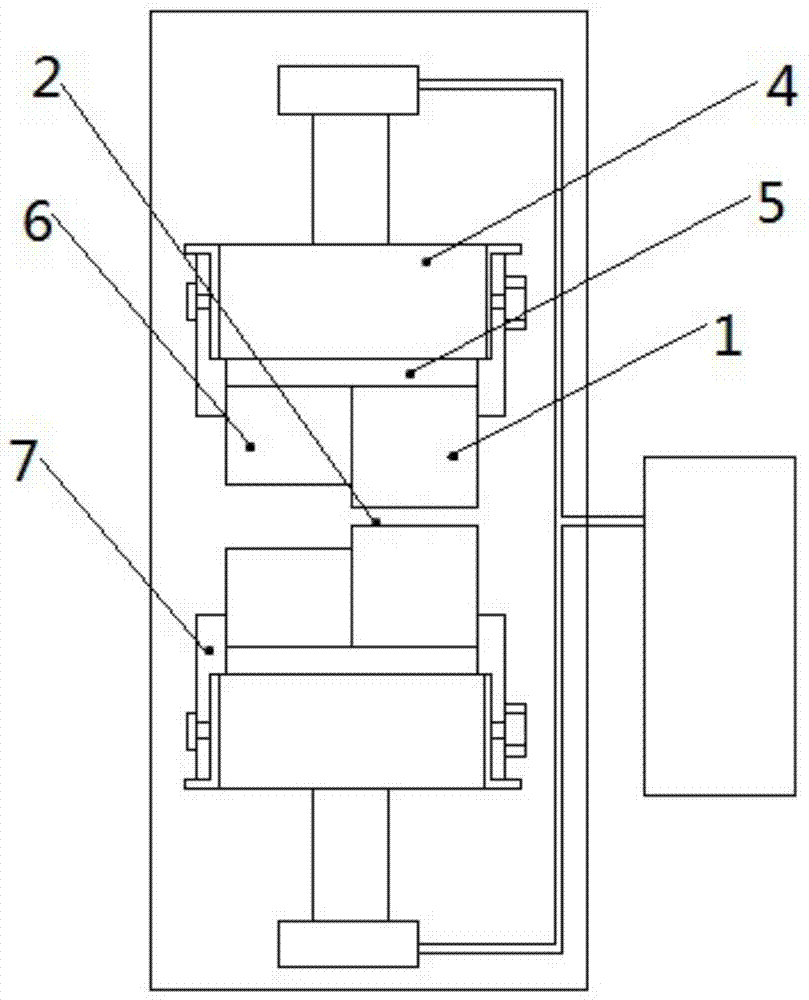
本实用新型涉及缩管机技术领域,具体涉及一种改进后的缩管机。
背景技术:
缩管机被广泛运用于管件接插、汽车油管、风管、水管、空调管等连接部位的加工成型,是理想的管端成型加工设备,加工形状包括:凸、凹节,长扁,正方,拓斜,V形,开口肘,平口肘等依产品化制造成成型模具。当压制一定形状的端头时,现有的缩管机模具通常为多个6.5cm或其他固定长度模块,形成成型腔,这样的成型方式,接触面为放入缩管机的半成品的一部分,但是往往我们需要压制的仅仅是端部的端头,比如加工带有球状端头的钨丝绳,加工目的是将球状端头压制在钨丝绳上,但是,伸入缩管机的整段钨丝绳压制时也会与缩管机模具接触,压强会由于接触面积大而减小。
技术实现要素:
鉴于现有技术的缺陷,本实用新型提供一种改进后的缩管机,其通过设置模块垫块,使得压制模块长度缩短,长度缩短后同样压力,压强更高,压制效果更佳。
为达到上述目的,本实用新型的技术方案是一种改进后的缩管机,包括压制模具、成型结构和液压控制装置,其所述成型结构包括模块底座;所述液压控制装置连接至模块底座,模块底座上设置燕尾型连接凸块,所述压制模具包括一组或多组压制模块、一组或多组模块垫块;每组压制模块形成中部成型腔,压制模块上设置燕尾型凹槽;每组模块垫块形成圆柱腔体,模块垫块上设置燕尾型凹槽,所述燕尾型连接凸块与模块垫块上设置的燕尾型凹槽相配合,燕尾型连接凸块与压制模块上燕尾型凹槽配合,一个模块底座上设置一个或多个模块垫块,一个模块底座上设置一个或多个压制模块;模块垫块与压制模块间隔设置。
基于上述的技术方案,模块底座及压制模块通过燕尾型凹凸结构进行连接,连接更加稳固,且容易更换。更换压头模具时,只要将模具往后滑动,衬套和螺母相互配合,不需移动即可将压头模具移出。该使用新型专利的用于各种金属丝或绳压头成型的缩管机,扇形压头模具便于更换,减少工人劳动强度;避免外力作用而引起的不必要变形;不用调整即可正常运行。
基于上述的技术方案,原来的缩管机压制模块是一个6.5cm长的模具,现在的通过设置模块垫块,使得压制模块长度缩短,长度缩短后同样压力,压强更高,压制效果更佳。
进一步的,所述压制模块边缘设置多个直径不等的球形缺口,每组压制模块的形成带有不同尺寸的球形结构的钨丝绳成型腔。
基于上述的技术方案,压制模块边缘设置多个直径不等的球形缺口,可用来加工不同尺寸的钨丝绳的球形端头,加工不同尺寸的产品时,可以不用更换压制模块,只需要用不同位置的球形缺口进行加工。此模具上同时制作了数个不同规格球形端头压制用的凹坑,以满足在不用更换模具的情况下进行不同规格球形端头的压制工作。加工不同尺寸的产品时,可以不用更换压制模块,只需要用不同位置的球形缺口进行加工。
进一步的,所述一个模块底座上设置两个模块垫块及一个压制模块,所述模块底座设置两侧各设置一个L型连接压板,所述L型连接压板与所述模块底座固定连接,所述L型连接压板另一端与所述压制模块接触连接。
所述一个模块底座上设置一个模块垫块及一个压制模块,所述模块底座设置两侧各设置一个L型连接压板,一侧的L型连接压板与所述模块底座固定连接, L型连接压板另一端与所述压制模块接触连接;另一侧的L型连接压板与所述模块底座固定连接,L型连接压板另一端与所述模块垫块接触连接。
所述压制结构内设置有油腔,所述液压控制装置的输出端、所述油腔和所述模块底座依次相连通。
本实用新型的的工作过程:控制控制器设置模块底座的压力,控制器并通过控制液压进出装置和模块底座使压制模块沿径向松开,选择一个合适尺寸规格的缺口,将需要压制的压头放入中空部内,将需要进行压制的半成品伸入压头,液压控制模块开始工作,控制器通过控制压力传感器和电磁阀使模块底座带动压制模块沿径向闭合,多个压制模块闭合形成与产品设计形状相同的镂空部,模块垫块不与压制件接触,压制模块闭合后并保持一定时间,经过反复的几次的操作,即可完成一个产品的压制成型。
本实用新型的有益效果:通过设置模块垫块,使得压制模块长度缩短,长度缩短后同样压力,压强更高,压制效果更佳。
附图说明
图1为本实用新型的结构示意图;
图2为压制模具的主视图;
图3为一组压制模块的结构示意图;
图4为一组模块垫块的结构示意图;
图5为实施例1的结构示意图;
图6为实施例2的结构示意图;
图7为本实用新型的液压原理图;
图8为压制成型的钨丝绳;
图中:1、压制模块,2、球形缺口,3、燕尾型凹槽,4、模块底座,5、燕尾型连接凸块,6、模块垫块,7、L型连接压板, 8、吸油滤网,9、油泵,10、压力表,11、电磁换向阀,12、液控单向阀,13、高压溢流阀,14、低压溢流阀,15、工作油缸,16、回位油缸,17、工作油缸。
具体实施方式
下面结合具体实施方式对本专利的技术方案作进一步详细地说明。
实施例1
一种改进后的缩管机,包括压制模具、成型结构和液压控制装置,其所述成型结构包括模块底座4;所述液压控制装置连接至模块底座4,模块底座4上设置燕尾型连接凸块5,所述压制模具包括一组或多组压制模块1、一组或多组模块垫块6;每组压制模块1形成中部成型腔,压制模块1上设置燕尾型凹槽3;每组模块垫块6形成圆柱腔体,模块垫块6上设置燕尾型凹槽3,所述燕尾型连接凸块5与模块垫块6上设置的燕尾型凹槽3相配合,燕尾型连接凸块5与压制模块1上燕尾型凹槽3配合,一个模块底座4上设置一个或多个模块垫块6,一个模块底座4上设置一个或多个压制模块1;模块垫块6与压制模块1间隔设置。
所述一个模块底座4上设置一个模块垫块6及一个压制模块1,所述模块底座4设置两侧各设置一个L型连接压板,一侧的L型连接压板与所述模块底座固定连接, L型连接压板另一端与所述压制模块1接触连接;另一侧的L型连接压板7与所述模块底座固定连接,L型连接压板7另一端与所述模块垫块6接触连接。
实施例2
一种改进后的缩管机,包括压制模具、成型结构和液压控制装置,所述压制模具包括两组(每组六个)压制模块1,压制模块1边缘设置多个直径不等的球形缺口2,每组(六个)压制模块1的形成带有不同尺寸的球形结构的钨丝绳成型腔,压制模块上设置燕尾型凹槽3;所述成型结构包括模块底座4;所述液压控制装置连接至六个模块底座4,每个模块底座4上设置燕尾型连接凸块5,燕尾型连接凸块5与压制模块1上燕尾型凹槽3配合,一个模块底座4上设置两个压制模块1。所述缩管机还包括一组模块垫块6,每组(六个)模块垫块6形成圆柱腔体,模块垫块6上设置燕尾型凹槽3,所述燕尾型连接凸块5与模块垫块6上设置的燕尾型凹槽3相配合,模块垫块6与压制模块1间隔设置,一个模块底座上设置一个模块垫块6。
所述模块底座4设置两侧各设置一个L型连接压板7,一侧的L型连接压板7与所述模块底座4固定连接,L型连接压板7另一端与所述压制模块1接触连接;另一侧的L型连接压板7与所述模块底座4固定连接,L型连接压板7另一端与所述模块垫块6接触连接。
基于上述的技术方案,压制模块1边缘设置多个直径不等的球形缺口,可用来加工不同尺寸的钨丝绳的球形端头,加工不同尺寸的产品时,可以不用更换压制模块1,只需要用不同位置的球形缺口进行加工。
基于上述的技术方案,模块底座4及压制模块1通过燕尾型凹凸结构进行连接,连接更加稳固,且容易更换。
实施例3
一种改进后的缩管机,包括压制模具、成型结构和液压控制装置,所述压制模具包括一组(六个)压制模块1,压制模块1边缘设置多个直径不等的球形缺口2,每组(六个)压制模块1的形成带有不同尺寸的球形结构的钨丝绳成型腔,压制模块上设置燕尾型凹槽3;所述成型结构包括模块底座4;所述液压控制装置连接至六个模块底座4,每个模块底座4上设置燕尾型连接凸块5,燕尾型连接凸块5与压制模块1上燕尾型凹槽3配合,一个模块底座4上设置两个压制模块1。所述缩管机还包括两组模块垫块6,每组(六个)模块垫块6形成圆柱腔体,模块垫块6上设置燕尾型凹槽3,所述燕尾型连接凸块5与模块垫块6上设置的燕尾型凹槽3相配合,模块垫块6与压制模块1间隔设置,一个模块底座4上设置两个模块垫块6。
所述模块底座4设置两侧各设置一个L型连接压板7,所述L型连接压板7与所述模块底座4固定连接,L型连接压板7另一端与所述模块垫块6接触连接。
工作过程:控制控制器设置模块底座的压力,控制器并通过控制液压进出装置和模块底座使压制模块沿径向松开,选择一个合适尺寸规格的球形缺口,将需要压制的钨丝绳球状压头放入中空部内,将钨丝绳伸入球状压头内,液压控制模块开始工作,控制器通过控制压力传感器和电磁阀使模块底座带动压制模块沿径向闭合,多个压制模块闭合形成与钨丝绳球形端头设计形状相同的镂空部,压制模块闭合后并保持一定时间,经过反复的几次的操作,即可完成一个钨丝绳球形端头的压制成型。
实施例4
一种改进后的缩管机,包括压制模具、成型结构和液压控制装置,其所述成型结构包括模块底座4;所述液压控制装置连接至模块底座4,模块底座4上设置燕尾型连接凸块5,所述压制模具包括一组或多组压制模块1、一组或多组模块垫块6;每组压制模块1形成中部成型腔,压制模块1上设置燕尾型凹槽3;每组模块垫块6形成圆柱腔体,模块垫块6上设置燕尾型凹槽3,所述燕尾型连接凸块5与模块垫块6上设置的燕尾型凹槽3相配合,燕尾型连接凸块5与压制模块1上燕尾型凹槽3配合,一个模块底座4上设置一个或多个模块垫块6,一个模块底座4上设置一个或多个压制模块1;模块垫块6与压制模块1间隔设置。
上面对本专利的较佳实施方式作了详细说明,但是本专利并不限于上述实施方式,在本领域的普通技术人员所具备的知识范围内,还可以在不脱离本专利宗旨的前提下作出各种变化。