护气的铝合金激光自熔焊接工艺,主要包括型材件与钣金件焊接和钣金件与钣金件焊接,其中型材件与钣金件焊接的焊接工艺为:a、焊前准备:将待焊接型材件与钣金件焊缝附近25~50mm的范围内打磨除去型材件与钣金件表面氧化膜后用丙酮或乙醇清洗型材件与钣金件表面油污,其中型材件为2mm厚的6系铝合金,钣金件为1mm厚的5系铝合金;b、装配组对:利用夹紧工装将焊缝两侧的型材件与钣金件压紧,保证型材件与钣金件焊缝间隙≤0.2mm;c、焊接:根据实际型材件与钣金件的匹配性编辑激光自熔焊的轨迹程序,轨迹程序编程过程中需要考虑夹紧工装的状态,防止出现撞枪,同时依据型材件与钣金件的装配状态进行机器人姿态调整,采用激光自熔焊焊接工艺自动焊接型材件与钣金件压紧之间焊缝,焊接速度为30~70mm/min,激光功率为1500~2200w,风刀为0.4~0.6mpa;d、焊后清理及检验:焊接完成后,对焊缝表面进行擦灰清理,按照型材件与钣金件焊缝质量要求进行检验;钣金件与钣金件焊接的焊接工艺为:e、焊前准备:将待焊接钣金件焊缝附近25~50mm的范围内打磨除去钣金件表面氧化膜后用丙酮或乙醇清洗钣金件表面油污,其中钣金件均为1mm厚的5系铝合金;f、装配组对:利用夹紧工装将焊缝两侧的钣金件压紧,保证钣金件之间焊缝间隙≤0.2mm;g、焊接:根据实际钣金件之间的匹配性编辑激光自熔焊的轨迹程序,轨迹程序编程过程中需要考虑夹紧工装的状态,防止出现撞枪,同时依据钣金件的装配状态进行机器人姿态调整,采用激光自熔焊焊接工艺自动焊接钣金件压紧之间焊缝,焊接速度为30~70mm/min,激光功率为1500~2200w,风刀为0.4~0.6mpa;h、焊后清理及检验:钣金件焊接完成后,对焊道周围进行擦灰清理,按钣金件的焊缝质量要求进行检验。进一步,步骤a和步骤e打磨所使用的打磨工具均为钢丝碗刷。进一步,步骤b和步骤f夹紧工装均为液压式压臂。进一步,步骤b和步骤f夹紧工装均匀相错排列。进一步,步骤b型材件与钣金件采用搭接方式,型材件和钣金件不开坡口,型材件与钣金件装配无间隙,型材件与钣金件对接焊道要求无变形现象。进一步,步骤f钣金件采用叠焊方式,钣金件不开坡口,钣金件之间装配无间隙,钣金件对接焊道要求无变形现象。进一步,步骤c和步骤g中激光自熔焊焊接工艺包括以下步骤:a、提前30min进行预热,检查激光器系统的工作状态,开启激光器;b、采用一块4mm的铝合金板材,进行寻点机构建立,在铝合金板材上连续打一排点,当出现焊点出现先减小后增大(或相反)时,中间最小点即为合适的焦点位置,将引导光路与该激光光斑重合后固定引导光路,便于调试;c、建立操作面板上的焊接模板,并采用1mm试板(叠焊、搭接),根据不同接头形式来设计不同的激光焊接波形以及起收弧参数;d、将步骤c中不同接头形式进行焊接工艺验证,首先进行轨迹编程,由于激光焊焊接过程中出现小孔,所以对起收弧处各增加一个点,使激光起弧参数逐渐从30%上升至100%,收弧参数从焊接功率的100%逐渐下降到50%,保证焊接质量。进一步,步骤c和步骤g自动焊接的环境温度≥10℃,湿度≤60%,风速小于2m/s,激光器采用通快激光器,激光器的镜片保护气为压缩空气。本发明的有益效果在于:1、本发明所公开的不加保护气的铝合金激光自熔焊接工艺,通过分析不同系列(5系与6系)不同板厚铝合金以及轻量化汽车的焊接特点,根据实际型材件与钣金件的匹配性以及实际钣金件之间的匹配性进行激光自熔焊轨迹程序的编辑,焊接机器人系统通过编程能够自动进行激光自熔焊焊接,保证了焊接工艺与零件状态的匹配性,克服了铝合金异种板厚异种型号在焊接过程中出现的厚板不熔,薄板易咬边等问题。2、本发明所公开的不加保护气的铝合金激光自熔焊接工艺,为保证轻量化汽车焊接过程中焊缝的稳定性,使用焊接机器人系统进行焊接,代替了手工焊接,焊缝美观,焊接缺陷较少,保证了焊缝质量和钣金件小变形量,无需矫形,飞溅小,同时减少了焊接与返工工作量,大大增加了轻量化汽车的合格率,提高了铝合金车身的生产效率。3、本发明所公开的不加保护气的铝合金激光自熔焊接工艺,整个轻量化汽车型材件和钣金件焊接过程中不需要增加保护气,也不需要添加焊丝,同时通过焊接程序的设置能够保证整个焊接过程参数自动切换,实现了自动化焊接,降低了焊接成本,同时提高了生产效率;还能够减小铝合金板焊接过程中的焊接变形、减少焊接缺陷的产生;增大焊道深宽比,保证异种型材焊接质量的一致性。附图说明为了使本发明的目的、技术方案和有益效果更加清楚,本发明提供如下附图进行说明:图1为本发明不加保护气的铝合金激光自熔焊接工艺的流程图;图2为本发明不加保护气的铝合金激光自熔焊接工艺中搭接方式的结构示意图;图3为本发明不加保护气的铝合金激光自熔焊接工艺中叠焊方式的结构示意图。具体实施方式下面将对本发明的优选实施例进行详细的描述。实施例1如图1所示的一种不加保护气的铝合金激光自熔焊接工艺,主要包括型材件与钣金件焊接和钣金件与钣金件焊接,其中型材件与钣金件焊接的焊接工艺为:a、焊前准备:将待焊接型材件与钣金件焊缝附近50mm的范围内用钢丝碗刷打磨除去型材件与钣金件表面氧化膜后用丙酮或乙醇清洗型材件与钣金件表面油污,其中型材件为2mm厚的6系铝合金,钣金件为1mm厚的5系铝合金;b、装配组对:利用夹紧工装将焊缝两侧的型材件与钣金件压紧,保证型材件与钣金件焊缝间隙为0.2mm,型材件与钣金件采用如图2所示的搭接方式,型材件和钣金件不开坡口,型材件与钣金件装配无间隙,型材件与钣金件对接焊道要求无变形现象,其中夹紧工装为液压式压臂,夹紧工装均匀相错排列,型材件与钣金件压紧后检查型材件、钣金件与夹紧工装的匹配性,如焊接间隙,错位等现象是否存在;c、焊接:根据实际型材件与钣金件的匹配性编辑激光自熔焊的轨迹程序,轨迹程序编程过程中需要考虑夹紧工装的状态,防止出现撞枪,同时依据型材件与钣金件的装配状态进行机器人姿态调整,采用激光自熔焊焊接工艺自动焊接型材件与钣金件压紧之间焊缝,焊接速度为30mm/min,激光功率为2200w,风刀为0.6mpa,自动焊接的环境温度为10℃,湿度为60%,风速为1.5m/s,激光器采用通快激光器,激光器的镜片保护气为压缩空气,其中激光自熔焊焊接工艺包括以下步骤:a、提前30min进行预热,检查激光器系统的工作状态,开启激光器;b、采用一块4mm的铝合金板材,进行寻点机构建立,在铝合金板材上连续打一排点,当出现焊点出现先减小后增大(或相反)时,中间最小点即为合适的焦点位置,将引导光路与该激光光斑重合后固定引导光路,便于调试;c、建立操作面板上的焊接模板,并采用1mm试板(叠焊、搭接),根据不同接头形式来设计不同的激光焊接波形以及起收弧参数;d、将步骤c中不同接头形式进行焊接工艺验证,首先进行轨迹编程,由于激光焊焊接过程中出现小孔,所以对起收弧处各增加一个点,使激光起弧参数逐渐从30%上升至100%,收弧参数从焊接功率的100%逐渐下降到50%,保证焊接质量,激光初始化后建立焊接工艺并进行焊参数调整,形成焊接程序,依据不同焊接位置,焊接姿态以及工件的焊接状态匹配焊接参数。d、焊后清理及检验:焊接完成后,对焊缝表面进行擦灰清理,按照型材件与钣金件焊缝质量要求进行检验;钣金件与钣金件焊接的焊接工艺为:e、焊前准备:将待焊接钣金件焊缝附近25mm的范围内用钢丝碗刷打磨除去钣金件表面氧化膜后用丙酮或乙醇清洗钣金件表面油污,其中钣金件均为1mm厚的5系铝合金;f、装配组对:利用夹紧工装将焊缝两侧的钣金件压紧,保证钣金件之间焊缝间隙为0.2mm,钣金件采用如图3所示的叠焊方式,钣金件不开坡口,钣金件之间装配无间隙,钣金件对接焊道要求无变形现象,其中夹紧工装为液压式压臂,夹紧工装均匀相错排列,钣金件压紧后检查钣金件与夹紧工装的匹配性,如焊接间隙,错位等现象是否存在;g、焊接:根据实际钣金件之间的匹配性编辑激光自熔焊的轨迹程序,轨迹程序编程过程中需要考虑夹紧工装的状态,防止出现撞枪,同时依据钣金件的装配状态进行机器人姿态调整,采用激光自熔焊焊接工艺自动焊接钣金件压紧之间焊缝,焊接速度为30mm/min,激光功率为2200w,风刀为0.6mpa,自动焊接的环境温度为10℃,湿度为60%,风速为1.5m/s,激光器采用通快激光器,激光器的镜片保护气为压缩空气,其中激光自熔焊焊接工艺包括以下步骤:a、提前30min进行预热,检查激光器系统的工作状态,开启激光器;b、采用一块4mm的铝合金板材,进行寻点机构建立,在铝合金板材上连续打一排点,当出现焊点出现先减小后增大(或相反)时,中间最小点即为合适的焦点位置,将引导光路与该激光光斑重合后固定引导光路,便于调试;c、建立操作面板上的焊接模板,并采用1mm试板(叠焊、搭接),根据不同接头形式来设计不同的激光焊接波形以及起收弧参数;d、将步骤c中不同接头形式进行焊接工艺验证,首先进行轨迹编程,由于激光焊焊接过程中出现小孔,所以对起收弧处各增加一个点,使激光起弧参数逐渐从30%上升至100%,收弧参数从焊接功率的100%逐渐下降到50%,保证焊接质量,激光初始化后建立焊接工艺并进行焊参数调整,形成焊接程序,依据不同焊接位置,焊接姿态以及工件的焊接状态匹配焊接参数。h、焊后清理及检验:钣金件焊接完成后,对焊道周围进行擦灰清理,按钣金件的焊缝质量要求进行检验。实施例2如图1所示的一种不加保护气的铝合金激光自熔焊接工艺,主要包括型材件与钣金件焊接和钣金件与钣金件焊接,其中型材件与钣金件焊接的焊接工艺为:a、焊前准备:将待焊接型材件与钣金件焊缝附近25mm的范围内用钢丝碗刷打磨除去型材件与钣金件表面氧化膜后用丙酮或乙醇清洗型材件与钣金件表面油污,其中型材件为2mm厚的6系铝合金,钣金件为1mm厚的5系铝合金;b、装配组对:利用夹紧工装将焊缝两侧的型材件与钣金件压紧,保证型材件与钣金件焊缝间隙为0.1mm,型材件与钣金件采用如图2所示的搭接方式,型材件和钣金件不开坡口,型材件与钣金件装配无间隙,型材件与钣金件对接焊道要求无变形现象,其中夹紧工装为液压式压臂,夹紧工装均匀相错排列,型材件与钣金件压紧后检查型材件、钣金件与夹紧工装的匹配性,如焊接间隙,错位等现象是否存在;c、焊接:根据实际型材件与钣金件的匹配性编辑激光自熔焊的轨迹程序,轨迹程序编程过程中需要考虑夹紧工装的状态,防止出现撞枪,同时依据型材件与钣金件的装配状态进行机器人姿态调整,采用激光自熔焊焊接工艺自动焊接型材件与钣金件压紧之间焊缝,焊接速度为70mm/min,激光功率为1500w,风刀为0.4mpa,自动焊接的环境温度为10℃,湿度为50%,风速为1m/s,激光器采用通快激光器,激光器的镜片保护气为压缩空气,其中激光自熔焊焊接工艺包括以下步骤:a、提前30min进行预热,检查激光器系统的工作状态,开启激光器;b、采用一块4mm的铝合金板材,进行寻点机构建立,在铝合金板材上连续打一排点,当出现焊点出现先减小后增大(或相反)时,中间最小点即为合适的焦点位置,将引导光路与该激光光斑重合后固定引导光路,便于调试;c、建立操作面板上的焊接模板,并采用1mm试板(叠焊、搭接),根据不同接头形式来设计不同的激光焊接波形以及起收弧参数;d、将步骤c中不同接头形式进行焊接工艺验证,首先进行轨迹编程,由于激光焊焊接过程中出现小孔,所以对起收弧处各增加一个点,使激光起弧参数逐渐从30%上升至100%,收弧参数从焊接功率的100%逐渐下降到50%,保证焊接质量,激光初始化后建立焊接工艺并进行焊参数调整,形成焊接程序,依据不同焊接位置,焊接姿态以及工件的焊接状态匹配焊接参数。d、焊后清理及检验:焊接完成后,对焊缝表面进行擦灰清理,按照型材件与钣金件焊缝质量要求进行检验;钣金件与钣金件焊接的焊接工艺为:e、焊前准备:将待焊接钣金件焊缝附近50mm的范围内用钢丝碗刷打磨除去钣金件表面氧化膜后用丙酮或乙醇清洗钣金件表面油污,其中钣金件均为1mm厚的5系铝合金;f、装配组对:利用夹紧工装将焊缝两侧的钣金件压紧,保证钣金件之间焊缝间隙为0.2mm,钣金件采用如图3所示的叠焊方式,钣金件不开坡口,钣金件之间装配无间隙,钣金件对接焊道要求无变形现象,其中夹紧工装为液压式压臂,夹紧工装均匀相错排列,钣金件压紧后检查钣金件与夹紧工装的匹配性,如焊接间隙,错位等现象是否存在;g、焊接:根据实际钣金件之间的匹配性编辑激光自熔焊的轨迹程序,轨迹程序编程过程中需要考虑夹紧工装的状态,防止出现撞枪,同时依据钣金件的装配状态进行机器人姿态调整,采用激光自熔焊焊接工艺自动焊接钣金件压紧之间焊缝,焊接速度为70mm/min,激光功率为1500w,风刀为0.4mpa,自动焊接的环境温度为10℃,湿度为60%,风速为1m/s,激光器采用通快激光器,激光器的镜片保护气为压缩空气,其中激光自熔焊焊接工艺包括以下步骤:a、提前30min进行预热,检查激光器系统的工作状态,开启激光器;b、采用一块4mm的铝合金板材,进行寻点机构建立,在铝合金板材上连续打一排点,当出现焊点出现先减小后增大(或相反)时,中间最小点即为合适的焦点位置,将引导光路与该激光光斑重合后固定引导光路,便于调试;c、建立操作面板上的焊接模板,并采用1mm试板(叠焊、搭接),根据不同接头形式来设计不同的激光焊接波形以及起收弧参数;d、将步骤c中不同接头形式进行焊接工艺验证,首先进行轨迹编程,由于激光焊焊接过程中出现小孔,所以对起收弧处各增加一个点,使激光起弧参数逐渐从30%上升至100%,收弧参数从焊接功率的100%逐渐下降到50%,保证焊接质量,激光初始化后建立焊接工艺并进行焊参数调整,形成焊接程序,依据不同焊接位置,焊接姿态以及工件的焊接状态匹配焊接参数。h、焊后清理及检验:钣金件焊接完成后,对焊道周围进行擦灰清理,按钣金件的焊缝质量要求进行检验。实施例3如图1所示的一种不加保护气的铝合金激光自熔焊接工艺,主要包括型材件与钣金件焊接和钣金件与钣金件焊接,其中型材件与钣金件焊接的焊接工艺为:a、焊前准备:将待焊接型材件与钣金件焊缝附近30mm的范围内用钢丝碗刷打磨除去型材件与钣金件表面氧化膜后用丙酮或乙醇清洗型材件与钣金件表面油污,其中型材件为2mm厚的6系铝合金,钣金件为1mm厚的5系铝合金;b、装配组对:利用夹紧工装将焊缝两侧的型材件与钣金件压紧,保证型材件与钣金件焊缝间隙为0.2mm,型材件与钣金件采用如图2所示的搭接方式,型材件和钣金件不开坡口,型材件与钣金件装配无间隙,型材件与钣金件对接焊道要求无变形现象,其中夹紧工装为液压式压臂,夹紧工装均匀相错排列,型材件与钣金件压紧后检查型材件、钣金件与夹紧工装的匹配性,如焊接间隙,错位等现象是否存在;c、焊接:根据实际型材件与钣金件的匹配性编辑激光自熔焊的轨迹程序,轨迹程序编程过程中需要考虑夹紧工装的状态,防止出现撞枪,同时依据型材件与钣金件的装配状态进行机器人姿态调整,采用激光自熔焊焊接工艺自动焊接型材件与钣金件压紧之间焊缝,焊接速度为50mm/min,激光功率为1800w,风刀为0.5mpa,自动焊接的环境温度为10℃,湿度为50%,风速为1m/s,激光器采用通快激光器,激光器的镜片保护气为压缩空气,其中激光自熔焊焊接工艺包括以下步骤:a、提前30min进行预热,检查激光器系统的工作状态,开启激光器;b、采用一块4mm的铝合金板材,进行寻点机构建立,在铝合金板材上连续打一排点,当出现焊点出现先减小后增大(或相反)时,中间最小点即为合适的焦点位置,将引导光路与该激光光斑重合后固定引导光路,便于调试;c、建立操作面板上的焊接模板,并采用1mm试板(叠焊、搭接),根据不同接头形式来设计不同的激光焊接波形以及起收弧参数;d、将步骤c中不同接头形式进行焊接工艺验证,首先进行轨迹编程,由于激光焊焊接过程中出现小孔,所以对起收弧处各增加一个点,使激光起弧参数逐渐从30%上升至100%,收弧参数从焊接功率的100%逐渐下降到50%,保证焊接质量,激光初始化后建立焊接工艺并进行焊参数调整,形成焊接程序,依据不同焊接位置,焊接姿态以及工件的焊接状态匹配焊接参数。d、焊后清理及检验:焊接完成后,对焊缝表面进行擦灰清理,按照型材件与钣金件焊缝质量要求进行检验;钣金件与钣金件焊接的焊接工艺为:e、焊前准备:将待焊接钣金件焊缝附近为30mm的范围内用钢丝碗刷打磨除去钣金件表面氧化膜后用丙酮或乙醇清洗钣金件表面油污,其中钣金件均为1mm厚的5系铝合金;f、装配组对:利用夹紧工装将焊缝两侧的钣金件压紧,保证钣金件之间焊缝间隙为0.2mm,钣金件采用如图3所示的叠焊方式,钣金件不开坡口,钣金件之间装配无间隙,钣金件对接焊道要求无变形现象,其中夹紧工装为液压式压臂,夹紧工装均匀相错排列,钣金件压紧后检查钣金件与夹紧工装的匹配性,如焊接间隙,错位等现象是否存在;g、焊接:根据实际钣金件之间的匹配性编辑激光自熔焊的轨迹程序,轨迹程序编程过程中需要考虑夹紧工装的状态,防止出现撞枪,同时依据钣金件的装配状态进行机器人姿态调整,采用激光自熔焊焊接工艺自动焊接钣金件压紧之间焊缝,焊接速度为为60mm/min,激光功率为1800w,风刀为0.5mpa,自动焊接的环境温度为10℃,湿度为60%,风速为1m/s,激光器采用通快激光器,激光器的镜片保护气为压缩空气,其中激光自熔焊焊接工艺包括以下步骤:a、提前30min进行预热,检查激光器系统的工作状态,开启激光器;b、采用一块4mm的铝合金板材,进行寻点机构建立,在铝合金板材上连续打一排点,当出现焊点出现先减小后增大(或相反)时,中间最小点即为合适的焦点位置,将引导光路与该激光光斑重合后固定引导光路,便于调试;c、建立操作面板上的焊接模板,并采用1mm试板(叠焊、搭接),根据不同接头形式来设计不同的激光焊接波形以及起收弧参数;d、将步骤c中不同接头形式进行焊接工艺验证,首先进行轨迹编程,由于激光焊焊接过程中出现小孔,所以对起收弧处各增加一个点,使激光起弧参数逐渐从30%上升至100%,收弧参数从焊接功率的100%逐渐下降到50%,保证焊接质量,激光初始化后建立焊接工艺并进行焊参数调整,形成焊接程序,依据不同焊接位置,焊接姿态以及工件的焊接状态匹配焊接参数。h、焊后清理及检验:钣金件焊接完成后,对焊道周围进行擦灰清理,按钣金件的焊缝质量要求进行检验。实施例1~3所制备的铝合金轻量车身合格率和生产效率见表一:表一实施例1实施例2实施例3合格率(%)99.599.399.2生产效率(s/件)180175185通过本发明所公开的铝合金轻量车身自动化焊接工艺制备的铝合金轻量车身,合格率达到99%,高于现有技术的95%,生产效率达到180s/件,高于现有技术的210s/件。最后说明的是,以上优选实施例仅用以说明本发明的技术方案而非限制,尽管通过上述优选实施例已经对本发明进行了详细的描述,但本领域技术人员应当理解,可以在形式上和细节上对其作出各种各样的改变,而不偏离本发明权利要求书所限定的范围。当前第1页12