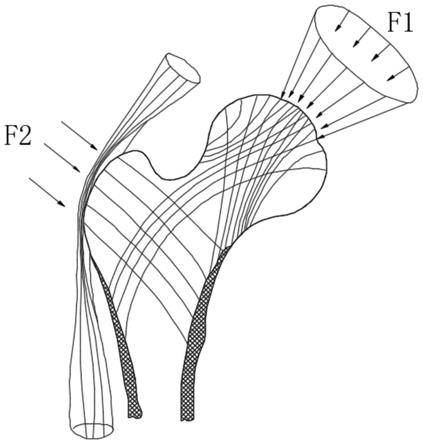
[0001]
本发明涉及人工骨,尤其涉及一种多孔钛人工骨微结构及应用和制造方法。
背景技术:[0002]
现今,人工骨材料方面有生物陶瓷、钛及其合金等。生物陶瓷与人体骨组织结合较好,但其杨氏模量与天然骨不匹配,力学性能差;钛及其合金力学性能较好,但其与人体结合差,易出现炎症、人工骨松动甚至脱落等情况。微结构形貌方面,大多是以仿生鲨鱼皮和莲花效应为代表的疏水性表面微结构,粘附性微结构形貌的非常少。
[0003]
在微结构表面的制造中,现有方法有喷丸、抛光、微铣削、电化学和光刻等。喷丸和抛光加工出的微结构表面虽具有特定粗糙度,但是微结构形状不可控;采用微铣削和电化学方法虽可以制备规则微结构表面,但存在方法复杂、过程繁琐,效率不高等问题;现有的脉冲能量激光刻蚀金属会造成热影响导致表面粗糙等缺陷。
[0004]
公开号为cn108081437a的中国专利公开了陶瓷植体的制备方法,该方法通过对模具进行表面形成多个微结构,利用模具,以陶瓷复合材料覆盖模具的表面,再经过脱模,对脱模后的陶瓷复合材料进行烧结,形成具有微结构表面的陶瓷植体,但是该方法仍存在如下问题:该方法制备的人工骨,虽可以制备表面微结构,但是其微结构形状精度难以保证,在脱模和烧结均会残生误差;同时制备方法过于难度大,模具精度要求高,对操作者熟练度要求较高,从而加大了制备难度。
[0005]
公开号为cn110757092a的中国专利公开了一种人工骨表面功能微结构加工装置及加工方法,该方法是通过五轴联动机床、电磁吸振、液电混合喷雾对人工骨表面进行加工,制备具有功能微结构表面的人工骨,但是该方法仍存在如下问题:该方法制备的人工骨,加工过程中不可避免出现刀具磨损,随着加工时间和里程变长,刀具刃口逐渐出现磨损,从而导致微结构深度不一致、形状不规则,容易产生毛刺和塑性变形、表面粗糙度变坏等。且制备方法复杂,对操作者熟练度要求较高,从而加大了制备难度。
[0006]
公开号为cn110919172a的中国专利公开了一种辊简表面微结构制作设备、系统及方法,该方法通过聚焦激光刻制微结构,保证形状的一致性,但是该方法仍存在如下问题:该方法制备的微结构表面,仅仅保证了形状,但加工成型的表面微结构受热影响,不能解决加工表面粗糙等缺陷。
[0007]
因此,亟待解决上述问题。
技术实现要素:[0008]
发明目的:本发明的第一目的是提供有利于骨组织生长、体液的传输和润滑,同时有效增大微结构表面的粘附性和耐磨性的多孔钛人工骨微结构。
[0009]
本发明的第二目的是提供一种多孔钛人工骨微结构的制造方法。
[0010]
技术方案:为实现以上目的,本发明公开了一种多孔钛人工骨微结构,包括可变拓扑内部微结构和复合三维曲面表面微结构,所述可变拓扑内部微结构包括沿空间应力点按
每个应力点的大小和方向设置的承力线和位于相交承力线围成内部微结构内与天然骨孔隙度值相同的人工骨孔隙,所述复合三维曲面表面微结构包括间隔均布于人工骨表面的主凸起部和次凸起部。
[0011]
其中,所述主凸起部和次凸起部沿水平方向交替排列,且该方向上的主凸起部中心和次凸起部中心连线记为凸起梯度线。
[0012]
优选的,所述主凸起部和次凸起部沿与水平方向成60
°
角方向交替排列,且该方向上的主凸起部中心和次凸起部中心连线记为凸起梯度线。
[0013]
再者,所述主凸起部沿与水平方向成120
°
角方向依次排列。
[0014]
进一步,所述次凸起部沿与水平方向成120
°
角方向依次排列。
[0015]
优选的,所述主凸起部为六边形棱柱,主凸起部的上棱边设有圆弧倒角;所述次凸起部为圆柱体,次凸起部的上边沿设有圆弧倒角。
[0016]
再者,所述主凸起部的边长l为100~300μm,高度h为10~30μm,圆弧倒角的半径与主凸起部高度相同。
[0017]
进一步,所述主凸起部边长与次凸起部的圆柱半径相同,主凸起部的高度与次凸起部的高度相同,相邻主凸起部和次凸起部的中心距离为2l+50~150μm。
[0018]
本发明一种多孔钛人工骨微结构的制造方法,包括如下步骤:
[0019]
(1)、将设计好的可变拓扑内部微结构模型导入三维软件,在可变拓扑内部微结构模型上按固定方向等距划分线,再在线上等距划分点,等距偏置面面上得点,获得加工轨迹控制程序;
[0020]
(2)、首先将钛的粉末铺置在金属基板上,然后根据步骤(1)获得加工轨迹控制程序,通过计算机控制激光束进行加工路径扫描;当能量激光作用于钛粉末时,位于激光束作用区域的钛粉末发生融化,与金属基板形成融合;接着金属基板下降,重新铺一层粉末,该层粉末中位于激光焦距内的粉末熔化,并与下层熔到一起,层层堆积最终形成所需的多孔钛可变拓扑内部微结构;
[0021]
(3)、打开激光器,使激光器发出激光,经由反射镜反射最终通过球面聚光透镜聚焦,再由凹透镜保证信标光光斑直径为一定值,使烧蚀宽度固定作用于工件表面,设置加工所需能量激光的功率、频率和速度,然后根据激光焦点将待加工工件准确放置在运动平台上;
[0022]
(4)、打开超声波发生器发出超声波,经由超声波换能器产生振动,使工件上下振动,调节电流、频率,实现工件上下振动;
[0023]
(5)、同时开启机床的移动平台,将根据复合三维曲面表面微结构编写机床移动平台控制程序,控制移动平台的运动,带动工件移动,完成工件不同位置的微结构形貌加工,对于复合三维曲面表面微结构深度不同的地方通过多次刻蚀完成;
[0024]
(6)、加工完成后立即关闭激光器和超声波发生器,终止平台运动,取下工件,依次放入丙酮、无水乙醇以及去离子水中超声清洗。
[0025]
有益效果:与现有技术相比,本发明具有以下显著优点:本发明的可变拓扑内部微结构利用承力线承担主要受力,内部遍布着孔隙可减轻质量,且有利于骨组织生长、体液的传输和润滑,在满足力学要求的情况下,能更好的与人体骨组织相结合,生物相容性好;本发明依据动物足掌粘附性表面微结构,设计复合三维曲面微结构复合三维曲面表面微结
构,其中主凸起和次凸起交错排列在保证良好的粘附性同时具有更好的耐磨性;本发明采用能量激光和超声波复合加工制备人工骨复合三维曲面微结构,能量激光聚焦光束尺寸可以小于1μm,刻制形状的精细微结构,同时超声振动,解决加工成型后的表面粗糙等问题,获得光滑的曲面微结构。
附图说明
[0026]
图1(a)~图1(c)为本发明中获得最佳承力线的流程图;
[0027]
图2为本发明中人工骨孔隙的结构示意图;
[0028]
图3为本发明中复合三维曲面表面微结构的结构示意图;
[0029]
图4为本发明中复合三维曲面表面微结构的局部示意图;
[0030]
图5为本发明加工系统的结构示意图;
[0031]
图6为本发明中加工透镜组合使用原理图。
具体实施方式
[0032]
下面结合附图对本发明的技术方案作进一步说明。
[0033]
本发明一种多孔钛人工骨微结构,其中人工骨的材料选择多孔钛,多孔钛的孔隙度为5.8~62%,开孔率为60~99.5%,从而保证优异的生物相容性和良好的耐腐蚀性;选取杨氏模量孔隙率与自然骨相匹配的多孔钛,从而保证新骨细胞组织在内生长及体液流通,提高其生物力学相容性。多孔钛人工骨微结构包括可变拓扑内部微结构和复合三维曲面表面微结构,可变拓扑内部微结构包括沿空间应力点按每个应力点的大小和方向设置的承力线和位于相交承力线围成内部微结构内与天然骨孔隙度值相同的人工骨孔隙。承力线根据受力点设置,首先根据人工骨受力情况,进行有限元分析,获得空间各个点的应力情况;根据应力分布作应力圆,据作出的应力圆最终获得主要承力线。如图1(a)~1(c)和图2所示,以股骨为例,首先将股骨模型划分为四面体网格网络,定义材料属性并施加一定的载荷,计算出每个四面体单元应力;拓扑优化迭代:将每个四面体单元应力进行大小排序,去除50%~70%的应力值较小的单元区域,保留剩余的单元区域,经过数次迭代,材料的不断去除50%~70%,结果分布在沿最大主应力方向,即抵抗载荷起关键作用的区域,根据结果得到最佳承力线。
[0034]
根据天然骨不同位置的孔隙度的不同,人工骨对应位置上设置孔隙度值与天然骨相同;人工骨孔隙的孔隙度为5.8~62%,通过增材制造完成,在满足力学要求的同时,质量减轻,且有利于骨组织生长、体液的传输和润滑。
[0035]
复合三维曲面表面微结构包括间隔均布于人工骨表面的主凸起部9和次凸起部10,依据动物足掌类粘附性表面结构特点,并结合天然骨表面特征设计确定,提高人工骨与骨组织的结合能力;从而在保证良好的粘附性同时具有更好的耐磨性。本发明的主凸起部和次凸起部沿水平方向交替排列,且该方向上的主凸起部中心和次凸起部中心连线记为凸起梯度线;主凸起部和次凸起部沿与水平方向成60
°
角方向交替排列,且该方向上的主凸起部中心和次凸起部中心连线记为凸起梯度线11;主凸起部沿与水平方向成120
°
角方向依次排列;次凸起部沿与水平方向成120
°
角方向依次排列。主凸起部为六边形棱柱,主凸起部的上棱边设有圆弧倒角;所述次凸起部为圆柱体,次凸起部的上边沿设有圆弧倒角。主凸起部
的边长l为100~300μm,高度h为10~30μm,圆弧倒角的半径与主凸起部高度相同。主凸起部边长与次凸起部的圆柱半径相同,主凸起部的高度与次凸起部的高度相同,相邻主凸起部和次凸起部的中心距离为2l+50~150μm。
[0036]
人工骨的复合三维曲面表面微结构采用能量波组合加工,具体为超声波和激光,通过搭建的加工系统制备。加工系统包括工件1、凹透镜2、球面透镜3、反光镜4、激光发生器5、移动平台6、超声波发生器7和超声波换能器8,其中球面透镜3和凹透镜2组合使用,两透镜均水平放置,球面透镜3在上,凹透镜2在下,光先经过球面透镜3聚焦,再经过凹透镜2,最终生成的恒定的光斑直径,保证能量光刻蚀宽度恒定;激光由激光发生器发出,激光的为功率10~100w,频率为1~100khz,光束直径为5mm,通过数字信号发生器调节激光功率,激光速度,激光脉冲频率,控制激光输出特定的波形、频率,最终作用于工件。超声波由超声波发生器发出,超声功率为0~300w,频率为20khz~40khz,超声经由换能器作用于机床移动平台,最终实现工件的上下振动,从而获得更好的微结构表面质量,使曲面更加平滑光整。移动平台6为平面运动平台,运动速度0.1~5m/min,加速度1~30m/min2,x轴和y轴行程-100mm~100mm;通过编写编写机床移动平台控制程序控制平台的x轴、y轴移动,带动工件进行加工。
[0037]
本发明的加工原理为:激光发生器发出激光,经由反射镜3次反射最终通过球面透镜聚焦,再由凹透镜保证激光光斑直径为一定值,使烧蚀宽度固定,作用于工件表面。同时超声波发生器发出超声波,经由超声换能器产生振动,使工件上下振动,加工的曲面表面更光滑。加工时打开激光器发出能量激光,调节速度、功率和频率,能量激光由反射镜反射,经过聚光透镜和凹透镜,保持恒定光斑直径烧蚀多孔钛人工骨表面。同时,开启机床的移动平台,将根据复合三维曲面表面微结构编写机床移动平台控制程序,控制移动平台的运动,带动工件移动,完成工件不同位置的微结构形貌加工,对于复合三维曲面表面微结构中深度不同的地方通过多次刻蚀完成。整个过程采用能量激光和超声波的复合加工,能量激光经过反光镜反光、透镜组合聚焦,竖直向下打在工件表面,对工件表面进行刻蚀;同时超声波发生器发出超声波,通过超声换能器作用于移动平台,使移动平台竖直方向上下振动,从而带动工件在竖直方向的上下振动,使得加工成型的微结构表面质量更高,曲面更加光整平滑。因单独的激光加工易造成材料表面的热缺陷,形成气孔、大颗粒熔渣等等;本发明超声振动增加冷却速度,减少加工表面氧化的作用;工件超声振动时激光刻蚀材料表面凝固的纳米颗粒更加细小、密集、分布均匀;有效大颗粒熔渣及重铸层的形成,提高加工表面精度,表面更加光整平滑;本发明采用能量激光和超声波复合加工制备人工骨表面微结构,能量激光聚焦光束尺寸可以小于1μm,刻制形状的精细微结构,同时超声振动,解决加工成型后的表面粗糙等问题,获得光滑的曲面微结构。本发明通过调节激光的速度、功率、频率,实现最终聚焦时的光斑刻蚀直径和刻蚀深度在几微米,实现对复合曲面微结构的沟槽和曲面的刻蚀。
[0038]
本发明一种多孔钛人工骨微结构的制造方法,包括如下步骤:
[0039]
(1)、将设计好的可变拓扑内部微结构模型导入三维软件,在可变拓扑内部微结构模型上按固定方向等距划分线,再在线上等距划分点,等距偏置面面上得点,获得加工轨迹控制程序;
[0040]
(2)、首先将钛的粉末铺置在金属基板上,然后根据步骤(1)获得加工轨迹控制程
序,通过计算机控制激光束进行加工路径扫描;当能量激光作用于钛粉末时,位于激光束作用区域的钛粉末发生融化,与金属基板形成融合;接着金属基板下降,重新铺一层粉末,该层粉末中位于激光焦距内的粉末熔化,并与下层熔到一起,层层堆积最终形成所需的多孔钛可变拓扑内部微结构;
[0041]
(3)、打开激光器,使激光器发出激光,经由反射镜反射最终通过球面聚光透镜聚焦,再由凹透镜保证信标光光斑直径为一定值,使烧蚀宽度固定作用于工件表面,设置加工所需能量激光的功率、频率和速度,然后根据激光焦点将待加工工件准确放置在运动平台上;
[0042]
(4)、打开超声波发生器发出超声波,经由超声波换能器产生振动,使工件上下振动,调节电流、频率,实现工件上下振动;
[0043]
(5)、同时开启机床的移动平台,将根据复合三维曲面表面微结构编写机床移动平台控制程序,控制移动平台的运动,带动工件移动,完成工件不同位置的微结构形貌加工,对于复合三维曲面表面微结构深度不同的地方通过多次刻蚀完成;
[0044]
(6)、加工完成后立即关闭激光器和超声波发生器,终止平台运动,取下工件,依次放入丙酮、无水乙醇以及去离子水中超声清洗。
[0045]
在本发明的描述中,需要说明的是,术语“中间”、“上”、“下”、“左”、“右”、“内”、“外”等指示的方位或位置关系为基于附图所示的方位或位置关系,或者是该发明产品使用时惯常摆放的方位或位置关系,仅是为了便于描述本发明和简化描述,而不是指示或暗示所指的装置或元件必须具有特定的方位、以特定的方位构造和操作,因此不能理解为对本发明的限制。此外,术语“第一”、“第二”等仅用于区分描述,而不能理解为指示或暗示相对重要性。
[0046]
以上详细描述了本发明的优选实施方式,但是,本发明并不限于上述实施方式中的具体细节,在本发明的技术构思范围内,可以对本发明的技术方案进行多种等同变换,这些等同变换均属于本发明的保护范围。另外需要说明的是,在上述具体实施方式中所描述的各个具体技术特征,在不矛盾的情况下,可以通过任何合适的方式进行组合。为了避免不必要的重复,本发明对各种可能的组合方式不再另行说明。