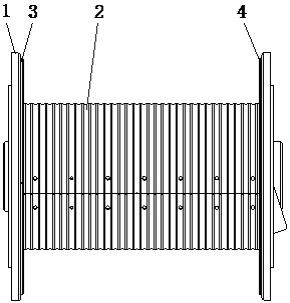
1.本发明涉及石油钻采机械设备技术领域,具体涉及一种分体剖开式结构滚筒的制造方法。
背景技术:2.石油钻机所配绞车是提升系统关键设备,绞车安装有开槽整体滚筒,绳槽在筒体上直接加工,使用过程中,绳槽及轮毂磨损后滚筒需更换,滚筒与轴过盈配合,热装,拆卸时采用液压压力机压出滚筒轴,绞车体积大、质量重,绞车需要拆下运到机修厂解体后方可更换,造成钻机长时间停用、增加维修成本和安全事故风险,对于在偏远山区、荒漠、戈壁滩、岛上或海上钻井平台,维修工期更长,费用和风险更大。
3.现有技术中,分体式结构滚筒是滚筒体和绳槽板分离,由滚筒体、绳槽板和挡板组成。绳槽板有两种制造方法,一种是将两端凸台单独加工后与槽主体焊接成活,另一种是在绳槽板主体两端沿槽焊接等同钢丝绳直径的圆钢后平端面成活,安装时绳槽板两端与滚筒体焊死。两端挡板也有两种制造方法,一种是加工螺孔,利用沉头螺钉连接滚筒体轮毂,挡板厚度有限,挡板磨损后,螺钉头与钢丝绳直接摩擦,一种是分成多块式,容易加工和表面硬度处理,由于数量多,焊接方位多,安装、更换时拼接、调整困难。
技术实现要素:4.为了克服现有技术中的不足,本发明提供了一种分体剖开式结构滚筒的制造方法,所述滚筒由滚筒体、左挡板、右挡板、绳槽板组成,滚筒体重复利用,绳槽板和挡板作为易损件可拆卸,滚筒体由左右轮毂和筒身组焊,轮毂上铸造出入绳口和配重,绳槽板绳槽和两端凸台一体加工,加工后切割成两件,绳槽板与滚筒体采用塞焊结构连接,挡板为下料件,呈剖分结构,入绳口配割,挡板外圆与轮毂断续焊。
5.作为上述方案的优选,所述左、右轮毂采用铸件,筒身毛坯采用铸件或管材下料或钢板卷制,轮毂、筒身先粗加工,与轮毂采用u型焊缝连接,焊缝经失效处理及无损检测,然后整体精加工。
6.作为上述方案的优选,所述绳槽板毛坯采用铸件或管材下料或钢板卷制,铸造毛坯的两端凸台铸造成型,管材下料或钢板卷制方法制作毛坯时,两端凸台采用厚板材下料,采用u形焊缝焊接。
7.作为上述方案的优选,所述绳槽板采用数控车床数控编程加工,绳槽板毛坯粗加工后分左、中、右三段进行精加工,平两端面,加工入绳口,最后在绳槽直段对称剖切成两件。
8.作为上述方案的优选,所述绳槽板加工时,定好基准,按左端绳槽、中间绳槽、右端绳槽顺序加工,采用不同程序,用尖刀、小半径圆弧车刀、圆弧成型车刀进行扎槽、修槽、车槽,按不同的吃刀量、车床转速分多次加工,加工过程中采用不同样板验证不同角度位置的绳槽,两端凸台按爬坡或换向段、直段、斜段分段加工,入绳口位置槽型按虚拟反向爬坡段
加工,再加工入绳口,入绳口加工在铣床上完成,基点位于斜段结束直段起点,先从基点向后外侧一定角度铣出缺口,缺口位于斜段末端,呈三角形,然后将直段的虚拟的爬坡段加工出所需槽型,绳槽板平两端面,修正凸台槽型宽度,达到凸台槽中心至端面距离为钢丝绳公称直径的一半,绳槽板距离切缝一定尺寸处沿轴向等距离加工数量的光孔和螺孔,光孔为绳槽板与筒身连接的塞焊孔,螺孔为顶丝孔。
9.作为上述方案的优选,所述绳槽板在半自动数控切割机上切割,切割前在两端钻两个通孔,作为切割起始点和终止点,绳槽板装夹在滚轮架上,沿轴向以一定速度切割,端面至切割起始点和终止点段不切开,待冷却后,手动切割。
10.作为上述方案的优选,所述左挡板和右挡板采用与挡板厚度相同的高强度板材下料,只加工内外圆,贴紧轮毂一侧内孔加工大于焊缝高度的倒角。
11.作为上述方案的优选,所述滚筒组装时,对齐轮毂、绳槽板、挡板入绳口基点进行预装,调整好角度和开档间隙后,将右挡板取出配割入绳口,重新组装并调整好后焊接挡板,打磨绳槽板入绳口和挡板棱角。
12.本发明的优点和技术效果有:1. 绳槽板和挡板采用剖分结构,可拆卸,磨损后现场进行更换,降低维修难度和拆装风险,缩短停机时间,节约成本,更换工艺简单,对设备无损害,所需机具和人员少。2. 滚筒体和绳槽板采用全数控加工,使用中,滚筒排绳整齐。
附图说明
13.图1为分体剖开式结构滚筒结构示意图。
14.图2为分体剖开式结构滚筒展开示意图。
15.图中1.滚筒体,2.绳槽板,3.左挡板,4.右挡板,5.左轮毂,6.右轮毂,7.筒身。
具体实施方式
16.以下结合附图详细描述本发明的实施例。
17.如图1至图2所示,本实施例的滚筒组成为滚筒体1、绳槽板2、左挡板3、右挡板4,其中,滚筒体1由左轮毂5、右轮毂6、筒身7组成,滚筒体1直接安装在滚筒轴上。
18.本实施例中,滚筒体1由左轮毂5、右轮毂6和筒身7焊接成一个整体加工,绳槽板2整体加工后剖切成两件,左挡板3、右挡板4成活后分别对称剖切,入绳口配割,绳槽板2利用光孔与滚筒体1塞焊连接,左挡板3、右挡板4安装时外圆与轮毂断续焊。
19.本实施例中,滚筒体1制造主要工序是:左轮毂5、右轮毂6、筒身7粗加工后焊接成滚筒体1,失效处理后,滚筒体1进行精加工,绳槽板2制造工序是:毛坯粗加工,按左绳槽、中间绳槽、右绳槽顺序精加工,钻孔,平断面,铣入绳口,切割,失效处理,挡板制作主要工序为:下料,校平,除锈处理,车内外圆,切割,装配主要工序为:滚筒体1、绳槽板2、左挡板3、右挡板4安装预调整好后,绳槽板2塞焊在滚筒体1上,右挡板4取出配开入绳口后回装,左挡板3和右挡板4外圆断续焊,打磨入绳口及焊缝。
20.本实施例中,轮毂采用合金铸件,右轮毂6铸造有入绳口及配重,入绳口底径与绳槽底径相同,筒身7毛坯采用合金铸件或管材下料或钢板卷制,左轮毂5、右轮毂6、筒身7先粗加工,采用u型焊缝对接,焊缝应力失效处理及无损检测,焊接完后整体精加工。
21.本实施例中,绳槽板2毛坯采用铸件或管材下料或钢板卷制,绳槽板2是中间段直径一致,左凸台、右凸台直径大于中间部分,铸造毛坯两端的凸台直接铸造成型,管材下料或钢板卷制方法制作毛坯时,两端凸台采用厚板材下料,中间部分选用管材下料或钢板卷制,用u形焊缝焊接成一体,毛坯制作完成后做相应的热处理。
22.本实施例中,绳槽板2加工采用大型数控车床数控编程加工,毛坯粗加工,然后分左、中、右三段进行编程精加工,整个绳槽加工成型后平两端面,在铣床上加工入绳口,完成机加工序后,采用数控切割机对称剖切成两件,并进行应力失效处理,绳槽加工时,定好基准,按左绳槽、中间绳槽、右绳槽顺序,各段采用不同程序加工,加工采用尖刀、小半径圆弧车刀、圆弧成型车刀进行扎槽、修槽、车槽,依据吃刀量、车床转速分多次加工,保证表面精度,加工过程中采用不同样板验证不同角度位置的绳槽,两端凸台按爬坡或换向段、直段、斜段分段加工,基点位于斜段结束直段起点,入绳口位置槽型按虚拟反向爬坡段加工,再进行入绳口加工,先从入绳口起始位置向后外侧倾斜一定角度铣出缺口,缺口位于斜段末端,呈三角形,然后再将虚拟的爬坡段按实际轨迹加工出所需槽型,清除毛刺,绳槽板2平两端端面,修正凸台槽宽度,达到凸台绳槽中心线至端面距离刚好为钢丝绳公称直径的一半,并控制精度,绳槽板2距切缝一定尺寸处沿轴向等距离加工数量光孔和螺孔,光孔为绳槽板2与筒身7连接的塞焊孔,螺孔为吊装孔和顶丝孔。
23.本实施例中,绳槽板2在半自动数控切割机上对称切割成两件,切割前先在距两端面一定尺寸处钻两个通孔,作为切割起始点和终止点,绳槽板2装夹在滚轮架工装上,利用半自动数控切割机沿轴向以一定速度切割,切割必须满足设计的切缝大小、对称度和直线度。端面至切割起始点和终止点段不切开,待冷却后,手动气割,角磨机打磨。
24.本实施例中,左挡板3和右挡板4采用与挡板厚度尺寸相同的对应强度的高强度板材下料,校平、除锈,只内外圆加工,贴紧滚筒体轮毂一边的内孔加工大倒角,其余不加工,表面不做硬度处理,成型后对称剖切成两件。
25.本实施例中,滚筒组装时,首先对齐右轮毂6、绳槽板2、左挡板3、右挡板4入绳口基点,然后预装,调整角度和开档间隙,再将右挡板4取出配割入绳口,重新组装并调整好后焊接左挡板3和右挡板4外圆,修磨入绳口后完成组装。
26.本实施例中,滚筒组装时,绳槽板2缺口和右挡板4棱角进行适当打磨,无凸点、尖棱角,保证钢丝绳穿过右轮毂6入绳口后能顺利沿绳槽绕绳,无死弯、扭曲、割绳现象。绳槽板2、左挡板3、右挡板4组装时,两件切缝间隙调整均匀。
27.本实施例中,滚筒组装时,开档间隙由滚筒体1、绳槽板2、左挡板3、右挡板4总的公称尺寸零配合,累计负公差作为安装间隙,挡板与滚筒体1轮毂之间必要时可加垫片调整。
28.本实施例中,左挡板3、右挡板4安装时,插入绳槽板2和滚筒体1轮毂之间,紧贴绳槽板端面,挡板外圆与轮毂断续焊接。
29.本实施例中,滚筒使用后,因磨损需更换绳槽板2、左挡板3、右挡板4,取出左挡板3、右挡板4时将外圆焊缝刨掉,即可抽出,绳槽板2取出前先将塞焊孔的焊缝利用电钻钻掉,然后用顶丝顶出。
30.本实施例做如下说明:绳槽板的加工重点是程序的编制和多种刀具的使用,吃刀量、加工精度是关键,斜段部分与直段部分圆滑过渡,爬坡段爬坡均匀、平顺,利用绳槽样板验证时,圆弧面贴实,无缝
隙,绳槽板平断面时,薄壁换向凸台不能损坏和变形,可适当修磨尖角和毛刺,绳槽板入绳口保留一定尺寸的绳槽最高段,入绳口基点位于斜段结束直段起点处。
31.切割工序控制点是避免切割开后应力释放导致的变形。
32.挡板平整,原材料除锈后厚度均匀,满足设计尺寸。
33.组装的关键点是滚筒体、绳槽板、右挡板入绳口基点对齐,间隙均匀。