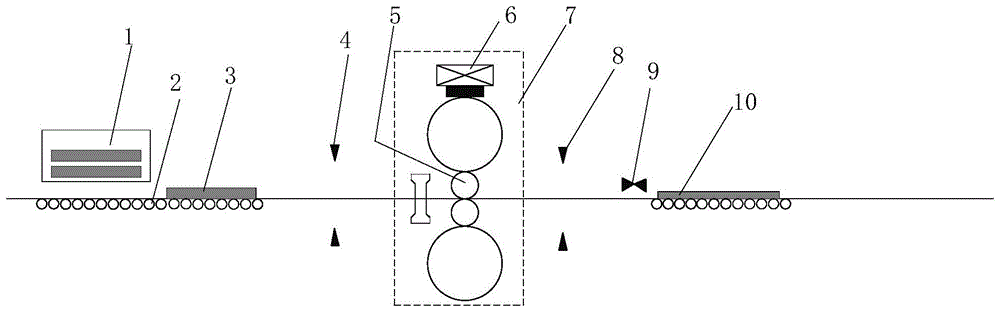
本发明属于轧钢自动控制
技术领域:
,具体涉及一种热连轧中间坯厚度分布的计算方法。
背景技术:
:在热连轧生产过程中,中间坯厚度是重要的工艺参数,中间坯厚度分布是精轧机组轧制力预报和产品厚度自动控制的前提和基础,直接影响到最终成品全长的厚度精度。由于热轧中间坯的厚度一般超过35mm,常规的x射线测厚仪难以测量,因此在热轧生产线上在粗轧出口处不安装测厚仪,导致中间坯厚度的无法直接测量。一般使用弹跳方程模型进行中间坯厚度预估,但因为弹跳方程受到轧辊刚度、轧辊磨辊以及热膨胀等的影响,所以导致中间坯厚度的预估存在偏差,对实际的厚度控制效果造成很大影响。轧件在加热炉加热的过程中,通过步进机构移动,导致轧件在长度方向上温度分布不均匀,另外轧件头部先于轧件尾部进行轧制,导致轧件从头至尾存在温度降低的趋势,轧制时轧件温度越高越容易发生轧制变形,而粗轧一般采用恒定辊缝轧制,在此过程中中间坯全长温度和厚度不一致,势必会存在厚度偏差。cn201510632907.4公开了《一种热连轧中间坯厚度计算方法》,该专利通过现场仪表实测数据,根据秒流量恒定原则计算中间坯平均厚度,得到了中间坯厚度的平均值;另外,《基于软测量模型的粗轧厚度预测方法》提出了一种简单的厚度软测量模型,基于典型粗轧区的仪表配置,模型从轧件跟踪、数据处理等方面进行了针对性的研究,通过软测量模型预报的各道次厚度平均值。上述方法能够得到的是中间坯厚度平均值,能够为后续精轧轧件的厚度控制提供参考,但是无法得到沿长度方向准确的中间坯厚度分布。技术实现要素:针对现有技术存在的不足,本发明提供一种热连轧中间坯厚度分布的计算方法。本发明的技术方案是:一种热连轧中间坯厚度分布的计算方法,包括以下步骤:步骤1:轧件出炉,将pdi数据发送给粗轧过程自动化,根据轧件长度划分样本;其中:pdi数据主要包括轧件尺寸数据、中间坯尺寸数据、成品尺寸数据、钢种名称以及化学组成成分;将轧件沿长度方向平均划分为n个样本,并标识样本之间的分界线,n≥1,将轧制时第1道次头部的第1个样本定义为第1样本;步骤2:根据pdi数据触发粗轧模型计算,轧件按照粗轧轧制规程开始进行轧制过程;步骤3:记录本道次粗轧入口温度,计算本道次轧制前各样本的温度;各样本的温度按照下式计算:式中:ti,j为第i道次,第j样本的轧制前的温度,k;i=1,2,3……a;j=1,2,3……n;ti,j,k为第i道次第j样本中第k个采样点的温度,k=1,2,3……n,k;n为每个样本内温度采样点总数;a为自然数;步骤4:计算各样本到达辊缝处的温度,计算各样本与第1样本的温度偏差和厚度偏差;若本道次为粗轧第1道次,则厚度偏差为0;若本道次不为粗轧第1道次,则采用上一道次的厚度偏差计算结果;步骤5:进行本道次的轧制过程,对本道次进行基于温度、厚度的轧制特性分析,计算辊缝处温度偏差和轧制前厚度偏差造成的轧制后厚度偏差;步骤6:继续后续道次轧制,重复步骤3-5;根据第a道次轧出的厚度和厚度偏差计算得到中间坯的厚度分布。所述热连轧中间坯厚度分布的计算方法,其中:所述步骤4具体步骤为:步骤4.1:计算各道次样本从测温仪到达辊缝处所用的时间;步骤4.2:利用计算得到的时间,计算各样本从测温仪到辊缝过程中各样本的空冷温降;步骤4.3:计算得到各样本到达辊缝处的温度;步骤4.4:最后计算得到各样本与第1样本辊缝处的温度偏差和厚度偏差。所述步骤5具体步骤为:步骤5.1:以本道次第1样本实测轧制力和理论轧制力计算为基准,对轧制力计算公式进行修正;步骤5.2:使用修正后的轧制力计算公式进行轧制特性分析,计算偏微分系数;步骤5.3:计算温度偏差造成的本道次轧制后各样本与第1样本的厚度偏差;步骤5.4:计算轧制前厚度偏差造成的本道次轧制后各样本与第1样本的厚度偏差;步骤5.5:计算本道次轧制后的厚度偏差总值。所述步骤6具体步骤为:步骤6.1:重复步骤3-5计算可得到第a道次轧制后的厚度偏差;步骤6.2:根据第a道次轧制后各样本的厚度偏差计算中间坯的厚度分布。本发明的有益效果:本发明根据轧件在粗轧过程中温度的变化,通过测温仪测得轧件的温度,通过温降模型计算得到了轧件在粗轧过程中温度变化情况,计算得到粗轧各道次轧件长度方向上不同位置的温度分布,基于在线轧制力的校核,借助于轧制特性分析计算得到了温度偏差、厚度偏差对轧制过程各道次厚度的影响规律,最终得到了中间坯长度方向上的厚度分布情况,为精轧区厚度控制提供准确的源数据,为产品厚度的高精度控制提供了良好条件。附图说明图1本发明实施方式采用的热连轧粗轧区主要设备及仪表布置图;1-加热炉,2-输送辊道,3-轧件,4-粗轧入口测温仪,5-速度传感器,6-压力传感器,7-粗轧机组,8-粗轧出口测温仪,9-粗轧出口测宽仪,10-中间坯;图2本发明实施方式的奇数道次轧制方向示意图;图3本发明实施方式的偶数道次轧制方向示意图;图4本发明实施方式的中间坯厚度计算流程图;图5本发明实施方式的第1道次各样本温度图;图6本发明实施方式的第5道次各样本温度图;图7本发明实施方式的中间坯厚度分布图。具体实施方式下面结合附图对本发明的具体实施方式做详细说明。本实施方式中热连轧粗轧区主要设备及仪表布置如图1所示,以总道次为5道次的粗轧轧制过程为例进行说明:轧件3从加热炉1中推出,通过输送辊道2运输,通过粗轧机组7进行轧制,粗轧区轧机上设有速度传感器5和压力传感器6,分别对轧辊速度和轧制力进行测量,之后经过总数为奇数道次(5道次)的粗轧轧制过程,得到中间坯10;其中,奇数道次轧制方向如图2所示,偶数道次轧制方向如图3所示;粗轧入口测温仪4用于测得粗轧奇数道次轧制前轧件温度,粗轧出口测温仪8用于测得粗轧偶数道次轧制前轧件温度,粗轧出口测宽仪9用于测量粗轧轧制后的中间坯宽度。一种热连轧中间坯厚度的计算方法,如图4所示,包括以下步骤:步骤1:轧件出炉,获取pdi数据,并将pdi数据发送给粗轧过程自动化,根据轧件长度划分样本;其中:pdi数据主要包括轧件尺寸数据、中间坯尺寸数据、成品尺寸数据、钢种名称以及化学组成成分,pdi数据如表1所示;表1pdi数据将轧件长度平均划分为n个样本,此处取n=20,将轧制时第1道次头部的第1个样本定义为第1样本;步骤2:根据pdi数据触发粗轧模型计算,轧件按照粗轧轧制规程开始进行轧制过程;步骤3:记录本道次粗轧入口温度,计算本道次轧制前各样本的温度,第1、5道次粗轧入口温度和各样本在粗轧入口温度如图5,6所示;各样本的温度按照下式计算:式中:ti,j为第i道次,第j样本的轧制前的温度,k;i=1,2,3,4,5;j=1,2,3……n;ti,j,k为第i道次第j样本中第k个采样点的温度,k=1,2,3……n,k;n本样本内温度采样点总数;第1道次各样本在粗轧入口处的温度如表2所示;表2第1道次各样本在粗轧入口处的温度样本温度/k样本温度/k样本温度/k样本温度/k11453.48061448.041111451.992161446.87321426.19171431.400121425.193171430.29631440.56081428.121131439.859181427.22641453.87491440.538141453.086191439.73451463.760101460.214151462.752201459.598步骤4:计算各样本到达辊缝处的温度,计算各样本与第1样本的温度偏差和厚度偏差;若本道次为粗轧第1道次,则厚度偏差为0;若本道次不为粗轧第1道次,则采用上一道次的厚度偏差计算结果;具体为:步骤4.1:计算各道次样本从测温仪到达辊缝所用的时间:式中:τ为各样本从测温仪到达轧机辊缝处所用的时间,s;l为测温仪与辊缝处的距离,m;v为输送辊道速度,m/s;步骤4.2:计算各样本从测温仪到辊缝过程中各样本的空冷温降:式中:为第i道次第j样本的空冷温降,k;ε为热辐射率,ε=0.8;σ为斯蒂芬-玻尔兹曼常数,σ=5.69w/(m2·k4);γ为轧件密度,kg/m3;c为轧件比热,j/(kg·k);hi,j为第i道次第j样本轧制前的厚度,mm;步骤4.3:计算各样本到达辊缝处的温度;式中:ti,j为第i道次第j样本在辊缝处的温度,k;第1道次各样本辊缝处的温度如表3所示;表3第1道次各样本辊缝处的温度样本温度/k样本温度/k样本温度/k样本温度/k11452.50561447.081111451.002161445.91621425.28871430.484121424.293171429.38331439.61981427.212131438.921181426.32141452.89991439.598141452.113191438.79551462.759101459.221151461.753201458.607步骤4.4:计算各样本与第1样本辊缝处的温度偏差和厚度偏差;在第1道次开始轧入时轧件没有厚度偏差,所以第1道次时各样本δh1,j=0;δti,j=ti,1-ti,jδhi,j=hi,1-hi,j式中:δti,j为辊缝处第i道次第j样本与第i道次第1样本的温度偏差,k;δhi,j为轧制前第i道次第j样本与第i道次第1样本的厚度偏差,mm;第1道次各样本与第1样本在辊缝处的温度偏差如表4所示;表4第1道次各样本与第1样本在辊缝处的温度偏差样本温度差/k样本温度差/k样本温度差/k样本温度差/k10.00065.424111.483166.589227.218722.0221228.2131723.123312.886825.2931313.5841826.1844-0.393912.907140.3921913.7105-10.25310-6.71615-9.24720-6.102步骤5:进行本道次的轧制过程,对本道次进行基于温度、厚度的轧制特性分析,计算辊缝处温度偏差和轧制前厚度偏差造成的轧制后厚度偏差;具体为:步骤5.1:轧制力计算修正;(1)轧制力理论结果计算公式:p理论=1.15blcqpks/1000式中:b为轧件宽度,mm;lc为压扁后的接触弧长,mm;qp为应力状态影响系数;ks为变形阻力,mpa;(2)记录本道次轧制过程实测轧制力计算轧制过程中各样本的实测轧制力以第1道次第1样本为例,各样本实测轧制力由下式计算:为第i道次第j样本中第k个采样点轧制力,j=1,2,3,……m,kn;m为每一个样本内轧制力采样点总数;为第i道次第j样本的实测轧制力,kn;第1道次各样本轧制力如表5所示;表5第1道次各样本轧制力(3)以本道次第1样本实测轧制力和理论轧制力计算为基准本道次轧制力修正系数f,计算公式如下:修正后的轧制力计算公式为:步骤5.2:使用修正后的轧制力计算公式进行轧制特性分析,计算偏微分系数;计算结果如下:式中:为第i道次轧轧制后厚度偏微分系数;为第i道次轧制前厚度偏微分系数;为第i道次温度偏微分系数;步骤5.3:计算温度偏差造成的本道次轧制后各样本与第1样本的厚度偏差;式中:为第i道次温度偏差对轧制后厚度的影响系数;为第i道次温度偏差引起的对第i道次第j样本轧制后厚度偏差,mm;cp为轧机刚度,取1000kn/mm;步骤5.4:计算轧制前厚度偏差造成的本道次轧制后各样本与第1样本的厚度偏差;式中:为轧制前厚度偏差对轧制后厚度的影响系数;为第i道次轧轧前厚度偏差引起的第i道次第j样本的轧制后厚度偏差,mm;步骤5.5:计算本道次轧制后的厚度偏差和值;式中:δhi,j为第i道次第j样本与第i道次第1样本轧制后的厚度偏差,mm;第1道次轧制后的厚度偏差如表6所示;表6第1道次轧制后的厚度偏差步骤6:继续后续道次轧制,重复步骤3-5;根据第5道次轧出的厚度和厚度偏差计算得到中间坯的厚度分布;具体为:步骤6.1:重复步骤3-5计算可得到第5道次轧制后的厚度偏差;第5道次轧制后各样本的厚度偏差如表7所示;表7第5道次轧制后各样本的厚度偏差步骤6.2:根据第5道次轧制后各样本的厚度偏差计算中间坯的厚度分布;中间坯各样本厚度由下式得到:h5,j=h5,1+δh5,j式中:h5,1为第5道次第1样本轧制后的厚度,h5,1=38mm;h5,j为第5道次第j样本轧制后的厚度,mm;根据上式计算得到的中间坯厚度分布如表8和图7所示;表8中间坯厚度分布表样本厚度/mm样本厚度/mm样本厚度/mm样本厚度/mm138.000637.8821137.8621637.741237.686737.6831237.5401737.533337.839837.6301337.7011837.480437.968937.7621437.8351937.318538.0551037.9601537.9232037.825。当前第1页12