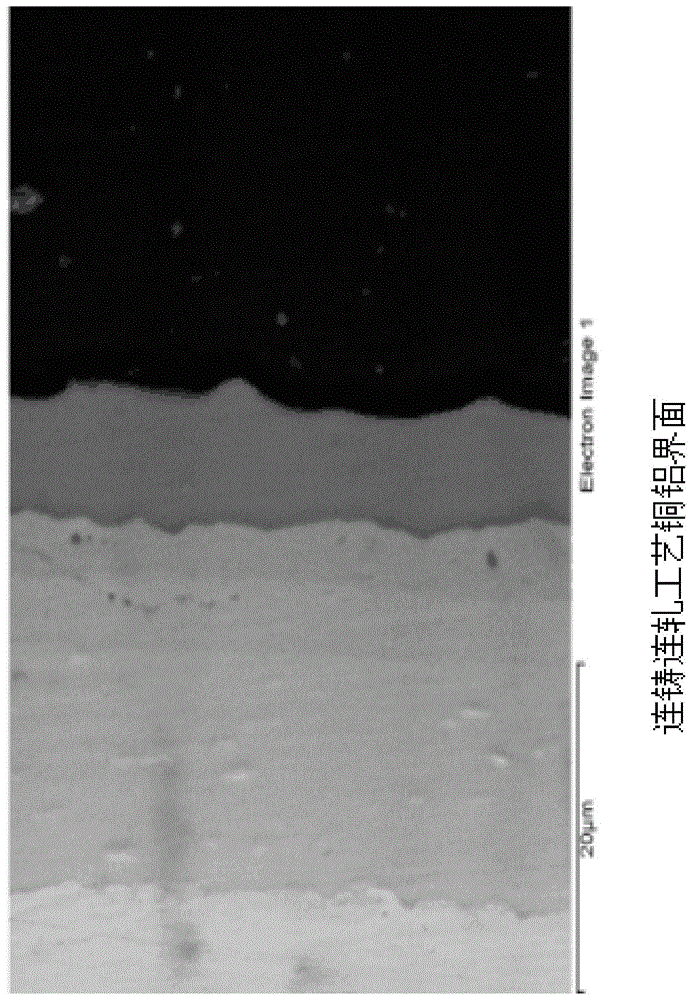
本发明涉及铝合金车体接地块
技术领域:
,特别是一种中低速磁悬浮列车方形接地块的生产方法。
背景技术:
:铜包铝复合导体是一种新型双金属复合导体,具有导电性能好、密度低、成本低等优点,其典型产品铜包铝矩形横断面复合导电母排,由于具有高的性价比,能够替代现有纯铜矩形导电母排,广泛应用于电力、母线槽、高、低压开关柜等行业。其中现有用于轻轨地铁铝合金车体上的导电接地装置的基本结构是:将铜制连接板用螺栓固定于铝合金车体上,再在铜制连接板上先用螺栓固定连接l型接地铜板,再将铜制连接板与l型接地铜板进行焊接,l型接地铜板非焊接面上钻有圆孔;例如中国专利(申请)cn200420040313.1公开了一种接地块,铜套和铝块通过铆钉连接,使用时间稍长,则铜套与铝块间形成氧化层,造成导电不良,铆钉容易松动脱落,同样也存在连接不牢固的问题;再例如,申请公布号为cn103010030a的中国专利申请,公开了一种电力机车车体接地块及其加工方法,电力机车车体接地块包括铝芯,在所述铝芯外包覆一铜层,且所述电力机车车体接地块至少一端头部的包覆铜层被铣除,露出所述铝芯,为了保证接地块与铝质车体焊接牢固,并公开了利用异型棒和异型管进行制作的具体步骤。该方法存在如下问题:由于铝芯和铜管必须采用间隙配合才能装配在一起,而间隙在之后的加工中难以完全消除,所以很难避免在使用过程中产生间隙放电腐蚀,产品性能难以保证。技术实现要素:本发明要解决的技术问题是提供一种效率高、连接牢度高、抗变形能力强的中低速磁悬浮列车方形接地块的生产方法。为解决上述技术问题,本发明提供的中低速磁悬浮列车方形接地块的生产方法,包括如下步骤:a、用水平连铸连轧方法铸造出需要的铜铝复合坯料,经过高温行星轧机轧制出铜铝复合锭相似圆形尺寸;b、将步骤a获得的铜铝复合锭锻切至所需长度,获得铜铝复合短锭,并将铜铝复合短锭通过自动传输系统进入中频电炉中进行预加热,加热温度为460℃~680℃,使铜层与铝层在瞬间加热,两种金属在瞬间进行软化;c、在氢氮混合保护气体下,将经过加热好的铜铝复合短锭利用自动密封输送平台送入具有相对的若干组上下平辊的连续轧机中进行连续温轧制,其轧制温度保持在430℃~630℃之间,轧制设备的速度设定在:80~150米/分,以获得铜铝复合坯;d、机械拉伸成型:将轧制好的铜铝复合坯进行液压拉伸直到得到铜铝复合坯体半成品;e、将拉制好的铜铝复合坯体利用驱动辊道进入冷却水槽进行校平校直,将校平校直好的铜铝复合坯体进入冷却床进行定尺锯切,将定尺锯切好的铜铝复合坯体利用驱动辊道进入涡流探伤进行无损检测;将检测好的铜铝复合坯体进行高温退火还原,退火温度为575℃-625℃,保温时间为3-5分钟;f、将退火后的铜铝复合坯体利用加工中心进行铣头及打孔,根据所需尺寸进行铣切加工,且至少一端头部的包覆铜层被铣除,以露出铝芯部分,获得方形接地块;g、表面处理:在方形接地块的表面利用锡铜合金药水表面镀锡,使得方形接地块后续与车体进行焊接时可以承受400-450℃的焊接温度。进一步,所述步骤e中,高温退火的温度为580℃,保温时间为3分钟。发明的技术效果:(1)本发明的中低速磁悬浮列车方形接地块的生产方法,相对于现有技术,铜铝复合锭采用水平连铸连轧方法制造,并经高温行星轧机轧制,无需采用铝芯和铜管的生产方式,从根本上避免铝芯与铜层之间的间隙;(2)铜铝复合坯体的校平校直在冷却水槽中进行,在校平校直的同时由冷却水槽中的冷却水进行冷却,加强了校平效果;(3)连续温轧制前进行了460℃~680℃的预热,通过该加热工序来保证铜铝晶格重组,确保产品质量,热变形的目的是降低材料的变形抗力、提高塑性,有利于后续轧制成形过程的稳定性;(4)成品热处理温度采用575℃-625℃的高温,并缩短保温时间,制定高温短时退火制度,使得方形接地块可实现铝芯来不及热透软化,而覆铜层达到相对的软化,提高了方形接地块的弯曲性能,利于后续加工;且铝芯可维持较高的硬度值,对于铝芯和覆铜层的结合强度有利;(5)在方形接地块的表面利用锡铜合金药水表面镀锡,有利于后续车体焊接中可以承受400-450℃焊接温度,保证焊接后表面光泽,接地块无发黄、变色、锡铜脱落等现象。附图说明下面结合说明书附图对本发明作进一步详细说明:图1是本发明采用连铸连轧方法获得的方形接地块的铜铝界面金相图;图2是采用固相结合方法获得的方形接地块的铜铝界面金相图。具体实施方式实施例1一种中低速磁悬浮列车方形接地块的生产方法,包括如下步骤:a、用水平连铸连轧方法铸造出需要的铜铝复合坯料,经过高温行星轧机轧制出铜铝复合锭相似圆形尺寸;b、将步骤a获得的铜铝复合锭锻切至所需长度,获得铜铝复合短锭,并将铜铝复合短锭通过自动传输系统进入中频电炉中进行预加热,加热温度为460℃~680℃,使铜层与铝层在瞬间加热,两种金属在瞬间进行软化;c、在氢氮混合保护气体下,将经过加热好的铜铝复合短锭利用自动密封输送平台送入具有相对的若干组上下平辊的连续轧机中进行连续温轧制,其轧制温度保持在430℃~630℃之间,轧制设备的速度设定在:80米/分,以获得铜铝复合坯;d、机械拉伸成型:将轧制好的铜铝复合坯进行液压拉伸直到得到铜铝复合坯体半成品;e、将拉制好的铜铝复合坯体利用驱动辊道进入冷却水槽进行校平校直,将校平校直好的铜铝复合坯体进入冷却床进行定尺锯切,将定尺锯切好的铜铝复合坯体利用驱动辊道进入涡流探伤进行无损检测;将检测好的铜铝复合坯体进行高温退火还原,退火温度为580℃,保温时间为3分钟;f、将退火后的铜铝复合坯体利用加工中心进行铣头及打孔,根据所需尺寸进行铣切加工,且至少一端头部的包覆铜层被铣除,以露出铝芯部分,获得方形接地块;g、表面处理:在方形接地块的表面利用锡铜合金药水表面镀锡,使得方形接地块后续与车体进行焊接时可以承受400-450℃的焊接温度。该方法获得的方形接地块进行了剥离强度检测和铝芯、覆铜层的硬度检测,具体结果参见表1。实施例2一种中低速磁悬浮列车方形接地块的生产方法,包括如下步骤:a、用水平连铸连轧方法铸造出需要的铜铝复合坯料,经过高温行星轧机轧制出铜铝复合锭相似圆形尺寸;b、将步骤a获得的铜铝复合锭锻切至所需长度,获得铜铝复合短锭,并将铜铝复合短锭通过自动传输系统进入中频电炉中进行预加热,加热温度为460℃~680℃,使铜层与铝层在瞬间加热,两种金属在瞬间进行软化;c、在氢氮混合保护气体下,将经过加热好的铜铝复合短锭利用自动密封输送平台送入具有相对的若干组上下平辊的连续轧机中进行连续温轧制,其轧制温度保持在430℃~630℃之间,轧制设备的速度设定在:100米/分,以获得铜铝复合坯;d、机械拉伸成型:将轧制好的铜铝复合坯进行液压拉伸直到得到铜铝复合坯体半成品;e、将拉制好的铜铝复合坯体利用驱动辊道进入冷却水槽进行校平校直,将校平校直好的铜铝复合坯体进入冷却床进行定尺锯切,将定尺锯切好的铜铝复合坯体利用驱动辊道进入涡流探伤进行无损检测;将检测好的铜铝复合坯体进行高温退火还原,退火温度为580℃,保温时间为5分钟;f、将退火后的铜铝复合坯体利用加工中心进行铣头及打孔,根据所需尺寸进行铣切加工,且至少一端头部的包覆铜层被铣除,以露出铝芯部分,获得方形接地块;g、表面处理:在方形接地块的表面利用锡铜合金药水表面镀锡,使得方形接地块后续与车体进行焊接时可以承受400-450℃的焊接温度。该方法获得的方形接地块进行了剥离强度检测和铝芯、覆铜层的硬度检测,具体结果参见表1。实施例3一种中低速磁悬浮列车方形接地块的生产方法,包括如下步骤:a、用水平连铸连轧方法铸造出需要的铜铝复合坯料,经过高温行星轧机轧制出铜铝复合锭相似圆形尺寸;b、将步骤a获得的铜铝复合锭锻切至所需长度,获得铜铝复合短锭,并将铜铝复合短锭通过自动传输系统进入中频电炉中进行预加热,加热温度为460℃~680℃,使铜层与铝层在瞬间加热,两种金属在瞬间进行软化;c、在氢氮混合保护气体下,将经过加热好的铜铝复合短锭利用自动密封输送平台送入具有相对的若干组上下平辊的连续轧机中进行连续温轧制,其轧制温度保持在430℃~630℃之间,轧制设备的速度设定在:120米/分,以获得铜铝复合坯;d、机械拉伸成型:将轧制好的铜铝复合坯进行液压拉伸直到得到铜铝复合坯体半成品;e、将拉制好的铜铝复合坯体利用驱动辊道进入冷却水槽进行校平校直,将校平校直好的铜铝复合坯体进入冷却床进行定尺锯切,将定尺锯切好的铜铝复合坯体利用驱动辊道进入涡流探伤进行无损检测;将检测好的铜铝复合坯体进行高温退火还原,退火温度为620℃,保温时间为3分钟;f、将退火后的铜铝复合坯体利用加工中心进行铣头及打孔,根据所需尺寸进行铣切加工,且至少一端头部的包覆铜层被铣除,以露出铝芯部分,获得方形接地块;g、表面处理:在方形接地块的表面利用锡铜合金药水表面镀锡,使得方形接地块后续与车体进行焊接时可以承受400-450℃的焊接温度。该方法获得的方形接地块进行了剥离强度检测和铝芯、覆铜层的硬度检测,具体结果参见表1。对比例1一种中低速磁悬浮列车方形接地块的生产方法,包括如下步骤:a、用水平连铸连轧方法铸造出需要的铜铝复合坯料,经过高温行星轧机轧制出铜铝复合锭相似圆形尺寸;b、将步骤a获得的铜铝复合锭锻切至所需长度,获得铜铝复合短锭,并将铜铝复合短锭通过自动传输系统进入中频电炉中进行预加热,加热温度为460℃~680℃,使铜层与铝层在瞬间加热,两种金属在瞬间进行软化;c、在氢氮混合保护气体下,将经过加热好的铜铝复合短锭利用自动密封输送平台送入具有相对的若干组上下平辊的连续轧机中进行连续温轧制,其轧制温度保持在430℃~630℃之间,轧制设备的速度设定在:80米/分,以获得铜铝复合坯;d、机械拉伸成型:将轧制好的铜铝复合坯进行液压拉伸直到得到铜铝复合坯体半成品;e、将拉制好的铜铝复合坯体利用驱动辊道进入冷却水槽进行校平校直,将校平校直好的铜铝复合坯体进入冷却床进行定尺锯切,将定尺锯切好的铜铝复合坯体利用驱动辊道进入涡流探伤进行无损检测;将检测好的铜铝复合坯体进行高温退火还原,退火温度为350℃,保温时间为120分钟;f、将退火后的铜铝复合坯体利用加工中心进行铣头及打孔,根据所需尺寸进行铣切加工,且至少一端头部的包覆铜层被铣除,以露出铝芯部分,获得方形接地块;g、表面处理:在方形接地块的表面利用锡铜合金药水表面镀锡,使得方形接地块后续与车体进行焊接时可以承受400-450℃的焊接温度。该方法获得的方形接地块进行了剥离强度检测和铝芯、覆铜层的硬度检测,具体结果参见表1。对比例2一种中低速磁悬浮列车方形接地块的生产方法,包括如下步骤:a、用水平连铸连轧方法铸造出需要的铜铝复合坯料,经过高温行星轧机轧制出铜铝复合锭相似圆形尺寸;b、将步骤a获得的铜铝复合锭锻切至所需长度,获得铜铝复合短锭,并将铜铝复合短锭通过自动传输系统进入中频电炉中进行预加热,加热温度为460℃~680℃,使铜层与铝层在瞬间加热,两种金属在瞬间进行软化;c、在氢氮混合保护气体下,将经过加热好的铜铝复合短锭利用自动密封输送平台送入具有相对的若干组上下平辊的连续轧机中进行连续温轧制,其轧制温度保持在430℃~630℃之间,轧制设备的速度设定在:80米/分,以获得铜铝复合坯;d、机械拉伸成型:将轧制好的铜铝复合坯进行液压拉伸直到得到铜铝复合坯体半成品;e、将拉制好的铜铝复合坯体利用驱动辊道进入冷却水槽进行校平校直,将校平校直好的铜铝复合坯体进入冷却床进行定尺锯切,将定尺锯切好的铜铝复合坯体利用驱动辊道进入涡流探伤进行无损检测;将检测好的铜铝复合坯体进行高温退火还原,退火温度为580℃,保温时间为10分钟;f、将退火后的铜铝复合坯体利用加工中心进行铣头及打孔,根据所需尺寸进行铣切加工,且至少一端头部的包覆铜层被铣除,以露出铝芯部分,获得方形接地块;g、表面处理:在方形接地块的表面利用锡铜合金药水表面镀锡,使得方形接地块后续与车体进行焊接时可以承受400-450℃的焊接温度。该方法获得的方形接地块进行了剥离强度检测和铝芯、覆铜层的硬度检测,具体结果参见表1。对比例3一种中低速磁悬浮列车方形接地块的生产方法,包括如下步骤:a、用水平连铸连轧方法铸造出需要的铜铝复合坯料,经过高温行星轧机轧制出铜铝复合锭相似圆形尺寸;b、将步骤a获得的铜铝复合锭锻切至所需长度,获得铜铝复合短锭,并将铜铝复合短锭通过自动传输系统进入中频电炉中进行预加热,加热温度为460℃~680℃,使铜层与铝层在瞬间加热,两种金属在瞬间进行软化;c、在氢氮混合保护气体下,将经过加热好的铜铝复合短锭利用自动密封输送平台送入具有相对的若干组上下平辊的连续轧机中进行连续温轧制,其轧制温度保持在430℃~630℃之间,轧制设备的速度设定在:80米/分,以获得铜铝复合坯;d、机械拉伸成型:将轧制好的铜铝复合坯进行液压拉伸直到得到铜铝复合坯体半成品;e、将拉制好的铜铝复合坯体利用驱动辊道进入冷却水槽进行校平校直,将校平校直好的铜铝复合坯体进入冷却床进行定尺锯切,将定尺锯切好的铜铝复合坯体利用驱动辊道进入涡流探伤进行无损检测;将检测好的铜铝复合坯体进行高温退火还原,退火温度为675℃,保温时间为3分钟;f、将退火后的铜铝复合坯体利用加工中心进行铣头及打孔,根据所需尺寸进行铣切加工,且至少一端头部的包覆铜层被铣除,以露出铝芯部分,获得方形接地块;g、表面处理:在方形接地块的表面利用锡铜合金药水表面镀锡,使得方形接地块后续与车体进行焊接时可以承受400-450℃的焊接温度。该方法获得的方形接地块进行了剥离强度检测和铝芯、覆铜层的硬度检测,具体结果参见表1。表1退火后方形接地块的剥离强度和硬度值序号实施例1实施例2实施例3对比例1对比例2对比例3退火温度580580620350580675保温时间353120103cu硬度值(hv)85.080.176.664.263.461.8al硬度值(hv)45.440.243.238.936.539.4剥离力(n/m)1236111195104099534779510209由表1可知,采用575至625℃、保温时间3至5分钟的高温短时退火工艺获得的方形接地块,在剥离强度和硬度值都十分优异,是最佳的热处理工艺;同时由说明附图1的金相照片可以看出,采用连铸连轧方法获得的方形接地块在铜铝界面处铜和铝的成分出现明显阶梯现象,说明形成了金属间化合物,从而保证界面的结合强度;作为对比,说明书附图2是采用固相结合工艺制得的方形接地块,其铜铝界面处较为突兀,无明显结合现象。显然,上述实施例仅仅是为清楚地说明本发明所作的举例,而并非是对本发明的实施方式的限定。对于所属领域的普通技术人员来说,在上述说明的基础上还可以做出其它不同形式的变化或变动。这里无需也无法对所有的实施方式予以穷举。而这些属于本发明的精神所引申出的显而易见的变化或变动仍处于本发明的保护范围之中。当前第1页12