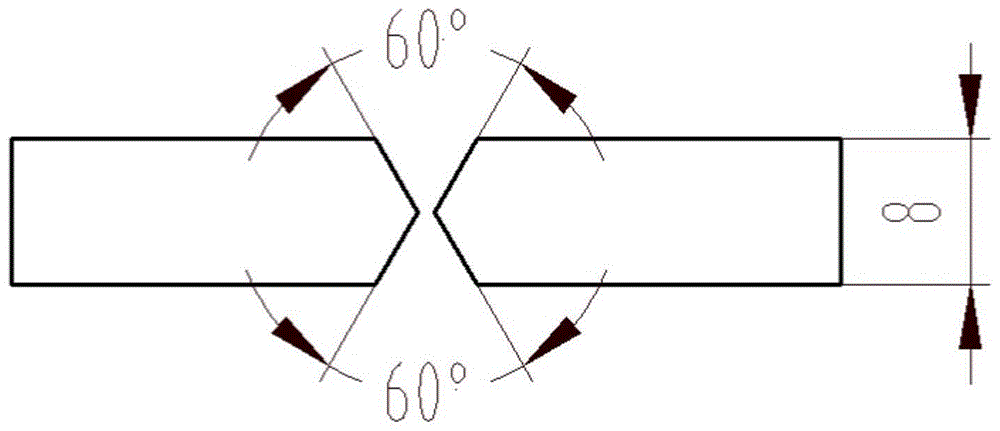
本发明涉及一种屈服强度≧1250mpa的超高强钢板焊接工艺,属于超高强度钢材焊接
技术领域:
。
背景技术:
:低合金高强度钢板主要应用于机械装备制造,为了提高中国机械制造行业的整体水平和市场竞争力,满足工程机械大型化、轻量化发展需求,迫切需要大量的优质高强度超厚钢板。目前,钢厂已经成功研发出强度超过1250mpa的超高强度钢板,钢板各项性能优异,但存在以下焊接问题:首先,可焊性较差,焊接后易于产生焊接冷裂纹,同时由于强度较高,对应的预热温度不能过高,否则会造成钢板强度的严重降低,但超高强钢冷裂纹敏感性要求预热温度尽可能的高,这种矛盾给焊接工作者带来了巨大的挑战。其次,焊接热输入的控制非常严格,热输入过高,会造成热影响区软化严重,进而严重降低了接头的强度;热输入过低,会造成焊缝成型不好,甚至会造成无法施焊的情况。最后,一般超高强钢板壁厚相对较薄,焊接后试板变形严重,焊接试板翘曲和弯曲现象时有发生。技术实现要素:本发明所要解决的技术问题是针对上述现有技术提供一种屈服强度≧1250mpa的超高强钢板焊接工艺,不仅提高可焊性焊接,避免焊后产生焊接冷裂纹,而且焊接接头变形小。本发明解决上述问题所采用的技术方案为:一种屈服强度≧1250mpa的超高强钢板焊接工艺,包括如下步骤:步骤一:小铁研试验,确定超高强钢的焊前预热温度,即抗冷裂纹敏感温度;步骤二:根据小铁研试验得出焊接试板的预热温度,焊接试板坡口加工成x型,对焊接试板进行整体预热;步骤三:出炉后将相同板厚的焊接试板进行对接,在试板两端加装引弧板和熄弧板,选用富氩气气体作为保护气体,采用焊丝进行正、反焊接;步骤四:焊后检查和探伤,焊后进行肉眼观察,观察焊缝成型性能,同时留意可见气孔缺陷;并进行超声波探伤,标出焊接缺陷部位,取样时避开。所述焊接试板的厚度为4~10mm。所述步骤二中,焊接试板在预热之前经过如下预处理:焊接试板对接接头处开双面对称x型坡口,所述坡口角度为60°,无钝边,并清理坡口表面;对待焊区域20mm范围内的铁锈、氧化皮、油污和脏污清除干净。所述步骤三中,对接接头的间隙为0~1mm,错边量≤0.5mm。设计所述焊接试板的反变形角度为10°~30°。在所述步骤三中,所述焊丝为奥氏体不锈钢mig,chm-307si;控制焊道层间和道间温度≤150℃,焊接线能量控制在8~12kj/cm。所述步骤三中,施焊过程中正面焊:焊接电流为125±10a,焊接电压为16±1v,焊接速度:13.9cm/min,焊接线能量为9±1kj/cm;反面焊:焊接电流为165±10a,焊接电压为20±1v,焊接速度为19.3±1cm/min,焊接线能量为10±1kj/cm。对所述焊接试板进行反面焊前,对焊接试板背面进行碳弧气刨清根。所述步骤三焊接过程的每一道次焊完,对焊缝进行打磨、消除毛刺。所述步骤三焊接过程中焊接线能量的实际输入值和工艺值波动范围控制在±1kj/cm。与现有技术相比,本发明的优点在于:一种屈服强度≧1250mpa的超高强钢板焊接工艺,采用对接方式进行焊接,通过选取奥氏体不锈钢mig焊丝、小铁研试验得出焊接试板的预热温度、设计合理的焊接工艺参数和严格控制焊接过程,不仅可焊性强,焊后焊缝具有良好的塑韧性和抗裂性能,而且焊接接头变形小、无焊接缺陷。附图说明图1为焊接试板坡口的示意图;图2为焊接接头显微硬度示意图;具体实施方式以下结合附图实施例对本发明作进一步详细描述。本实施例中的一种屈服强度≧1250mpa的超高强钢板焊接工艺,其中,超高强钢板的化学成分重量百分比如下:c:0.2~0.5;si:0.1~0.4;mn:0.5~1.4;p:≤0.015;s:≤0.01;cr:0.5~0.8;mo:0.4~0.9;ni:0.2~0.8;其余为fe;超高强钢板的壁厚为8mm,本实施例焊接工艺如下:1)焊材选择:考虑到该钢板焊接的构件焊缝区域承载力较小的特点,选用奥氏体不锈钢mig焊丝,chm-307si,采用该焊材焊接的接头冷裂纹敏感性将大幅降低,提高了可焊性。采用直流反接,焊缝成型细且光亮,飞溅小而少,焊缝具有良好的塑韧性和抗裂性能。2)小铁研试验:由于本钢属于超高强钢,裂纹敏感性强,需要执行严格的焊前预热,通过小铁研试验摸索焊前预热温度(抗冷裂纹敏感温度)。参照标准gb/t32260.2-2015《金属材料焊缝的破坏性试验焊件冷裂纹试验弧焊方法》,小铁研试验采用的预热温度分别为:室温、40℃、80℃和100℃四个温度。通过测定,以上四个温度下裂纹率均为0。本实施例中选取室温为焊接试板的预热温度。3)焊接试板坡口加工如图1所示,由于焊接试板的壁厚较薄,采用对称焊接,以确保焊接后焊接接头附近应力分布均匀,降低焊接后试板翘曲或弯曲风险。在焊接前,焊接试板对接接头处开双面对称x型坡口,坡口角度为60°,无钝边。4)待焊区域清理在焊前将坡口、对待焊区域20mm范围及待焊部位的表面铁锈、氧化皮、油污和脏污等清除干净。5)焊接试板组对将焊接试板进行组对,使得对接接头间隙为0.5mm,错边量为0.2mm;在焊接试板两端加装引弧板和熄弧板。考虑到焊接试板壁厚较薄,且强度较高,焊接后产生严重的变形,焊前会设计合理的反变形角度。根据本实施例焊接试板的壁厚为8mm,焊接试板的反变形为角度15°,减小焊接接头变形。6)焊接工艺参数采用富氩气气体保护焊(80%ar+20%co2);如表1所示,正面焊:焊接电流:125a;焊接电压:16.5v;焊接速度:13.9cm/min;焊接线能量:8.88kj/cm;反面焊:焊接电流:165a;焊接电压:20v;焊接速度:19.3cm/min;热输入控制在:10.26kj/cm。焊接时控制层间和道间温度≤150℃,背面焊前用碳弧气刨清根,后按照表1工艺进行焊接。表1为焊接工艺参数焊接位置电流a电压v速度cm/min线能量kj/cm保护气体预热情况反面焊12516.513.98.8880%ar+20%co2无预热正面焊1652019.310.2680%ar+20%co2无预热8)焊后检查和探伤焊后首先进行肉眼观察,观察焊缝成型性能,同时留意是否有可见气孔缺陷等;然后进行超声波探伤,标出焊接缺陷部位,取样时避开。在焊接时,需要对焊接过程进行控制:a)按照小铁研试验摸索的预热温度区间,采用安全区间内温度预热,为了保证充分预热,加热炉对待焊试板整体加热。b)焊接过程中,对焊接线能量的把握需要计算控制精确,线能量的实际输入值和工艺值会有波动,本申请的线能量实际输入值和工艺值之间的波动范围控制在±1kj/cm。c)焊接过程中,每一道次焊完都需要打磨消除毛刺,避免产生焊接缺陷。如图2所示,从焊接接头显微硬度看,热影响区软化不明显,说明所选的焊接工艺中线能量适中。采用chm-307si焊丝进行施焊形成奥氏体焊缝,既起到连接作用,又对母材或热影响区无大影响,焊接后对焊接接头强度影响不大,且力学性能指标优异,如下表二、表三所示。表2焊接接头拉伸性能表3焊接接头低温冲击韧性本申请采用对接方式进行焊接,通过选取合理的焊材、小铁研试验得出的预热温度、设计合理的焊接工艺参数和严格控制焊接过程,不仅可焊性强,焊后焊缝具有良好的塑韧性和抗裂性能,而且焊接接头变形小、无焊接缺陷。除上述实施例外,本发明还包括有其他实施方式,凡采用等同变换或者等效替换方式形成的技术方案,均应落入本发明权利要求的保护范围之内。当前第1页12