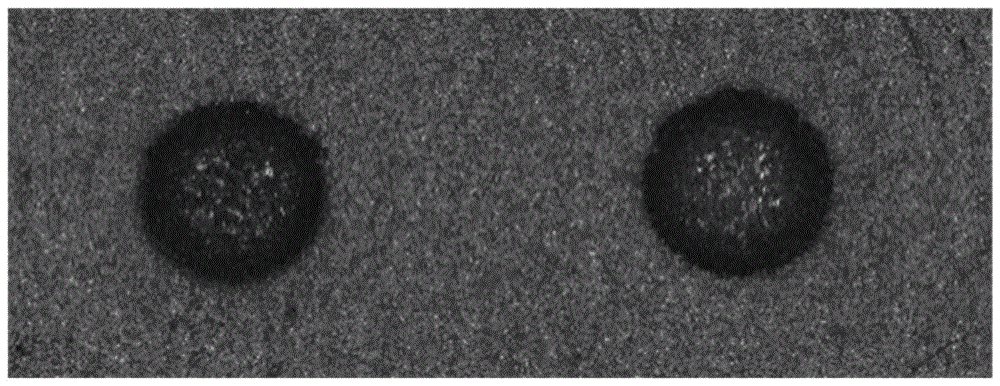
本发明涉及微细电解加工领域,更加具体地说,涉及一种在电解槽中对铝基碳化硅复合材料进行微细电解加工的加工方法。
背景技术:
:电解加工(electrochemicalmachining,ecm)是一种基于电化学腐蚀原理,利用可控的阳极溶解定域去除工件材料,从而获得所需形状与尺寸的加工技术。电解加工过程中,阴极为加工工具,阳极为被加工工件,阴阳两极之间维持一个极小的加工间隙。根据法拉第定律,工件阳极的材料溶解由电流密度分布决定。通过采用不同工艺方法,控制电流密度分布,从而获得所需的形状与尺寸。电解加工由于其特殊的加工机理,具有无切削力与切削热影响,加工效率高、加工表面无残余应力与刀痕等优点,在航空航天、汽车、国防装备等工业领域已得到了成功应用。微细电解加工(electrochemicalmicro-machining,ecmm)是指在微细加工范围内(1μm-1mm),电解加工得到高精度、微小尺寸零件的加工方法。在微细电解加工中,工件材料以离子的形式被蚀除,理论上可以达到μm甚至mm级加工精度,微细电解加工对装备要求高,加工间隙小。该方法不需要采用与加工工件形状一样的成型阴极电极工具,对阴极工具没有磨损和损耗,具有很好的灵活性和方便性,可以实现难加工材料、复杂三维型面的加工,加工后工件表面几乎不存在缺陷且表面光滑、没有毛刺,已广泛应用于飞机涡轮叶片和微电子仪器等的小直径孔和复杂形状孔的加工。微细电解加工是一门具有综合性和交叉性的学科,近年来发展迅速。微细电解加工在脉冲电源机制、控制策略、精度进给、检测方式、磁场影响、减少污染和改善工艺等方面取得了重大进展。铝基碳化硅复合材料是以铝或者铝合金为基体,以sic颗粒或纤维为增强相的一种复合材料,具有优异的物理和力学性能,如高比强度、高比模量、低膨胀系数、耐磨、耐高温、良好的热稳定性等。其制备工艺简单、成本低,适于批量生产,且可用常规金属加工方法—铸造、挤压、轧制、焊接等制造各种形状的零件和型材,因而成为金属基复合材料(简称mmc)发展的主要方向,也是目前应用最广、发展最快、价格最便宜、能最早实现大规模生产的一种mmc。在航空航天、汽车、电子、医学等领域具有极高的应用价值,是空间
技术领域:
中理想的结构材料。铝基碳化硅复合材料拥有优异的性能,但因为碳化硅的高强度和硬度,一般的加工的方法很难对其加工,并且会对材料产生磨损和残余应力。因此采用微细电解加工对铝基碳化硅复合材料进行加工成为一种潜在的加工方法。微细电解加工是一种非接触的方法,通过控制加工条件,可以实现工具材料在无热、力的影响下进行材料去除,因此微细电解加工成为一种潜在的加工铝基碳化硅复合材料的加工方法。因此探究一种有利于加工铝基碳化硅复合材料的微细电解加工具体方法和参数成为迫切需求。技术实现要素:本发明的目的在于克服现有技术的不足,针对传统的加工方法加工铝基碳化硅复合材料的种种缺陷,提供一种使用微细电解加工对铝基碳化硅复合材料加工的方法,能够成功加工出效果良好的铝基碳化硅复合材料工件。本发明的技术目的通过下述技术方案予以实现:一种使用微细电解加工对铝基碳化硅复合材料加工的方法,按照下述步骤进行:步骤1,将工件安装到固定装置上并放置在电解槽中,将配置好的电解液倒入电解槽中,使电解液漫过工件,工件为铝基碳化硅复合材料,电解液为1—3mol/l的nano3水溶液或者nacl水溶液;在步骤1中,加入电解液后,电解液的水平面高于工件平面1—1.5mm。在步骤1中,选用的nano3纯度为ar,杂质不超过1%;nacl纯度为ar,杂质不超过1%;使用的去离子水电阻率大于0.5mω·cm。步骤2,将钨丝阴极和电解槽安装在工作台上,打开z轴运动平台,调节钨丝阴极和工件的距离,使钨丝阴极垂直于工件上方50μm并对准加工位置(即加工间隙控制在50μm),使用导线串联阴极和工件,并连接示波器;在步骤2中,钨丝阴极直径为100—120μm。步骤3,设定加工平台的移动参数,进行微细电解加工:加工电压20-30v,电源频率为800—1000hz;环境温度为20-25℃。在步骤3中,加工平台的移动参数包括运动初始坐标,运动终点坐标,运动速度。在步骤3中,制备点槽时,打开电解加工电源开关,开始进行电解加工,直到将点槽打出。在步骤3中,制备沟槽时,同时打开电解加工开关和平台行走开关,进行沟槽制备,直至制备完成,阴极移动速度为1—3mm/min。在进行加工时,工件的尺寸为21mm×11mm×2mm。与现有的技术相比,本发明提供了一种利用电解液对铝基碳化硅复合材料进行微细电解加工的方法,减小了常规加工工艺中对本材料的负面影响,以及提高了加工精度和加工效率,并且能够提高加工质量。本发明探索了微细电解加工中的加工参数对加工质量的影响,提供了良好可靠的加工参数,适用于碳化硅含量小于50%的铝基碳化硅复合材料的加工。附图说明图1为加工所得的工件形貌超景深显微镜图片(1)。图2为微细电解加工平台示意图。图3为加工所得的工件形貌超景深显微镜图片(2)。图4为本发明实施例使用的碳化硅铝基复合材料的光学显微镜拍摄的图片。具体实施方式下面通过具体实施例对本发明的技术方案作进一步描述。应当理解,此处所描述的具体实施例仅用以解释本发明,并不用于限定本发明。nano3、nacl粉末、去离子水的来源如下表所示:药品名称化学式纯度规格生产厂家硝酸钠nano399%分析纯上海泰坦科技公司氯化钠nacl99%分析纯上海泰坦科技公司去离子水h2o—分析纯天津天利化学试剂厂本发明实施例使用的碳化硅铝基复合材料如附图4所示,所用材料为20%含量的碳化硅铝基复合材料,并对该材料进行了性能测试,如下表所示。按照下述方法进行实施:(1)按照浓度计算所需nano3或者nacl的质量与去离子水体积,准确称量出所需的nano3与去离子水后在烧杯中充分溶解。(2)将工件安装到固定装置上,并将固定装置放置在电解槽中,再将配置好的溶液倒入电解槽中,保证水平面浸过工件且高于工件平面1mm。(3)将微细阴极和电解槽安装在加工平台上,并通过加工平台调整阴极位置,使得阴极垂直于工件上方,加工间隙为50μm。(4)设定加工平台的实验参数包括运动初始坐标,运动终点坐标,运动速度,加工电压以及电源频率。(5)加工点槽时,通过行走装置调整位置,开启加工电源,进行微细电解加工,实验过程根据加工深度计算加工时间;加工沟槽时,同时开启加工电源和平台移动机构。(6)对所得的加工工件采用超景深显微镜进行观察。实施案例1(1)按照1mol/l浓度计算所需nano3质量与去离子水体积,准确称量出所需的nano3与去离子水后在烧杯中充分溶解。(2)将工件安装到固定装置上,并将固定装置放置在电解槽中,再将配置好的溶液倒入电解槽中,保证水平面浸过工件且高于工件平面1mm。(3)将微细阴极和电解槽安装在加工平台上,并通过加工平台调整阴极位置,使得阴极垂直于工件上方,加工间隙为50μm。(4)设定加工平台的实验参数包括运动初始坐标0(μm),运动终点坐标0(μm),运动速度0(μm/s),以及加工电压20v,电源频率1000hz,加工温度25℃。(5)开启加工电源,进行电解加工,进行时间为30s。(6)加工所得的工件采用超景深显微镜进行观察。加工出的工件点槽深度为112.4μm,凹坑平均直径为1430.3μm,表面光滑且直径均匀,如附图1左侧照片所示。实施案例2(1)按照1mol/l浓度计算所需nano3质量与去离子水体积,准确称量出所需的nano3与去离子水后在烧杯中充分溶解。(2)将工件安装到固定装置上,并将固定装置放置在电解槽中,再将配置好的溶液倒入电解槽中,保证水平面浸过工件且高于工件平面1mm。(3)将微细阴极和电解槽安装在加工平台上,并通过加工平台调整阴极位置,使得阴极垂直于工件上方,加工间隙为50μm。(4)设定加工平台的实验参数包括运动初始坐标0(μm),运动终点坐标0(μm),运动速度0(μm/s),以及加工电压25v,电源频率1000hz,加工温度25℃。(5)开启加工电源,进行电解加工,进行时间为30s。(6)加工所得的工件采用超景深显微镜进行观察。加工出的工件点槽深度为129.7μm,凹坑平均直径为1576.3μm,表面光滑且直径均匀,如附图1右侧照片所示。实施案例3(1)按照1mol/l浓度计算所需nacl质量与去离子水体积,准确称量出所需的nacl与去离子水后在烧杯中充分溶解。(2)将工件安装到固定装置上,并将固定装置放置在电解槽中,再将配置好的溶液倒入电解槽中,保证水平面浸过工件且高于工件平面1mm。(3)将微细阴极和电解槽安装在加工平台上,并通过加工平台调整阴极位置,使得阴极垂直于工件上方,加工间隙为50μm。(4)设定加工平台的实验参数包括运动初始坐标0(μm),运动终点坐标0(μm),运动速度0(μm/s),以及加工电压20v,电源频率1000hz,加工温度25℃。(5)开启加工电源,进行电解加工,进行时间为30s。(6)加工所得的工件采用超景深显微镜进行观察。加工出的工件点槽深度为115.8μm,凹坑平均直径为1480.5μm,表面光滑且直径均匀,如附图3所示。根据本
发明内容进行工艺参数的调整,均可实现在碳化硅含量小于50%的铝基碳化硅复合材料的微细电解加工,实现点槽或者沟槽的制备,类似附图1和3所示形貌。以上对本发明做了示例性的描述,应该说明的是,在不脱离本发明的核心的情况下,任何简单的变形、修改或者其他本领域技术人员能够不花费创造性劳动的等同替换均落入本发明的保护范围。当前第1页12