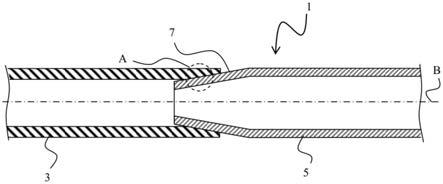
1.本发明涉及将铜管和铝管接合的接合体以及其接合方法。
背景技术:2.以往,使用铜管作为空调设备的配管材料,但是近年来,从降低材料成本或者轻量化的观点出发,铝管的使用逐渐增加以代替铜管。尤其是换热器的铝化正在广泛进行。这样,在铜管和铝管混合存在的状况下,需要连接铜管和铝管。
3.铜管和铝管的连接方法有几种,目前在批量生产中广泛使用的方法之一是共晶接合(例如,非专利文献1)。共晶接合是扩散接合的一种,其特征在于接合面暂时液化。其方法为在铝管中嵌入前端进行了缩管加工的铜管,在用力压入铜管的同时加热进行接合。
4.由于在铜和铝的二元状态图中存在共晶点(548℃),因此若使铜管和铝管接触并进行加热,则通过扩散使得在接触面上发生彼此的原子的混合,在温度达到共晶点时接触面附近熔融。共晶接合是利用这一点在短时间内将铜管和铝管接合的方法(非专利文献2)。
5.现有技术文献
6.非专利文献
7.非专利文献1:浅野祐一郎“异种金属管的接合”轻金属焊接vol.42(2004),no.9,pp429
‑
434
8.非专利文献2:里达雄、北冈山治、神尾彰彦“al
‑
cu系合金”轻金属vol.38(1988),no.9,pp558
‑
578
9.专利文献
10.专利文献1:日本特开平11
‑
33747号公报
11.专利文献2:日本特开2011
‑
140049号公报
技术实现要素:12.发明要解决的问题
13.然而,作为以往的共晶接合技术,主要研究的是通过优化铜管的前端的锥形状或铜管向铝合金管的插入条件、加热条件等,从而得到更高的接合质量。
14.例如,在专利文献1中,详细公开了如下共晶接合方法:加热前端加工成锥状的铜管,以特定的速度将其压入铝管。在专利文献1中,使用了外径比铝管的内径稍大的铜管。将铜管的前端以锥角1度~8度进行加工,使用高频加热线圈将该铜管加热到铜
‑
铝的共晶点(548℃)以上、铝管的熔点以下的温度。在该状态下,以10mm/秒以上的速度将铜管压入铝管,之后通过通入压缩空气进行冷却,从而将两者接合。
15.例如,在专利文献1的实施例中,作为实际具体的接合例,使用了外径壁厚0.6mm的脱氧铜管和同样外径壁厚0.6mm的铝管(99.3%al)。加热铜管10秒钟使铜管温度达到750℃,之后降低加热速度使铜管温度为560℃,然后以50mm/秒的速度将铜管压入铝管,之后通过利用压缩空气进行冷却,将两者接合。然而,在这样的方法中,仅初期加热就需
要10秒,从生产率的观点来看,该方法不能直接适用于批量生产。
16.对于此,在专利文献2中,作为用于批量生产的方法,提出了像电阻焊接那样,通过经由电极向铜原材料和铝原材料流通电流,从而迅速进行加热的方法。另外,为了提高共晶接合的质量,提出了附加二次加压。若在铜原材料和铝原材料互相挤压的界面上发生共晶反应,则在界面上产生液相,其结果是导致挤压面上可能发生位移,因此检测出该位移并在该时机进行二次加压。
17.然而,专利文献1、2的方法均是在接合时铝管的连接部膨胀,并且外径变大。其中,获得高质量的共晶接合的重要因素之一是铜管和铝管的接触压力高。由于在铜管的插入导致铝管的连接部膨胀时,在铜管和铝管的接触面上产生的压力降低,因此有发生接合层的质量降低、接合强度降低等的风险。另外,在铝管膨胀的情况下,由于接合部的管的偏心等形状异常,因此有产生接合部的强度降低和外观异常等问题的风险。因此,不希望是铝管乍一看是膨胀的接合部。
18.另外,专利文献1、2均示出了铜管形状和接合时的条件的详细数值,但没有考虑例如由于设计变更或材料尺寸变动等导致管壁厚变化的情况下,在提出的方法和条件下是否能够进行共晶接合这样的与进行实际生产时必须面对的状况相关的内容。
19.本发明是鉴于这样的问题而提出的,其目的在于提供制造性优异、可靠性高的铜管和铝管的接合体及其接合方法。
20.用于解决问题的方案
21.为了达到上述目的,第一发明是铜管和铝管的接合体,其特征在于,所述接合体由铜管和铝管构成,在接合体的长度方向的截面视图中,所述铝管的内表面和所述铜管的外表面相对于长度方向倾斜地接触,所述铝管的外表面相对于长度方向大致平行,所述铝管的内表面和所述铜管的外表面上形成有共晶层。
22.在与所述铝管接合的所述铜管的端部上优选设置有随着趋向前端而缩径的锥形部,并且所述铝管的内表面与所述铜管的所述锥形部的外表面接触。
23.在与接合体的长度方向垂直的截面上,所述铜管的管坯部分的截面积优选比所述铝管的管坯部分的截面积小。
24.在与接合体的长度方向垂直的截面上,所述铜管的管坯部分相对于所述铝管的管坯部分的截面积的截面积比优选为0.53~0.85。
25.根据第一发明,铜管的外表面与铝管的内表面的接触部相对于长度方向倾斜地接合,但由于铝管的外表面呈大致直线状,因此铜管和铝管的外径不变大。因此,能够提高铜管和铝管的接触面上产生的压力,另外由于不易发生接合部的管的偏心等形状异常,因此能够获得高质量的接合部。
26.另外,通过在与铝管接合的铜管的端部上设置随着趋向前端而缩径的锥形部,能够容易地插入铝管中,容易接合。
27.另外,在与接合体的长度方向垂直的截面上,通过使铜管的管坯部分的截面积比铝管的管坯部分的截面积小,在相同条件下同时进行加热时,能够减小接合部中的铜管和铝管的温度差,从而以更高质量进行接合。
28.尤其,若铜管的管坯部分相对于铝管的管坯部分的截面积的截面积比为0.53~0.85,则能够更可靠地高质量地进行接合。例如,若不考虑截面积而进行加热,则铜管的温
度难以高于铝管的温度,因此没有充分加热到共晶温度,有接合不良的风险。另外,若充分加热铜管,则铝管的温度会过高,存在部分熔融等问题。对于此,通过适当地设定截面积,能够使两者的温度大致相等,能够高质量地进行接合。
29.第二发明是铜管和铝管的接合方法,其特征在于,所述铜管在一方的端部具有随着趋向前端而缩径的锥形部,将所述铜管的锥形部插入所述铝管的端部,直接向所述铜管和所述铝管通电进行加热,在所述铜管的外表面和所述铝管的内表面的接合部上形成共晶层进行接合。
30.在与长度方向垂直的截面上,所述铜管的管坯部分相对于所述铝管的管坯部分的截面积的截面积比优选为0.53~0.85。
31.根据第二发明,通过直接向铜管和铝管通电,能够在短时间内对两者进行加热从而接合。
32.此时,若铜管的管坯部分相对于铝管的管坯部分的截面积的截面积比为0.53~0.85,则如上所述,能够高质量地进行铜管和铝管的接合。
33.发明效果
34.根据本发明,能够提供制造性优异、可靠性高的铜管和铝管的接合体及其接合方法。
附图说明
35.图1a是示出接合体1的图。
36.图1b是图1a的a部的放大图。
37.图2a是示出接合体1的生产过程的图。
38.图2b是示出接合体1的生产过程的图。
39.图3a是示出接合体1的弯曲试验方法的图。
40.图3b是示出接合体1的弯曲试验方法的图。
41.图4是示出的接合体1的水压气密试验方法的图。
具体实施方式
42.以下参照附图对本发明的实施方式进行说明。图1a是接合体1在长度方向上的剖视图,图1b是图1a的a部的放大图。接合体1是铜管5和铝管3的接合体。此外,铜管5是铜制或者铜合金制的管体,铝管3是铝或者铝合金制的管体。
43.在与铝管3接合的铜管5的端部上设置有随着趋向前端而缩径的锥形部7。铜管5的锥形部7插入铝管3中,铝管3的内表面与铜管5的锥形部7的外表面接触。
44.在接合体1在长度方向上的截面视图中,铝管3的内表面和铜管5的外表面相对于接合体1的长度方向(图1a的线b)倾斜地接触。另外,铝管3的外表面形成为相对于接合体1的长度方向(图1a的线b)大致平行。此外,铝管3的外表面相对于长度方向大致平行,是指接合部的外径相对于铝管3的外径增加5%以下。
45.另外,如图1b所示,在围绕铝管3的内表面和铜管5的外表面的整个圆周上形成有共晶层9。即,铝管3和铜管5通过共晶层9接合。
46.接着,对铜管5和铝管3的接合方法进行说明。首先,如图2a所示,使铝管3和铜管5
对置。此外,铝管3配置在省略了图示的电极上。例如,通过使用具有与铝管3的外径对应的槽的一对电极夹住铝管3,能够从外表面约束铝管3。
47.此外,如上所述,铜管5在与铝管3对置的一方的端部上具有随着趋向前端而缩径的锥形部7。其中,锥形部7的锥角(图中θ)优选为3度~9度。
48.接着,如图2b所示,通过将铜管5的锥形部7插入由电极保持的铝管3的端部,将电源11连接到铜管5和铝管3上并直接通电,从而进行加热。电源11例如通过流通数千a的大电流约1秒左右,能够将铜管5和铝管3的温度急剧上升到共晶点附近。其结果是铜管5的外表面和铝管3的内表面的接合部上能够形成共晶层9并接合。此时,由于铝管3被从外表面约束,因此不会扩径。
49.其中,在本实施方式中,在与接合体1的长度方向垂直的截面上,铜管5的管坯部分的截面积优选比铝管3的管坯部分的截面积小。其中,管坯部分的截面积是指不是锥形部,并且不受接合时的截面积的变化的影响的部位的管体的截面积,与接合前的各管体(管坯)的截面积大致相等。
50.这样,使铜管5和铝管3的截面积不同是基于以下理由。在共晶接合中,铜管5和铝管3的接触部的温度达到共晶点以上而发生反应。发明人注意到,在铜管5和铝管3的共晶接合中,双方的材料温度非常重要,并且发现适当地设定共晶接合时的材料温度对得到更高质量的接合部很重要。
51.其中,若同时在相同条件下加热铜管5和铝管3,则铜管5和铝管3的温度将根据两者的热容量而变化。即,若热容量大则温度难以上升,若热容量小则温度容易上升。
52.另外,使铜管5和铝管3的前端接触形成串联电路,在电流流过时,主要的发热源是管中产生的焦耳热。单位长度的焦耳热的大小由材料的电阻率决定。另外,由该热引起的温度的变化的程度由材料的比热容决定。这样的物理参数是材料所固有的,但是若截面积发生变化,则单位长度的热容量和发热量也会发生变化,因此能够通过调整截面积来补偿两个管之间因物理参数而产生的温度差。即,发明人发现,由于铜管5和铝管3的截面积是可调节的,因此通过适当地设定铜管5和铝管3的截面积,能够使两者处于适当的温度。
53.例如,若截面积增加1%,则管体的单位长度的热容量增加1%,但是管体的单位长度的电阻値减少1%,结果是发热量减少1%,因此管体的单位长度的温度上升减少约2%。这样,假定热模型来计算温度,结果发现,通过使铜管5的截面积比铝管3的截面积小预定的量,能够补偿由铜管5和铝管3的物理参数引起的温度差。
54.即,通过适当地设定铜管5和铝管3的截面积比,能够在零度~超过共晶点(约550℃)约600℃的温度范围内,使两者的温度上升率大致相同,因此在从相同温度同时加热铜管5和铝管3时,两者的温度在相同时刻达到相同温度。这样,在进行铜管5和铝管3的接合时,通过适当地设定两者的截面积比,能够将两者的温度同时加热到共晶点,由此能够改善共晶接合质量。
55.发明人进一步对适当的截面积比进行了验证,发现特别优选的是,在与长度方向垂直的截面上,铜管5的管坯部分相对于铝管3的管坯部分的截面积的截面积比为0.53~0.85。
56.此外,作为截面积的测定方法,在相对于长度方向正交的两个方向上测定未进行末端加工且未受到末端加工的影响的管坯部分的外径和壁厚,从而根据直径和壁厚的测定
值的平均值计算截面积。
57.在接合体1的接合部附近,由于接合时的加热等,各管体的截面积有可能从接合前开始发生变化,但只要是充分远离接合体1的接合部的位置,接合前后的截面积几乎没有变化。因此,如图2a所示,铜管5的管坯部分的截面积是指在锥形部7的长度为l时,距离铜管5的端部3l的位置处的铜管5的截面积。同样地,铝管3的管坯部分的截面积是指距离铝管3的端部3l的位置处的铝管3的截面积。
58.此外,实际上,由于在共晶接合中应该考虑的各管体的截面积是两者的接合部,因此铜管5的截面积为锥形部7的截面积。在锥形部7中,由于截面积根据部位而不同,因此铜管5的截面积的准确计算很复杂。然而,若锥角为3度~9度左右,则即使使用在管坯部测定的截面积,也不会出现大的差异。因此,在本实施方式中,为了简便,利用在管坯部测定的截面积确定优选的截面积比的范围。
59.通过这样做,能够更可靠地在围绕铝管3的内表面和铜管5的外表面的整个圆周上形成高质量的共晶层9。其中,在与接合体1的轴向垂直的一个截面上可以不完全环状地形成共晶层9。例如,共晶层9也可以在管轴向上弯曲的同时形成。即,共晶层9也可以是在锥形面上的周向和轴向上起伏的三维闭合曲线。
60.此外,在接合体1例如作为空调的配管使用时,在空调运行时施加在配管内部的压力通常最大为4.2mpa左右。若接合部上有效地存在共晶层9,则能够充分确保对这种压力的耐压性能。另一方面,若共晶层9没有充分形成等、接合部中存在不良部,则无法得到上述耐压性能。
61.另外,通过使用sem等进行图像的分析、接合面厚度方向的组成变化的线分析等,也能够调查到泄漏部位的共晶层9的存在。此外,根据经验,在共晶层9的区域内,成分分析的结果是铜在30%~60%的范围内(铜侧的铜浓度高,作为趋势,铜浓度从铜侧向铝侧逐渐减少)。若脱离共晶层9的区域,则铜浓度或者铝浓度会急剧变化,因此也能够判定有无共晶层9。
62.如上所述,在本实施方式中,通过适当地设定铜管5和铝管3的截面积比,能够有效地加热两者,并进行共晶接合。
63.另外,由于能够抑制铜管5和铝管3的一方过热,因此能够抑制在接合时铜管5的变形和铝管3的熔断等,并且能够获得高的接合强度。
64.实施例
65.作为空调配管,使用普通外径的铜管和铝管进行共晶接合,评价了接合质量相对于截面积比的不同的差异。铜管的壁厚为0.4mm、0.5mm、0.6mm、0.8mm、1.0mm,铝管的壁厚为1.0mm、1.2mm。铜管和铝管的组合如表1所示。
66.表1
[0067][0068]
如表1所示,no.1~no.5是将铝管的壁厚设为相同的1mm,将铜管的壁厚设为0.4mm~1mm变化的情况。no.5、no.6是将铜管的壁厚设为1mm,将铝管的壁厚设为1.0mm、1.2mm变化的情况。对表1的组合进行共晶接合的结果如表2所示。
[0069]
表2
[0070][0071]
共晶接合质量通过水压气密试验、剥离试验以及外观进行评价。水压气密试验是在考虑到上述空调配管的耐压性能的基础上实施的。首先,如图3a所示,将接合体1竖直地固定在固定夹具13上。接着,如图3b所示,从竖直方向向左右各弯曲θ1=5度,恢复到竖直设为一次来回,重复进行三次来回。
[0072]
其后,如图4所示,利用密封部15密封接合体1的一端,另一端与泵17连接,利用泵17从水槽19向接合体1附加4.2mpa的水压,从而调查泄漏。若没有泄漏,则将接合体1返回固定夹具13,使弯曲角度为10度,在施加了三次来回的弯曲负载后,进行同样水压下的气密试验。在表2中,未发现泄漏的记为“good”,发现泄漏的记为“bad”。
[0073]
剥离试验通过使用工具将接合体的铝管从铜管剥离,测定残留在铜管接合面的铝管的剥离痕迹的轴向长度从而进行评价。接合弱时,铝管从与铜管的界面作为整体一次剥离,没有发现铝的残留。另一方面,接合牢固时,铝管无法从铜管上剥离,若强行剥离,则铝管会断裂并残留下来。在这种情况下,剥离痕迹的长度包括了残留的铝管的长度。如上所
述,在剥离试验中测定铝管的剥离痕迹相对于铜管的长度,评价接合强度。
[0074]
此外,由于剥离痕迹的长度在铜管周向上略有变动,因此,从整个圆周来看,将最短的剥离痕迹的长度定义为其接合体的接合长度。在相同条件下进行n=3的试验,利用剥离痕迹的平均长度进行各条件的评价。接合长度的平均值为0的为“bad”,发现剥离痕迹但平均接合长度不足5mm的为“average”,平均接合长度在5mm以上的为“good”。
[0075]
另外,在外观方面,在共晶接合之后立即对接合部附近,通过目视调查铝管的熔融、伤、孔、断裂、铜管的膨胀、变形等。在表2中,未发现特别异常的为“good”,发现对接合强度和气密试验有影响的异常为“bad”,虽然发现了一些变形等,但判断为对质量没有大的影响的为“average”。
[0076]
另外,在表2中,作为综合评价,所有项目均为“good”评价的为“excellent”,一部分有“average”评价的为“good”,即使有一个“bad”评价也为“bad”。
[0077]
根据结果,截面积比为0.53~0.85(no.2~no.4、no.5),无论在哪个情况下,气密试验都为“good”评价,接合强度也为“average”~“good”评价。随着截面积比为0.53、0.63、0.82(no.2~no.4)的增加,接合长度增加,但在截面积比为0.85(no.6)时,与截面积比为0.82(no.4)相比,接合长度略有减少。
[0078]
另一方面,截面积比为0.43(no.1)时,气密试验为“bad”评价,调查共晶接合部时,没有形成共晶层。另外,截面积比为0.43(no.1)时,由于铜管的截面积过小,因此铜管过热和刚性不足,发现铜管变形,外观为“bad”评价。
[0079]
另外,截面积比为1.0(no.5)时,与截面积比为0.82(no.4)相比,接合长度减少。另外,与截面积比为0.82(no.4)、或截面积比为0.85(no.6)相比,在温度下降时的接合长度的减少较大,有不适合要求稳定性的批量生产的趋势。
[0080]
另外,截面积比为1.0(no.5)时,发现了一部分铝的熔融。no.6的铜管的壁厚为与no.5相同的1.0mm,但通过将铝管的壁厚增厚到1.2mm,截面积比减少,与铜管的壁厚相同的no.5相比,接合长度提高,接近no.4。另外,未发现铝管的熔融。
[0081]
由上可知,对截面积比为0.43~1.0的铜管和铝管的组合进行共晶接合,结果在截面积比为0.53~0.85的范围内,能够进行特别高质量的共晶接合。
[0082]
以上,参照附图说明了本发明的实施方式,但本发明的技术范围不限于上述实施方式。本领域技术人员能够在权利要求书的范围内所记载的技术思想的范畴内想到各种变更例或修正例,应该理解这些也自然属于本发明的技术范围。
[0083]
附图标记说明:
[0084]
1:接合体
[0085]
3:铝管
[0086]
5:铜管
[0087]
7:锥形部
[0088]
9:共晶层
[0089]
11:电源
[0090]
13:固定夹具
[0091]
15:密封部
[0092]
17:泵
[0093]
19:水槽