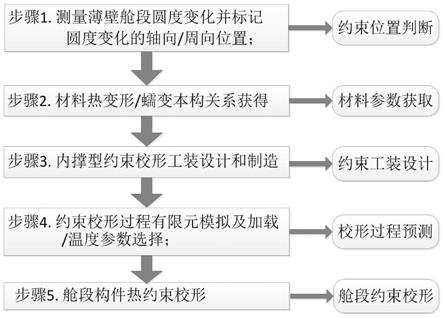
[0001]
本发明属于热处理变形控制领域,特别是涉及一种铝镁合金薄壁舱段制造变形的校形方法。
背景技术:[0002]
舱段类构件是航空航天装备的主承载构件,是飞行器高效、可靠服役的重要基础。为了实现凸台、复杂筋板等复杂结构的精确制造,达成高效承载的设计目标,舱段类构件大量使用镁合金、铝合金薄壁铸件作为坯件、以机加工方法进行制造。受镁合金/铝合金性能特点及制造过程的复杂性决定,舱段类构件在制造过程中容易发生形状畸变并导致变形超差、无法装配甚至服役性能退化。统计表明,舱段类构件的变形问题较为普遍、主要变形形式为圆度畸变;分析表明,舱段圆度畸变原因十分复杂,铸件冷却、固溶淬火和时效处理等工艺过程均会诱发圆度畸变。鉴于上述统计和分析,在热处理过程中施加载荷对构件进行靶向约束是实现形状校正和保持最有效的技术措施。
[0003]
舱段类构件约束校形的实现的基础是在应力-温度适当施加的基础上实现蠕变过程精确预测和控制。为此,需要建立涵盖“形状畸变测量-应力可控施加-材料蠕变行为控制”全过程的方法。
技术实现要素:[0004]
本发明为了解决现有技术中的问题,提出一种铝镁合金薄壁舱段制造变形的校形方法。
[0005]
为实现上述目的,本发明采用以下技术方案:一种铝镁合金薄壁舱段制造变形的校形方法,它包括以下步骤:
[0006]
步骤1:通过三维轮廓仪对舱段构件外廓进行测量,形成舱段构件外轮廓的数模,将舱段构件外轮廓的数模与理想舱段数模进行三维比对,获得圆度变化的空间分布;
[0007]
步骤2:通过热模拟实验和蠕变试验获得舱段构件的材料变形和蠕变本构关系;
[0008]
步骤3:根据步骤1中得到的舱段构件外轮廓的数模设计和制造内撑工装,对舱段构件的变形位置进行可调节约束;
[0009]
步骤4:建立有限元仿真平台,根据步骤2中得到的数据对约束热处理过程中应力分布、应力-蠕变演化以及卸载回弹进行系统的预测,基于仿真平台的系统试算进行加载位置和加载强度的选择;
[0010]
步骤5:基于仿真平台的结果确定约束位置、约束强度进行舱段构件与内撑工装的组装和锁紧,之后将舱段构件与内撑工装同时放入热处理炉进行热处理。
[0011]
更进一步的,所述步骤1中通过轴向不同位置测定径向轮廓,从而选定约束加载位置。
[0012]
更进一步的,所述约束加载位置为舱段构件变形量最大的位置。
[0013]
更进一步的,所述步骤2中通过选用相同热处理状态的合金进行热模拟实验和蠕
变试验得到系列化的应力应变曲线,并从中计算获得合金的变形和蠕变本构关系。
[0014]
更进一步的,所述步骤4中选定轴向位置以及径向顶正的位置,并在有限元仿真系统中建立舱段构件与内撑工装组合体的模型,对舱段构件与内撑工装组合体中各径向位置加载过程以及舱段构件与内撑工装组合体温升过程进行仿真,获得应力、应变与的温度分布,模拟舱段构件中应力和应变的变化并对卸载回弹进行预测;基于回弹预测对加载位置、加载强度和温度进行调整。
[0015]
更进一步的,所述步骤5中热处理结束后自然冷却至室温,拆除内撑工装,检查舱段构件内腔截面的圆度尺寸。
[0016]
更进一步的,所述内撑工装为平面四向或平面六向均匀分布自对顶结构,在轴向根据校形需要进行多层纵列组装。
[0017]
更进一步的,所述内撑工装包括顶块、中心环和安装螺栓,所述顶块通过安装螺栓与中心环相连。
[0018]
与现有技术相比,本发明的有益效果是:本发明解决了现有铝镁合金薄壁舱段制造过程中的变形问题。本发明在舱段构件中施加载荷可调的约束,可以同时实现控制热处理过程的变形和对已有变形的校正,可实现铝镁合金舱段的精确制造,显著提高该类构件制造效率,基于热处理过程控制的实现舱段圆度畸变的控制和校正。采用的内撑工装轴向位置可调节、轴向可旋转、径向位移可调,因此可以实现约束位置、约束强度的灵活调控。
附图说明
[0019]
图1为本发明所述的一种铝镁合金薄壁舱段制造变形的校形方法流程图;
[0020]
图2为本发明所述的一种铝镁合金薄壁舱段制造变形的校形方法技术构成图;
[0021]
图3为本发明所述的舱段构件与内撑工装组装状态结构示意图;
[0022]
图4为本发明所述的内撑工装结构示意图;
[0023]
图5为本发明所述的舱段构件选定位置径向载荷—校形位移曲线图;
[0024]
图6为本发明所述的不同温度下校形时舱段构件的塑性变形。
[0025]
1-舱段构件,2-内撑工装,3-顶块,4-中心环,5-安装螺栓。
具体实施方式
[0026]
下面将结合本发明实施例中的附图,对本发明实施例中的技术方案进行清楚、完整地阐述。
[0027]
参见图1-6说明本实施方式,一种铝镁合金薄壁舱段制造变形的校形方法,它包括以下步骤:
[0028]
步骤1:通过三维轮廓仪对舱段构件1外廓进行测量,形成舱段构件1外轮廓的数模,将舱段构件1外轮廓的数模与理想舱段数模进行三维比对,获得圆度变化的空间分布;
[0029]
步骤2:通过热模拟实验和蠕变试验获得舱段构件1的材料变形和蠕变本构关系;
[0030]
步骤3:根据步骤1中得到的舱段构件1外轮廓的数模设计和制造内撑工装2,对舱段构件1的变形位置进行可调节约束;
[0031]
步骤4:建立有限元仿真平台,根据步骤2中得到的数据对约束热处理过程中应力分布、应力-蠕变演化以及卸载回弹进行系统的预测,基于仿真平台的系统试算进行加载位
置和加载强度的选择;
[0032]
步骤5:基于仿真平台的结果确定约束位置、约束强度进行舱段构件1与内撑工装2的组装和锁紧,之后将舱段构件1与内撑工装2同时放入热处理炉进行热处理。
[0033]
本实施例步骤1:对舱段构件1的形状畸变进行测量,对约束位置进行判断,通过三维轮廓仪对舱段构件1外廓进行测量,形成舱段构件1外轮廓的数模,之后通过与理想数模三维比对获得圆度变化的空间分布。步骤2:获取变形和蠕变的本构关系,获取材料参数,主要基于热模拟实验和蠕变试验获得舱段构件1材料本构关系,为了涵盖舱段构件1热处理全过程,变形和蠕变关系的获取必须涵盖不同材料状态。步骤3:在步骤1的基础上,根据舱段构件1变形的方式,考虑可能的加载位置和加载载荷,进行内撑工装2的设计以实现选定位置的可调节约束,该过程中,内撑工装2材料选择应该考虑约束校形的温度范围,保证内撑工装2在全温域内具备足够的强度和刚度。步骤4:建立有限元仿真平台、进行系统验证以保证平台仿真的准确性;之后,基于步骤2获得的数据对约束热处理过程中应力分布、应力-蠕变演化以及卸载回弹进行系统的预测;基于仿真平台的系统试算进行加载位置、加载强度的优化选择,实现最优控制。步骤5:在步骤:4的基础上,基于仿真设计的结果确定的约束位置、约束强度进行舱舱段构件1与内撑工装2的组装和锁紧,之后将舱舱段构件1与内撑工装2同时放入热处理炉进行处理。
[0034]
本实施例步骤1中通过轴向不同位置测定径向轮廓,从而选定约束加载位置,不做三维轮廓对比,此方案主要针对结构简单、但舱段构件1三维轮廓难以测量的情形。
[0035]
本实施例中步骤1:通过三维轮廓仪对舱段构件1的外轮廓进行测试,形成外轮廓图;通过与舱段设计数模的对比获得构件圆度变化的情况,标记变形最大的位置作为约束施加的预选位置。步骤2:通过选用相同热处理状态的合金进行热模拟实验和蠕变试验,获得宽温域、宽应变范围、小应变量条件下的应力应变曲线,并据此获得合金的热变形和蠕变本构关系;步骤3:设计和制造舱段内撑工装2,内撑工装2为平面四向或平面六向均匀分布自对顶结构,在轴向可根据校形需要进行多层纵列组装,内撑工装2包括顶块3、中心环4和安装螺栓5,顶块3通过安装螺栓5与中心环4相连。顶块3四向或六向对顶,均匀分布,分别对舱段构件1内腔型面施加载荷可调的约束,将变形舱段构件1尺寸挤压至标准构件尺寸。步骤4:步骤4中选定轴向位置以及径向顶正的位置,并在有限元仿真系统中建立舱段构件1与内撑工装2组合体的模型,对舱段构件1与内撑工装2组合体中各径向位置加载过程以及舱段构件1与内撑工装2组合体温升过程进行仿真,获得应力、应变与的温度分布,模拟舱段构件1中应力和应变的变化并对卸载回弹进行预测;基于回弹预测对加载位置、加载强度和温度进行调整,优化校形工艺。步骤5:在舱段构件1内腔安装内撑工装2,通过安装螺栓5旋进对舱段构件1内腔型面选定位置施压顶正至仿真确定的反弯量,将加载结束的舱段构件1和内撑工装2组合体放入热处理炉,热处理结束后自然冷却至室温,拆除内撑工装2,检查舱段构件1内腔截面的圆度尺寸。
[0036]
以上对本发明所提供的一种铝镁合金薄壁舱段制造变形的校形方法,进行了详细介绍,本文中应用了具体个例对本发明的原理及实施方式进行了阐述,以上实施例的说明只是用于帮助理解本发明的方法及其核心思想;同时,对于本领域的一般技术人员,依据本发明的思想,在具体实施方式及应用范围上均会有改变之处,综上所述,本说明书内容不应理解为对本发明的限制。