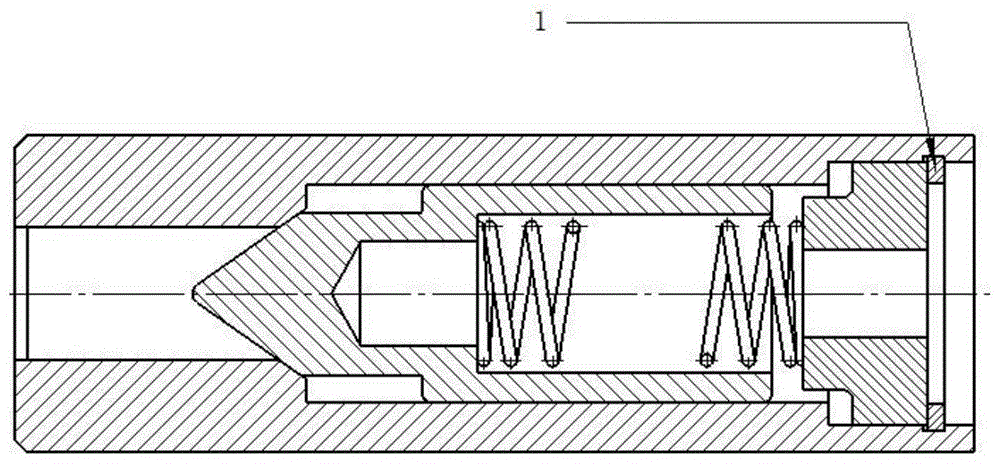
本发明涉及机械加工领域,具体为一种开口挡圈及其加工方法。
背景技术:
作为航空发动机燃油喷嘴的主要部件之一,活门用于控制燃油的定时定量供给。通过燃油压力与弹簧弹力的变化可控制活门的开启与关闭,因而需要采用开口挡圈固定弹簧及其安装座,如图1所示。
开口挡圈结构如图2所示,所用材料为弹簧钢,开口挡圈的最大外圆呈圆形结构,用于配合活门壳体内槽;开口挡圈的内孔由多段圆弧组成,开口挡圈的厚度为0.6mm左右,下端加工有开口及两个小孔。从开口挡圈的结构以及功能来看,外圆及两侧端面精密加工后有助于提升喷嘴稳定性,但受限于其厚度较薄以及开口等特点,该类开口挡圈在以冲压的方式粗加工成型后不易进行精密加工或进行返修。
技术实现要素:
针对现有技术中存在的问题,本发明提供一种开口挡圈及其加工方法,能提升开口挡圈的加工效率、表面粗糙度和平行度,针对现场活门装配过程中遇到的尺寸超差挡圈可实现快速和准确的返修。
本发明是通过以下技术方案来实现:
一种开口挡圈的加工方法,包括如下步骤,
步骤1,通过线切割或激光切割得到粗加工的开口挡圈,使其厚度和外圆直径均大于标准尺寸;
步骤2,磨削外圆;
将至少一个粗加工的开口挡圈套设在同一个芯棒后固定,再将芯棒固定后按照标准尺寸磨削粗加工的开口挡圈,完成后得到至少一个精加工的开口挡圈;
步骤3,磨削端面;
在两块板材边缘上分别加工至少一个豁口,两块板材上的豁口相对夹紧将精加工的开口挡圈固定,其中两块板材的厚度相同且小于粗加工的开口挡圈厚度;
在两块板材的固定下,磨削开口挡圈的一个端面,完成后对开口挡圈的另一个端面重复该过程,得到加工完成的开口挡圈。
优选的,步骤1中线切割或激光切割时所用板材厚度大于待加工开口挡圈厚度,得到粗加工的开口挡圈。
进一步,连续线切割或激光切割大于待加工开口挡圈厚度的板材得到若干个粗加工的开口挡圈。
再进一步,板材的厚度比标准尺寸大0.2-0.4mm,粗加工的开口挡圈外圆直径比标准尺寸大0.5-2mm。
优选的,步骤2中所述的芯棒通过加工得到,加工的芯棒一侧最大外圆直径大于粗加工的开口挡圈内孔直径,另一侧最大外圆直径不大于粗加工的开口挡圈内孔直径。
进一步,在芯棒最大外圆直径不大于粗加工的开口挡圈内孔直径一侧的最外侧加工螺纹,使粗加工的开口挡圈穿入芯棒后用螺母固定时螺母的高度不超过开口挡圈,再将至少一个粗加工的开口挡圈用螺母固定。
优选的,步骤3中两块板材的豁口均为相同直径的半圆状圆弧且直径均小于精加工的挡圈外圆。
进一步,两块板材上的半圆状圆弧豁口将至少一个精加工的开口挡圈相对夹紧,吸附于工作台上固定。
进一步,所述的板材为钢板或磁性合金板。
一种由上述任意一项所述的方法加工得到的开口挡圈。
与现有技术相比,本发明具有以下有益的技术效果:
本发明一种开口挡圈的加工方法,线切割或激光切割可以得到粗加工的开口挡圈,将至少一个粗加工的开口挡圈固定在同一个芯棒上固定可精确磨削粗加工的开口挡圈外圆,在两块板材上加工至少一个豁口可以将精加工的开口挡圈固定,从而分别磨削精加工的开口挡圈上端面和下端面,得到精加工完成后的开口挡圈,能提升开口挡圈的平面度、平行度和表面质量,有利于加工后的开口挡圈在装配时与配合零件尺寸不相符时进行返修。
进一步的,板材的豁口均为相同直径的半圆状圆弧且直径均小于精加工的挡圈外圆,不仅能将开口挡圈固定在较多的圆弧区域,便于磨削端面,而且便于加工,提高了效率。
附图说明
图1为开口挡圈的安装示意图。
图2为本发明开口挡圈的结构示意图。
图3为本发明粗切开口挡圈的外形示意图。
图4为本发明开口挡圈外圆磨削的芯棒示意图。
图5为图4的a-a剖面图。
图6为本发明开口挡圈端面磨削的示意图。
其中:1-开口挡圈。
具体实施方式
下面结合具体的实施例对本发明做进一步的详细说明,所述是对本发明的解释而不是限定。
本发明提供一种喷嘴活门开口挡圈及其加工方法,加工方法可以提升开口挡圈的加工效率、表面粗糙度和平行度,有利于加工后的开口挡圈在装配时与配合零件尺寸不相符时进行返修。
本发明的技术方案分为三步:
第一步,粗加工外形,
首先选用厚度大于待加工零件的板材,板材的厚度大于待加工零件0.2-0.4mm,将其固定后,使用激光切割或者电火花线切割进行连续多个开口挡圈的外形粗切割,如图3所示。加工后的零件外圆直径大于图纸要求的尺寸,具体的数值为0.5-2mm,这是需要给零件最大外圆保留加工余量用于精密加工,然后加工出下端两小孔。
第二步,磨削外圆,
首先,按照开口挡圈的内孔尺寸,采用电火花线切割或者激光切割的方式在棒料上粗加工芯棒,加工后的芯棒最大外圆直径比开口挡圈的内孔直径大0.2-0.5mm;
其次,将芯棒装夹于数控车床后,车削芯棒外圆一侧,使其外圆尺寸与开口挡圈的内孔配合,而后在最外侧加工螺纹,使螺纹在配合螺母后螺母的高度不超过开口挡圈,并在两侧加工顶尖孔,芯棒加工完成后如图4和图5所示;
最后,将开口挡圈逐个穿于芯棒之上,并用螺母压紧,在外圆磨床上使用双顶尖固定后进行磨外圆加工,磨削开口挡圈外圆。
第三步,磨削端面,
在小于开口挡圈厚度的两块磁性材料的板材上分别加工出小于开口挡圈外圆的两个相同直径的半圆豁口,然后用这两块板材依次固定压紧开口挡圈外圆后吸附在平面磨床工作台上,进行端面磨削加工,另一面重复该步骤,得到对应的开口挡圈,可同时加工多个开口挡圈,如图6所示,其中两块板材的厚度相同,可以为钢板或磁性合金板,两块板材的厚度比开口挡圈小0.1-0.2mm。
以某一规格的开口挡圈为例,其内孔最大外圆尺寸为φ10,外圆尺寸需要由φ12加工至φ11,厚度需要由0.8mm加工至0.6mm,通过上述方法进行加工,其具体步骤如下,
步骤1,如图3所示,选取厚度为0.8mm的弹簧钢板,沿板材进行线切割,粗加工零件外形尺寸:大外圆直径φ12,内形尺寸为φ10圆弧与r2.5、r1圆弧转接,然后加工下端两个小孔;
步骤2,如图4和图5的结构所示,然后采用线切割加工芯棒,其外形的最大外圆尺寸为φ10.5;
步骤3,将芯棒一端装夹于数控车床上,车外圆,保证外圆尺寸为φ10,长度为40,然后车螺纹m8*1.5,长度10,打顶尖孔a0.8/1.7,掉头后加工另一端顶尖孔a0.8/1.7;
步骤4,将开口挡圈逐个串于芯棒φ10外圆处,利用φ10与未加工处φ10.5之间的台阶进行定位,采用m8螺帽进行压紧,最后将芯棒利用双顶尖孔定位于外圆磨床上磨削挡圈外圆至φ11,提升表面粗糙度;
步骤5,如图6所示,在厚度为0.5mm的两块钢板上,分别加工直径为φ10.8的7组半圆豁口,将7个挡圈用钢板压紧后吸附于平台上进行端面磨加工,两侧加工后保证厚度尺寸为0.6mm,得到上述规格的开口挡圈。