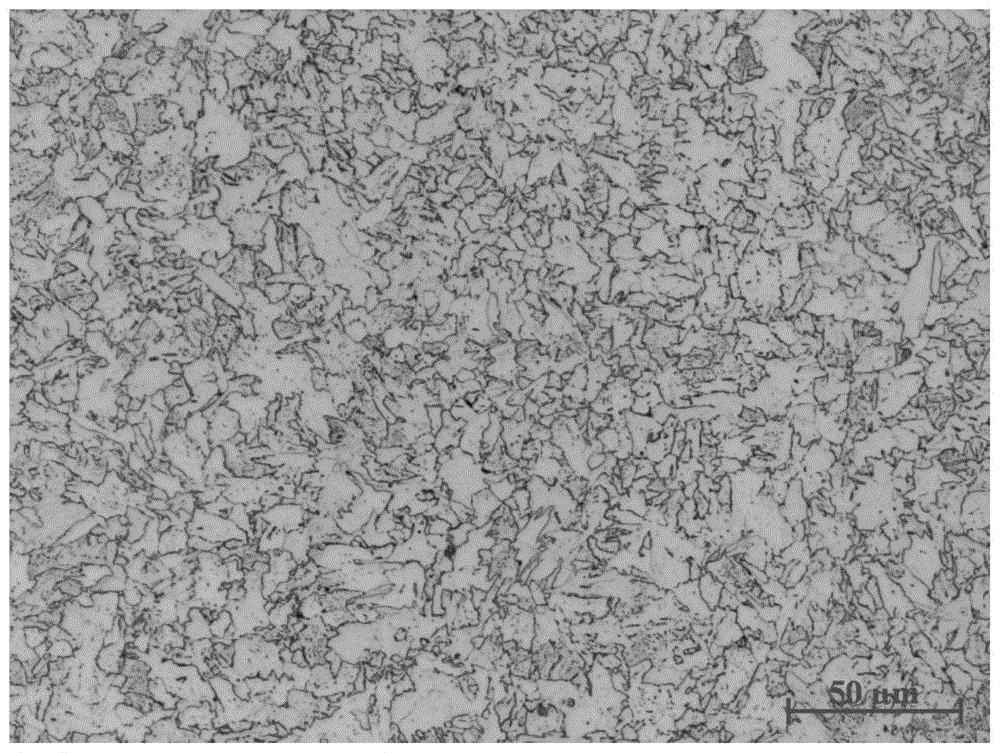
本发明涉及钢铁冶炼领域,具体地,涉及一种440mpa级薄规格热轧酸洗汽车板的生产方法。
背景技术:
:2017年,我国汽车产量2902万辆,连续9年位居全球第一。各类汽车用钢需求为7825万吨。在庞大的需求量中,目前酸洗汽车板的需求量相对较小,这是因为当前市场上酸洗汽车板的厚度规格目前主要为2~6mm,更薄规格的酸洗汽车板虽然有市场需求,但受限于传统热轧机的生产能力,薄规格酸洗汽车板的表面质量和性能通卷均匀性均难以满足汽车工业自动化生产的需要。未来酸洗板将向薄规格、高强度发展,并将逐步替代部分连退板,市场前景广阔。热轧酸洗板卷是以优质热轧板卷为原料,经开卷、酸洗、漂洗、烘干、切边和涂油等工序处理后得到的热轧酸洗板。热轧酸洗板是介于冷轧板和热轧板之间的性价比较高的一种产品。其表面质量和使用要求介于热轧板和冷轧板之间,是部分热轧板和冷轧板的理想替代产品。与冷轧板相比,常规酸洗板厚度较厚,不利于汽车减重,同时表面质量、板形质量和通卷性能的稳定性均不能满足汽车零部件连续批量稳定冲压的要求。技术实现要素:针对现有技术生产的薄规格酸洗汽车板的表面质量和性能通卷均匀性均难以满足汽车工业自动化生产需要的不足,本发明的目的在于提供一种440mpa级薄规格热轧酸洗汽车板的生产方法,该热轧酸洗汽车板采用常规热连轧机组生产,酸洗工艺在推拉式酸洗机组完成,成品厚度薄,为1.5~2.5mm,表面质量好、通卷性能稳定、尺寸精度高、板形质量好,且具有良好延伸率,可代替普冷汽车板用于制造各类汽车结构件,有利于降低汽车生产成本,市场前景广阔。为了实现上述目的,本发明提供一种440mpa级薄规格热轧酸洗汽车板的生产方法,以重量百分比计,所述热轧酸洗板含有,c:0.07~0.09、si≤0.05、mn:1.00~1.20、p≤0.020、s≤0.020、nb:0.010~0.020、als:0.030~0.050、ti:0.010~0.030,n≤0.008,余量为fe及不可避免的杂质。热轧酸洗汽车板的成品厚度为1.5~2.5mm,抗拉强度为440~500mpa,其中通卷抗拉强度波动控制在±15mpa,延伸率≥35%。1)炼钢连铸:铁水预脱硫处理→转炉炼钢→钢包lf精炼→连铸;铁水进行脱硫,脱硫后硫含量低于0.008%,转炉终点c控制在0.06~0.08%,精炼al、mn调整到位后进行nb、ti合金化,精炼结束后进行钙处理,并软搅拌10±1分钟,后连铸,结晶器液面波动控制在±2mm内,铸坯厚度220±2mm。2)热轧:铸坯加热→粗轧→精轧→层流冷却→卷取;加热炉温度1230±20℃,在炉内保温时间150~180min;铸坯出炉进行高压水除磷,除磷压力≥30mpa;进行粗轧和精轧。3)平整:目标平整延伸率1.0%,控轧平整轧制力为2000±100kn,前张力55±5kn,后张力180±10kn。4)酸洗:开卷→酸洗→漂洗→涂油→卷取。采用盐酸四级酸洗,1级酸液浓度为30~50g/l,2级酸液浓度为70~90g/l,3级酸液浓度为100~120g/l,4级酸液浓度为140~160g/l,1级酸液中fe2+浓度≤130g/l,2级酸液中fe2+浓度≤100g/l、3级酸液中fe2+浓度≤85g/l,4级酸液中fe2+浓度≤50g/l酸液温度75~85℃。酸洗时在酸液中加入缓蚀剂,缓蚀剂占酸洗溶液的重量百分比为0.05~0.10%。漂洗液温度45~55℃,酸洗和漂洗速度控制在60~100mpm。最后进行涂油分卷,得到成品。进一步,所述热轧酸洗汽车板的生产方法,热轧工序中,进行6道次粗轧和7道次精轧,每道次粗轧进行表面除磷,粗轧结束温度1020±20℃,精轧前进行高压水除磷,除磷压力≥30mpa,精轧间除磷水全开,精轧压下率93~95%,终轧温度860±15℃,卷取温度660±15℃,热卷厚度1.535~2.545mm;热卷目标厚度=酸洗目标厚度*101%+氧化皮厚度0.02mm。进一步,所述热轧酸洗汽车板的生产方法中酸洗汽车板抗拉强度为440~500mpa,通卷抗拉强度波动控制在±15mpa,延伸率≥35%。以下对本发明所含合金元素的作用及其用量的选择具体分析说明:c:0.07~0.09%在热轧酸洗汽车板中,c是重要的强化元素,通过固溶强化和析出强化作用提高钢板的强度。过低的c含量会降低钢的屈服和抗拉强度,过高的c含量会影响冲压性能,同时c含量的选择还应该尽量避开钢的包晶相变区间,降低连铸出现裂纹的风险。因此本发明的热轧酸洗汽车板将c含量控制在0.07~0.09%之间。si≤0.05在热轧酸洗汽车板中,si含量偏高时,在加热炉中会形成硅酸亚铁,增加除磷难度。但过低的si含量又提高了炼钢成本。因此本发明的热轧酸洗汽车板将si含量控制在0.05%以下,既利于炼钢成本的控制,又可通过增加除磷压力保证酸洗表面质量。mn:1.00~1.20%在热轧酸洗汽车板中,mn是提高带钢强度和韧性的有效元素,但mn含量过高会导致铸坯中心出现mns偏析。因此本发明的热轧酸洗汽车板将mn含量控制在1.00~1.20%之间。p≤0.020%在热轧酸洗汽车板中,p是有害杂质元素,易引起铸坯中心偏析,影响冷弯和成型性能。但过低的p要求将增加炼钢成本。因此本发明的热轧酸洗汽车板将p含量控制在0.020%以下。s≤0.020在热轧酸洗汽车板中,s是有害元素,易与钢中mn元素形成mns夹杂,影响带钢冷弯和成型要求。但过低的s要求将增加炼钢成本。本发明对mn的合理控制可以降低对s的控制要求。因此本发明的热轧酸洗汽车板将s含量控制在0.020%以下。nb:0.010~0.020%在热轧酸洗汽车板中,nb可以通过细晶强化和析出强化同时提高带钢的强度和韧性。但由于nb成本高,且单位nb含量的强化效果增长率随着其含量增加而降低,nb含量在0.010~0.020%时,可实现以低成本达到最佳强化效果的目的。因此本发明的热轧酸洗汽车板将nb含量控制在0.010~0.020%之间。als:0.030~0.050在热轧酸洗汽车板中,al是重要的脱氧元素,同时al可与n结合形成aln析出,细化晶粒,提高带钢强度。因此本发明的热轧酸洗汽车板将al含量控制在0.030~0.050%之间。ti:0.010~0.030在热轧酸洗汽车板中,微量ti可以提高带钢焊接性能。因此,在考虑生产成本的情况下,本发明的热轧酸洗汽车板将ti含量控制在0.010~0.030%之间。n≤0.0080在热轧酸洗汽车板中,n是有害杂质元素,但是同时n可与al结合形成aln析出,细化晶粒,提高带钢强度。因此本发明的热轧酸洗汽车板将n含量控制在0.008%以下。与现有技术相比较,本发明至少具有如下有益效果:本发明通过精确控制钢中的化学成分、热轧工艺和酸洗工艺,特别是通过添加适量的nb、ti元素,匹配特定参数的热轧、酸洗工艺,在较低生产成本的情况下得到了一种440mpa级的薄规格热轧酸洗汽车板,且本发明的热轧酸洗汽车板表面质量好、通卷性能稳定、尺寸精度高、板形质量好,具有良好延伸率,可代替普冷汽车板用于制造各类汽车结构件;本发明的热轧酸洗汽车板生产方法还具有工艺控制难度小、可操作性强、方法简单、成本低等优点,适宜工厂批量生产。同时,本发明对炼钢成分特别是p、s、n的要求易于实现,可降低全流程生产成本。附图说明图1为实施例1中热轧酸洗汽车板的金相组织;图2为实施例2中热轧酸洗汽车板的金相组织;图3为实施例3中热轧酸洗汽车板的金相组织。具体实施方式首先,对本发明的440mpa级薄规格热轧酸洗汽车板的生产方法进行详细地描述。要获得表面质量好、通卷性能稳定、尺寸精度高、板形质量好、具有良好延伸率且成本低的抗拉强度为440mpa级薄规格热轧酸洗汽车板,首先要保证全流程生产工艺的合理性,主要技术措施有:(1)炼钢成分设计充分利用c、mn、nb的组合强化效果,降低负面影响。c含量0.07~0.09%,提高强化效果,同时避开钢的包晶相变区间,降低连铸出现裂纹的风险。mn含量1.00~1.20%,充分利用其强化作用,又避免mn含量过高导致铸坯中心出现mns偏析。nb含量0.010~0.020%,将nb的强化效果发挥到最佳。(2)通过低温热轧、短时加热,多道次高压除磷来保证带钢表面质量。热轧加热炉温度1230±20℃,在炉内保温时间150~180min;铸坯出炉进行高压水除磷,除磷压力≥30mpa;进行6道次粗轧和7道次精轧,每道次粗轧前进行表面除磷,精轧前进行高压水除磷,除磷压力≥30mpa,精轧间除磷水全开。(3)精确控制热轧轧制温度,精轧变形量,保证力学性能稳定性和板形质量。粗轧结束温度1020±20℃,精轧压下率93~95%,终轧温度860±15℃,卷取温度660±15℃,热卷厚度1.535~2.545mm。热卷目标厚度=酸洗目标厚度*101%+氧化皮厚度0.020mm。热卷厚度设定时考虑了平整延伸率和氧化铁皮对成品厚度的影响。(4)最优化平整工艺,既保证板形质量,又保证力学性能稳定性。控轧平整轧制力为2000±100kn,前张力55±5kn,后张力180±10kn。具体地,本发明的440mpa级薄规格热轧酸洗汽车板的生产方法具体包括如下步骤:首先,制备具有一定化学成分的钢坯。其中,以重量百分比计,钢坯含有,c:0.07~0.09、si≤0.05、mn:1.00~1.20、p≤0.020、s≤0.020、nb:0.010~0.020、als:0.030~0.050、ti:0.010~0.030,n≤0.008,余量为fe及不可避免的杂质。制备过程包括:铁水预脱硫处理→转炉炼钢→钢包lf精炼→连铸。铁水要求进行脱硫,脱硫后硫含量低于0.008%,转炉终点c控制在0.06~0.08%,精炼al、mn调整到位后进行nb、ti合金化,精炼结束后进行钙处理,并软搅拌10±1分钟,后连铸,结晶器液面波动控制在±2mm内,铸坯厚度220±2mm。之后,将钢坯加热至1230±20℃,在炉内保温时间150~180min;铸坯出炉进行高压水除磷,除磷压力≥30mpa;然后进行6道次粗轧和7道次精轧,每道次粗轧前进行表面除磷,粗轧结束温度1020±20℃,精轧前进行高压水除磷,除磷压力≥30mpa,精轧间除磷水全开,精轧压下率93~95%,终轧温度860±15℃,卷取温度660±15℃,热卷厚度1.535~2.545mm。热卷目标厚度=酸洗目标厚度*101%+氧化皮厚度0.020mm。再将热卷进行平整,保证目标平整延伸率1%稳定前提下,进一步提升板型质量。控轧平整轧制力为2000±100kn,前张力55±5kn,后张力180±10kn。然后将带钢进行四级酸洗,酸洗液采用盐酸,1级酸液浓度为30~50g/l,2级酸液浓度为70~90g/l,3级酸液浓度为100~120g/l,4级酸液浓度为140~160g/l,1级酸液中fe2+浓度≤130g/l,2级酸液中fe2+浓度≤100g/l、3级酸液中fe2+浓度≤85g/l,4级酸液中fe2+浓度≤50g/l,酸液温度75~85℃。酸洗时在酸液中加入缓蚀剂,缓蚀剂占酸洗溶液的重量百分比为0.05~0.10%。漂洗水温度45~55℃,酸洗和漂洗速度控制在60~100mpm。最后进行涂油分卷,得到成品,成品厚度1.5~2.5mm。通过上述生产方法制得的本发明的440mpa级薄规格热轧酸洗汽车板含有以重量百分比计的c:0.07~0.09、si≤0.05、mn:1.00~1.20、p≤0.020、s≤0.020、nb:0.010~0.020、als:0.030~0.050、ti:0.010~0.030,n≤0.008,余量为fe及不可避免的杂质。本发明的热轧酸洗汽车板成品厚度为1.5~2.5mm,厚度波动±0.08mm。并且,根据试验结果,本发明的热轧酸洗汽车板的抗拉强度可达440~520mpa,其中通卷抗拉强度波动控制在±15mpa,延伸率≥35%。下面通过具体实施例对本发明的440mpa级薄规格热轧酸洗汽车板的生产方法进行说明。其中,本发明实施例中的屈服强度、抗拉强度、延伸率的测定方法都是按照国家标准进行测定的。实施例11)按重量百分比计,钢坯的化学成分为:c:0.078、si:0.02、mn:1.12、p:0.015、s:0.009、nb:0.014、als:0.037、ti:0.021,n:0.006,余量为fe及不可避免的杂质。其生产过程为:铁水预脱硫处理→转炉炼钢→钢包lf精炼→连铸;铁水进行脱硫,脱硫后硫含量低于0.008%,转炉终点c控制在0.06~0.08%,精炼过程中al、mn调整到位后进行nb、ti合金化,精炼结束后进行钙处理,并软搅拌10min,后连铸,结晶器液面波动控制在±2mm内,铸坯厚度220±2mm;铸坯加热→6道次粗轧→7道次精轧→层流冷却→卷取→平整→酸洗→涂油→成品。钢坯经1220℃加热163分钟后,进行高压水除磷,除磷压力325bar,经两个可逆式粗轧机6道次粗轧成28mm厚的中间坯,每道次粗轧前进行表面除磷,粗轧结束温度1028℃;再经热卷箱保温后进行7道次精轧,轧制成目标为1.535mm厚的钢卷,精轧前进行高压水除磷,除磷压力325bar,精轧间除磷水全开,精轧压下率94.6%,终轧温度872℃。钢卷经层流冷却后进入卷取机卷取,卷取温度为670℃。平整平整轧制力为2000±100kn,前张力55±5kn,后张力180±10kn。最后涂油分卷,得到规格为1.5mm厚的汽车结构用热轧酸洗板。经测定,本实施例所生产的汽车结构用热轧酸洗板的厚度和性能如表1所示:表1实施例1中汽车结构用热轧酸洗板的厚度和性能项目头部头部100米头部200米中间尾部200米尾部100米尾部厚度/mm1.5041.4761.4651.4781.4761.4851.502屈服强度/mpa415412405408396391409抗拉强度/mpa472465477468472461482延伸率/%36.937.838.238.138.637.537.3从表1中可以看出,在实施例1中通过精确控制热轧轧制温度,精轧变形量,以及最优化平整工艺,获得了预期的有益效果。钢卷通卷表面质量好,钢卷通卷的厚度和力学性能稳定,厚度1.465~1.504mm,屈服强度391~415mpa,抗拉强度461~482mpa,延伸率36.9%~38.6%,可以满足汽车工业自动化生产需要。附图1为钢卷金相组织,主要为针状铁素体组织。实施例21)按重量百分比计,钢坯的化学成分为:c:0.082、si:0.04、mn:1.16、p:0.016、s:0.012、nb:0.014、als:0.041、ti:0.015,n:0.003,余量为fe及不可避免的杂质。其生产过程为:铁水预脱硫处理→转炉炼钢→钢包lf精炼→连铸;铁水进行脱硫,脱硫后硫含量低于0.008%,转炉终点c控制在0.06~0.08%,精炼过程中al、mn调整到位后进行nb、ti合金化,精炼结束后进行钙处理,并软搅拌10min,后连铸,结晶器液面波动控制在±2mm内,铸坯厚度220±2mm;铸坯加热→6道次粗轧→7道次精轧→层流冷却→卷取→平整→酸洗→涂油→成品。钢坯经1220℃加热158分钟后,进行高压水除磷,除磷压力325bar,经两个可逆式粗轧机6道次粗轧成35mm厚的中间坯,每道次粗轧前进行表面除磷,粗轧结束温度1031℃;再经热卷箱保温后进行7道次精轧,轧制成目标为2.04mm厚的钢卷,精轧前进行高压水除磷,除磷压力325bar,精轧间除磷水全开,精轧压下率94.3%,终轧温度855℃。钢卷经层流冷却后进入卷取机卷取,卷取温度为662℃。平整平整轧制力为2000±100kn,前张力55±5kn,后张力180±10kn。最后涂油分卷,得到规格为2.0mm厚的汽车结构用热轧酸洗板。经测定,本实施例所生产的汽车结构用热轧酸洗板的厚度和性能如下:表2实施例2中汽车结构用热轧酸洗板的厚度和性能项目头部头部100米头部200米中间尾部200米尾部100米尾部厚度/mm2.0051.9551.9681.9821.9961.9742.022屈服强度/mpa415402390398410387408抗拉强度/mpa480478465472462459473延伸率/%38.038.638.240.539.338.737.9从表2中可以看出,在实施例2中通过精确控制热轧轧制温度,精轧变形量,以及最优化平整工艺,获得了预期的有益效果。钢卷通卷表面质量好,钢卷通卷的厚度和力学性能稳定,厚度1.955~2.022mm,屈服强度387~415mpa,抗拉强度459~480mpa,延伸率37.9%~40.5%,可以满足汽车工业自动化生产需要。附图2为钢卷金相组织,主要为针状铁素体组织。实施例31)按重量百分比计,钢坯的化学成分为:c:0.074、si:0.04、mn:1.05、p:0.010、s:0.011、nb:0.017、als:0.042、ti:0.025,n:0.005,余量为fe及不可避免的杂质。其生产过程为:铁水预脱硫处理→转炉炼钢→钢包lf精炼→连铸;铁水进行脱硫,脱硫后硫含量低于0.008%,转炉终点c控制在0.06~0.08%,精炼过程中al、mn调整到位后进行nb、ti合金化,精炼结束后进行钙处理,并软搅拌10min,后连铸,结晶器液面波动控制在±2mm内,铸坯厚度220±2mm;铸坯加热→6道次粗轧→7道次精轧→层流冷却→卷取→平整→酸洗→涂油→成品。钢坯经1220℃加热170分钟后,进行高压水除磷,除磷压力325bar,经两个可逆式粗轧机6道次粗轧成38mm厚的中间坯,每道次粗轧前进行表面除磷,粗轧结束温度1031℃;再经热卷箱保温后进行7道次精轧,轧制成目标为2.545mm厚的钢卷,精轧前进行高压水除磷,除磷压力325bar,精轧间除磷水全开,精轧压下率93.4%,终轧温度857℃。钢卷经层流冷却后进入卷取机卷取,卷取温度为663℃。平整平整轧制力为2000±100kn,前张力55±5kn,后张力180±10kn。最后涂油分卷,得到规格为2.5mm厚的汽车结构用热轧酸洗板。经测定,本实施例所生产的汽车结构用热轧酸洗板的厚度和性能如下:表3实施例3中汽车结构用热轧酸洗板的厚度和性能项目头部头部100米头部200米中间尾部200米尾部100米尾部厚度/mm2.5432.5022.4842.4742.4892.5082.536屈服强度/mpa402405389380392392395抗拉强度/mpa468460459453478467475延伸率/%38.939.537.638.538.938.238.2从表3中可以看出,在实施例3中通过精确控制热轧轧制温度,精轧变形量,以及最优化平整工艺,获得了预期的有益效果。钢卷通卷表面质量好,钢卷通卷的厚度和力学性能稳定,厚度2.474~2.543mm,屈服强度380~405mpa,抗拉强度453~478mpa,延伸率37.6%~39.5%,可以满足汽车工业自动化生产需要。附图3为钢卷金相组织,主要为针状铁素体组织。显然,上述实施例仅仅是为清楚地说明所作的举例,而并非对实施方式的限定。对于所属领域的普通技术人员来说,在上述说明的基础上还可以做出其它不同形式的变化或变动。这里无需也无法对所有的实施方式予以穷举。而由此所引伸出的显而易见的变化或变动仍处于本发明创造的保护范围之中。当前第1页12