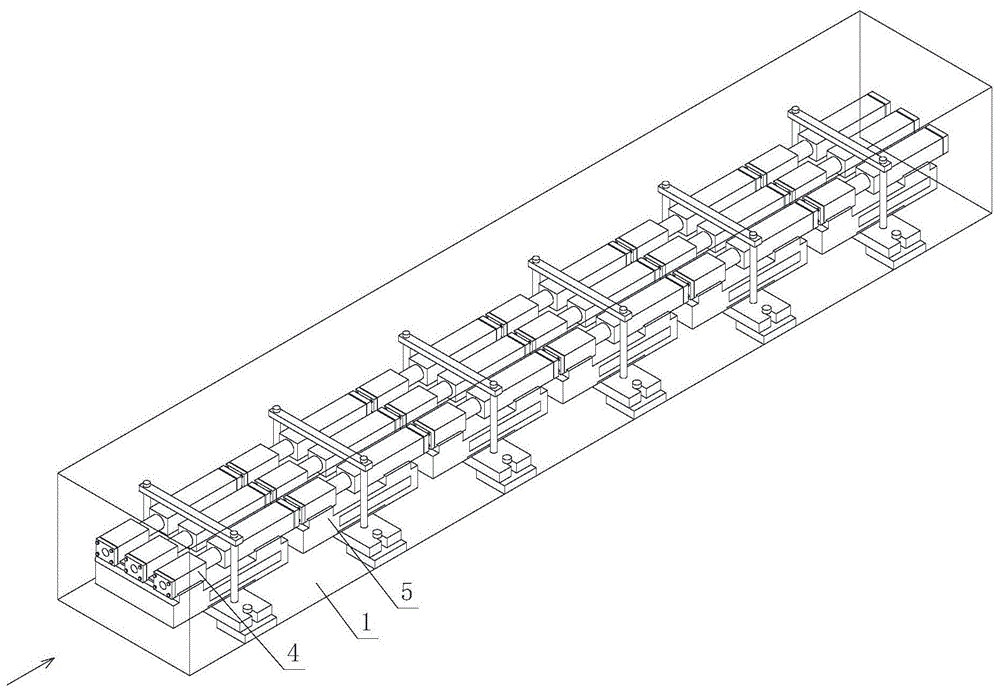
本发明属于轧钢生产设备
技术领域:
,涉及一种冷却装置,具体地说是一种轧钢棒线材生产过程中用的控冷装置。
背景技术:
:随着我国钢铁事业发展壮大,如何提高产品性能、达到节能降耗的目的成为未来钢铁企业的发展方向。当前大部分企业均采用微合金化法的方法生产ⅲ级螺纹钢筋,提高钒或铌的含量,利用钒或铌的碳氮化物的析出强化作用提高螺纹钢筋强度,但提高钒或铌的含量又使得产品成本大大提高。因此,轧钢过程中控温技术应用成为我国今后建筑钢材生产的一种值得广泛推广的可行、经济和使用的工艺技术,通过采用金属加热、轧制和冷却的合理控制的轧制工艺,优化钢材金相组织,大幅度提高钢筋的强度。目前钢厂普遍采用的冷却方法是净水直喷冷却,为了达到更好的冷却效果,大规格棒材生产时,通常用增大水压的方式来提高冷却效率,但过高的水压使能耗相应增高,且提高了生产过程中的危险性;在传统的高压冷却形式下,由于被冷却的轧件壁面温度很高,沸腾换热处于膜态沸腾阶段,轧件表面会形成一层气膜,阻止冷却水和轧件进一步接触,大大降低了沸腾换热系数,使传热效率降低,影响生产效率,同时由于钢材的冷却效果不理想,所生产出来的产品质量也受到一定影响,降低产品的品质。技术实现要素:针对现有技术的不足,本发明提供了一种轧钢棒线生产过程中用的控冷装置,冷却水压力大大降低,且减少了气膜的形成,实现冷却的高效低耗,轧钢棒线的强度和韧性得到大幅提高。本发明采用的技术方案是:一种轧钢棒线生产过程中用的控冷装置,包括水冷箱和设置于水冷箱中的冷却单元,水冷箱上分别设置有与冷却单元配套的箱体进水孔及落水孔,关键在于,所述的冷却单元包括一组沿轧件的进料方向依次设置的冷却器,冷却器借助安装单元与水冷箱固定连接,所述的冷却器包括壳体、沿轧件的进料方向依次设置于壳体内的进料导向管、中间导向管和出料导向管,前一个冷却器的出料导向管与后一个冷却器的进料导向管之间设置有间隙,所述的壳体上设置有借助壳体进水孔与箱体进水孔连接的进水腔,所述的进料导向管的出料端位于进水腔内且与中间导向管之间设置有间隙,所述的进水腔末端、中间导向管的内腔两端及出料导向管的内腔前端的横截面分别呈梯形结构,中间导向管的内腔两端的下底分别与进水腔末端的上底、出料导向管的内腔前端的下底连接。所述的中间导向管的外壁、出料导向管的外壁分别与壳体的内壁贴合,壳体上设置有与出料导向管配套的端盖。所述的安装单元包括与水冷箱连接的分水梁、压板,分水梁上沿垂直于轧件的进料方向的水平方向设置有一组与壳体配套的限位凸起,压板借助连接螺栓与分水梁固连且压板上设置有与壳体配套的压紧螺栓,分水梁上设置有的过水孔,过水孔的入口、出口分别与箱体进水孔、壳体进水孔贯通。所述的分水梁的中部设置有与限位凸起的设置方向平行的通孔。所述的过水孔中设置有进水分线管,进水分线管端部设置有位于分水梁外部的转柄,转柄与分水梁之间设置有旋转密封圈,过水孔内设置有一组进水分线管的支架,所述的进水分线管的前端与过水孔的入口连接,进水分线管上沿其圆周方向依次开设有与过水孔的出口配套的单通口及多通口。所述的进料导向管的出料端的外壁呈锥形。所述的冷却器与水冷箱的长度比为1:(7-10)。所述的进料导向管的外壁上设置有一组呈环形阵列排布的分流凸块。本发明的有益效果是:在水冷箱中沿轧件的进料方向设置多个冷却器,在相同冷却长度的情况下,增加了冷却器的数量,使冷却器的长度大大减少,喷水次数增多,显著的降低了所需冷却水的压力,提高了冷却水与轧件的直接接触效率,缩短了中间导向管与出料导向管的总长度,减少了气膜的形成,实线了冷却水与轧件充分接触进行高效的热交换,通过高效低耗的冷却方式,杜绝了轧件中马氏体的产生,铁素体晶粒度达到10级以上,金相组织为铁素体+珠光体(50%),轧件的强度和韧性大幅度提高,在保证产品品质的前提下可以大幅降低轧件中钒或铌的含量,降低生产成本;将进水腔末端、中间导向管的内腔两端及出料导向管的内腔前端分别设置为横截面呈梯形的结构,轧件由进料导向管、经过进水腔末端进入中间导向管时,与进水腔中的水产生挤压,增加轧件携带水的能力,便于轧件将进水腔中的水带向前方,为中间导向管、出料导向管提供冷却水;中间导向管的内腔两端、出料导向管的内腔前端设置为横截面呈梯形的结构,便于轧件的输出及输入,同时为冷却水进入中间导向管内腔、出料导向管内腔中提供便利。附图说明图1是本发明的结构示意图;图2是安装单元与冷却器的装配示意图;图3是图2中分水梁的a-a向的剖视图;图4是进水分线管的轴测图;图5是冷却器的轴测图;图6是图5的b-b向的剖视图;图7是图6中进料导向管的c-c向的剖视图;图8是水冷箱的结构示意图;图9是使用旧的冷却装置的钢筋在500倍下的中间组织图;图10是使用本发明的冷却装置的钢筋在500倍下的中间组织图;附图中,1、水冷箱,2、箱体进水孔,3、落水孔,4、冷却器,5、安装单元,6、壳体,7、进料导向管,8、中间导向管,9、出料导向管,10、壳体进水孔,11、进水腔,12、出料端,13、过水孔,14、端盖,15、分水梁,16、压板,17、限位凸起,18、连接螺栓,19、压紧螺栓,20、通孔,21、进水分线管,22、转柄,23、支架,24、分流凸块,25、单通口,26、多通口。具体实施方式下面结合附图及具体实施例对本发明作进一步说明。具体实施例,如图1-10所示,一种轧钢棒线生产过程中用的控冷装置,包括水冷箱1和设置于水冷箱1中的冷却单元,水冷箱1的两端均开设有轧件的穿入孔,水冷箱1上分别设置有与冷却单元配套的箱体进水孔2及落水孔3,关键是,所述的冷却单元包括一组沿轧件的进料方向依次设置的冷却器4,即一根轧件穿过水冷箱1需要经过多个冷却器4,冷却器4借助安装单元5与水冷箱1固定连接,安装单元5上可沿横向(垂直于轧件进料方向的水平向)设置多个安装位置,则水冷箱1可同时对多个轧件进行冷却,所述的冷却器4包括壳体6、沿轧件的进料方向依次设置于壳体6内的进料导向管7、中间导向管8和出料导向管9,在图1中即为进料导向管7、中间导向管8、出料导向管9由左向右依次设置,前一个冷却器4的出料导向管9与后一个冷却器4的进料导向管7之间设置有间隙,所述的壳体6上设置有借助壳体进水孔10与箱体进水孔2连接的进水腔11,所述的进料导向管7的出料端12位于进水腔11内且与中间导向管8之间设置有间隙,所述的进水腔11末端、中间导向管8的内腔两端及出料导向管9的内腔前端的横截面分别呈梯形结构,中间导向管8的内腔两端的下底分别与进水腔11末端的上底、出料导向管9的内腔前端的下底连接,在梯形结构中,较长的一条底边叫下底,较短的一条底边叫上底,因此进水腔11的梯形结构的末端(右端)中,下底在左、上底在右;中间导向管8的梯形结构的左端中,下底在左、上底在右;中间导向管8的梯形结构的右端中,上底在左、下底在右;出料导向管9的前端(左端)中,下底在左、上底在右;中间导向管8的左端与进水腔11的末端贴合,中间导向管8的右端与出料导向管9的前端贴合;进水腔11的前端(左端)为环形腔,进水孔10设置在环形腔处。其中,进料导向管7的外壁上设置有一组呈环形阵列排布的分流凸块24,分流凸块24位于进水腔11的呈梯形结构的末端中,对进入进水腔11的冷却水进行分流,使水流更加均步。所述的中间导向管8的外壁、出料导向管9的外壁分别与壳体6的内壁贴合,形成芯轴配套的形式,壳体6上设置有与出料导向管9配套的端盖14,进水腔11的末端的立壁形成了对中间导向管8的左端的限位,端盖14对出料导向管9的右端进行限位,端盖14借助固定螺栓与壳体6固定连接,便于对中间导向管8、出料导向管9的拆装替换。进料导向管7的前端设置有阶梯状的侧壁,壳体6的前端与进料导向管7的阶梯状的侧壁配套进行限位,进料导向管7借助固定螺栓与壳体6固定连接。端盖14及用于固定端盖14的固定螺栓的头部、固定进料导向管7的固定螺栓的头部相接触形成相邻两冷却器4之间的出料导向管9、进料导向管8之间的间隙,尤其是固定螺栓头部的接触,使间隙与水冷箱1贯通,轧件由上一个冷却器4进入下一个冷却器4时有短暂的无冷却水的行程。该冷却器4中所有零件均可根据实际使用情况及时更换,方便长期使用,降低了维修成本。所述的进料导向管7的出料端12的外壁呈锥形,锥形的出料端12与进水腔11的横截面为梯形的末端间隔设置且侧壁之间平行,二者之间的间距增加了进水的湍流,进一步提高了冷却水与轧件的接触效率。冷却器4(包括两端的固定螺栓的头部)与水冷箱1长度比在1:7-1:10的范围内且分母为整数,优选的长度比为1:9,即一根轧件需要经过九个冷却器4,在相同冷却长度的情况下,增加了冷却器的数量,使冷却器的长度大大减少,喷水次数增多,显著的降低了所需冷却水的压力,提高了冷却水与轧件的直接接触效率。轧件接收多个冷却器4的多点加压水冷,使冷却器4中的水压稳定,充分与轧件接触进行冷却,且长度较短的冷却器4内的加压水能够充分填充在轧件与冷却器4的内壁之间,起到润滑的作用,减少轧件输送过程中冷却器4内壁的磨损。安装单元5包括与水冷箱1连接的分水梁15、压板16,分水梁15上沿垂直于轧件的进料方向的水平方向设置有一组与壳体6配套的限位凸起17,相邻的两个限位凸起17之间形成对壳体6卡持的卡槽,本实施例中共设置4个限位凸起17,即一个分水梁15上可横向安装三个冷却器4,冷却器4之间借助分水梁15进行定位、安装,压板16借助连接螺栓18与分水梁15固连且压板16上设置有与壳体6配套的压紧螺栓19,安装冷却器4时,将冷却器4依次放置在限位凸起17之间形成的卡槽内,压板16两侧设置连接螺栓18,分水梁15上设置有与连接螺栓18配套的固定板,将连接螺栓18旋转进入固定板使压板16与分水梁15形成固定,再继续调整压紧螺栓19在竖向上的位置,使压紧螺栓19与卡槽配套形成对冷却器4在竖向上的夹紧,从而完成冷却器4的固定,拆装方便,分水梁15上设置有分别与箱体进水孔2、壳体进水孔10贯通的过水孔13,壳体进水孔10借助过水孔13与箱体进水孔2连接。过水孔13的入口、出口分别与箱体进水孔2、壳体进水孔10贯通。其中,分水梁15的中部设置有与限位凸起17的设置方向平行的通孔20,该通孔20的设置有效增大了分水梁15的散热面积,避免分水梁15及冷却器4内部的热量积累。所述的过水孔13中设置有进水分线管21,进水分线管21端部设置有位于分水梁15外部的转柄22,转柄22与分水梁15之间设置有旋转密封圈,即可实现进水分线管21的转动,又能防止水流出;过水孔13内设置有一组进水分线管21的支架23,所述的进水分线管21的前端与过水孔13的入口连接,进水分线管21上沿其圆周方向依次开设有与过水孔13的出口配套的单通口25及多通口26,由于本实施例中分水梁15上设置有三个冷却器4,所以进水分线管21上分别设置有单通口、双通口(双通口中的两个通口沿进水分线管21设置)和三通口(三通口中的三个通口沿进水分线管21的轴线设置);当进行单线通水(即分水梁15上只有一个冷却器4工作)时,旋转进水分线管21使其上的单通口与其所在竖直位置对应的过水孔13的出口对应,过水孔13的其他两个出口对应的是进水分线管21的侧壁;进行双线通水(即分水梁15上有两个冷却器4工作)时,旋转进水分线管21,使其上的双通口与各自所在竖直位置对应的过水孔13的出口对应;进行全线通水(分水梁15上三个冷却器4全部工作)时,旋转进水分线管21,使三通口分别与各自所在竖直位置对应的过水孔13的出口对应,则过水孔13中的冷却水可向三个冷却器4供水;进水分线管21的设置,使本发明的控冷装置实现了多线可控操作,即可进行单线冷却,又可进行多线冷却,且结构简单,调节方便。工作时,冷却水由外部的供水设备向水冷箱1中供水,冷却水沿箱体进水孔2进入分水梁15上的过水孔,再由过水孔依次向三个横向排列的冷却器4进行供水,冷却水由过水孔经过壳体进水孔10,随即进入进水腔11中;轧件由水冷箱1的左端的穿入孔穿入冷却器4中,首先经过冷却器4中的进料导向管7中,进料导向管7的内腔的前端的横截面为梯形结构,便于轧件进入进料导向管7的内腔,随后依次经过进水腔11、中间导向管8、出料导向管9,将进水腔11中的冷却水带入中间导向管8、出料导向管9中;由左侧的第一个分水梁15上的冷却器4出来后,随即进入第二个分水梁15上的冷却器4中,在沿轧件的进料方向依次排列的冷却器4中依次进行冷却。由于冷却器4之间端盖14安装用的固定螺栓的头部与进料导向管7安装用的固定螺栓的头部相互接触,因此造成上一个冷却器4的出料导向管9与下一个冷却器4的进料导向管7之间呈间隔无冷却水的状态,轧件在冷却器4之间运行时,气膜会消失,多个冷却器4使气膜重复消失,提高了冷却水与轧件的热交换效率。下面对实际生产中采用旧控冷装置冷却和本发明的控冷装置冷却的使用情况进行对比分析。本次共轧制四个规格钢筋,钢种牌号hrb400e,各项性能对比中旧控冷装置所对应的钢种中钒的含量为0.025-0.035%,使用本发明的控制冷制的钢种中钒的含量为0.01-0.015%,具体的成分表如下:旧控冷装置对应的钢种化学成分:csimnspv0.22-0.25%0.65-0.75%1.4-1.5%≤0.045≤0.0450.025-0.035%本发明的控冷装置对应的钢种化学成分:csimnspv0.22-0.25%0.65-0.75%1.4-1.5%≤0.045≤0.0450.01-0.015%指标对比如下[统计数据为11月(旧控冷装置)与12月、1月及2月(本发明的控冷装置)的加权平均数的对比情况]:1、产量对比可见,使用本发明的控冷装置后平均日产提高了561t;2、机时产量及作业率对比使用本发明的控冷装置后机时产量平均提高18.48t/h,日历作业率平均提高了14.51%;3、性能对比使用旧控冷装置时的平均性能:使用本发明的控冷装置时的平均性能:尽管降低了轧件中钒的含量,但利用本发明的控冷装置冷却后的性能均能够符合gb1499.2-2018标准要求,均匀性较好;后期我们利用旧控冷装置对钒的含量为0.01-0.015%的钢种进行冷却,最终得出各直径的屈服强度均低于400mpa,且金相组织不合格。4、轧件弯曲度对比使用旧控冷装置四个规格钢筋均有不同程度的波浪弯曲,且单米弯曲度为0.4-0.6%,超过了gb1499.2中规定的“直条钢筋的弯曲度应不影响使用,总弯曲度不大于钢筋总长度的0.4%”,因此需要后期进行矫直,增加了成本投入;使用本发明的控冷装置后波浪弯曲基本消除,平直度较之前有较大改观,经测量,钢筋单米弯曲度低于0.3%,成品弯曲度好且无需后期矫直。5、钢材后尾翘头对比使用旧控冷装置四个规格钢筋的头尾弯曲长度在600mm左右;使用本发明的控冷装置后,每根钢材备尺前头及后尾的弯曲分叉现象消除,钢筋头尾弯曲长度小于200mm,裙板扎钢、乱钢现象基本消除;齐头辊道处齐头效果较好,改善了之前因齐头差影响生产节奏的现象,为后区钢材收集提供了良好条件。6、晶粒度及金相组织方面对比实行钢筋混凝土用热轧带肋钢筋gb1499.2-2018之新国家标准后对钢筋的晶粒度和金相组织提出了明确要求:热轧钢筋晶粒度为9级以上且金相组织基圆上不能出现回火马氏体组织。使用旧的控冷装置维氏硬度差,宏观金相及高倍微观组织、晶粒度情况(控冷温度控制在820-850℃之间):维氏硬度及晶粒度差超标。维氏硬度检测报告高倍试验报告钢筋中间组织参见图9;使用本发明的控冷装置后维氏硬度好,宏观金相及高倍微观组织、晶粒度情况(控冷温度控制在820-850℃之间):维氏硬度检测报告高倍试验报告钢筋中间组织参见图10;使用本发明的控冷装置后,实现了棒材hrb400/eφ18-25mm控冷工艺的稳定生产,上冷床温度控制在820-890℃之间,调整余量较大。钢材产品的性能、强屈比、弯曲度及金相组织等质量指标均符合gb1499.2-2018标准要求,质量较稳定。效益测算:1、节能降耗效益控冷区域三台水泵电机均为315kw,其中两台变频(6/7号水泵),一台工频(8号水泵)。使用旧的控冷装置时:生产时,水泵的开启采用一变频加一工频的模式,6/7号泵开至47赫兹,8号泵进口侧阀门开口度为100%,出口侧阀门开口度为55%。水压控制在1.45-1.75mpa,流量在335m3/h。使用本发明的控冷装置后:生产时,水泵的开启采用一变频加一工频的模式,6/7号泵开至40赫兹,8号泵进口侧阀门开口度为100%,出口侧阀门开口度为30%。水压控制在0.55-1.05mpa,流量在210m3/h。压力和流量的降低使电耗大大降低,吨钢节电约1.8kwh/t,年创造效益=产量×节约电量×电耗单价=7.5万吨×12×1.8kwh/t×0.486元/kwh=78.73万元。2、增产效益每日增产约561吨,按吨材效益100元/吨计算。年创造效益=365天×增产吨位×平均日历作业率×吨材效益=365×561吨×51%×100元/吨=1044.30万元。3、成材率提高效益在使用旧的控冷装置时钢材前头不合格处至少需剪切3m,使用本发明的控冷装置后完全消除了此问题,只此一项成材率上升0.47%,直接效益达4.3元/吨。年创造效益=7.5万吨×12×直接经济效益=7.5万×12×4.3元/吨=387万元。4、钢坯合金成分效益本发明的控冷装置解决了成品波浪弯、性能波动大、金相组织不稳定、穿水调整难度大的问题,在保证质量的前提下,钢坯化学成分进行了合金优化,使钢材产品性能达标:原有钢坯化学成分:csimnspv0.22-0.25%0.65-0.75%1.4-1.5%≤0.045≤0.0450.025-0.035%优化后钢坯化学成分:csimnspv0.22-0.25%0.65-0.75%1.4-1.5%≤0.045≤0.0450.01-0.015%采用本发明的冷却装置还可实现钢坯化学成分的进一步优化,实现不加钒或铌等贵金属,使钢材产品性能符合新国标gb/t1499.2-2018的要求:进一步优化的钢坯目标化学成分为:csimnsp0.22-0.25%0.68-0.78%1.48-1.58%≤0.045≤0.045按2018年10月份市场价格的平均值:钢中v每降低0.010%,添加氮化钒铁钢种生产成本降低110元/t。本发明的发明人在实际生产中发现,在一个单位热交换系统中,当流量相对小时,流量的改变对冷却的效果影响较大;当流量增大到一定值后,随着流量的持续增大,对冷却效果的影响逐渐减小,因此,本发明的控冷装置中采用多冷却器4逐级冷却,使冷却水所需的压力大大降低,约0.35-6mp的水压即可满足钢厂的生产需要,相对于传统强穿需要的1.8mp压力相比,吨钢可节约电耗1元左右,在实际生产中,长度12-18m水冷线降温幅度达到400-600℃(根据轧制规格,例如φ14、φ16、φ18、φ20、φ22、φ25、φ28等),仅高压泵站一项,所节约的用电量就可使轧钢厂每年减少成本达上千万;在产品性能方面,由于气膜的减少,冷却水与轧件之间的接触更加充分,增大了沸腾换热系数,提高了传热效果,进而提高了生产效率,通过这种高效低耗的冷却方式,杜绝了马氏体的产生,使轧件的强度和韧性大幅度提高,在保证质量的前提下进一步节省了生产成本。当前第1页12